1
/
of
10
PayPal, credit cards. Download editable-PDF and invoice in 1 second!
GB/T 9722-2006 English PDF (GB/T9722-2006)
GB/T 9722-2006 English PDF (GB/T9722-2006)
Regular price
$225.00
Regular price
Sale price
$225.00
Unit price
/
per
Shipping calculated at checkout.
Couldn't load pickup availability
GB/T 9722-2006: Chemical reagent -- General rules for the gas chromatography
Delivery: 9 seconds. Download (and Email) true-PDF + Invoice.
Newer version: (Replacing this standard) GB/T 9722-2023
Get Quotation: Click GB/T 9722-2006 (Self-service in 1-minute)
Newer / historical versions: GB/T 9722-2023
Preview True-PDF (Reload/Scroll-down if blank)
Delivery: 9 seconds. Download (and Email) true-PDF + Invoice.
Newer version: (Replacing this standard) GB/T 9722-2023
Get Quotation: Click GB/T 9722-2006 (Self-service in 1-minute)
Newer / historical versions: GB/T 9722-2023
Preview True-PDF (Reload/Scroll-down if blank)
Share
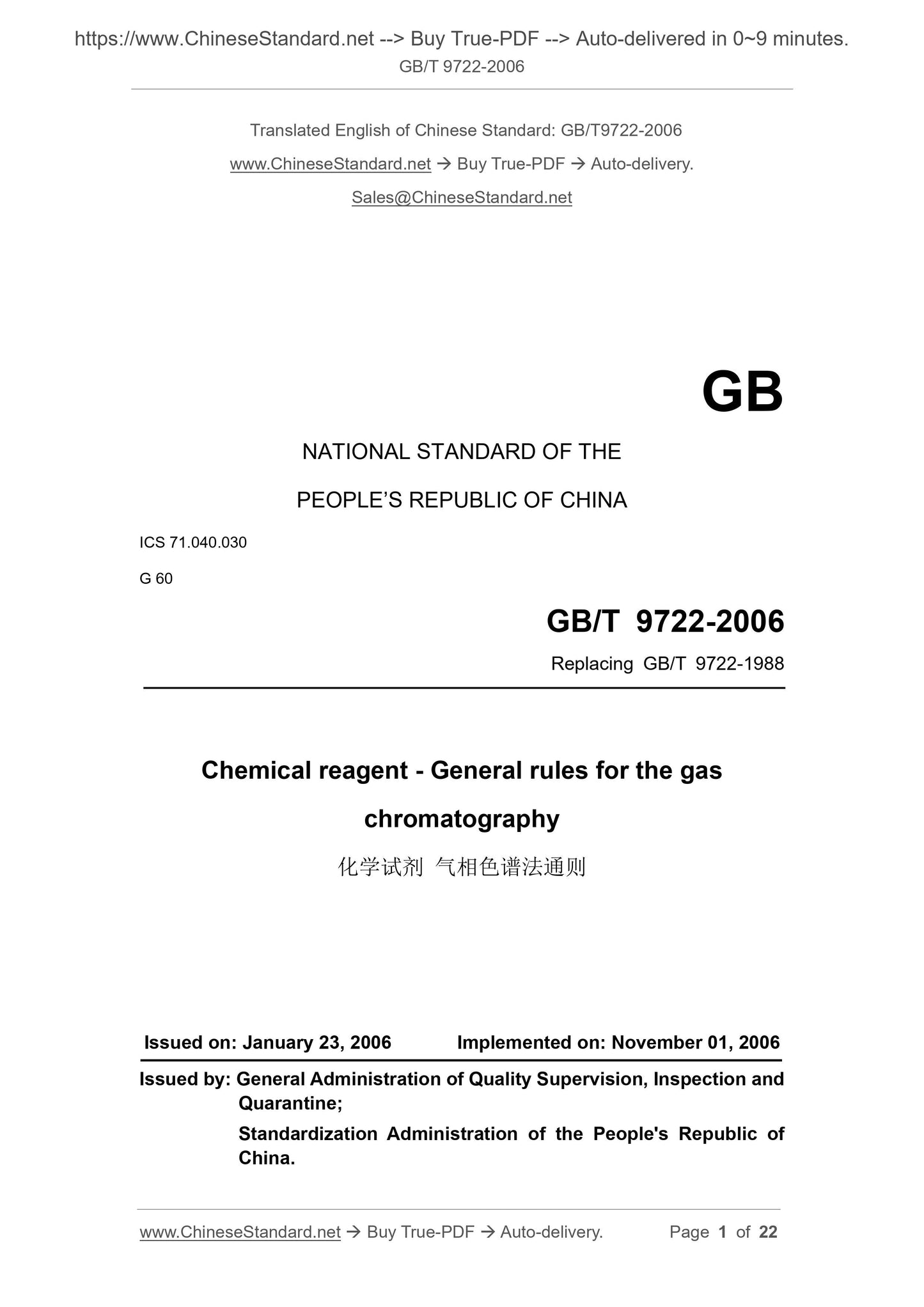
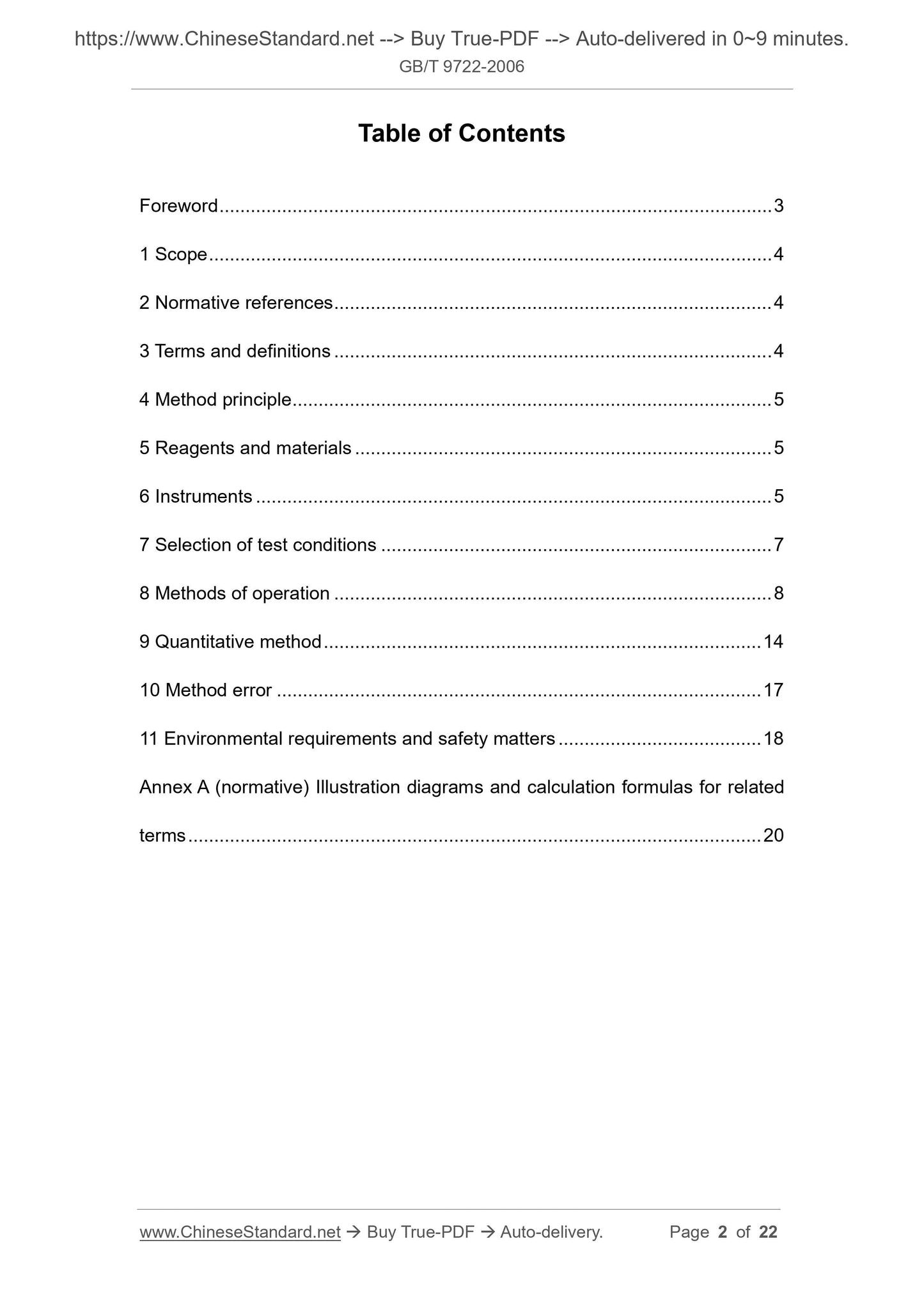
