1
/
of
8
PayPal, credit cards. Download editable-PDF and invoice in 1 second!
GB/T 30029-2013 English PDF (GB/T30029-2013)
GB/T 30029-2013 English PDF (GB/T30029-2013)
Regular price
$125.00
Regular price
Sale price
$125.00
Unit price
/
per
Shipping calculated at checkout.
Couldn't load pickup availability
GB/T 30029-2013: Automated guided vehicle (AGV) -- General rule of design
Delivery: 9 seconds. Download (and Email) true-PDF + Invoice.
Newer version: (Replacing this standard) GB/T 30029-2023
Get Quotation: Click GB/T 30029-2013 (Self-service in 1-minute)
Newer / historical versions: GB/T 30029-2023
Preview True-PDF (Reload/Scroll-down if blank)
Delivery: 9 seconds. Download (and Email) true-PDF + Invoice.
Newer version: (Replacing this standard) GB/T 30029-2023
Get Quotation: Click GB/T 30029-2013 (Self-service in 1-minute)
Newer / historical versions: GB/T 30029-2023
Preview True-PDF (Reload/Scroll-down if blank)
Share
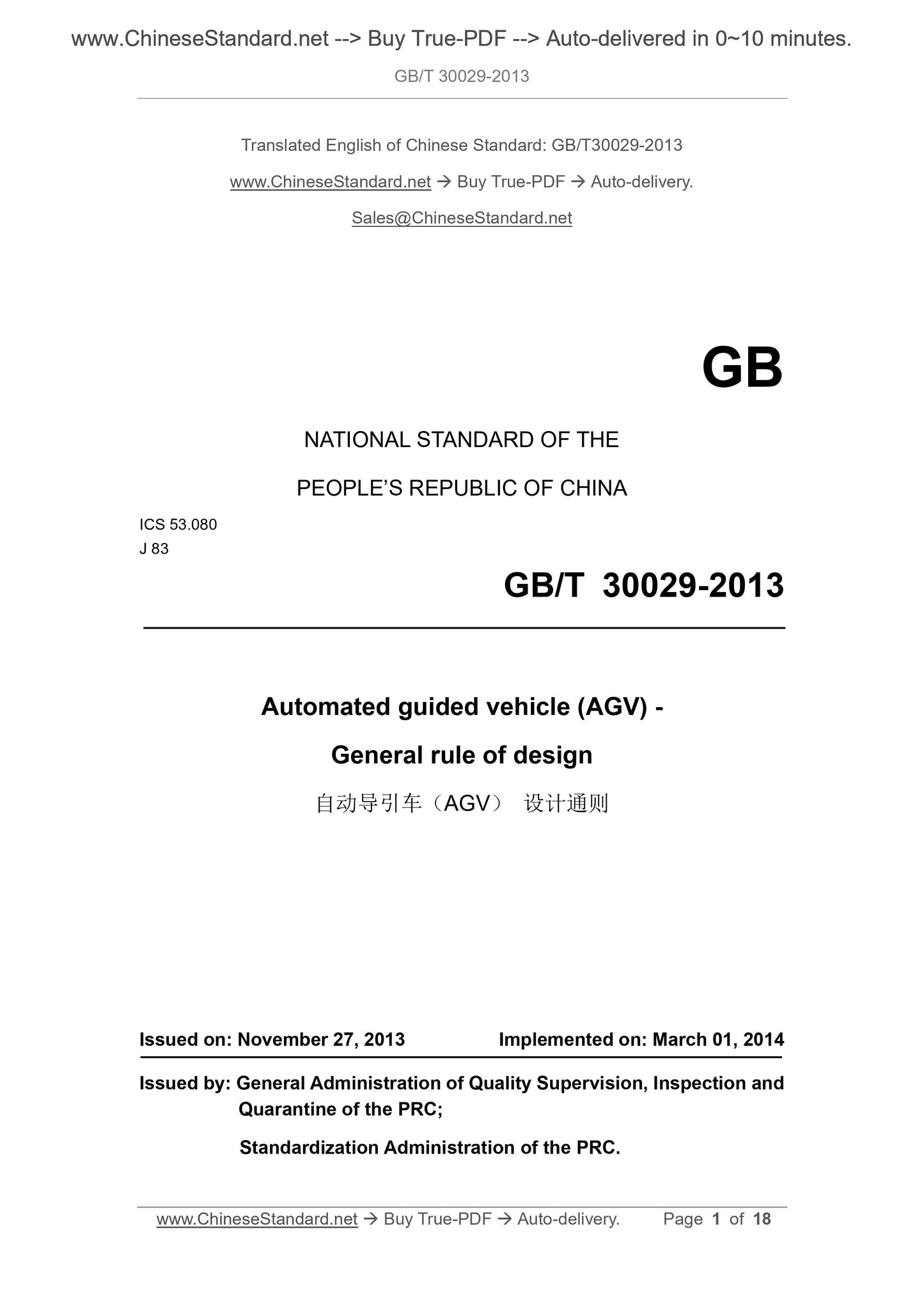
