1
/
of
6
www.ChineseStandard.us -- Field Test Asia Pte. Ltd.
GB/T 8753.1-2017 English PDF (GB/T8753.1-2017)
GB/T 8753.1-2017 English PDF (GB/T8753.1-2017)
Regular price
$110.00
Regular price
Sale price
$110.00
Unit price
/
per
Shipping calculated at checkout.
Couldn't load pickup availability
GB/T 8753.1-2017: Anodizing of aluminum and its alloys - Assessment of quality of sealed anodic oxidation coatings - Part 1: Measurement of the loss of mass after immersion in acid solution(s)
Delivery: 9 seconds. Download (and Email) true-PDF + Invoice.
Get Quotation: Click GB/T 8753.1-2017 (Self-service in 1-minute)
Newer / historical versions: GB/T 8753.1-2017
Preview True-PDF (Reload/Scroll-down if blank)
Delivery: 9 seconds. Download (and Email) true-PDF + Invoice.
Get Quotation: Click GB/T 8753.1-2017 (Self-service in 1-minute)
Newer / historical versions: GB/T 8753.1-2017
Preview True-PDF (Reload/Scroll-down if blank)
Share
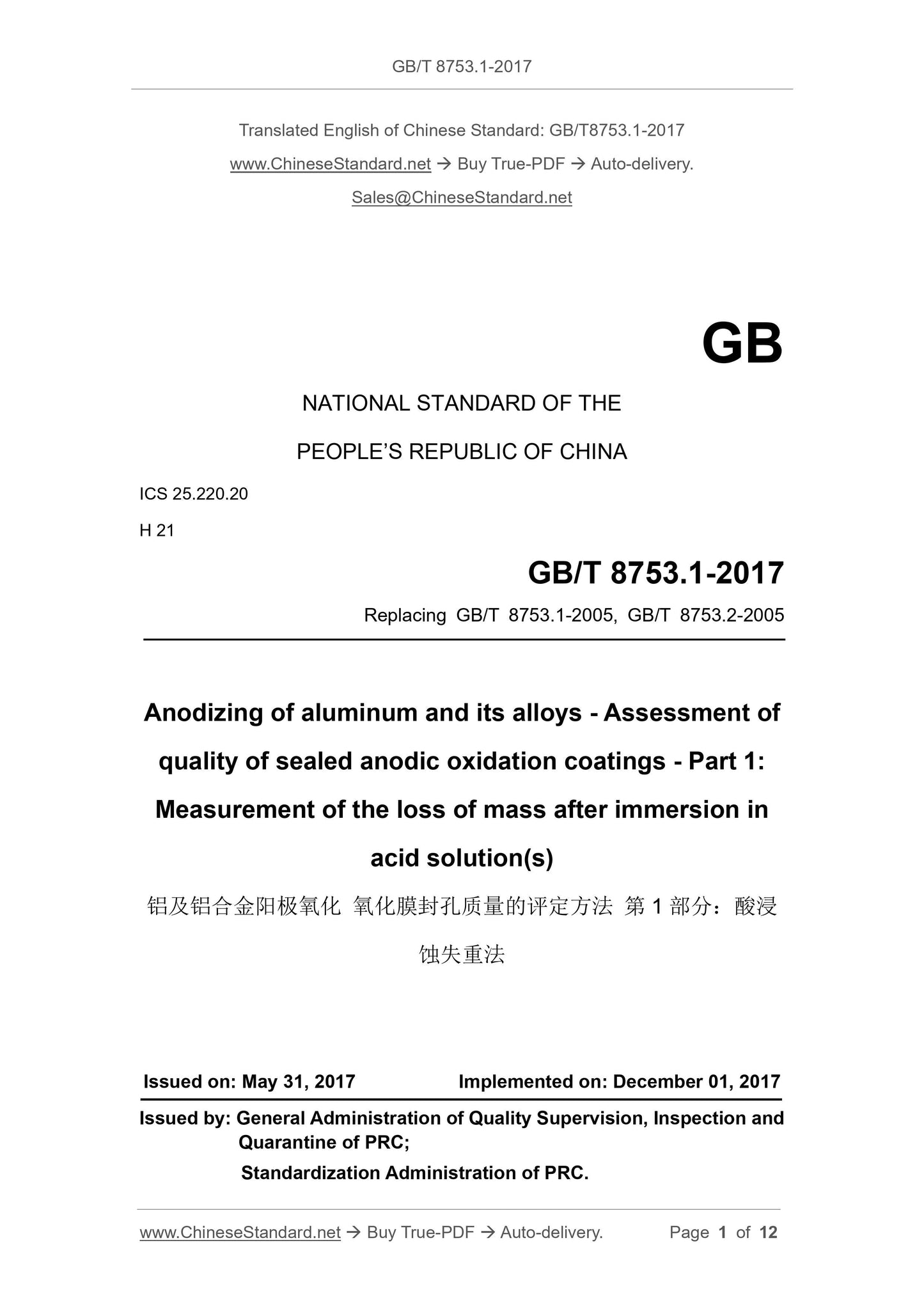

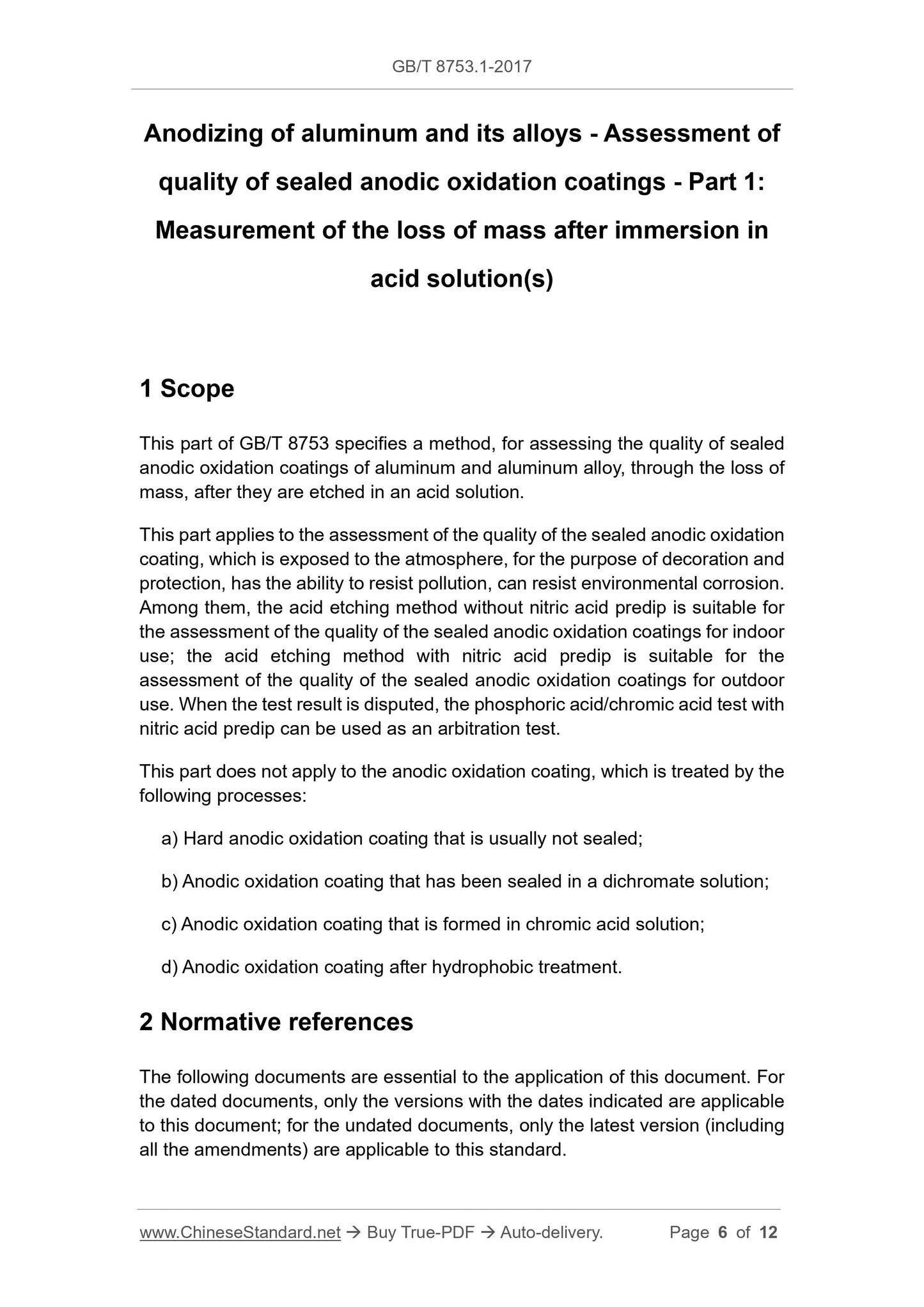
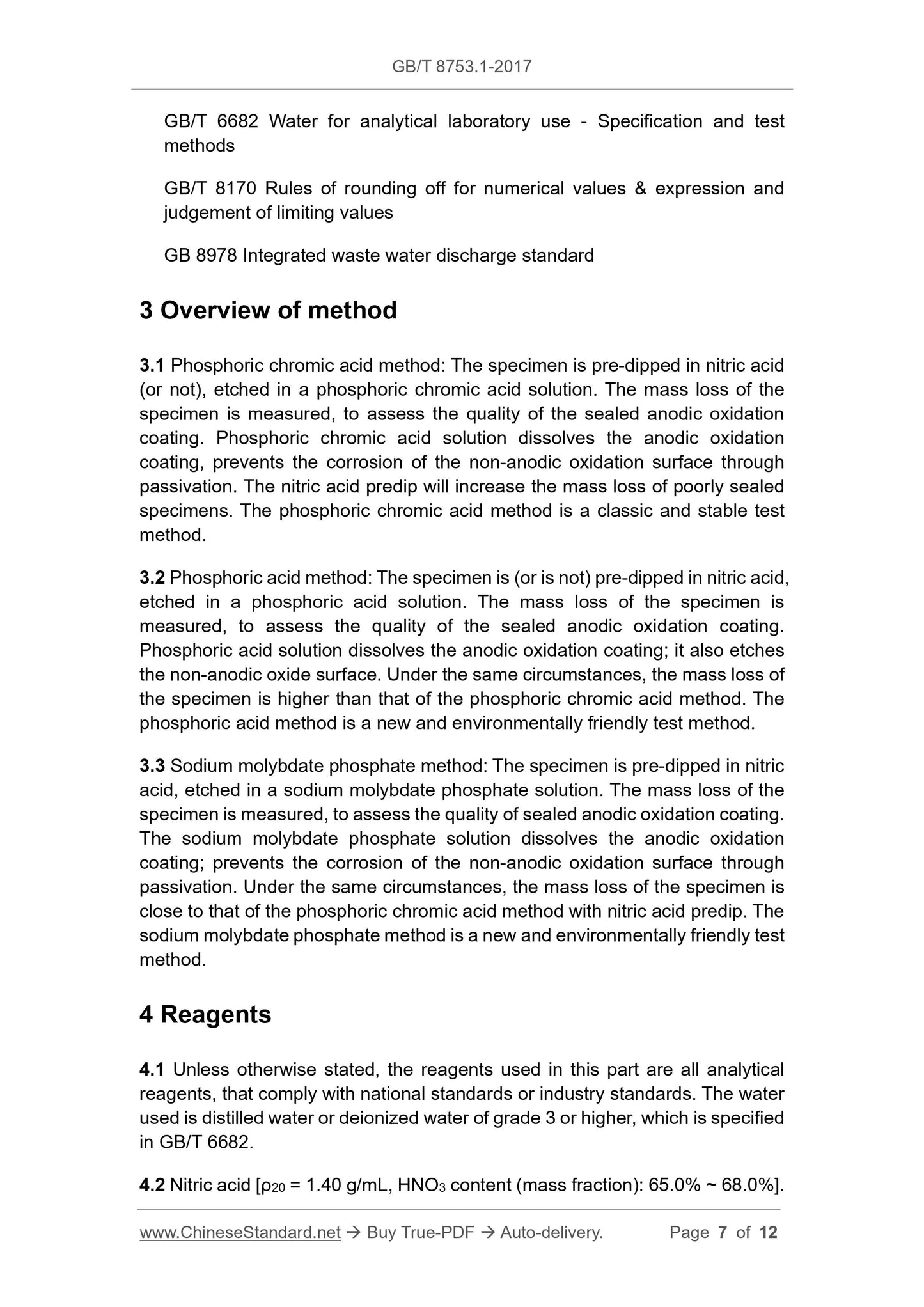
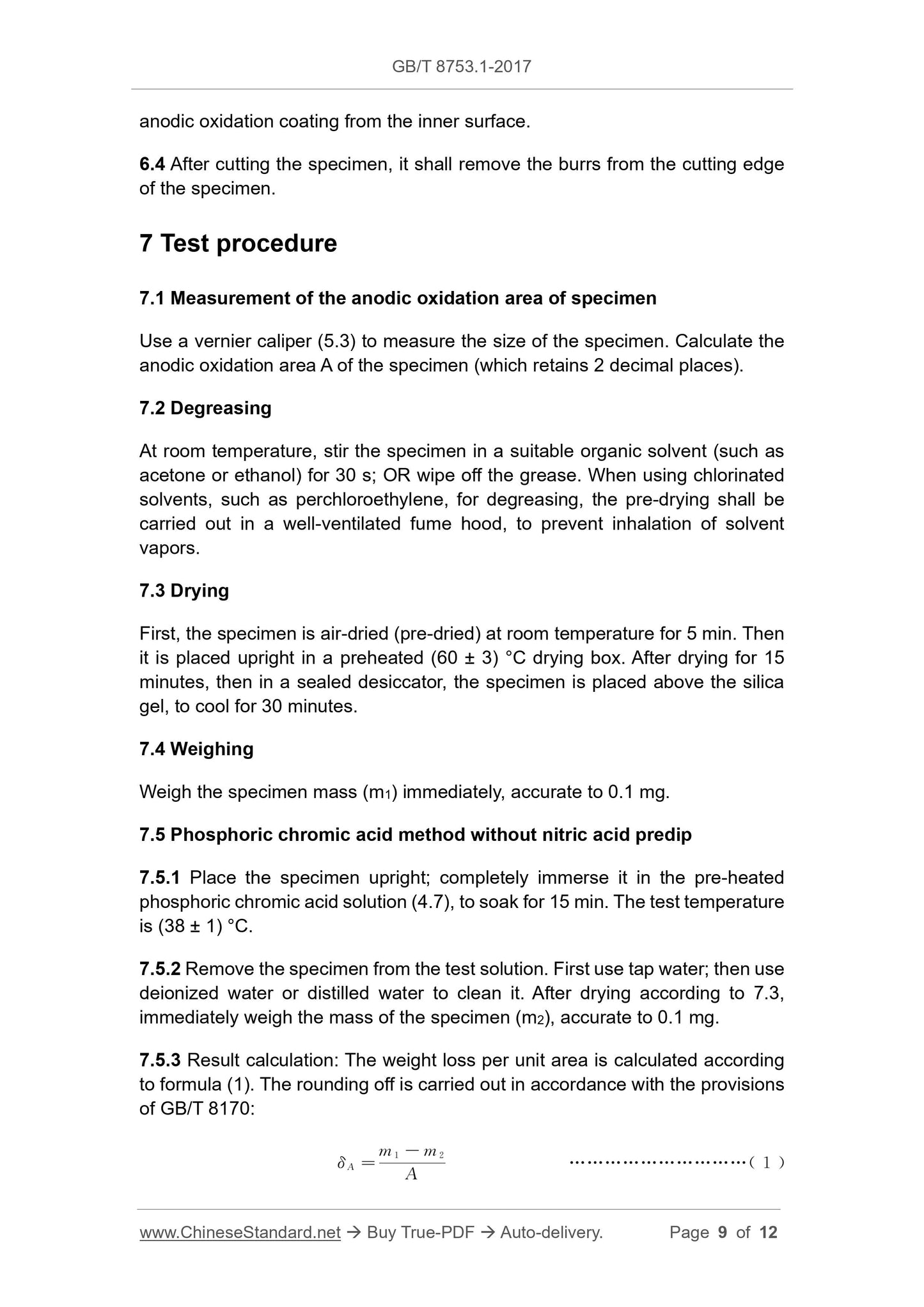
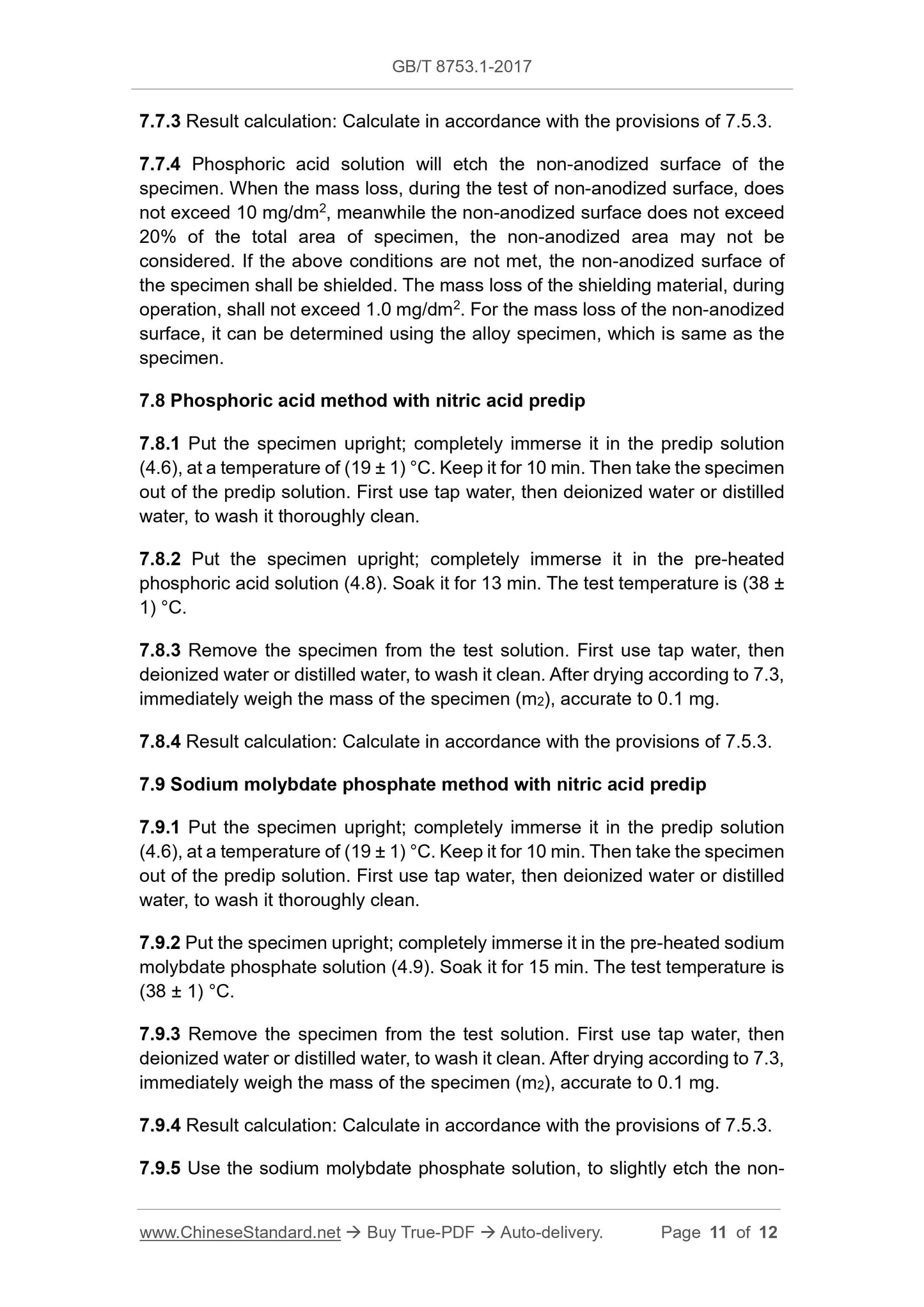