1
/
of
9
PayPal, credit cards. Download editable-PDF & invoice in 1 second!
GB/T 5686.5-2008 English PDF (GB/T5686.5-2008)
GB/T 5686.5-2008 English PDF (GB/T5686.5-2008)
Regular price
$180.00
Regular price
Sale price
$180.00
Unit price
/
per
Shipping calculated at checkout.
Couldn't load pickup availability
GB/T 5686.5-2008: Ferromanganese, ferromanganese-silicon, nitrogen-bearing ferromanganese and manganese metal - Determination of carbon content - The infrared absorption method, the gasometric method, the gravimetric and the coulometric method
Delivery: 9 seconds. Download (and Email) true-PDF + Invoice.
Newer version: (Replacing this standard) GB/T 5686.5-2023
Get Quotation: Click GB/T 5686.5-2008 (Self-service in 1-minute)
Newer / historical versions: GB/T 5686.5-2023
Preview True-PDF (Reload/Scroll-down if blank)
Delivery: 9 seconds. Download (and Email) true-PDF + Invoice.
Newer version: (Replacing this standard) GB/T 5686.5-2023
Get Quotation: Click GB/T 5686.5-2008 (Self-service in 1-minute)
Newer / historical versions: GB/T 5686.5-2023
Preview True-PDF (Reload/Scroll-down if blank)
Share
