1
/
of
6
www.ChineseStandard.us -- Field Test Asia Pte. Ltd.
GB/T 38804-2020 English PDF (GB/T38804-2020)
GB/T 38804-2020 English PDF (GB/T38804-2020)
Regular price
$165.00
Regular price
Sale price
$165.00
Unit price
/
per
Shipping calculated at checkout.
Couldn't load pickup availability
GB/T 38804-2020: Test method for oxidation of metallic materials exposed in high-temperature steam
Delivery: 9 seconds. Download (and Email) true-PDF + Invoice.
Get Quotation: Click GB/T 38804-2020 (Self-service in 1-minute)
Newer / historical versions: GB/T 38804-2020
Preview True-PDF (Reload/Scroll-down if blank)
Delivery: 9 seconds. Download (and Email) true-PDF + Invoice.
Get Quotation: Click GB/T 38804-2020 (Self-service in 1-minute)
Newer / historical versions: GB/T 38804-2020
Preview True-PDF (Reload/Scroll-down if blank)
Share
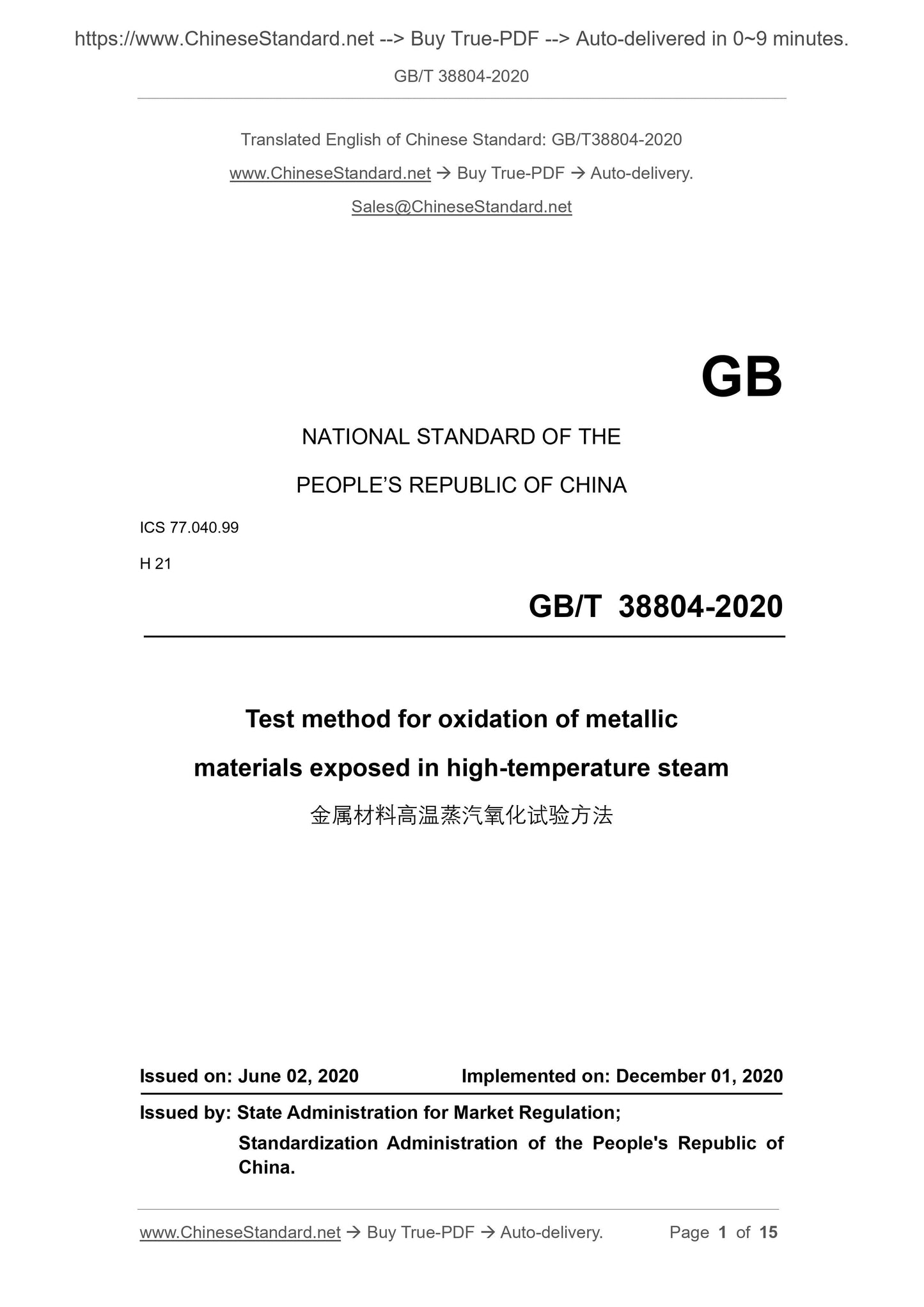
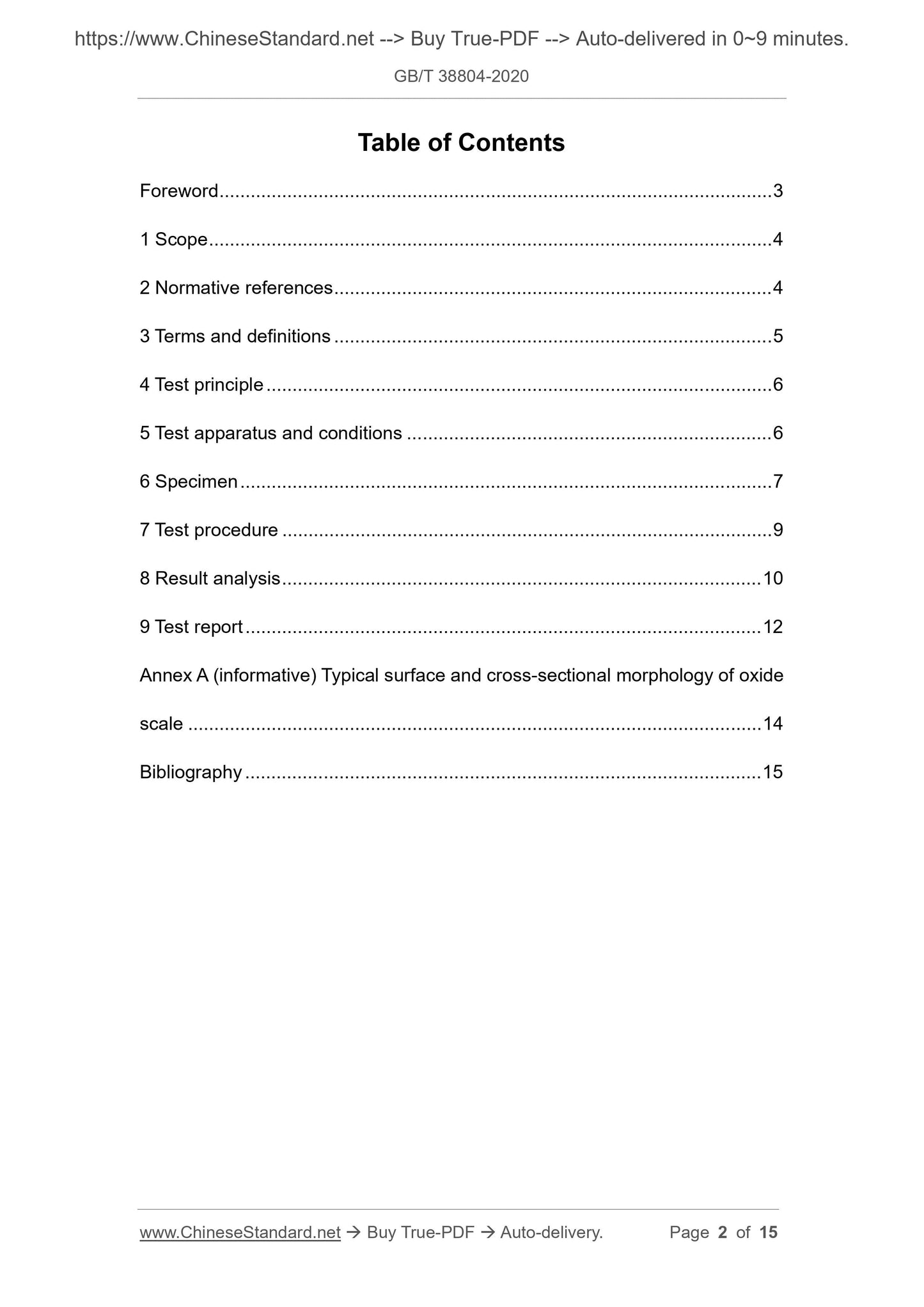

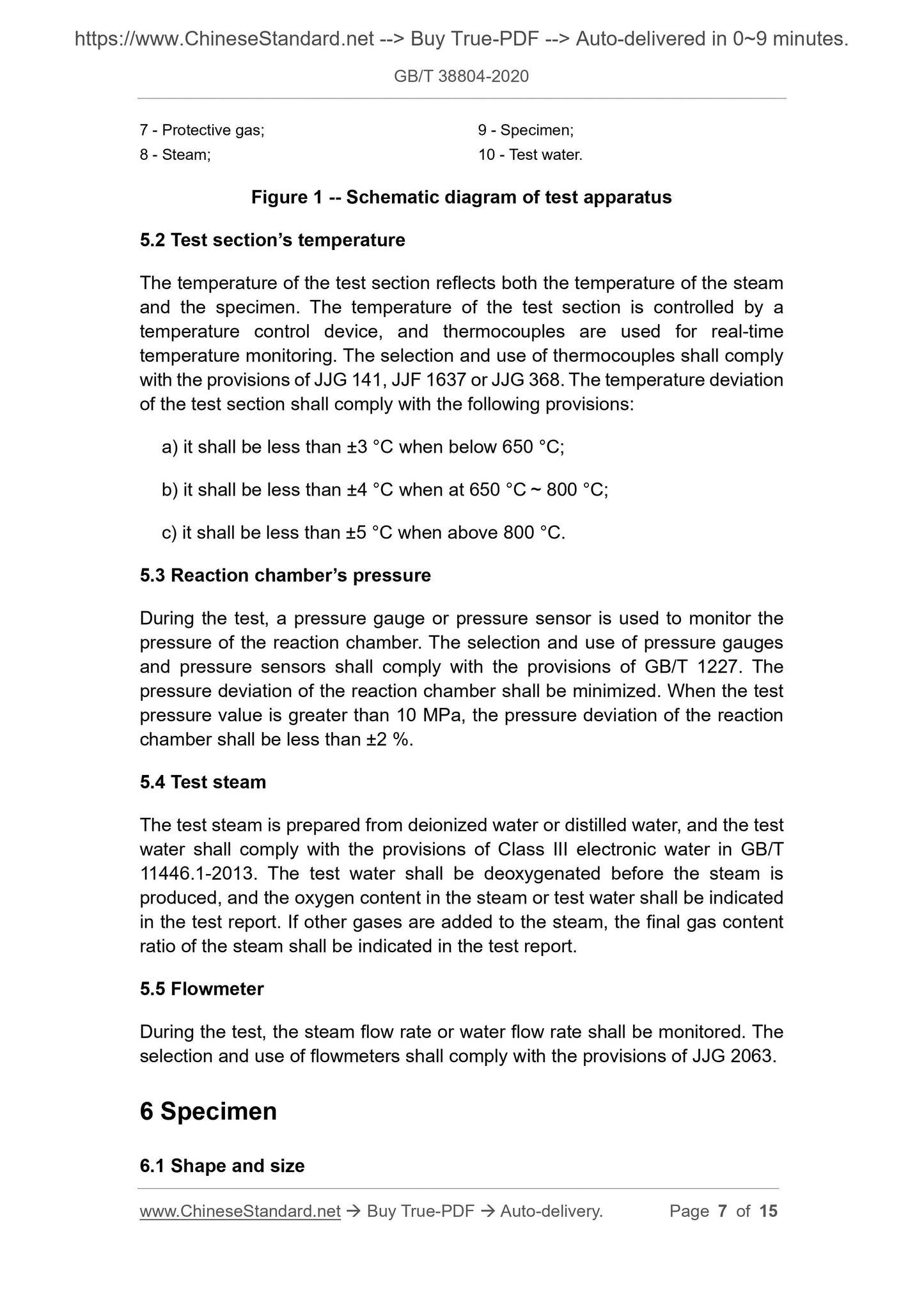
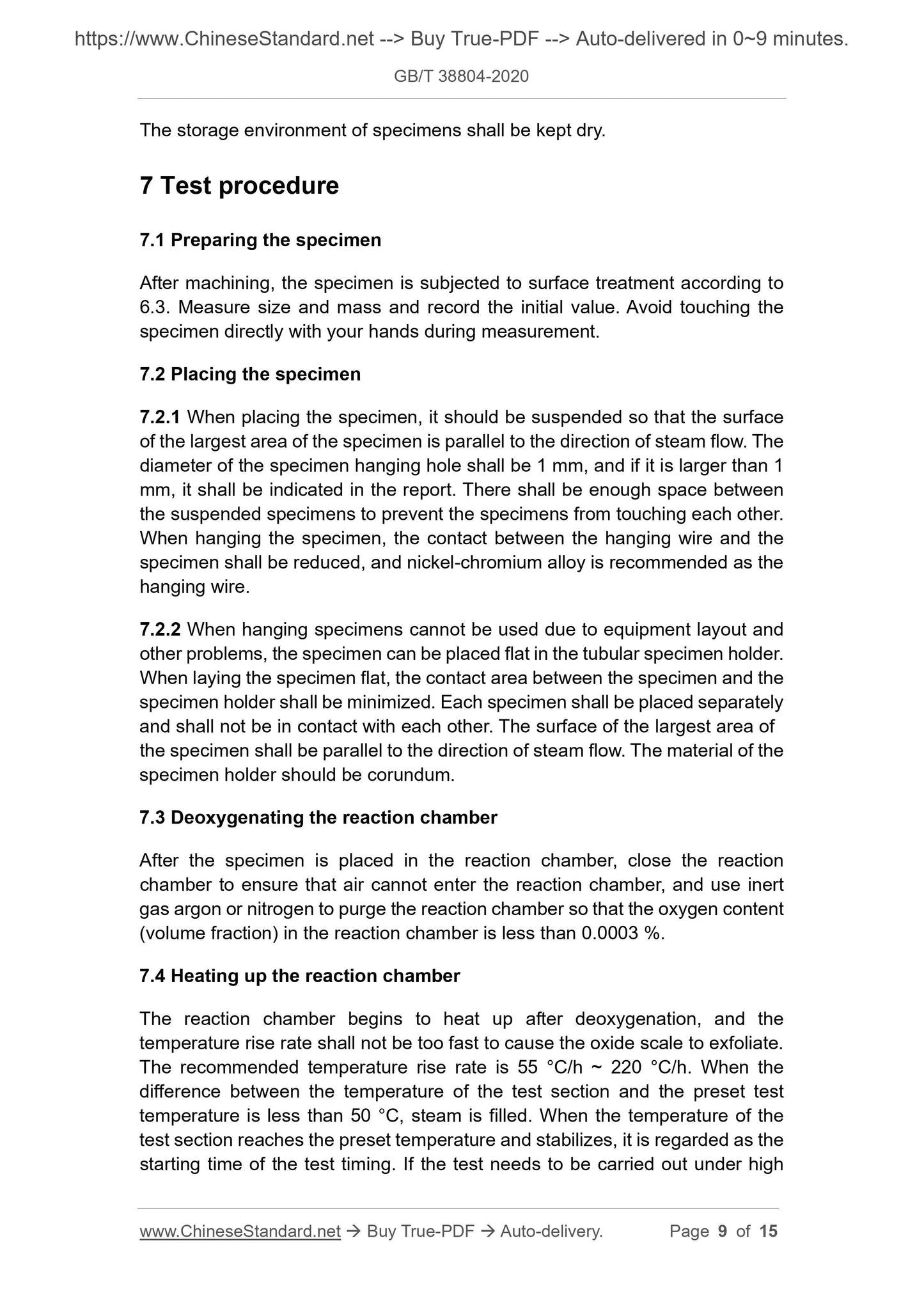
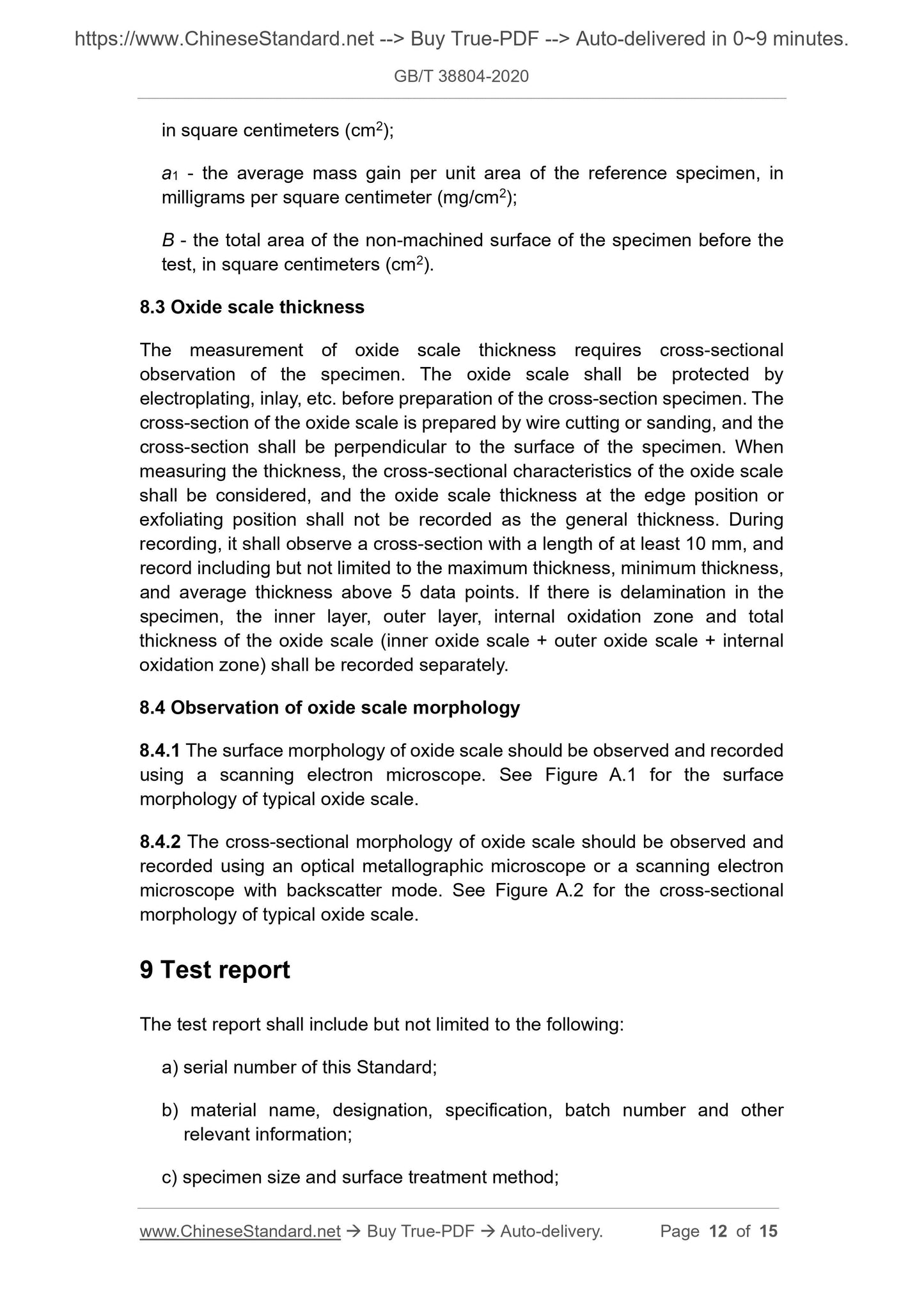