1
/
of
9
www.ChineseStandard.us -- Field Test Asia Pte. Ltd.
JG/T 157-2009 English PDF (JG/T157-2009)
JG/T 157-2009 English PDF (JG/T157-2009)
Regular price
$150.00
Regular price
Sale price
$150.00
Unit price
/
per
Shipping calculated at checkout.
Couldn't load pickup availability
JG/T 157-2009: Putty for exterior wall
Delivery: 9 seconds. Download (and Email) true-PDF + Invoice.
Get Quotation: Click JG/T 157-2009 (Self-service in 1-minute)
Newer / historical versions: JG/T 157-2009
Preview True-PDF (Reload/Scroll-down if blank)
Delivery: 9 seconds. Download (and Email) true-PDF + Invoice.
Get Quotation: Click JG/T 157-2009 (Self-service in 1-minute)
Newer / historical versions: JG/T 157-2009
Preview True-PDF (Reload/Scroll-down if blank)
Share
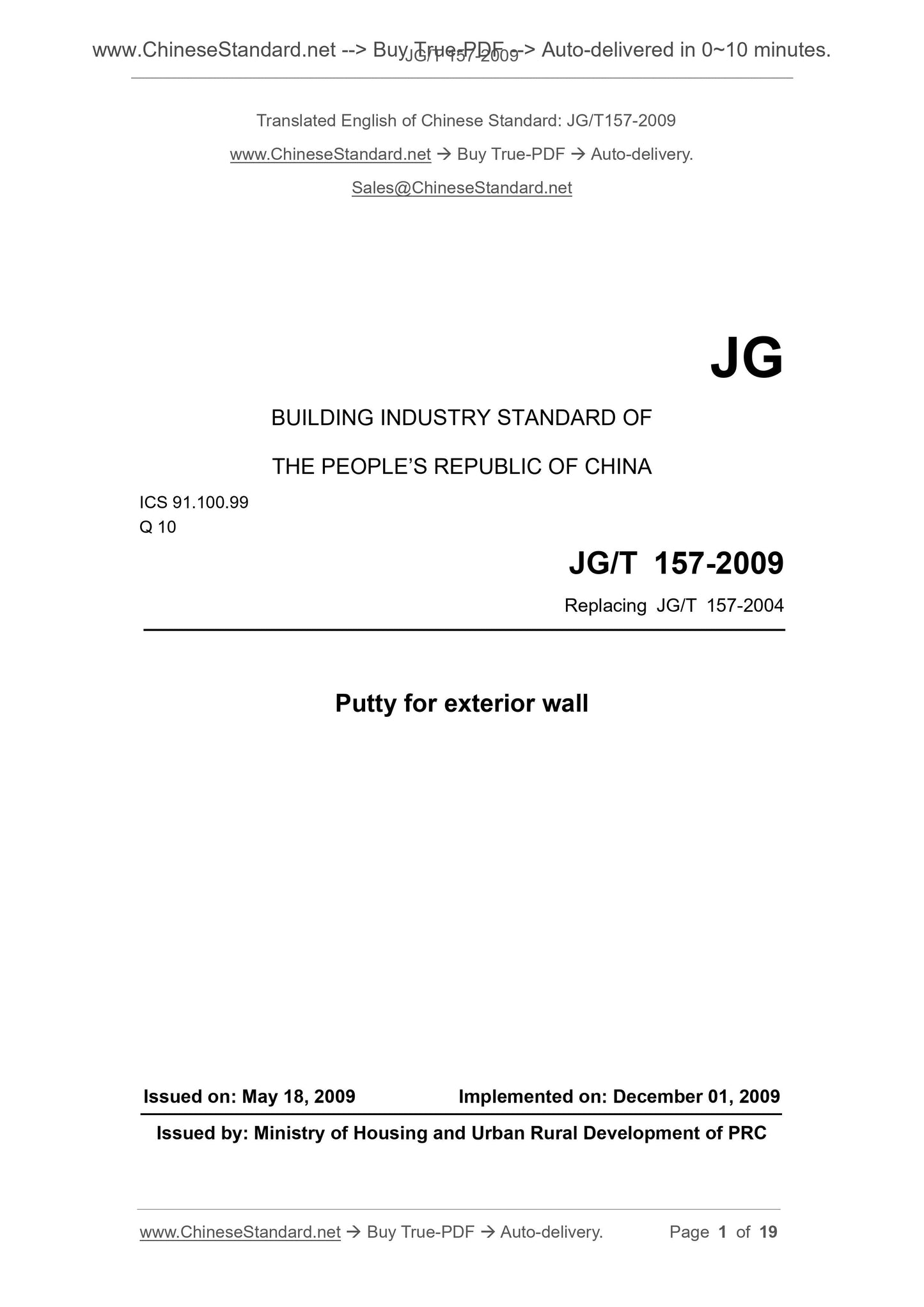
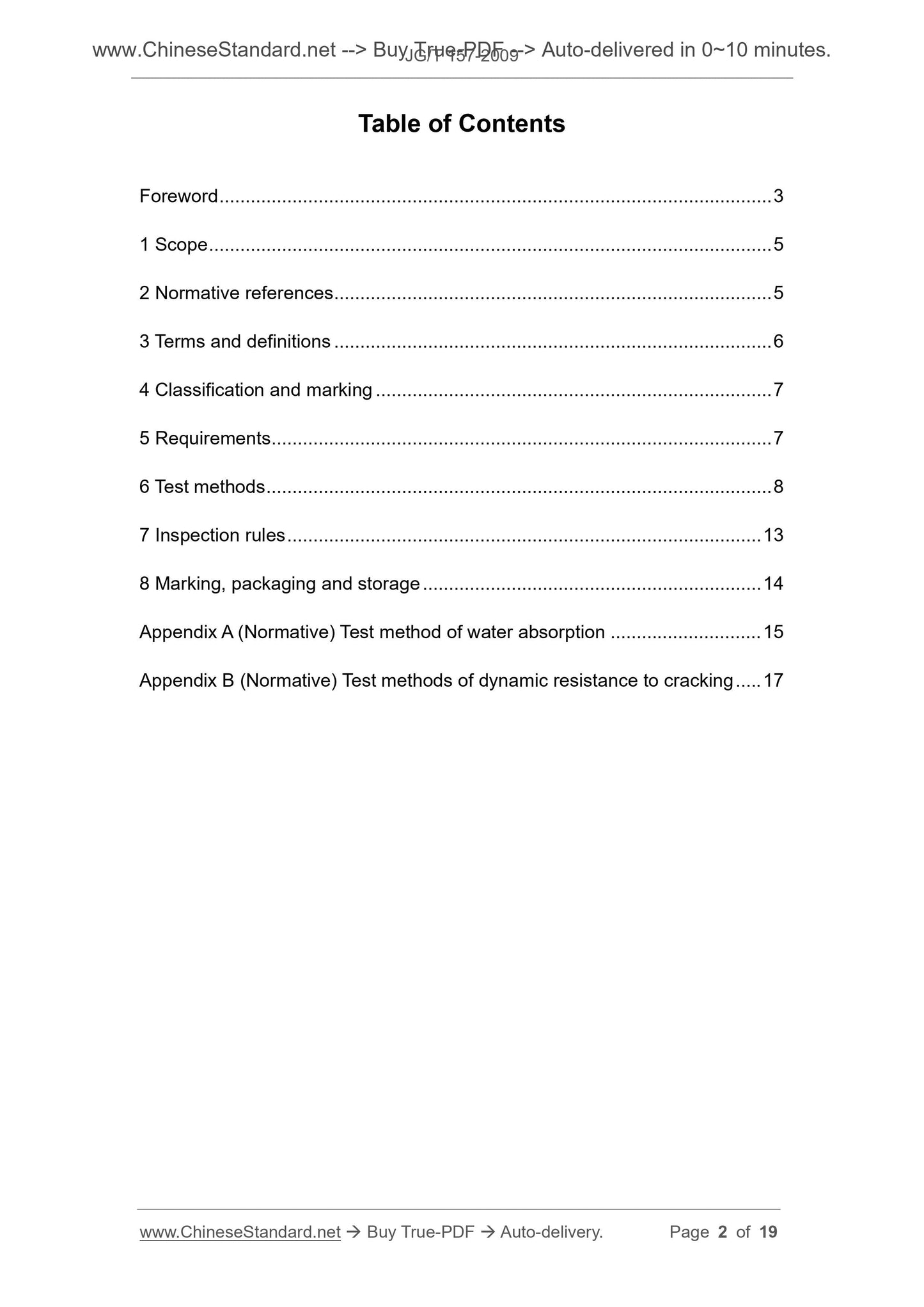
