1
/
of
9
www.ChineseStandard.us -- Field Test Asia Pte. Ltd.
GB/T 3246.1-2024 English PDF (GB/T3246.1-2024)
GB/T 3246.1-2024 English PDF (GB/T3246.1-2024)
Regular price
$1,060.00
Regular price
Sale price
$1,060.00
Unit price
/
per
Shipping calculated at checkout.
Couldn't load pickup availability
GB/T 3246.1-2024: Inspection method for structure of wrought aluminium and aluminium alloy products - Part 1: Inspection method for microstructure
Delivery: 9 seconds. Download (and Email) true-PDF + Invoice.
Get Quotation: Click GB/T 3246.1-2024 (Self-service in 1-minute)
Newer / historical versions: GB/T 3246.1-2024
Preview True-PDF (Reload/Scroll-down if blank)
Delivery: 9 seconds. Download (and Email) true-PDF + Invoice.
Get Quotation: Click GB/T 3246.1-2024 (Self-service in 1-minute)
Newer / historical versions: GB/T 3246.1-2024
Preview True-PDF (Reload/Scroll-down if blank)
Share
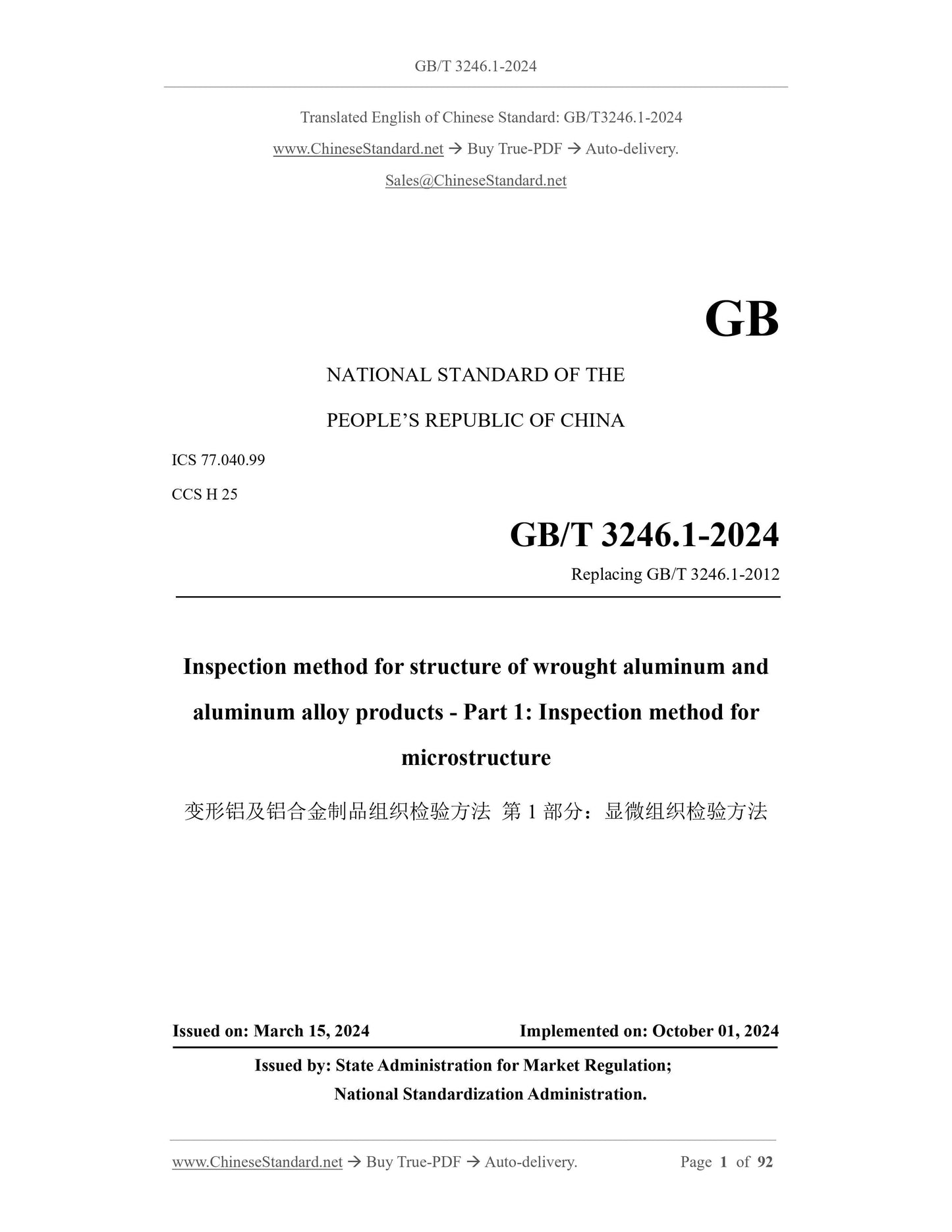
