1
/
of
12
www.ChineseStandard.us -- Field Test Asia Pte. Ltd.
GB/T 3291.3-1997 English PDF (GB/T3291.3-1997)
GB/T 3291.3-1997 English PDF (GB/T3291.3-1997)
Regular price
$200.00
Regular price
Sale price
$200.00
Unit price
/
per
Shipping calculated at checkout.
Couldn't load pickup availability
GB/T 3291.3-1997: Textiles. Terms of textile material properties and test. Part 3: General
Delivery: 9 seconds. Download (and Email) true-PDF + Invoice.
Get Quotation: Click GB/T 3291.3-1997 (Self-service in 1-minute)
Newer / historical versions: GB/T 3291.3-1997
Preview True-PDF (Reload/Scroll-down if blank)
Delivery: 9 seconds. Download (and Email) true-PDF + Invoice.
Get Quotation: Click GB/T 3291.3-1997 (Self-service in 1-minute)
Newer / historical versions: GB/T 3291.3-1997
Preview True-PDF (Reload/Scroll-down if blank)
Share
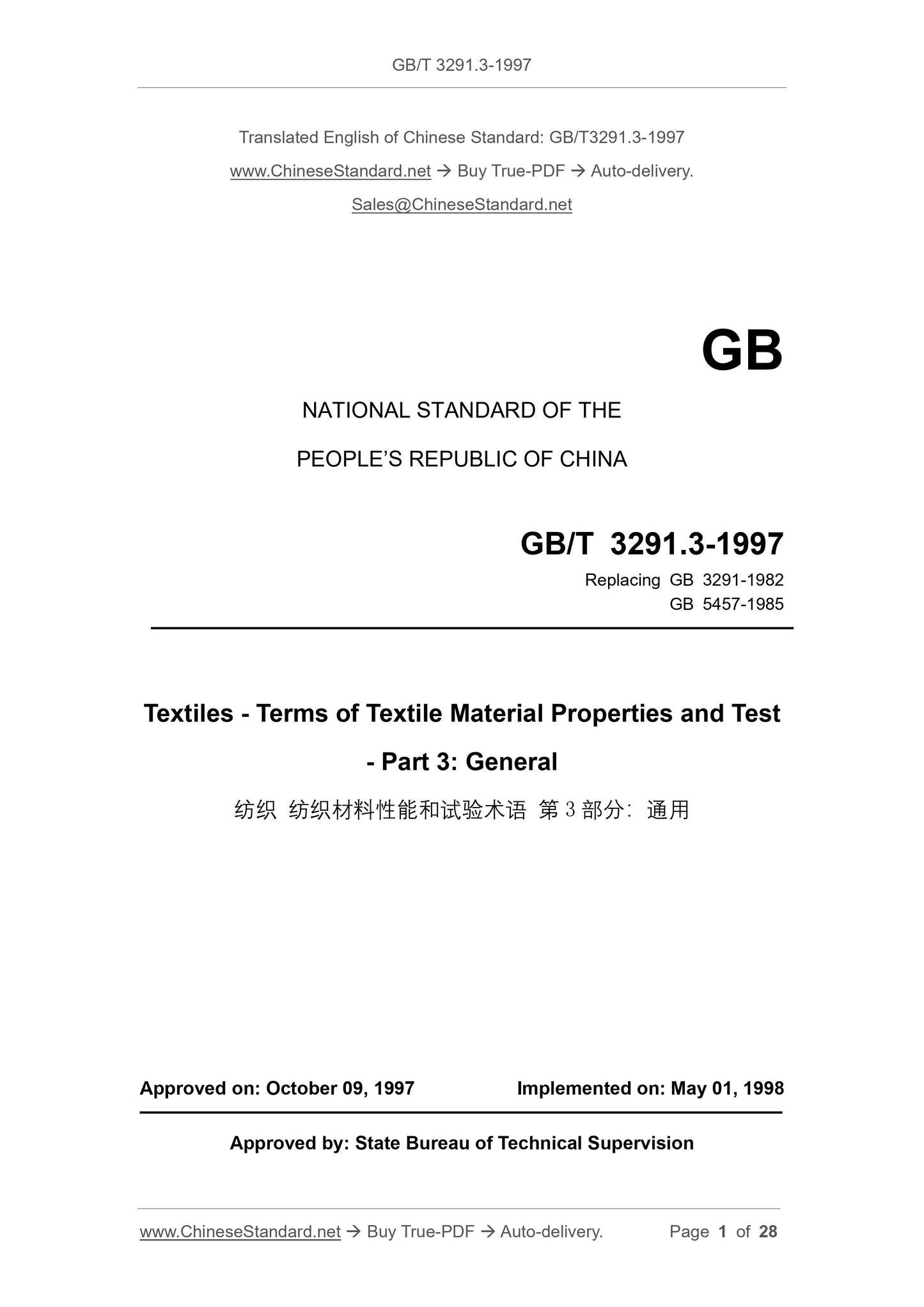
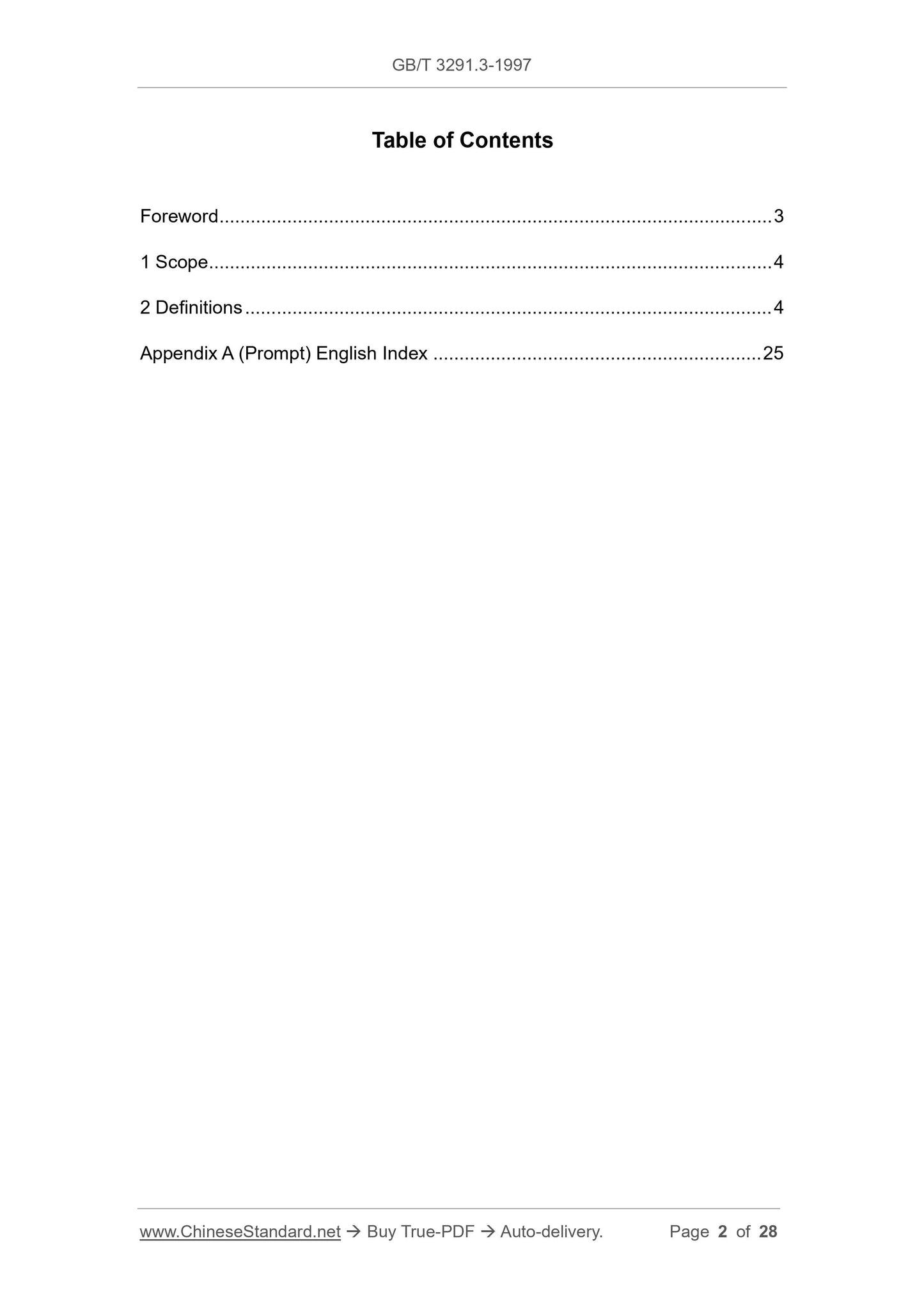
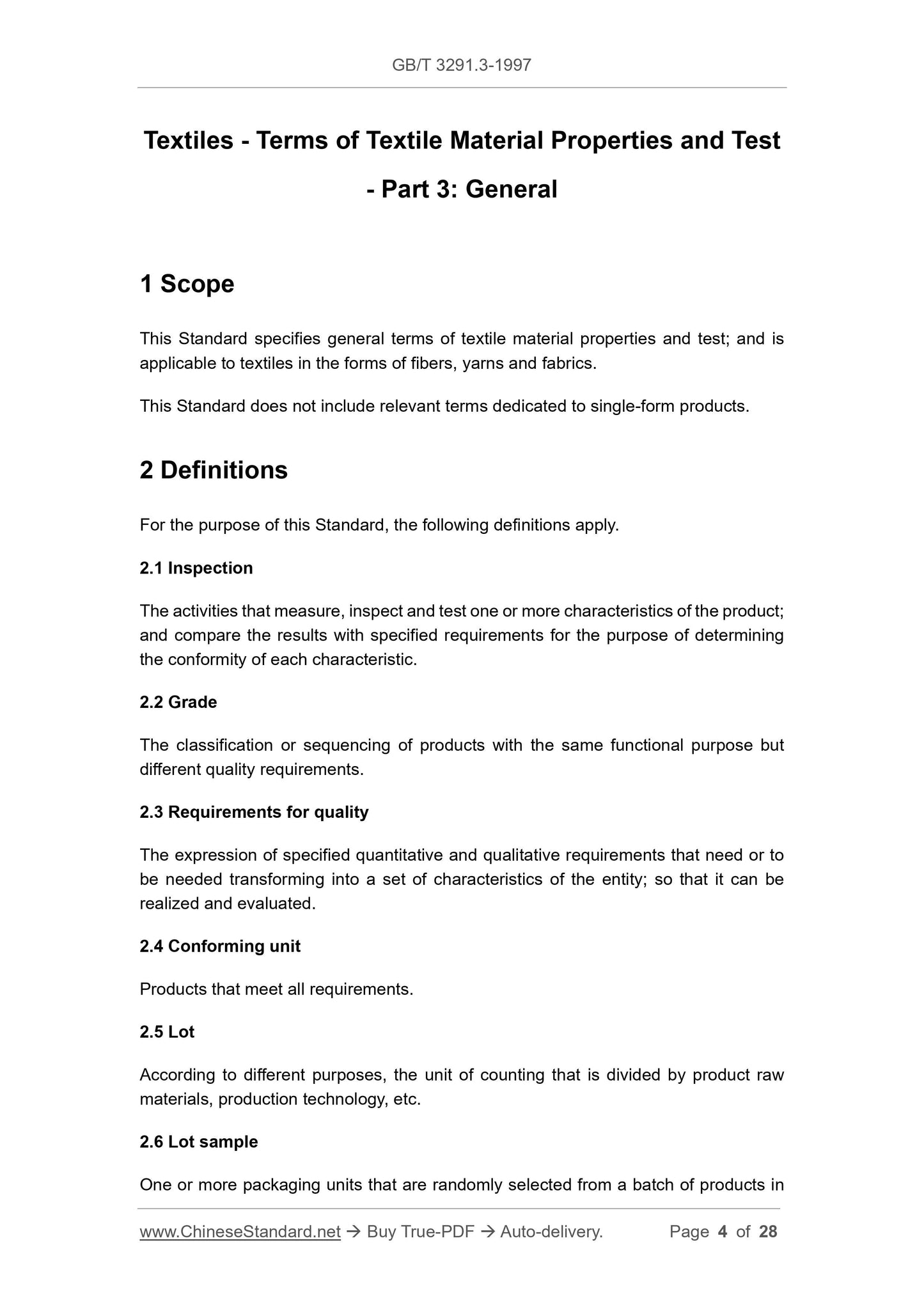
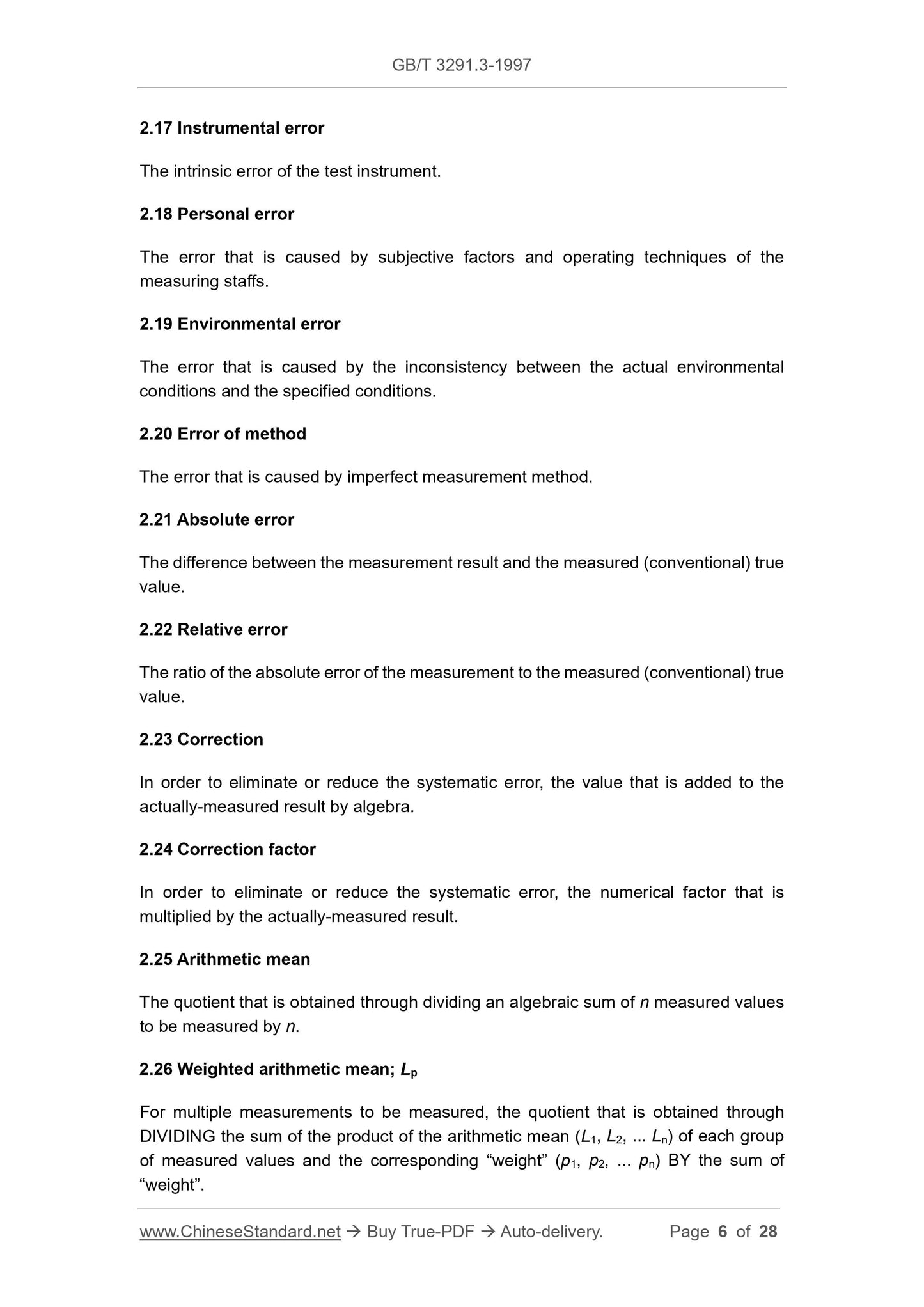
