1
/
of
12
www.ChineseStandard.us -- Field Test Asia Pte. Ltd.
GB/T 30092-2013 English PDF (GB/T30092-2013)
GB/T 30092-2013 English PDF (GB/T30092-2013)
Regular price
$400.00
Regular price
Sale price
$400.00
Unit price
/
per
Shipping calculated at checkout.
Couldn't load pickup availability
GB/T 30092-2013: Metal bellows compensator used in high voltage combined electrical appliance
Delivery: 9 seconds. Download (and Email) true-PDF + Invoice.Get Quotation: Click GB/T 30092-2013 (Self-service in 1-minute)
Newer / historical versions: GB/T 30092-2013
Preview True-PDF
Scope
This Standard specifies the product classification, requirements, test methods,inspection rules, as well as marking, packaging and storage of metal bellows
compensator used in high voltage combined electrical appliance (hereinafter referred to
as compensator).
This Standard applies to metal bellows compensator used in high voltage combined
electrical appliance.
Basic Data
Standard ID | GB/T 30092-2013 (GB/T30092-2013) |
Description (Translated English) | Metal bellows compensator used in high voltage combined electrical appliance |
Sector / Industry | National Standard (Recommended) |
Classification of Chinese Standard | K43 |
Classification of International Standard | 29.130.10 |
Word Count Estimation | 26,288 |
