1
/
of
10
www.ChineseStandard.us -- Field Test Asia Pte. Ltd.
GB/T 33389-2016 English PDF (GB/T33389-2016)
GB/T 33389-2016 English PDF (GB/T33389-2016)
Regular price
$150.00
Regular price
Sale price
$150.00
Unit price
/
per
Shipping calculated at checkout.
Couldn't load pickup availability
GB/T 33389-2016: Woven fabrics and woven composite fabrics for automotive interior
Delivery: 9 seconds. Download (and Email) true-PDF + Invoice.
Get Quotation: Click GB/T 33389-2016 (Self-service in 1-minute)
Newer / historical versions: GB/T 33389-2016
Preview True-PDF (Reload/Scroll-down if blank)
Delivery: 9 seconds. Download (and Email) true-PDF + Invoice.
Get Quotation: Click GB/T 33389-2016 (Self-service in 1-minute)
Newer / historical versions: GB/T 33389-2016
Preview True-PDF (Reload/Scroll-down if blank)
Share
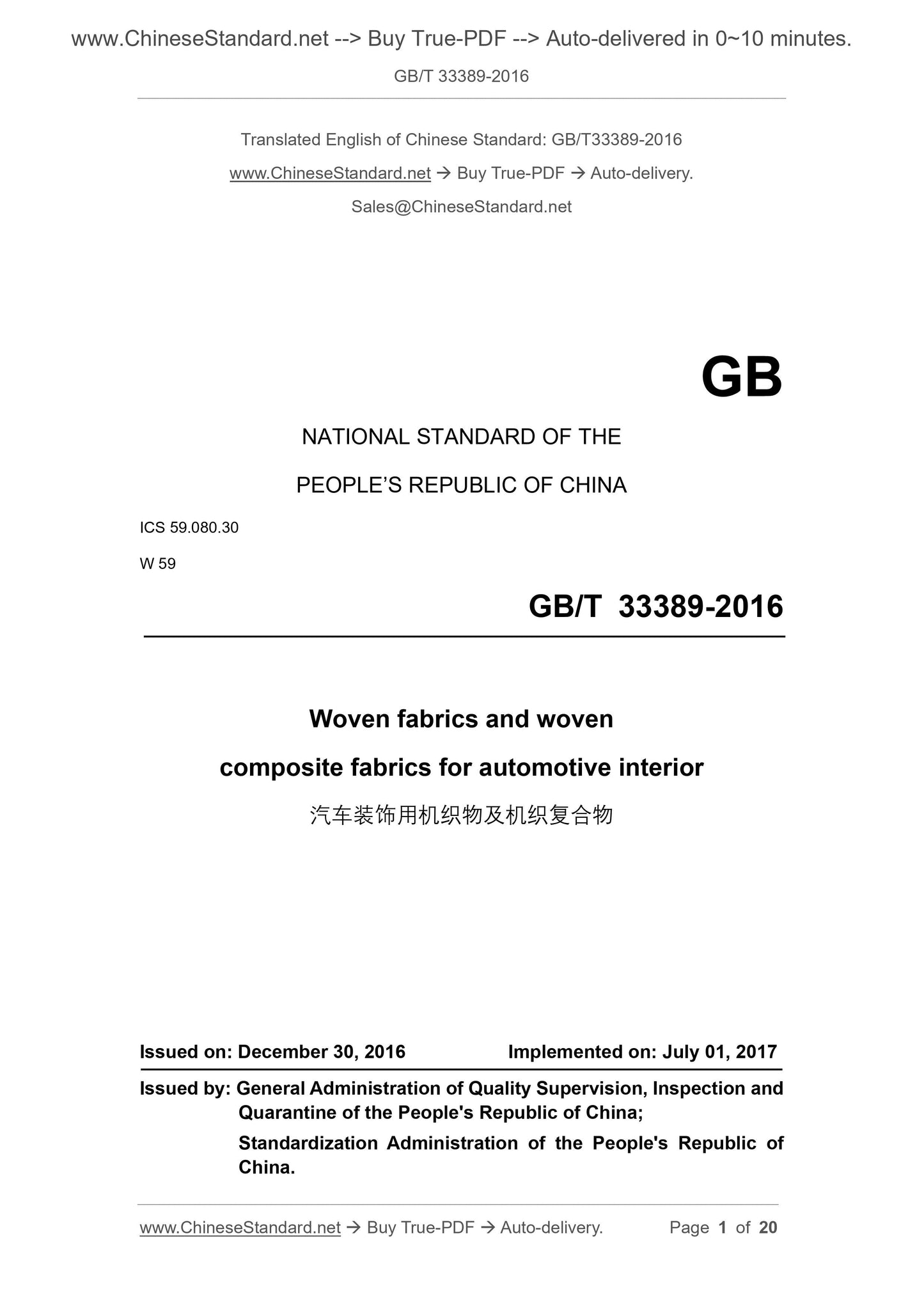
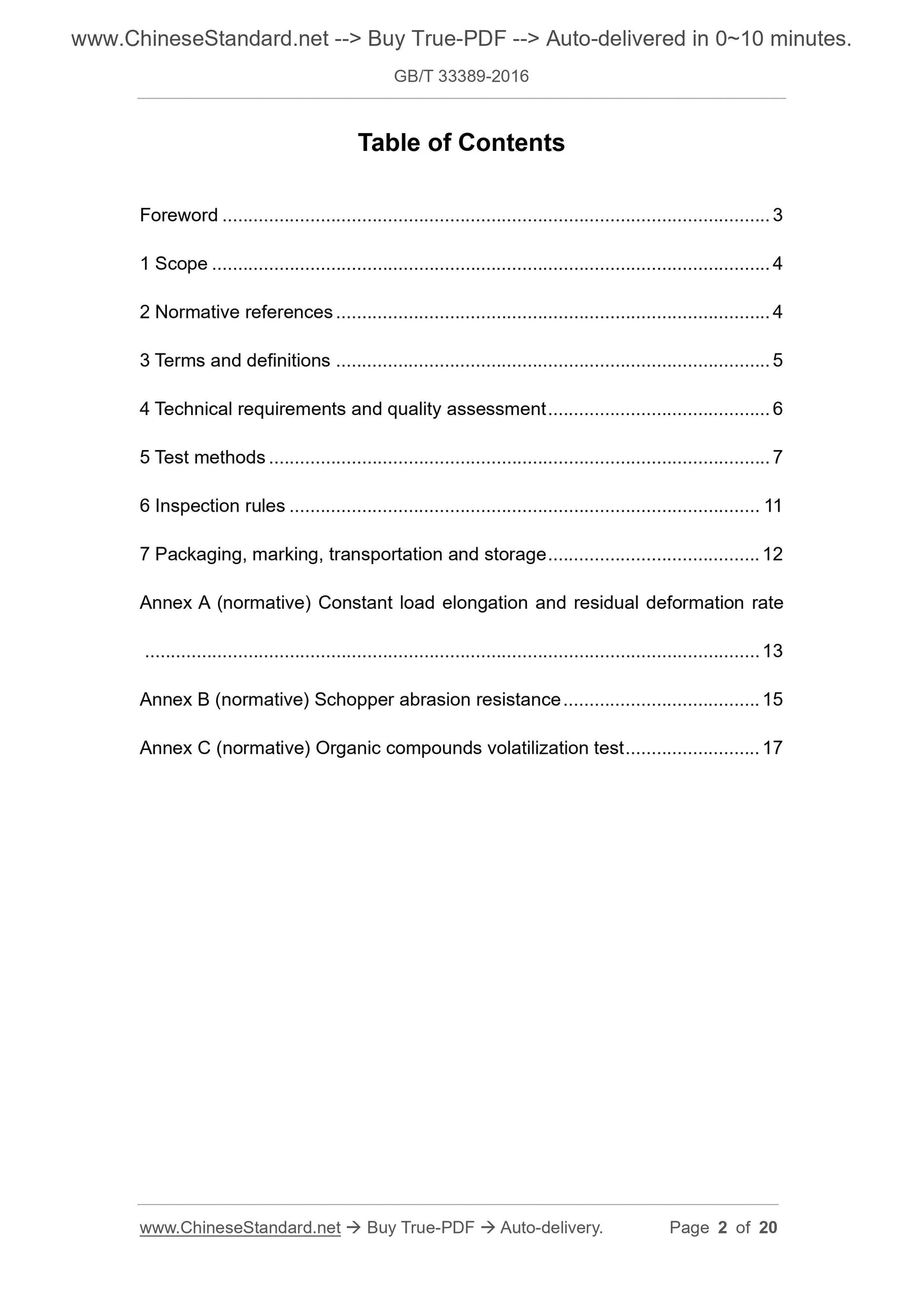
