1
/
of
7
www.ChineseStandard.us -- Field Test Asia Pte. Ltd.
SY/T 6996-2014 English PDF (SY/T6996-2014)
SY/T 6996-2014 English PDF (SY/T6996-2014)
Regular price
$145.00
Regular price
Sale price
$145.00
Unit price
/
per
Shipping calculated at checkout.
Couldn't load pickup availability
SY/T 6996-2014: Assessment of Steel Oil and Gas Pipeline with Dent
Delivery: 9 seconds. Download (and Email) true-PDF + Invoice.Get Quotation: Click SY/T 6996-2014 (Self-service in 1-minute)
Newer / historical versions: SY/T 6996-2014
Preview True-PDF
Scope
This Standard specifies the technical requirements for test and assessment ofunder-construction steel oil and gas pipeline with dent.
This Standard is applicable to the assessment of land carbon steel and low-alloy steel
oil and gas pipeline with dent.
Basic Data
Standard ID | SY/T 6996-2014 (SY/T6996-2014) |
Description (Translated English) | Assessment of Steel Oil and Gas Pipeline with Dent |
Sector / Industry | Oil and Gas Industry Standard (Recommended) |
Classification of Chinese Standard | E10 |
Classification of International Standard | 75.010 |
Word Count Estimation | 14,136 |