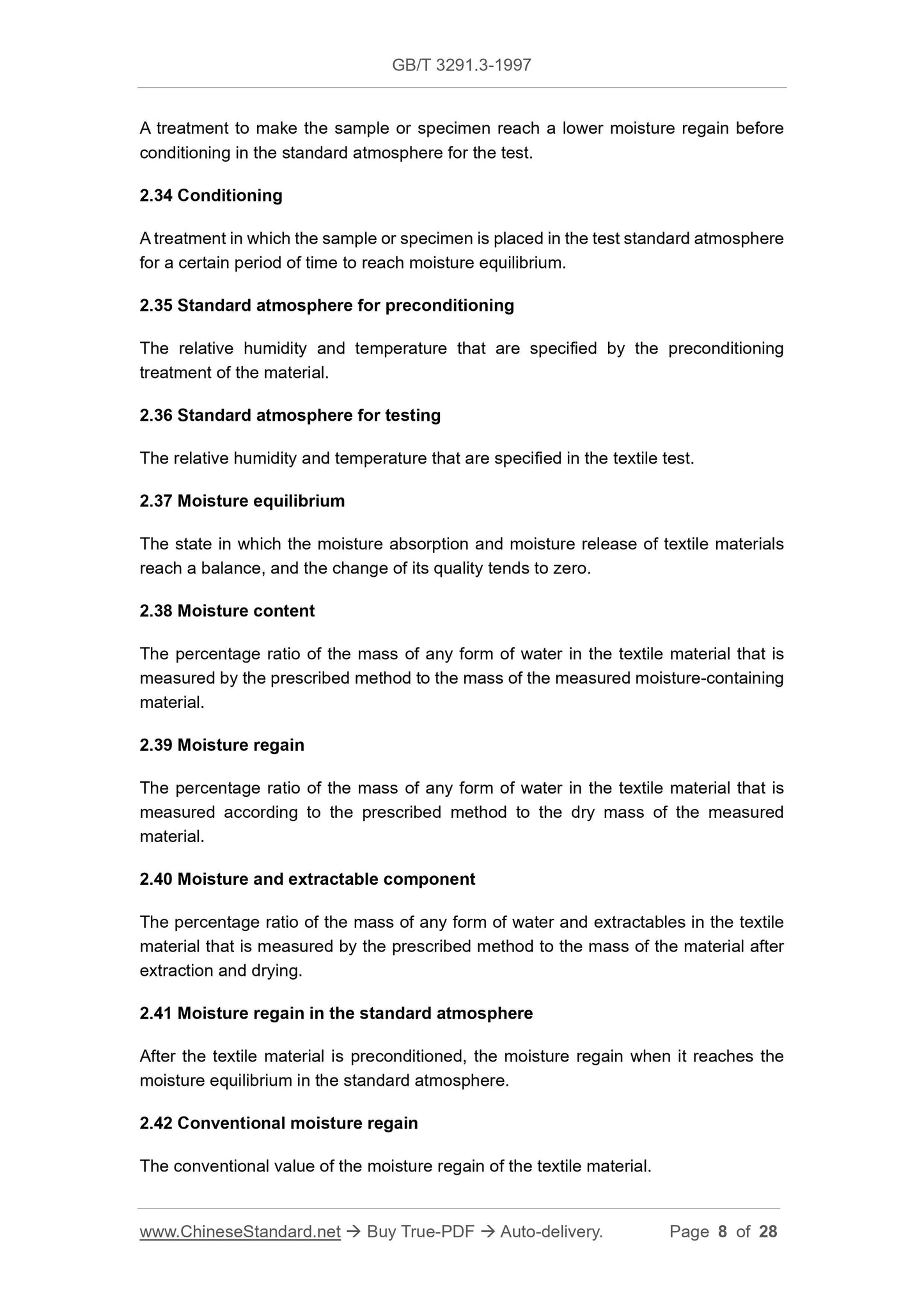
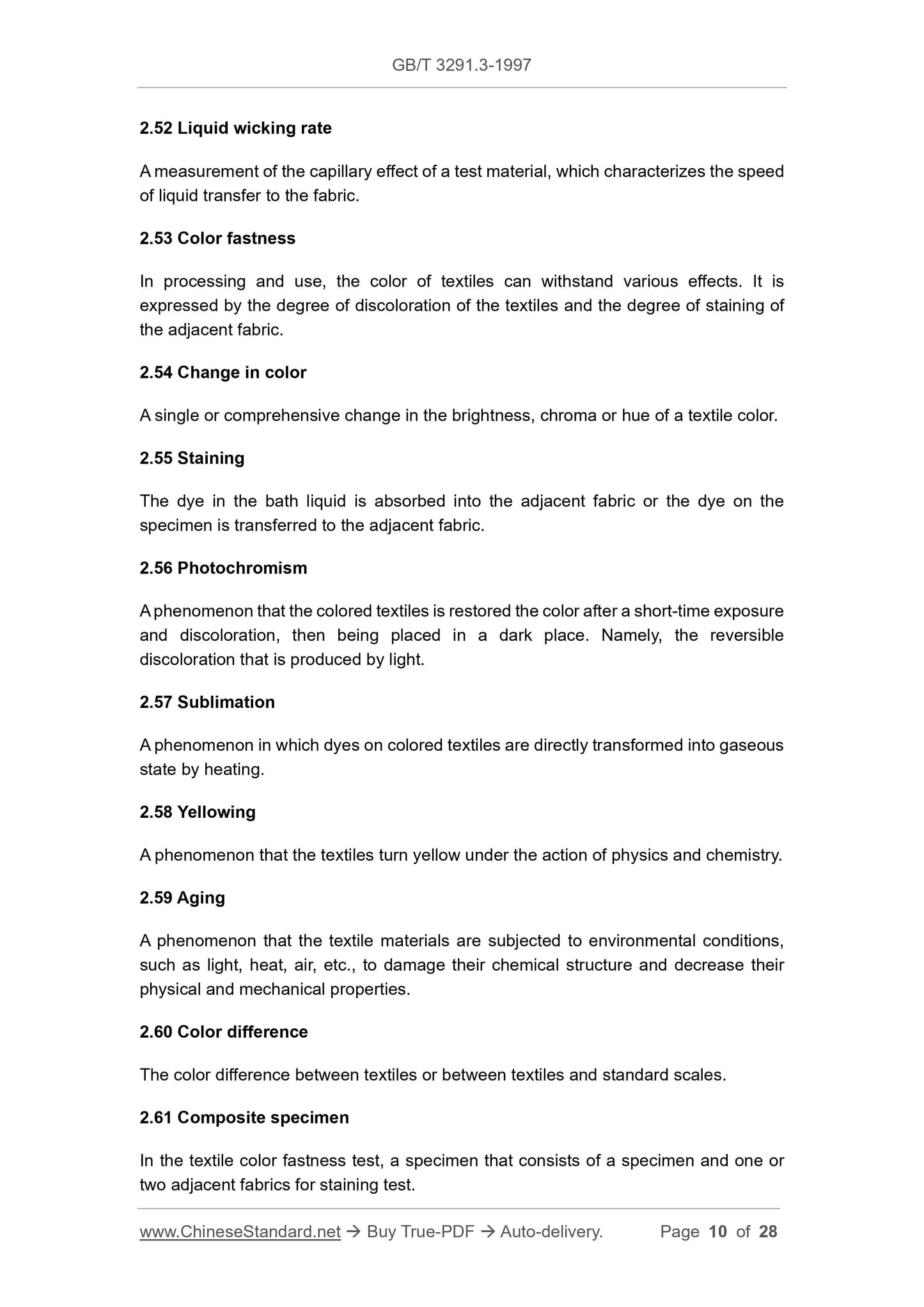
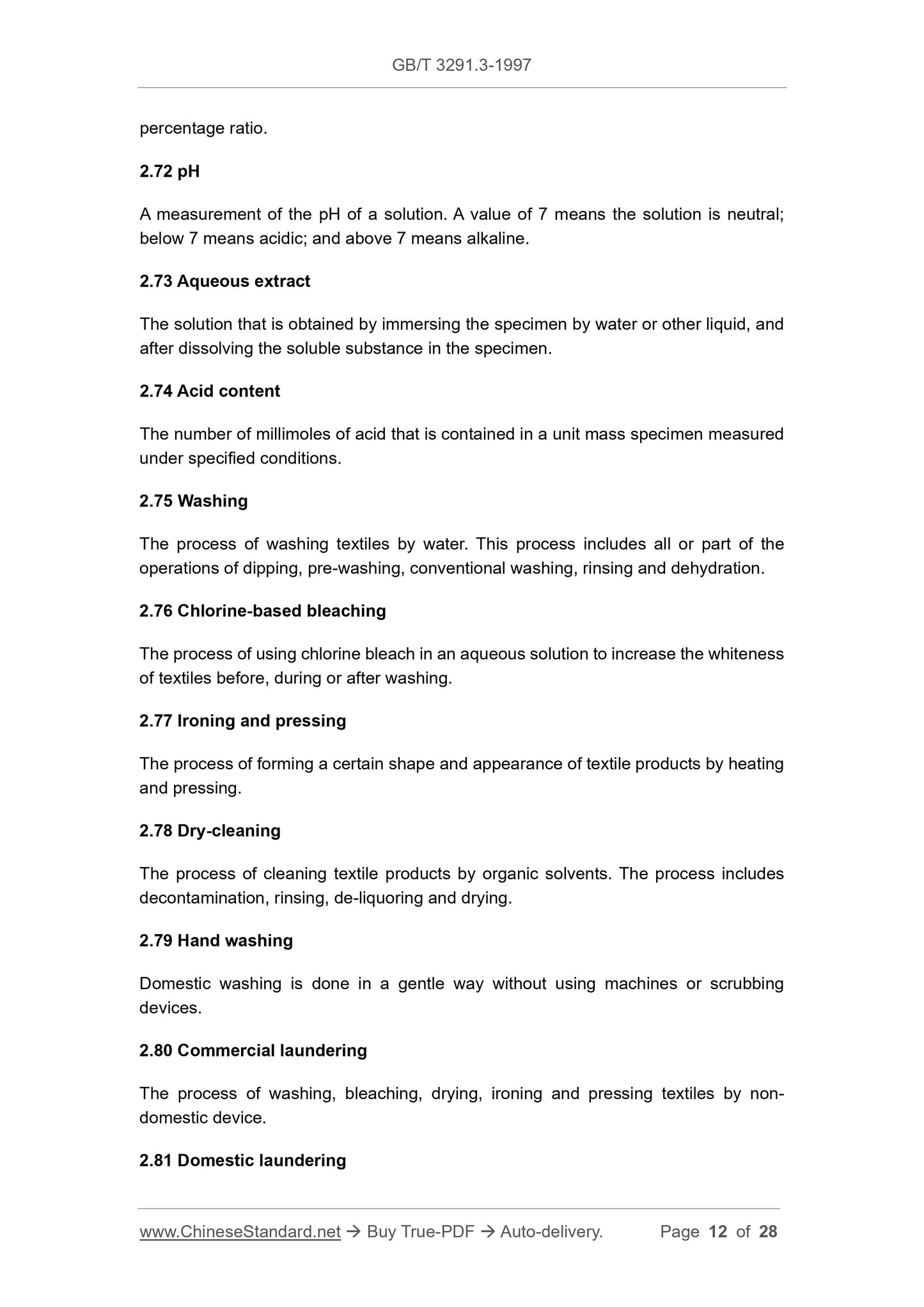
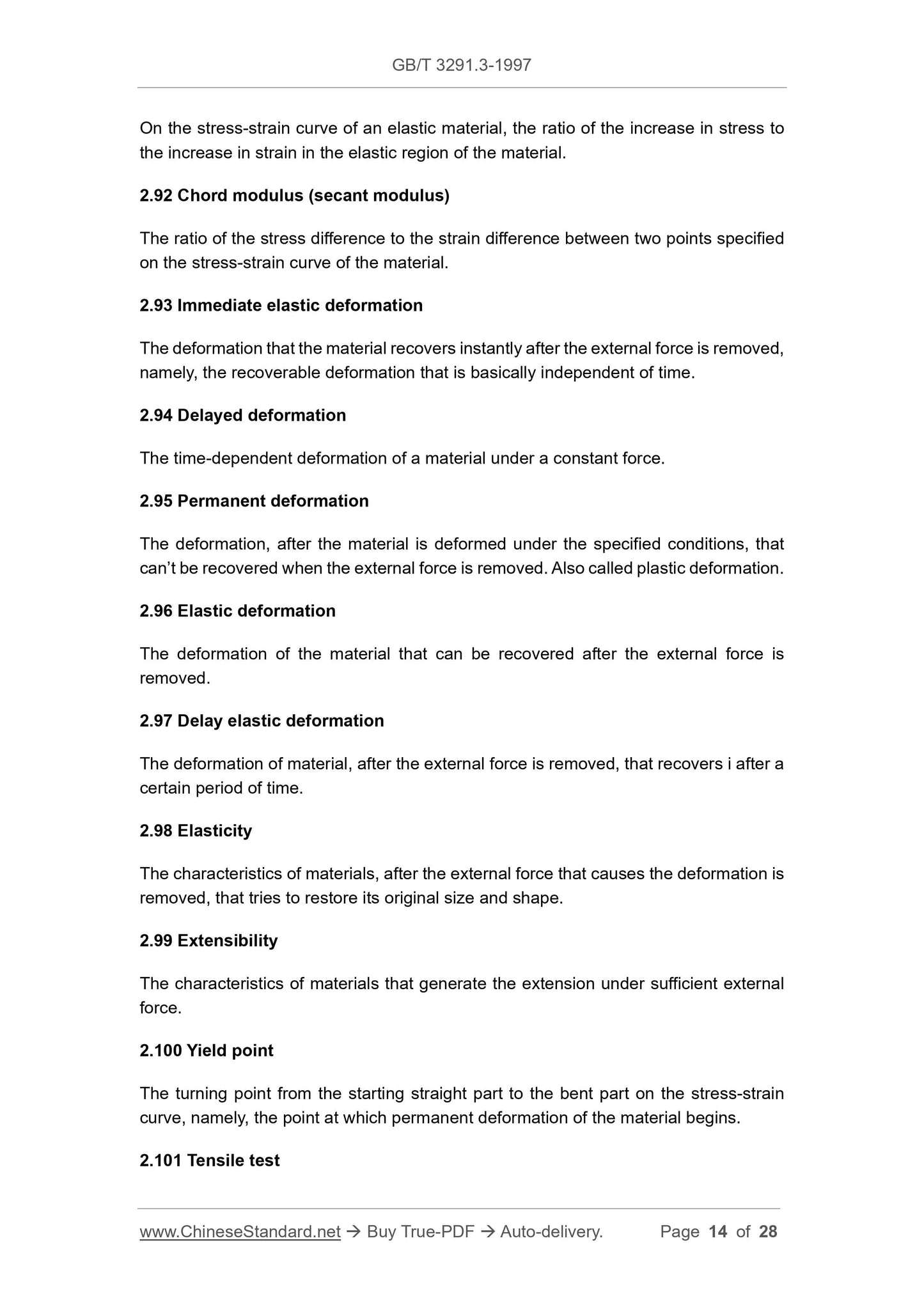
