1
/
of
9
www.ChineseStandard.us -- Field Test Asia Pte. Ltd.
YY/T 0681.2-2010 English PDF (YY/T0681.2-2010)
YY/T 0681.2-2010 English PDF (YY/T0681.2-2010)
Regular price
$275.00
Regular price
Sale price
$275.00
Unit price
/
per
Shipping calculated at checkout.
Couldn't load pickup availability
YY/T 0681.2-2010: Test methods for sterile medical device package. Part 2: Seal strength of flexible battier materials
Delivery: 9 seconds. Download (and Email) true-PDF + Invoice.
Get Quotation: Click YY/T 0681.2-2010 (Self-service in 1-minute)
Newer / historical versions: YY/T 0681.2-2010
Preview True-PDF (Reload/Scroll-down if blank)
Delivery: 9 seconds. Download (and Email) true-PDF + Invoice.
Get Quotation: Click YY/T 0681.2-2010 (Self-service in 1-minute)
Newer / historical versions: YY/T 0681.2-2010
Preview True-PDF (Reload/Scroll-down if blank)
Share
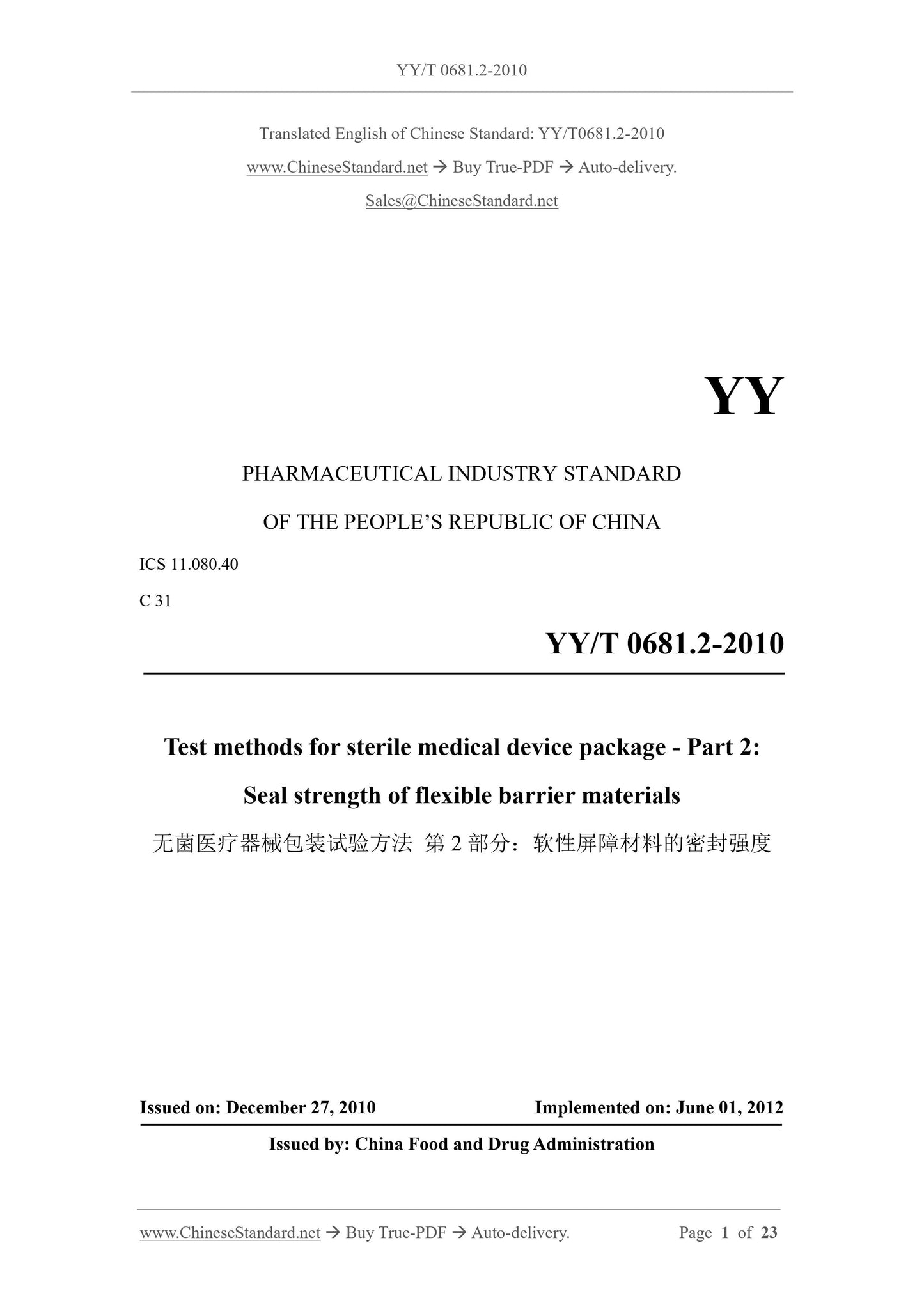
