1
/
of
5
www.ChineseStandard.us -- Field Test Asia Pte. Ltd.
GB/T 8753.4-2005 English PDF (GB/T8753.4-2005)
GB/T 8753.4-2005 English PDF (GB/T8753.4-2005)
Regular price
$120.00
Regular price
Sale price
$120.00
Unit price
/
per
Shipping calculated at checkout.
Couldn't load pickup availability
GB/T 8753.4-2005: Anodizing of aluminium and aluminium alloys -- Assessment of quality of sealed anodic oxide coatings -- Part 4: Dye spot test with prior acid treatment
Delivery: 9 seconds. Download (and Email) true-PDF + Invoice.
Get Quotation: Click GB/T 8753.4-2005 (Self-service in 1-minute)
Newer / historical versions: GB/T 8753.4-2005
Preview True-PDF (Reload/Scroll-down if blank)
Delivery: 9 seconds. Download (and Email) true-PDF + Invoice.
Get Quotation: Click GB/T 8753.4-2005 (Self-service in 1-minute)
Newer / historical versions: GB/T 8753.4-2005
Preview True-PDF (Reload/Scroll-down if blank)
Share
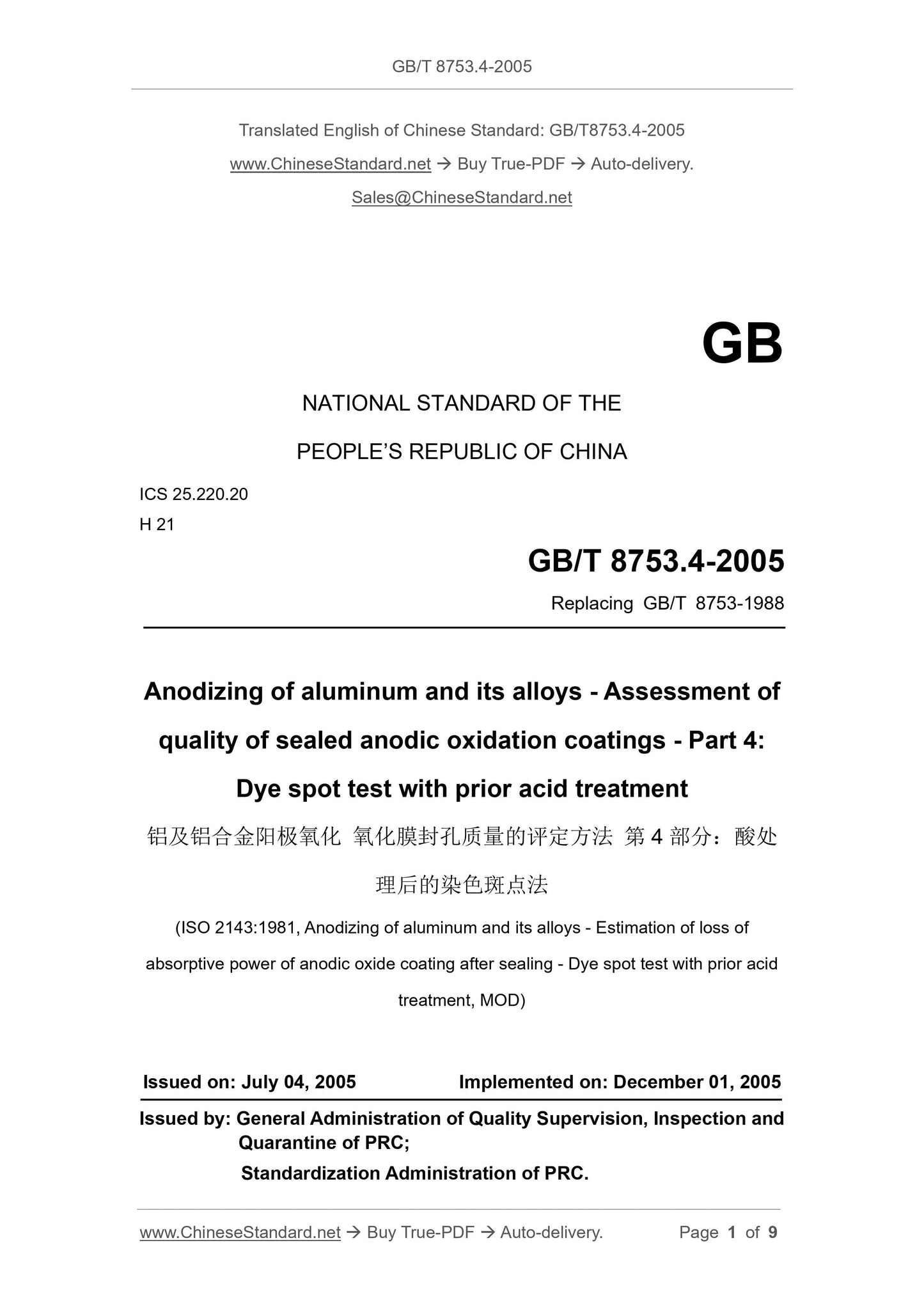
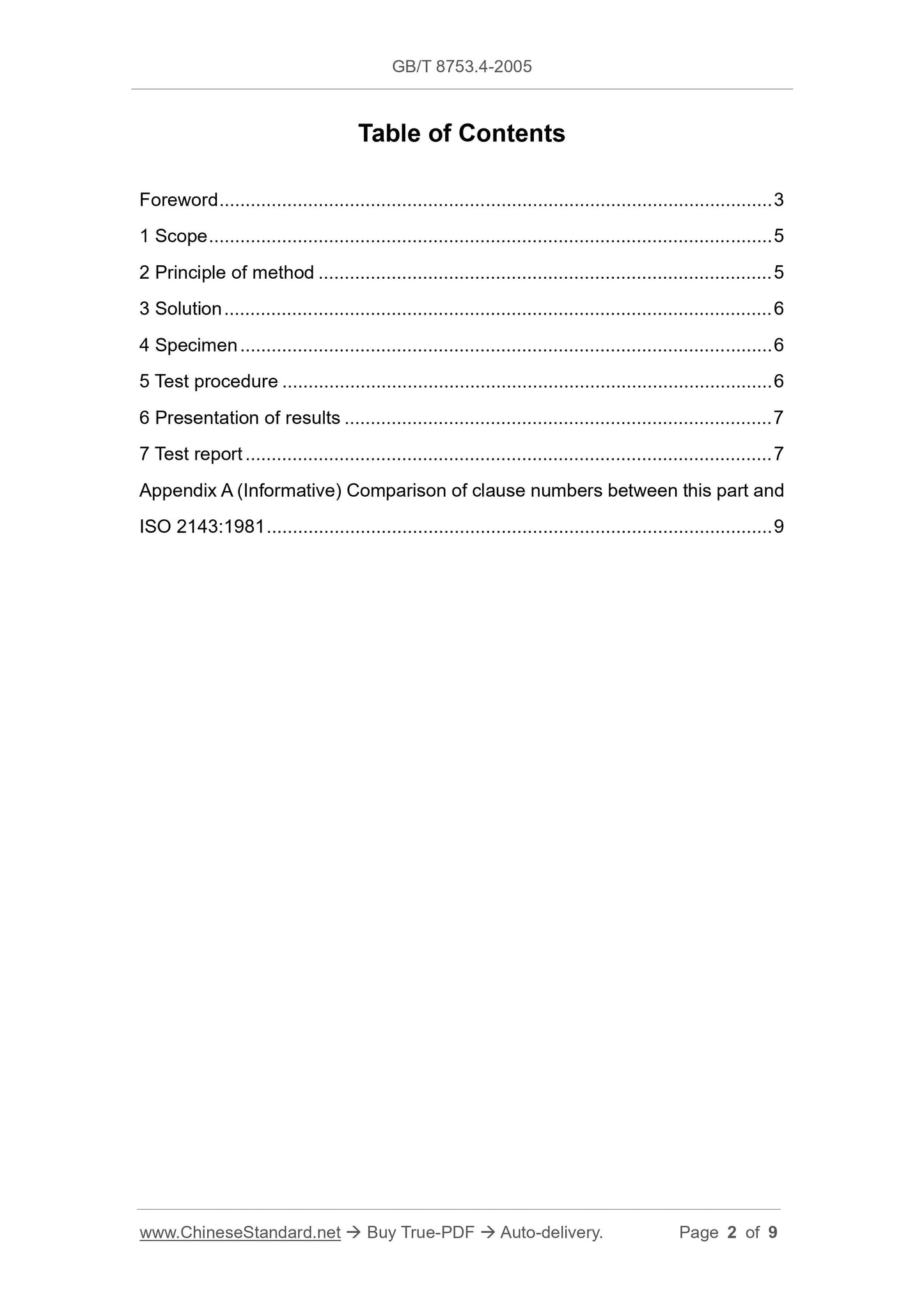
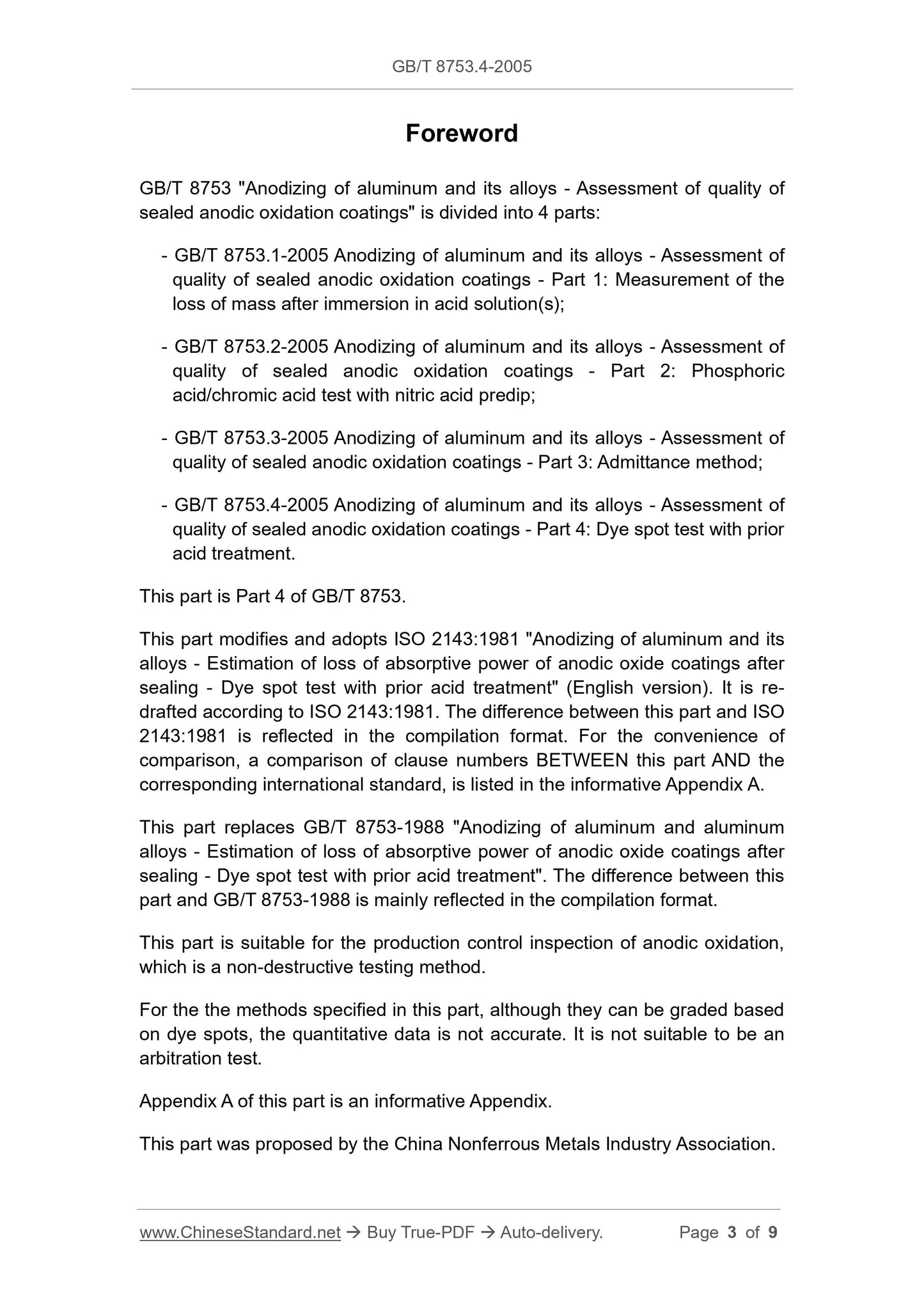
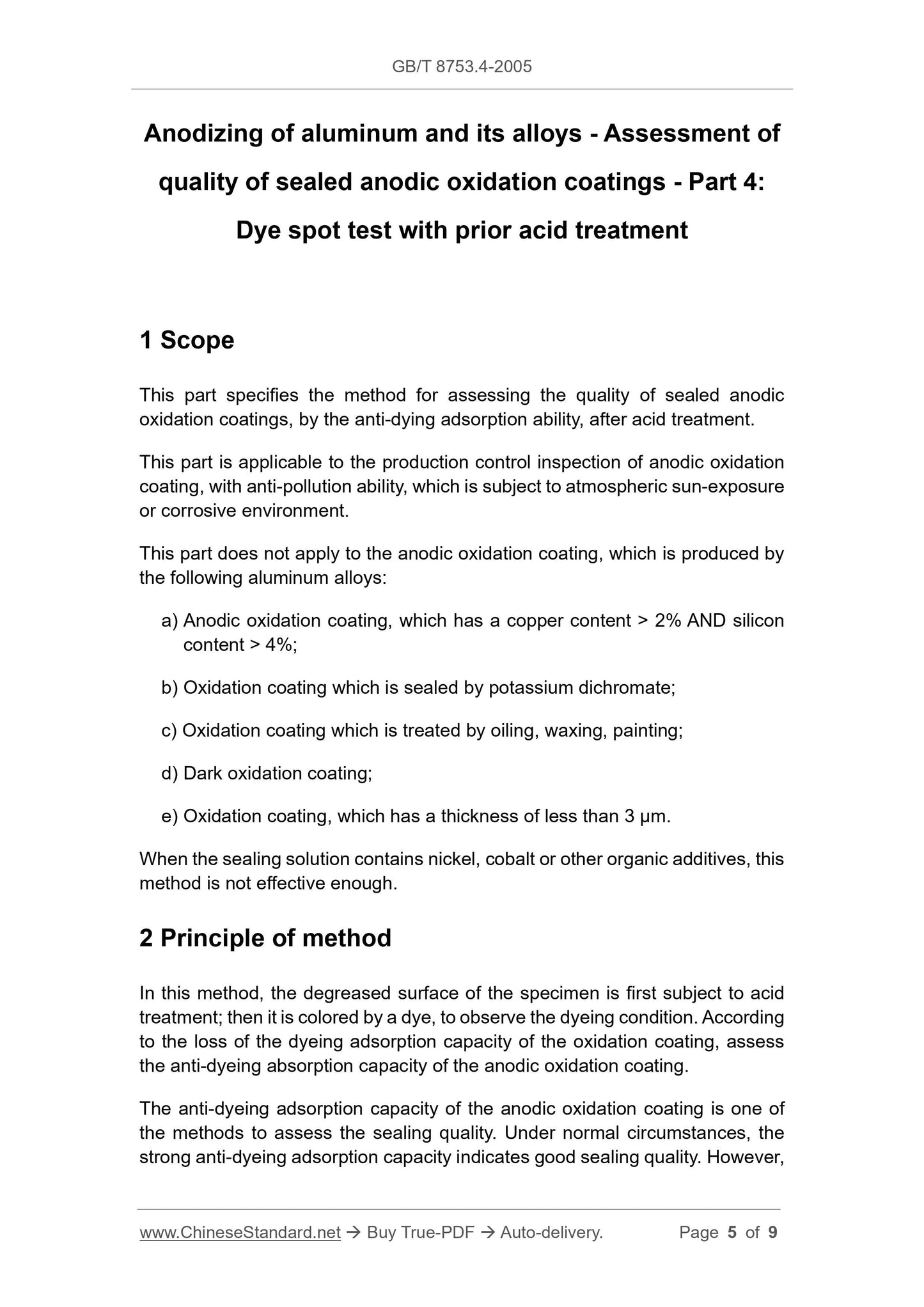
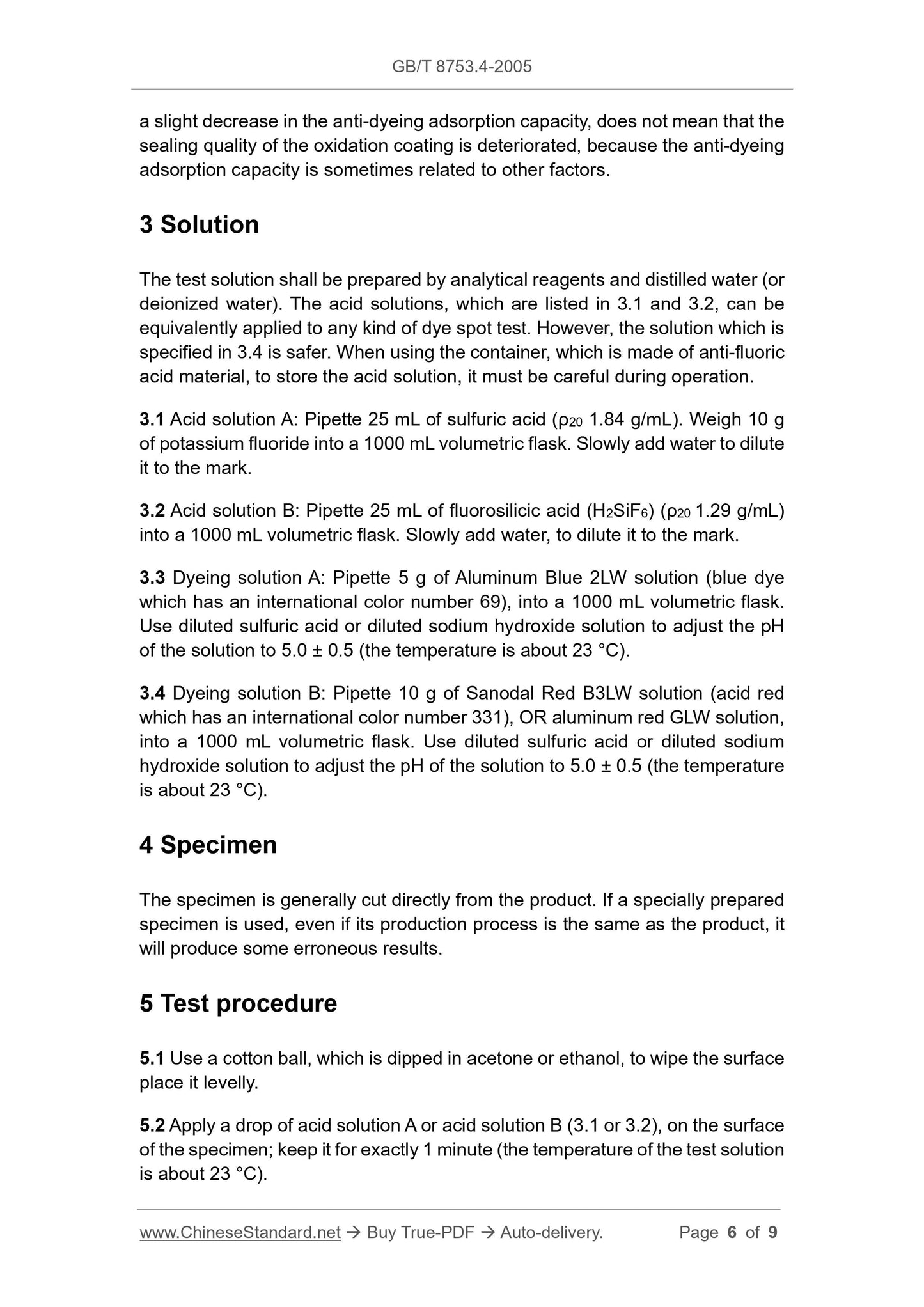