Date of Issue | 10/15/2014 |
Date of Implementation | 3/1/2015 |
Quoted Standard | SY/T 6151; SY/T 6597; SY/T 6825; SY/T 6889 |
Regulation (derived from) | State Energy Bureau Notice 2014 No. 11 |
Issuing agency(ies) | National Development and Reform Commission |
Summary | This Standard specifies the depressed oil and gas pipelines in service steel testing and evaluation of the technical requirements. This Standard applies to the evaluation of carbon steel and low alloy steel onshore oil and gas pipelines recess. Depression |
Share
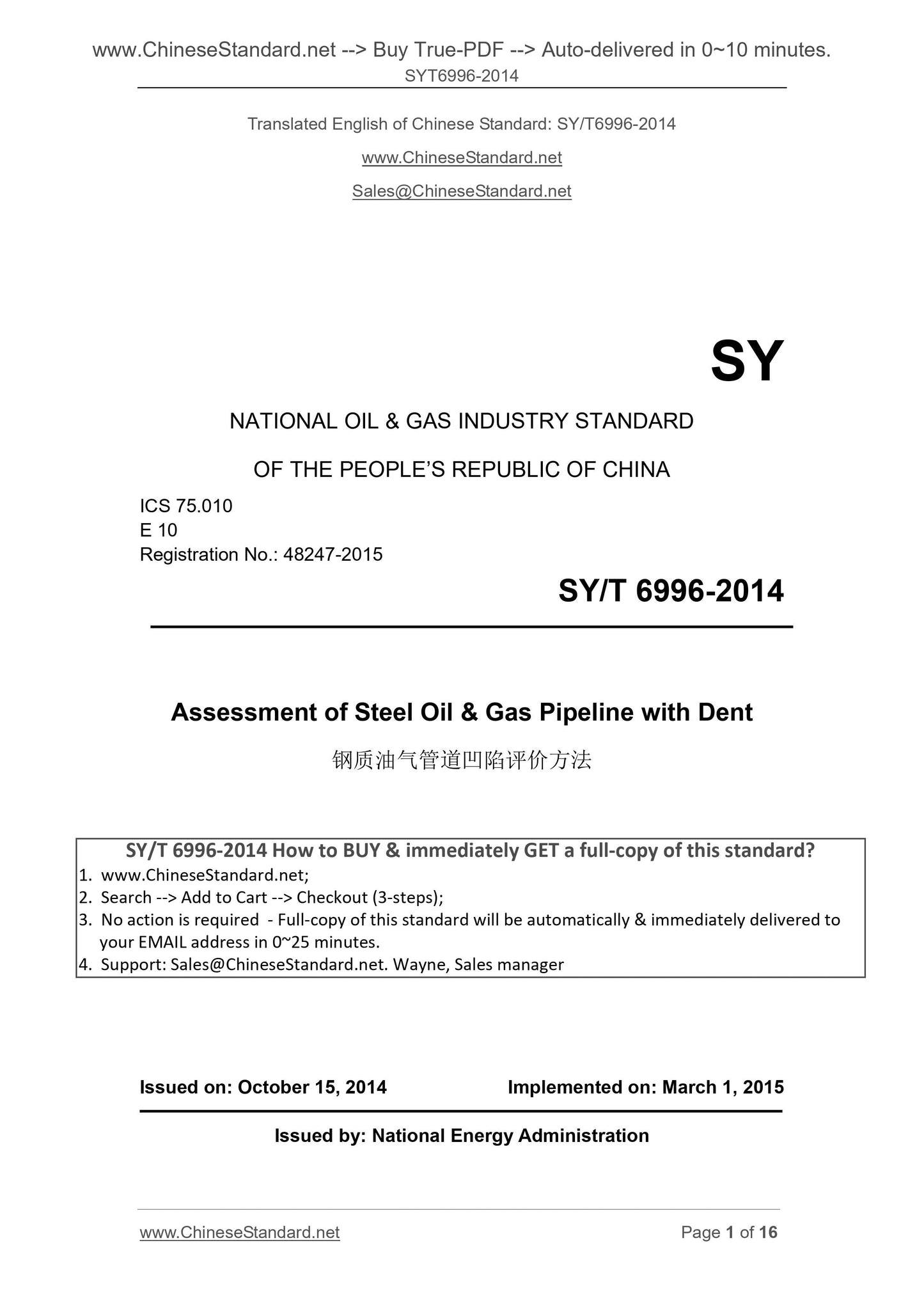
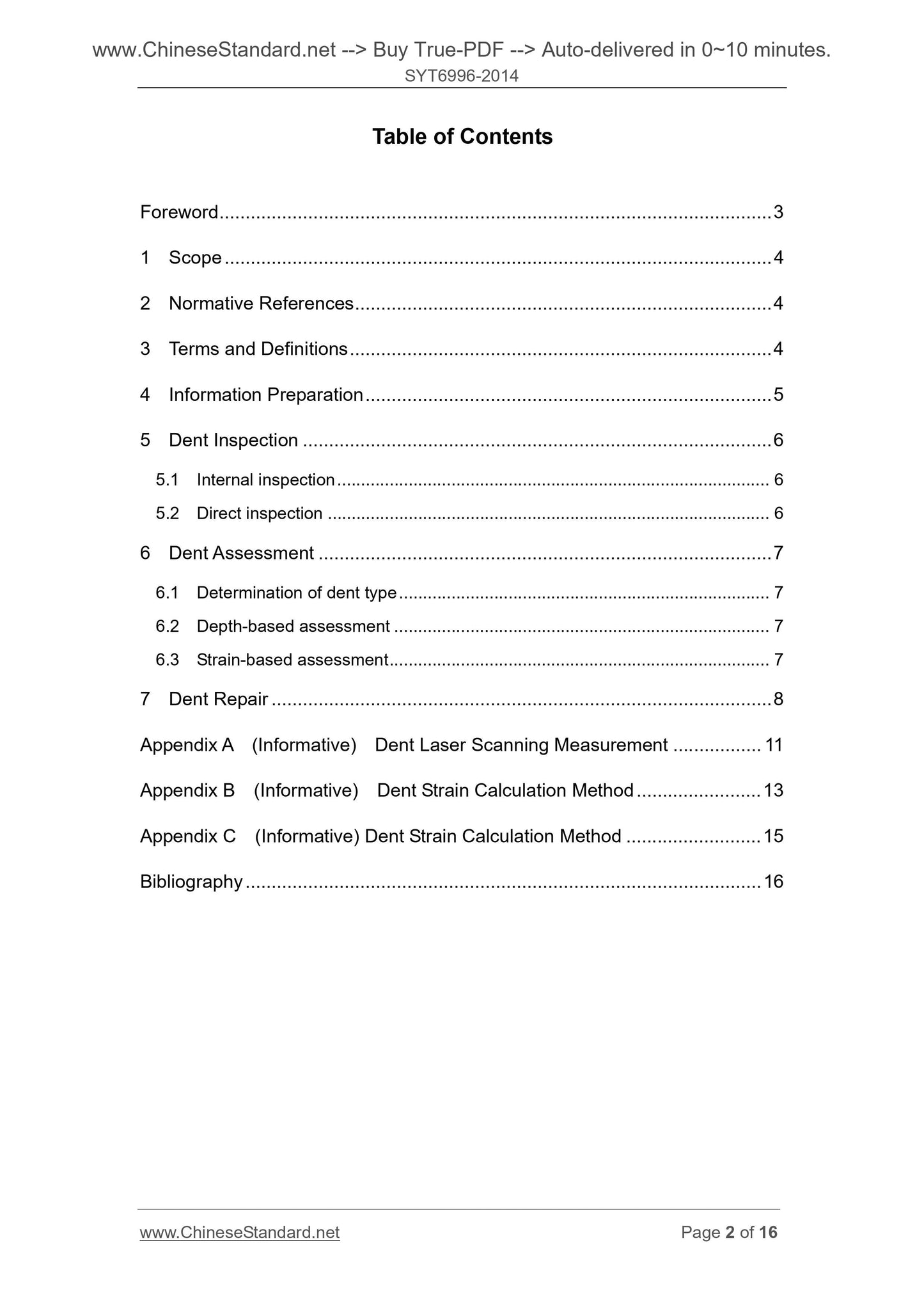
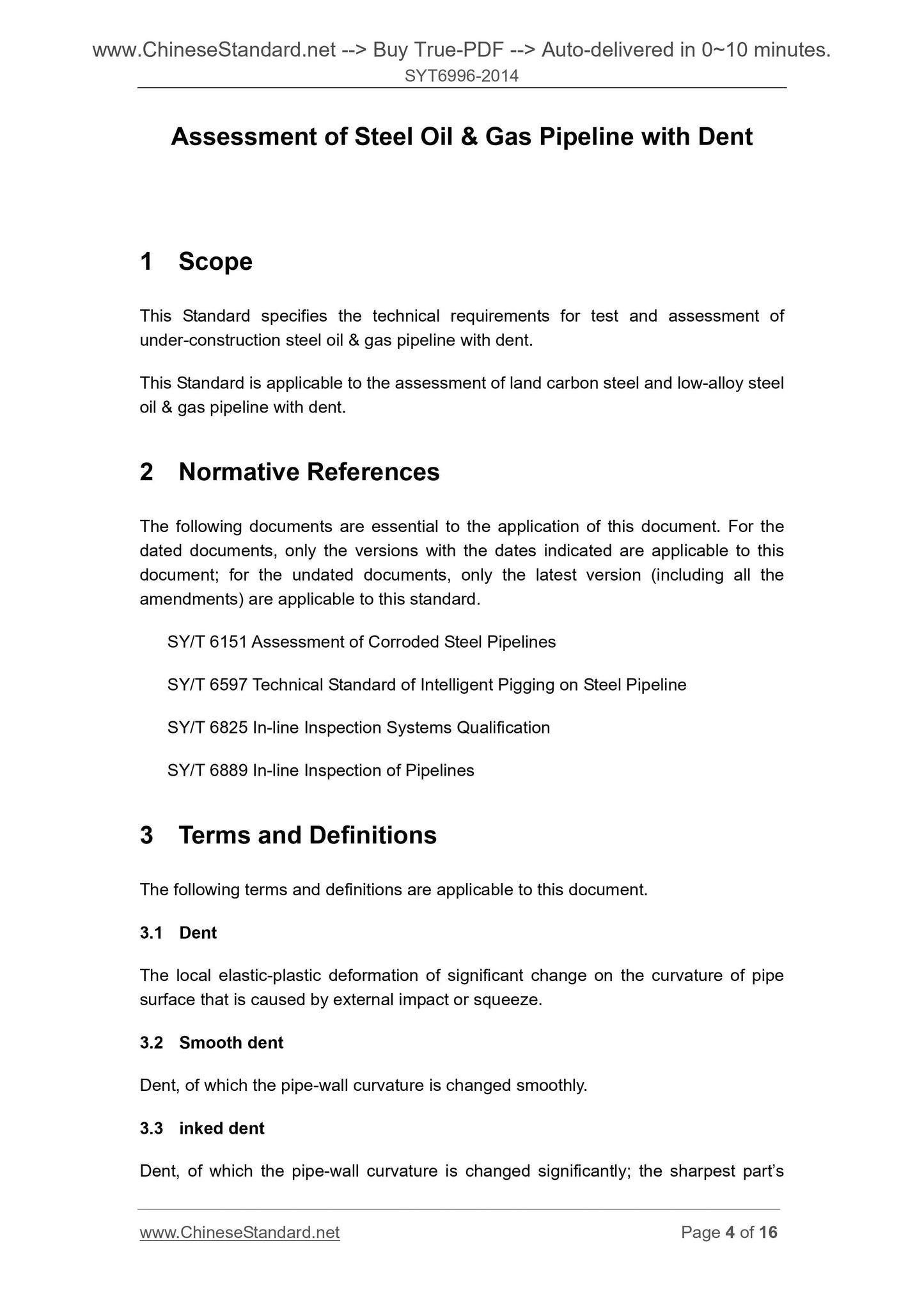
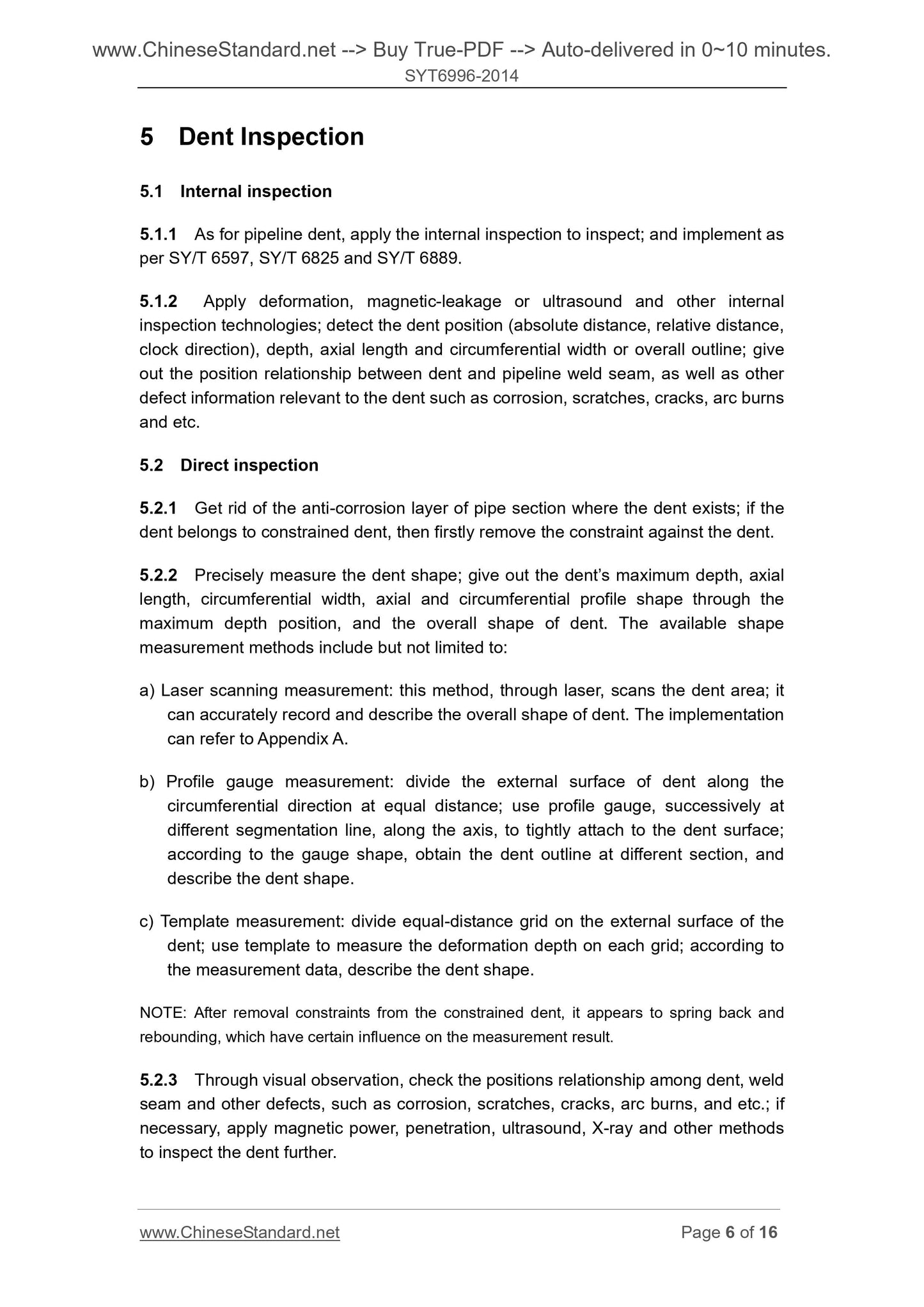
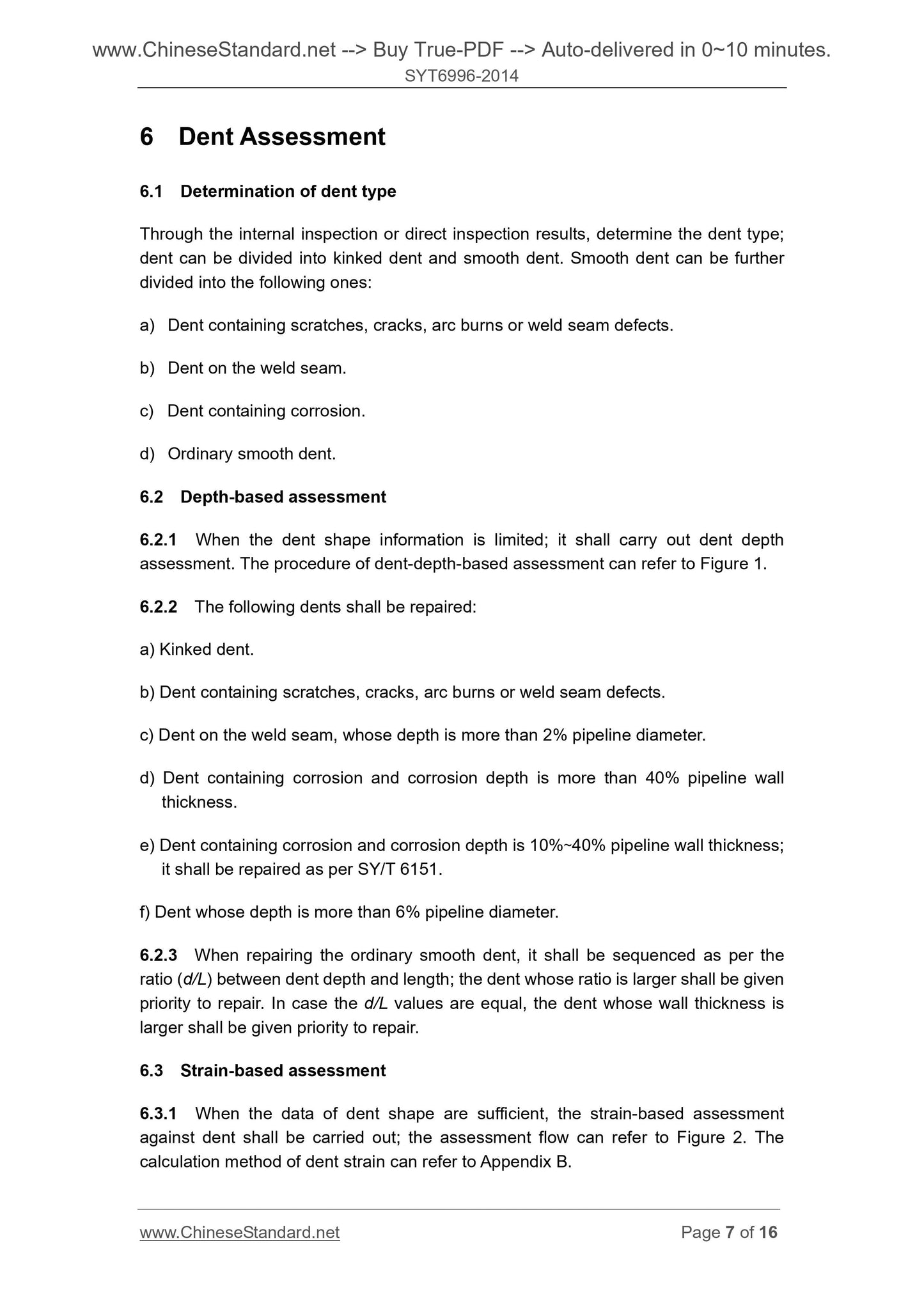
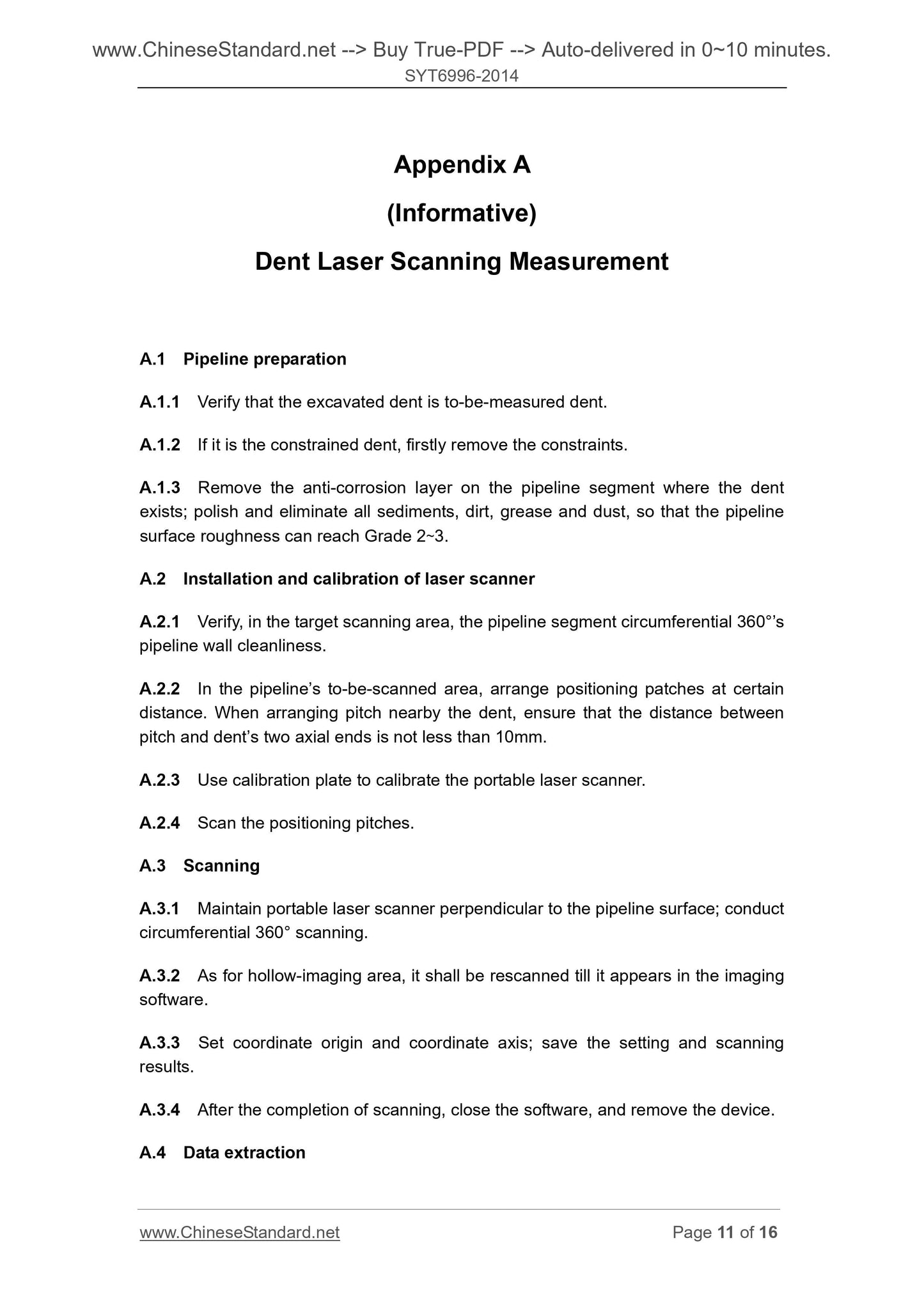
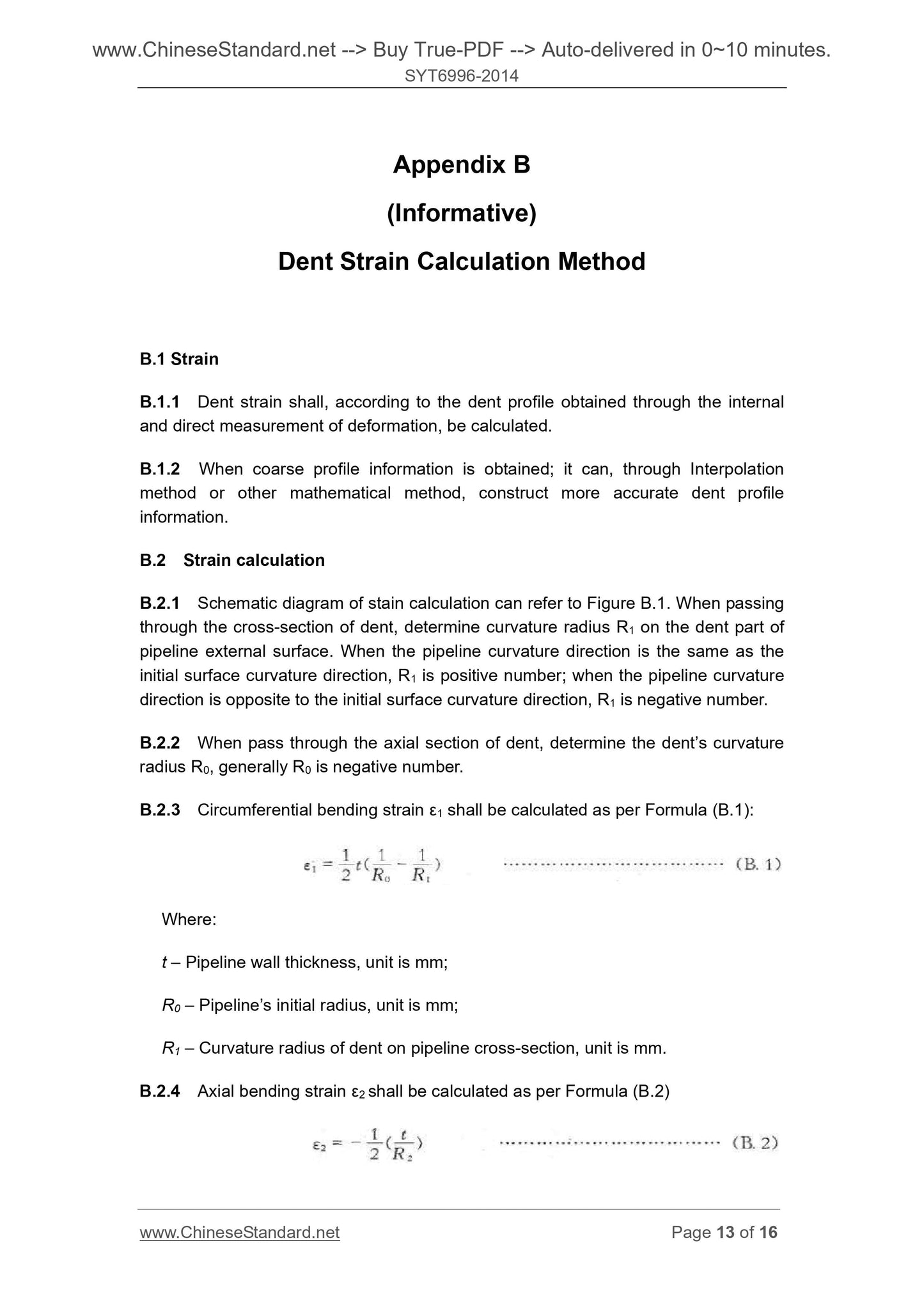