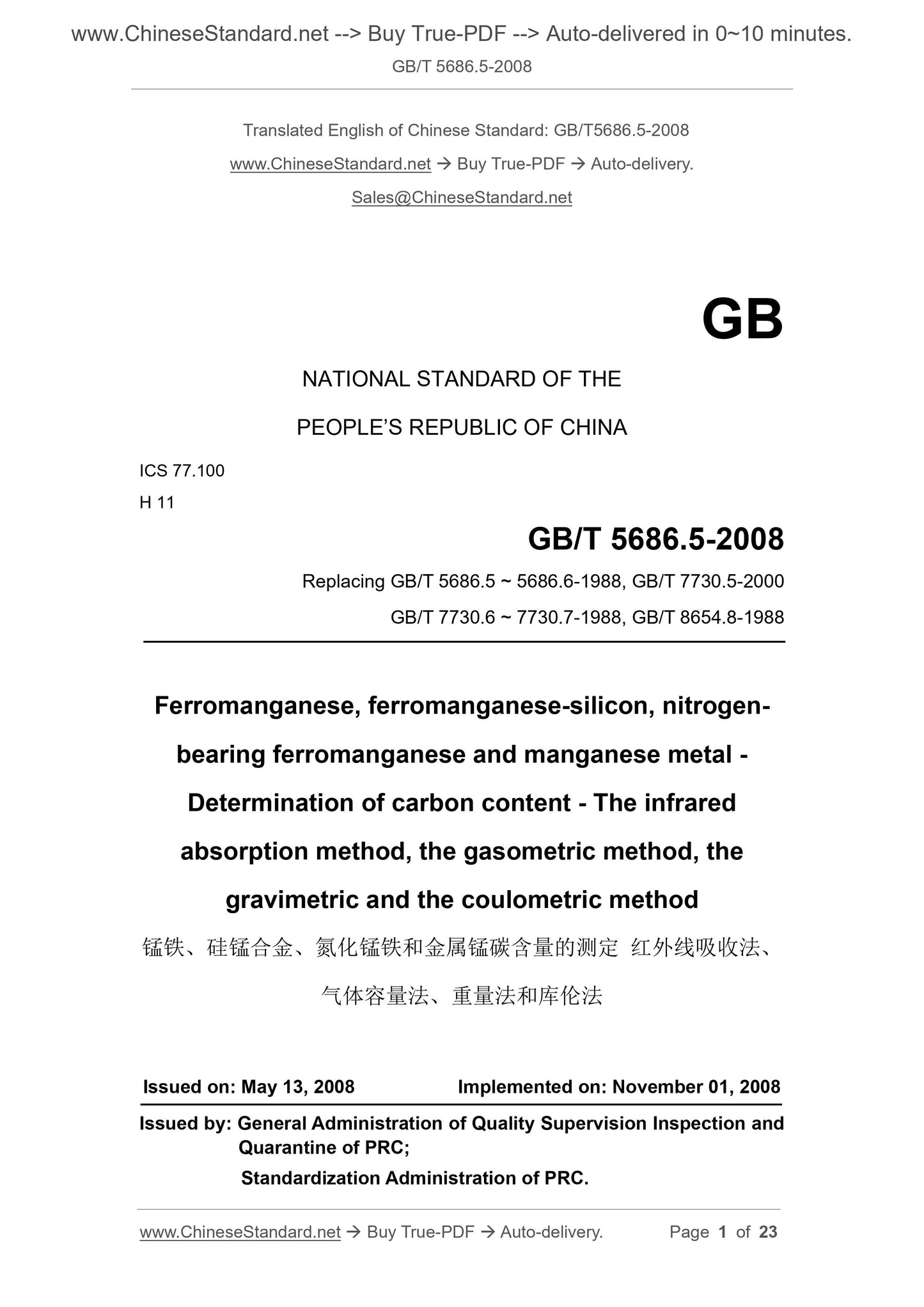
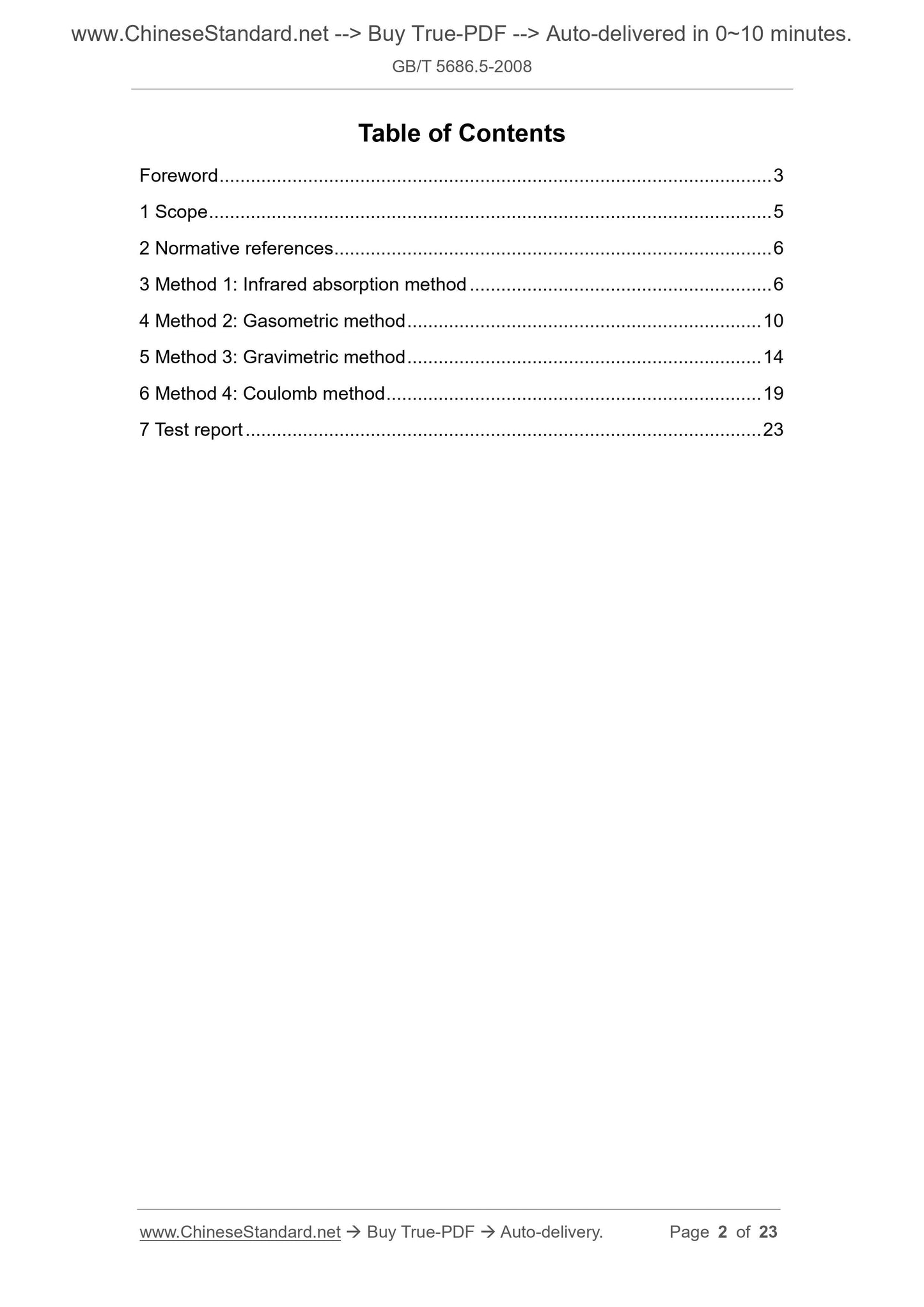
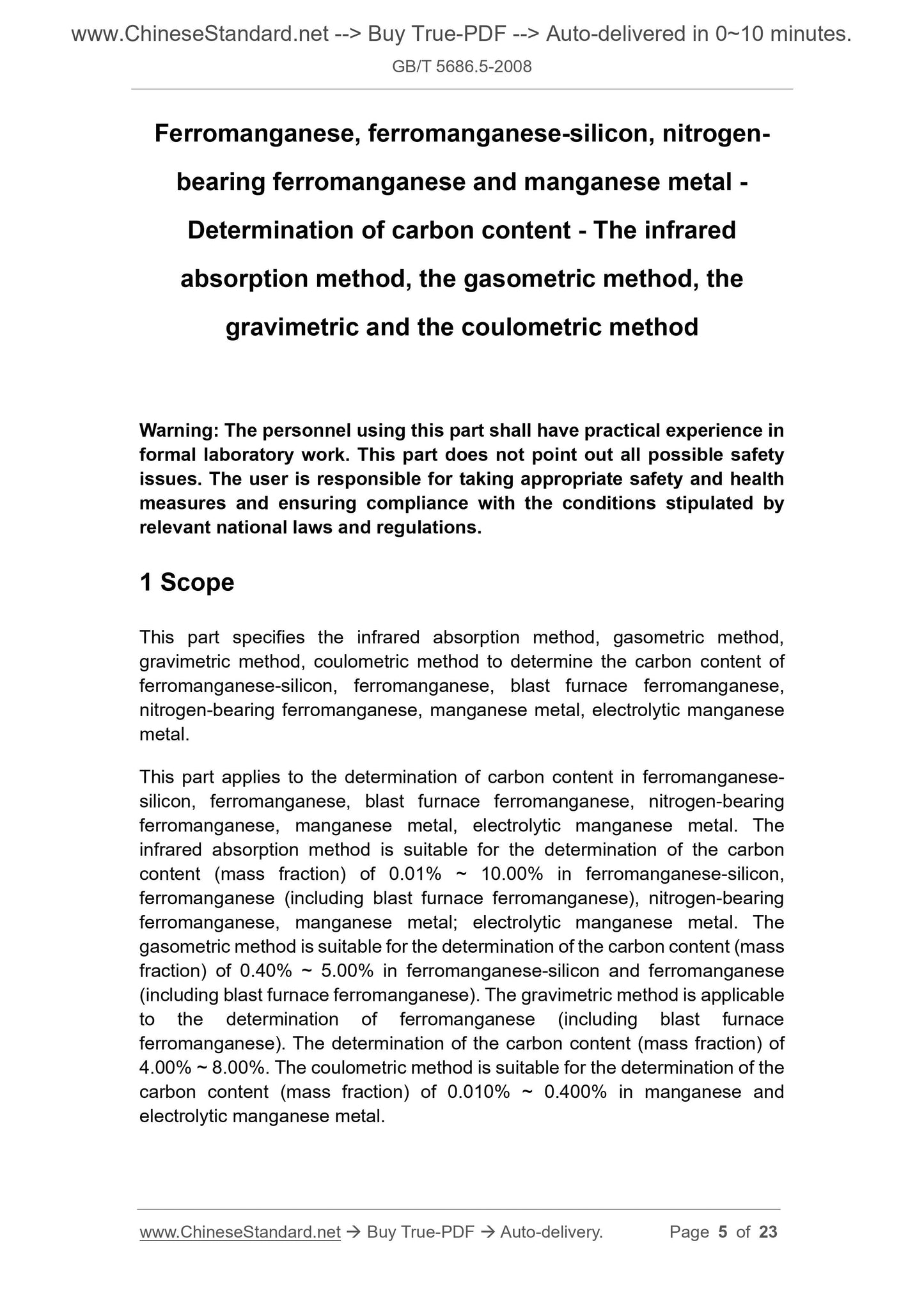
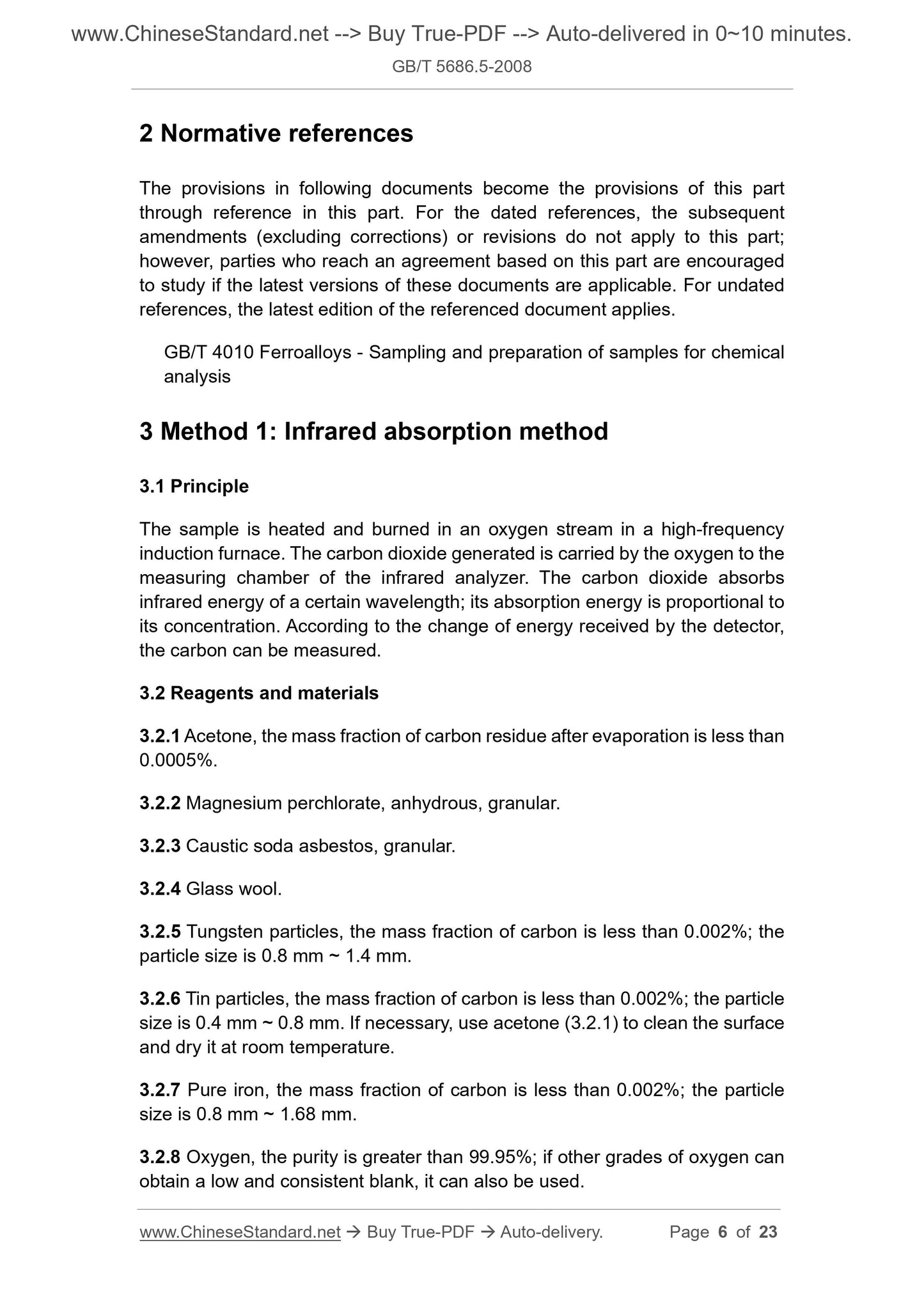