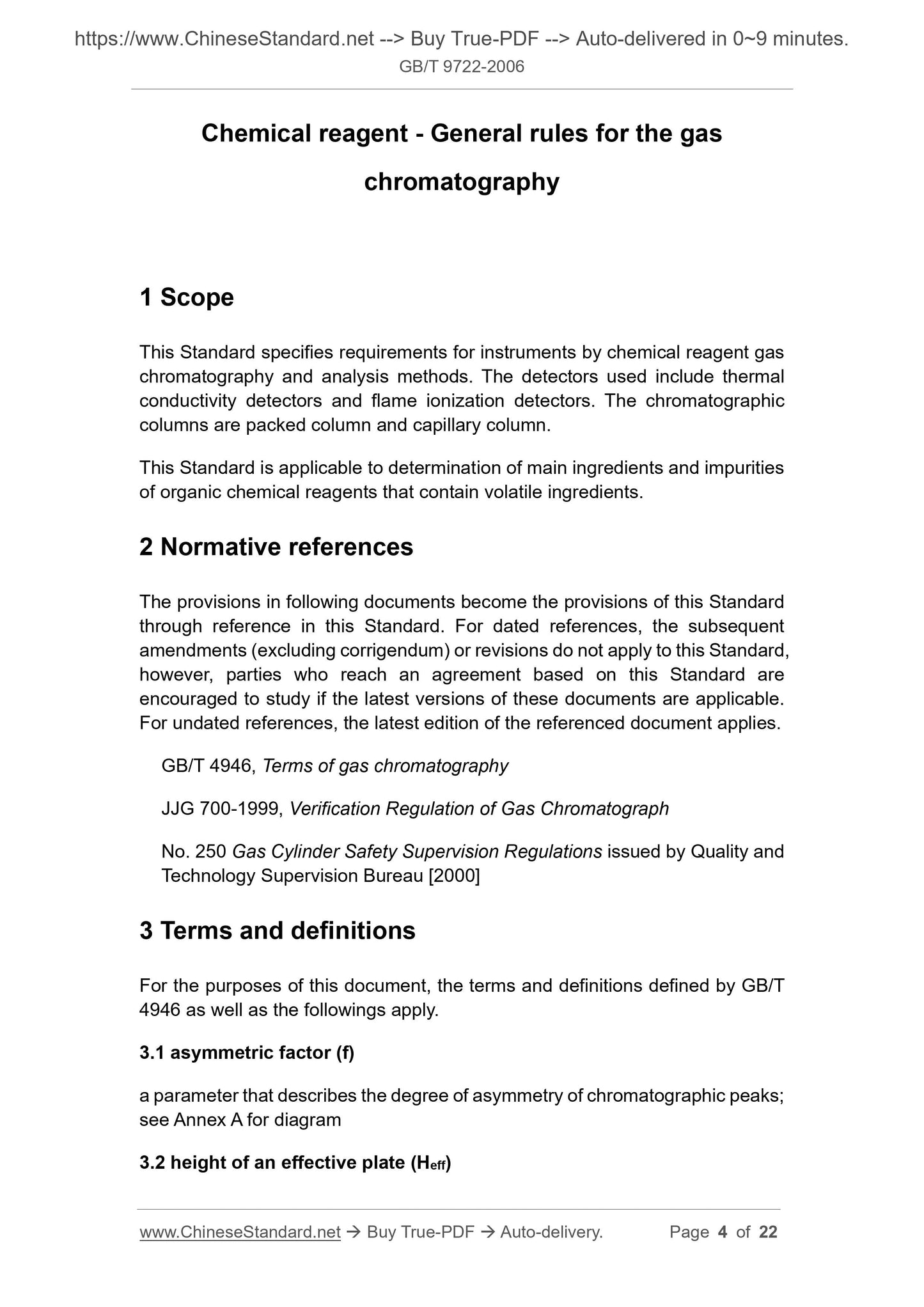
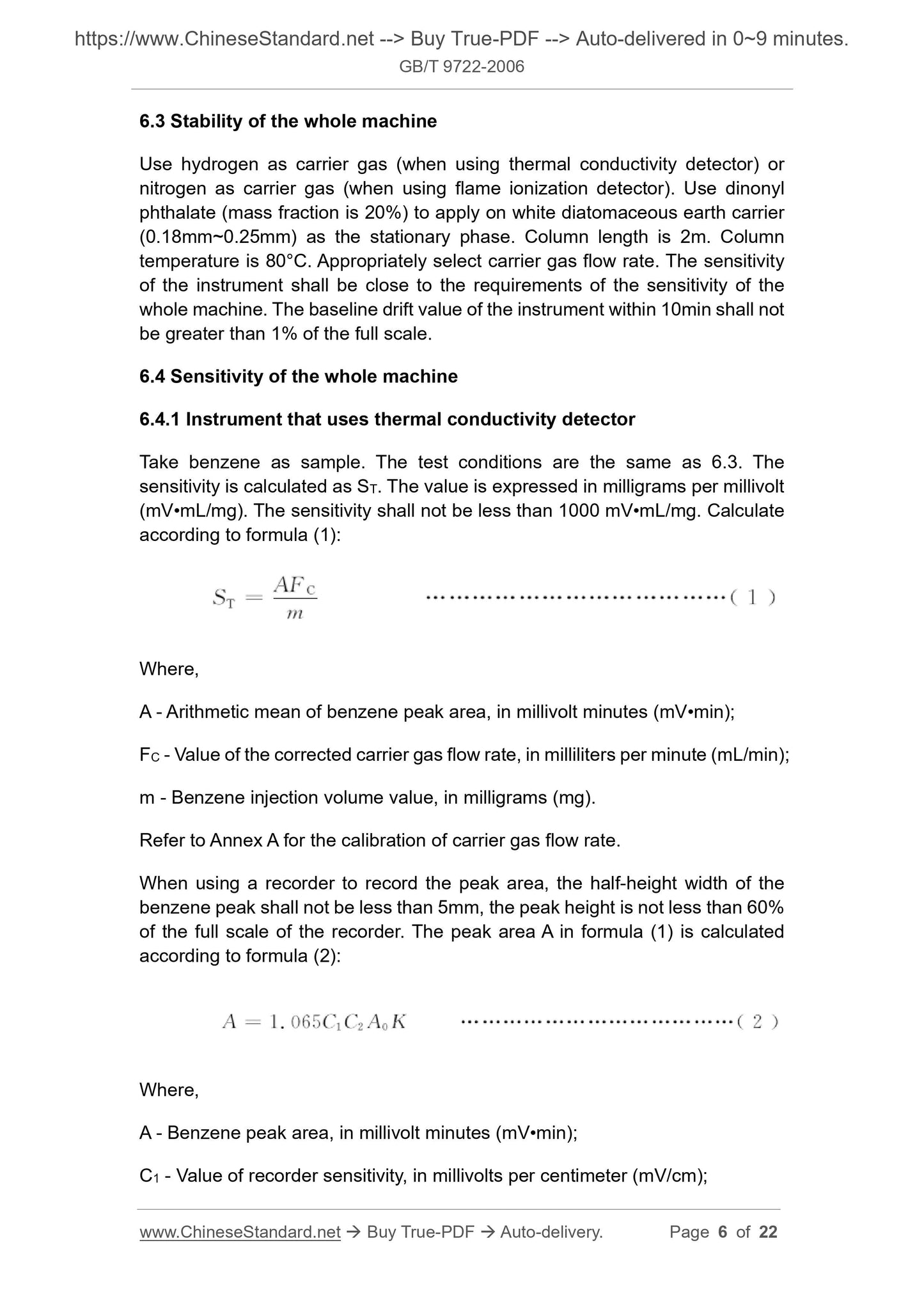
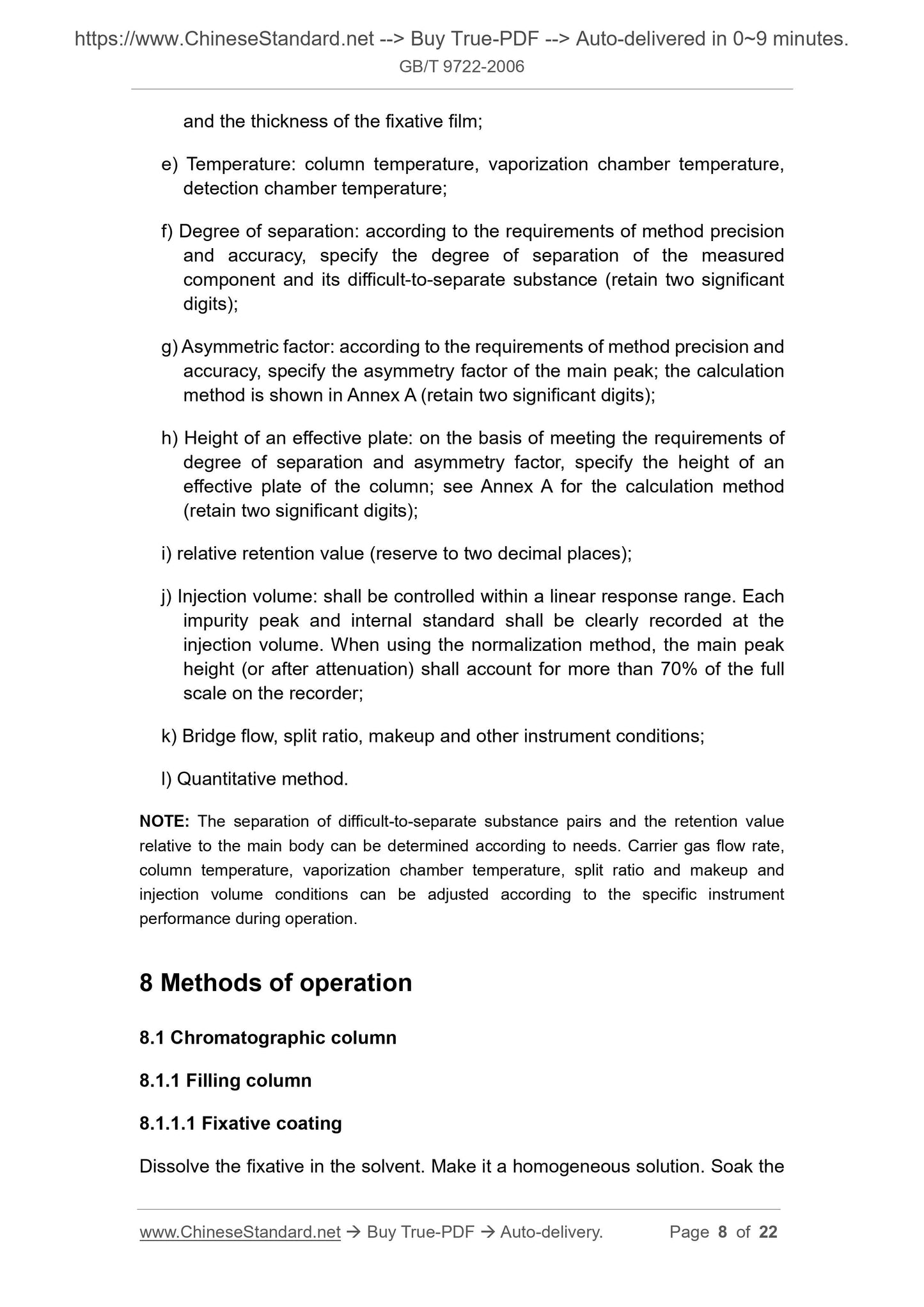
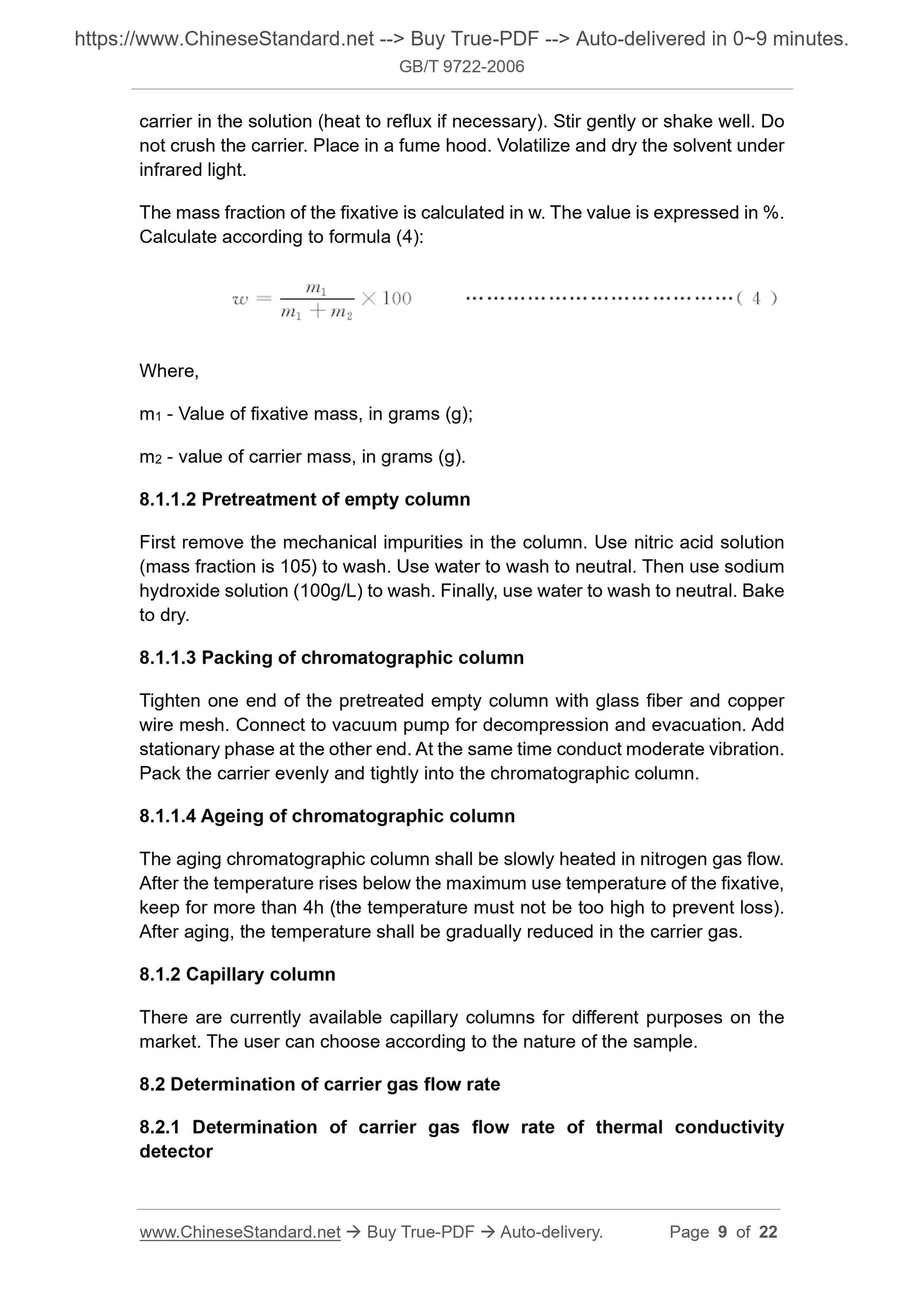
