1
/
of
6
PayPal, credit cards. Download editable-PDF and invoice in 1 second!
GB/T 3246.1-2012 English PDF (GB/T3246.1-2012)
GB/T 3246.1-2012 English PDF (GB/T3246.1-2012)
Regular price
$315.00
Regular price
Sale price
$315.00
Unit price
/
per
Shipping calculated at checkout.
Couldn't load pickup availability
GB/T 3246.1-2012: Inspection method for structure of wrought aluminum and aluminum alloy products -- Part 1: Inspection method for microstructure
Delivery: 9 seconds. Download (and Email) true-PDF + Invoice.
Newer version: (Replacing this standard) GB/T 3246.1-2024
Get Quotation: Click GB/T 3246.1-2012 (Self-service in 1-minute)
Newer / historical versions: GB/T 3246.1-2024
Preview True-PDF (Reload/Scroll-down if blank)
Delivery: 9 seconds. Download (and Email) true-PDF + Invoice.
Newer version: (Replacing this standard) GB/T 3246.1-2024
Get Quotation: Click GB/T 3246.1-2012 (Self-service in 1-minute)
Newer / historical versions: GB/T 3246.1-2024
Preview True-PDF (Reload/Scroll-down if blank)
Share
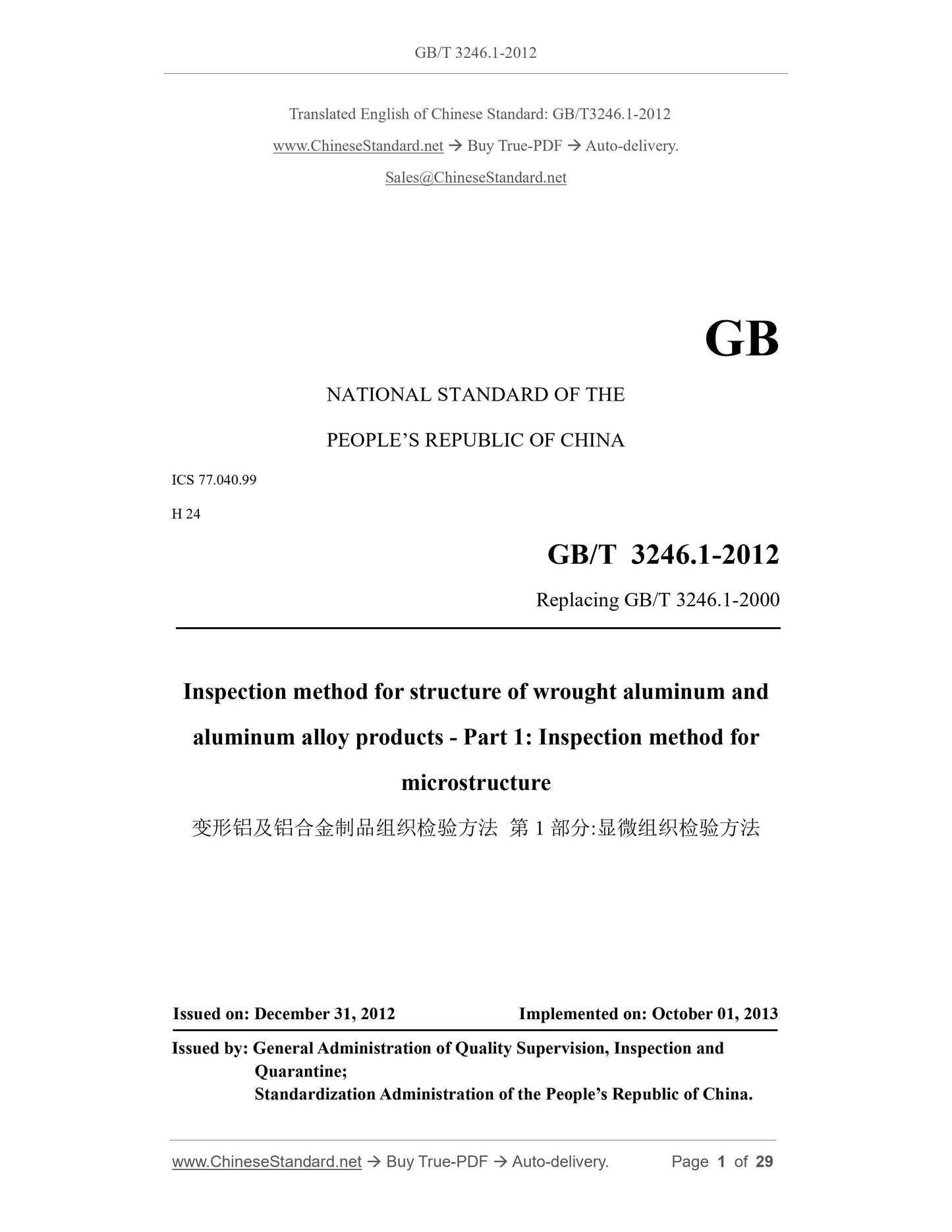