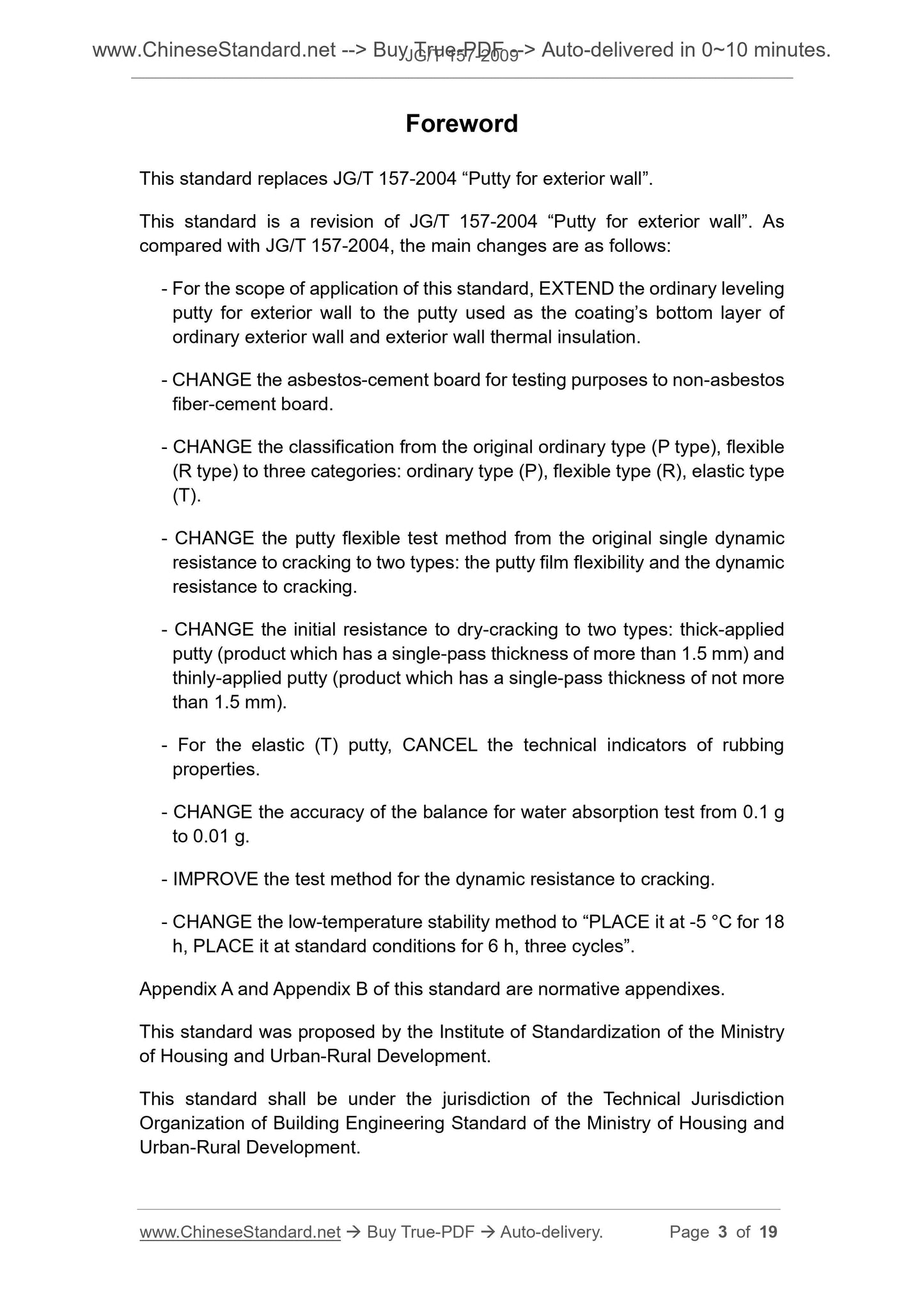
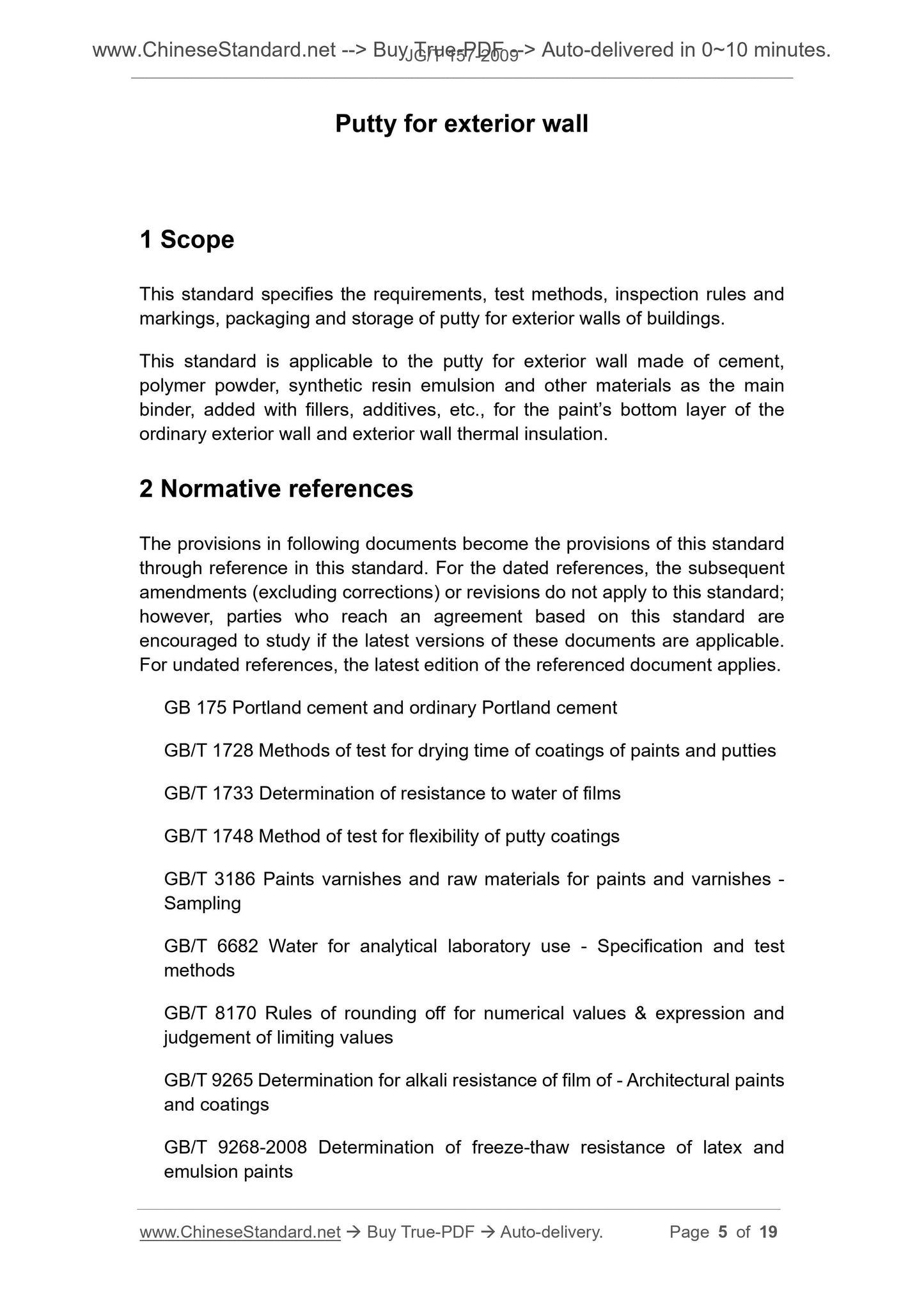
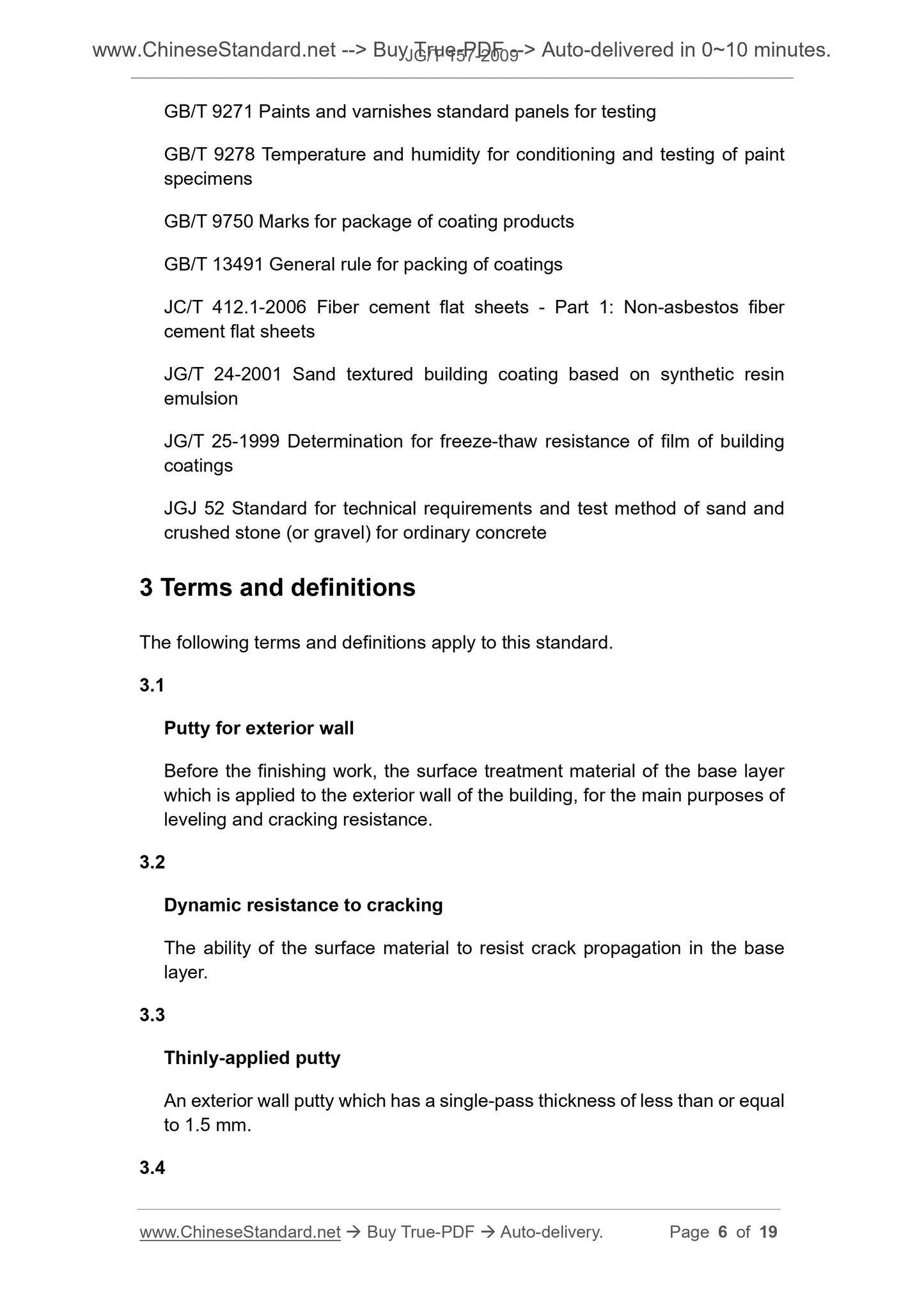
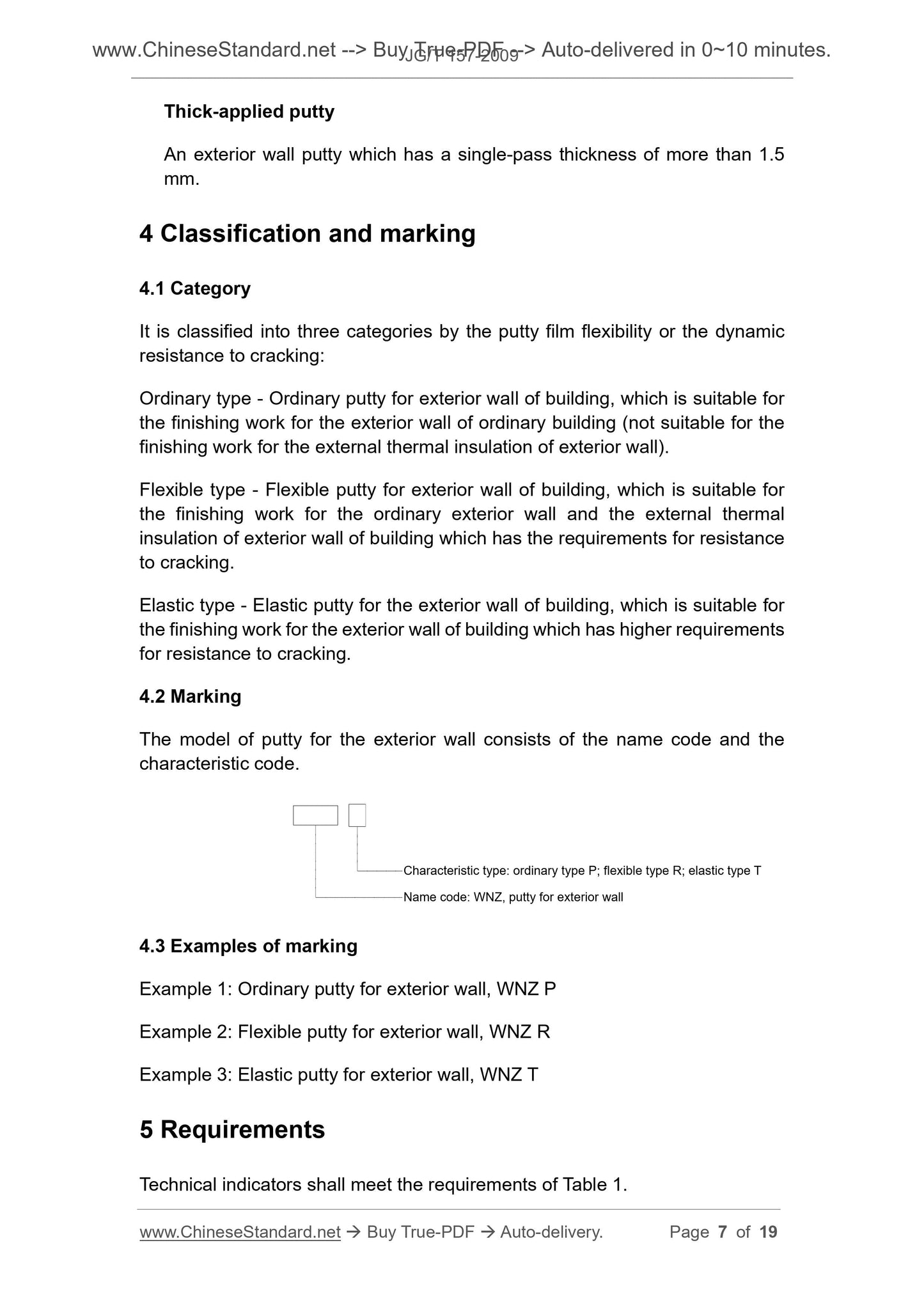
