1
/
of
12
www.ChineseStandard.us -- Field Test Asia Pte. Ltd.
GB/T 36699-2018 English PDF (GB/T36699-2018)
GB/T 36699-2018 English PDF (GB/T36699-2018)
Regular price
$455.00
Regular price
Sale price
$455.00
Unit price
/
per
Shipping calculated at checkout.
Couldn't load pickup availability
GB/T 36699-2018: Specification for liquid-fuels and gaseous-fuels burners of boilers
Delivery: 9 seconds. Download (and Email) true-PDF + Invoice.
Get Quotation: Click GB/T 36699-2018 (Self-service in 1-minute)
Newer / historical versions: GB/T 36699-2018
Preview True-PDF (Reload/Scroll-down if blank)
Delivery: 9 seconds. Download (and Email) true-PDF + Invoice.
Get Quotation: Click GB/T 36699-2018 (Self-service in 1-minute)
Newer / historical versions: GB/T 36699-2018
Preview True-PDF (Reload/Scroll-down if blank)
Share
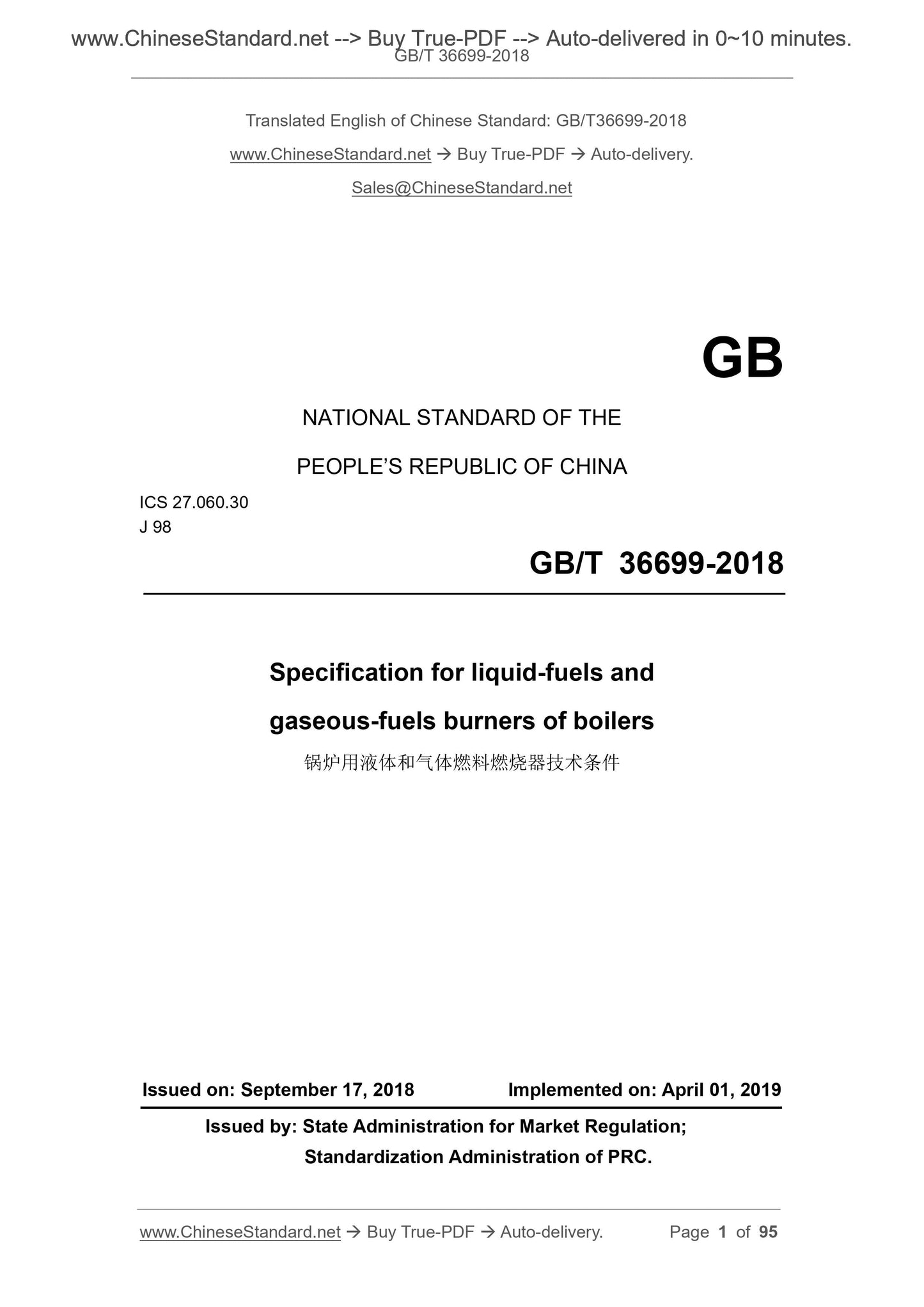
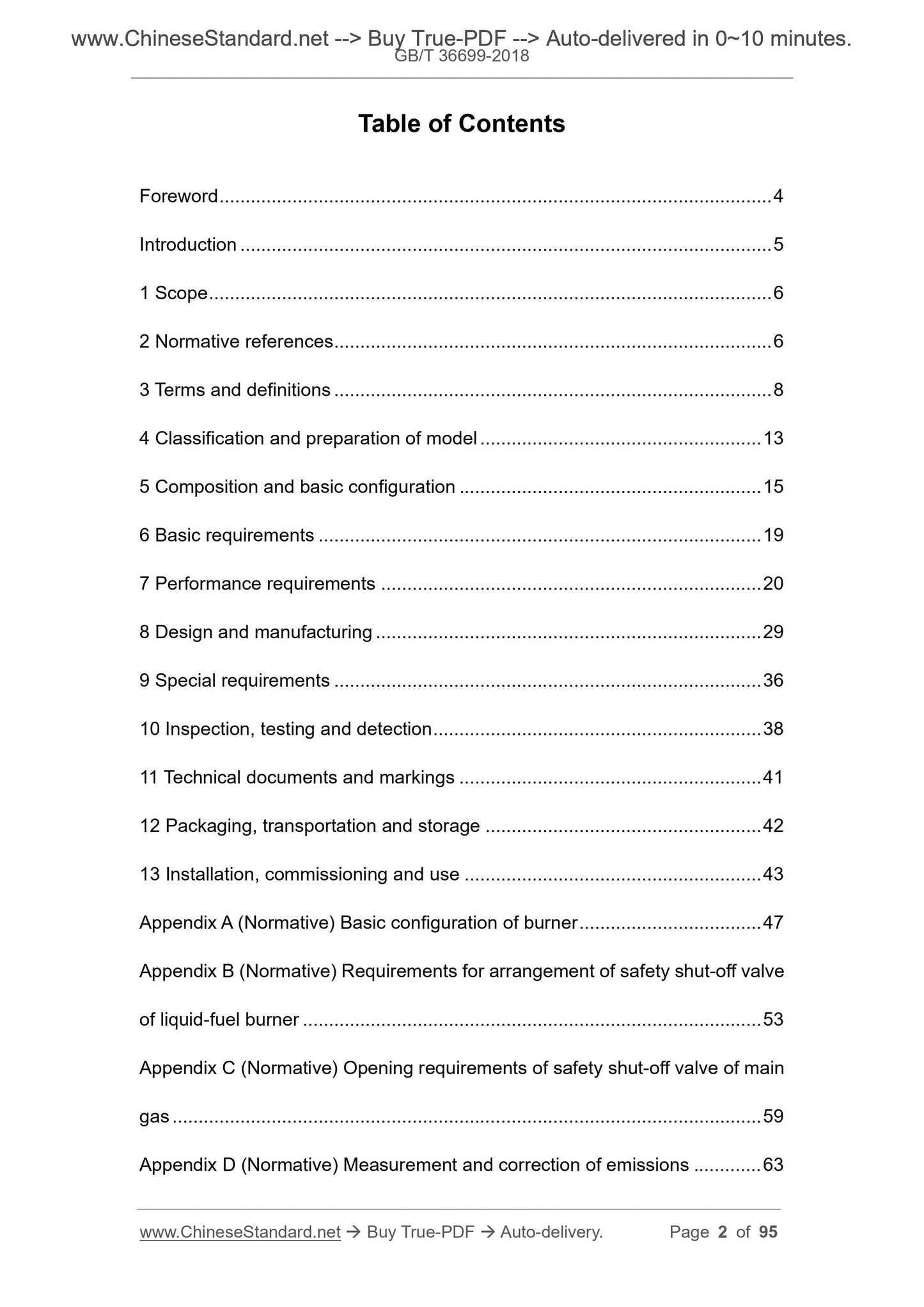
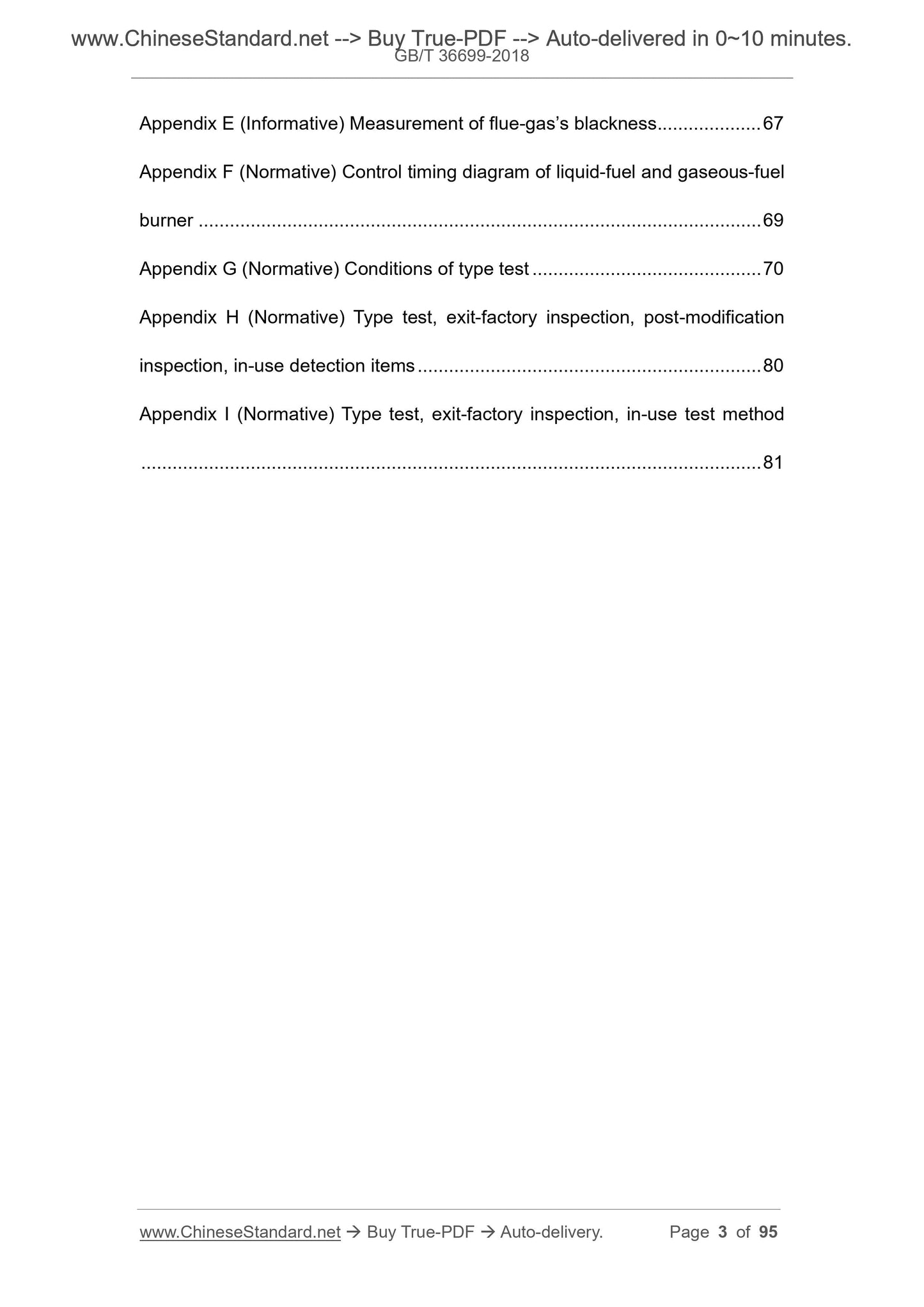
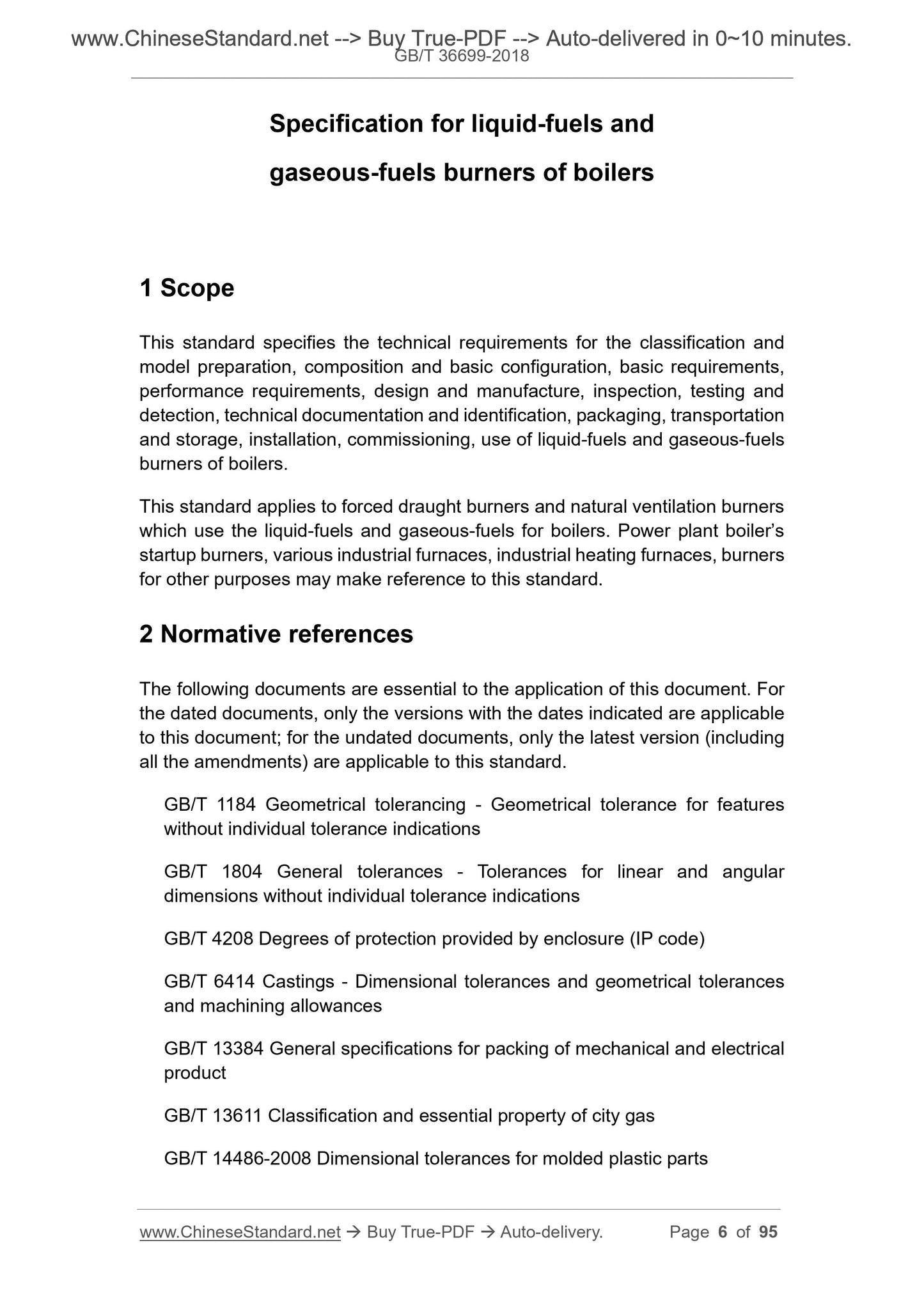