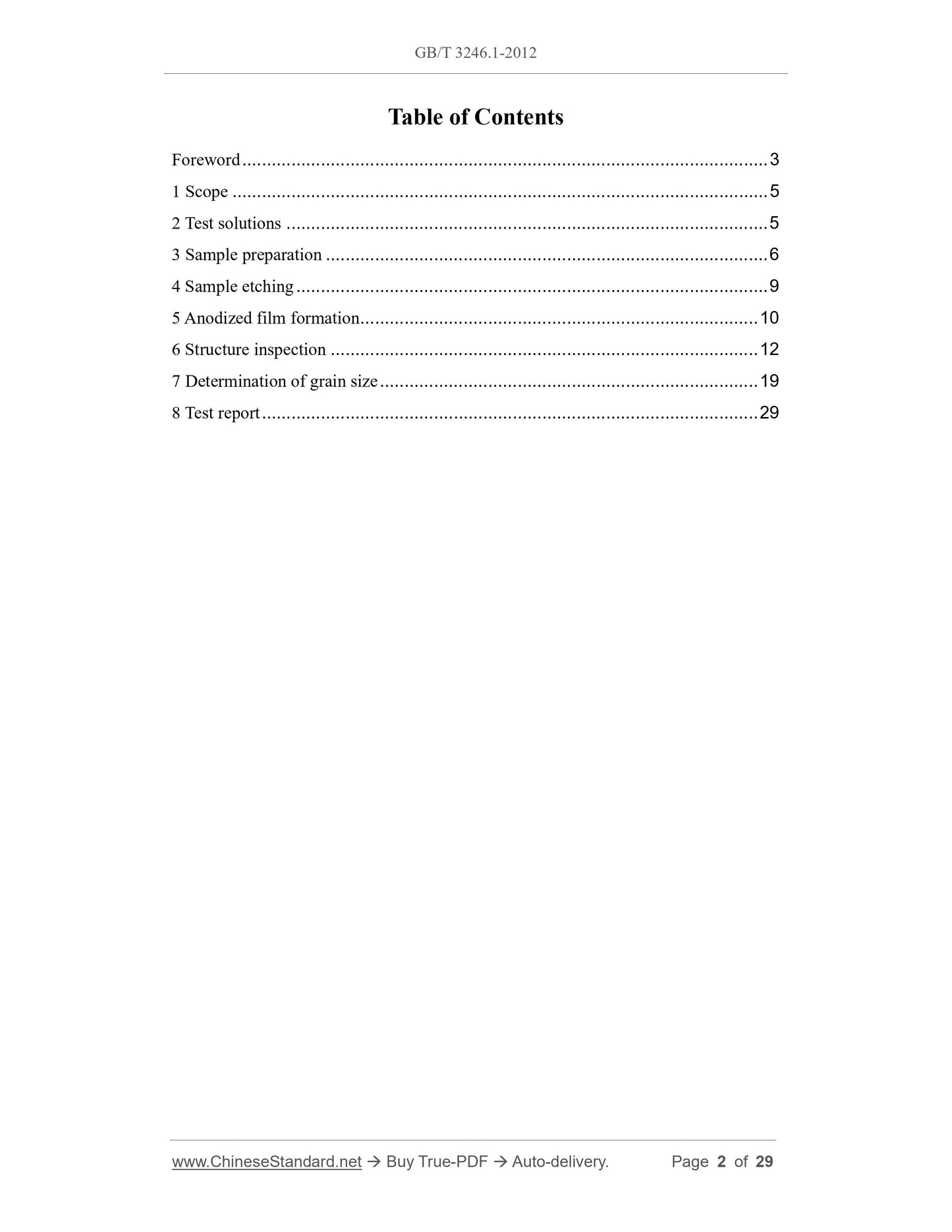
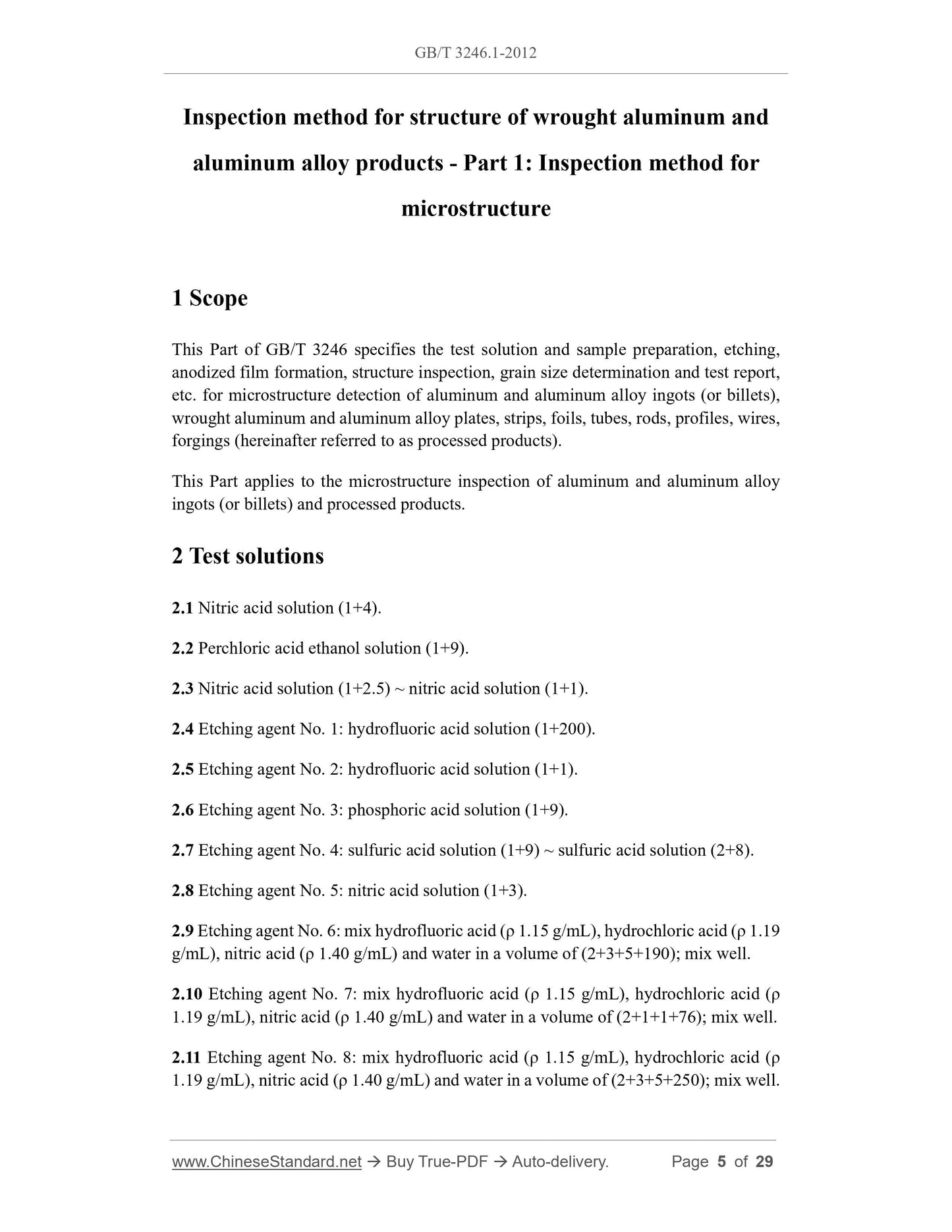
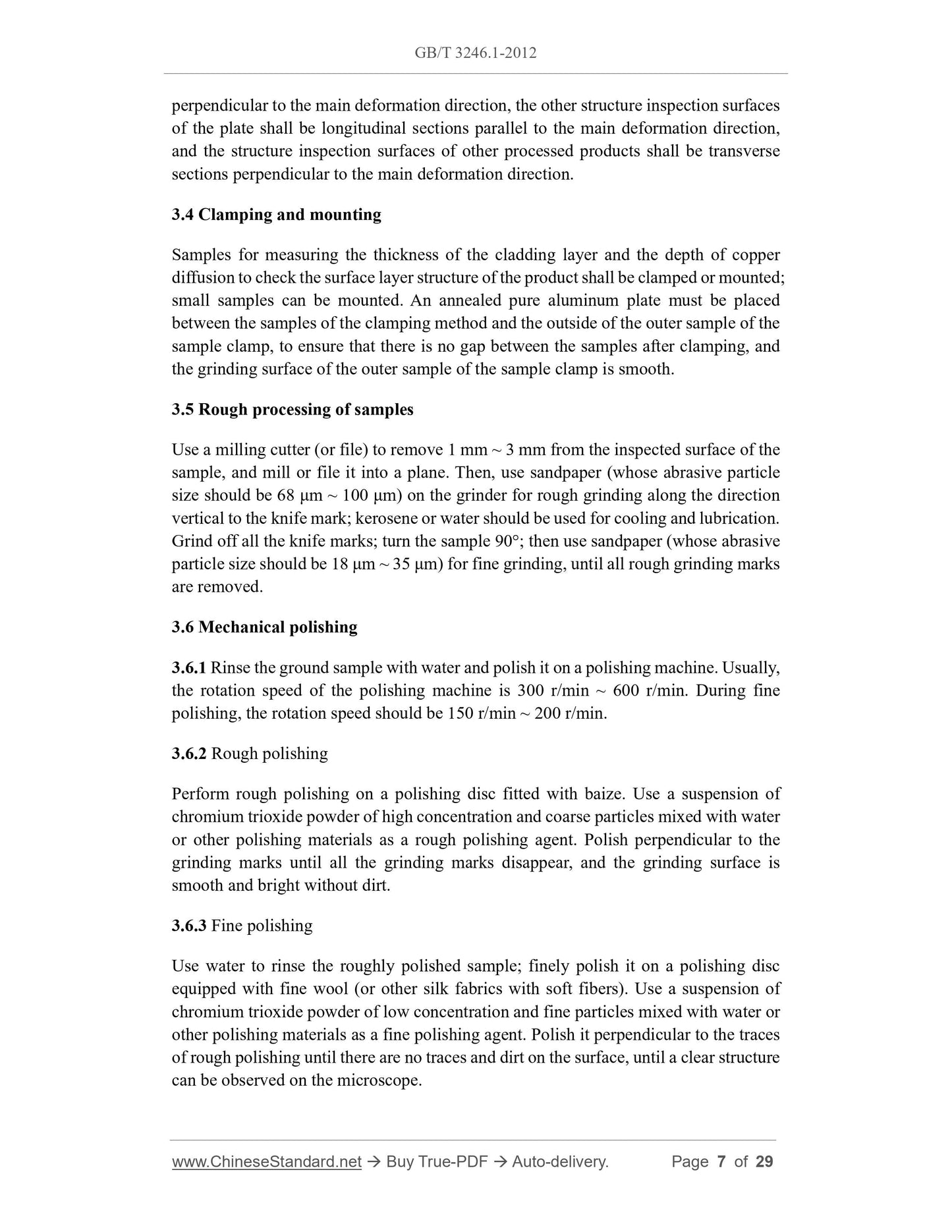
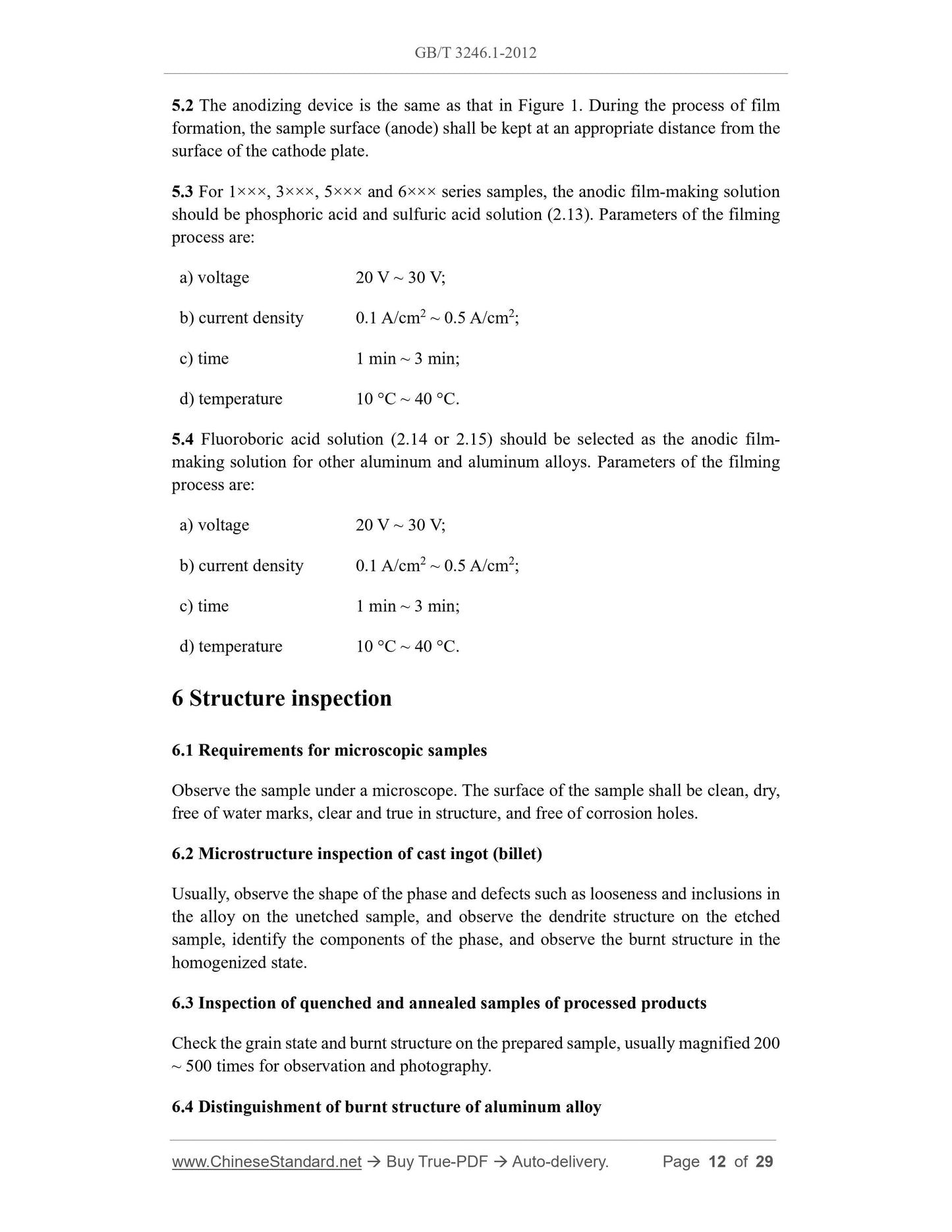
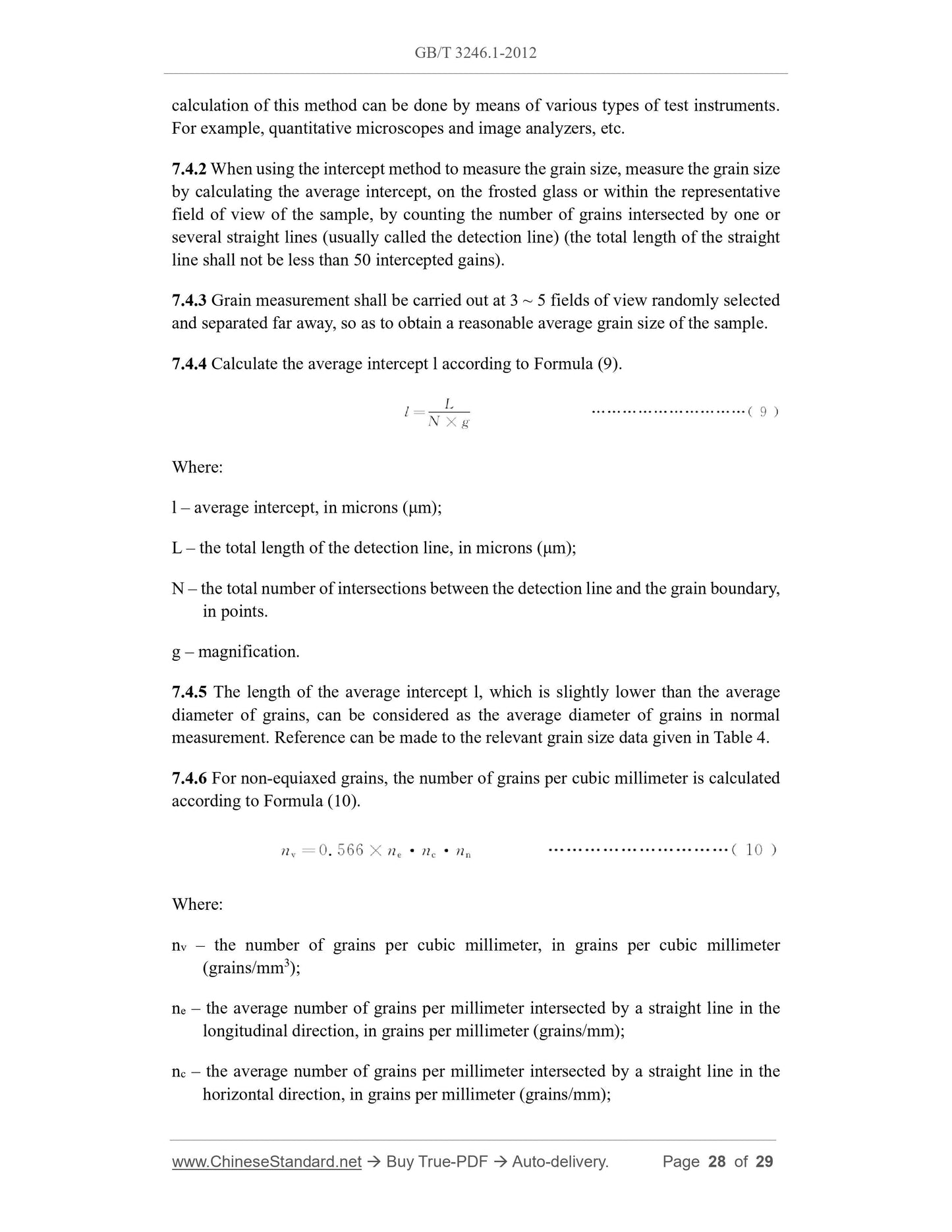