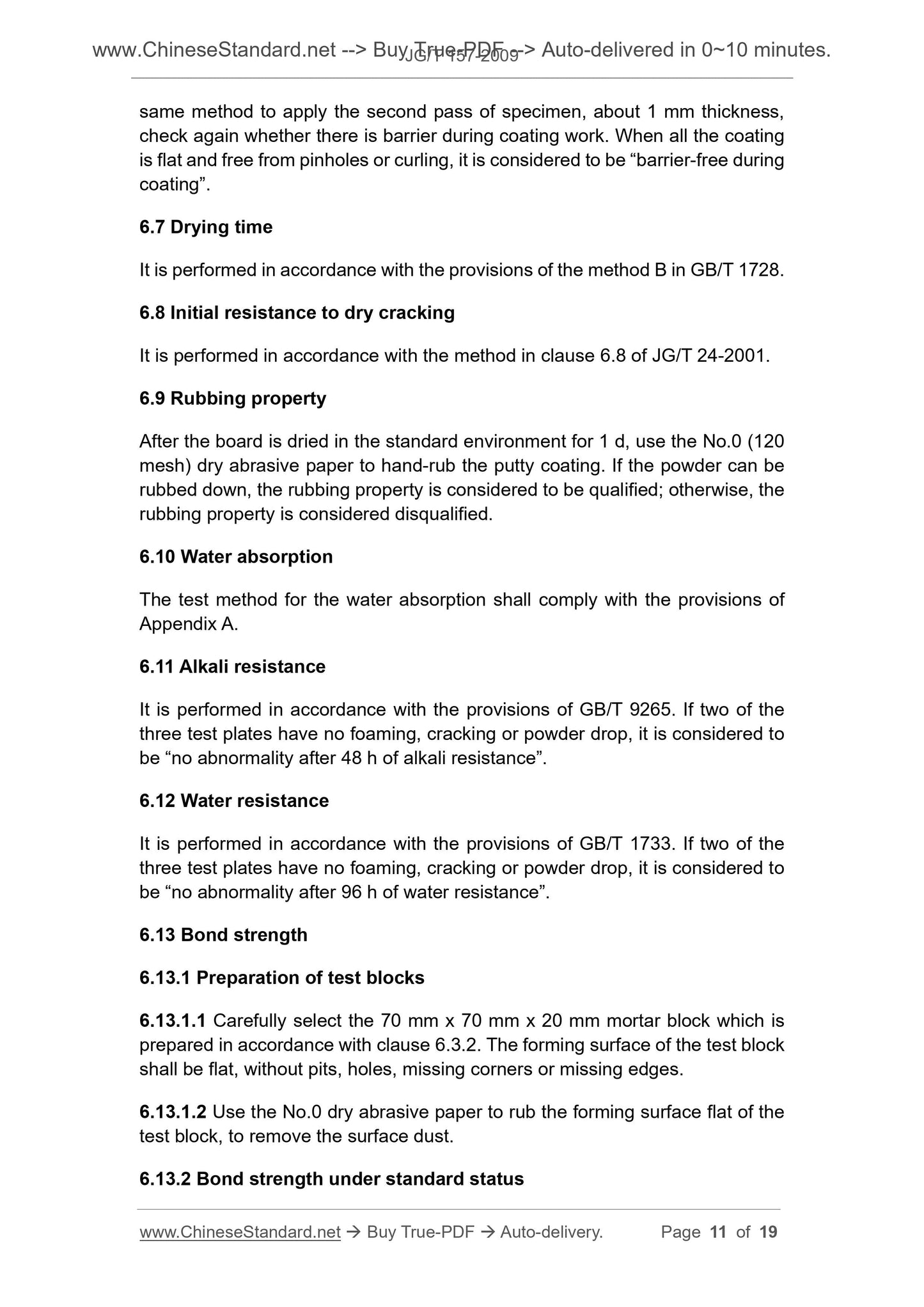
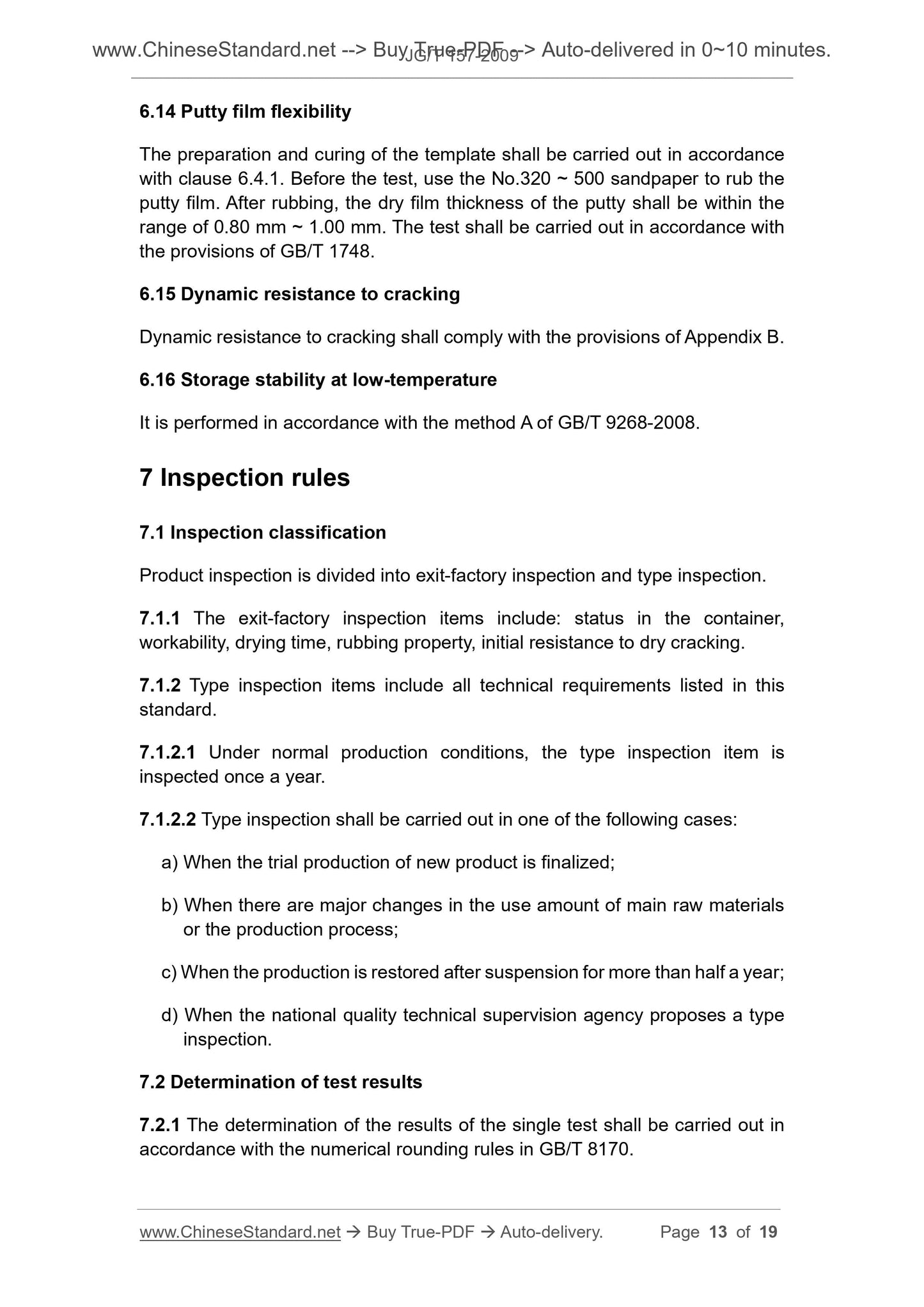
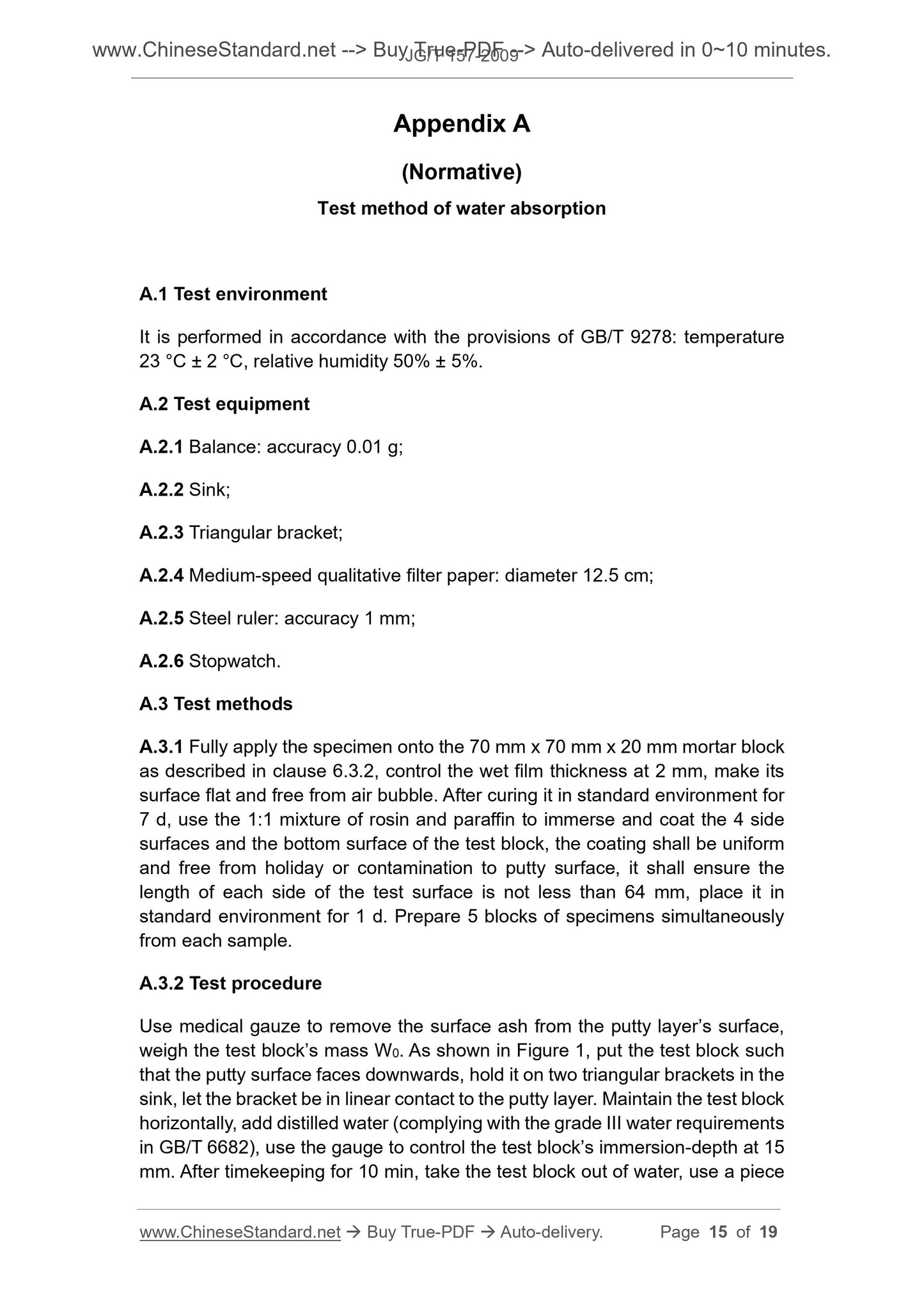