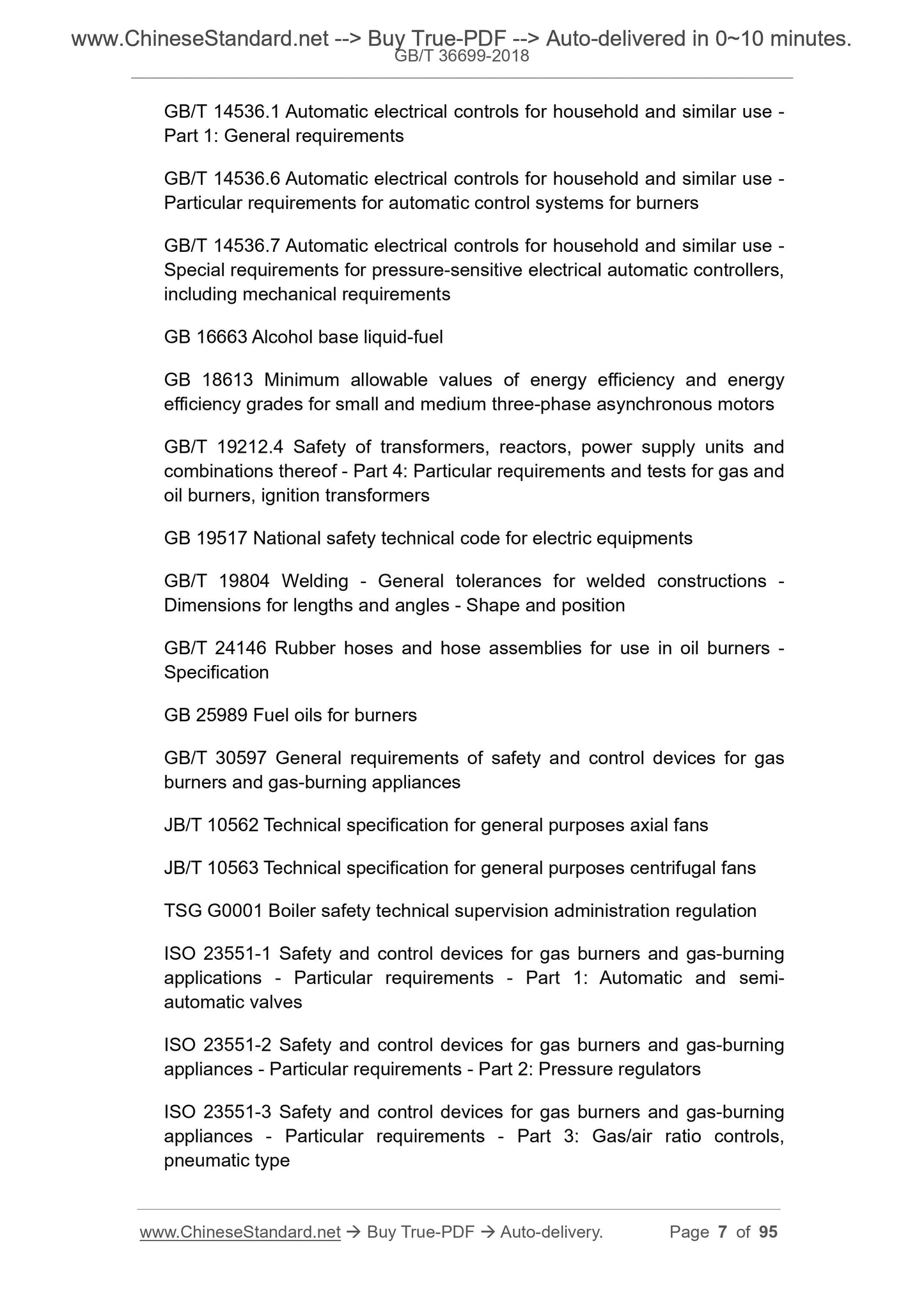
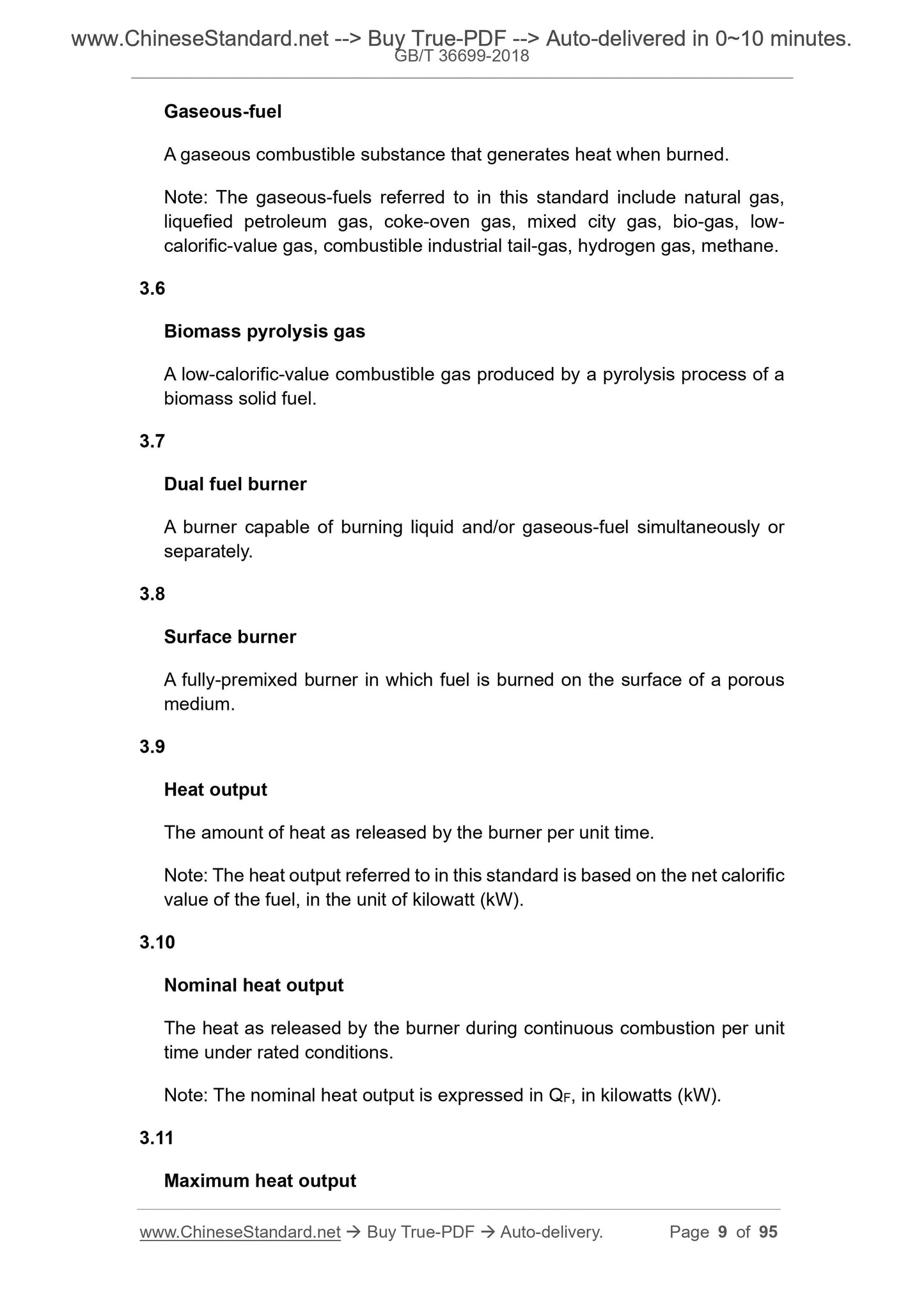
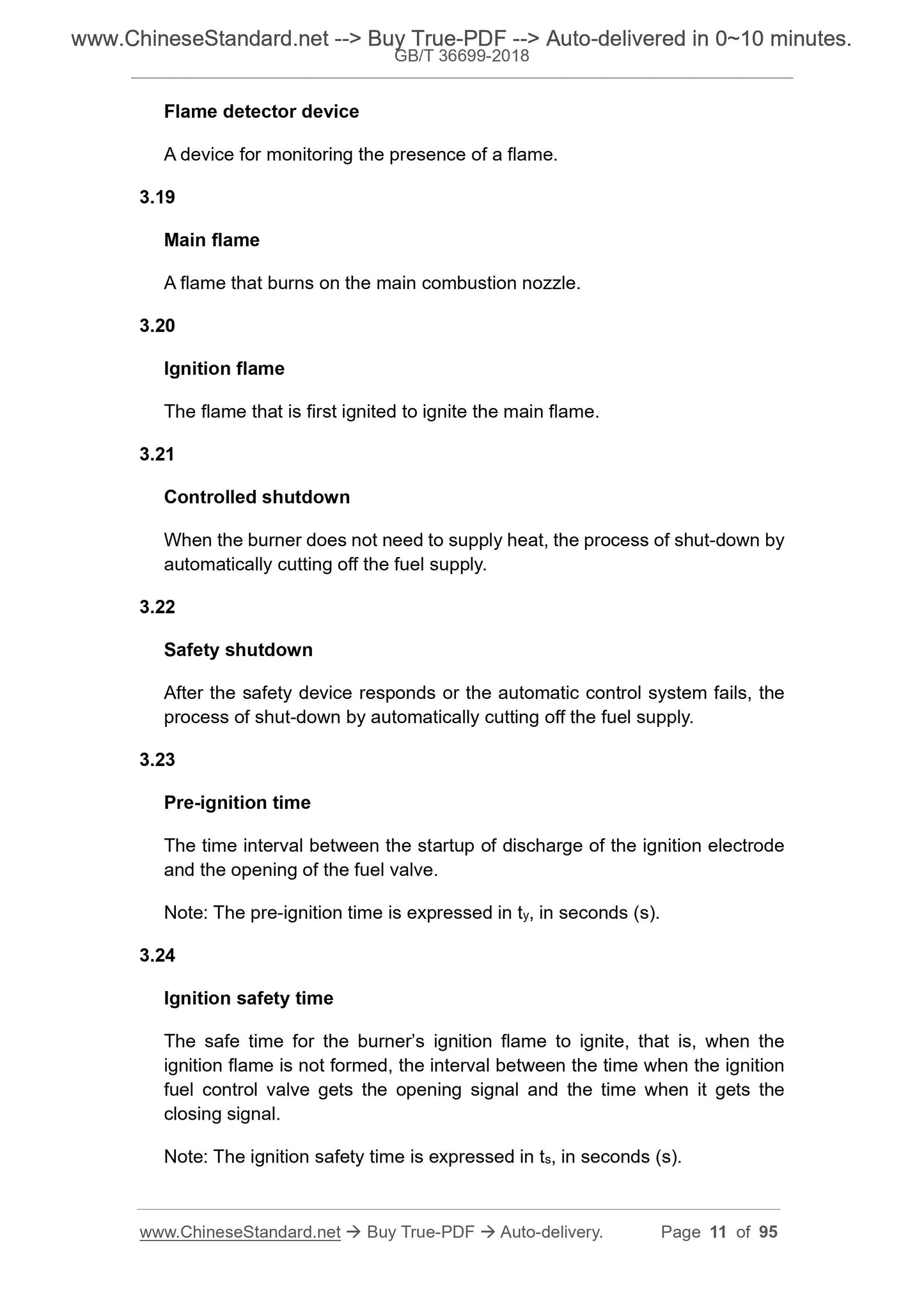
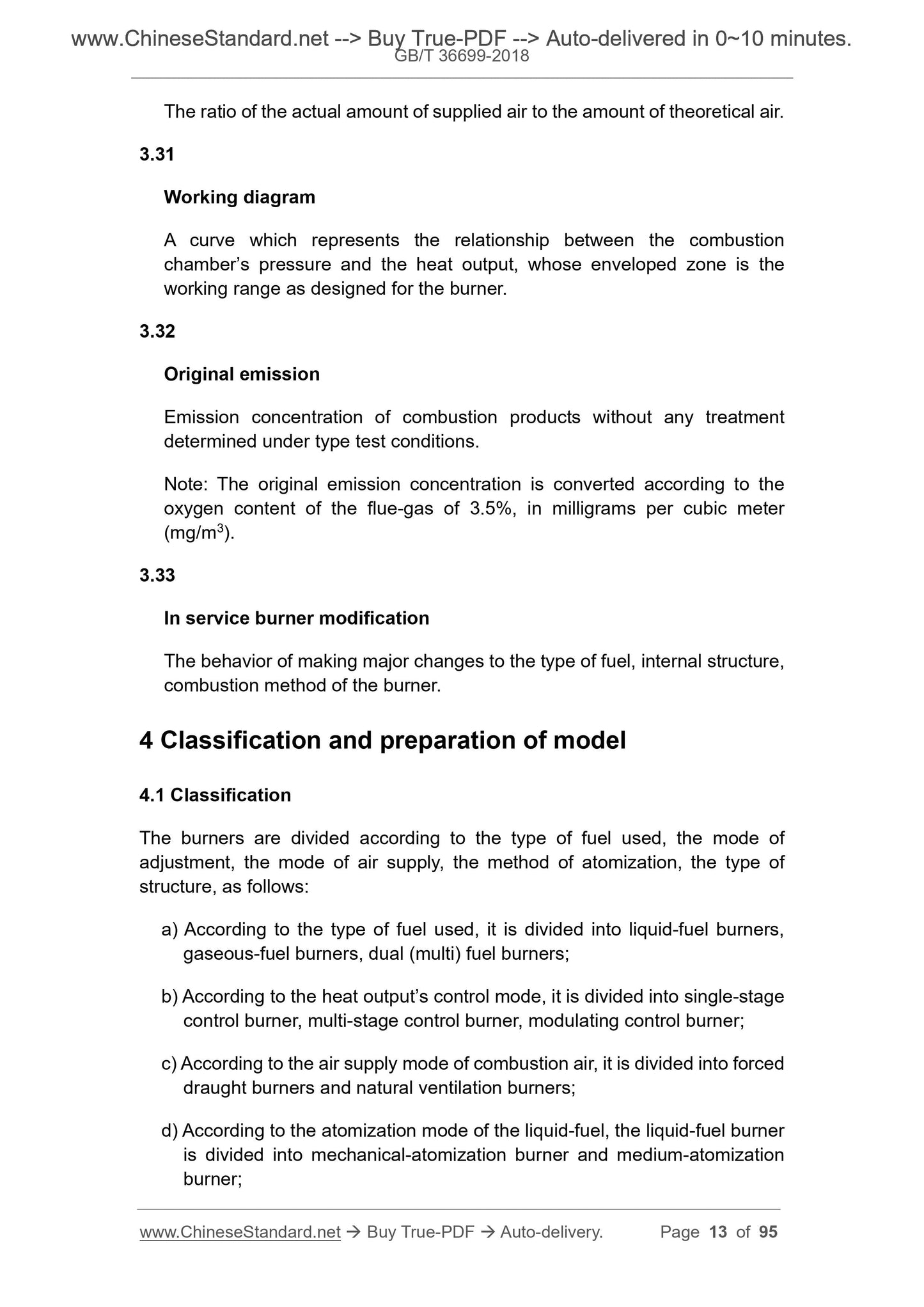