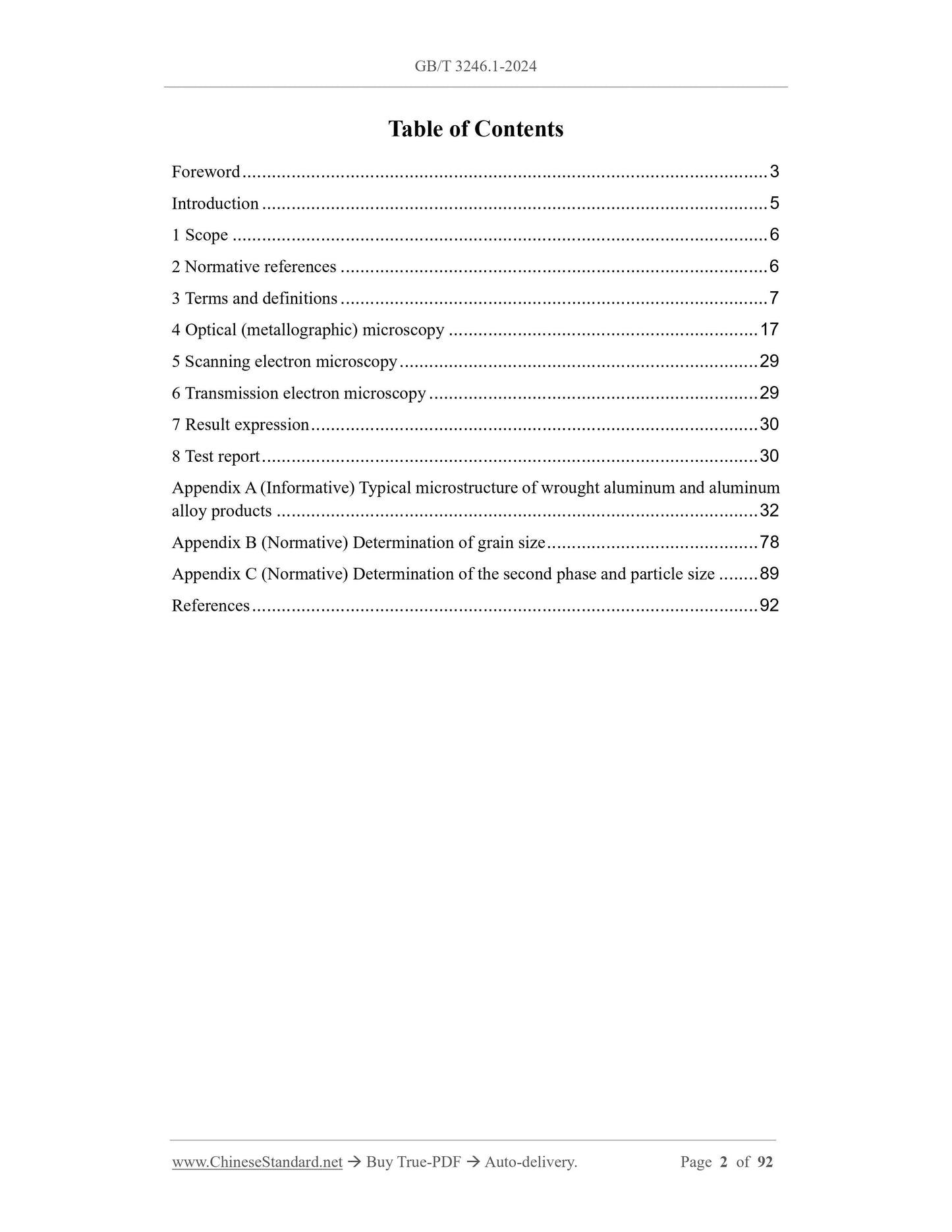
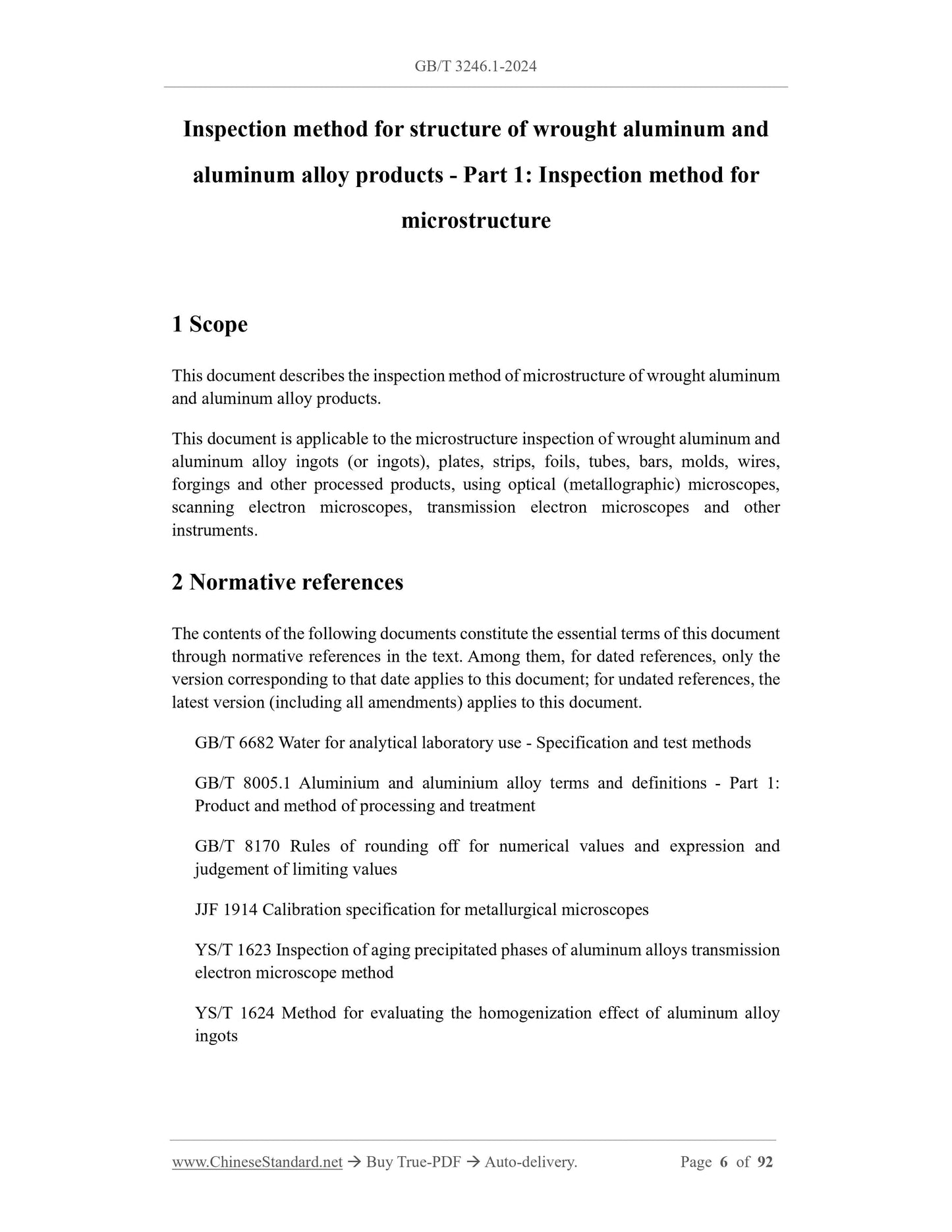
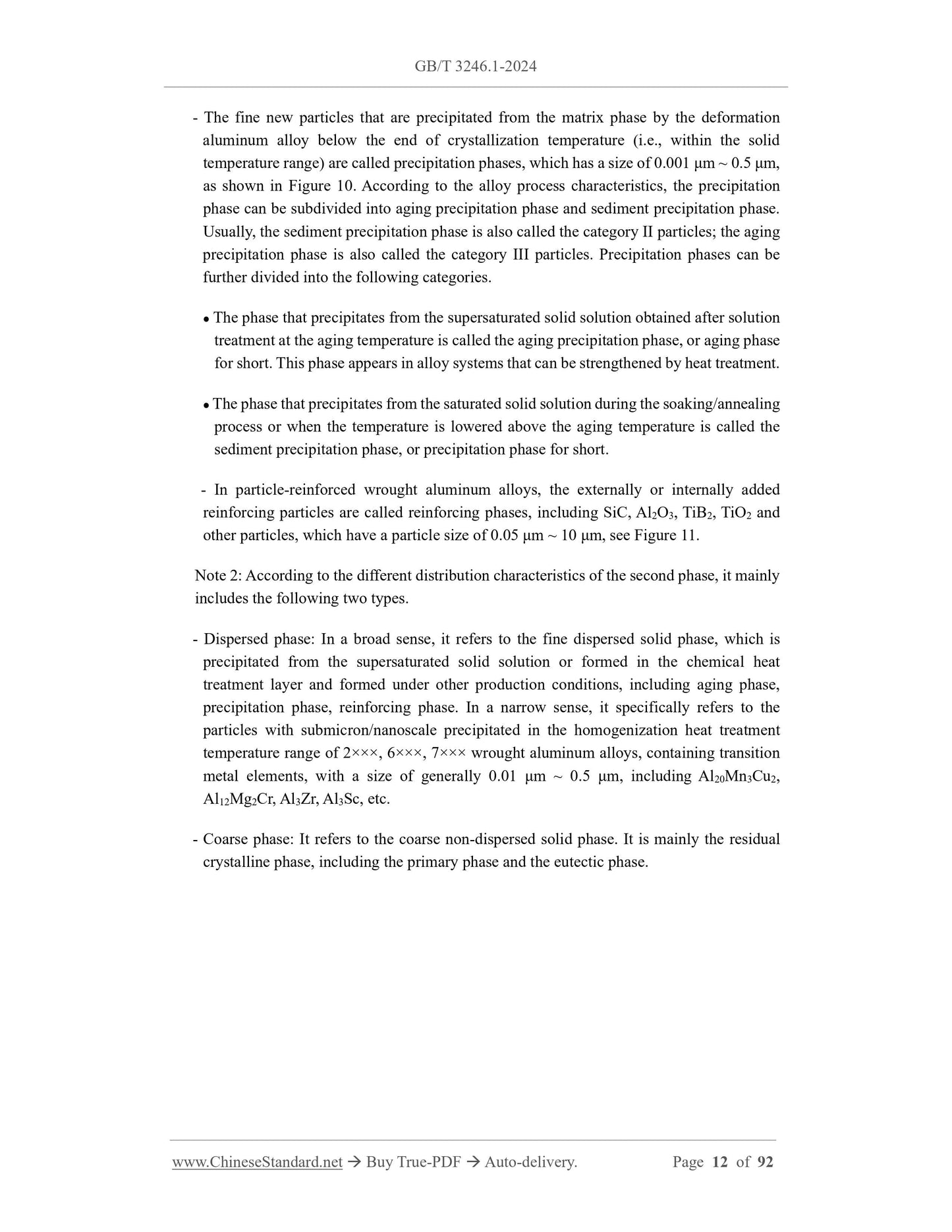
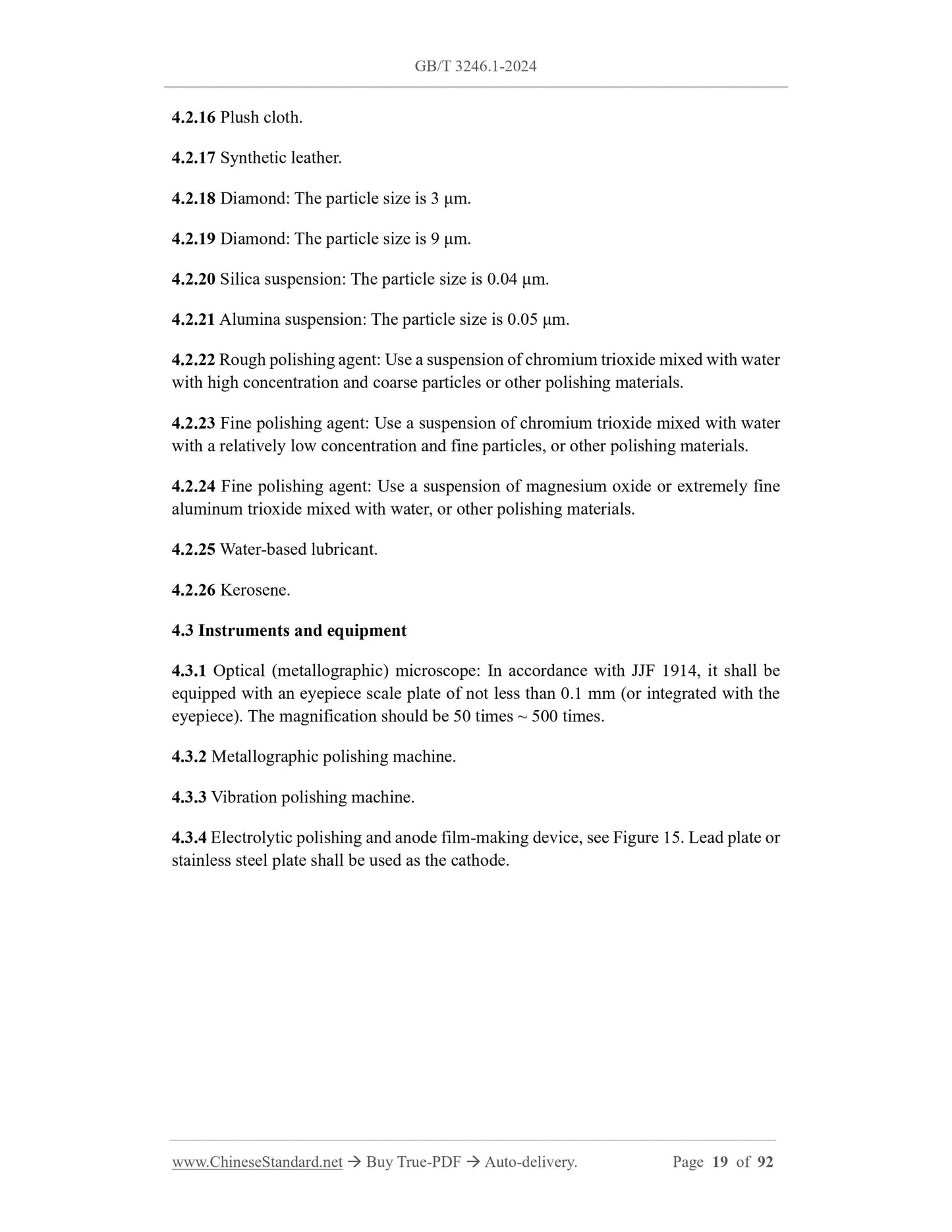