Quoted Standard | GB/T 1173; GB/T 1222; GB/T 1958-2004; GB/T 1972-2005; GB/T 2829-2002; GB/T 3274; GB/T 3280; GB/T 4237; GB 7674-2008; GB/T 8163; GB/T 11023-1989; GB/T 14976; GB 16749-1997; JB/T 4711-2003; JB/T 4730.2-2005; JB/T 4730.5-2005 |
Regulation (derived from) | National Standards Bulletin No. 25 of 2013 |
Issuing agency(ies) | General Administration of Quality Supervision, Inspection and Quarantine of the People's Republic of China, Standardization Administration of the People's Republic of China |
Summary | This standard specifies the combination of high-voltage electrical metal bellows compensator (hereinafter referred to as compensation) product classification, requirements, test methods, inspection rules and signs, packaging and storage. This standard app |
Share
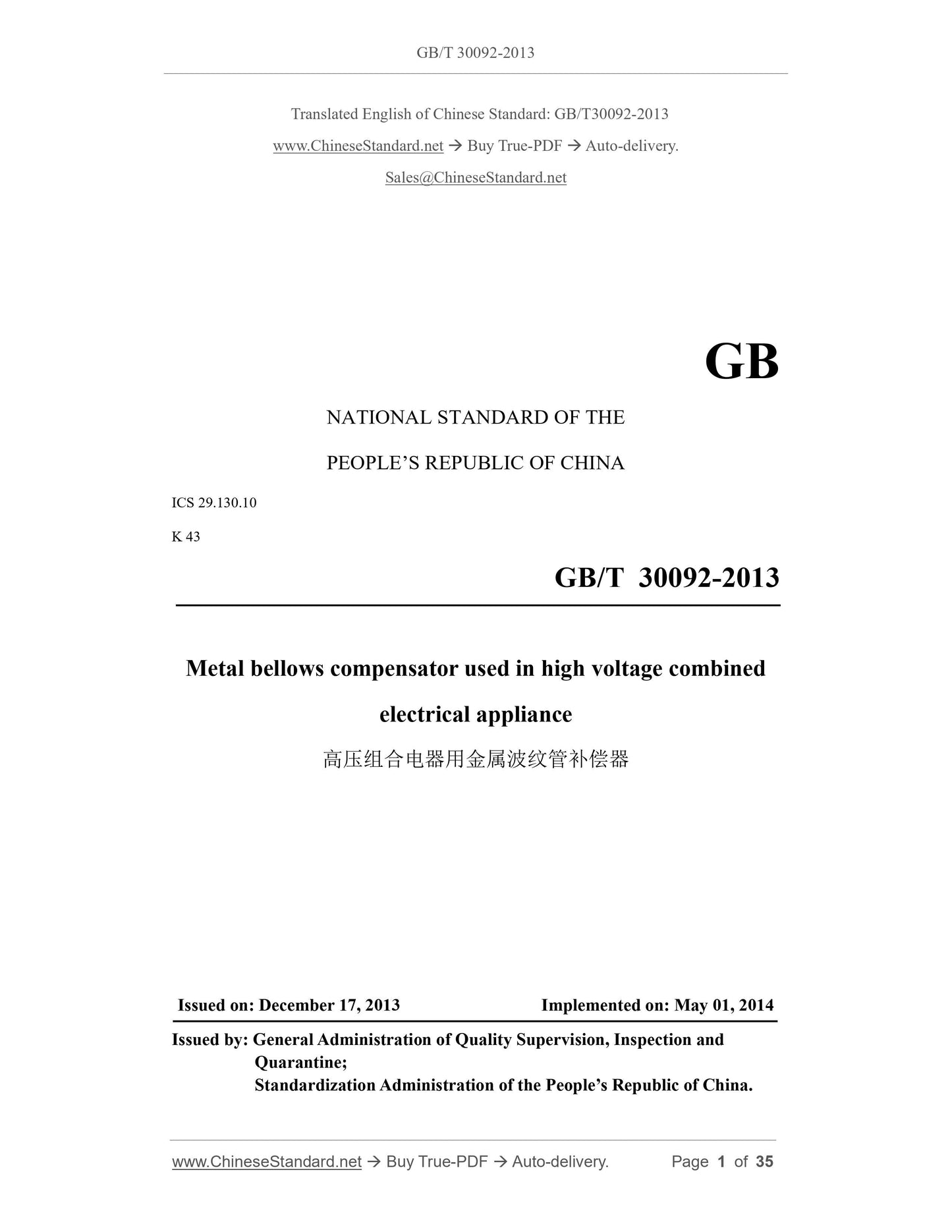
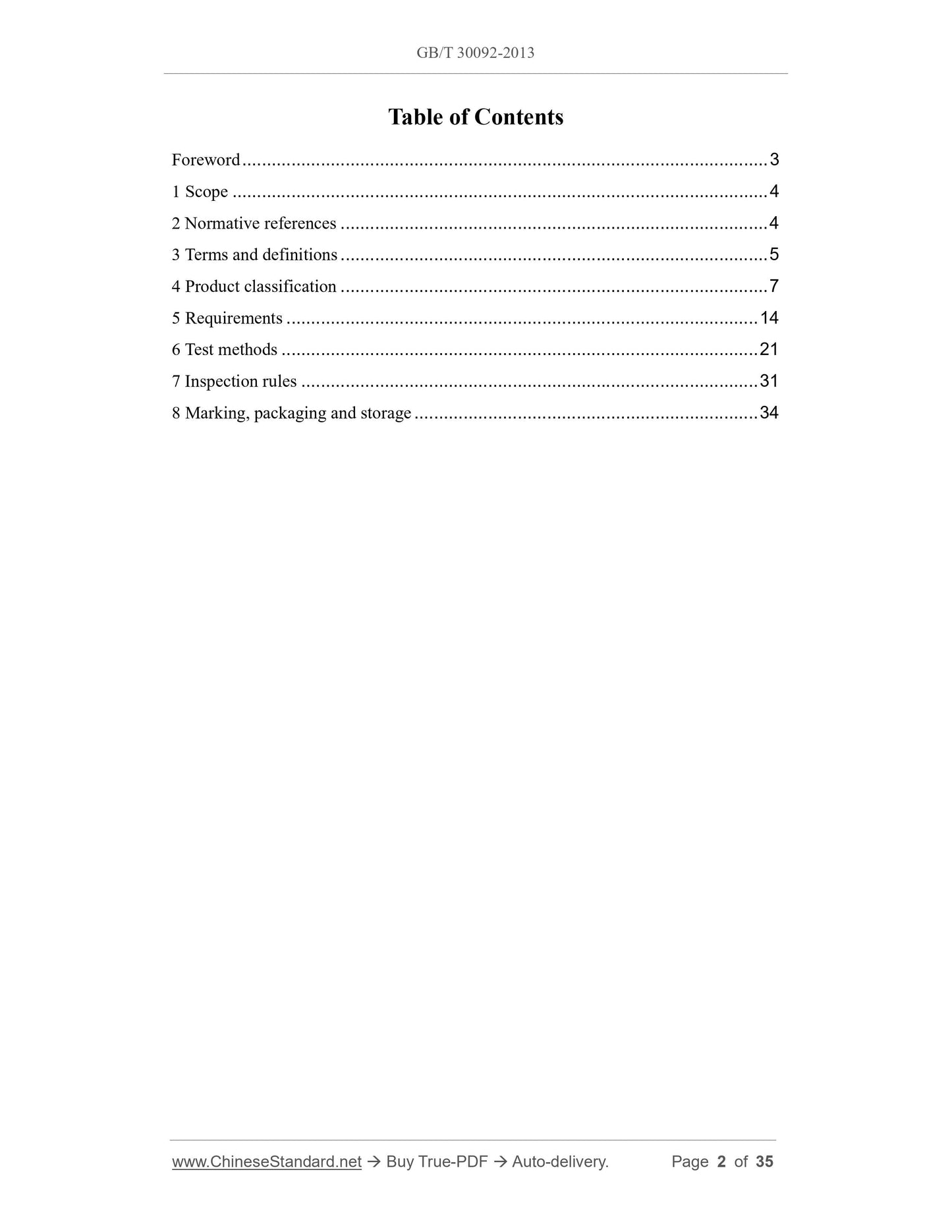
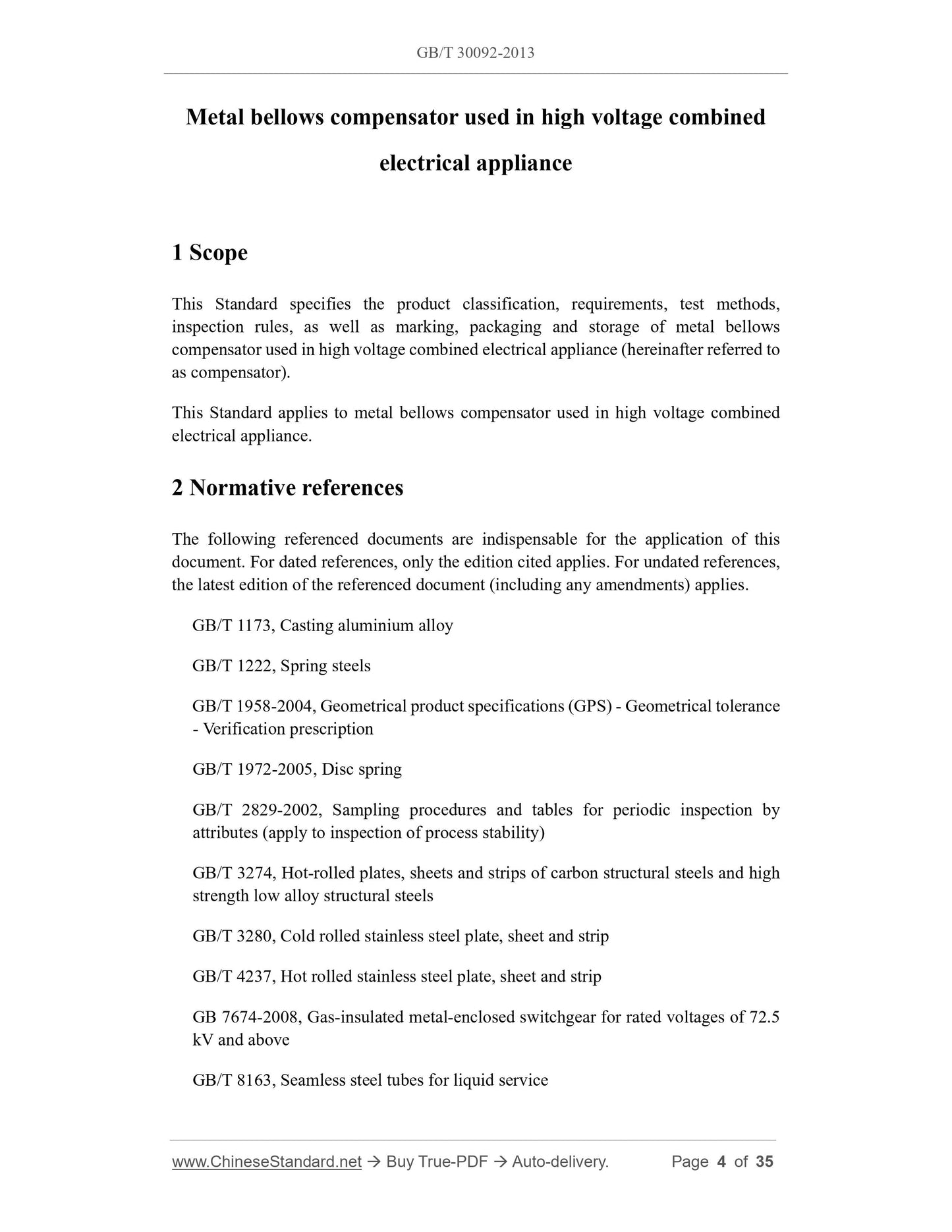
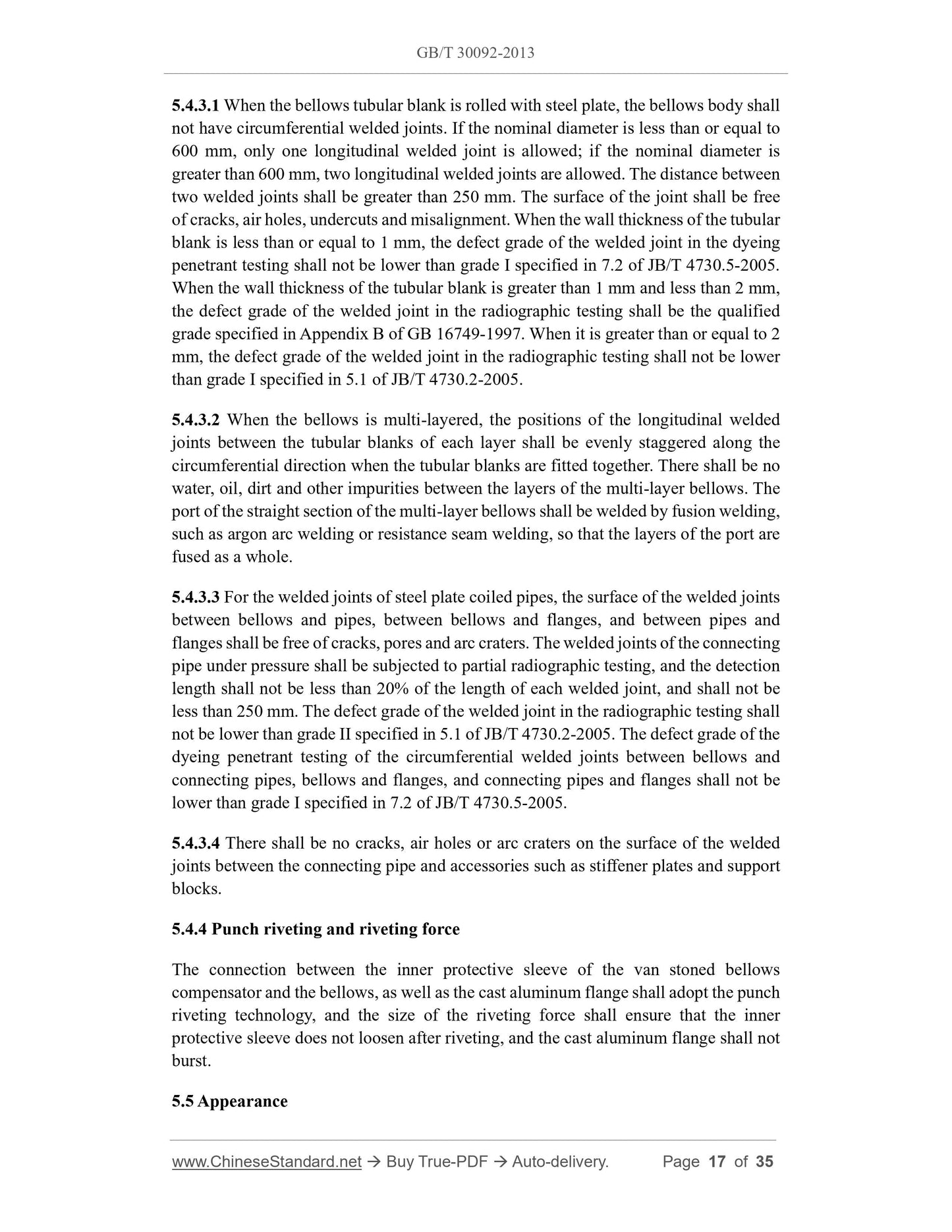