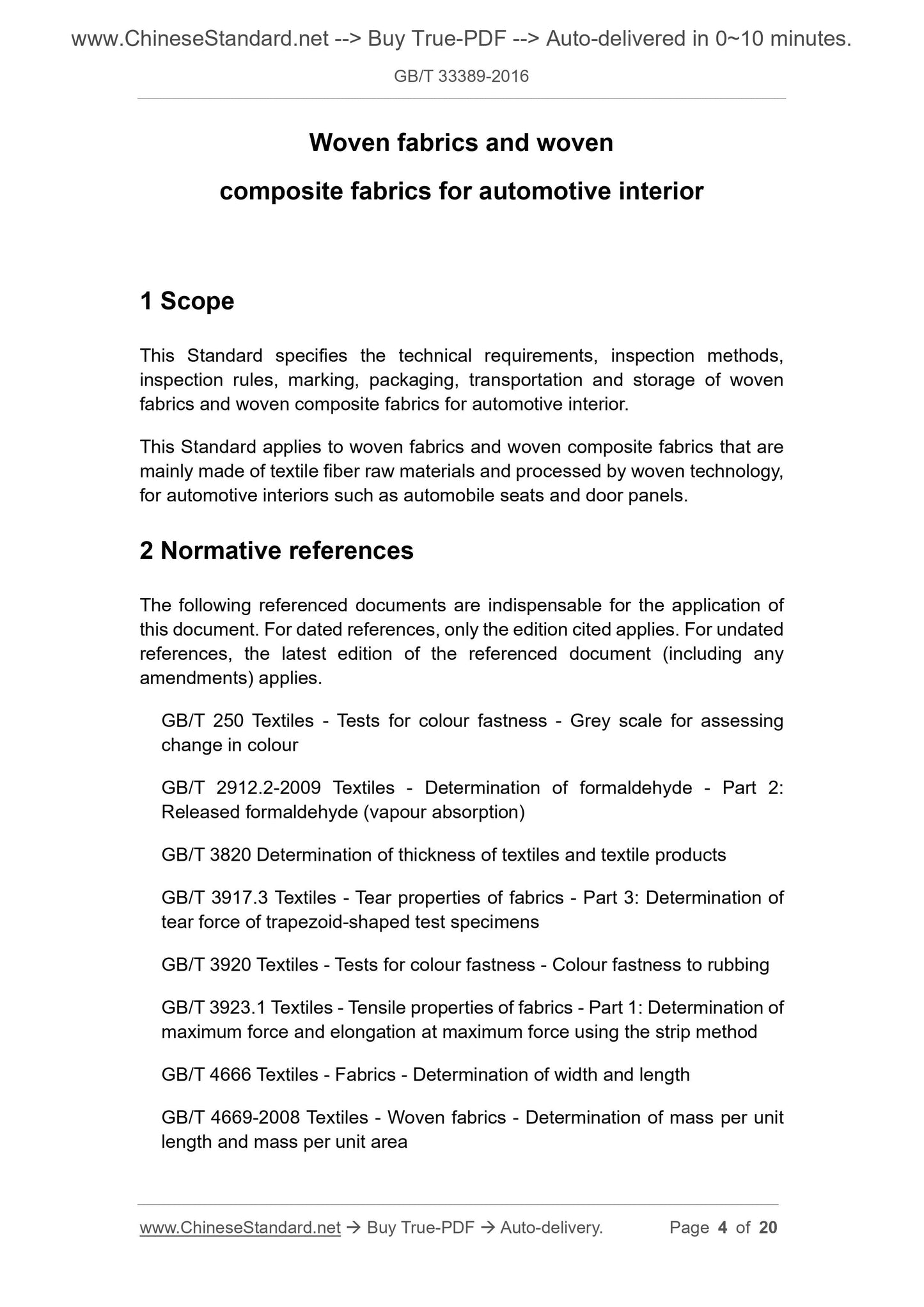
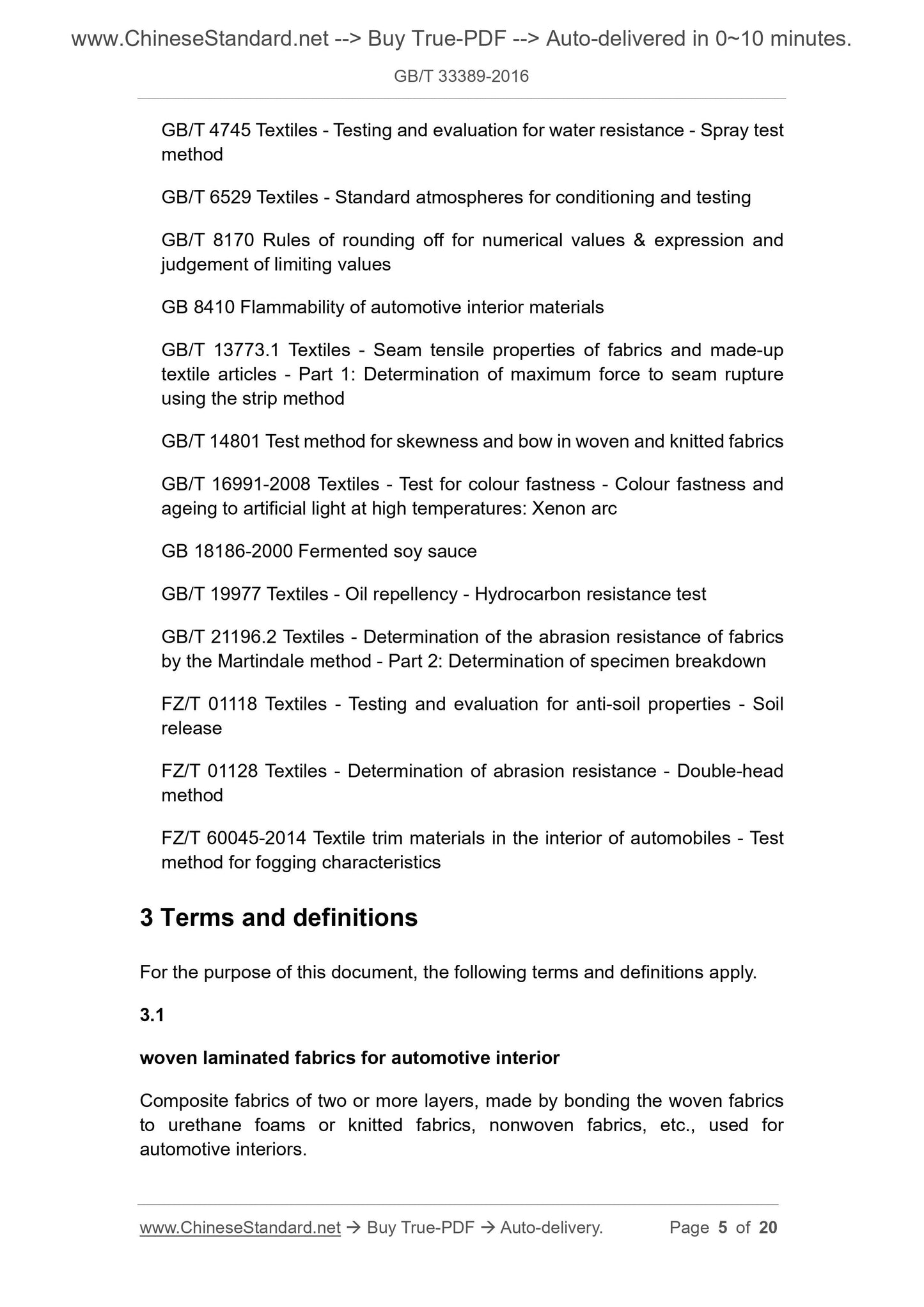
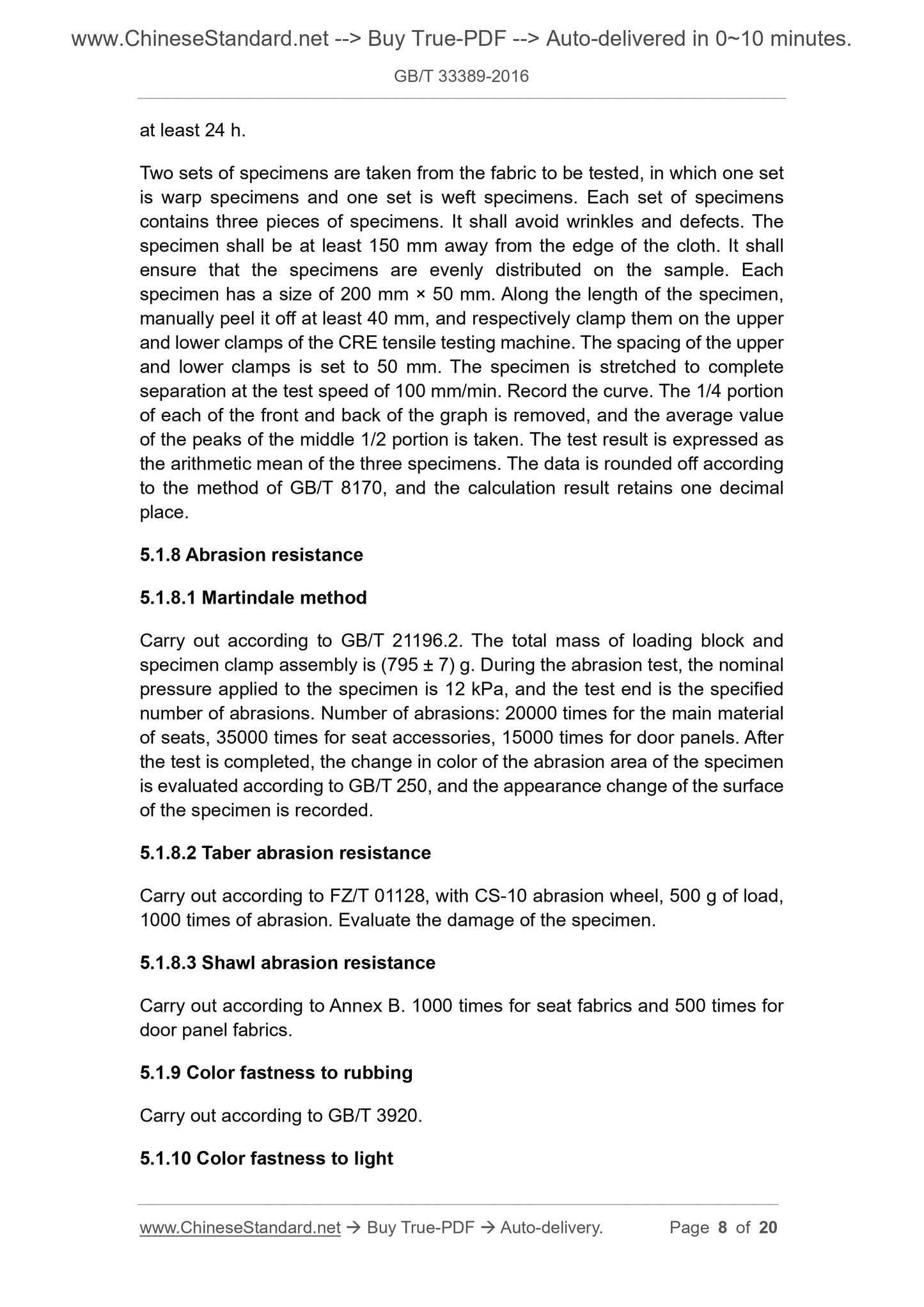
