1
/
of
7
www.ChineseStandard.us -- Field Test Asia Pte. Ltd.
QC/T 661-2019 English PDF (QC/T661-2019)
QC/T 661-2019 English PDF (QC/T661-2019)
Regular price
$265.00
Regular price
Sale price
$265.00
Unit price
/
per
Shipping calculated at checkout.
Couldn't load pickup availability
QC/T 661-2019: Vehicle air conditioner accumulator
Delivery: 9 seconds. Download (and Email) true-PDF + Invoice.Get Quotation: Click QC/T 661-2019 (Self-service in 1-minute)
Newer / historical versions: QC/T 661-2019
Preview True-PDF
Scope
This standard specifies the technical requirements, test methods, inspection rules,marking, packaging, transportation, storage of accumulators (hereinafter referred to as
accumulators) for automobile air conditioning systems.
This standard is applicable to accumulators for automobile air conditioners using HFC-
134a and HFO-1234yf as refrigerants. Those using other types of refrigerants may refer
to it.
Basic Data
Standard ID | QC/T 661-2019 (QC/T661-2019) |
Description (Translated English) | Vehicle air conditioner accumulator |
Sector / Industry | Automobile and Vehicle Industry Standard (Recommended) |
Classification of Chinese Standard | T26 |
Classification of International Standard | 43.040.60 |
Word Count Estimation | 17,160 |
Date of Issue | 2019 |
Date of Implementation | 2020-04-01 |