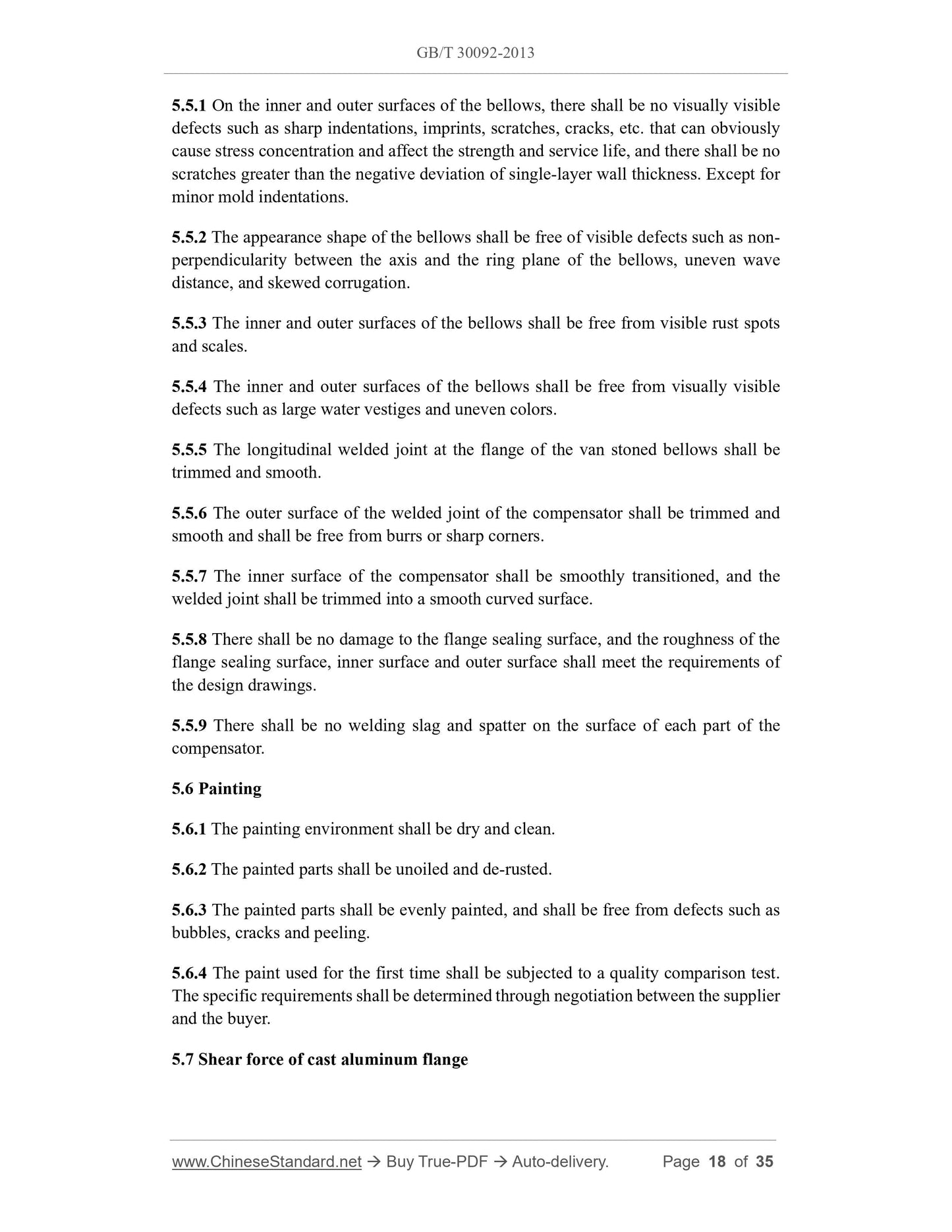
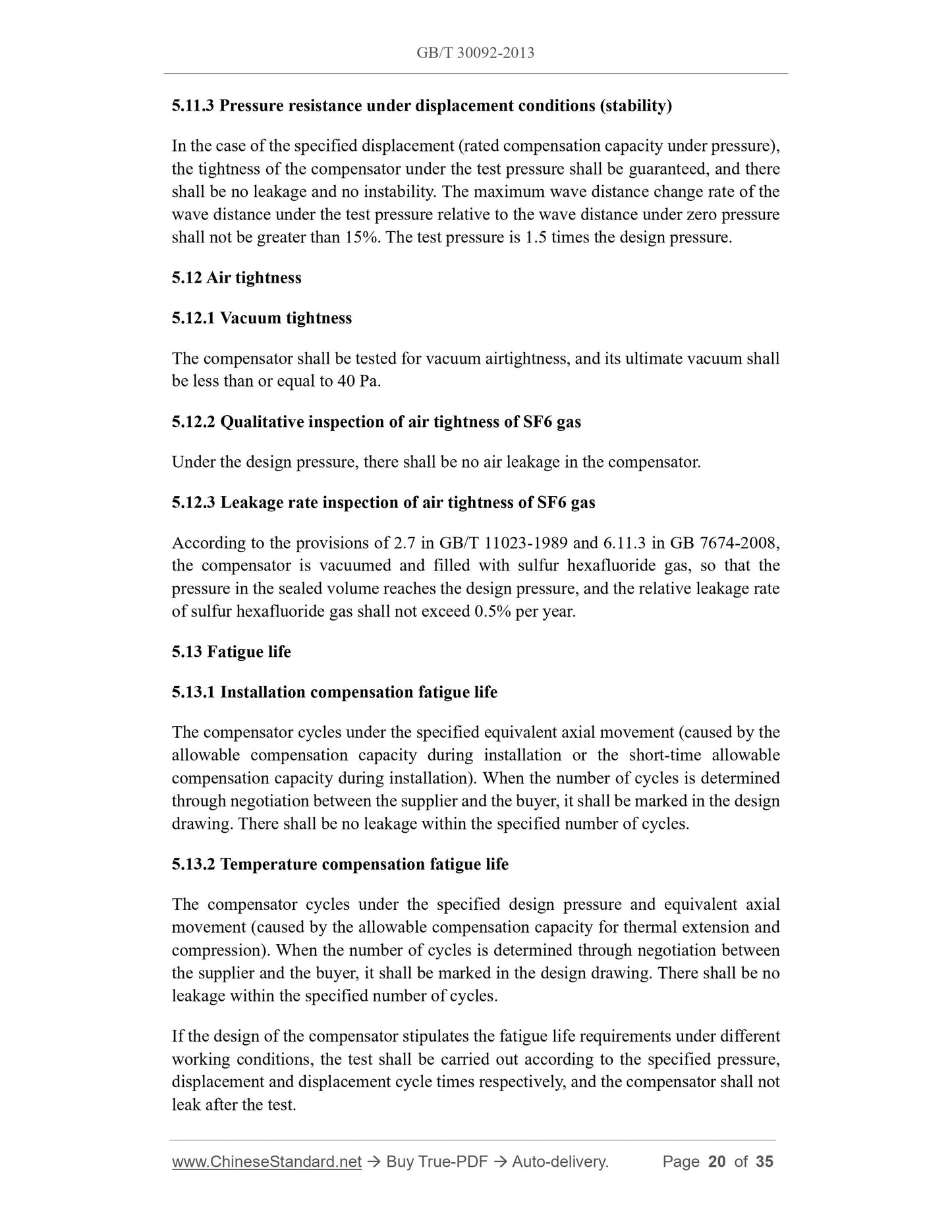
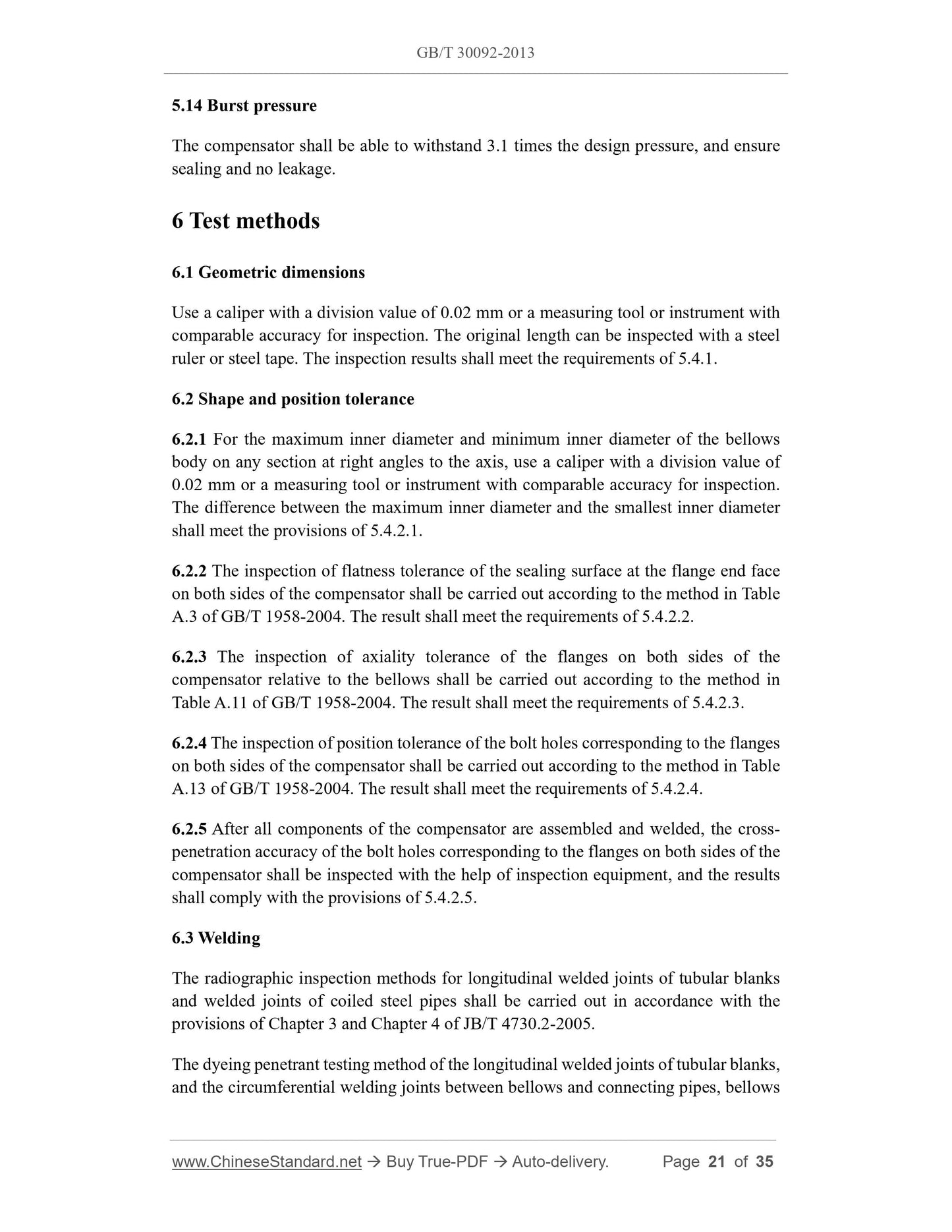
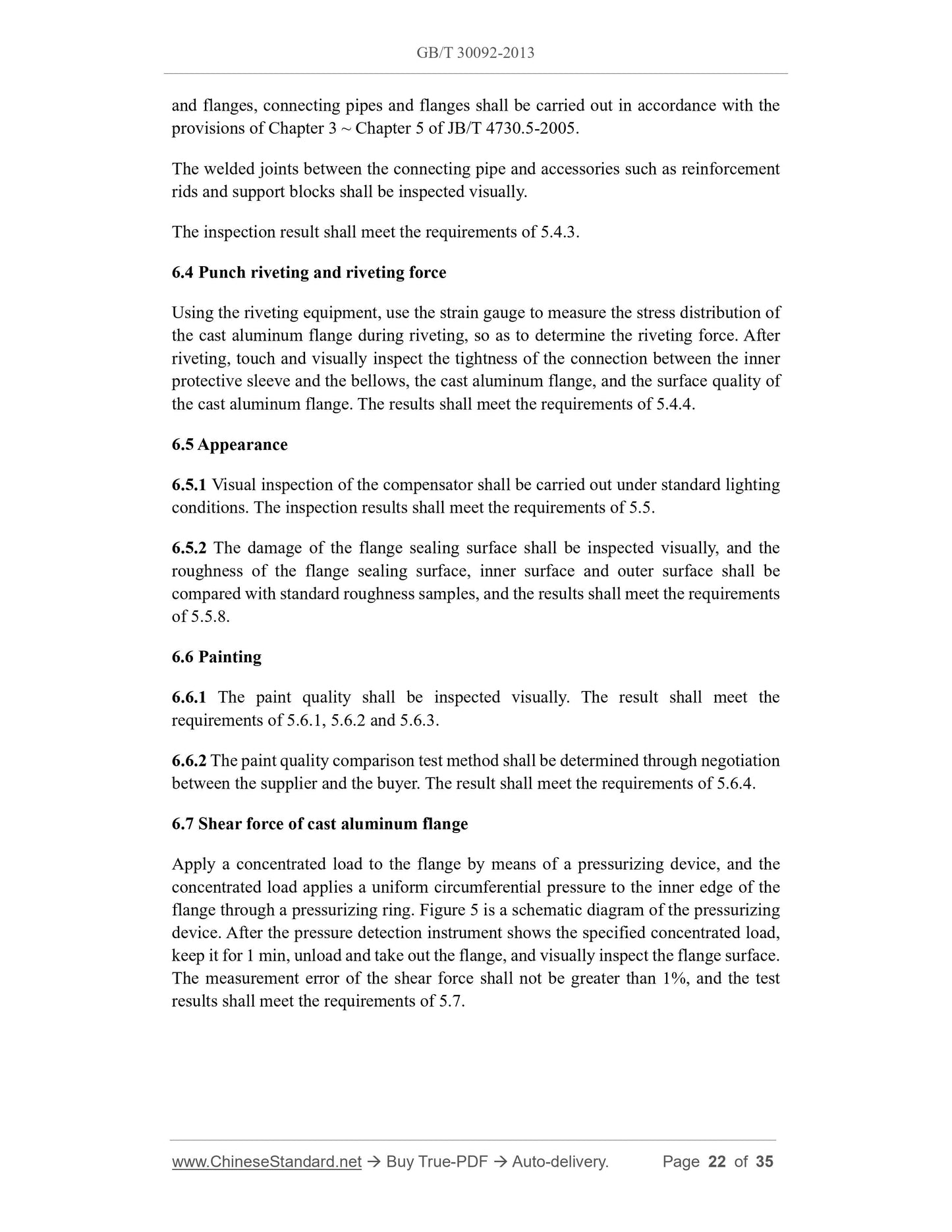
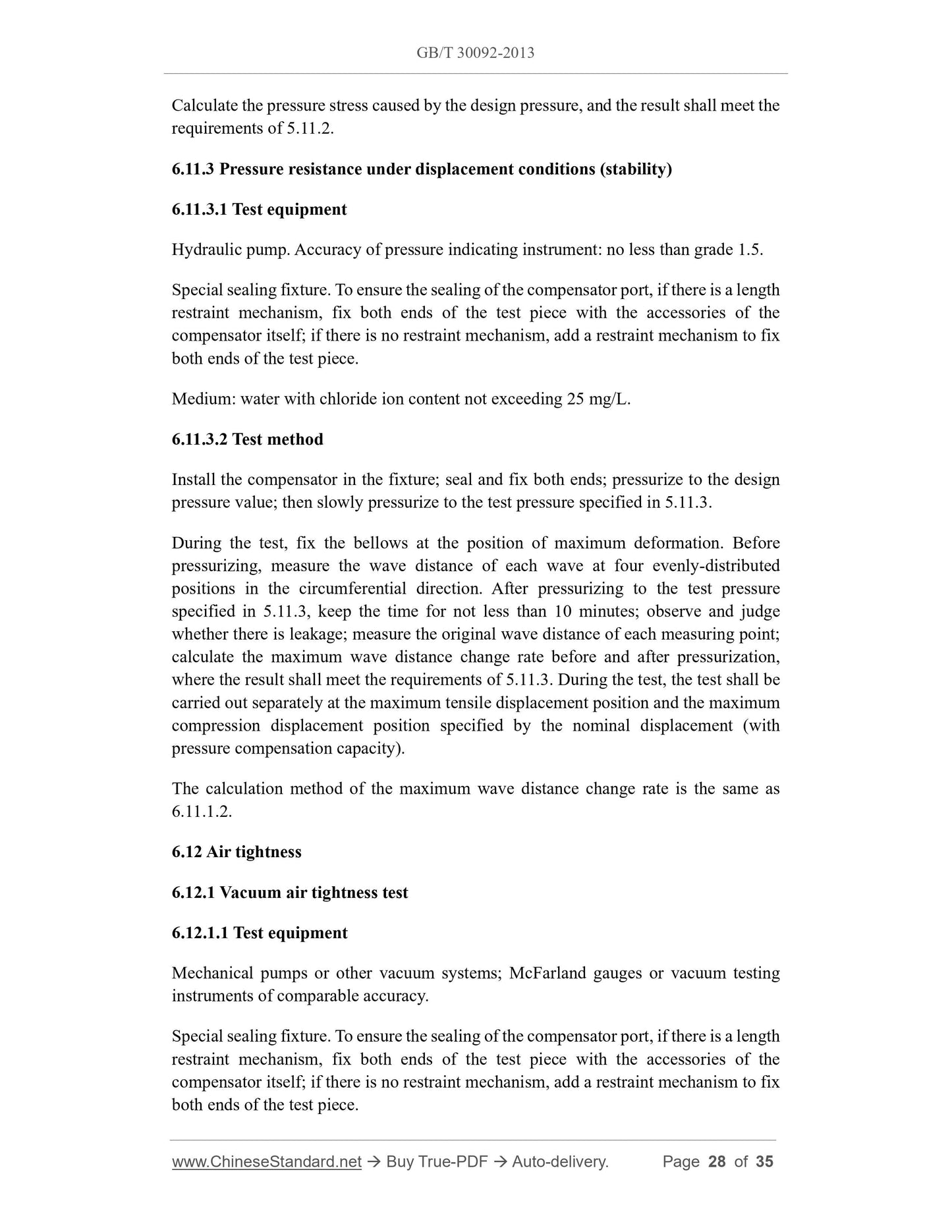
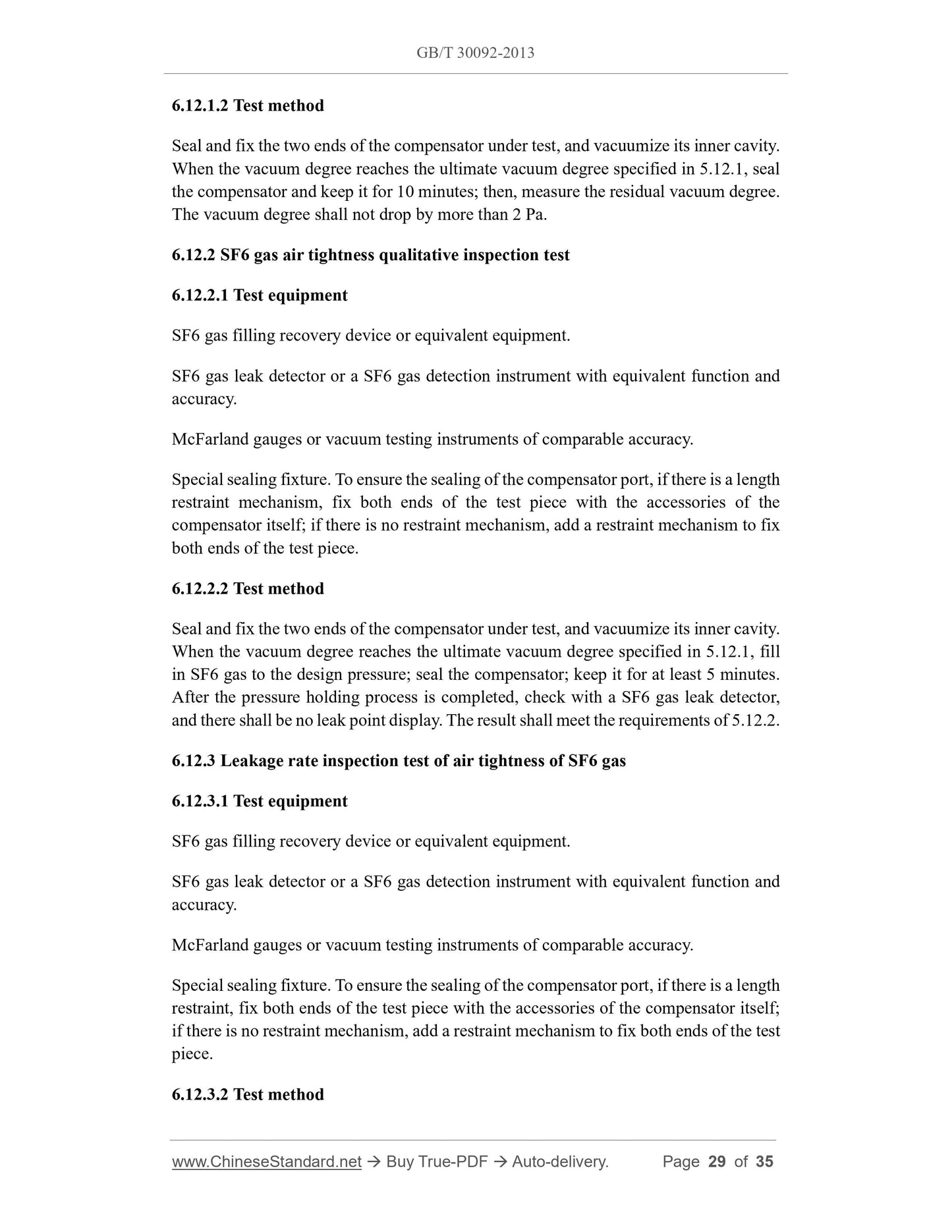
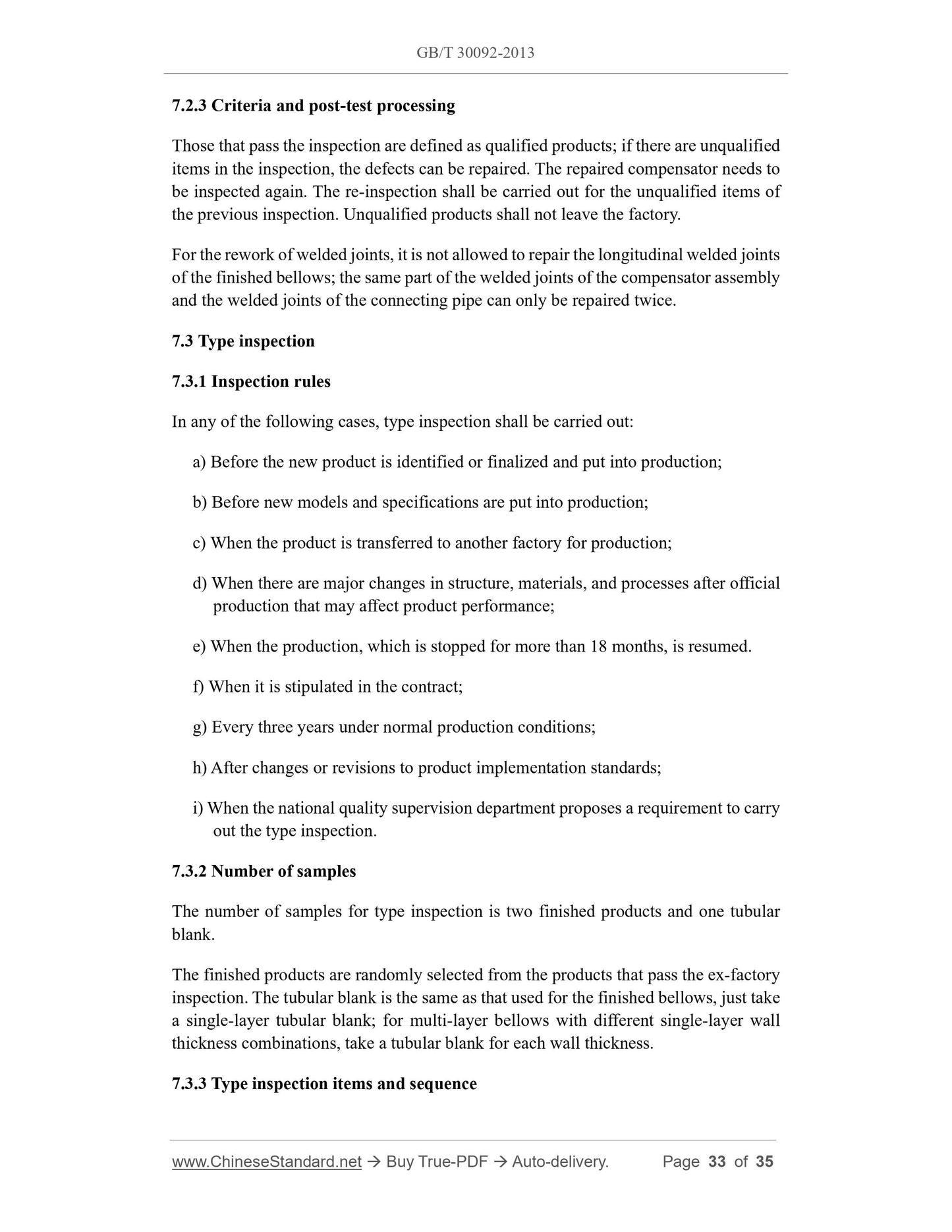
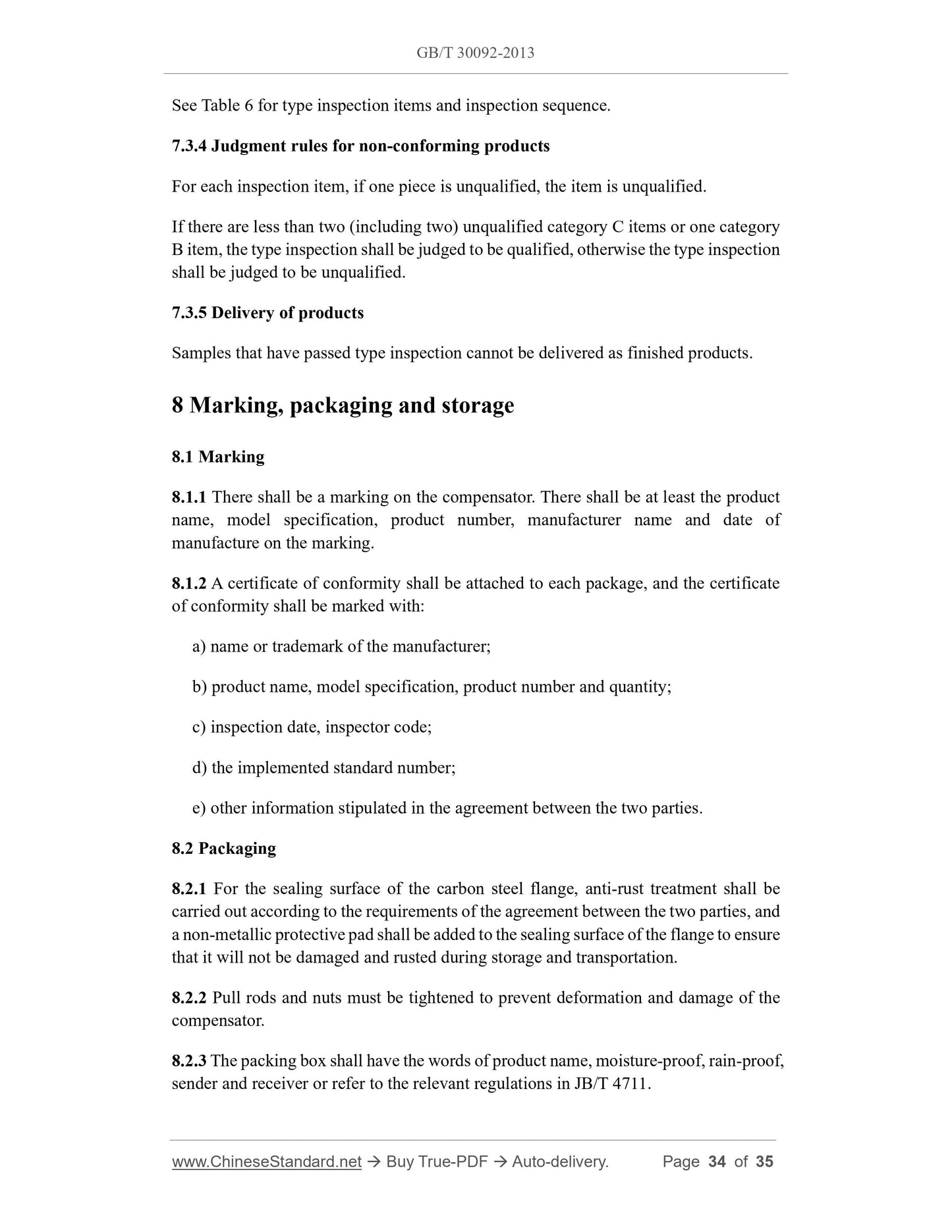