1
/
of
12
www.ChineseStandard.us -- Field Test Asia Pte. Ltd.
JGJ 52-2006 English PDF
JGJ 52-2006 English PDF
Regular price
$555.00
Regular price
Sale price
$555.00
Unit price
/
per
Shipping calculated at checkout.
Couldn't load pickup availability
JGJ 52-2006: Standard for technical requirements and test method of sand and crushed stone (or gravel) for ordinary concrete
Delivery: 9 seconds. Download (and Email) true-PDF + Invoice.Get Quotation: Click JGJ 52-2006 (Self-service in 1-minute)
Newer / historical versions: JGJ 52-2006
Preview True-PDF
Scope
1.0.1 This Standard is established to utilize nature sand, artificial sand, crushed stoneand gravel reasonably in ordinary concrete, so that quality of sand and stone for
ordinary concrete can be ensured.
1.0.2 This Standard is applicable to quality requirements and test of sand and stone
for ordinary concrete used in general industrial and civil buildings and structures.
1.0.3 For sand and stone used for important concrete structure in long-term
moisture environment, alkali activity test shall be required.
1.0.4 For quality requirements and test of sand and stone, besides this Standard,
specification in current national related standard shall be followed.
Basic Data
Standard ID | JGJ 52-2006 (JGJ52-2006) |