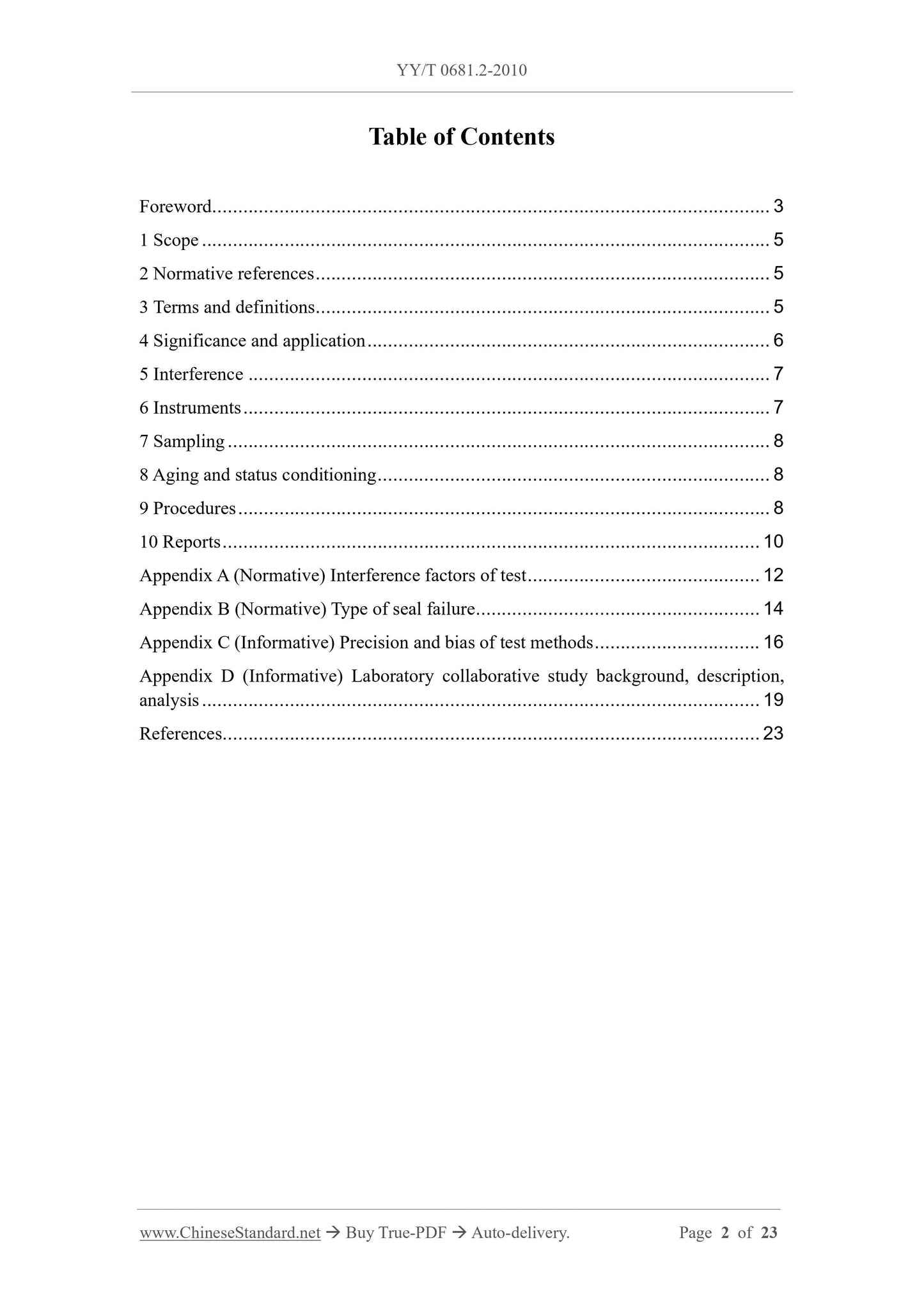
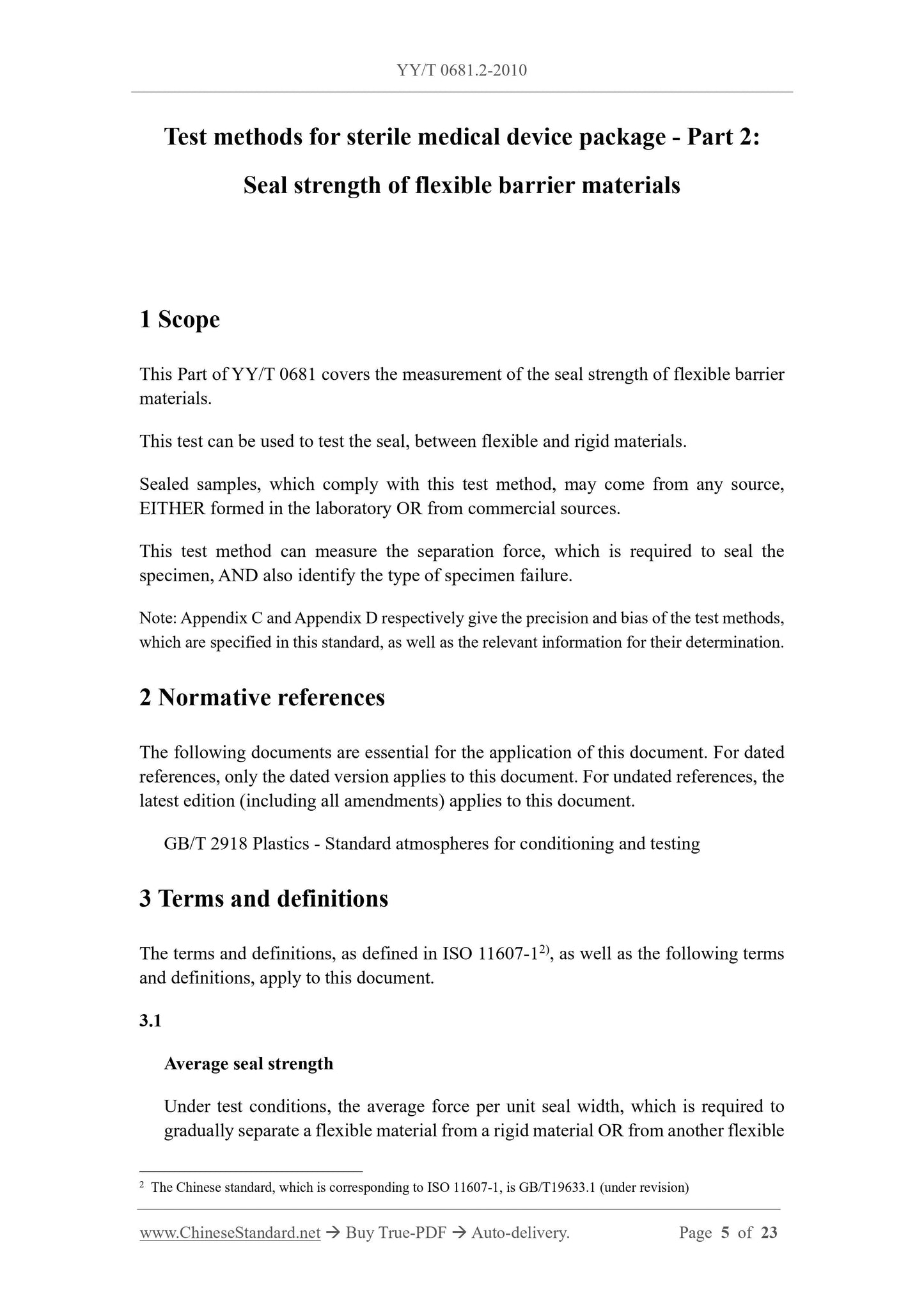
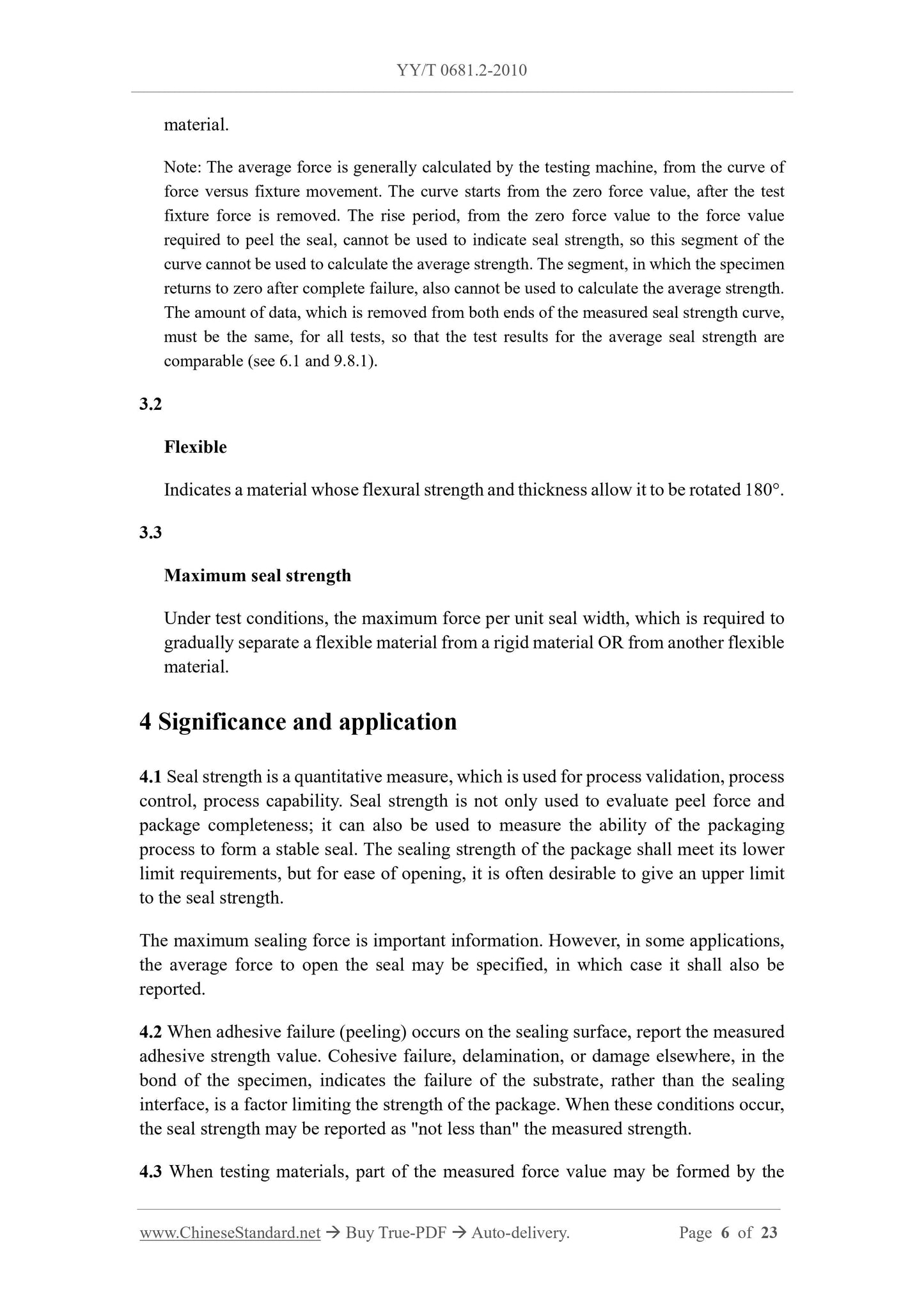
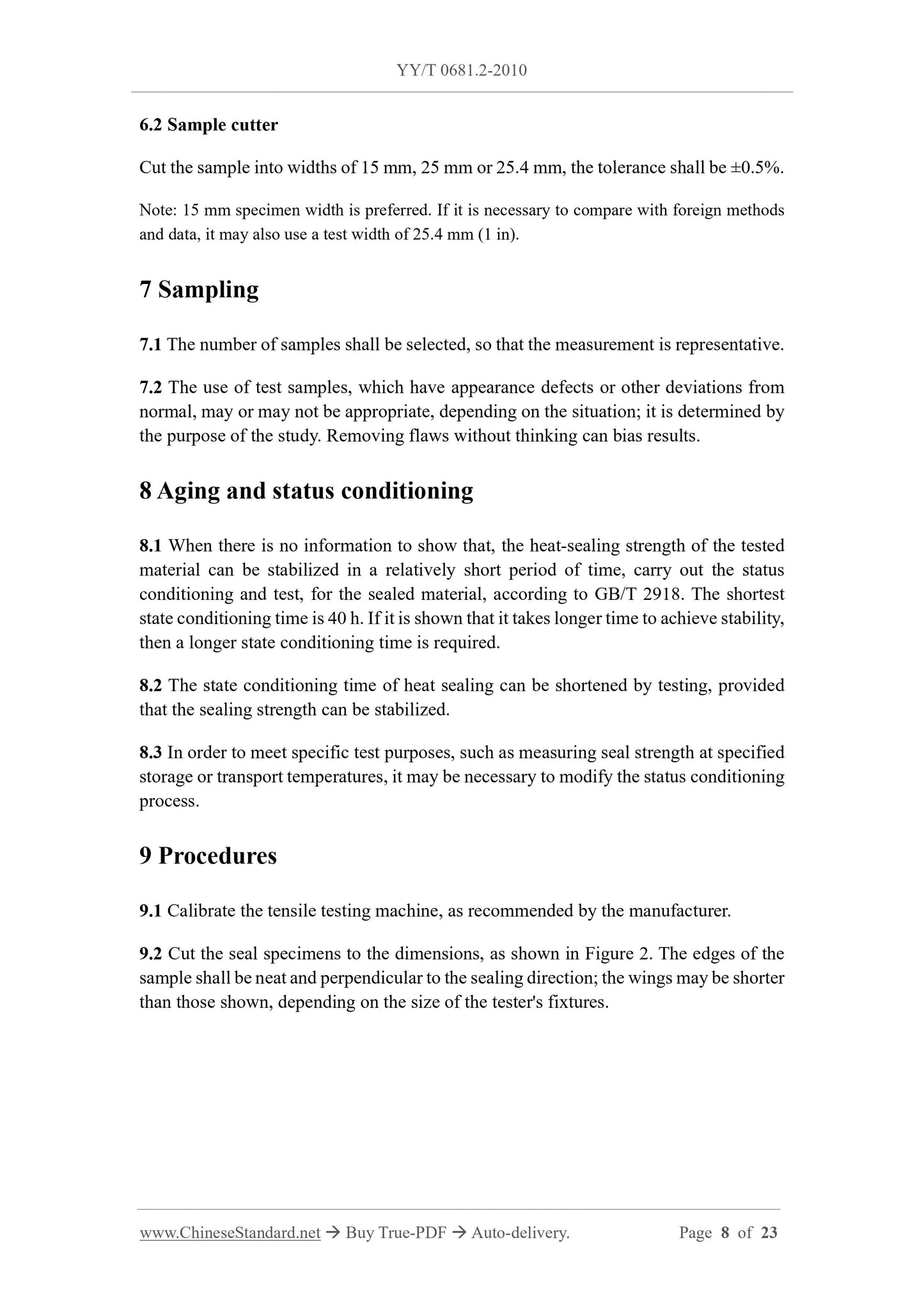