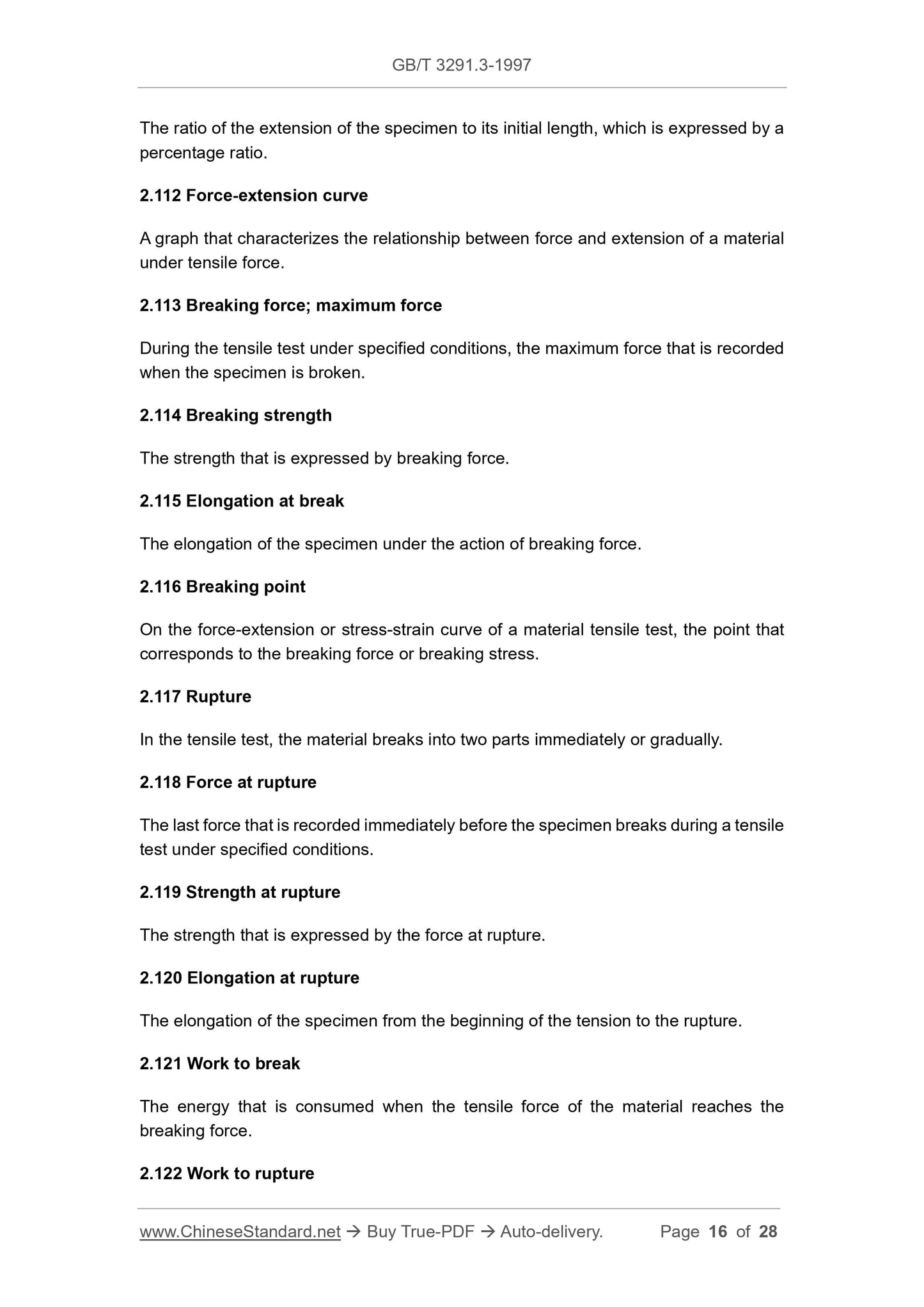
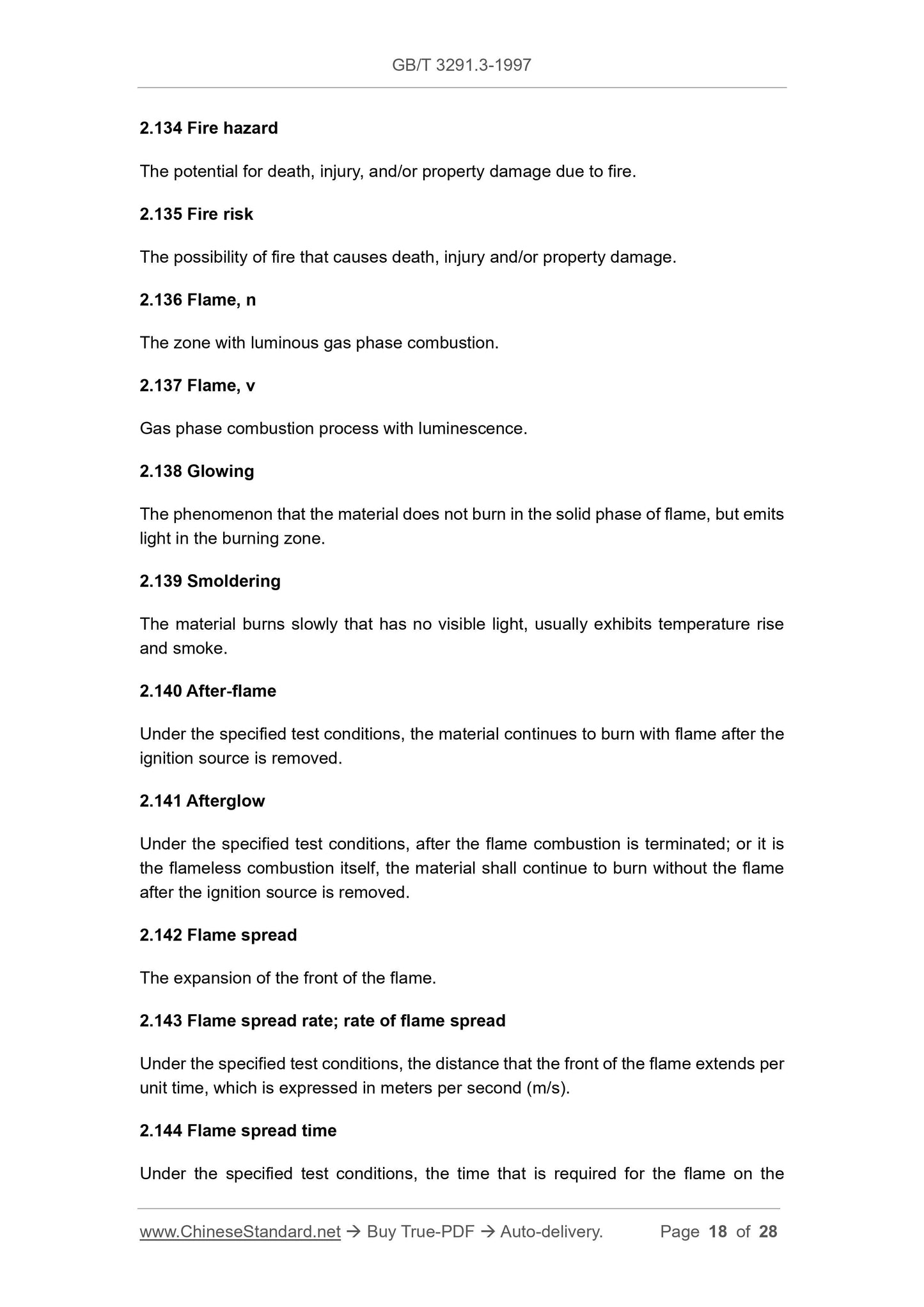
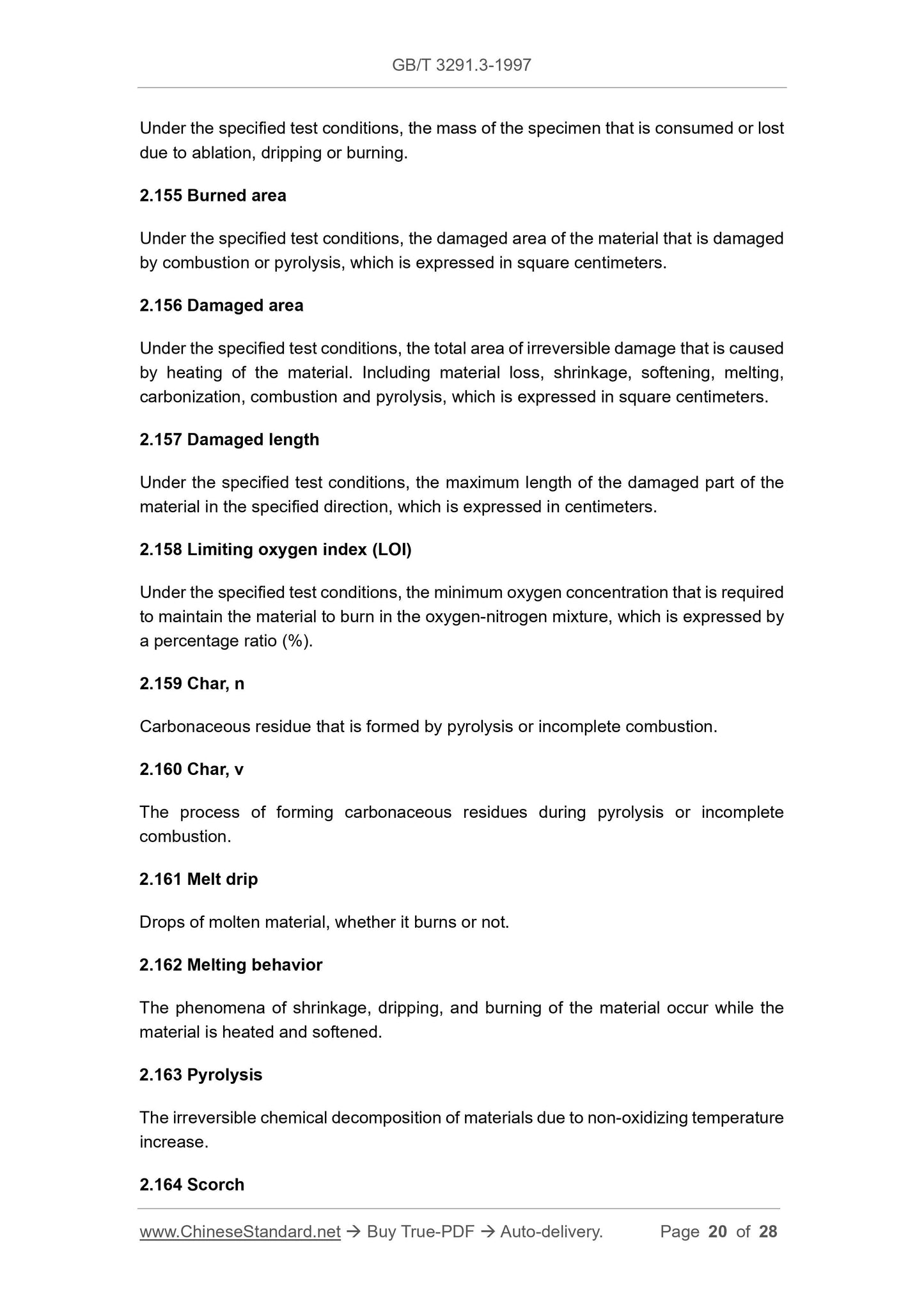
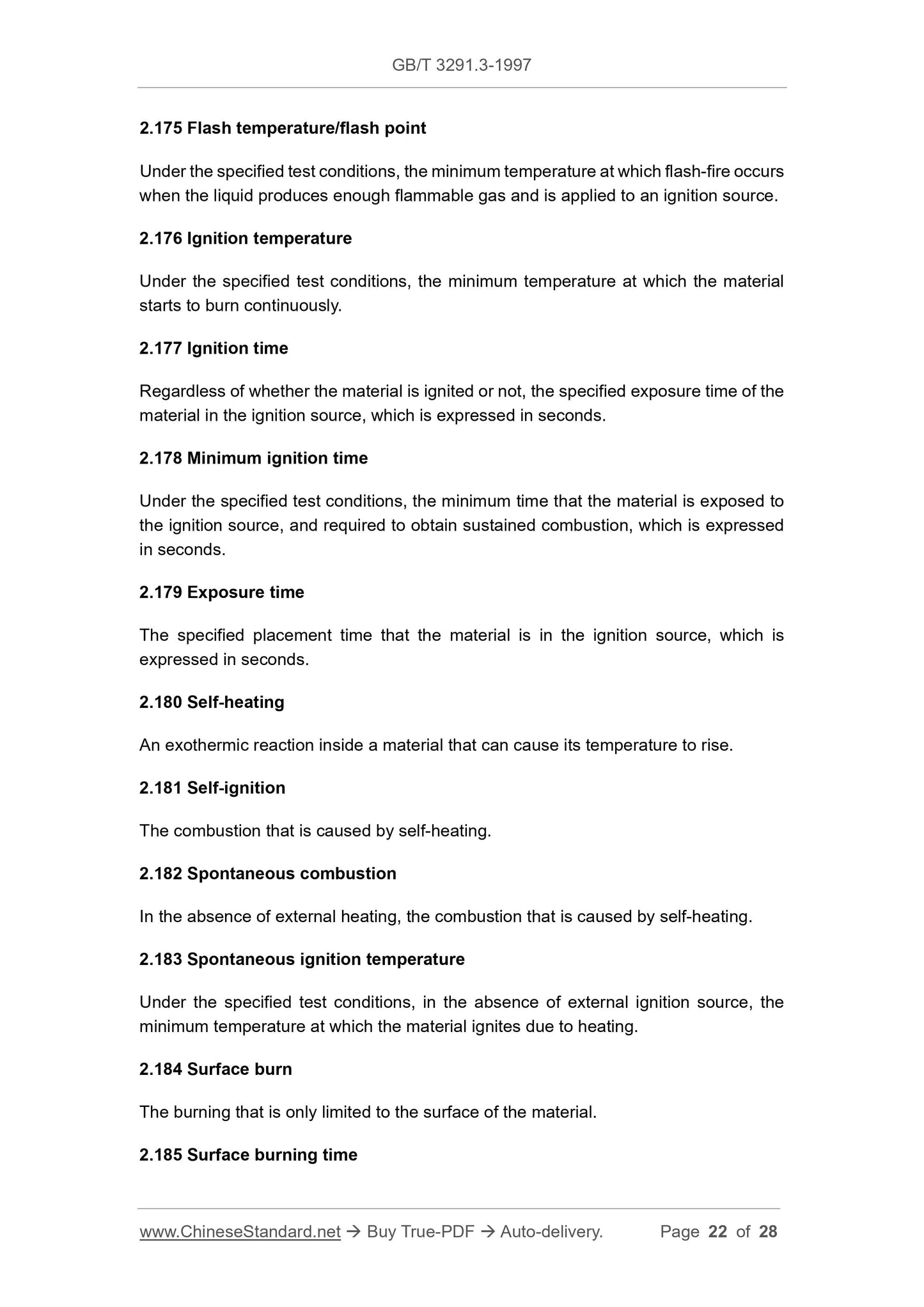