1
/
of
11
www.ChineseStandard.us -- Field Test Asia Pte. Ltd.
YY/T 1702-2020 English PDF (YY/T1702-2020)
YY/T 1702-2020 English PDF (YY/T1702-2020)
Regular price
$260.00
Regular price
Sale price
$260.00
Unit price
/
per
Shipping calculated at checkout.
Couldn't load pickup availability
YY/T 1702-2020: Dentistry - Additive Manufacturing - Selective Laser Melting Metallic Materials for Fixed and Removable Restorations and Appliances
Delivery: 9 seconds. Download (and Email) true-PDF + Invoice.
Get Quotation: Click YY/T 1702-2020 (Self-service in 1-minute)
Newer / historical versions: YY/T 1702-2020
Preview True-PDF (Reload/Scroll-down if blank)
Delivery: 9 seconds. Download (and Email) true-PDF + Invoice.
Get Quotation: Click YY/T 1702-2020 (Self-service in 1-minute)
Newer / historical versions: YY/T 1702-2020
Preview True-PDF (Reload/Scroll-down if blank)
Share
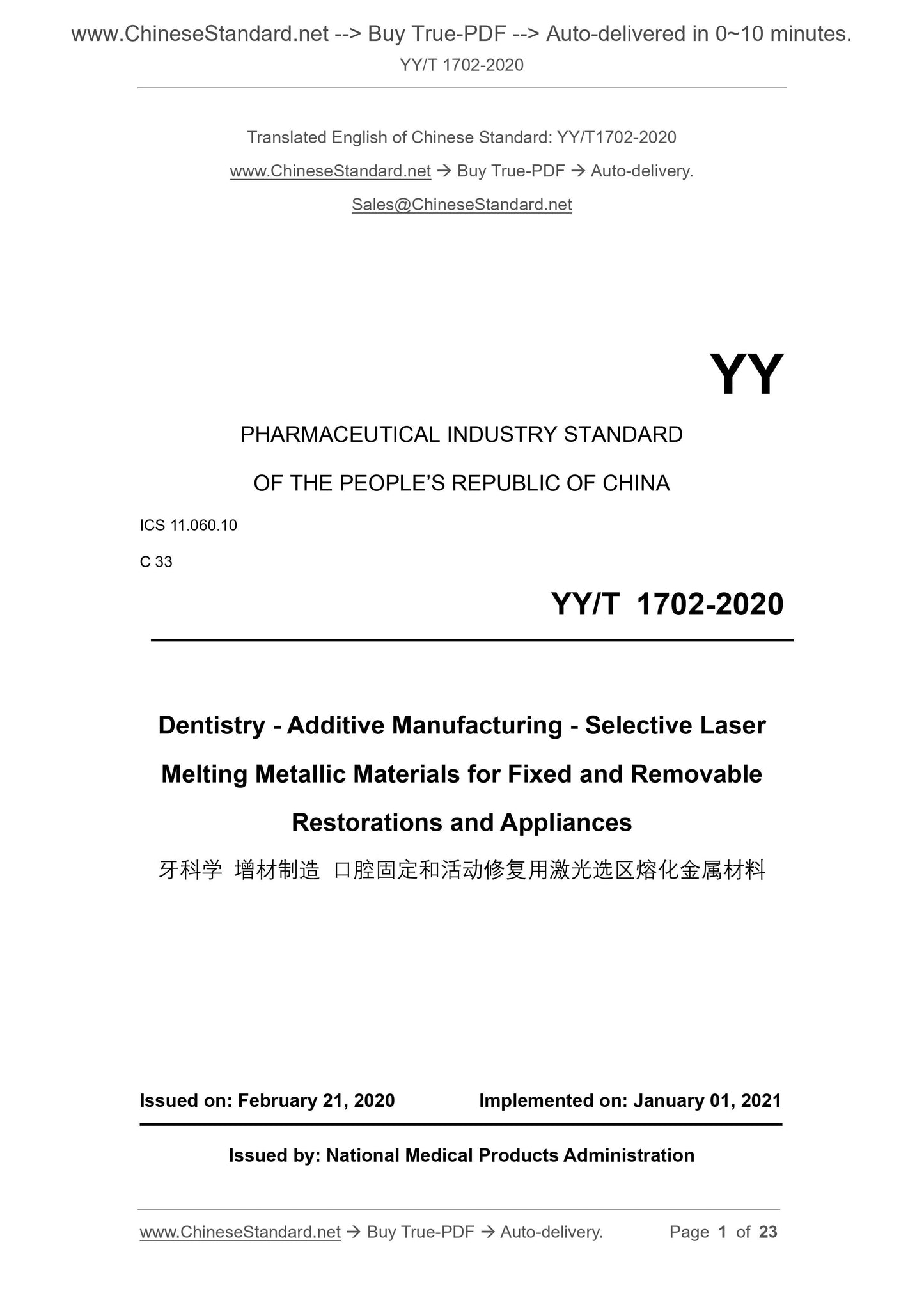
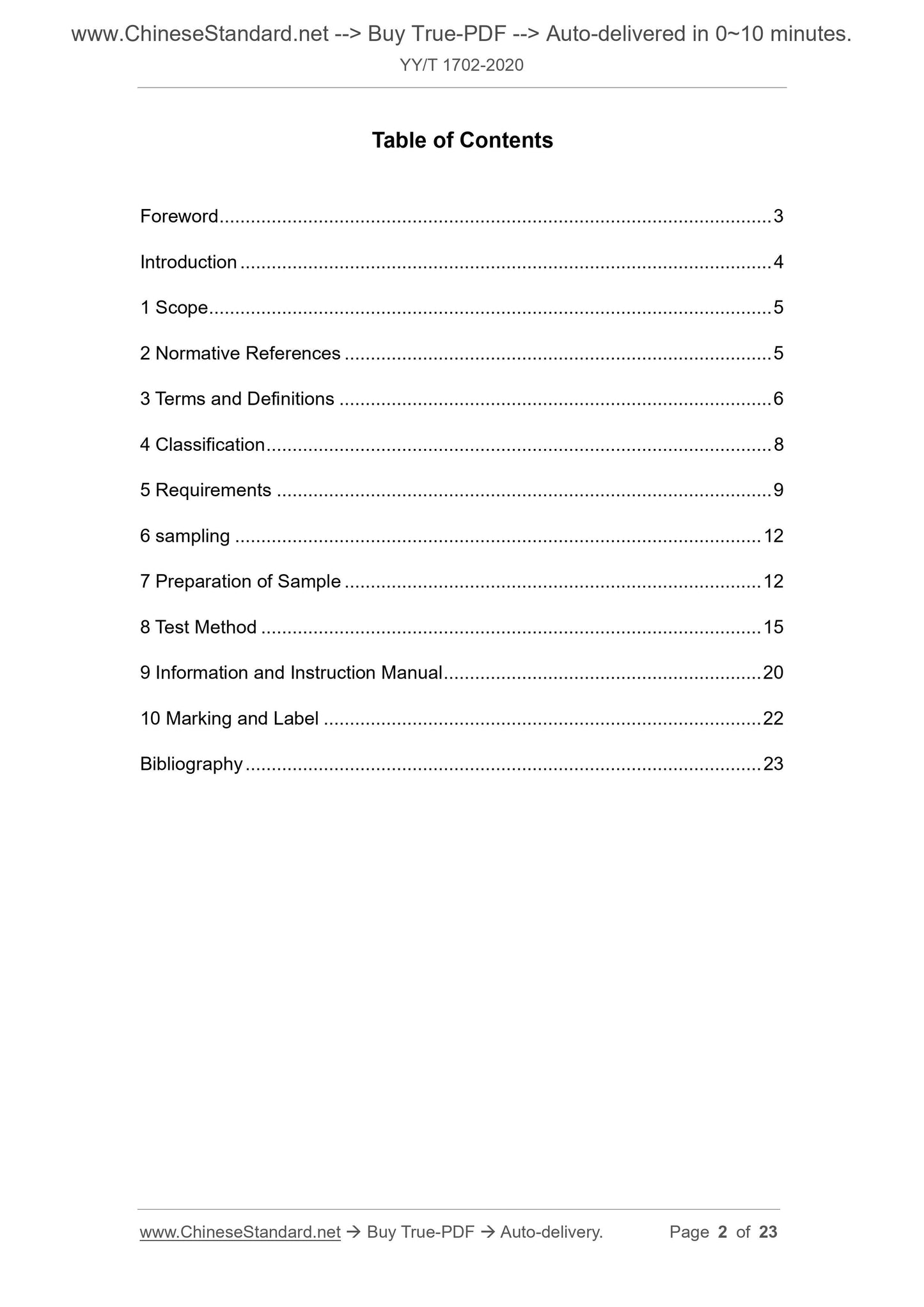
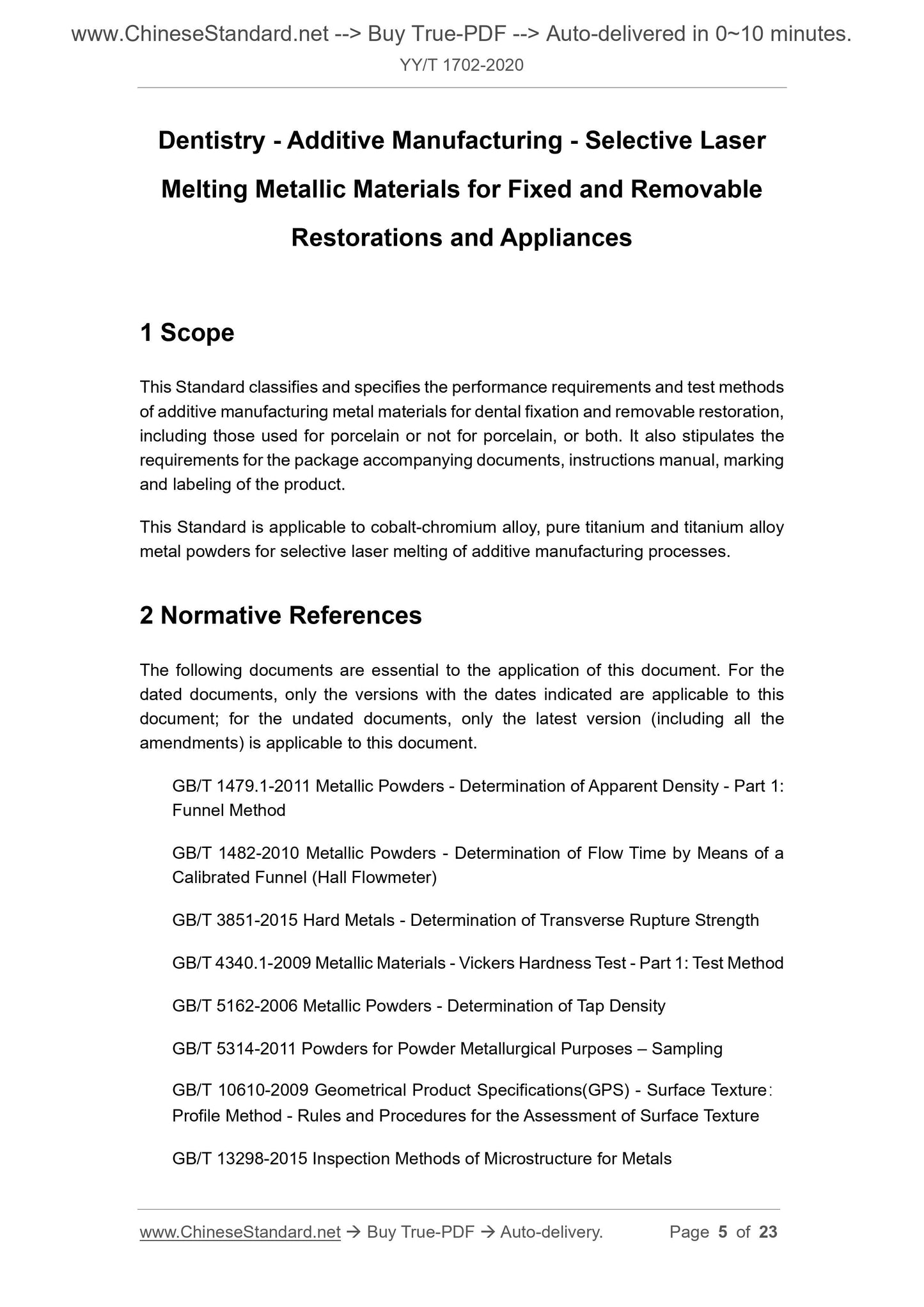