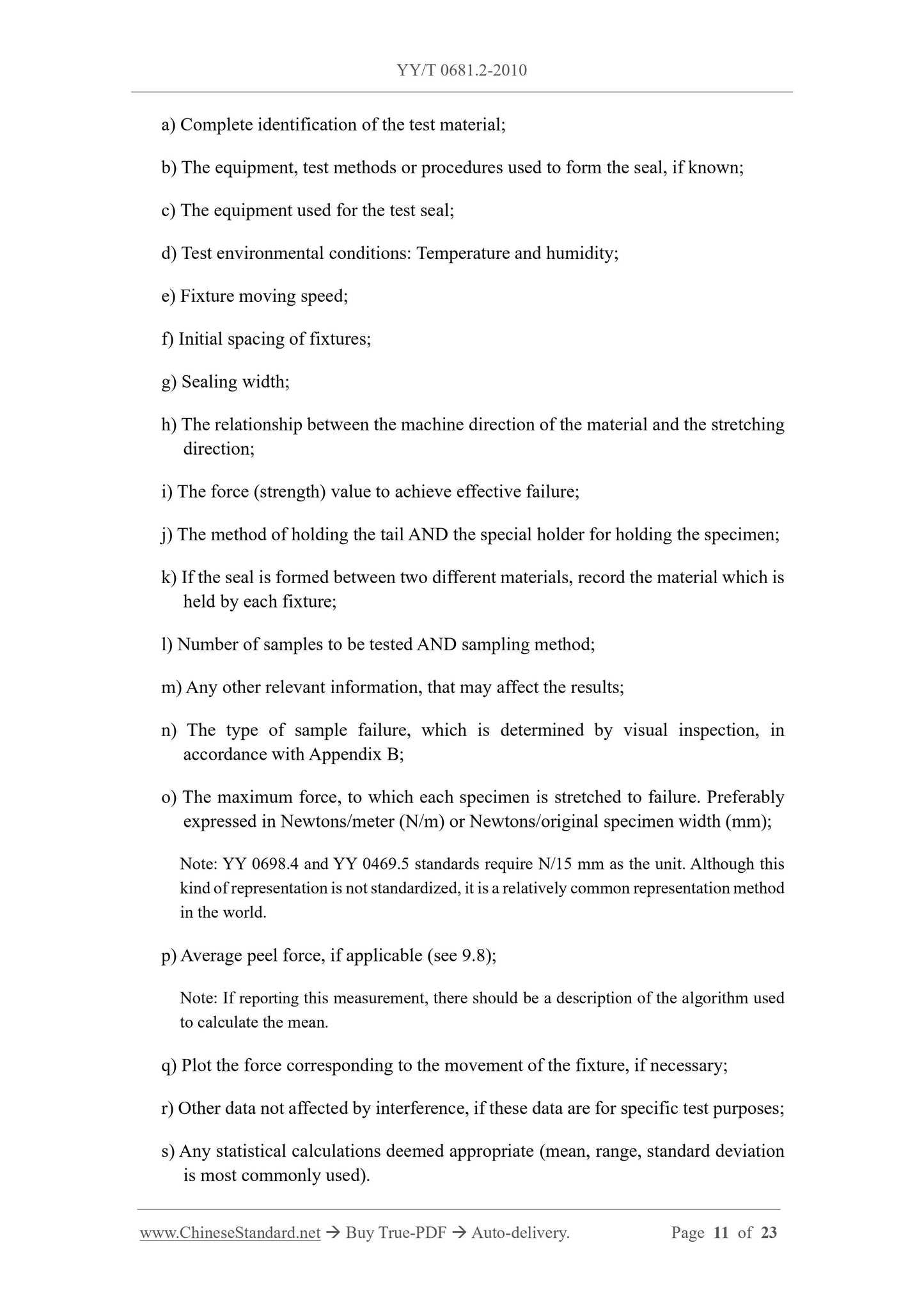
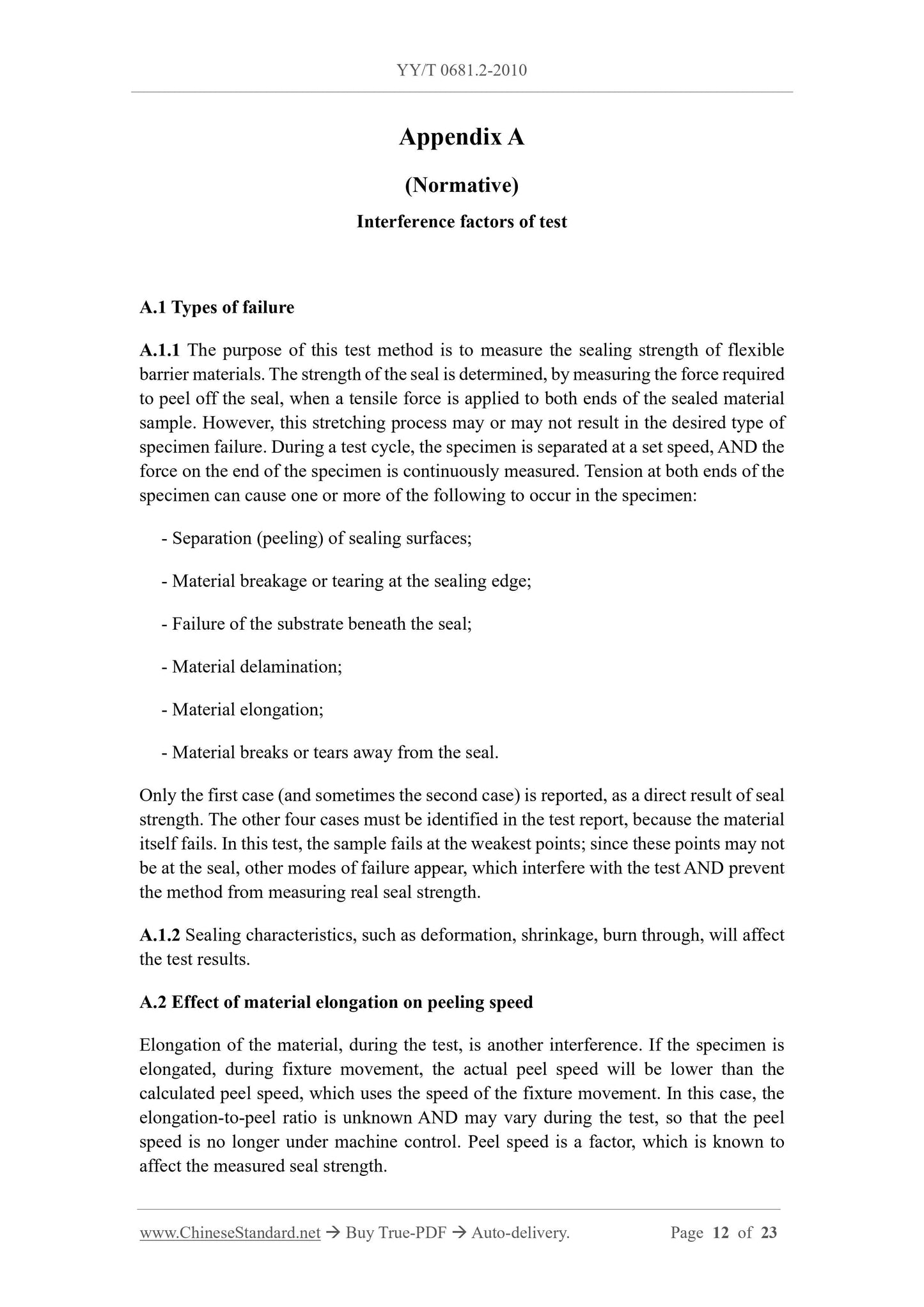
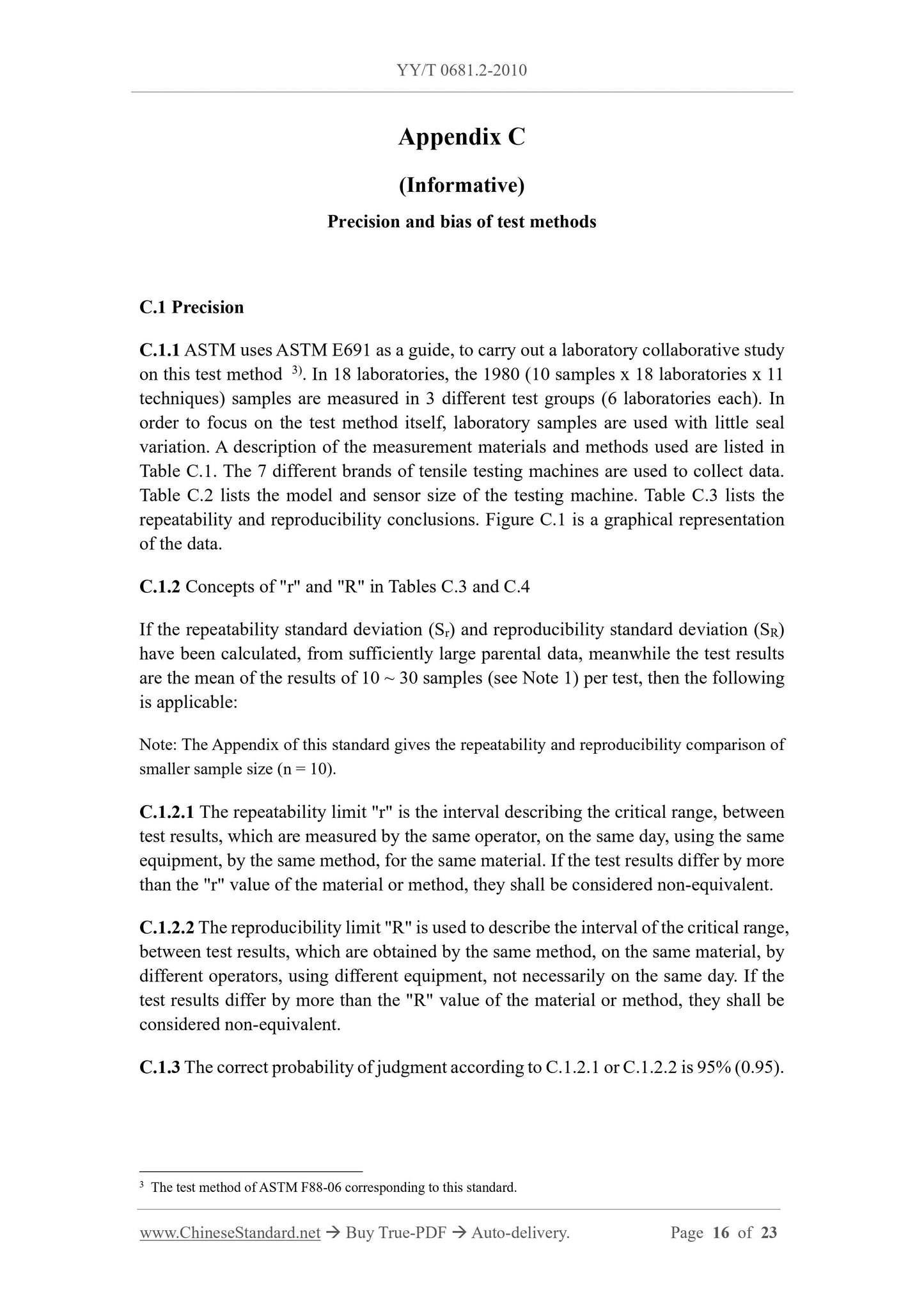
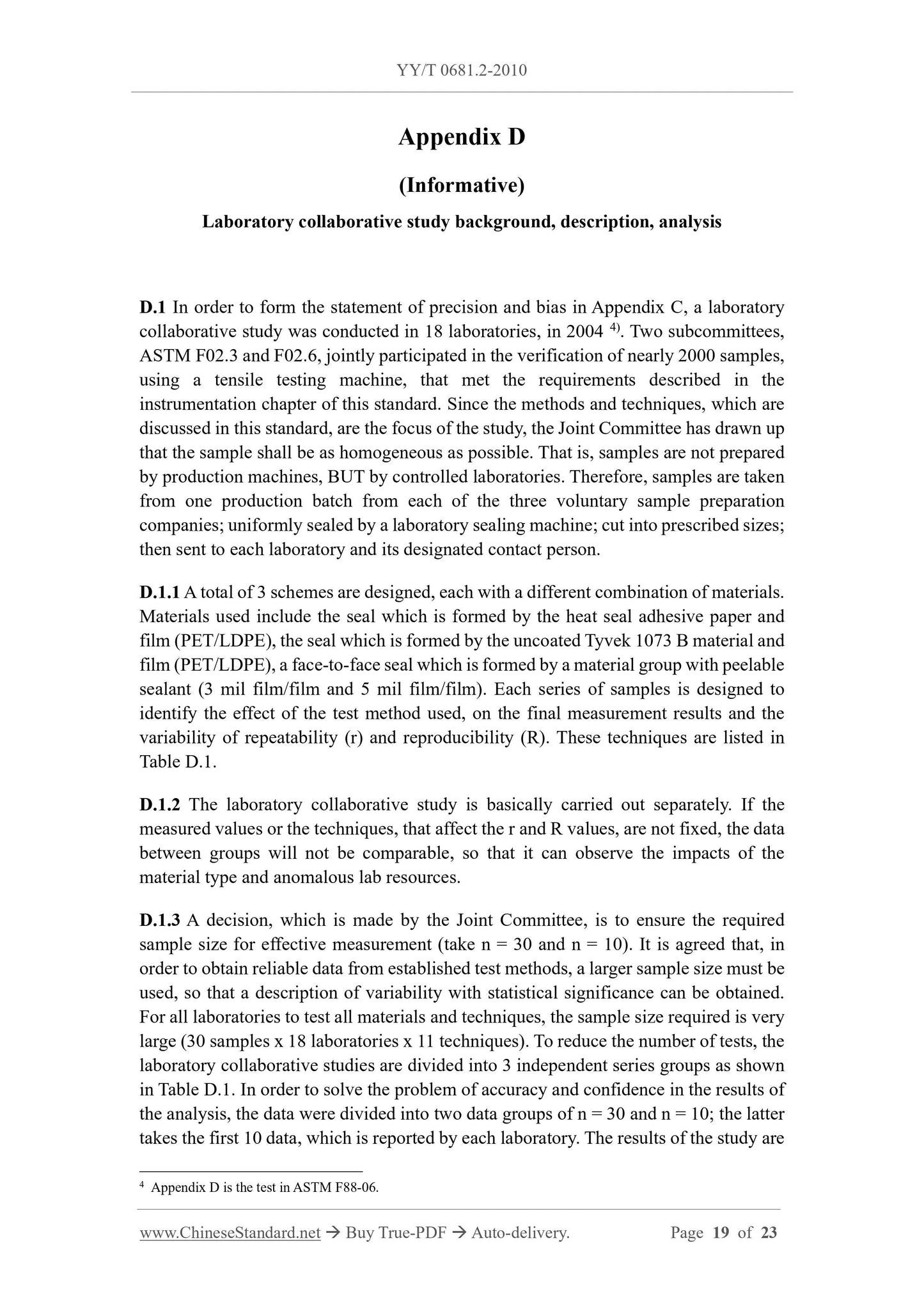