1
/
of
12
PayPal, credit cards. Download editable-PDF and invoice in 1 second!
GB/T 6519-2013 English PDF (GB/T6519-2013)
GB/T 6519-2013 English PDF (GB/T6519-2013)
Regular price
$430.00
Regular price
Sale price
$430.00
Unit price
/
per
Shipping calculated at checkout.
Couldn't load pickup availability
GB/T 6519-2013: Ultrasonic inspection of wrought aluminium and magnesium alloy products
Delivery: 9 seconds. Download (and Email) true-PDF + Invoice.
Newer version: (Replacing this standard) GB/T 6519-2024
Get Quotation: Click GB/T 6519-2013 (Self-service in 1-minute)
Newer / historical versions: GB/T 6519-2024
Preview True-PDF (Reload/Scroll-down if blank)
Delivery: 9 seconds. Download (and Email) true-PDF + Invoice.
Newer version: (Replacing this standard) GB/T 6519-2024
Get Quotation: Click GB/T 6519-2013 (Self-service in 1-minute)
Newer / historical versions: GB/T 6519-2024
Preview True-PDF (Reload/Scroll-down if blank)
Share

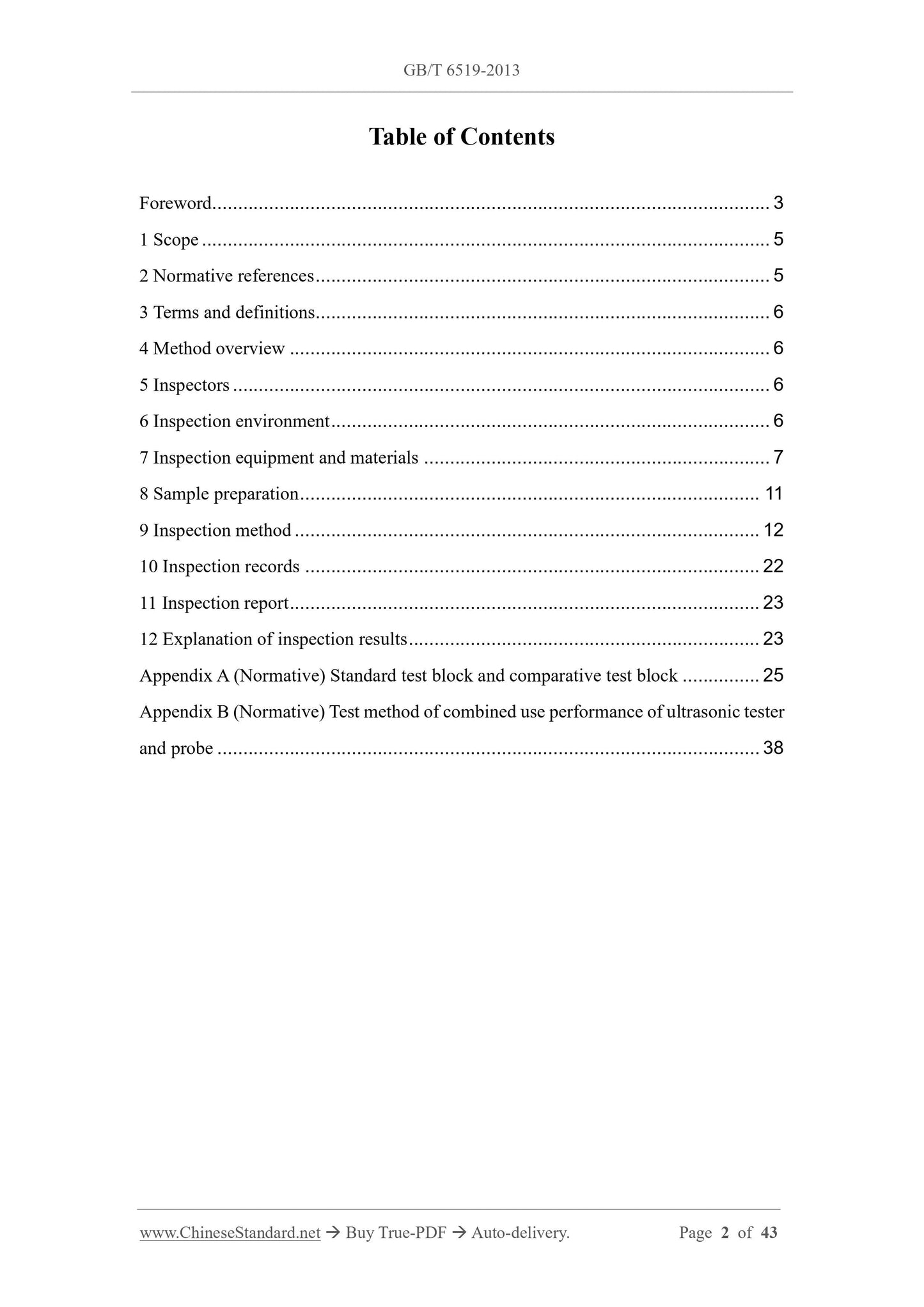