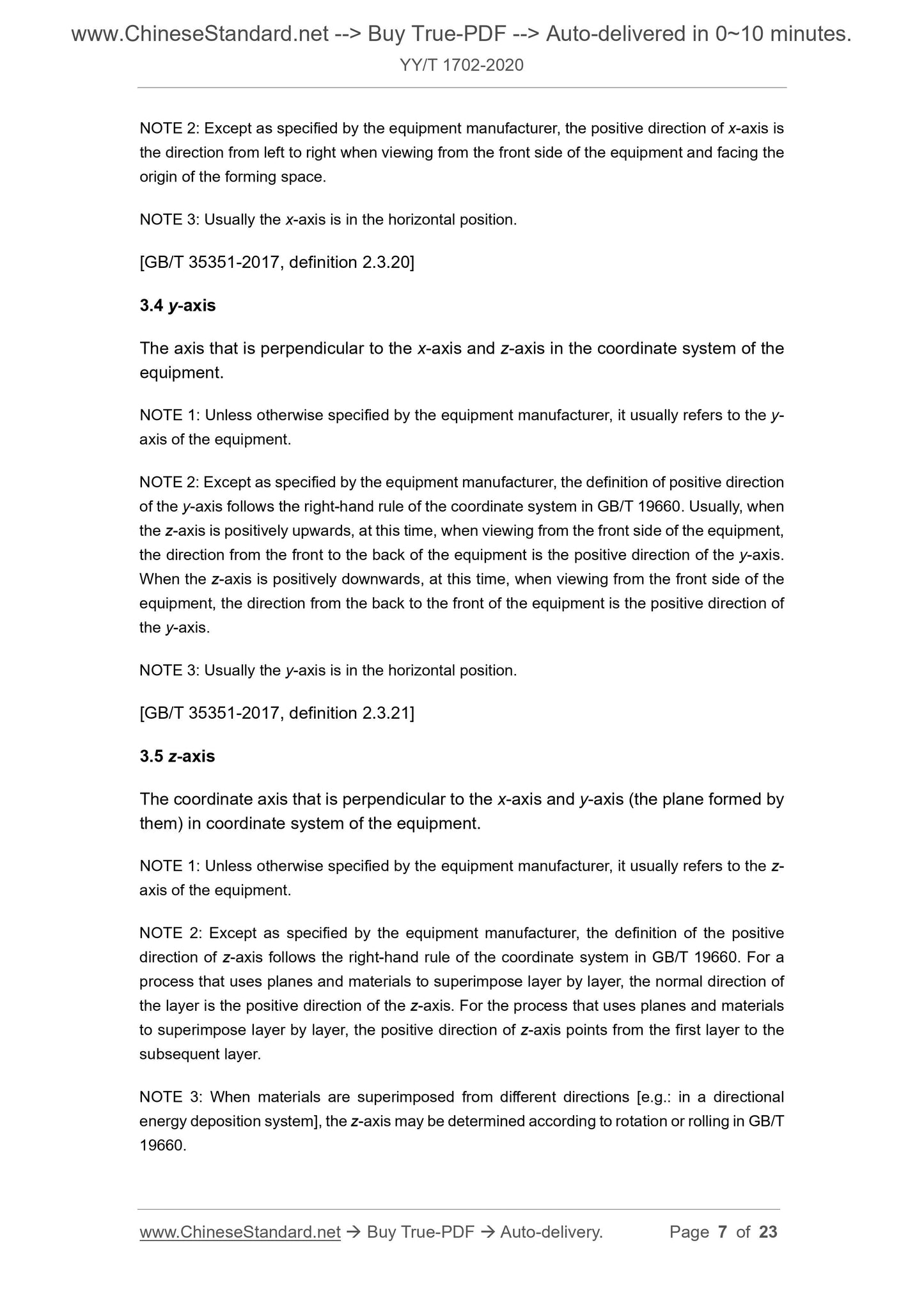
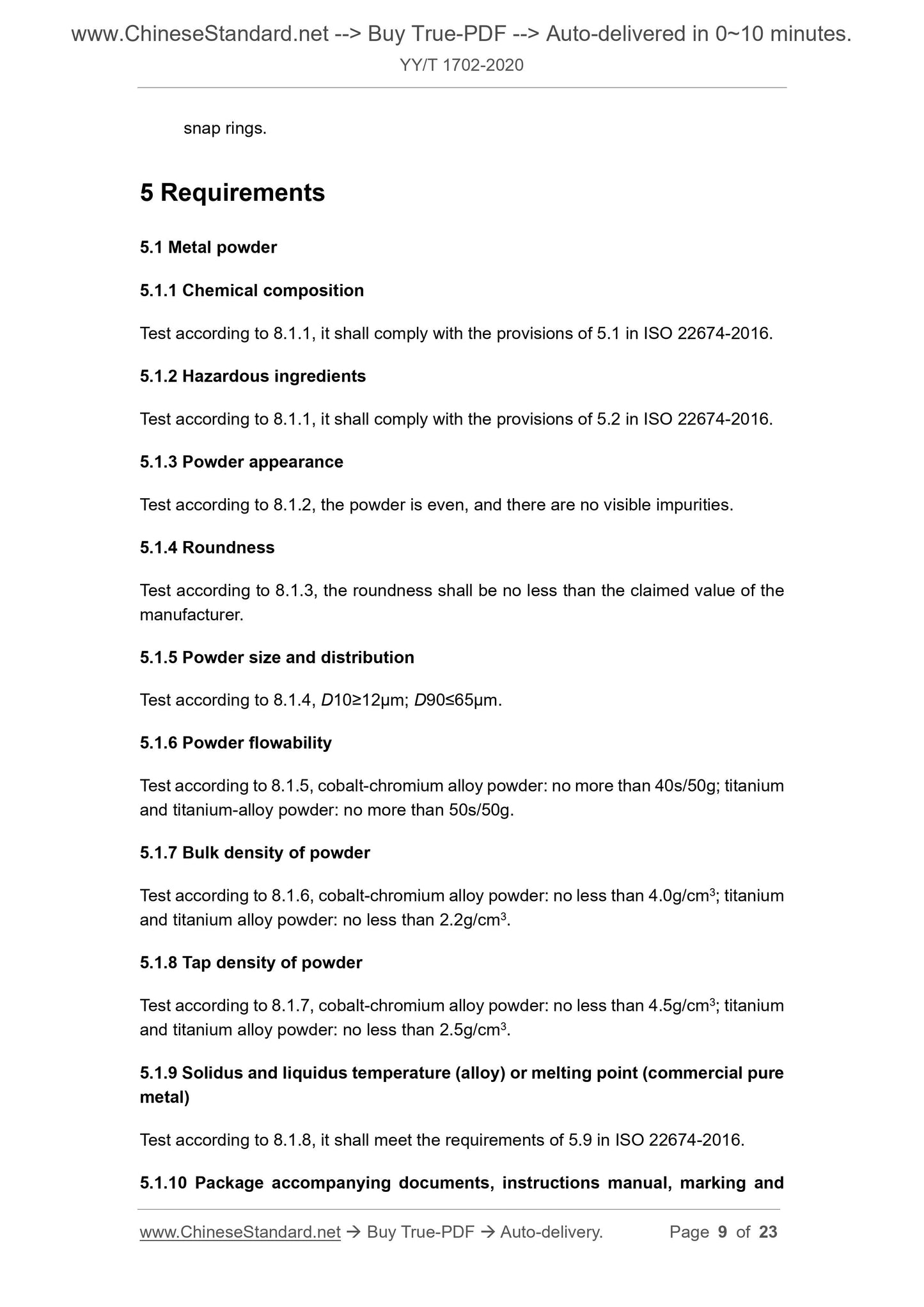
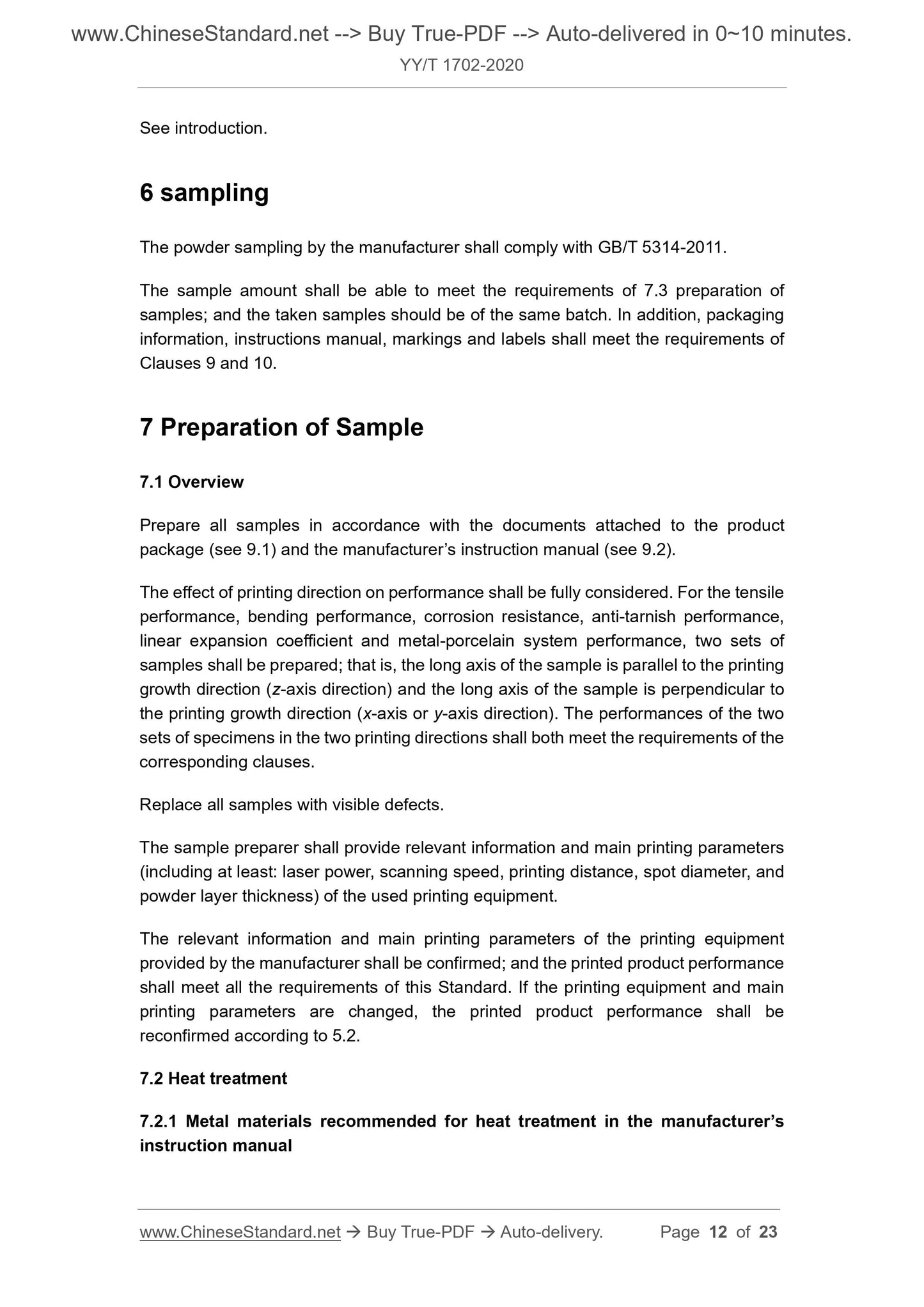
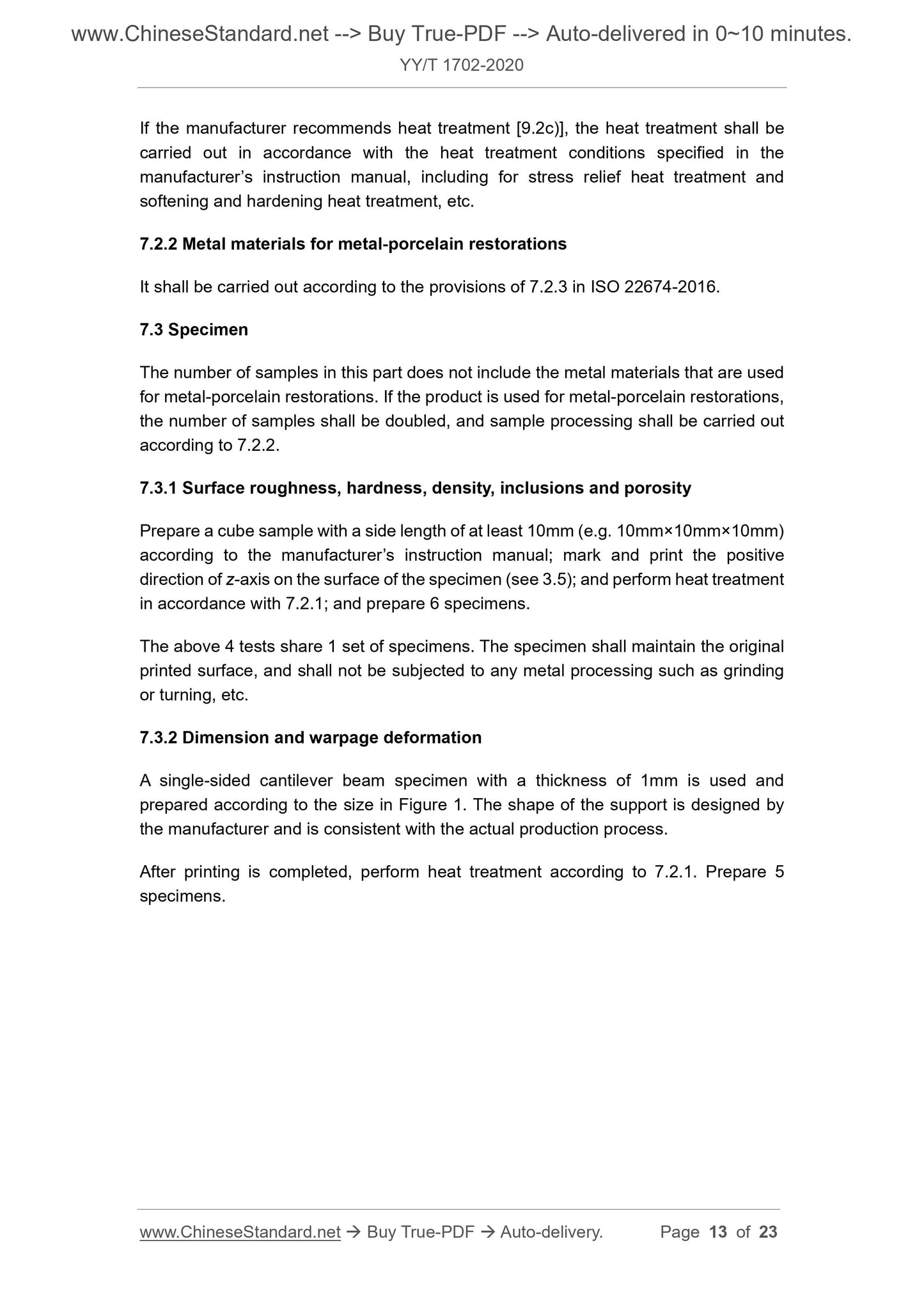