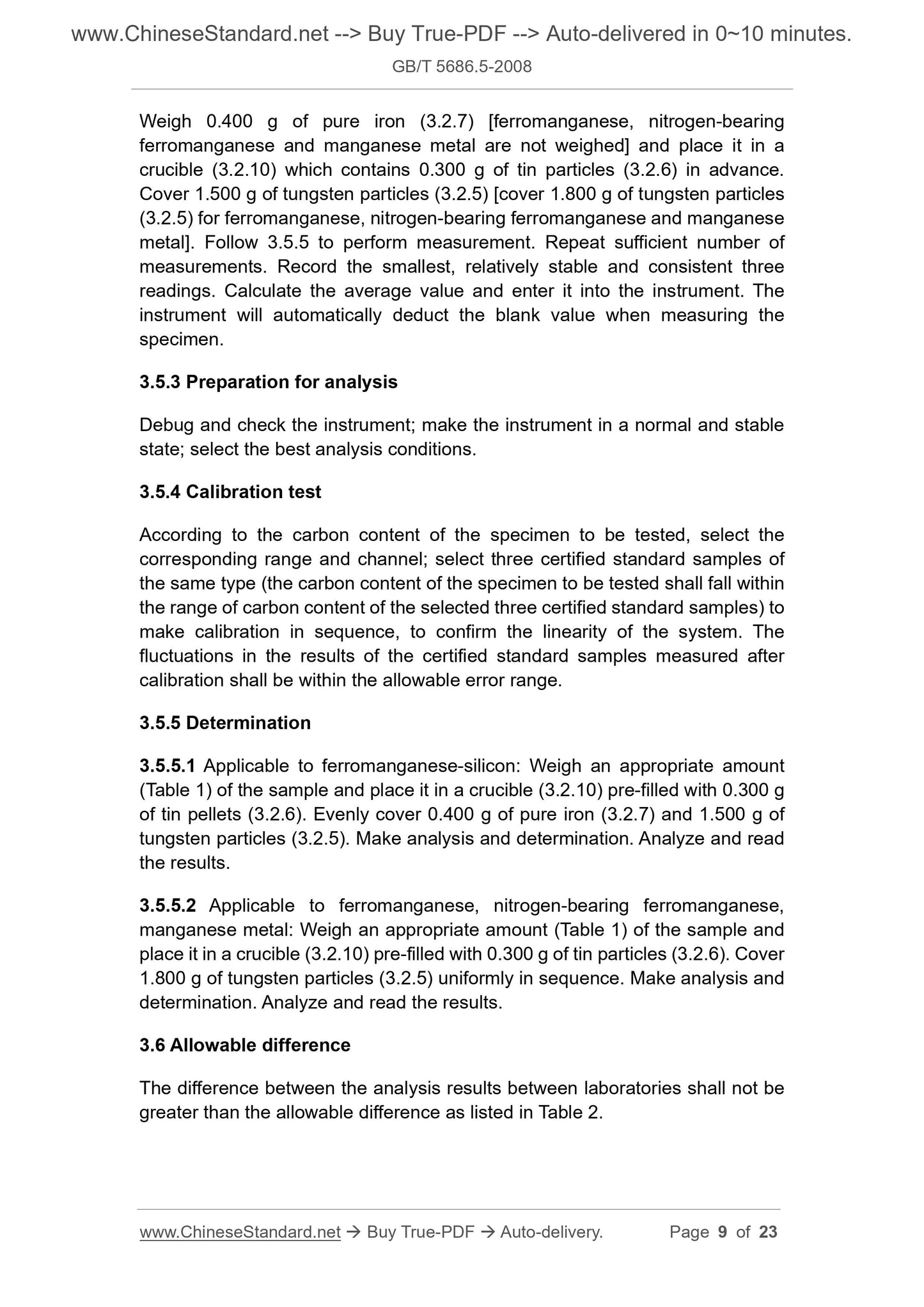
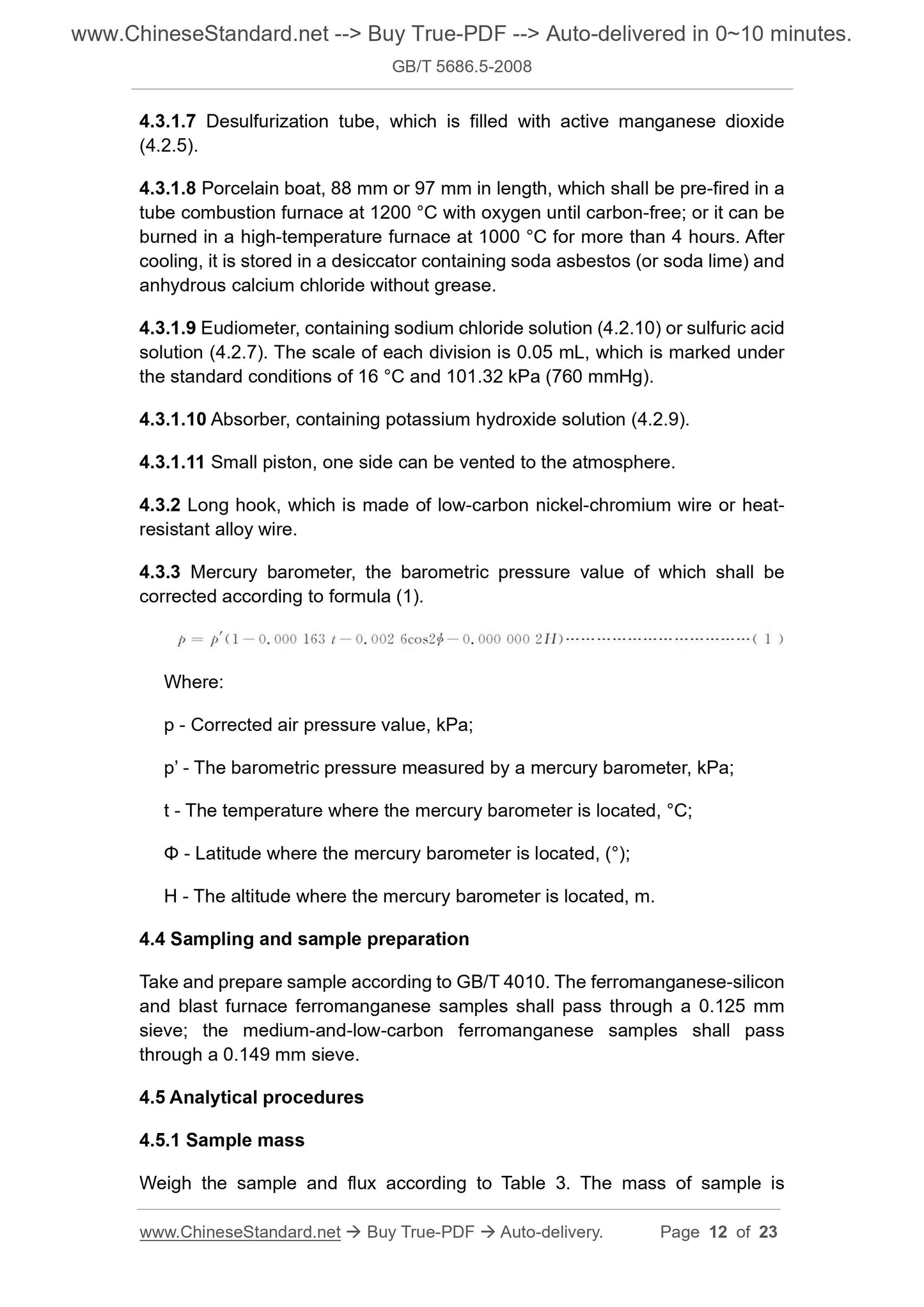
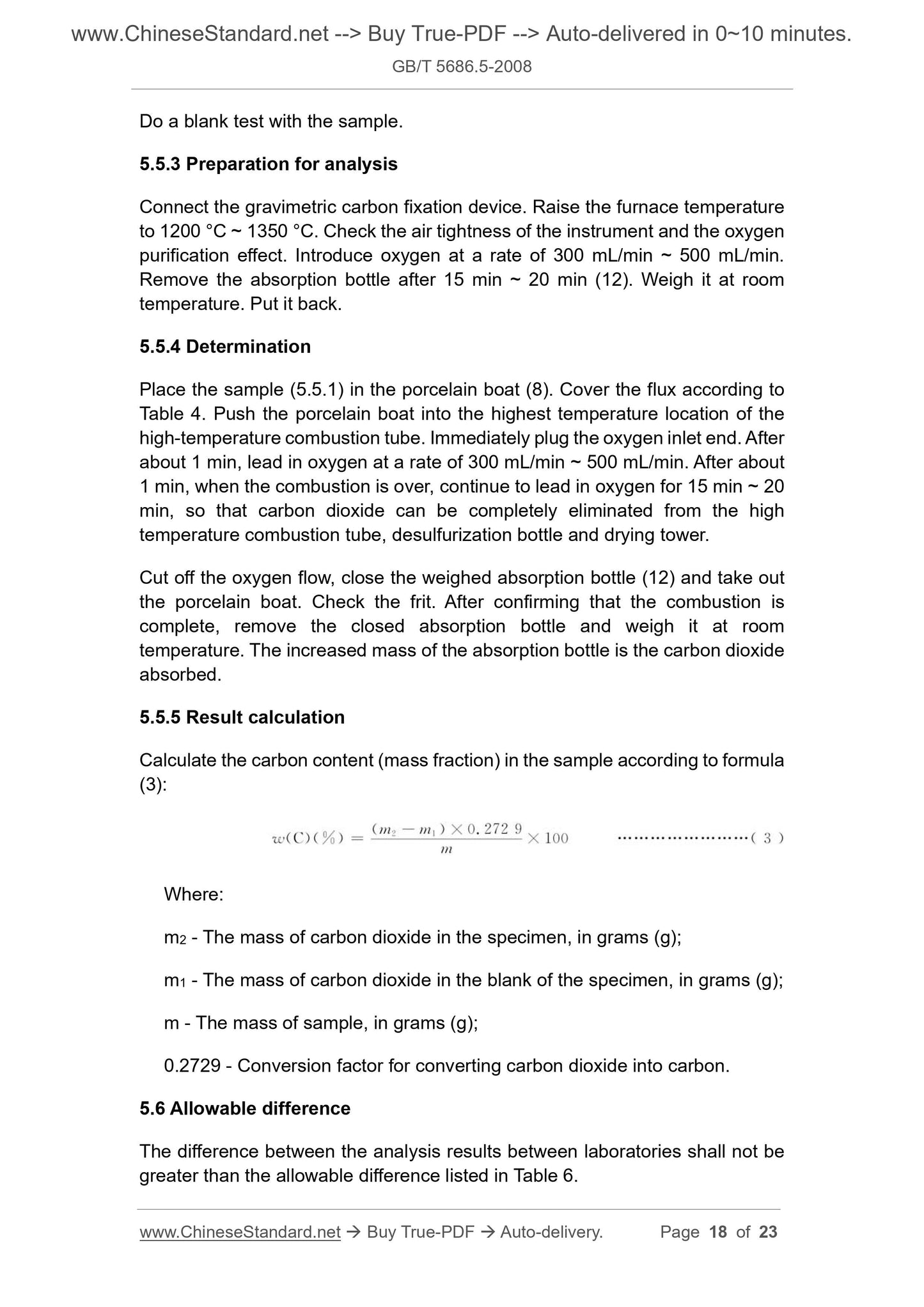
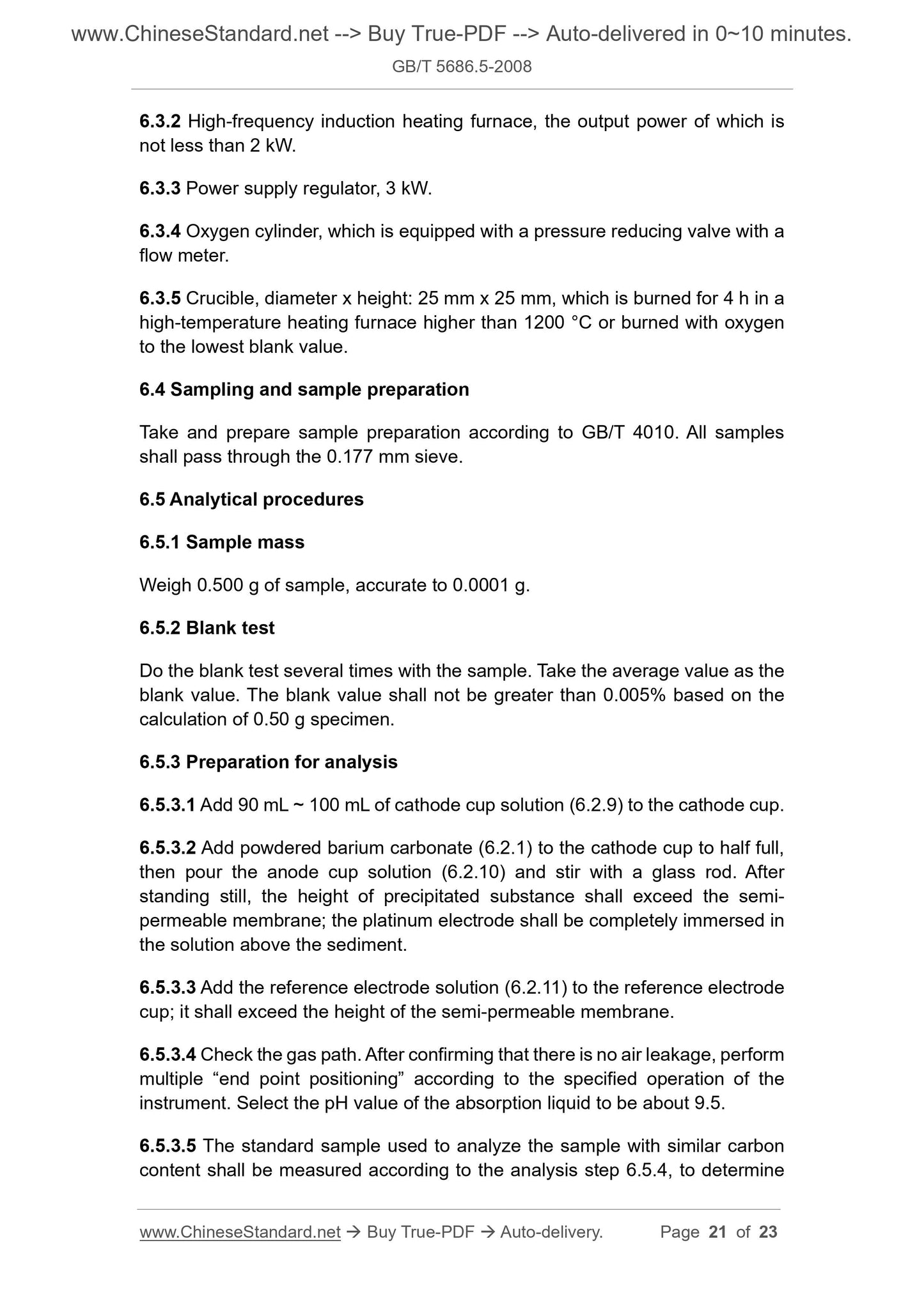
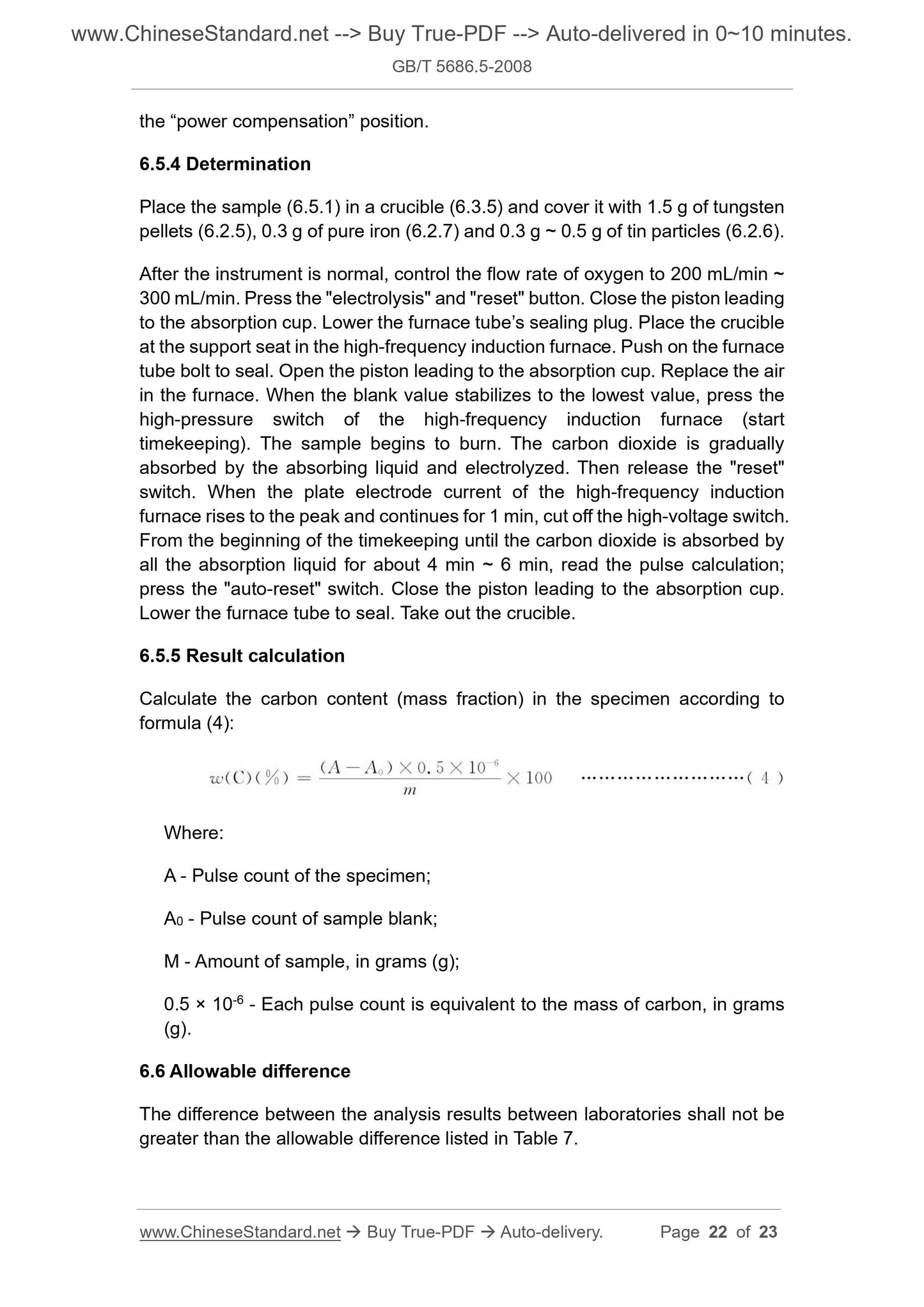