Issuing agency(ies) | Ministry of Industry and Information Technology |
Summary | This standard specifies test methods for automotive air-conditioning compressors. This standard is applicable to various types of pulley-driven automotive air-conditioning compressors using HFC-134a/HFO-1234yf refrigerants, and other environmentally friendly refrigerants can be implemented by reference. |
Share
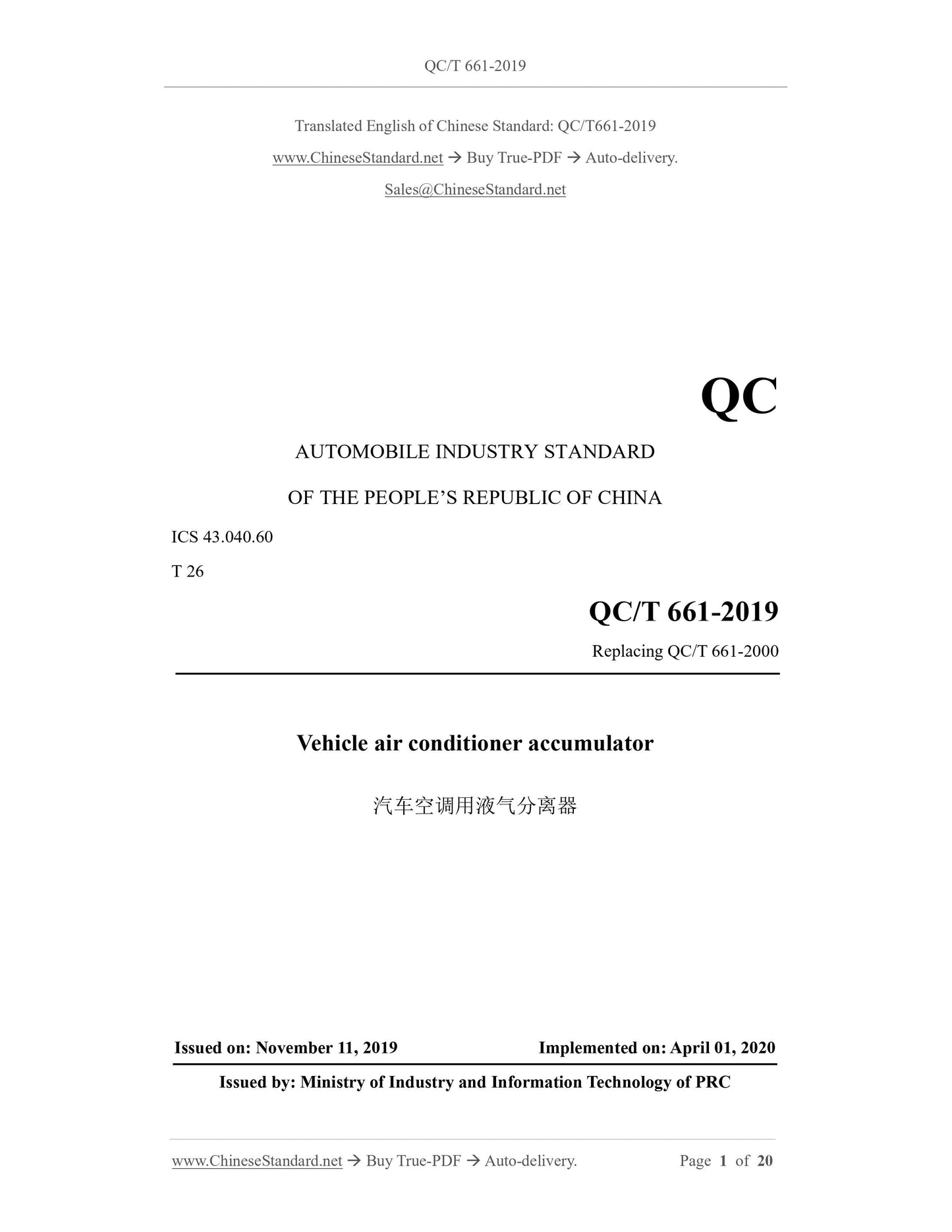
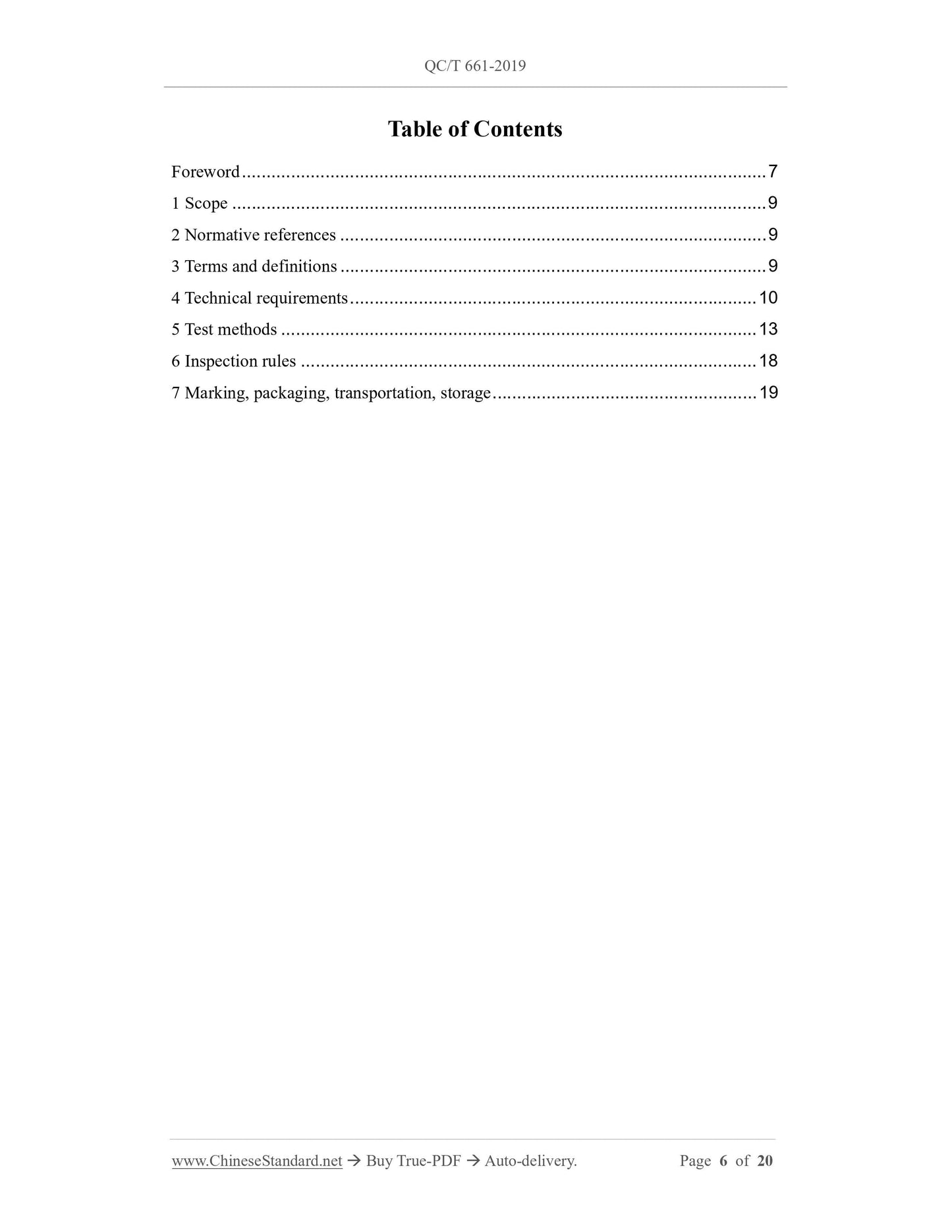
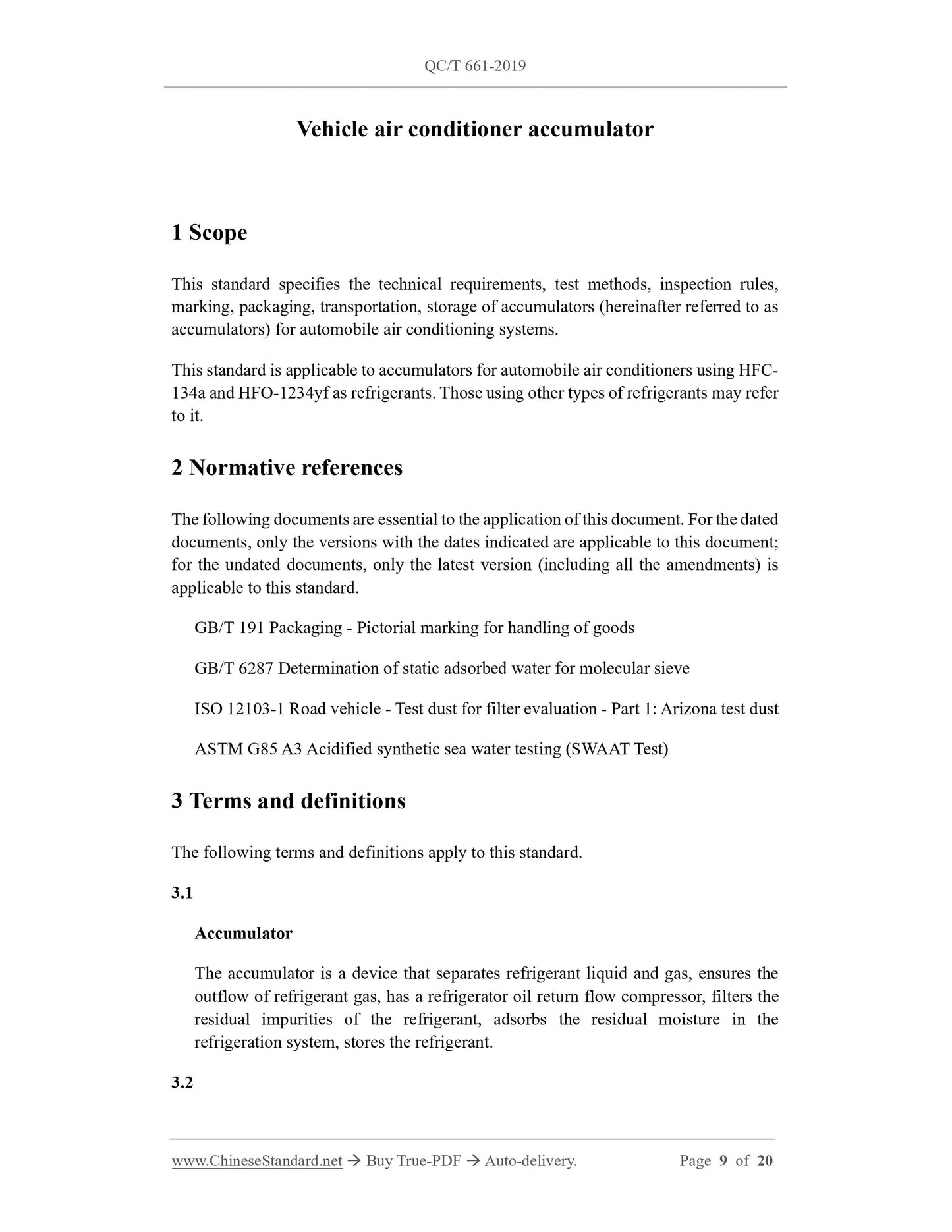
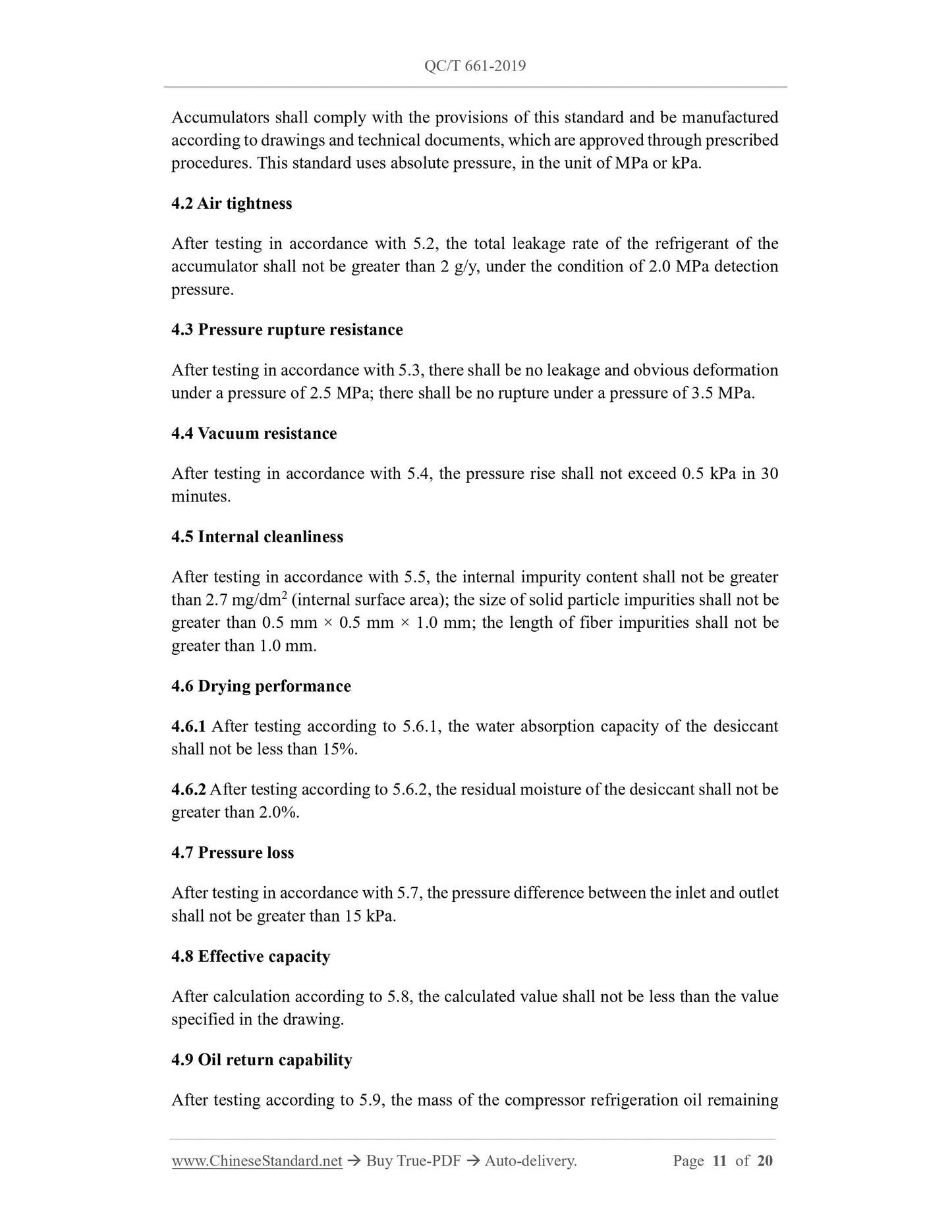
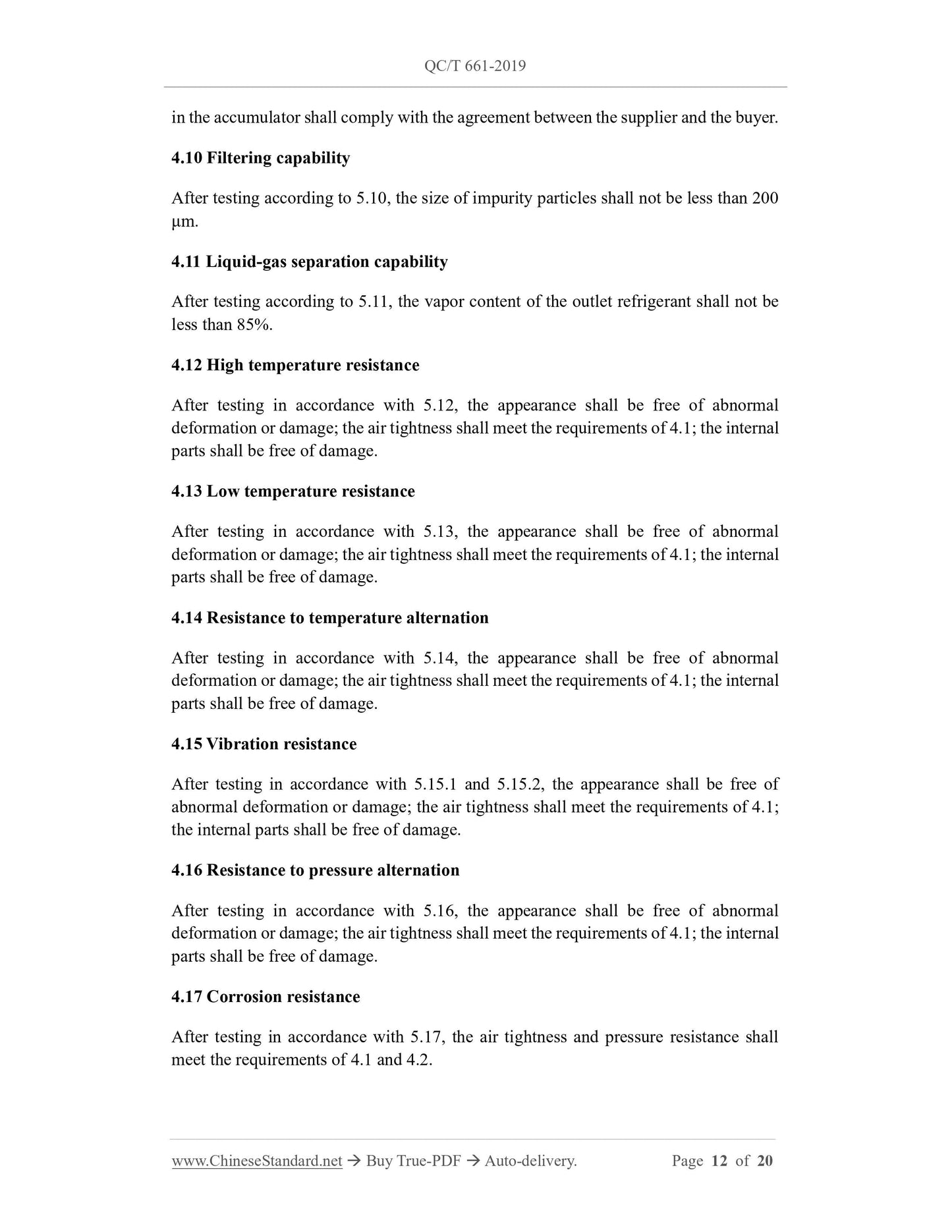
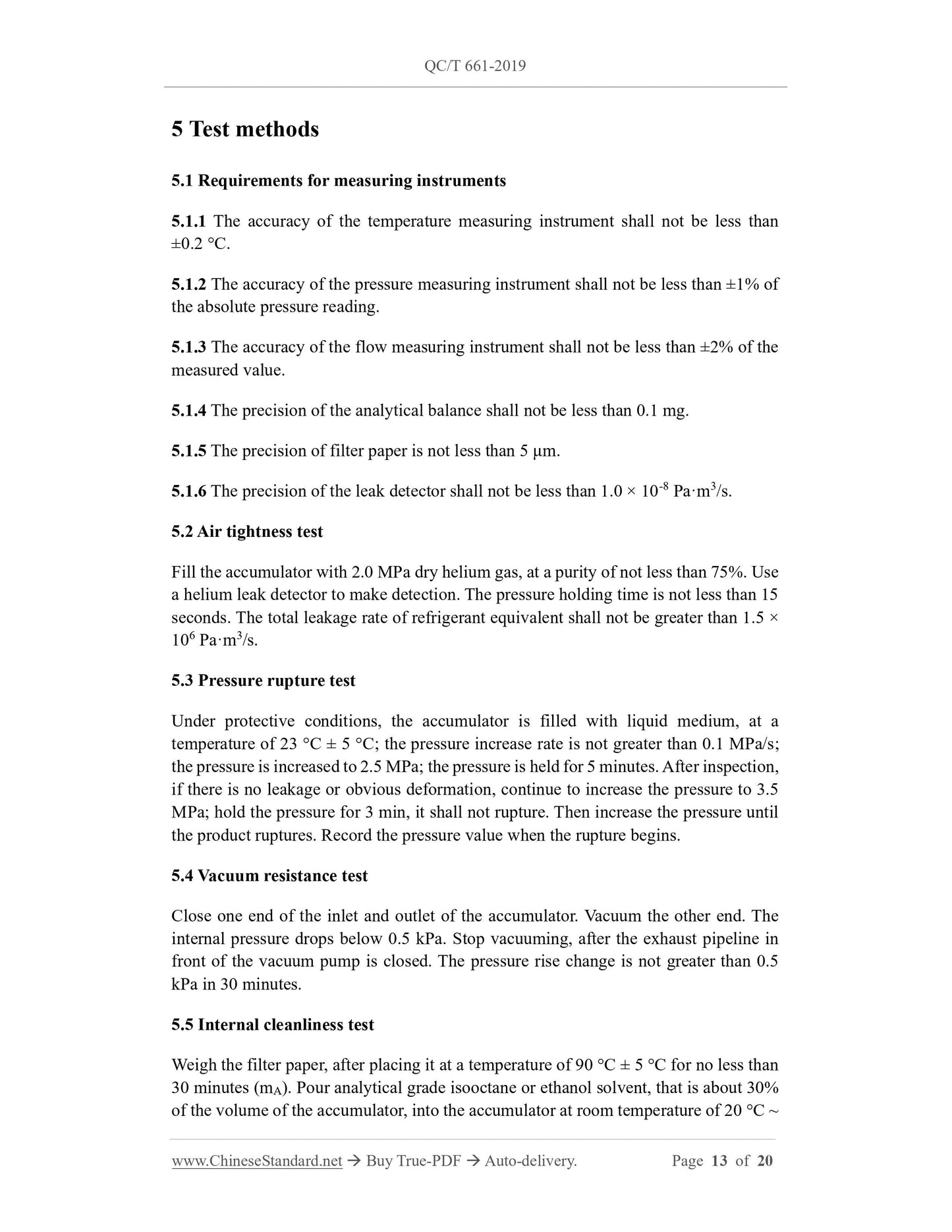