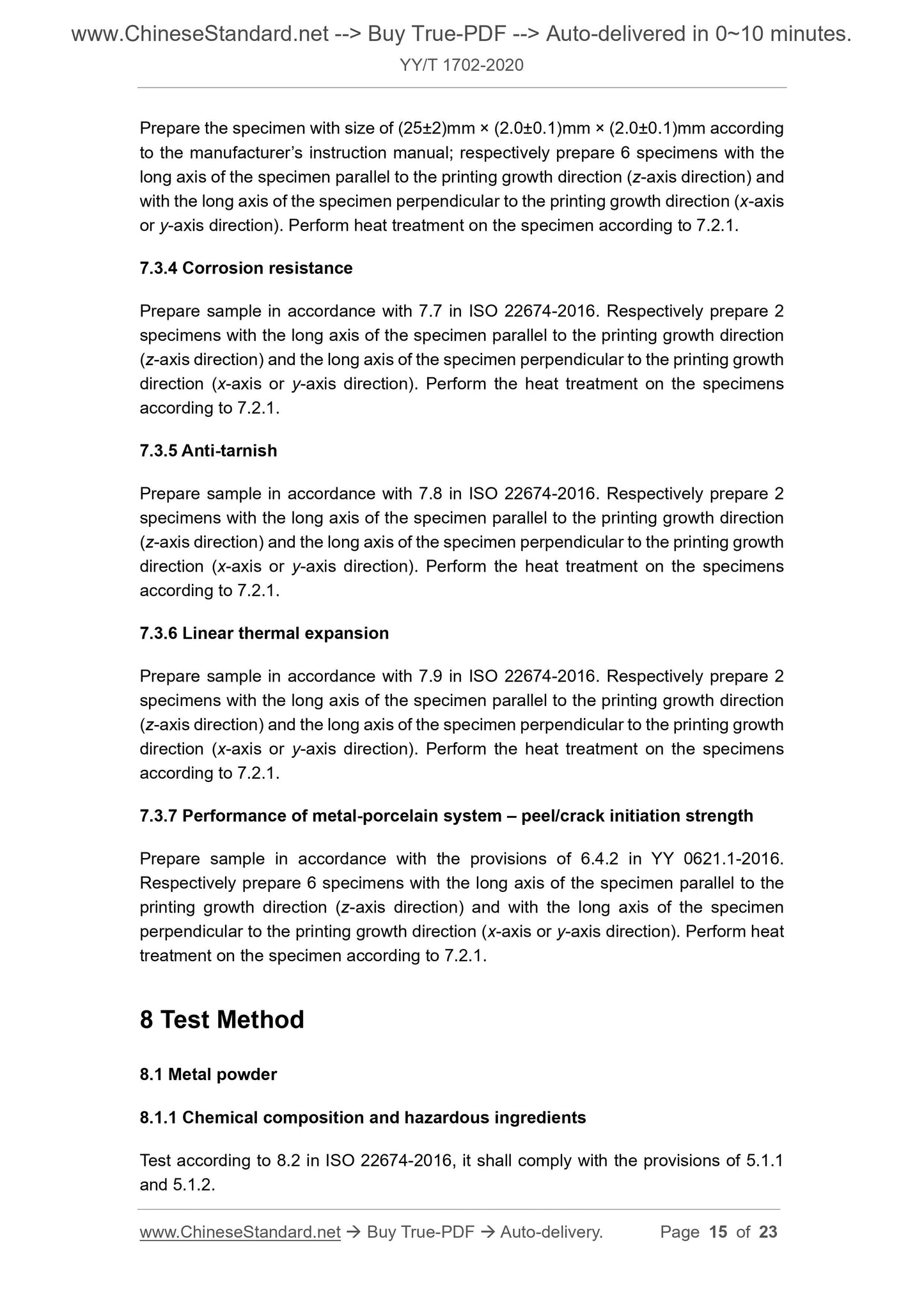
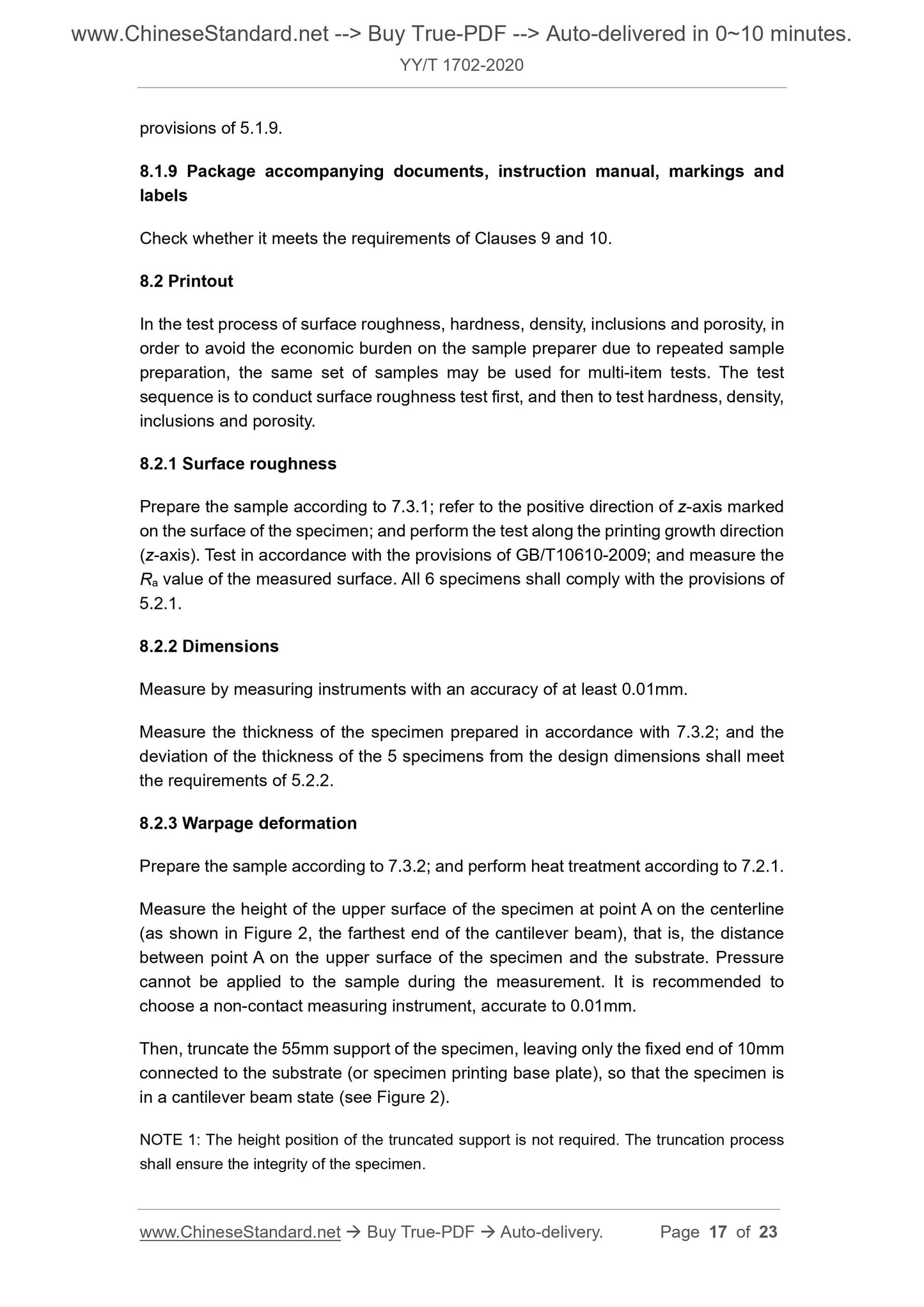
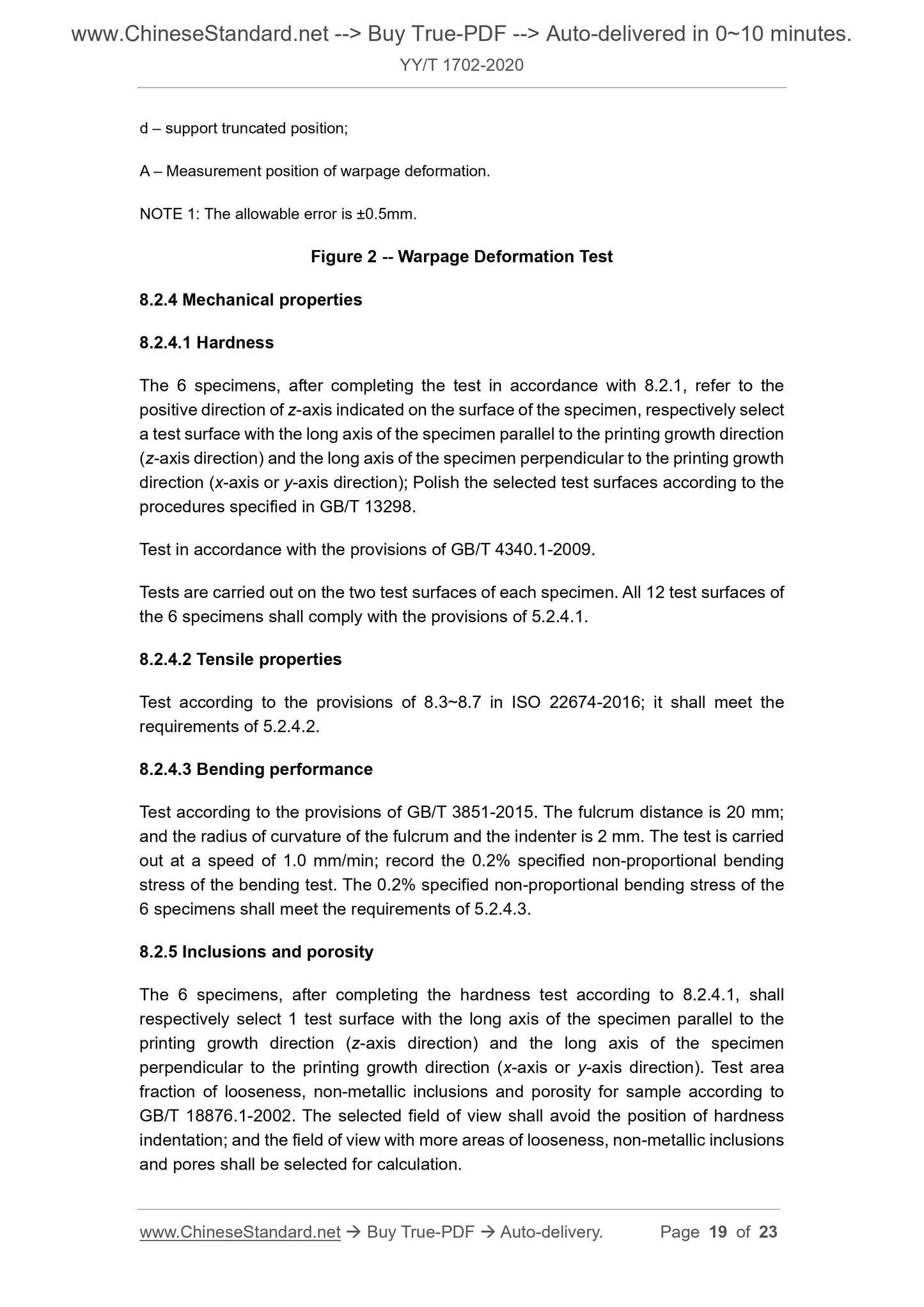
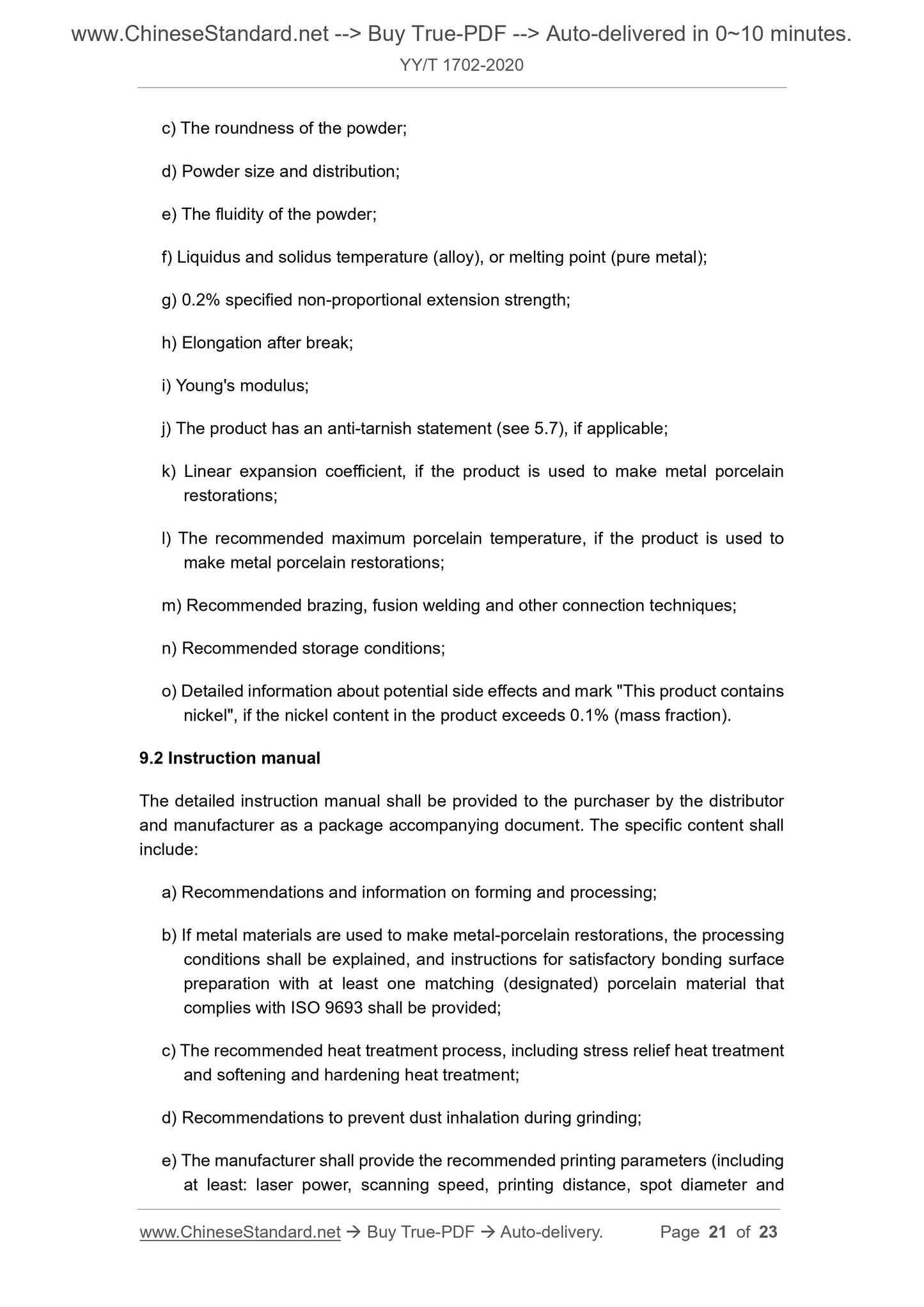