1
/
of
6
www.ChineseStandard.us -- Field Test Asia Pte. Ltd.
GB/T 8651-2015 English PDF (GB/T8651-2015)
GB/T 8651-2015 English PDF (GB/T8651-2015)
Regular price
$150.00
Regular price
Sale price
$150.00
Unit price
/
per
Shipping calculated at checkout.
Couldn't load pickup availability
GB/T 8651-2015: Flaw Detection Method by the Ultrasonic Plate Wave for Metal Plates
Delivery: 9 seconds. Download (and Email) true-PDF + Invoice.Get Quotation: Click GB/T 8651-2015 (Self-service in 1-minute)
Newer / historical versions: GB/T 8651-2015
Preview True-PDF
Scope
This Standard specifies the terms, definitions, general requirements, flaw detection equipment, contrast sample, selection of plate wave mode, flaw detection method and flaw assessment of flaw detection method by the ultrasonic plate wave for metal plates.This Standard is applicable to flaw detection by the ultrasonic plate wave for metal plates whose thickness is not more than 5 times of the surface wavelength of detected plates. However, it must be confirmed that the stimulated sound wave is plate wave, and flaw detection can be conducted under sufficient sensitivity of flaw detection.
Basic Data
Standard ID | GB/T 8651-2015 (GB/T8651-2015) |
Description (Translated English) | Flaw Detection Method by the Ultrasonic Plate Wave for Metal Plates |
Sector / Industry | National Standard (Recommended) |