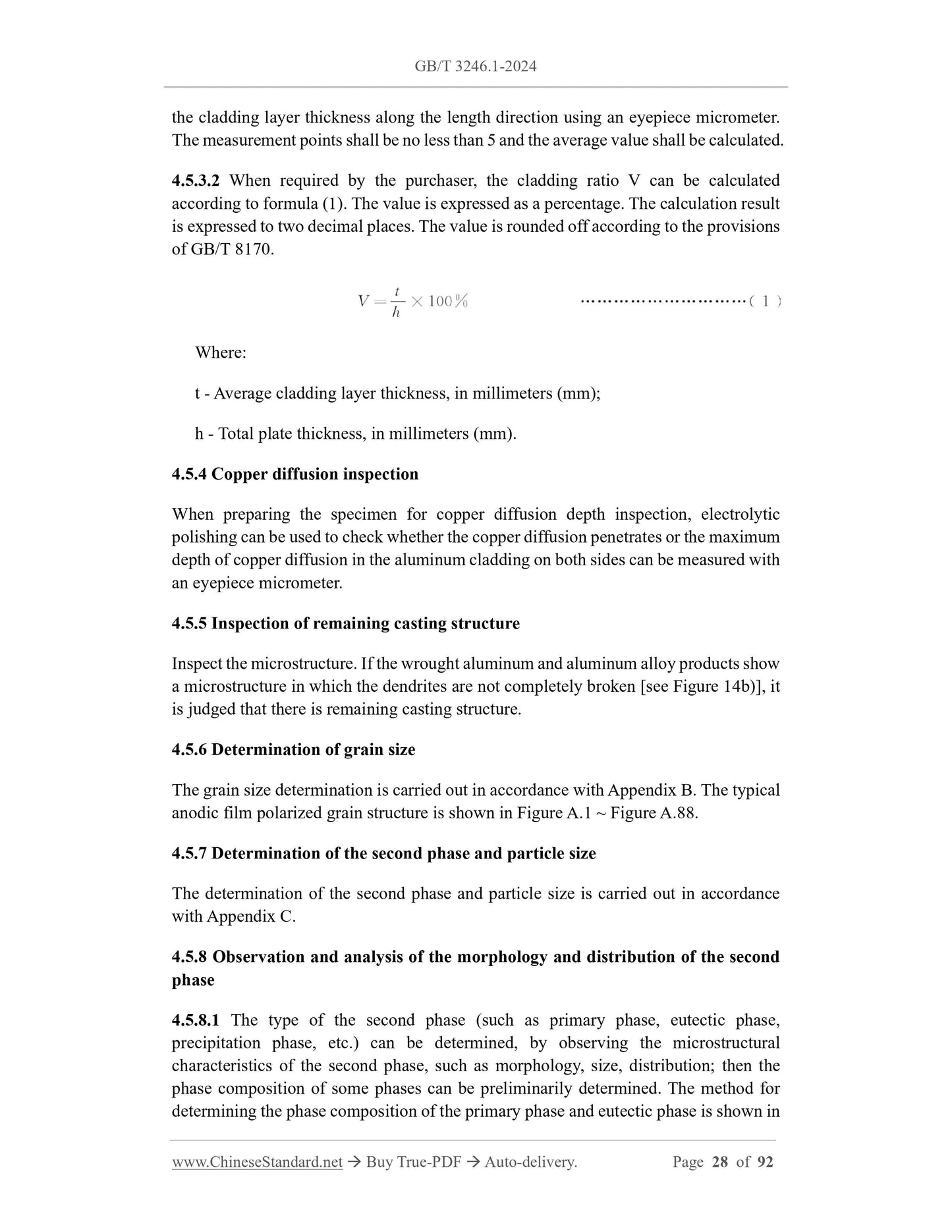
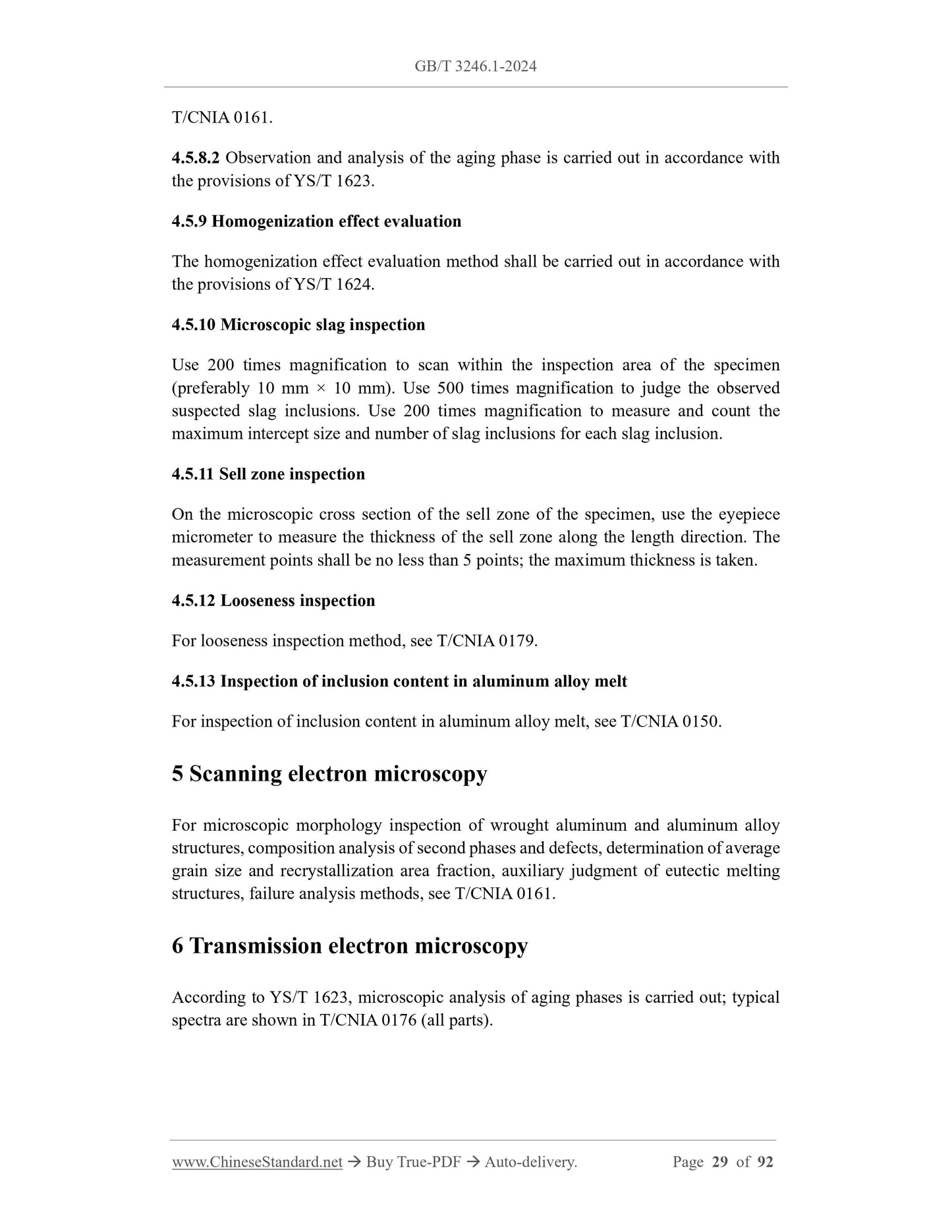
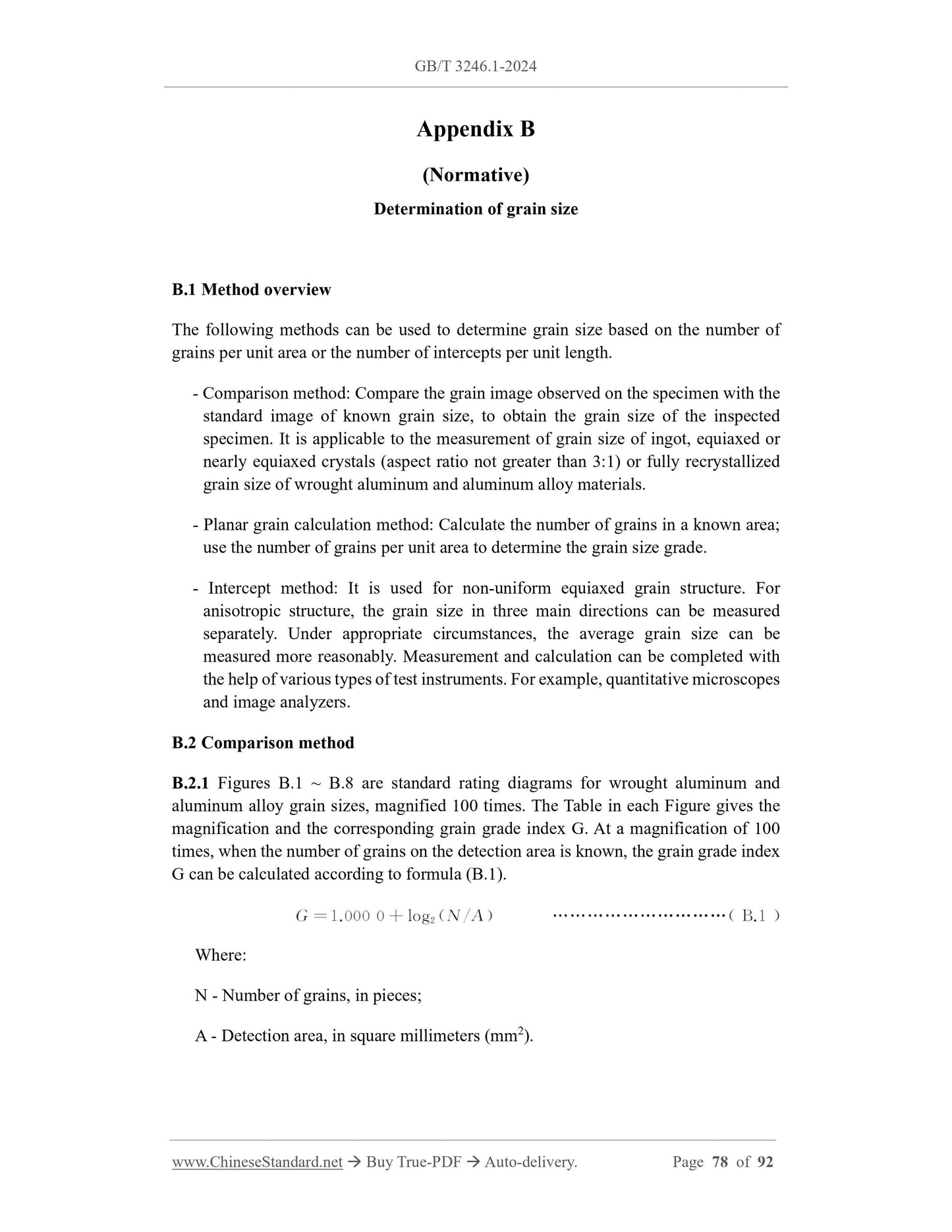
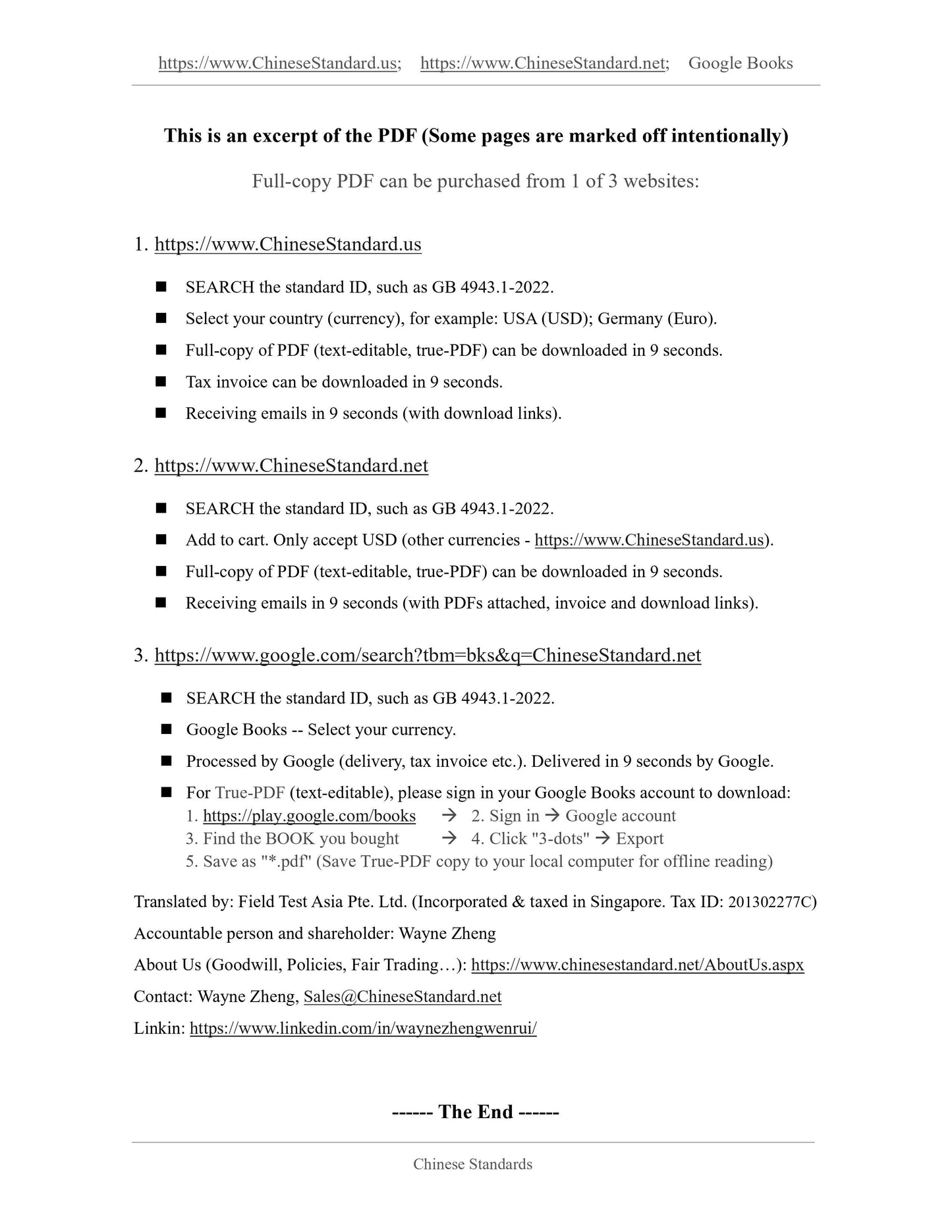