1
/
of
7
www.ChineseStandard.us -- Field Test Asia Pte. Ltd.
GB/T 35974.5-2018 English PDF (GB/T35974.5-2018)
GB/T 35974.5-2018 English PDF (GB/T35974.5-2018)
Regular price
$150.00
Regular price
Sale price
$150.00
Unit price
/
per
Shipping calculated at checkout.
Couldn't load pickup availability
GB/T 35974.5-2018: Plastics and Plastic Lining Pressure Vessels - Part 5: Fabrication, Inspection and Testing for Pressure Vessels with Plastic Lining
Delivery: 9 seconds. Download (and Email) true-PDF + Invoice.
Get Quotation: Click GB/T 35974.5-2018 (Self-service in 1-minute)
Newer / historical versions: GB/T 35974.5-2018
Preview True-PDF (Reload/Scroll-down if blank)
Delivery: 9 seconds. Download (and Email) true-PDF + Invoice.
Get Quotation: Click GB/T 35974.5-2018 (Self-service in 1-minute)
Newer / historical versions: GB/T 35974.5-2018
Preview True-PDF (Reload/Scroll-down if blank)
Share
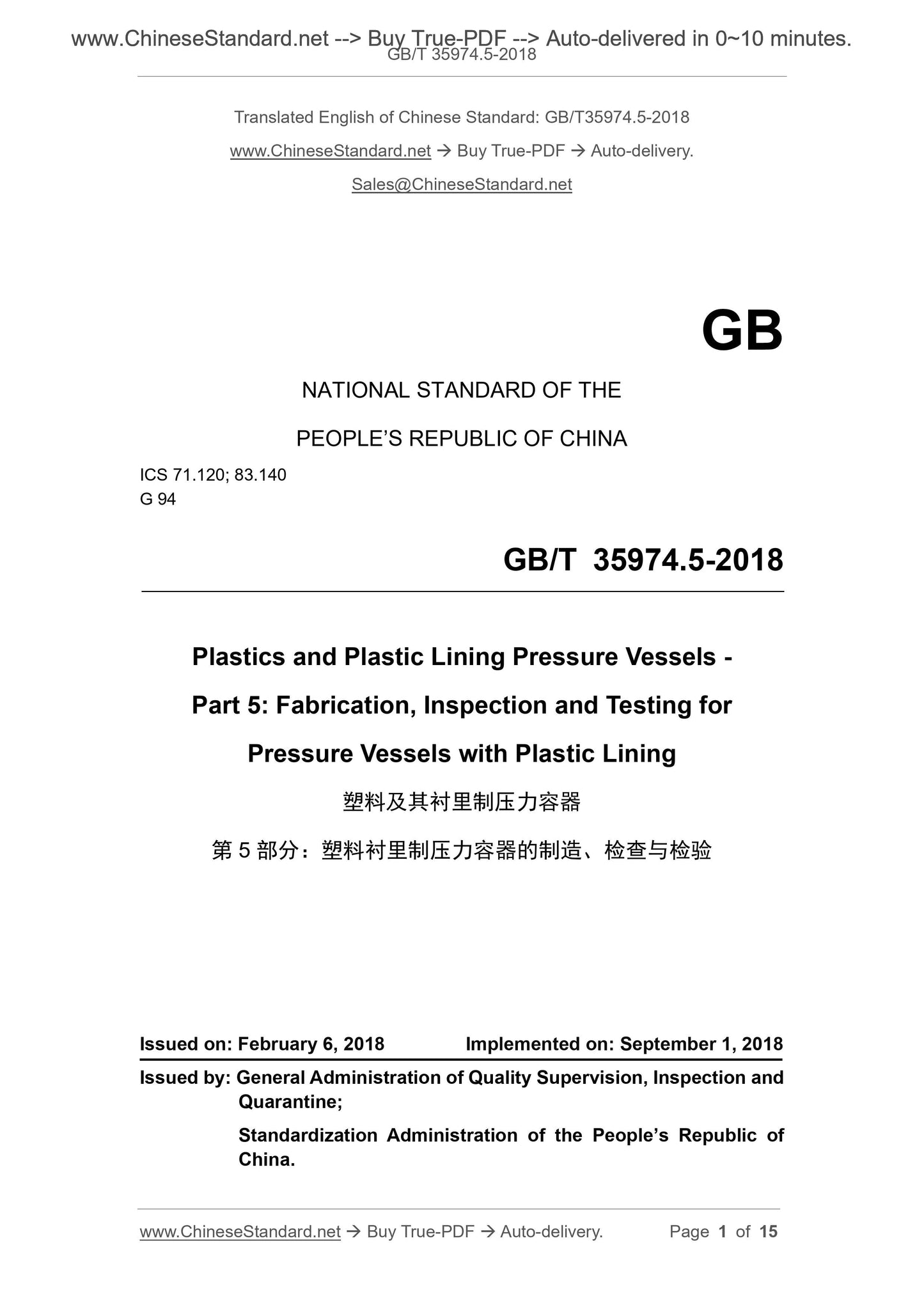