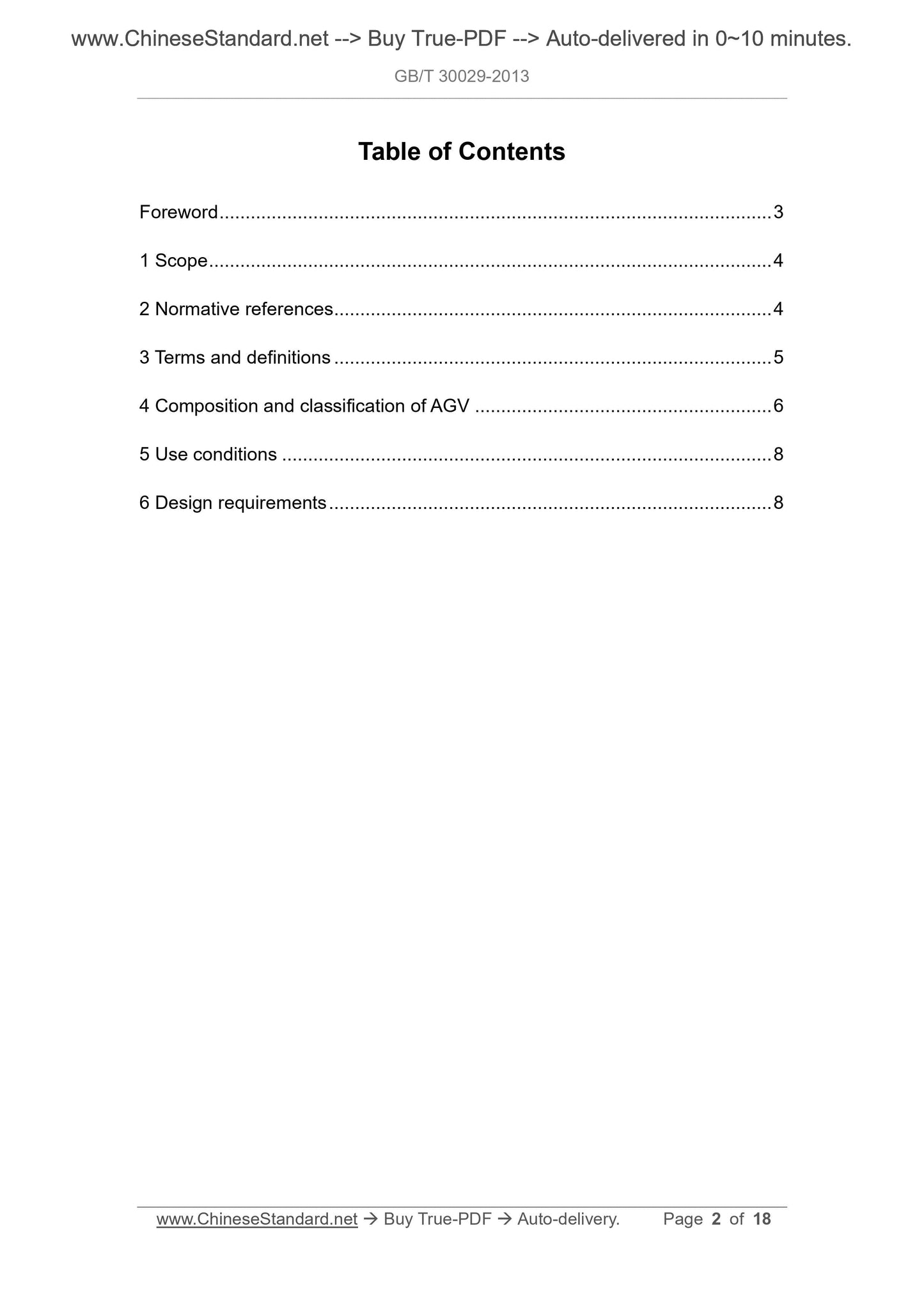
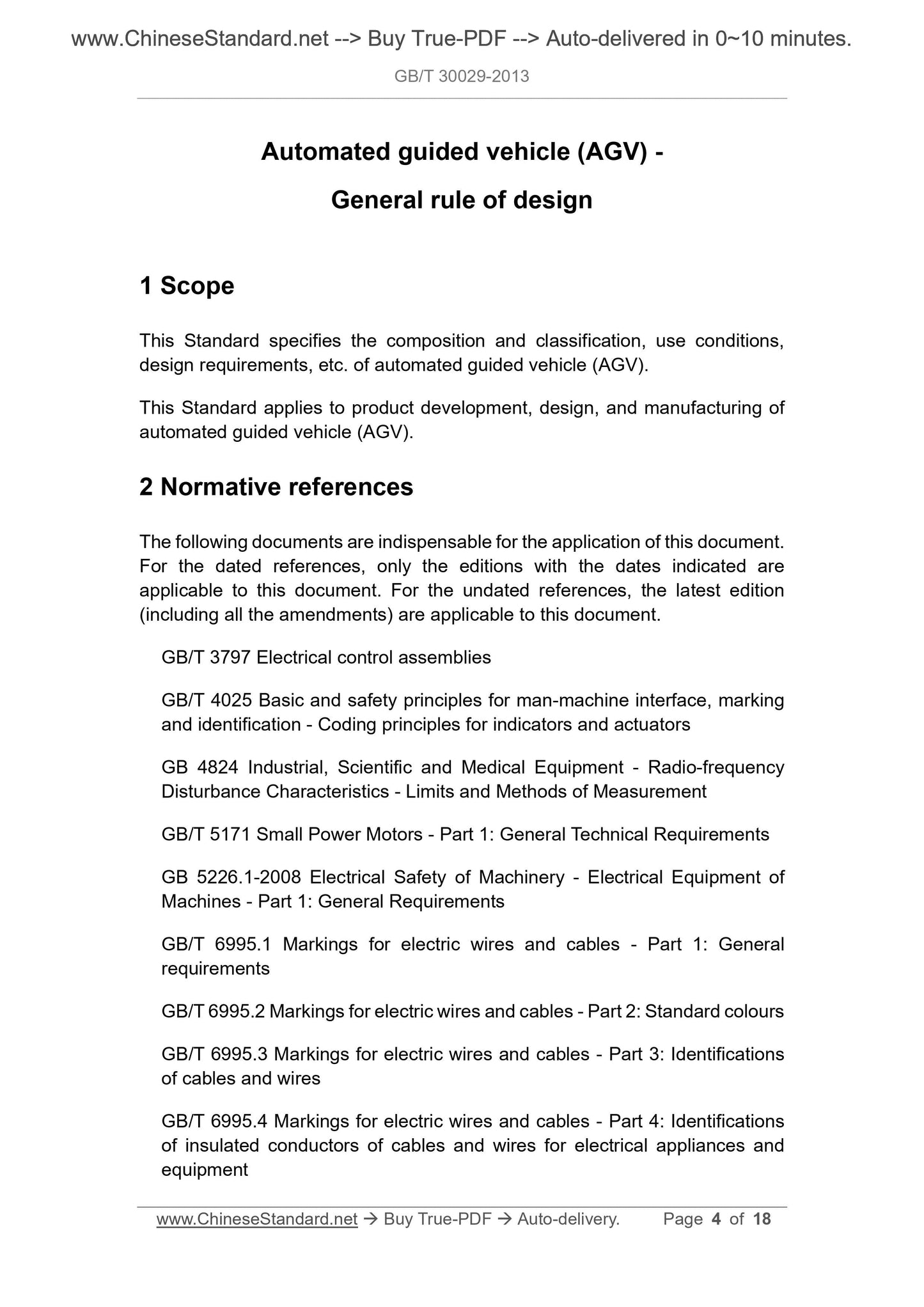
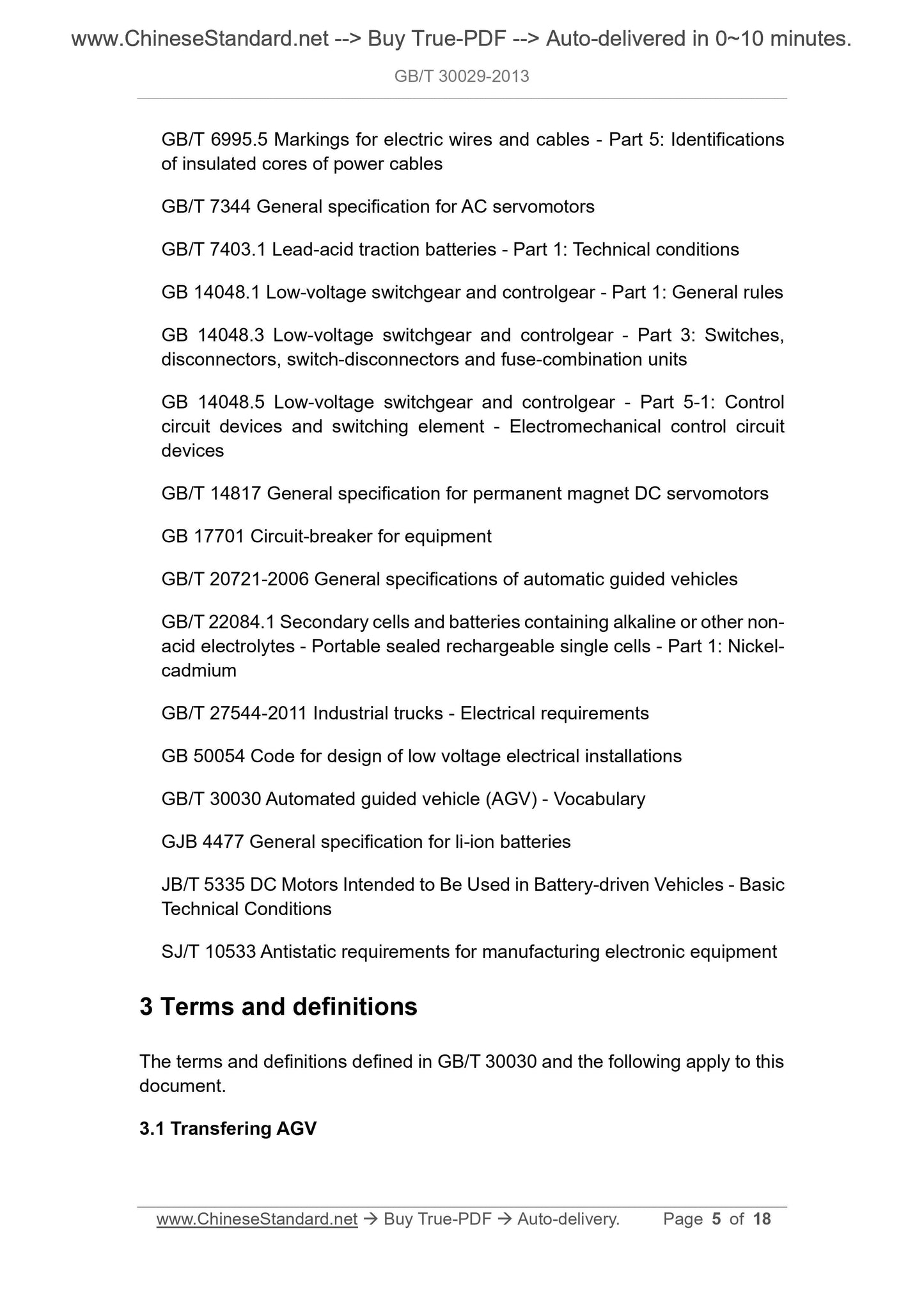


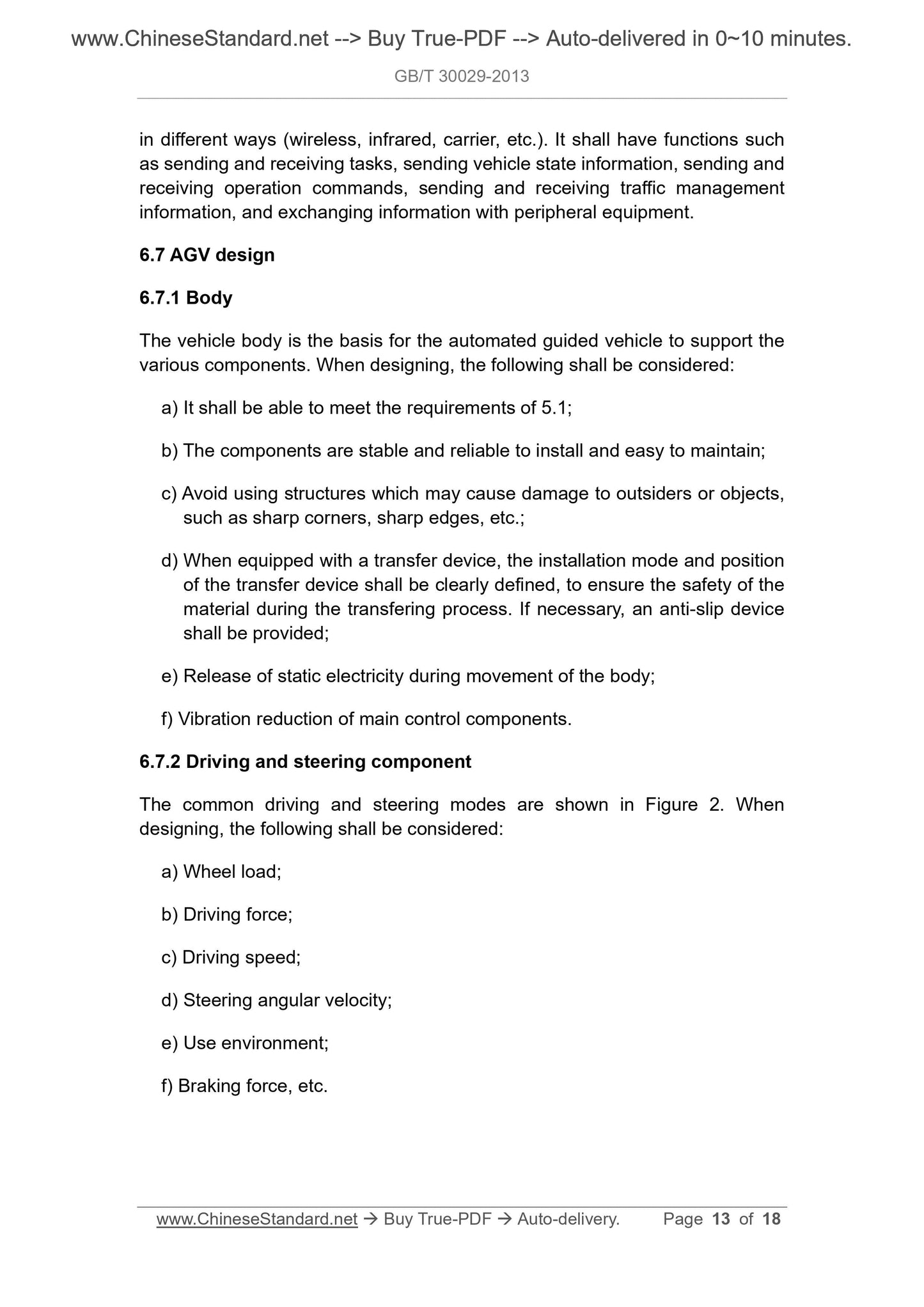
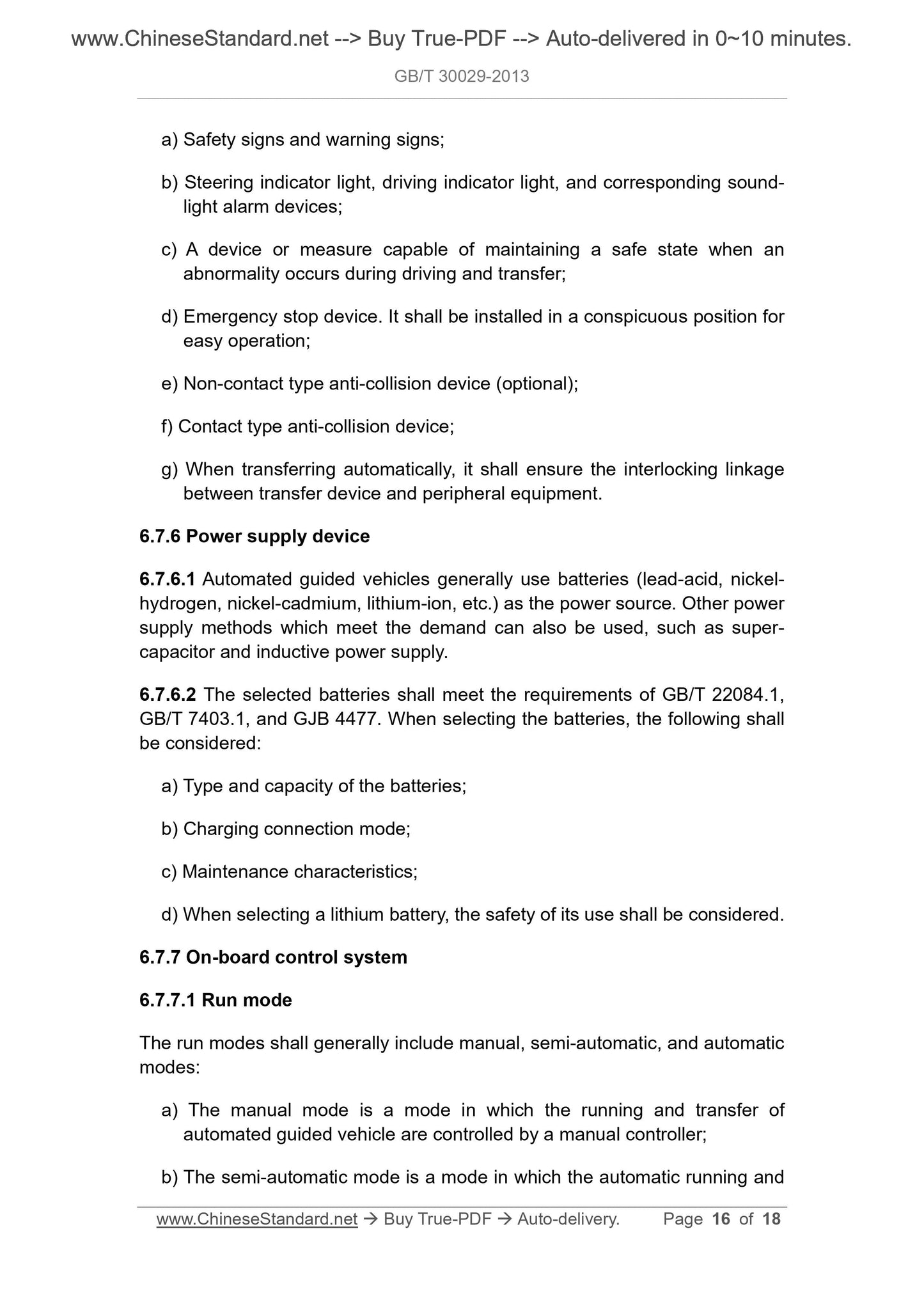