Description (Translated English) | Standard for technical requirements and test method of sand and crushed stone (or gravel) for ordinary concrete |
Sector / Industry | Building and Construction Industry Standard |
Classification of Chinese Standard | Q13 |
Classification of International Standard | 91.100.15 |
Word Count Estimation | 60,660 |
Date of Issue | 2006-12-19 |
Date of Implementation | 2007-06-01 |
Older Standard (superseded by this standard) | JGJ 52-1992; JGJ 53-1992 |
Regulation (derived from) | ?Ministry of Construction Announcement 529 |
Issuing agency(ies) | Ministry of Construction of the People's Republic of China |
Summary | This standard applies to general industrial and civil buildings and structures in ordinary concrete sand and stone quality requirements and testing. |
Share
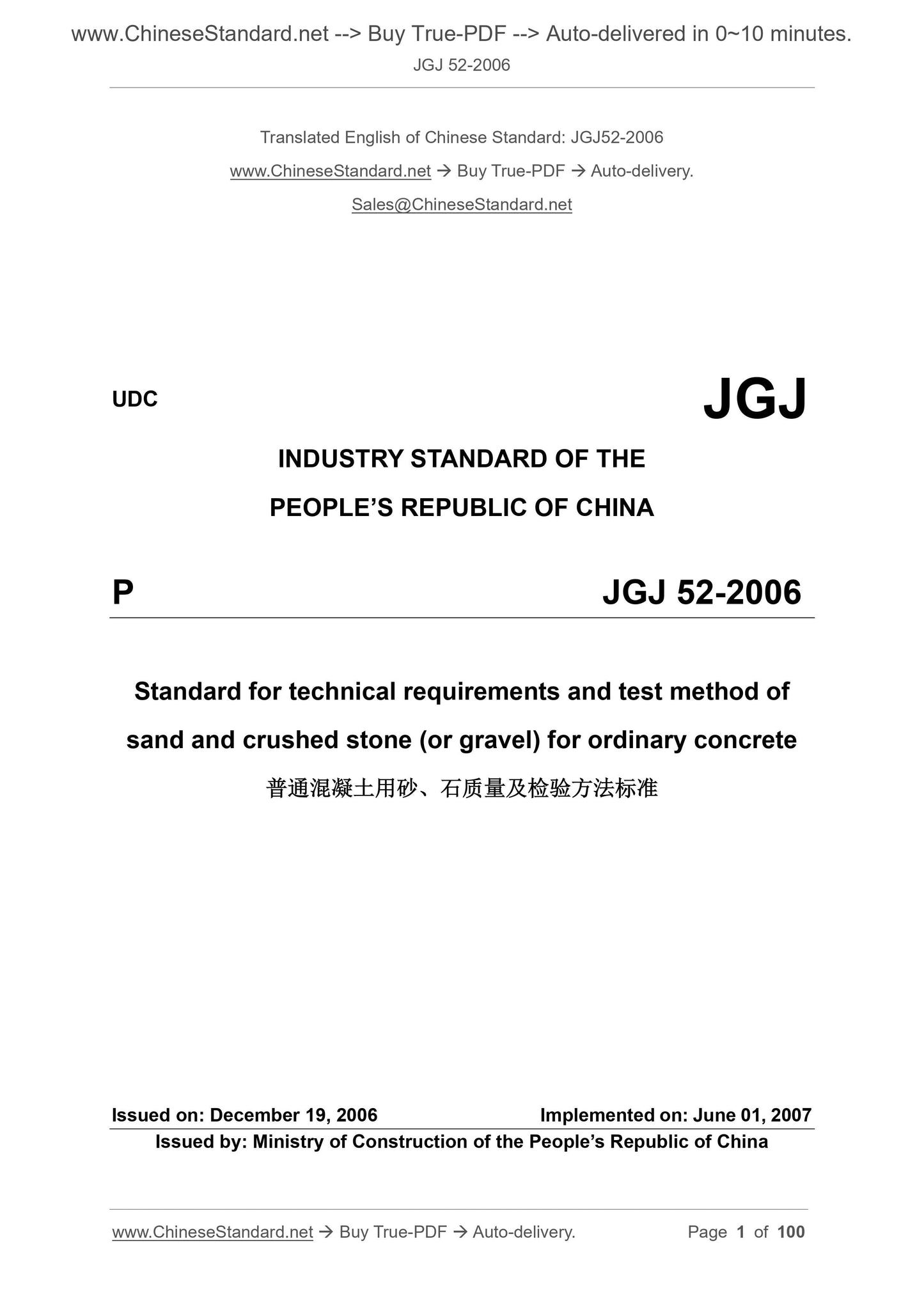
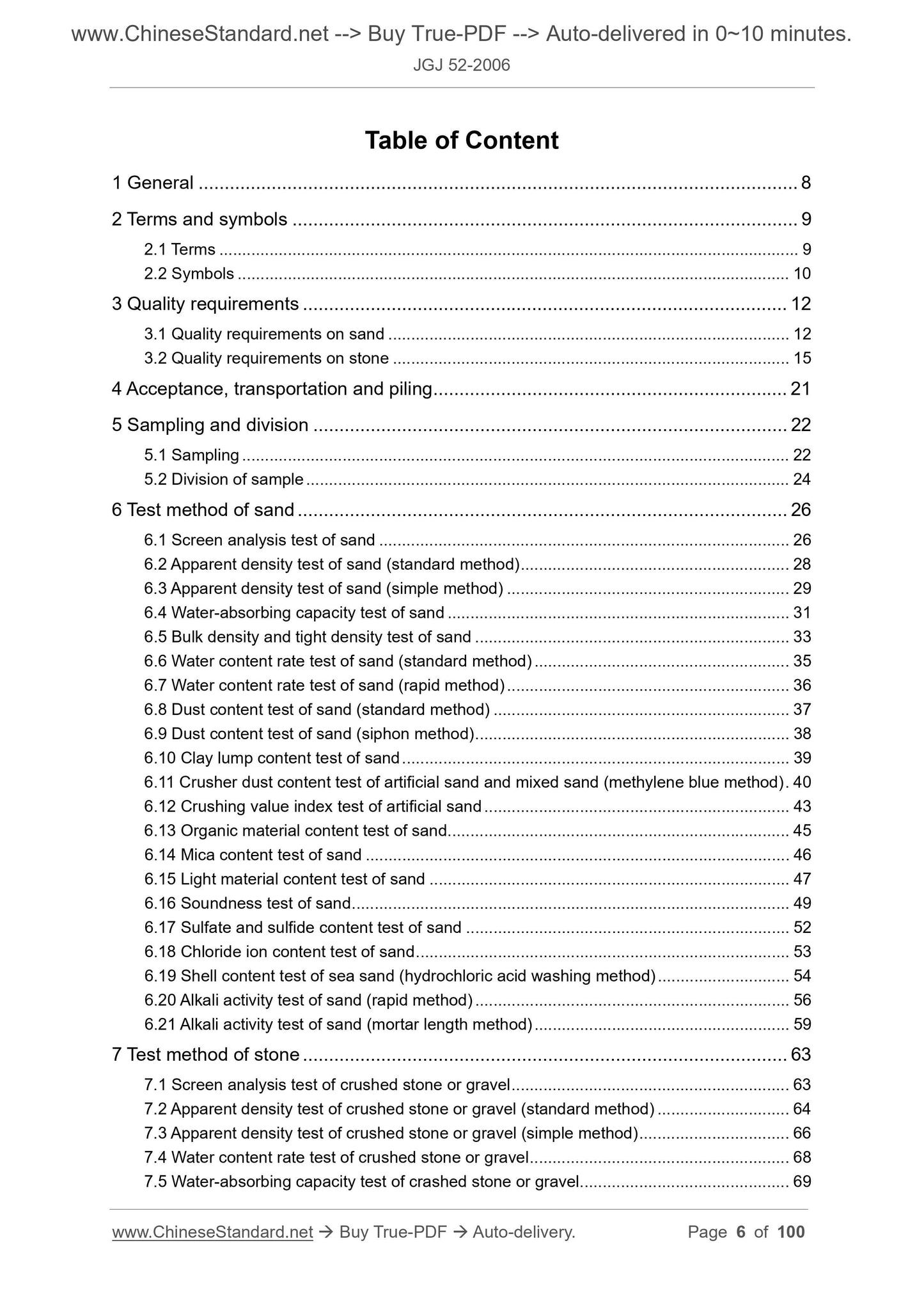
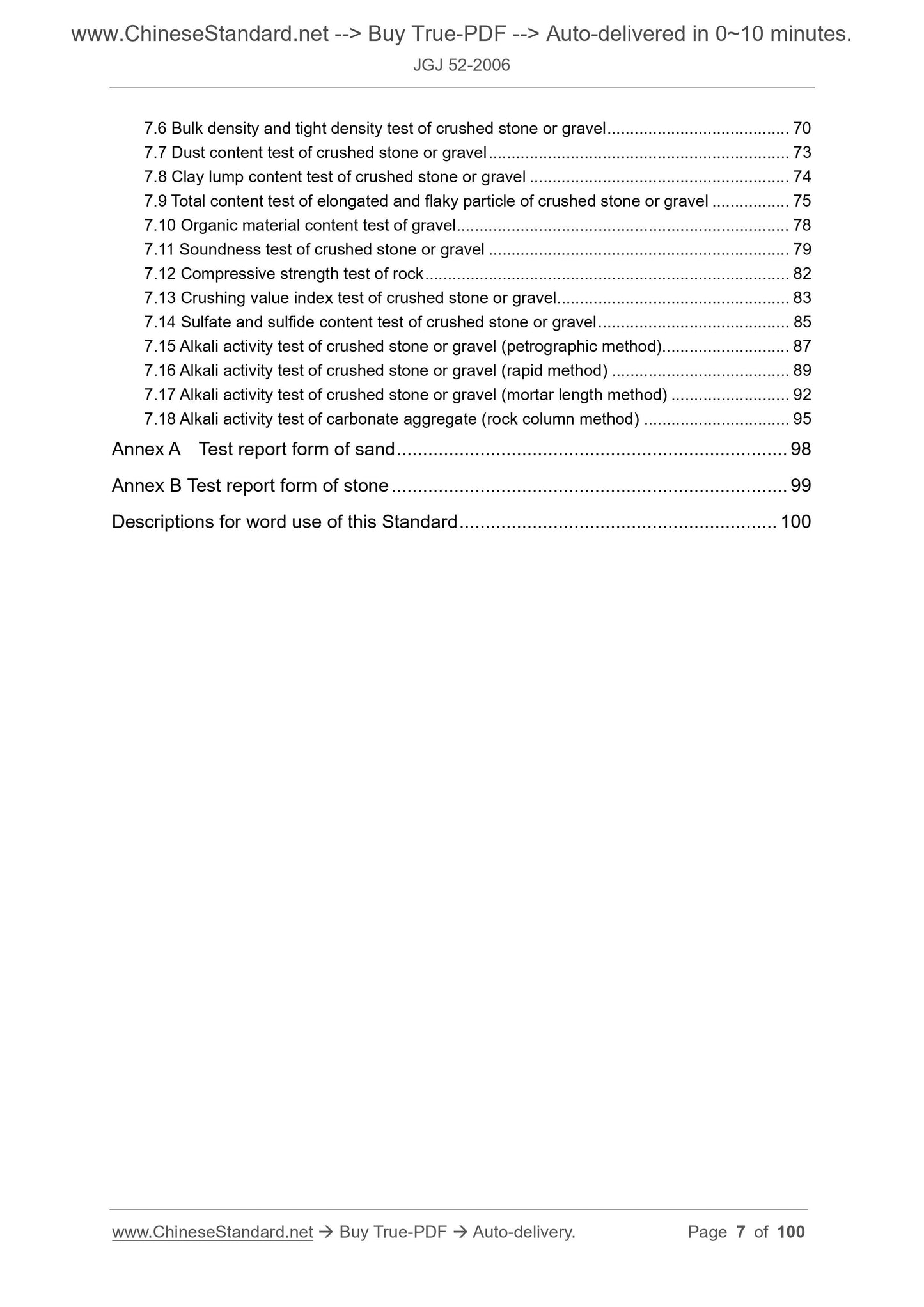
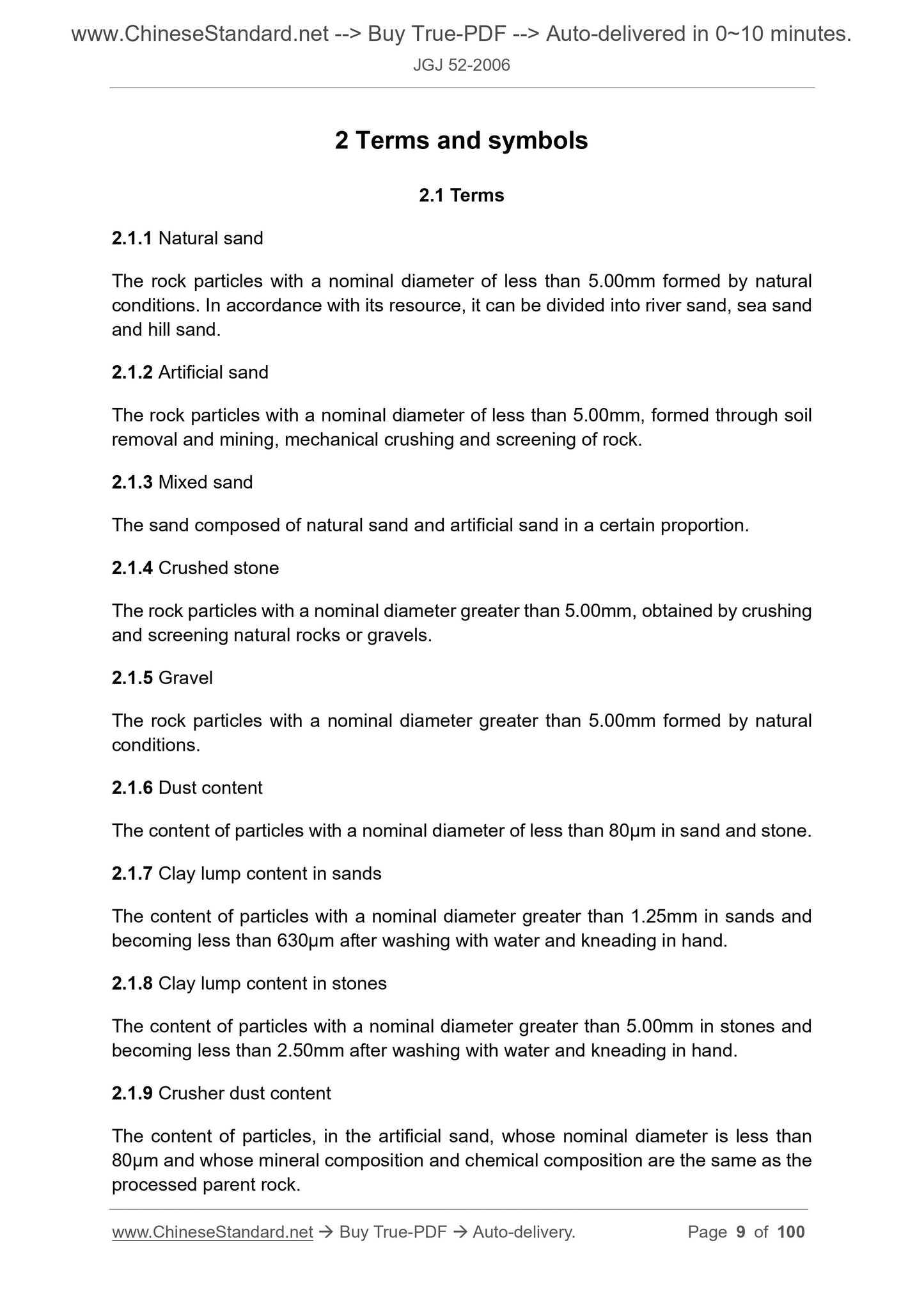