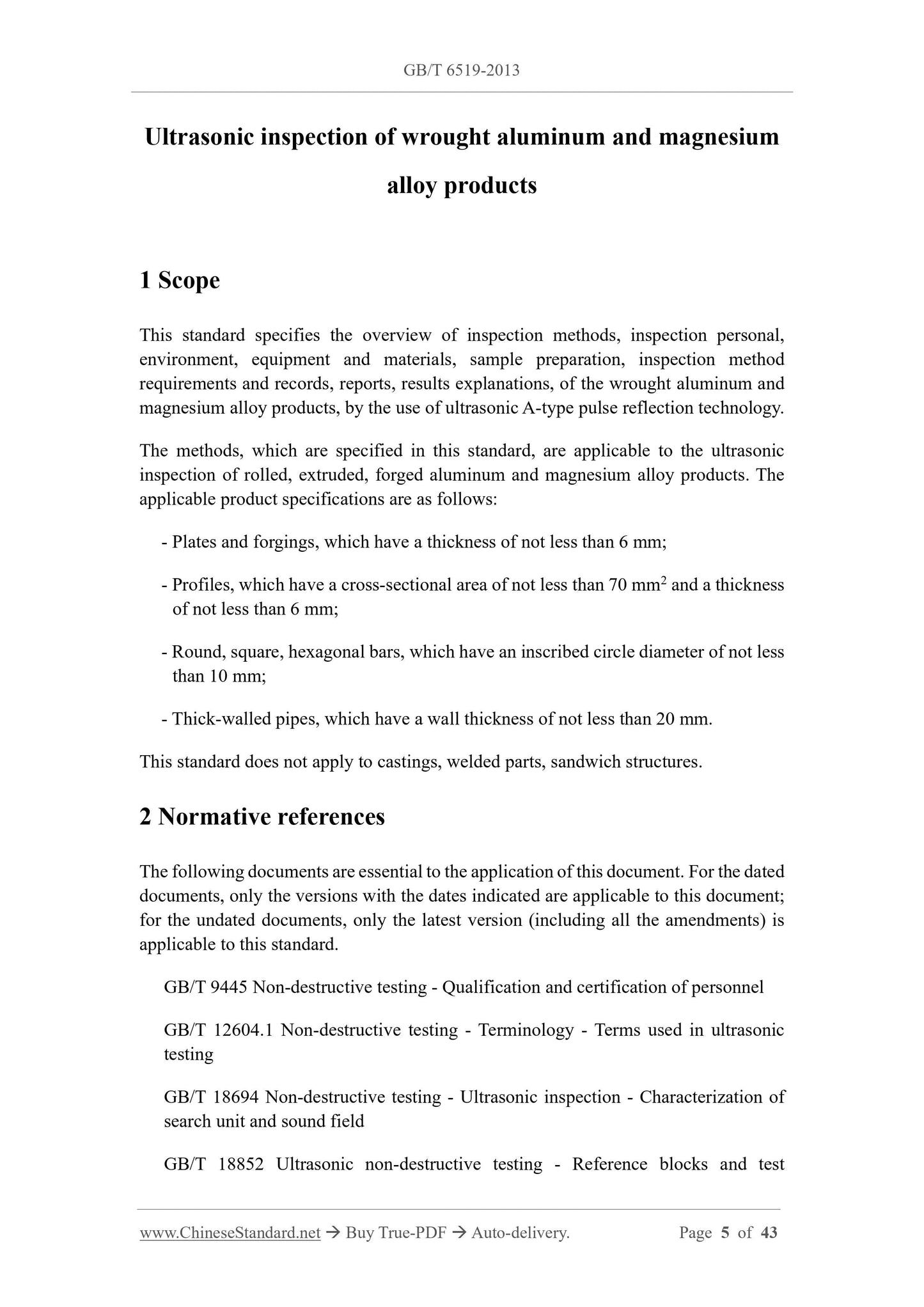

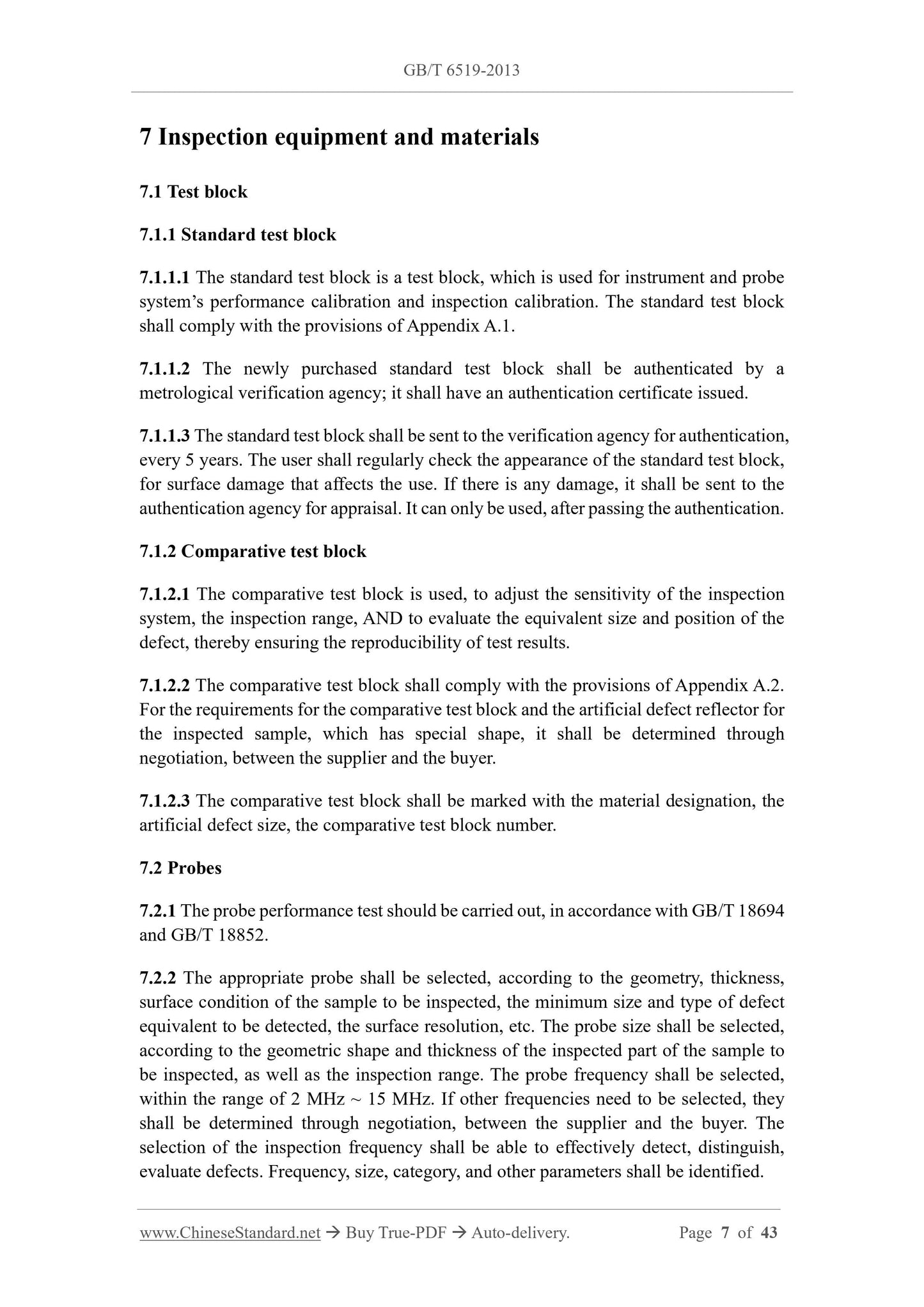
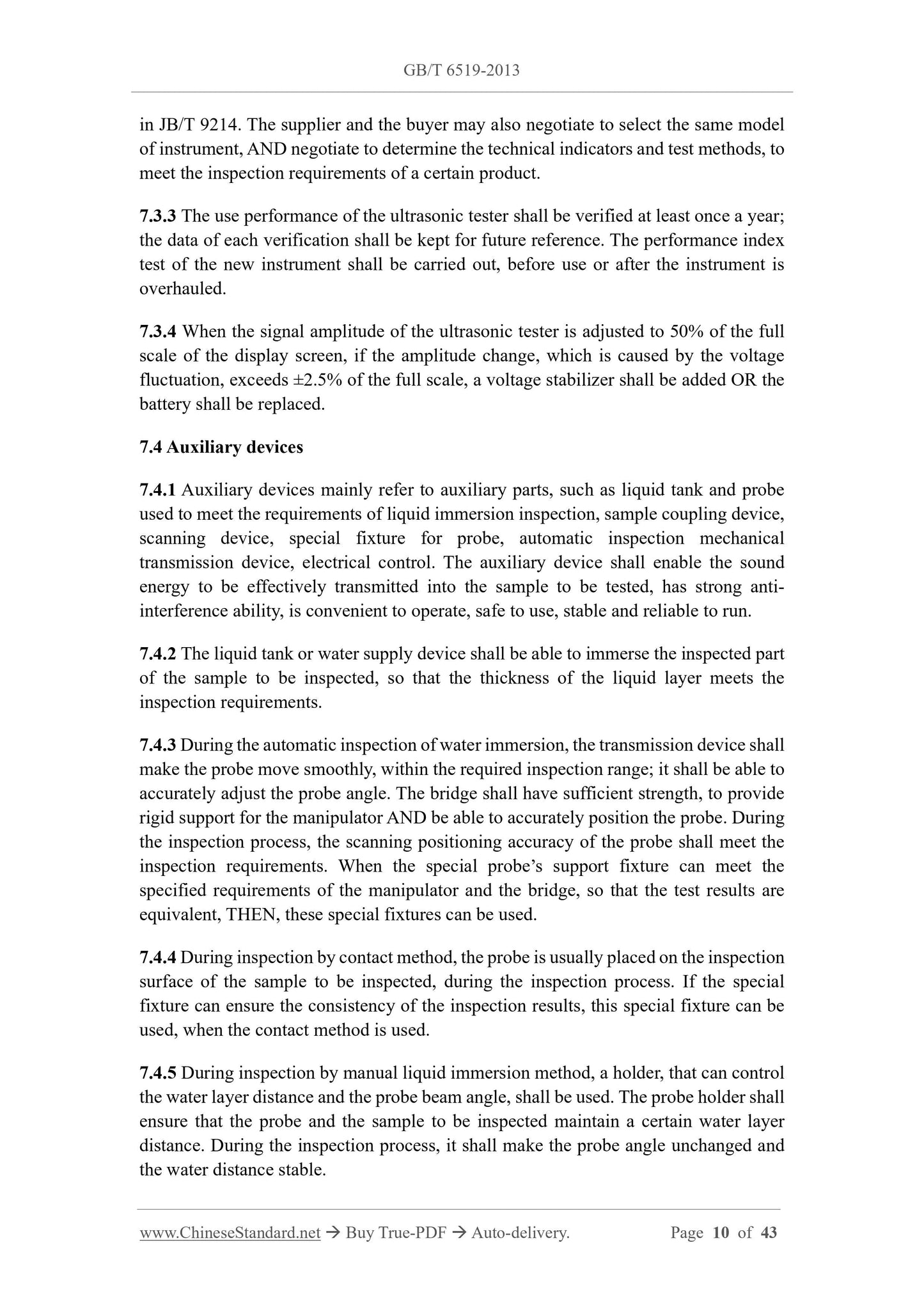




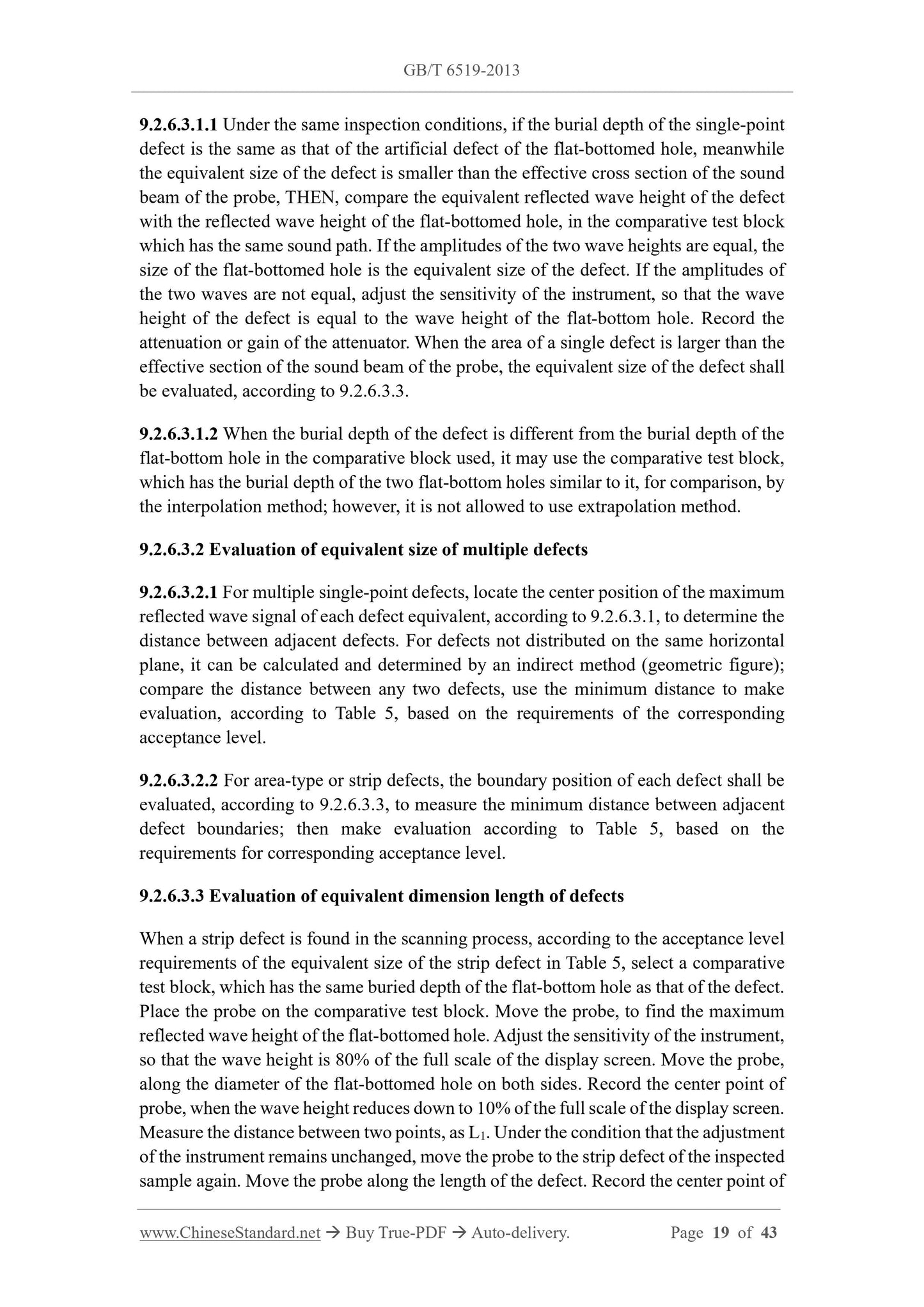
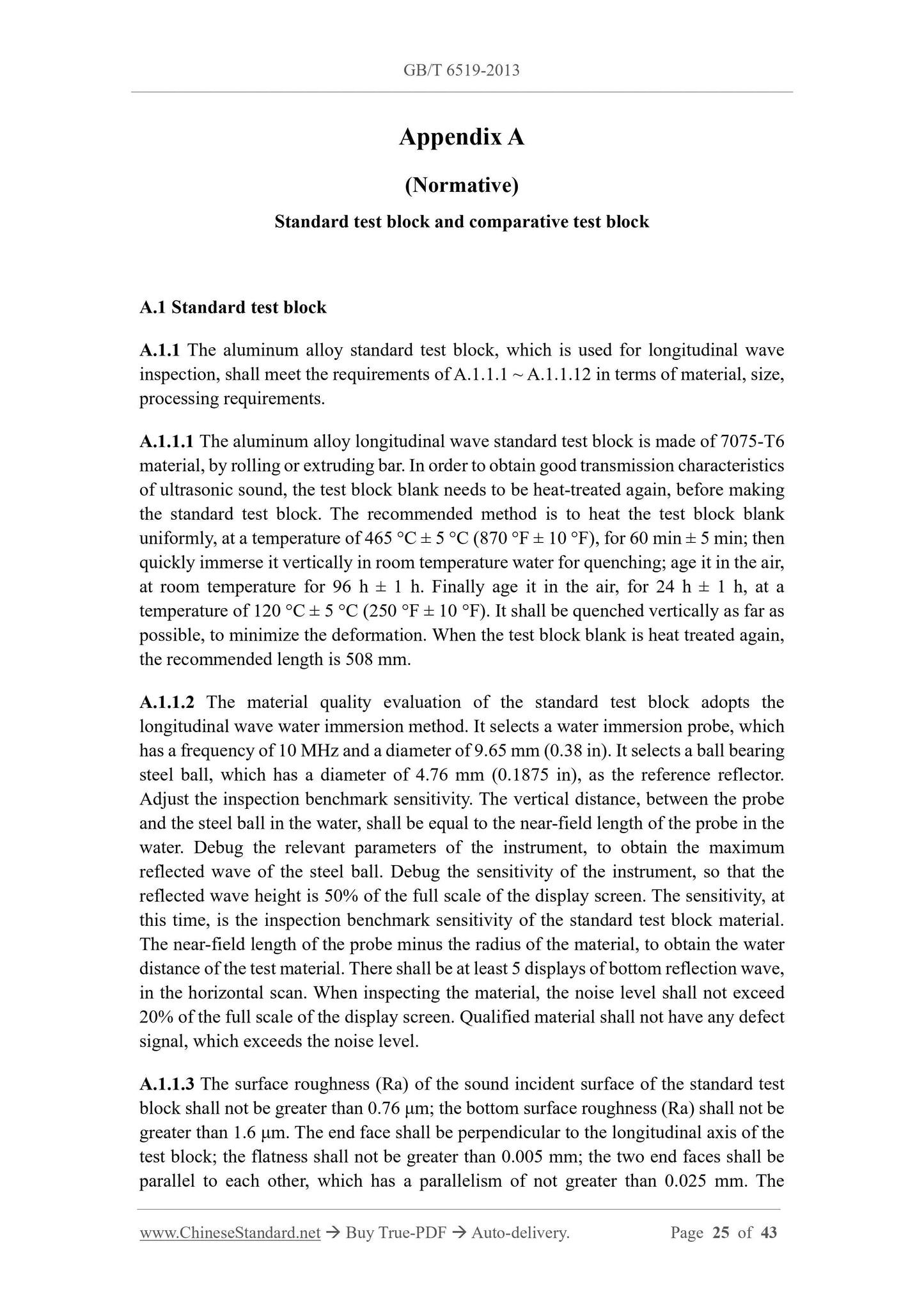