Classification of Chinese Standard | H26 |
Classification of International Standard | 77.040.20 |
Word Count Estimation | 21,230 |
Date of Issue | 2015-09-11 |
Date of Implementation | 2016-06-01 |
Older Standard (superseded by this standard) | GB/T 8651-2002 |
Quoted Standard | GB/T 9445; GB/T 12604.1; JB/T 10061 |
Regulation (derived from) | National Standard Announcement 2015 No.25 |
Issuing agency(ies) | General Administration of Quality Supervision, Inspection and Quarantine of the People's Republic of China, Standardization Administration of the People's Republic of China |
Summary | This standard specifies the terms and definitions of sheet metal plate wave ultrasonic flaw detection methods, general requirements, testing equipment, the comparative sample, select the plate wave mode, testing methods and defect assessment and so on. Sheet metal plate wave ultrasonic flaw detection This standard applies to the subject sheet thickness of not more than five times the wavelength of the surface wave, but must be confirmed indeed inspired acoustic wave plate, and with sufficient detection sensitivity testing. |
Share
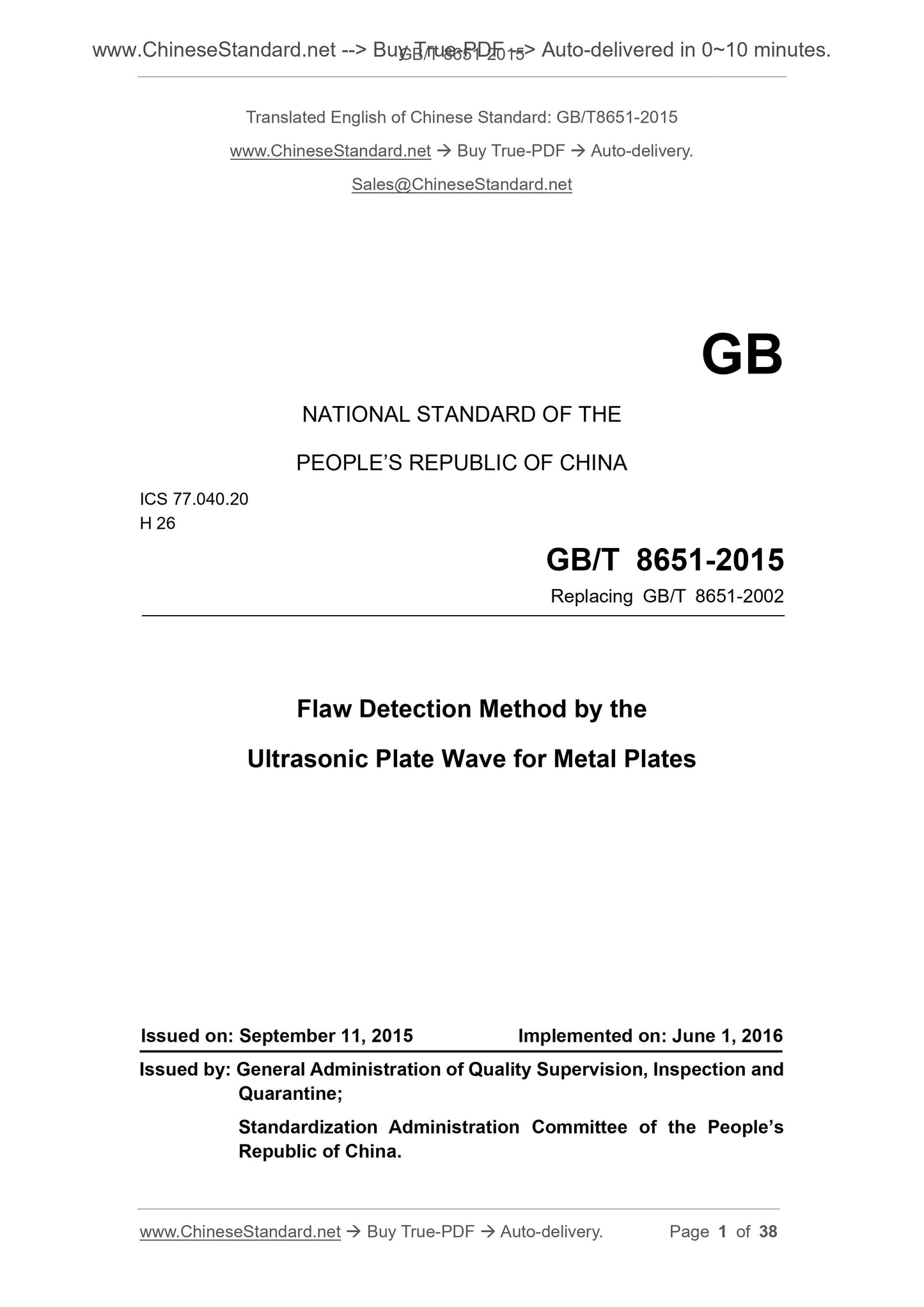
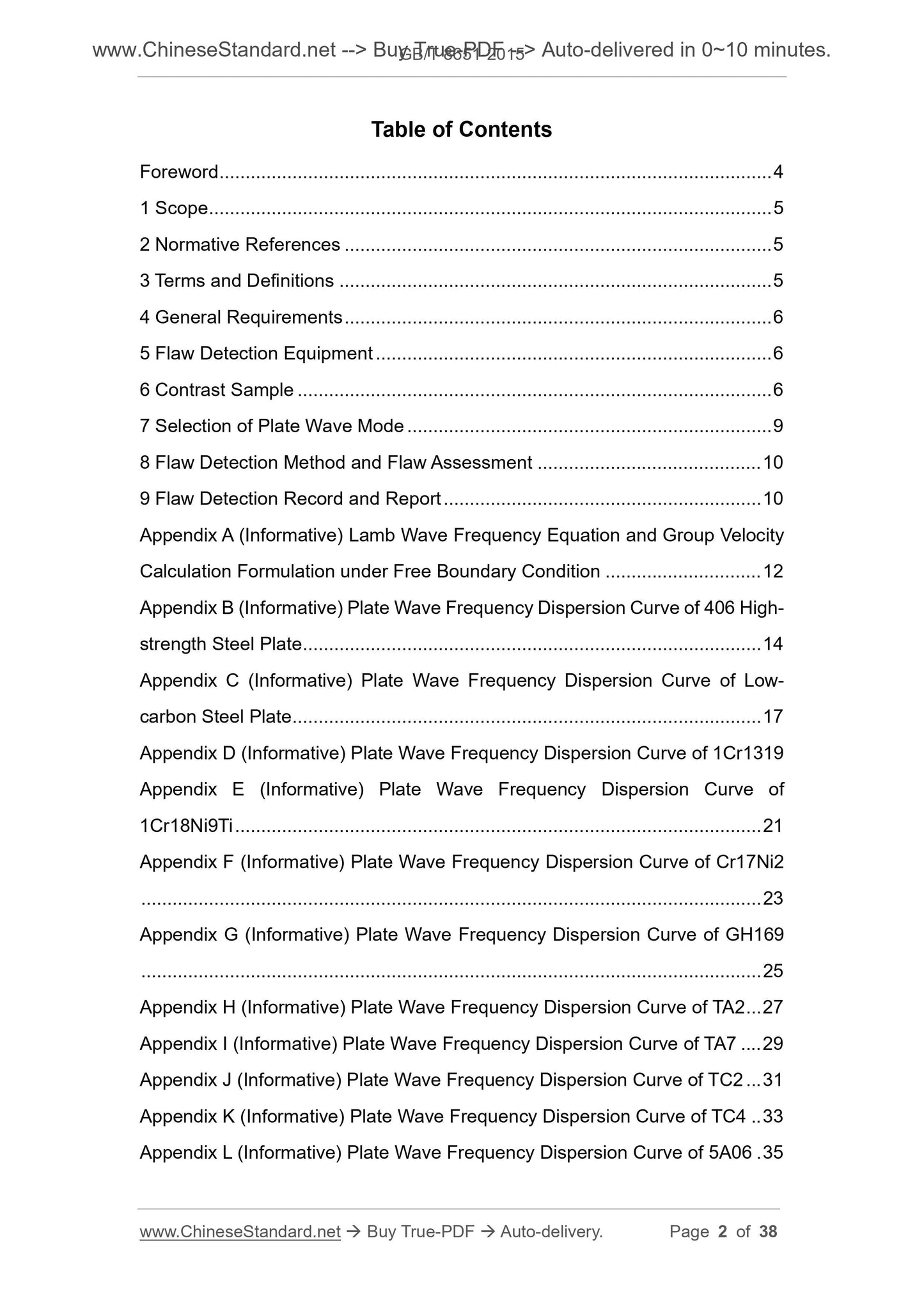
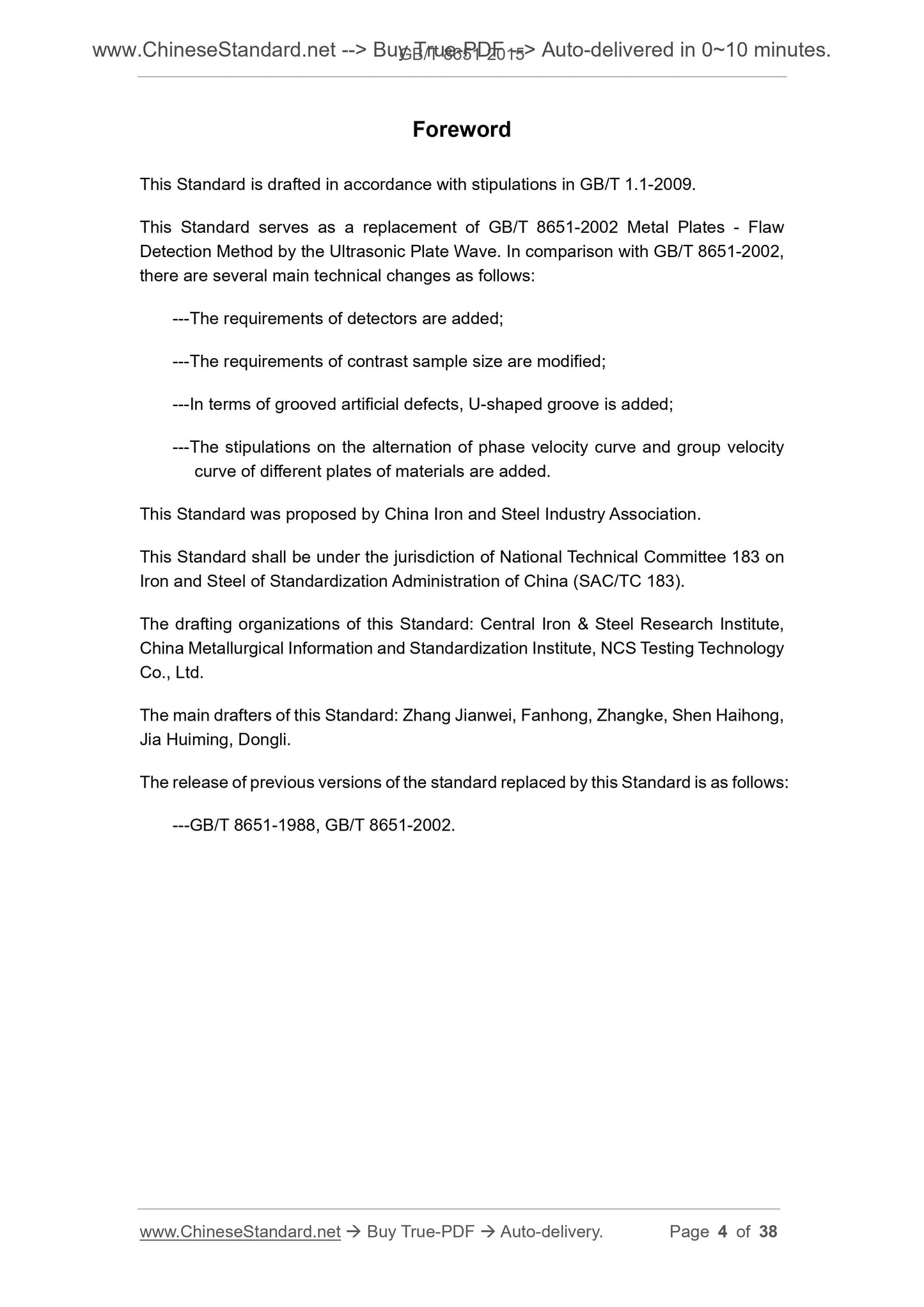
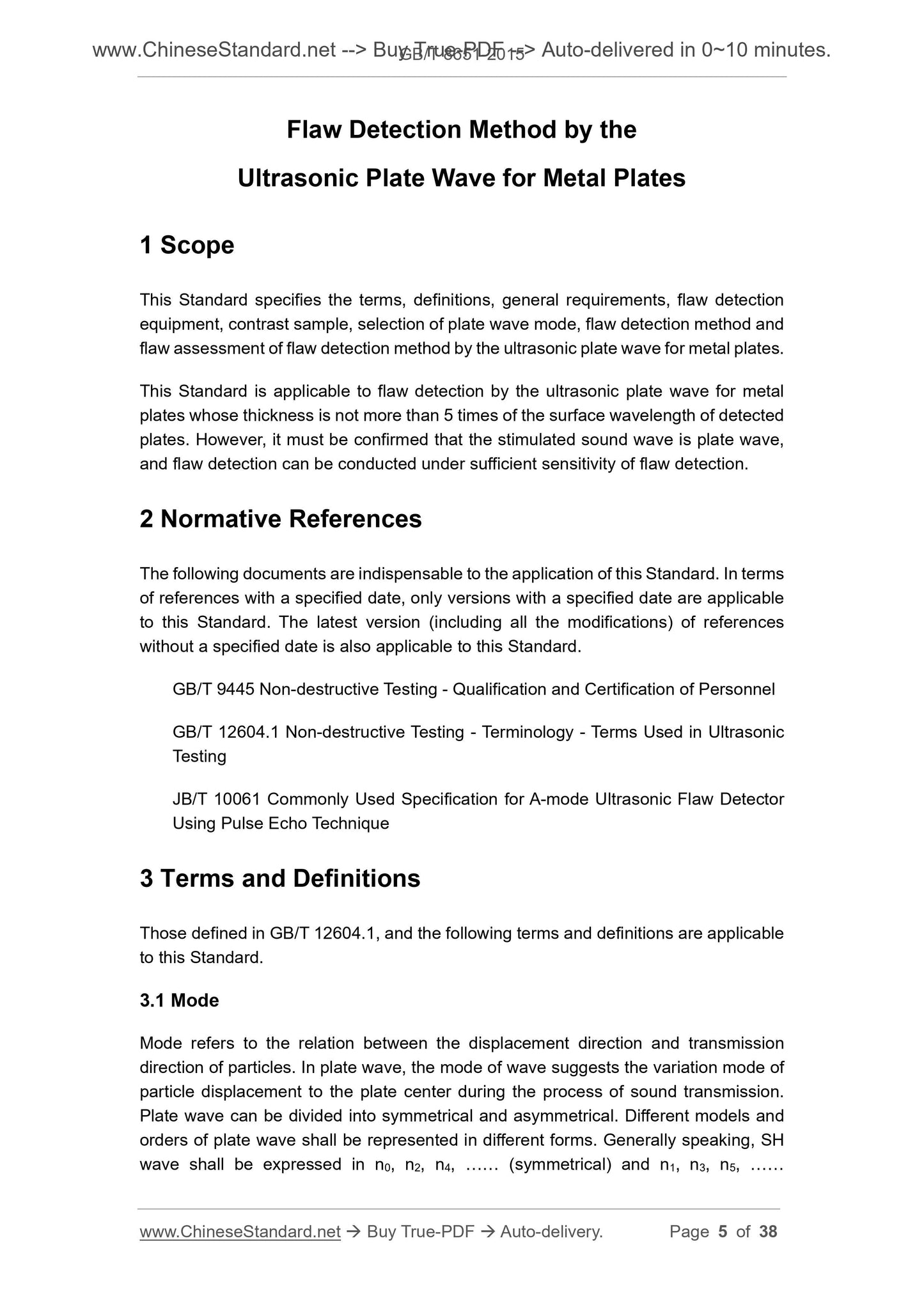
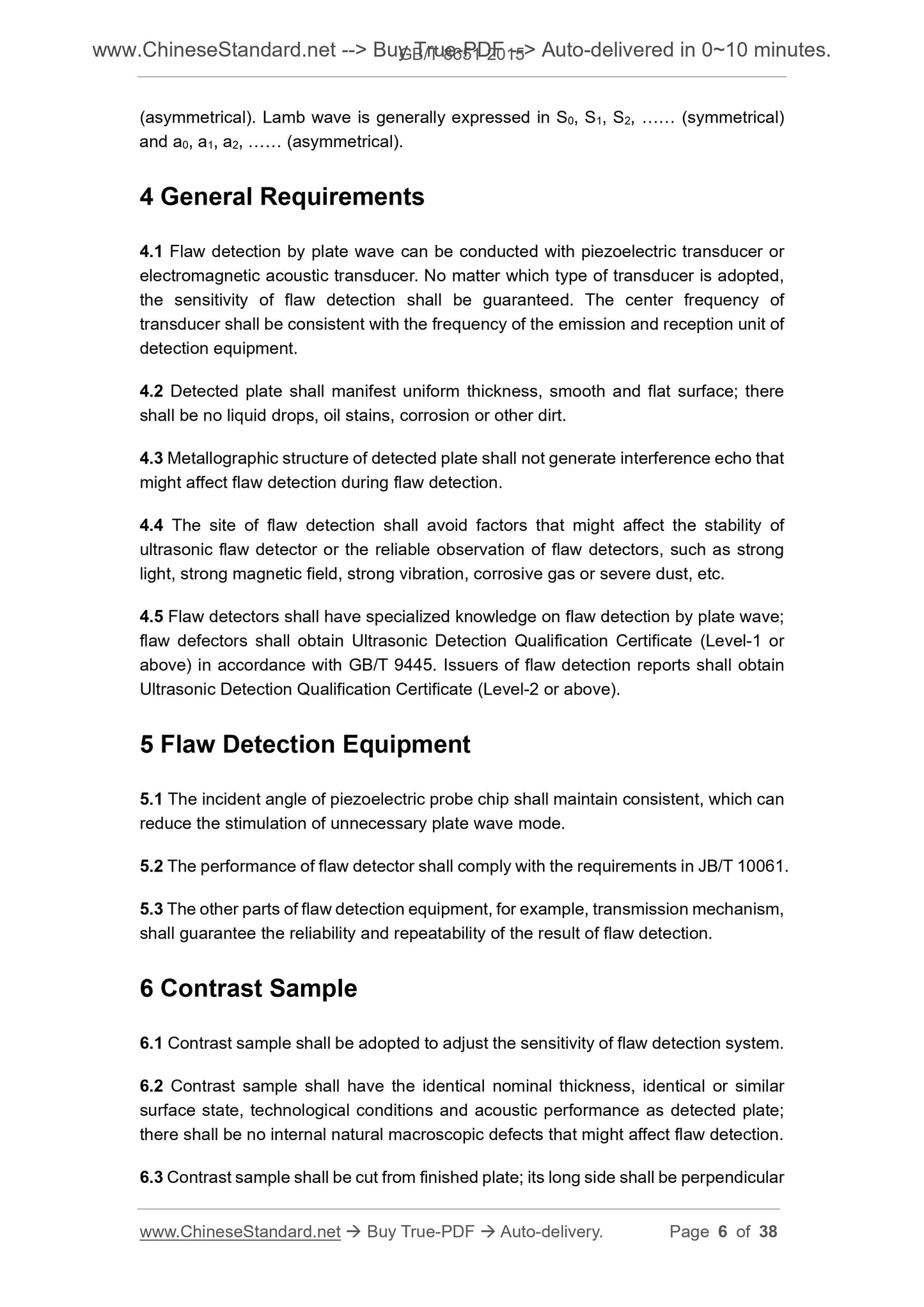
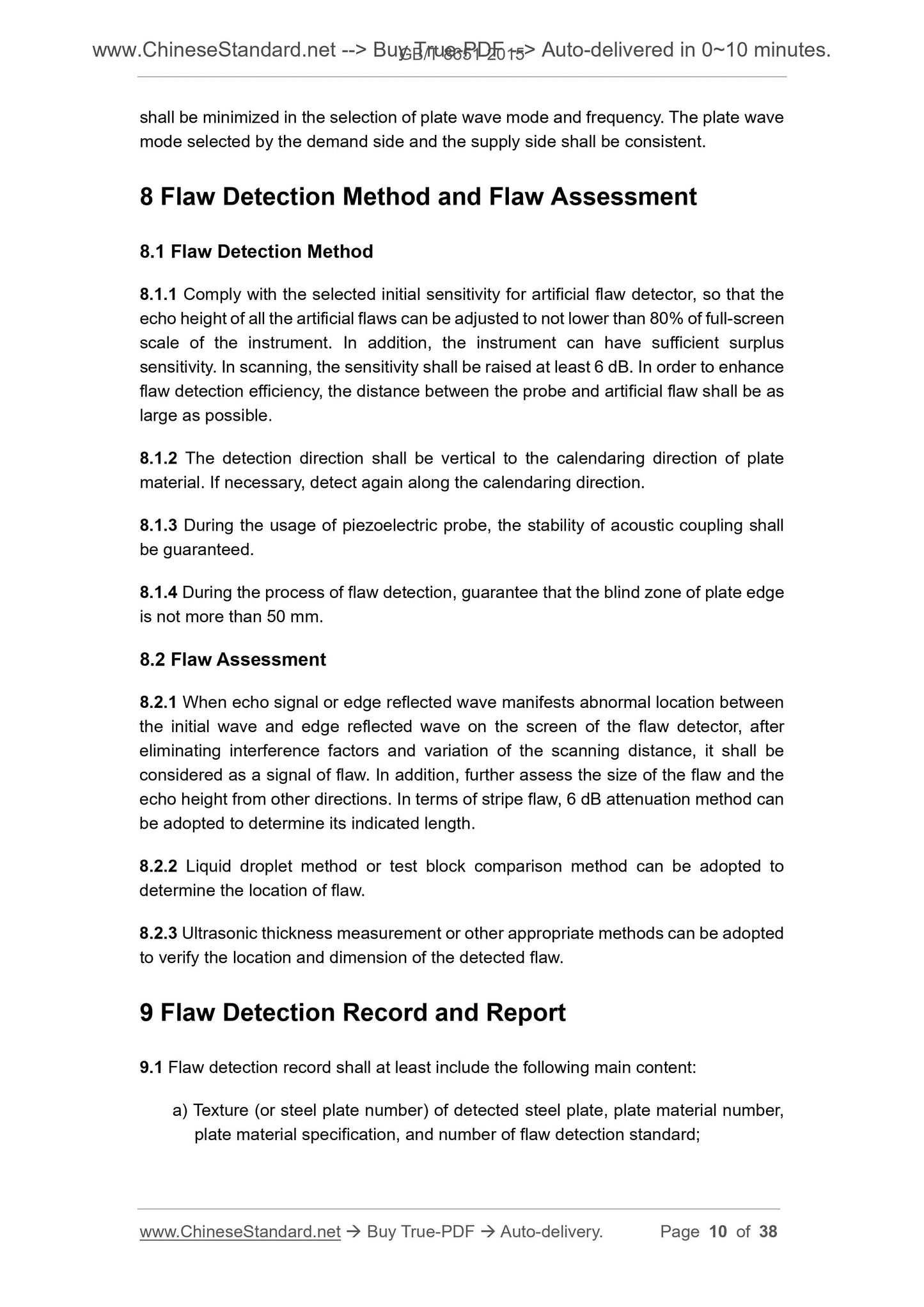