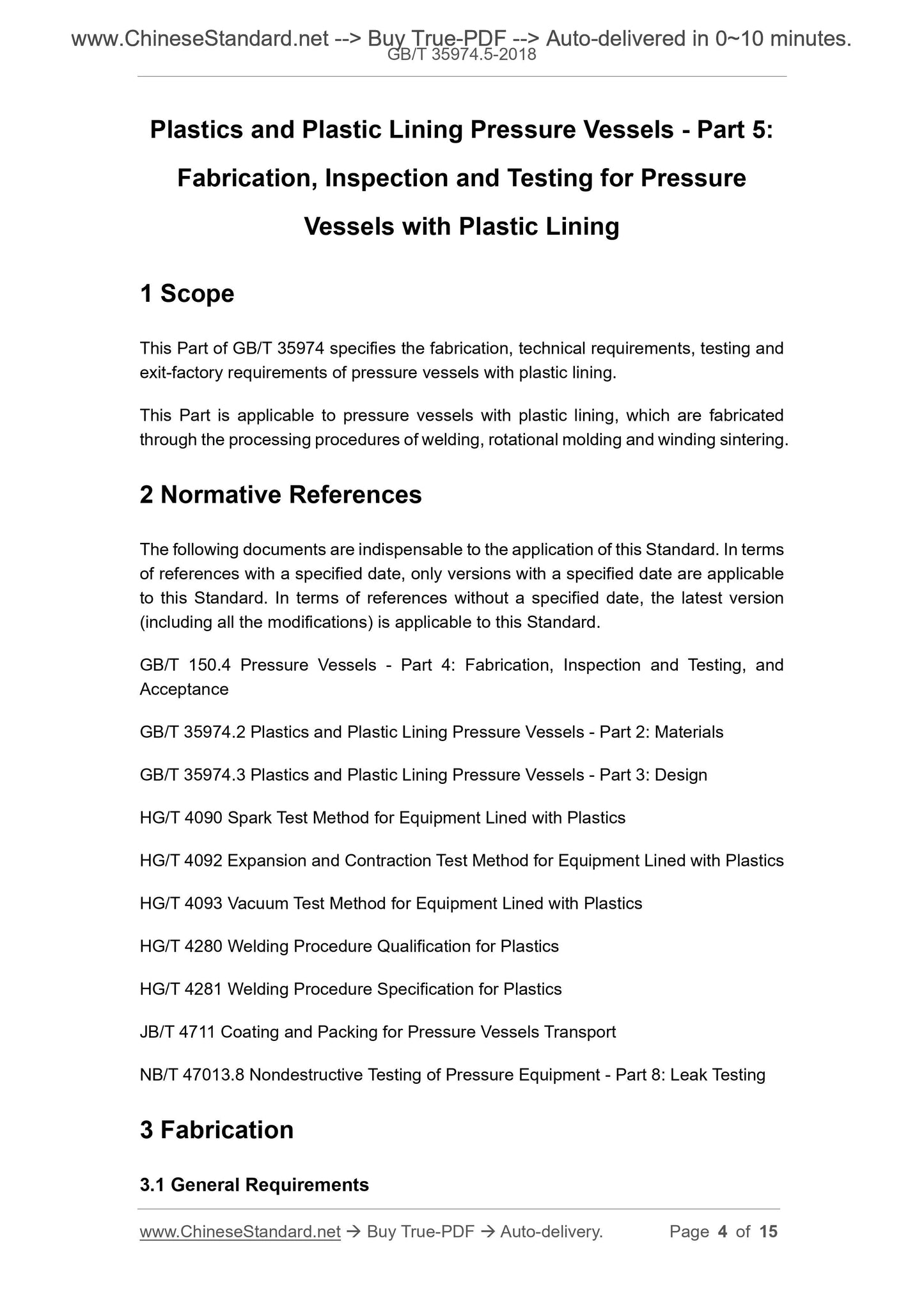
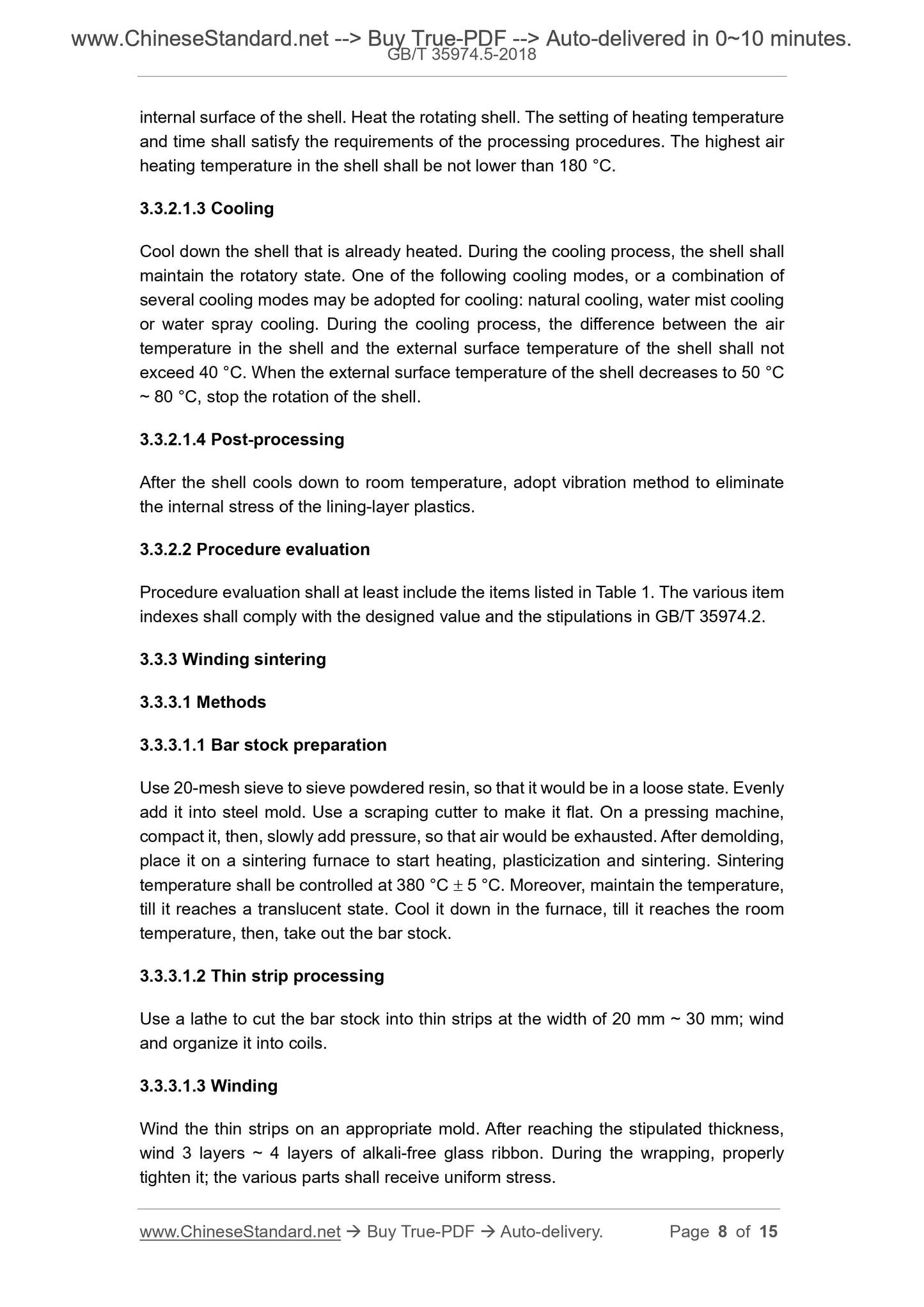
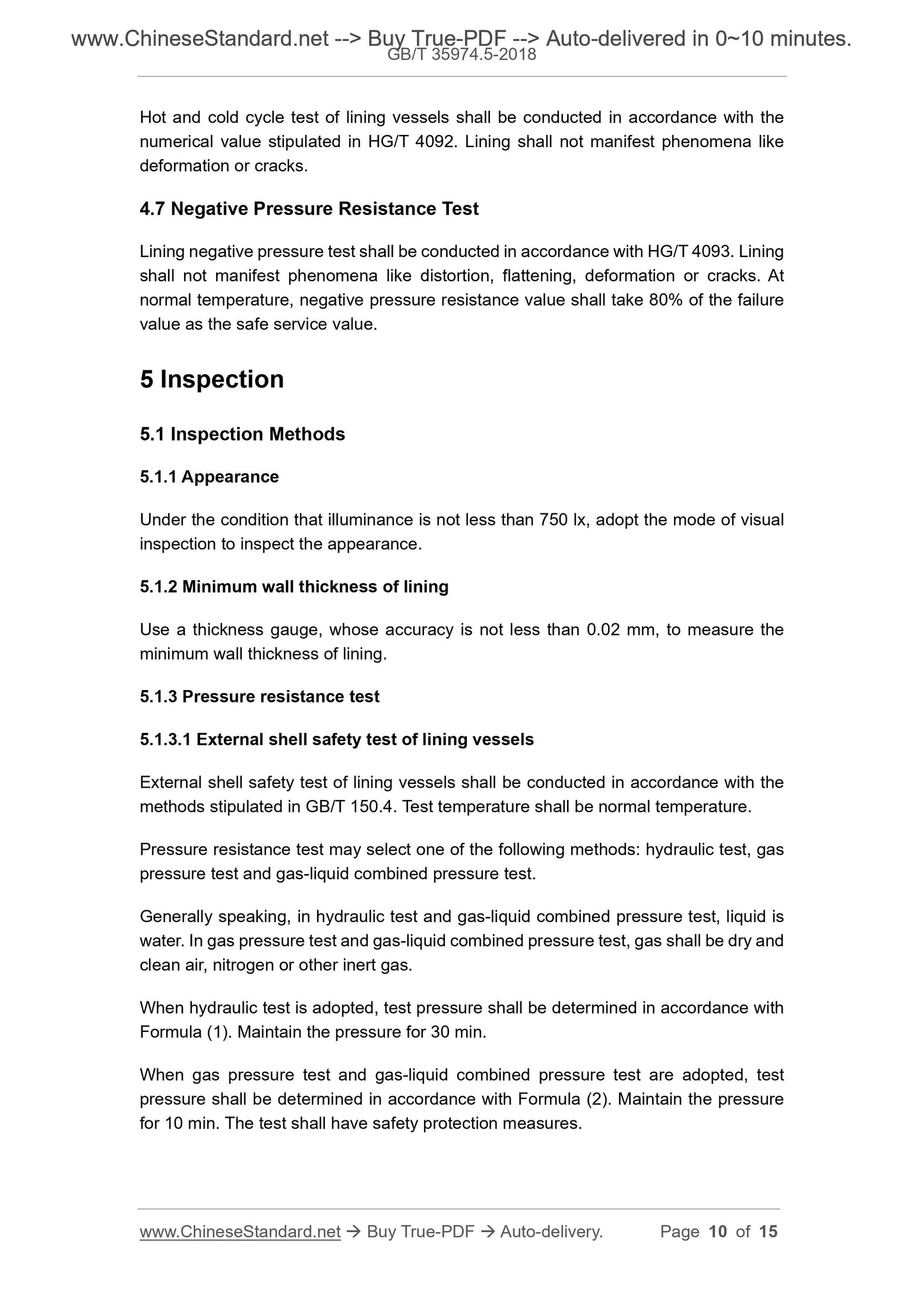
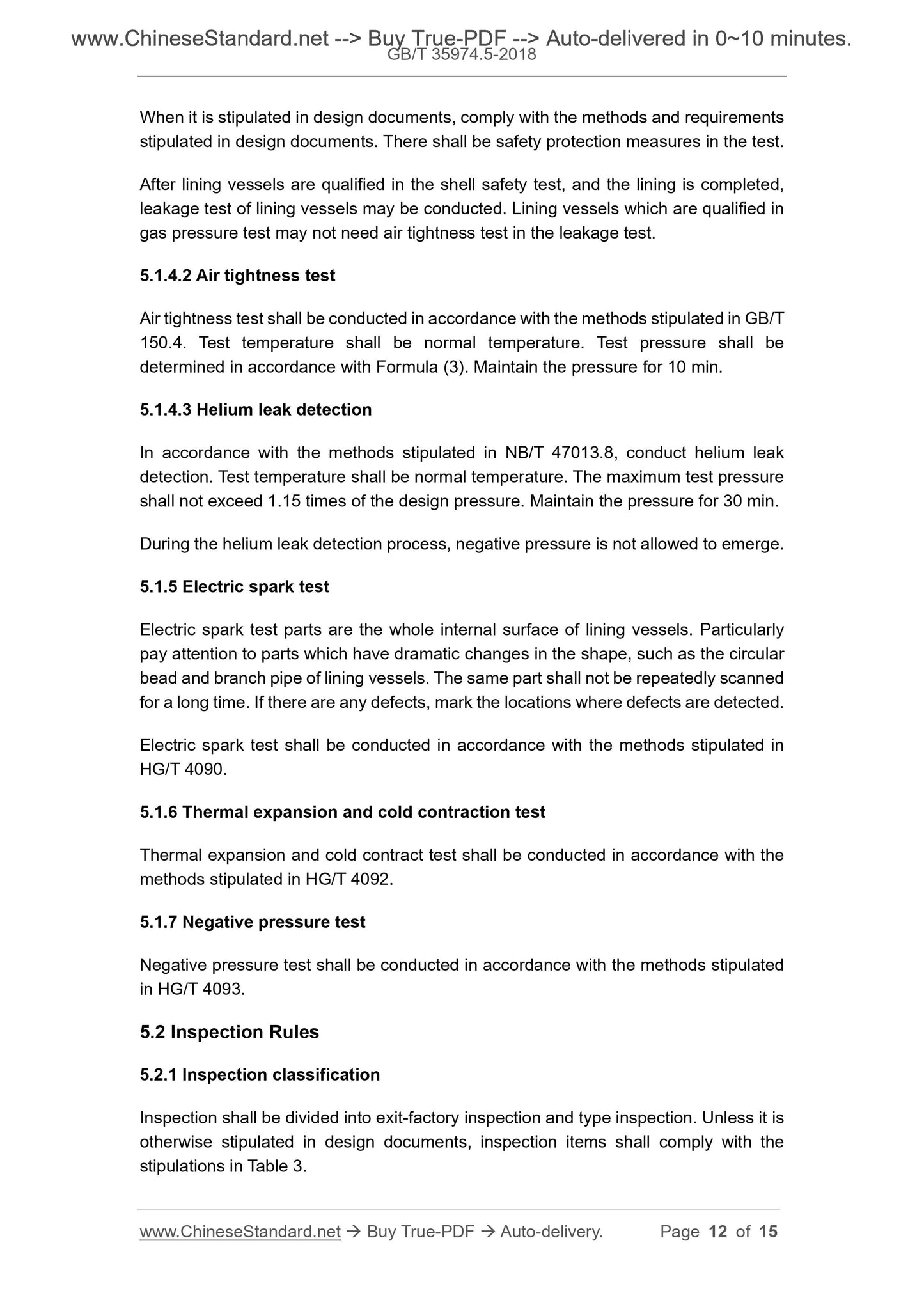
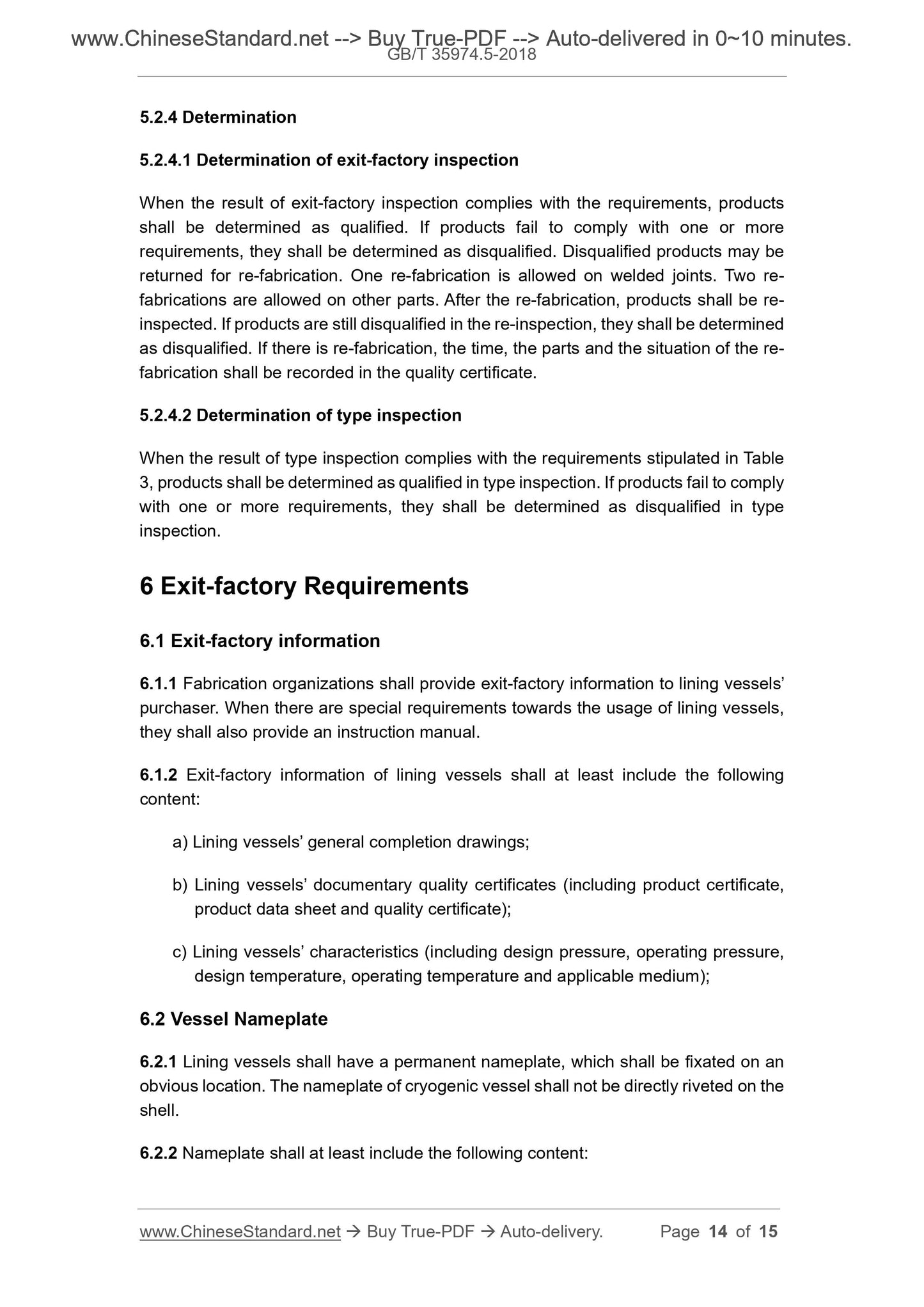