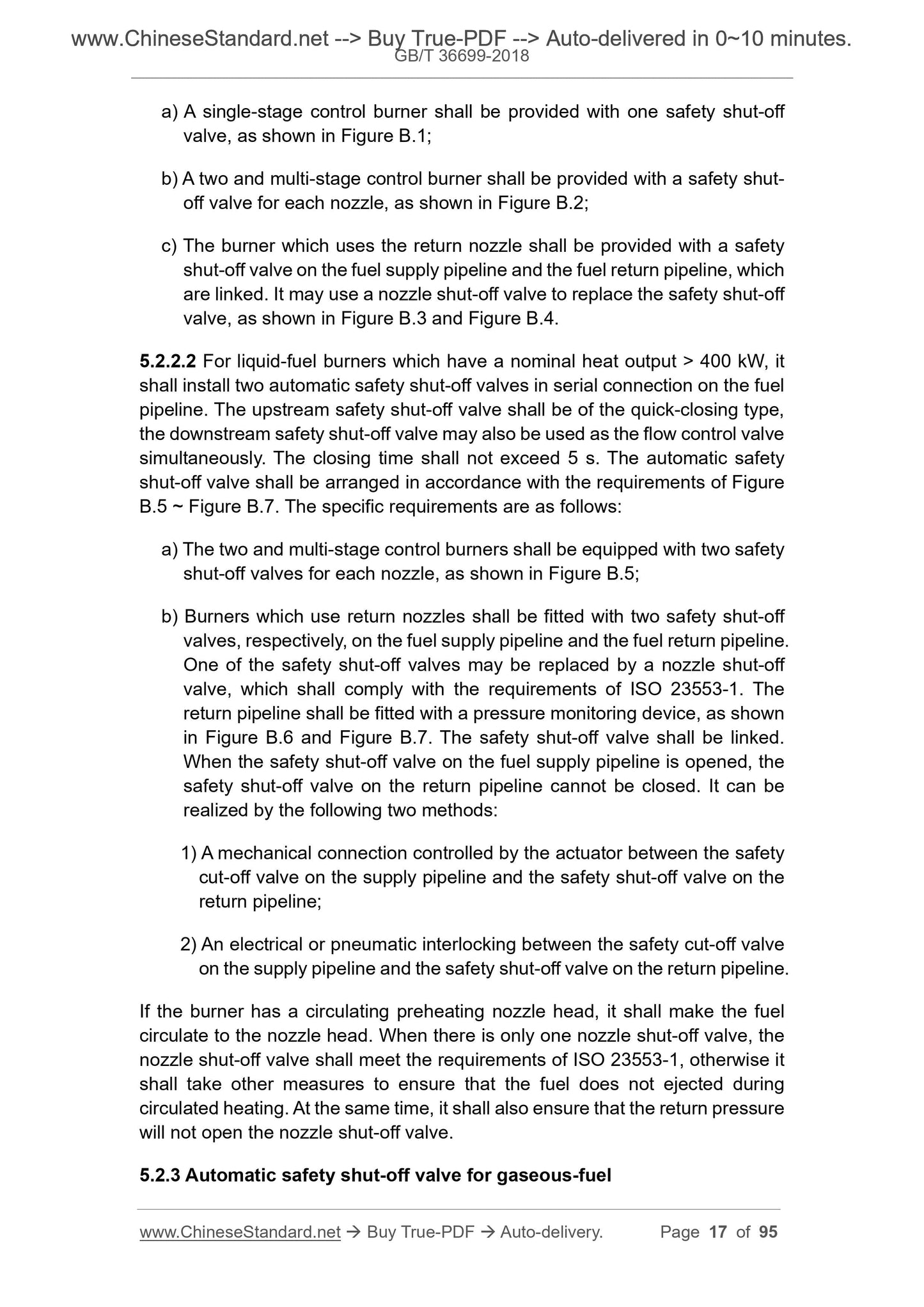
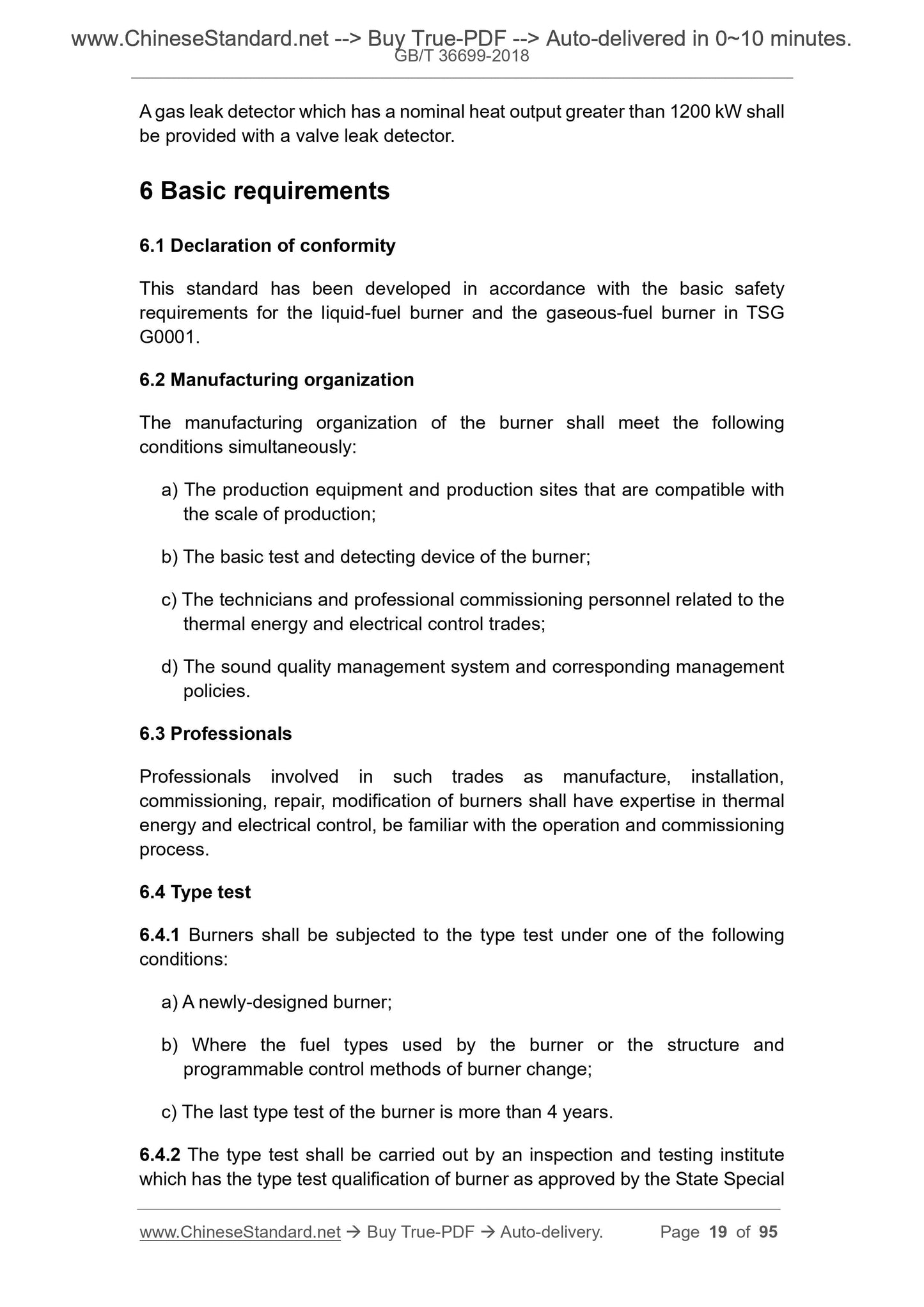
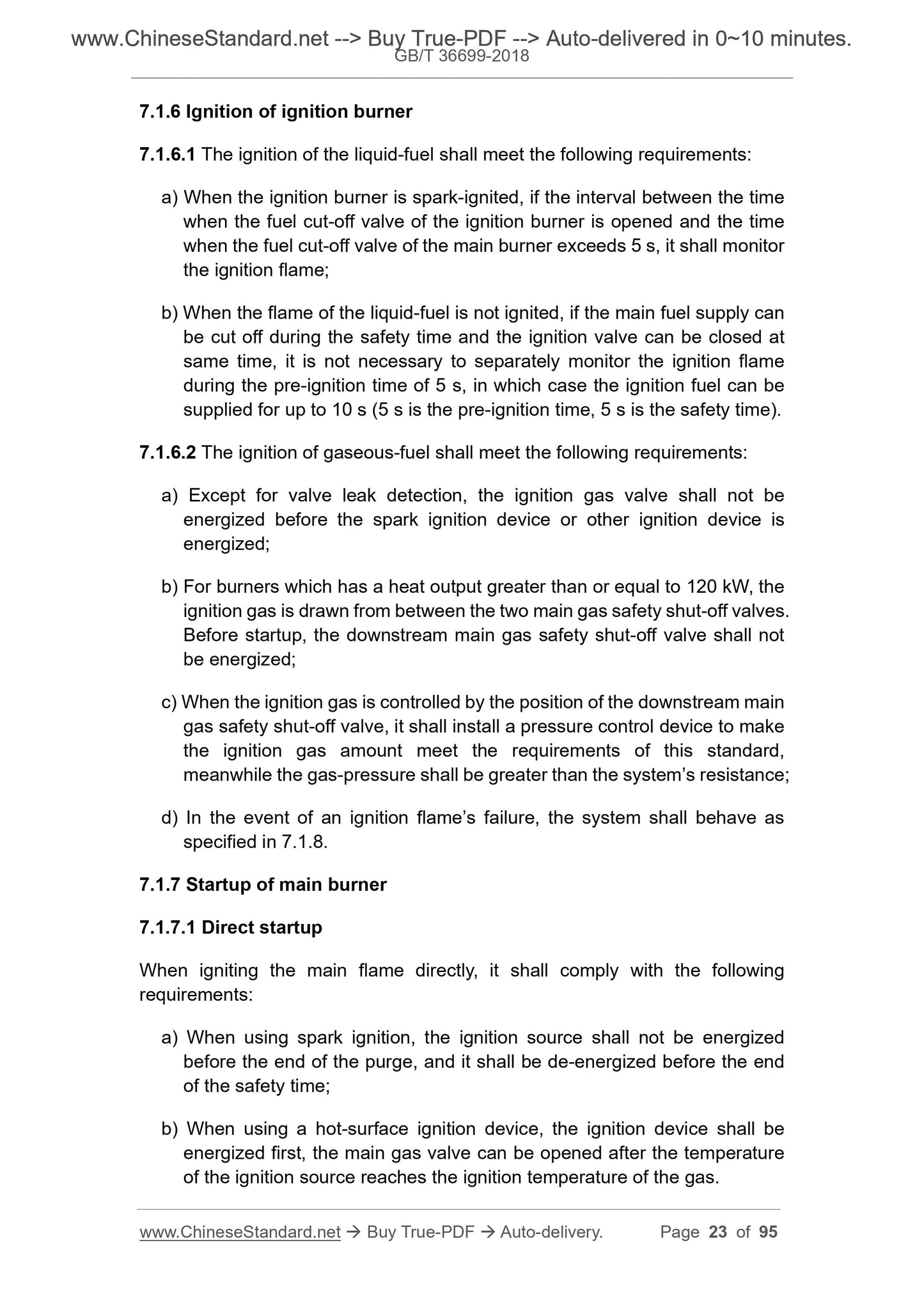
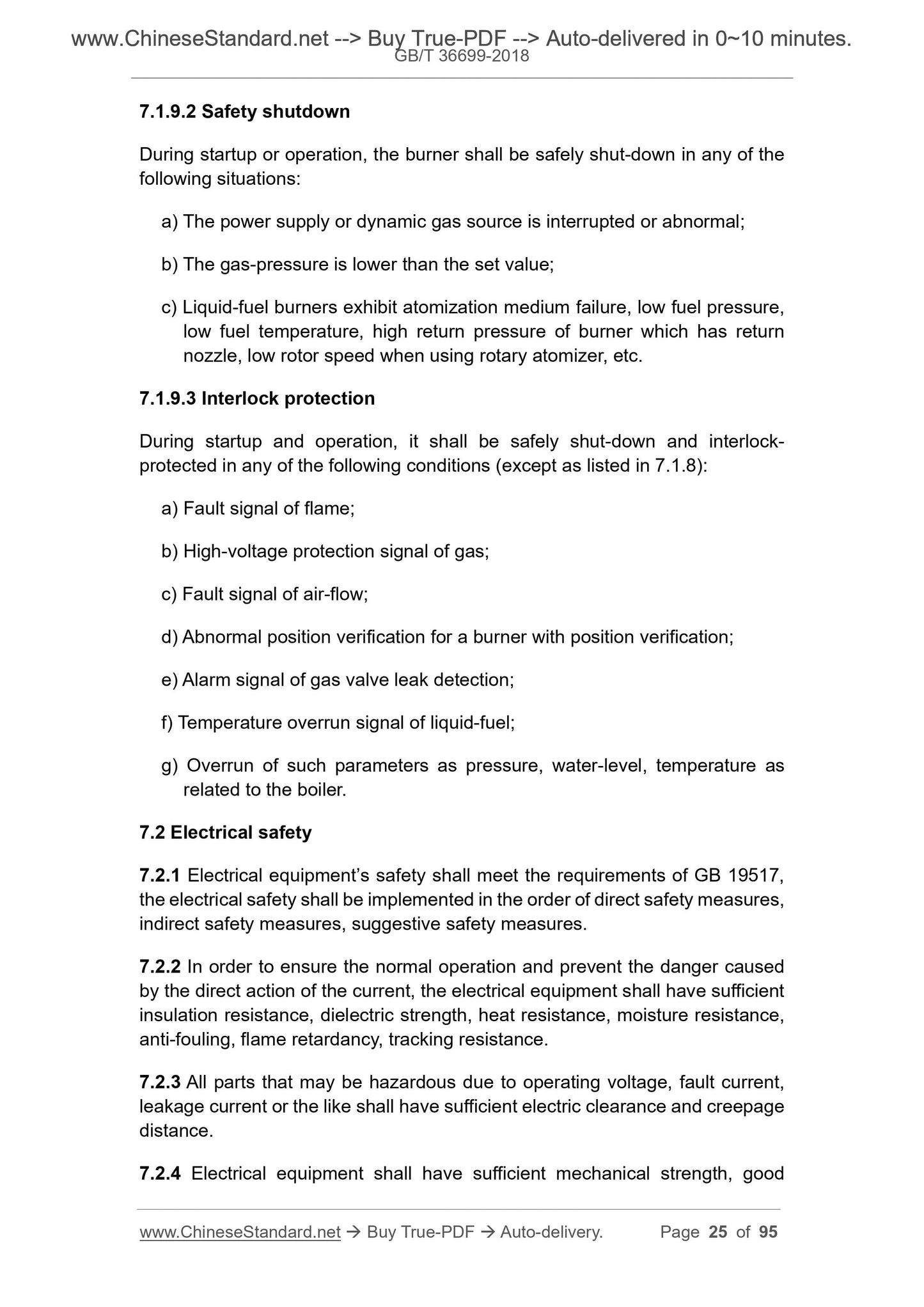