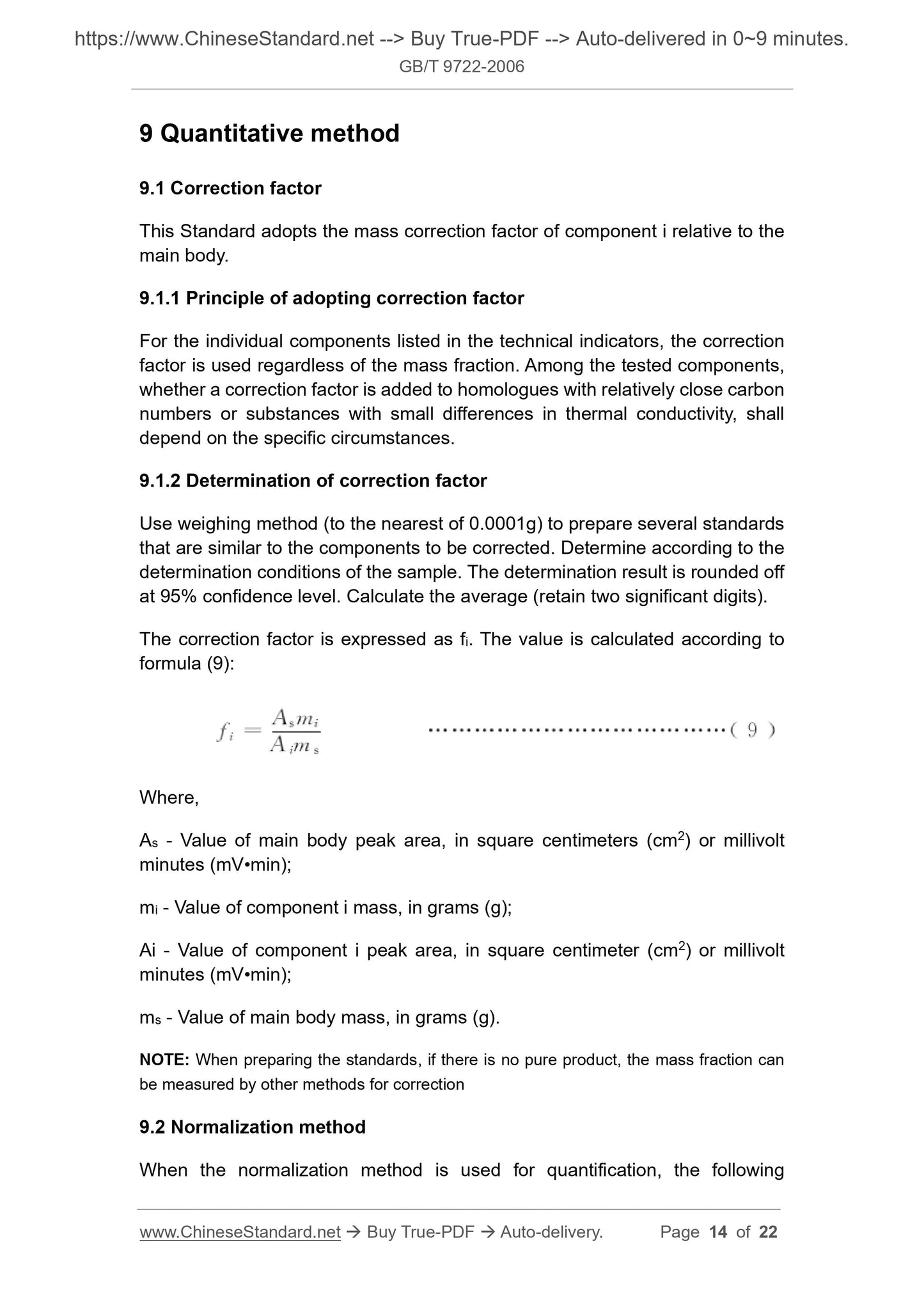
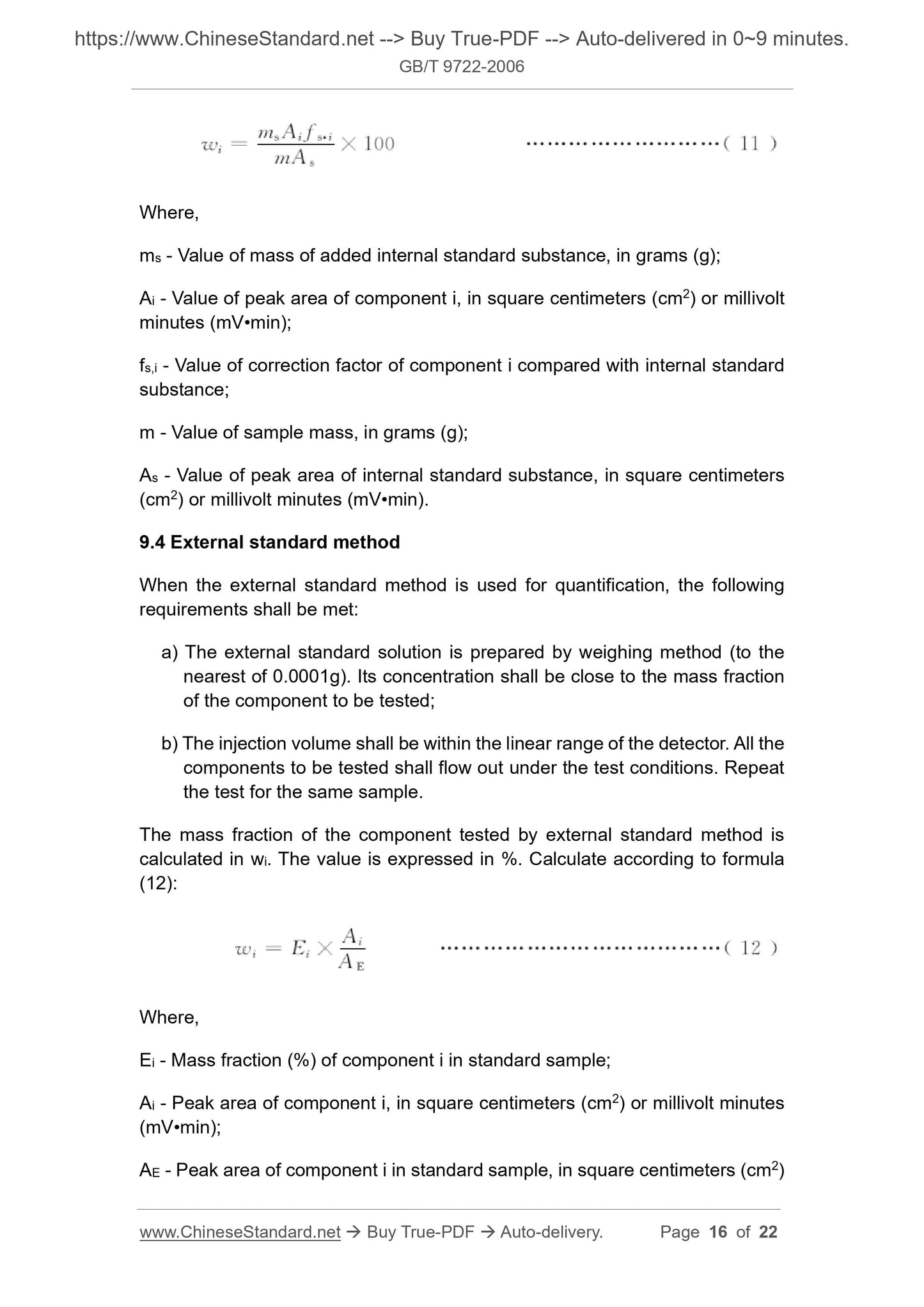
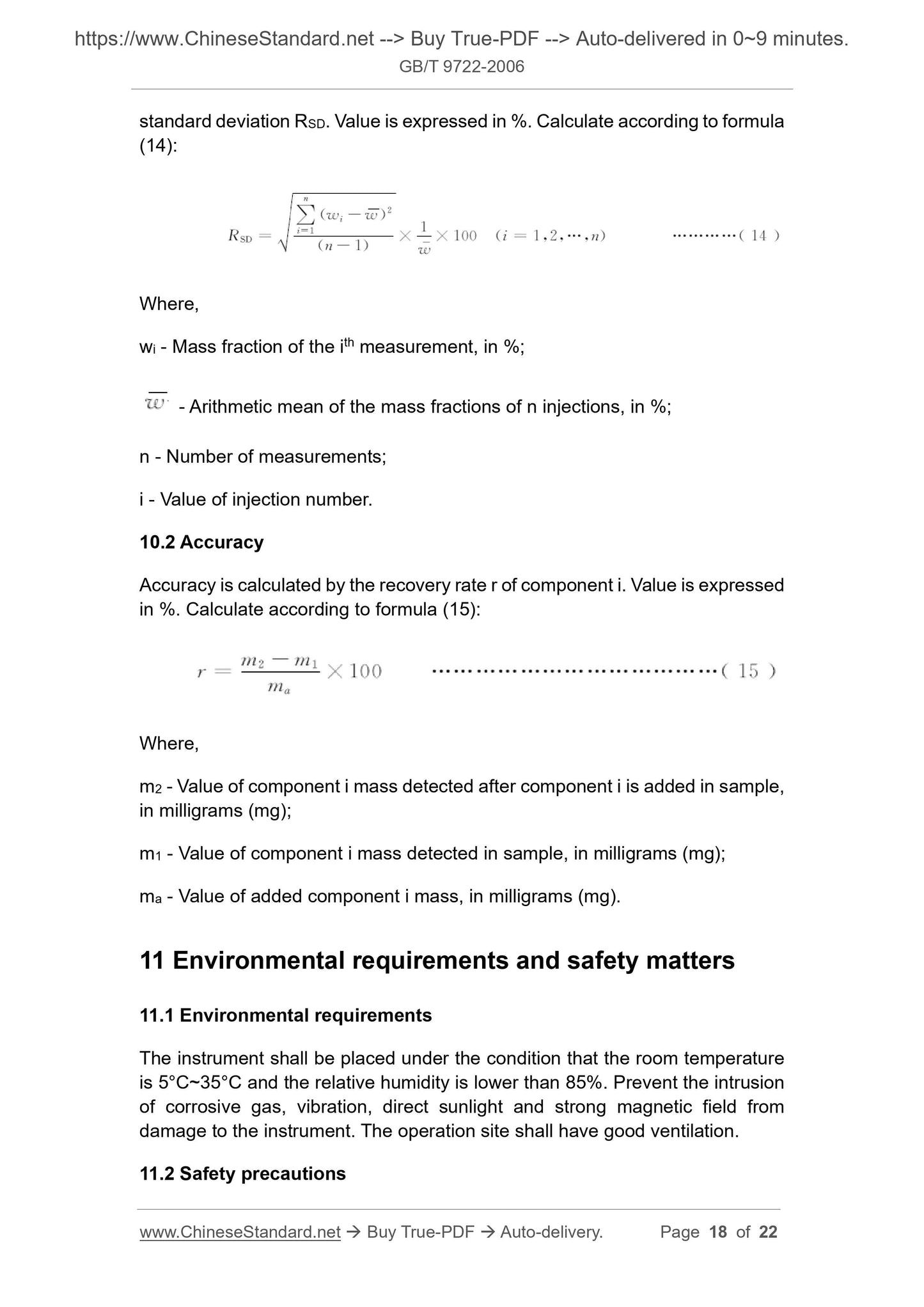
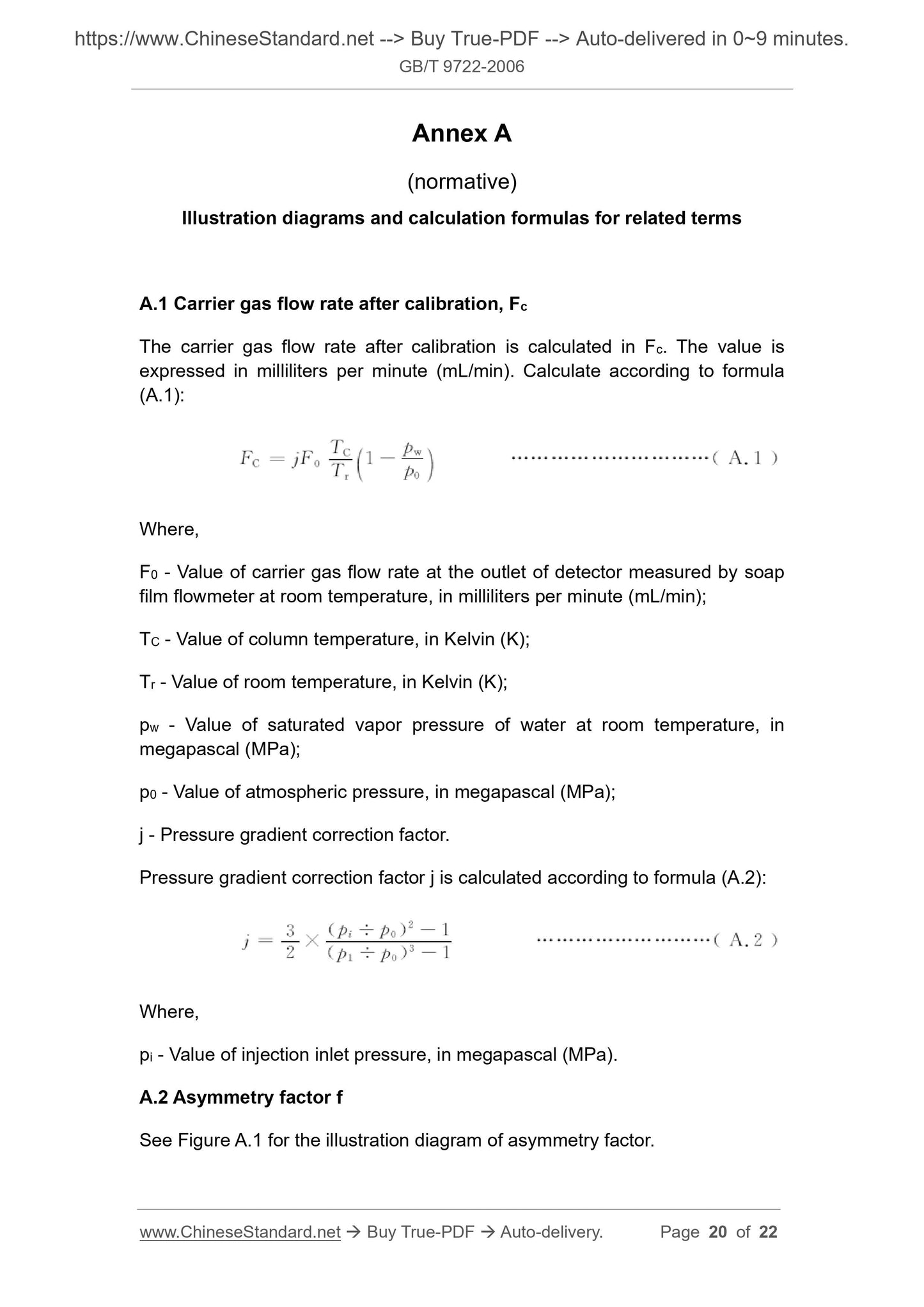