1
/
of
5
www.ChineseStandard.us -- Field Test Asia Pte. Ltd.
GB/T 24610.4-2019 English PDF (GB/T24610.4-2019)
GB/T 24610.4-2019 English PDF (GB/T24610.4-2019)
Regular price
$165.00
Regular price
Sale price
$165.00
Unit price
/
per
Shipping calculated at checkout.
Couldn't load pickup availability
GB/T 24610.4-2019: Rolling bearings -- Measuring methods for vibration -- Part 4: Radial cylindrical roller bearings with cylindrical bore and outside surface
Delivery: 9 seconds. Download (and Email) true-PDF + Invoice.
Get Quotation: Click GB/T 24610.4-2019 (Self-service in 1-minute)
Newer / historical versions: GB/T 24610.4-2019
Preview True-PDF (Reload/Scroll-down if blank)
Delivery: 9 seconds. Download (and Email) true-PDF + Invoice.
Get Quotation: Click GB/T 24610.4-2019 (Self-service in 1-minute)
Newer / historical versions: GB/T 24610.4-2019
Preview True-PDF (Reload/Scroll-down if blank)
Share
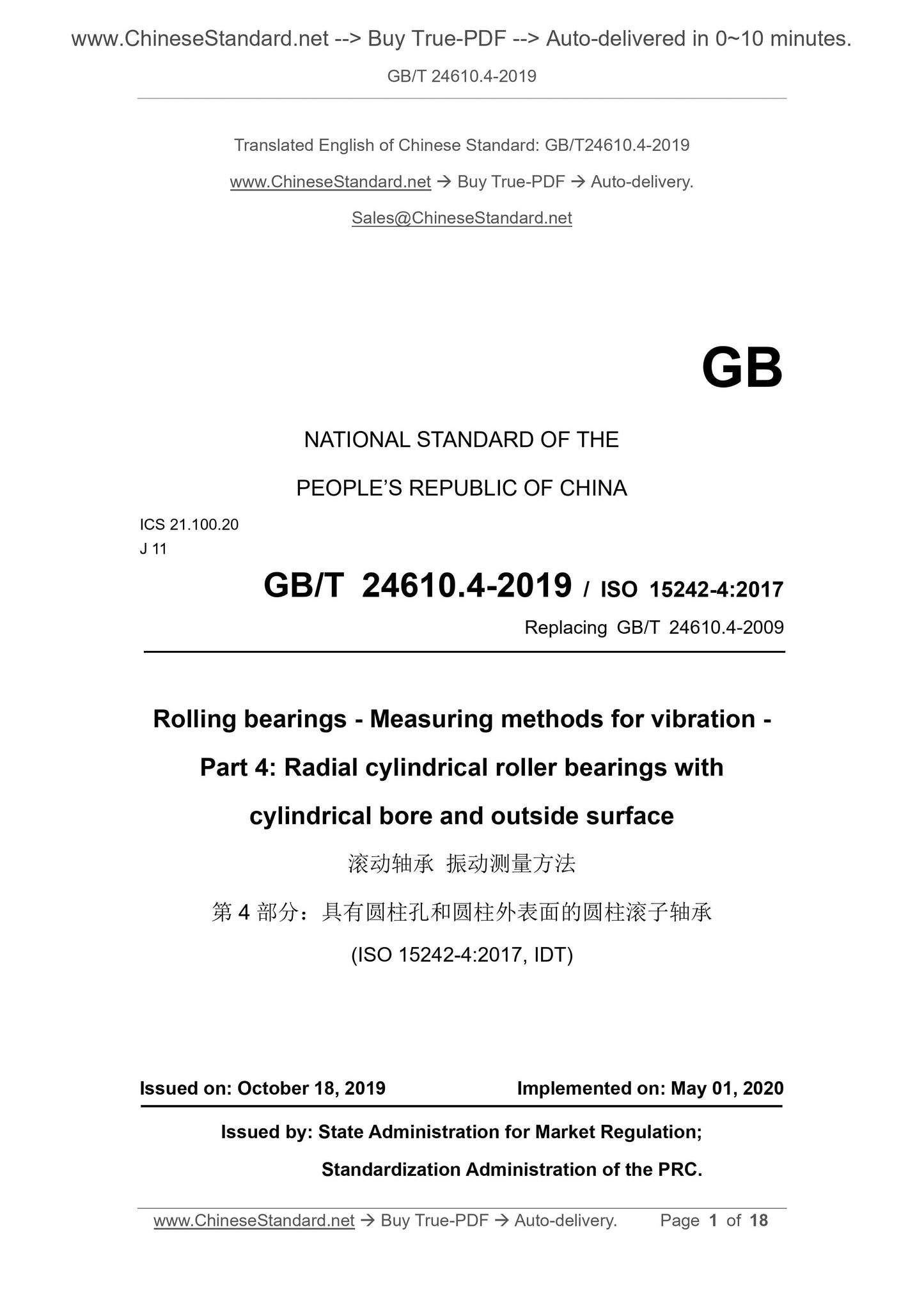
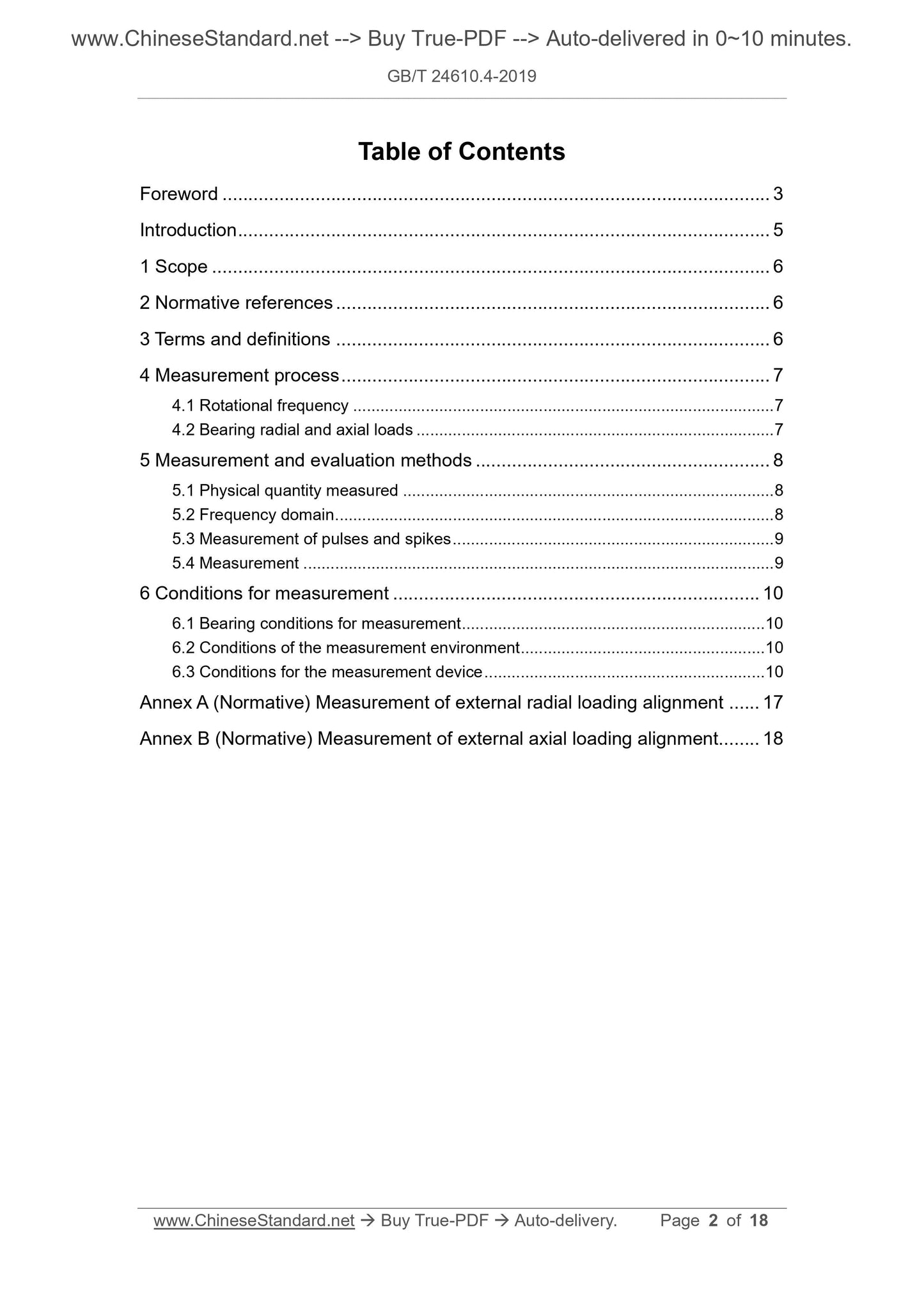
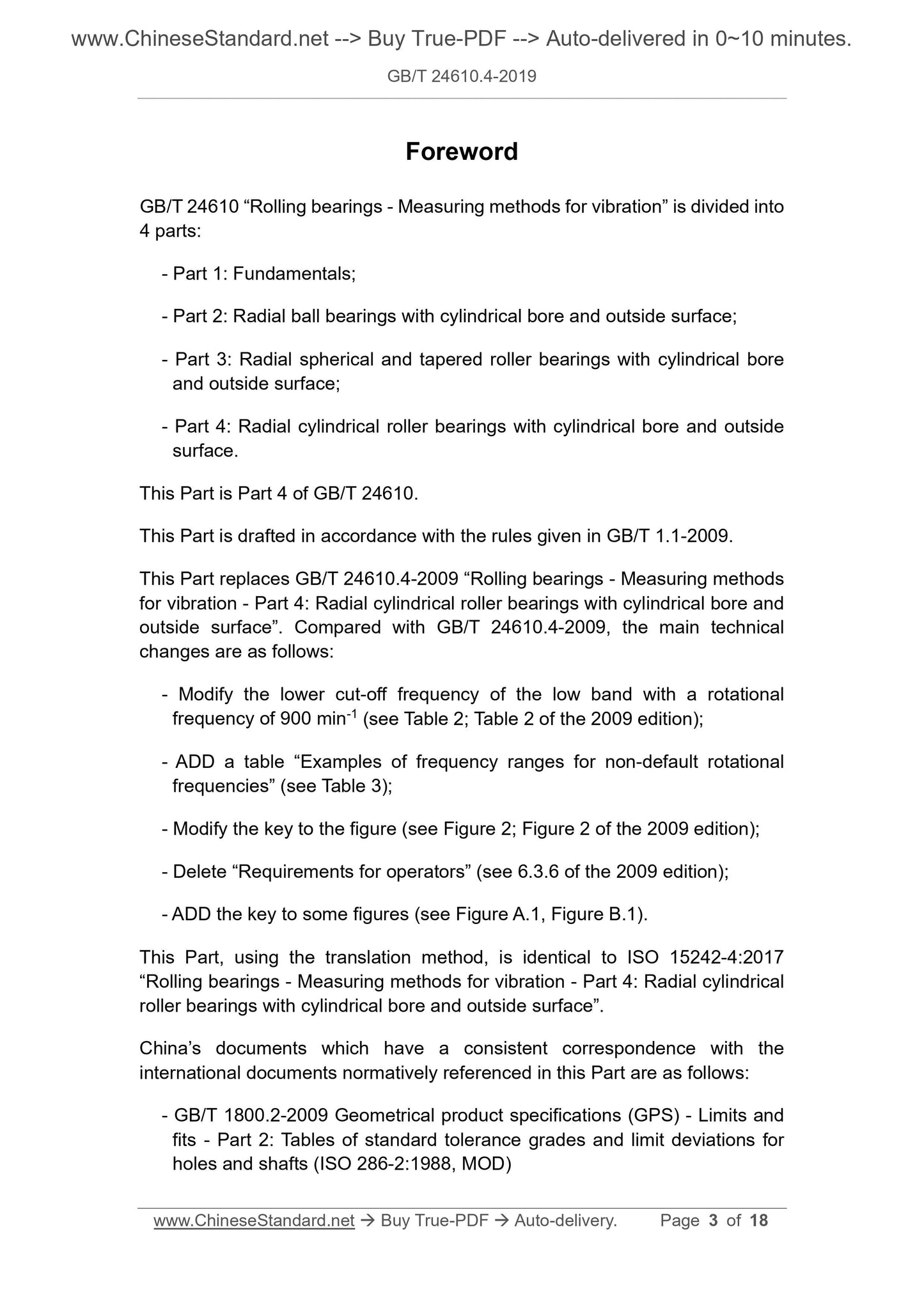
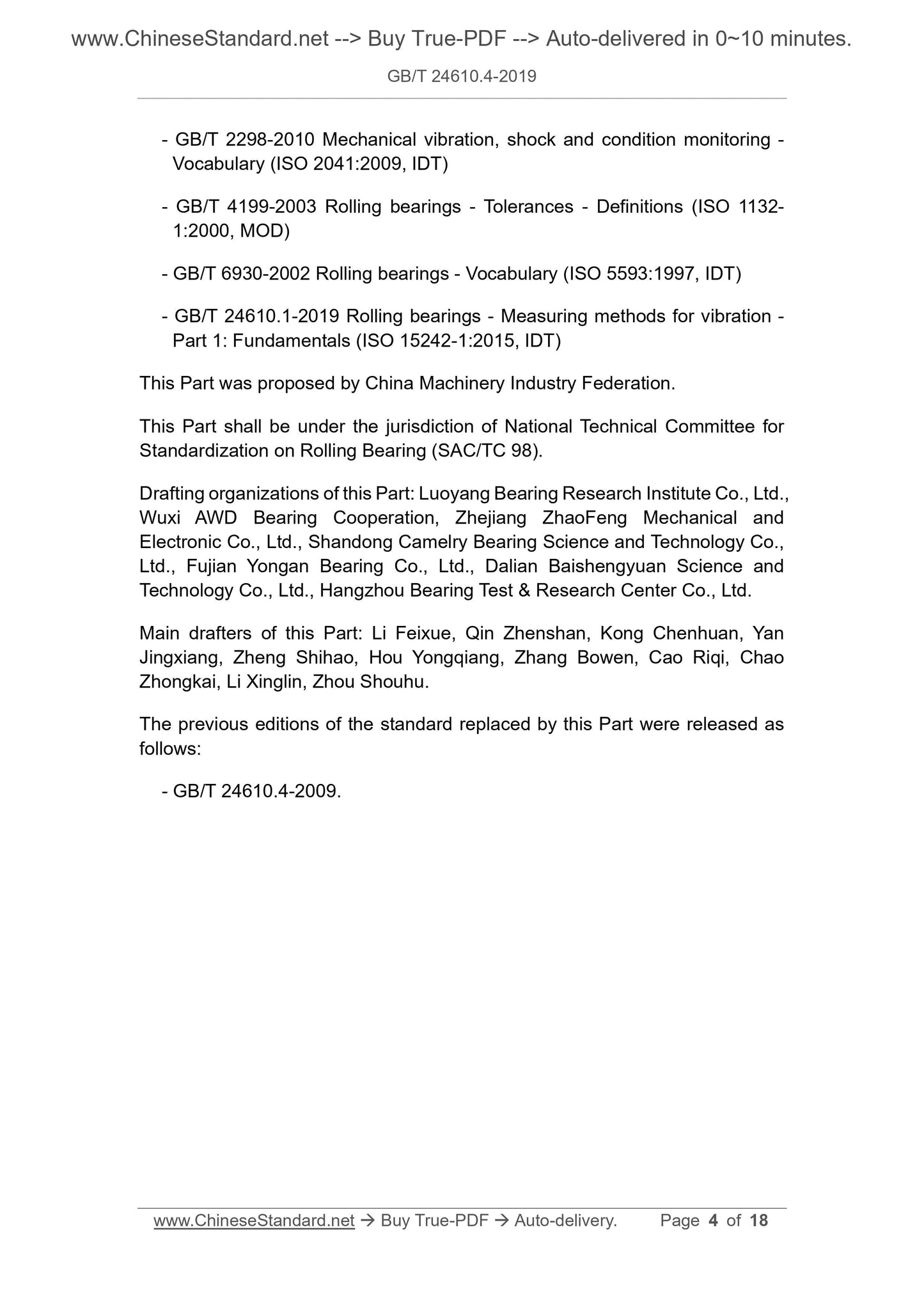
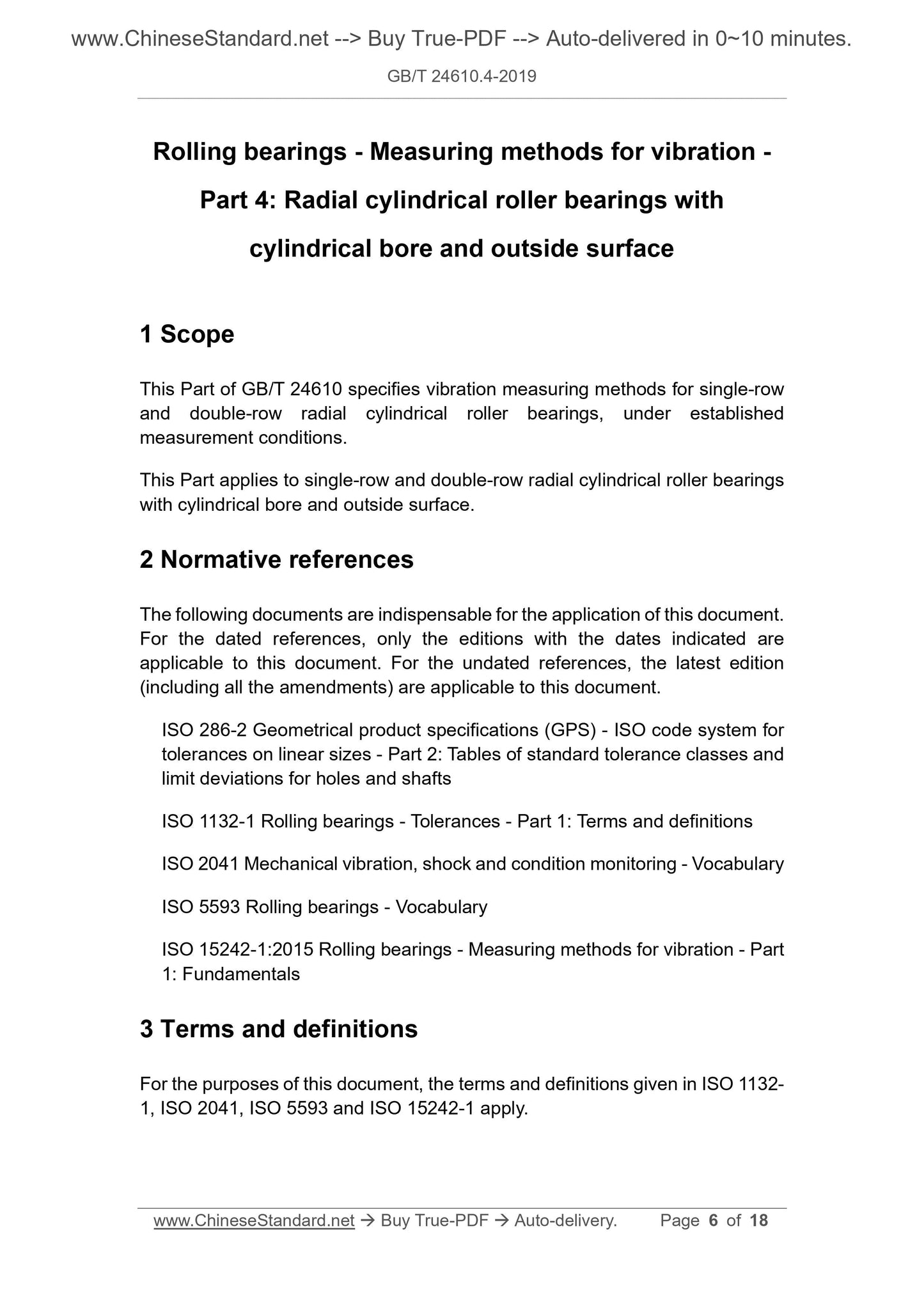