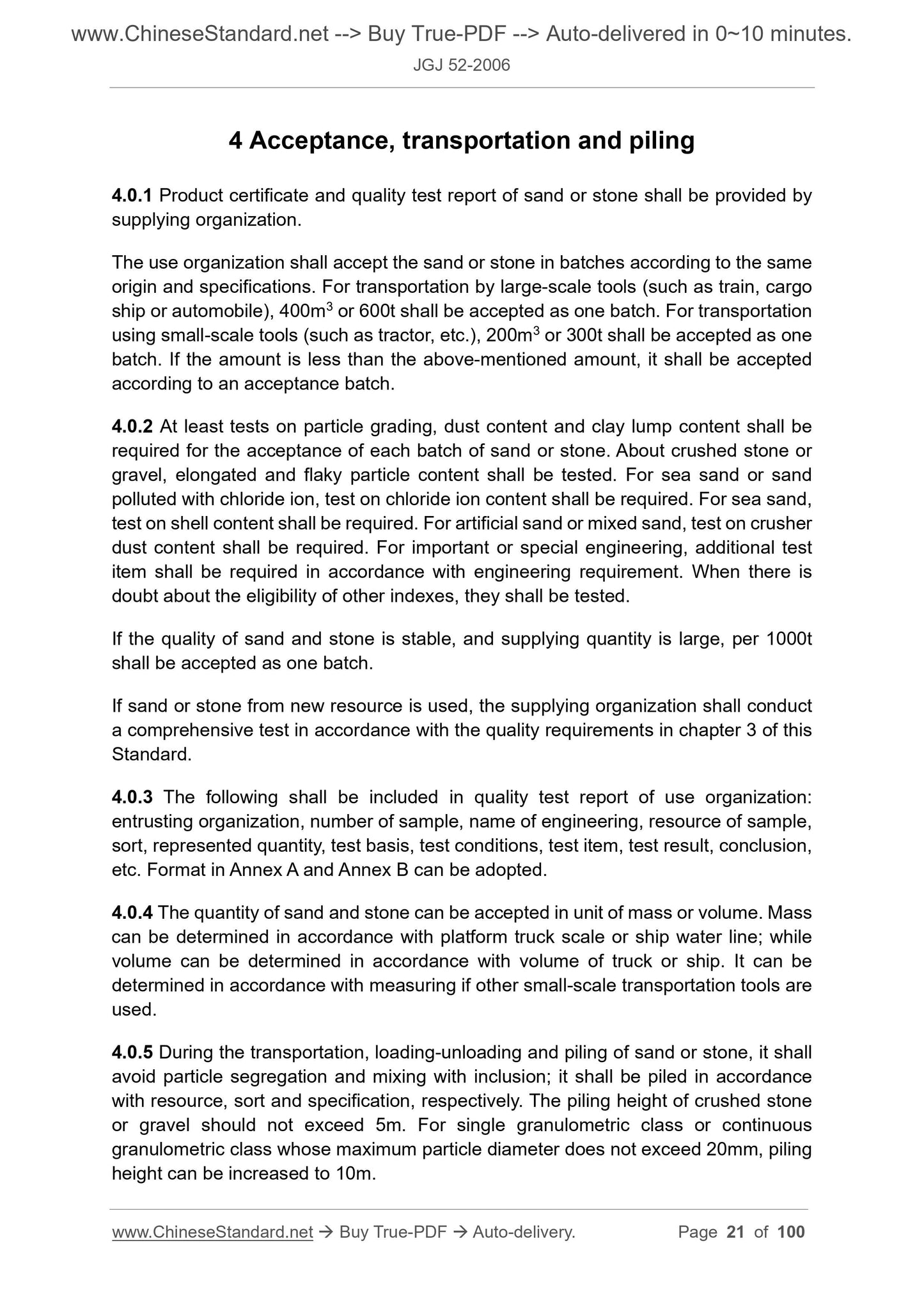
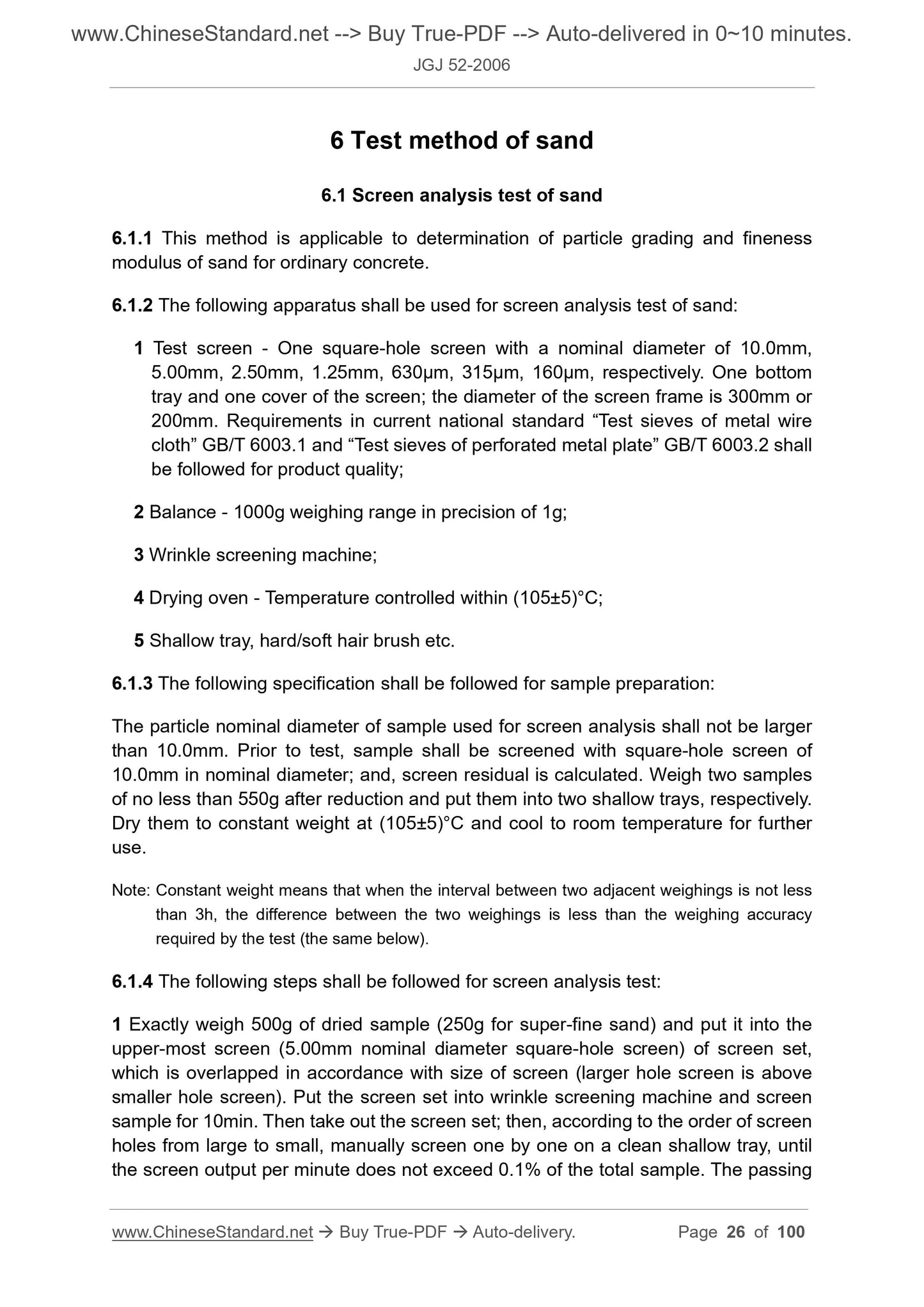
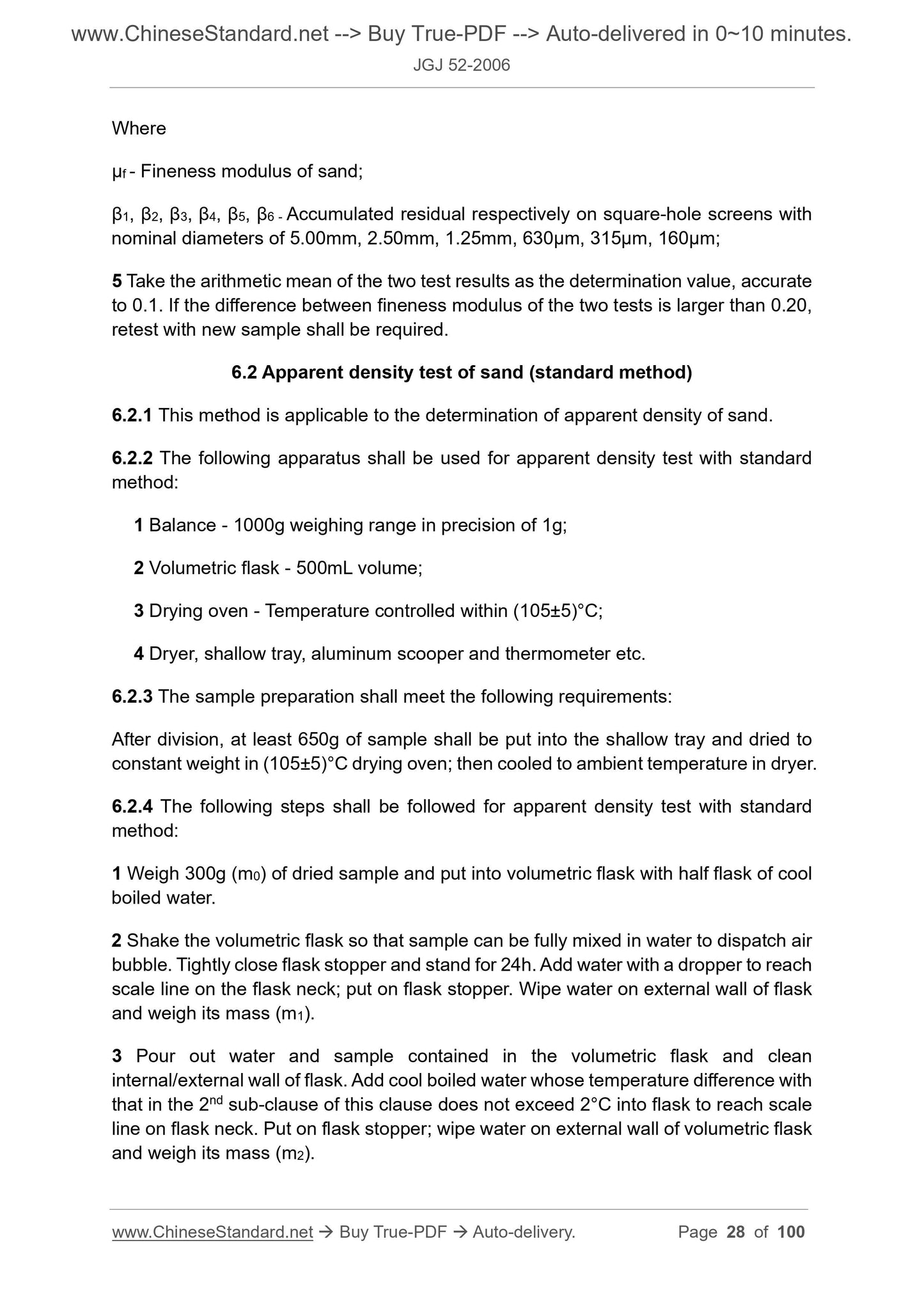
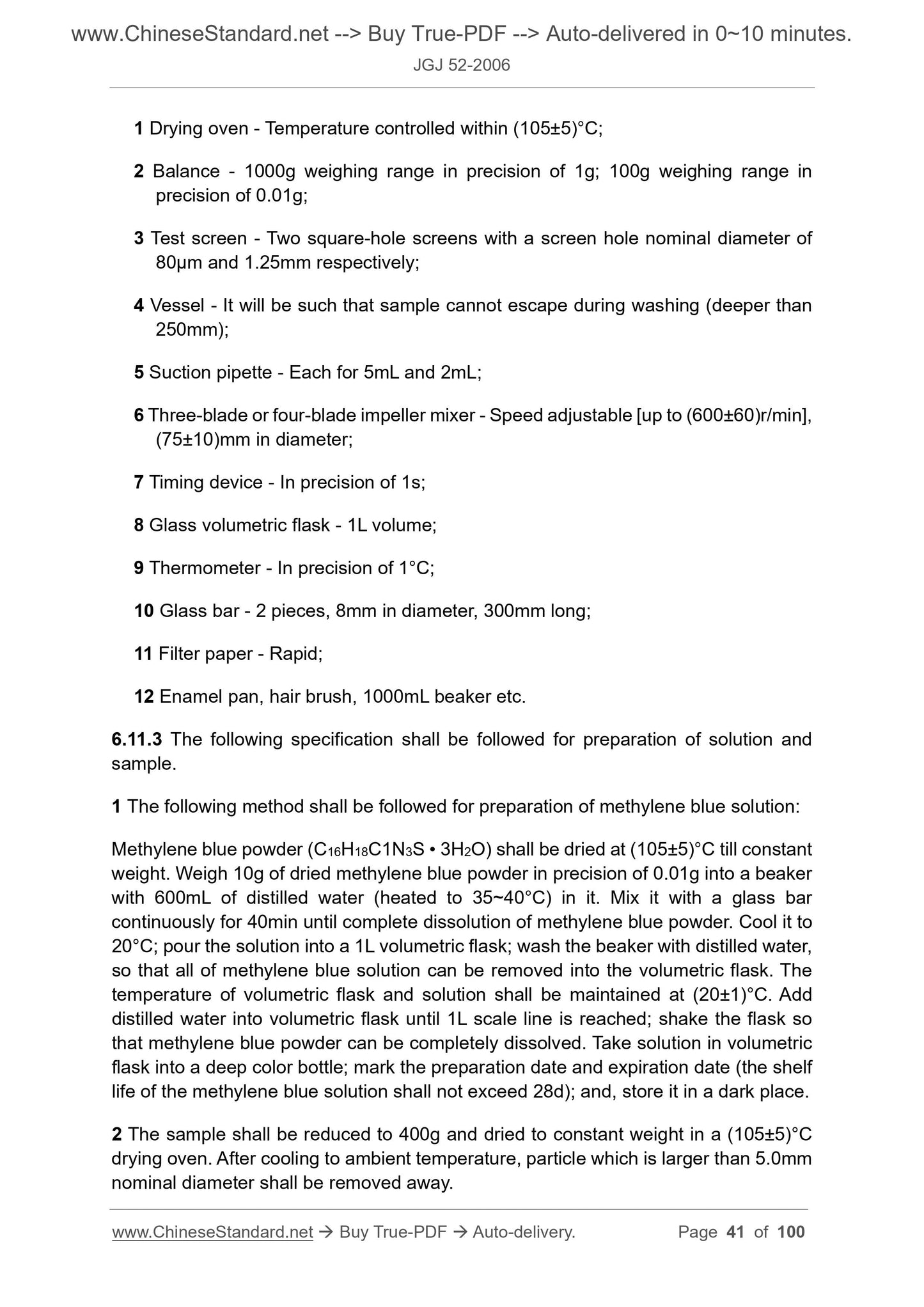
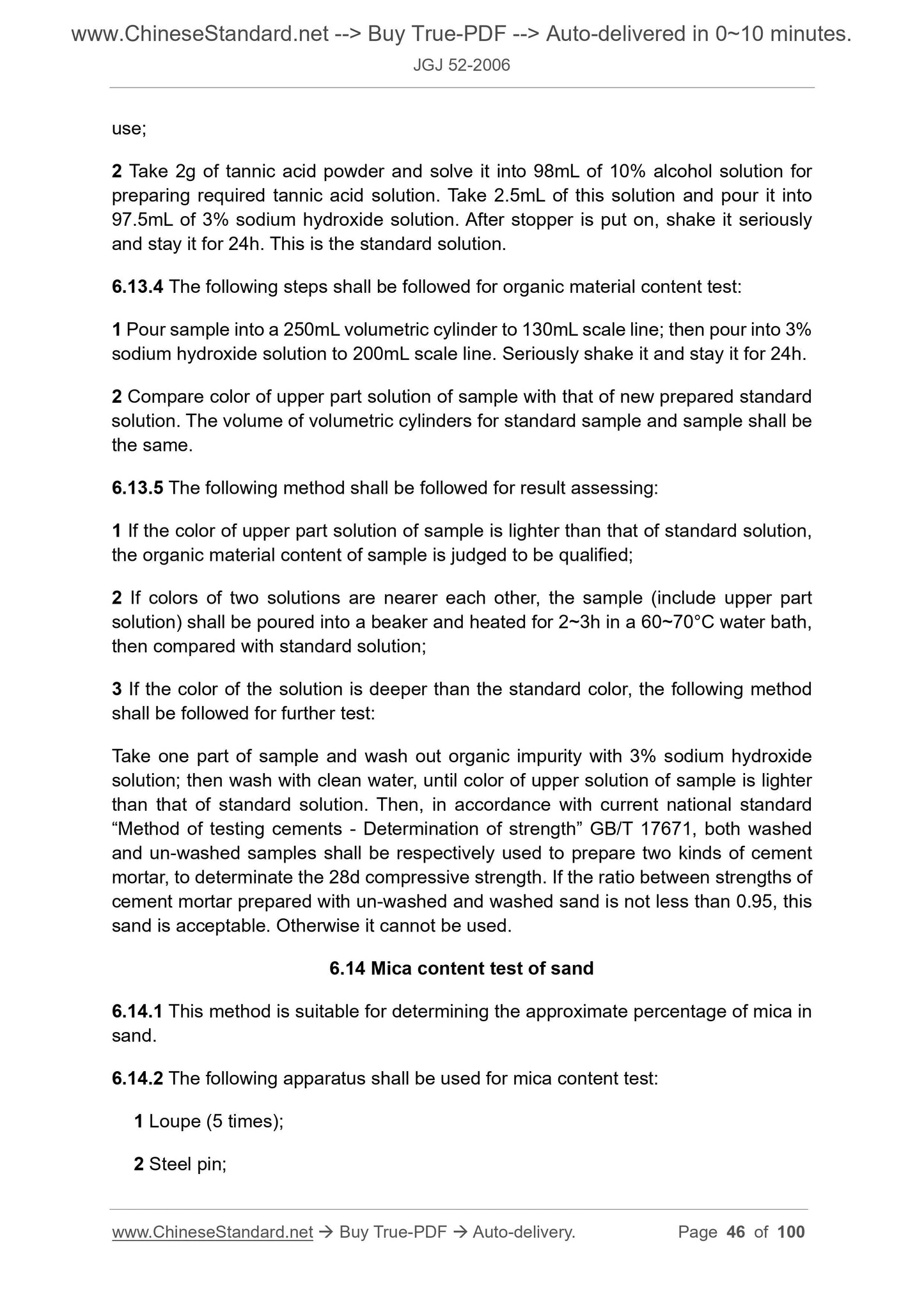
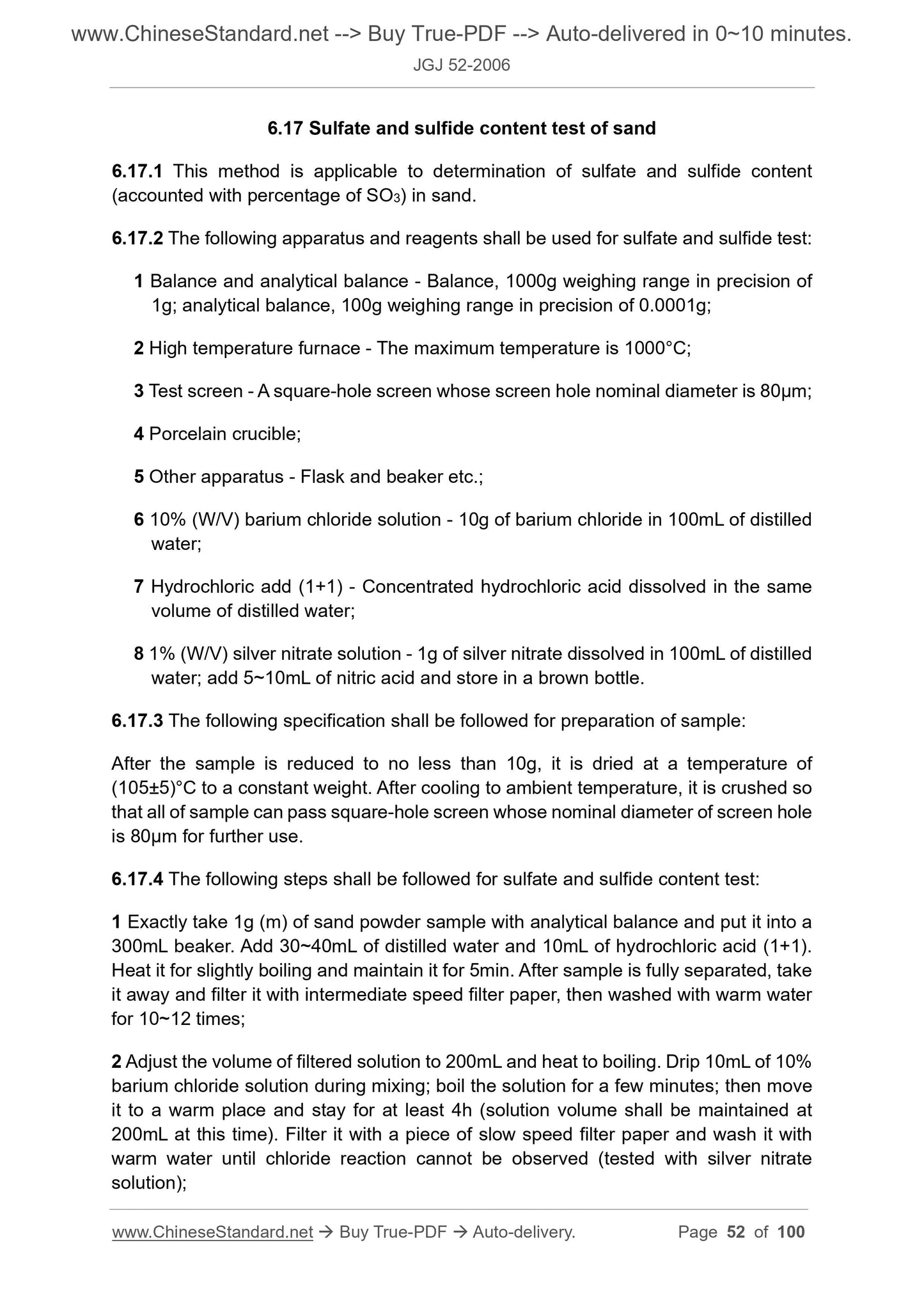
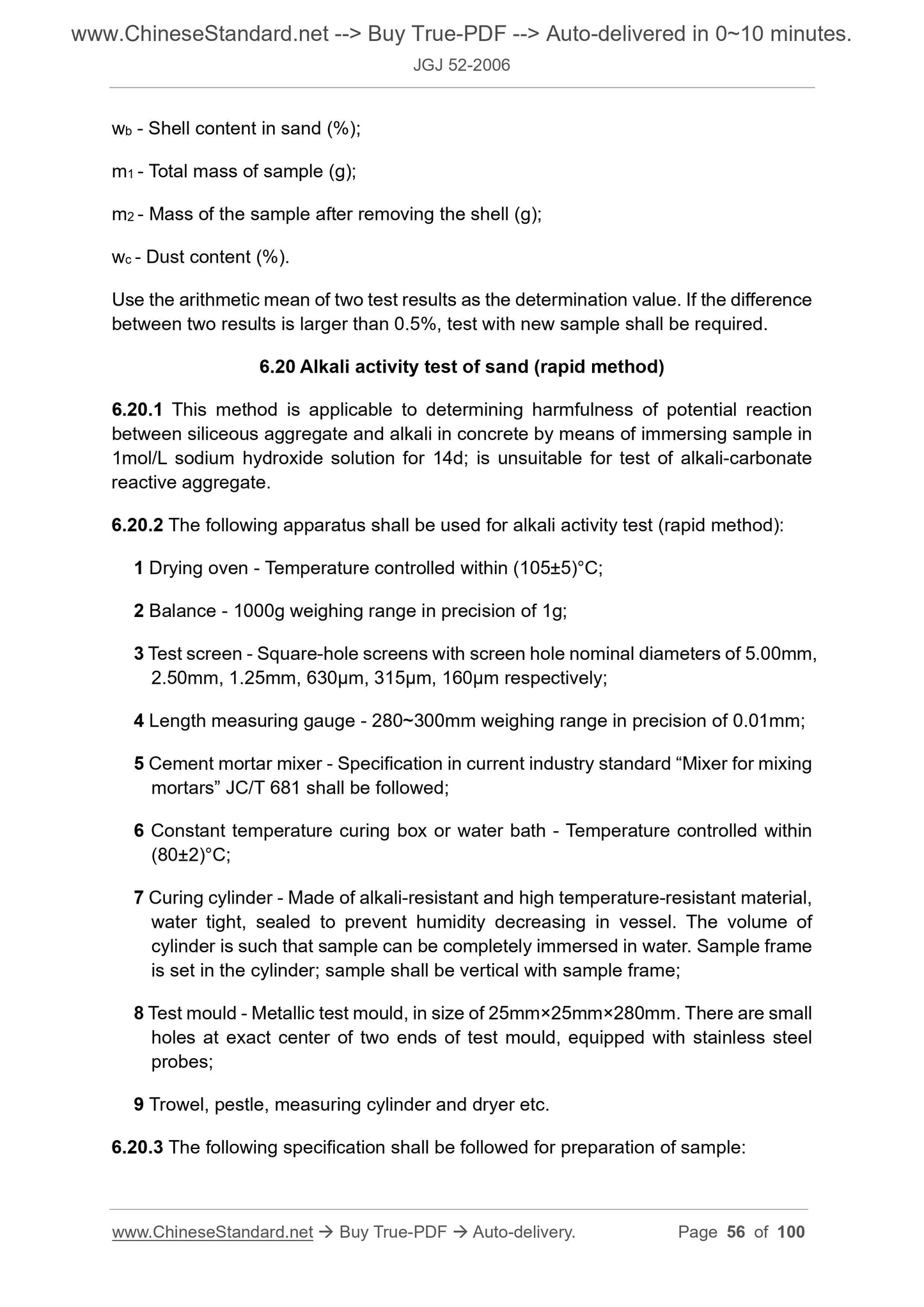
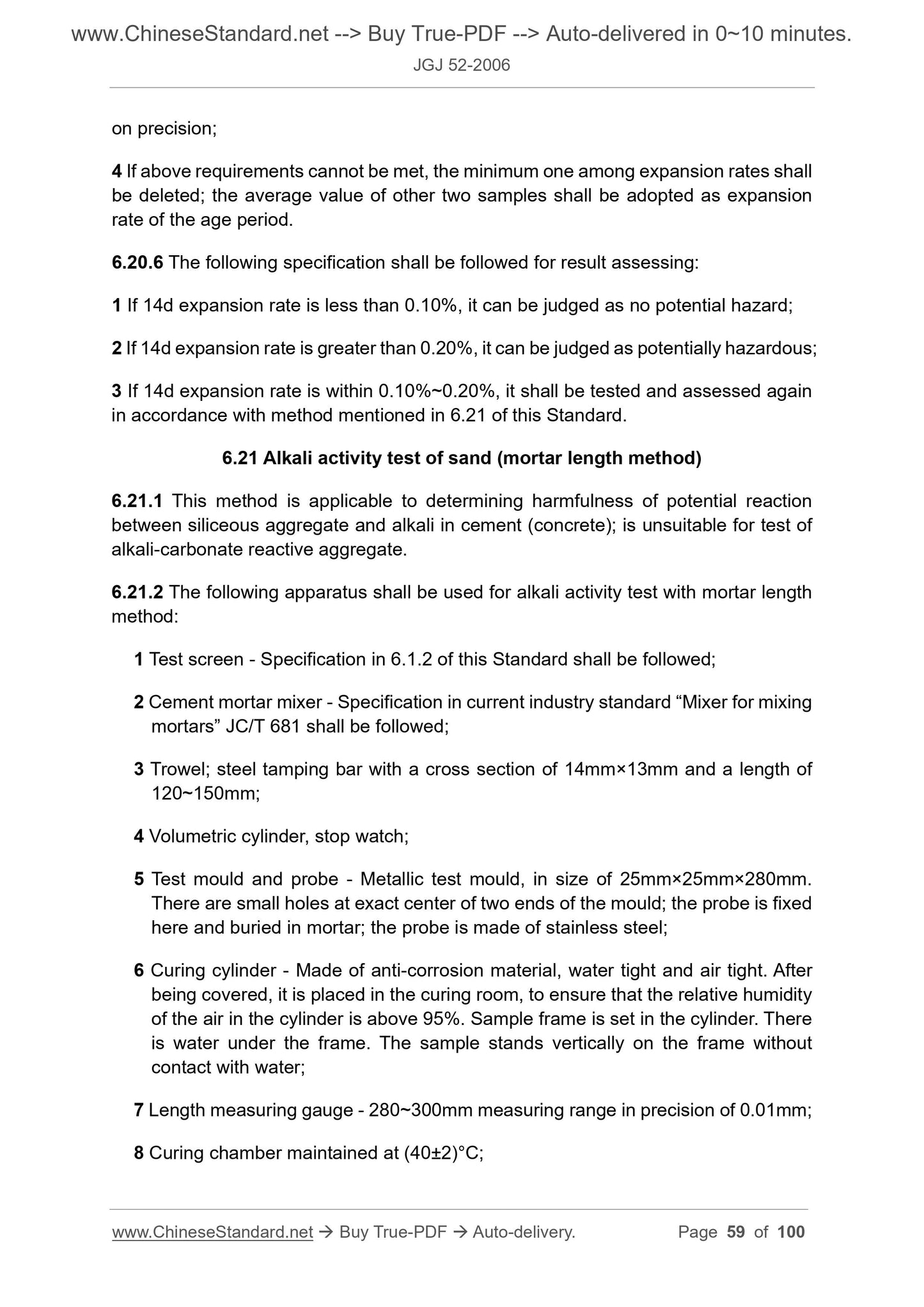