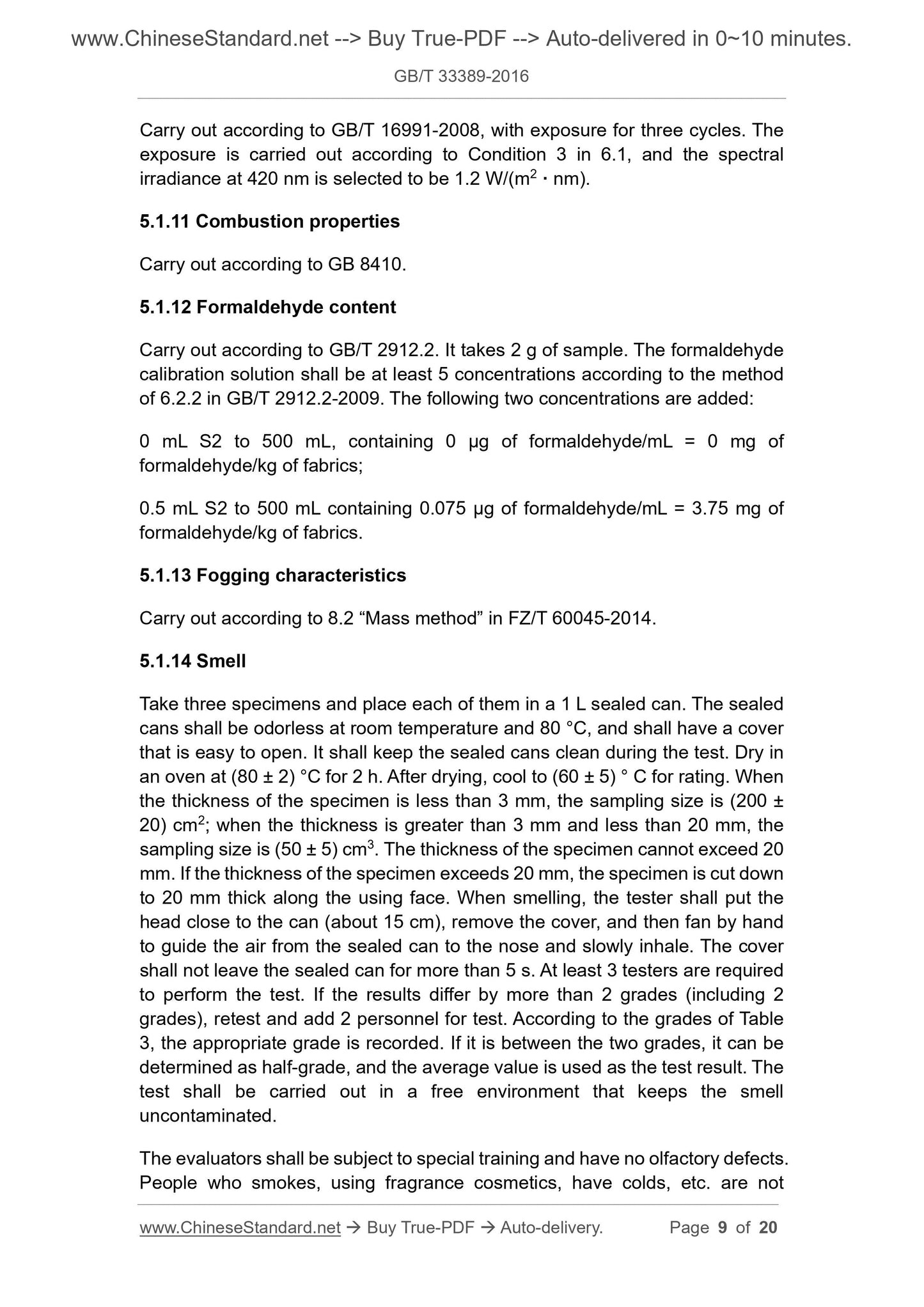
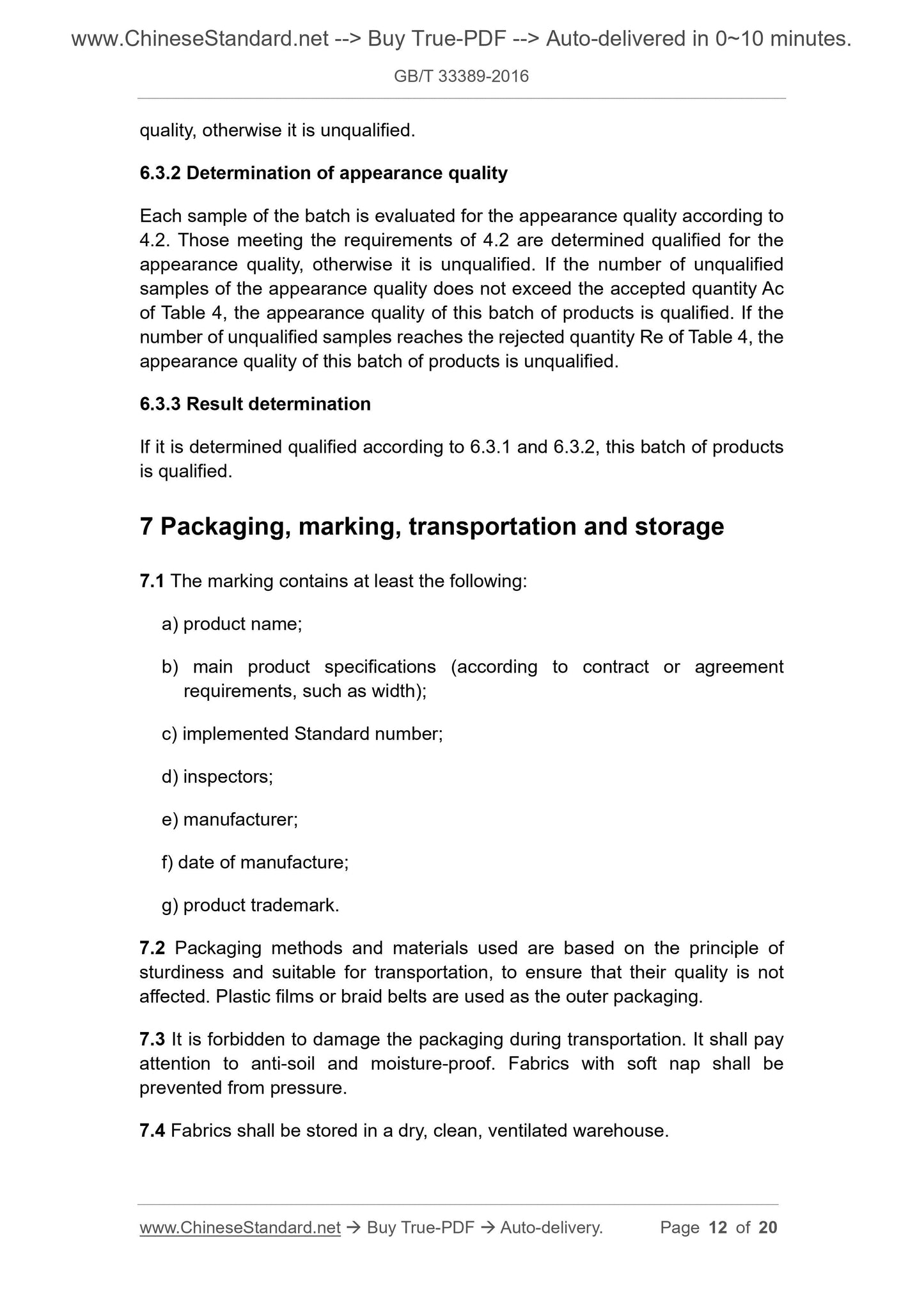
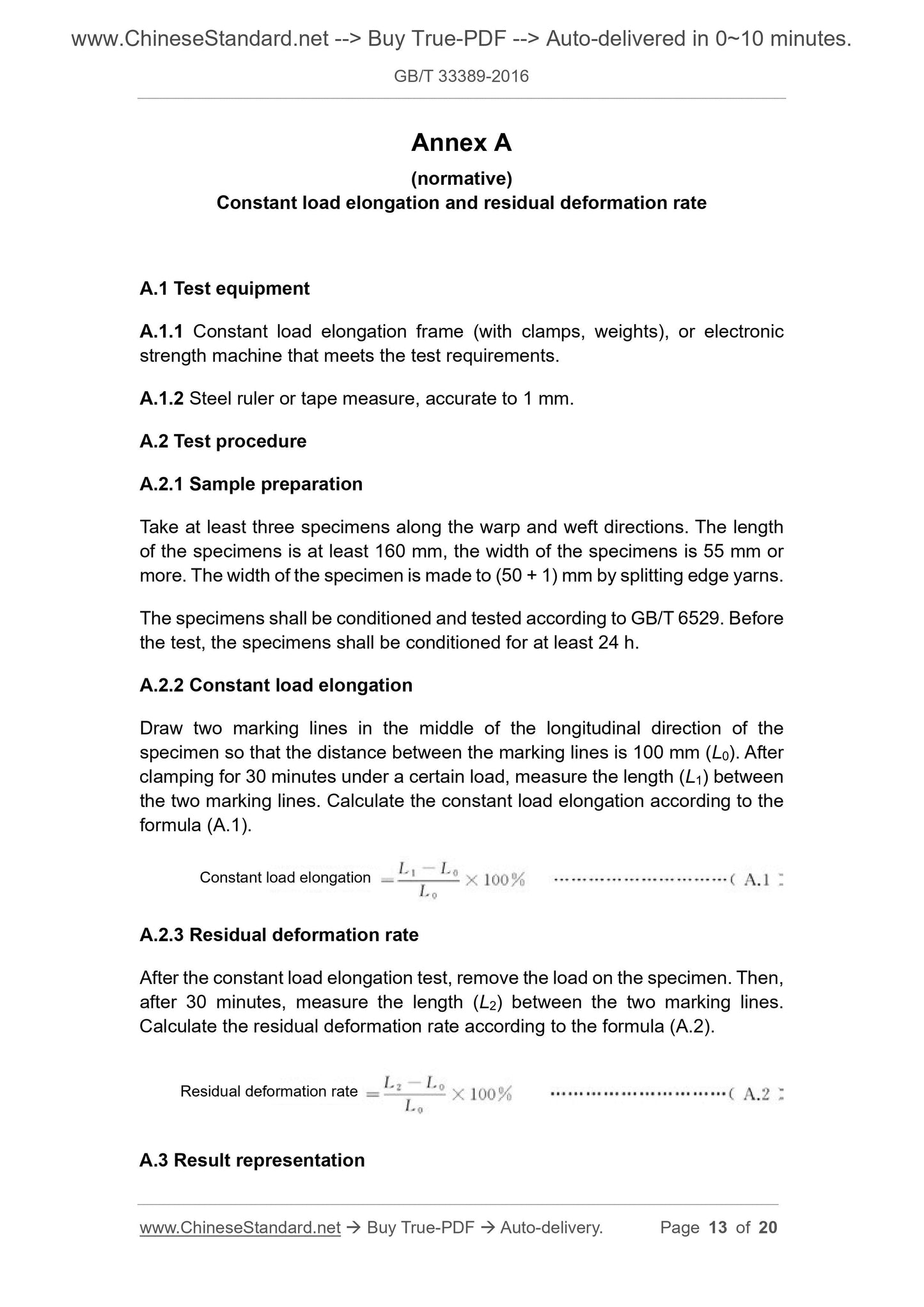
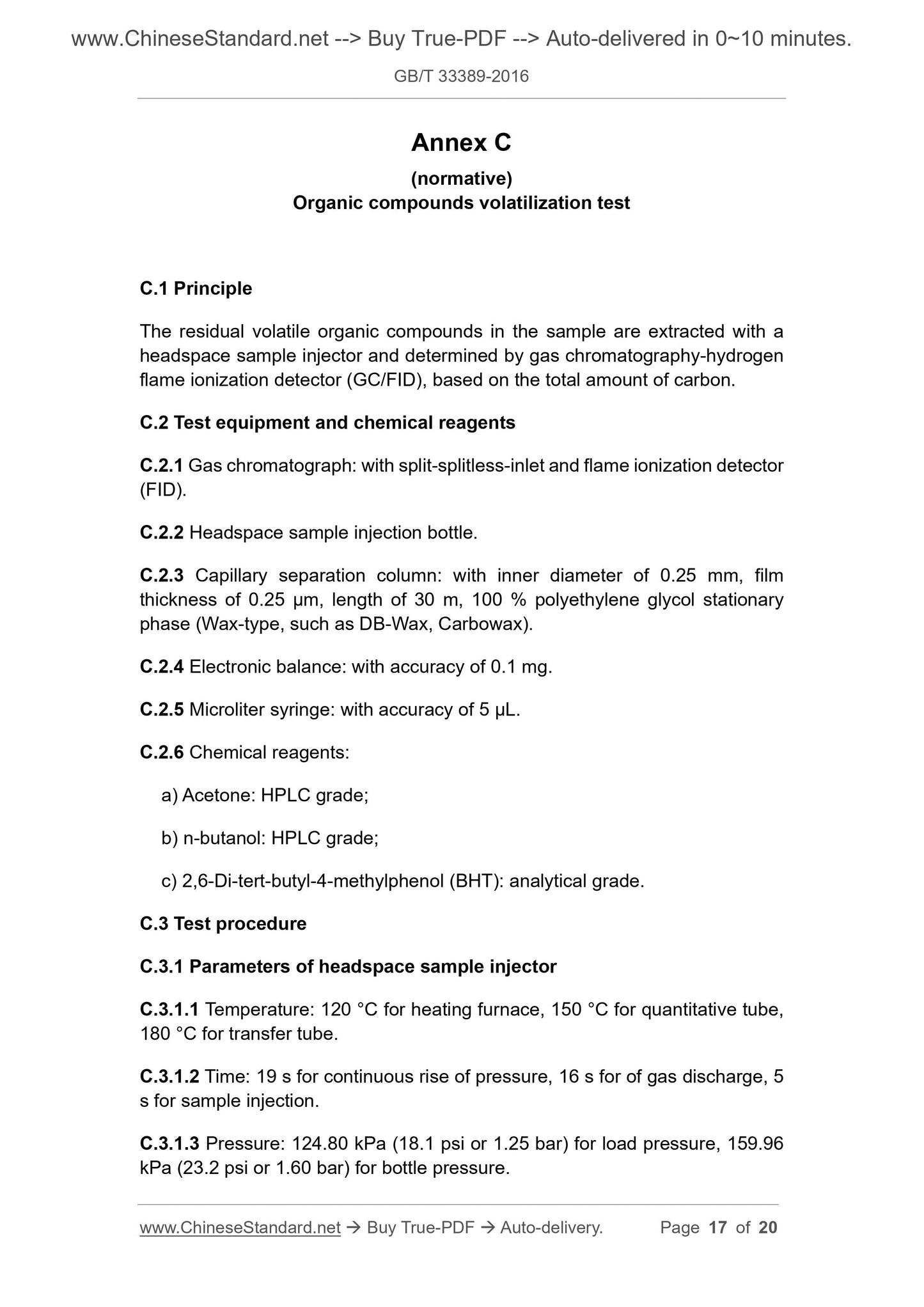
