1
/
of
10
www.ChineseStandard.us -- Field Test Asia Pte. Ltd.
GB/T 23249-2009 English PDF (GB/T23249-2009)
GB/T 23249-2009 English PDF (GB/T23249-2009)
Regular price
$230.00
Regular price
Sale price
$230.00
Unit price
/
per
Shipping calculated at checkout.
Couldn't load pickup availability
GB/T 23249-2009: Coalbed Gas Content Measurement Methods in Geological Exploration Period
Delivery: 9 seconds. Download (and Email) true-PDF + Invoice.
Get Quotation: Click GB/T 23249-2009 (Self-service in 1-minute)
Newer / historical versions: GB/T 23249-2009
Preview True-PDF (Reload/Scroll-down if blank)
Delivery: 9 seconds. Download (and Email) true-PDF + Invoice.
Get Quotation: Click GB/T 23249-2009 (Self-service in 1-minute)
Newer / historical versions: GB/T 23249-2009
Preview True-PDF (Reload/Scroll-down if blank)
Share
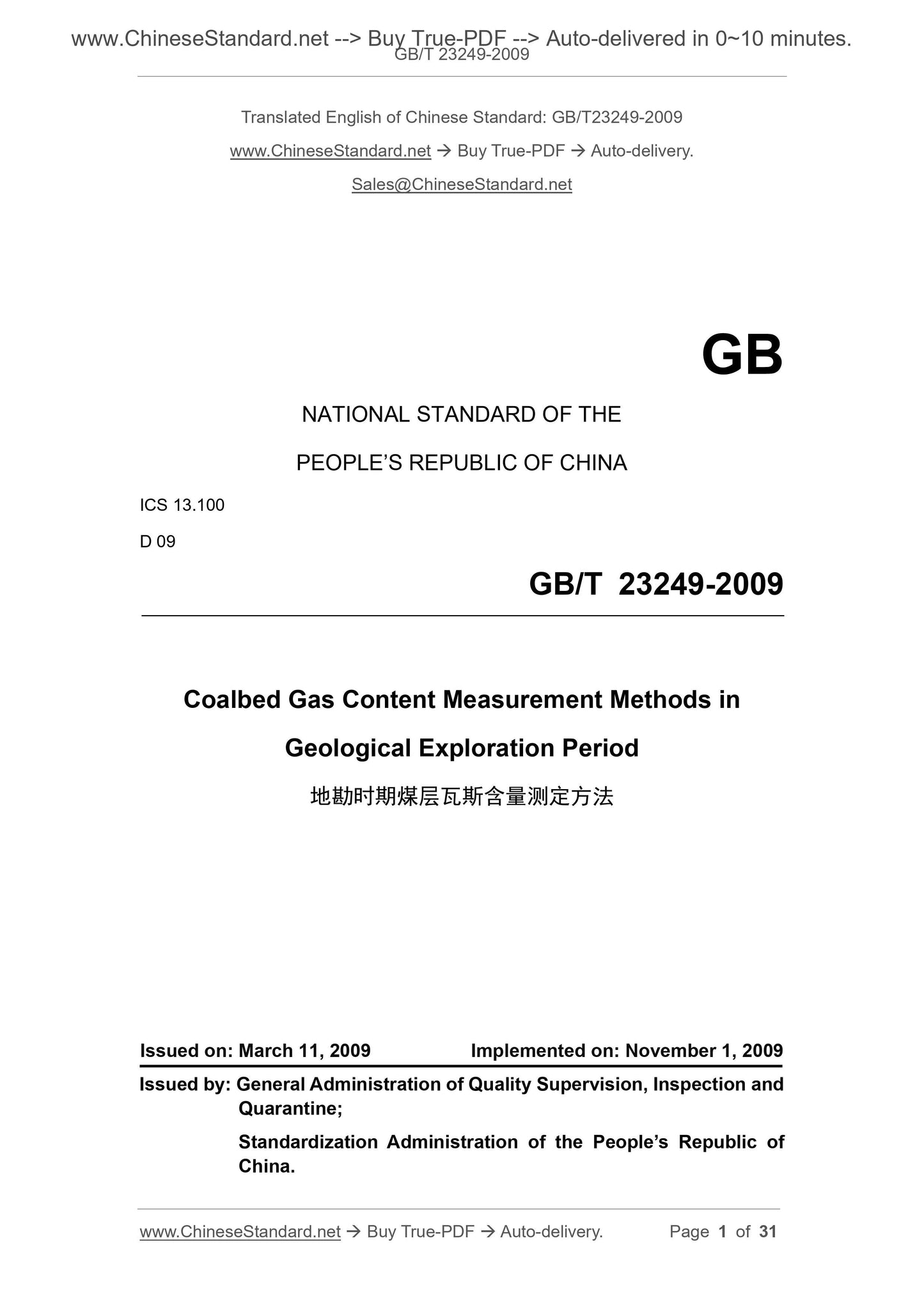
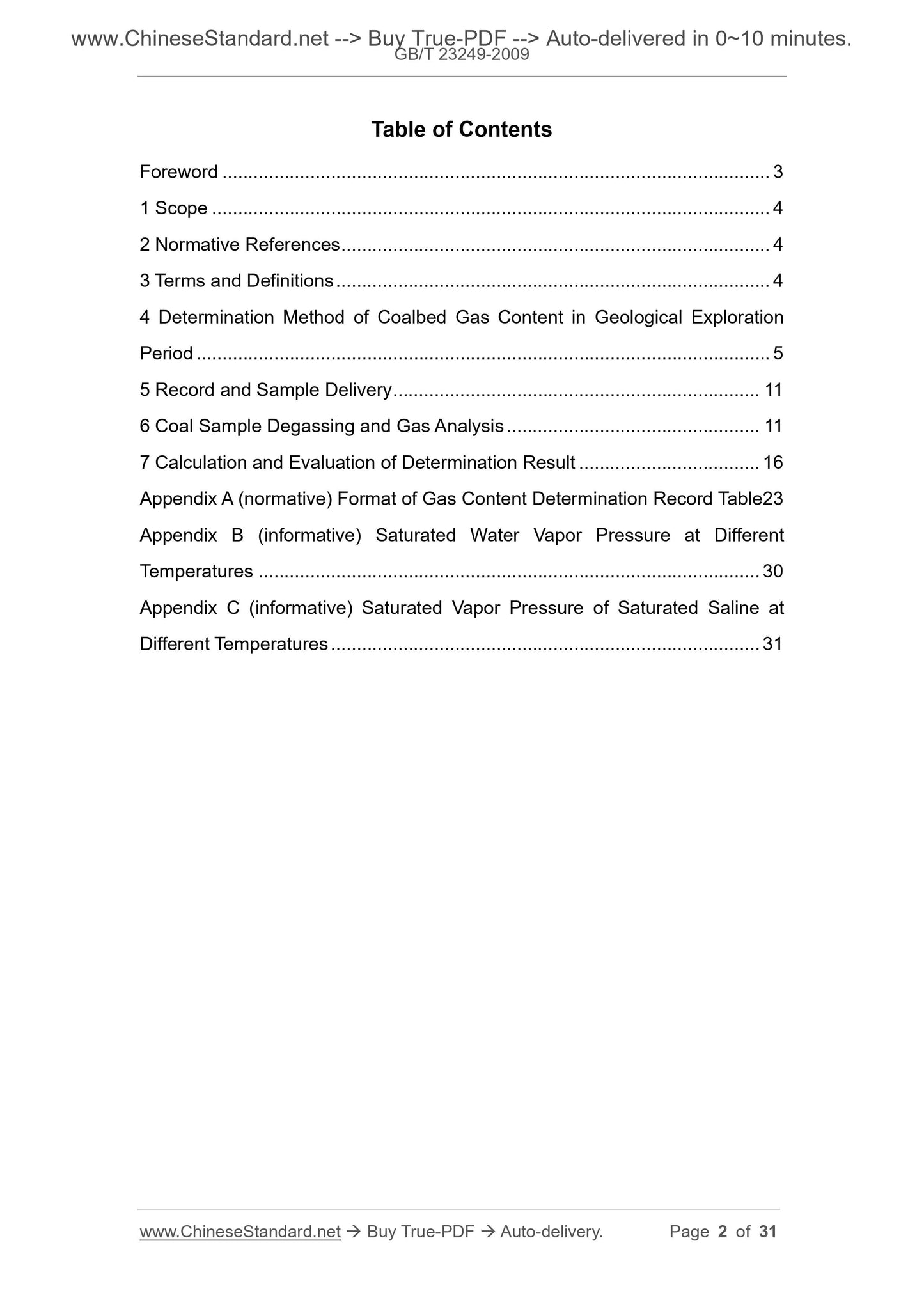
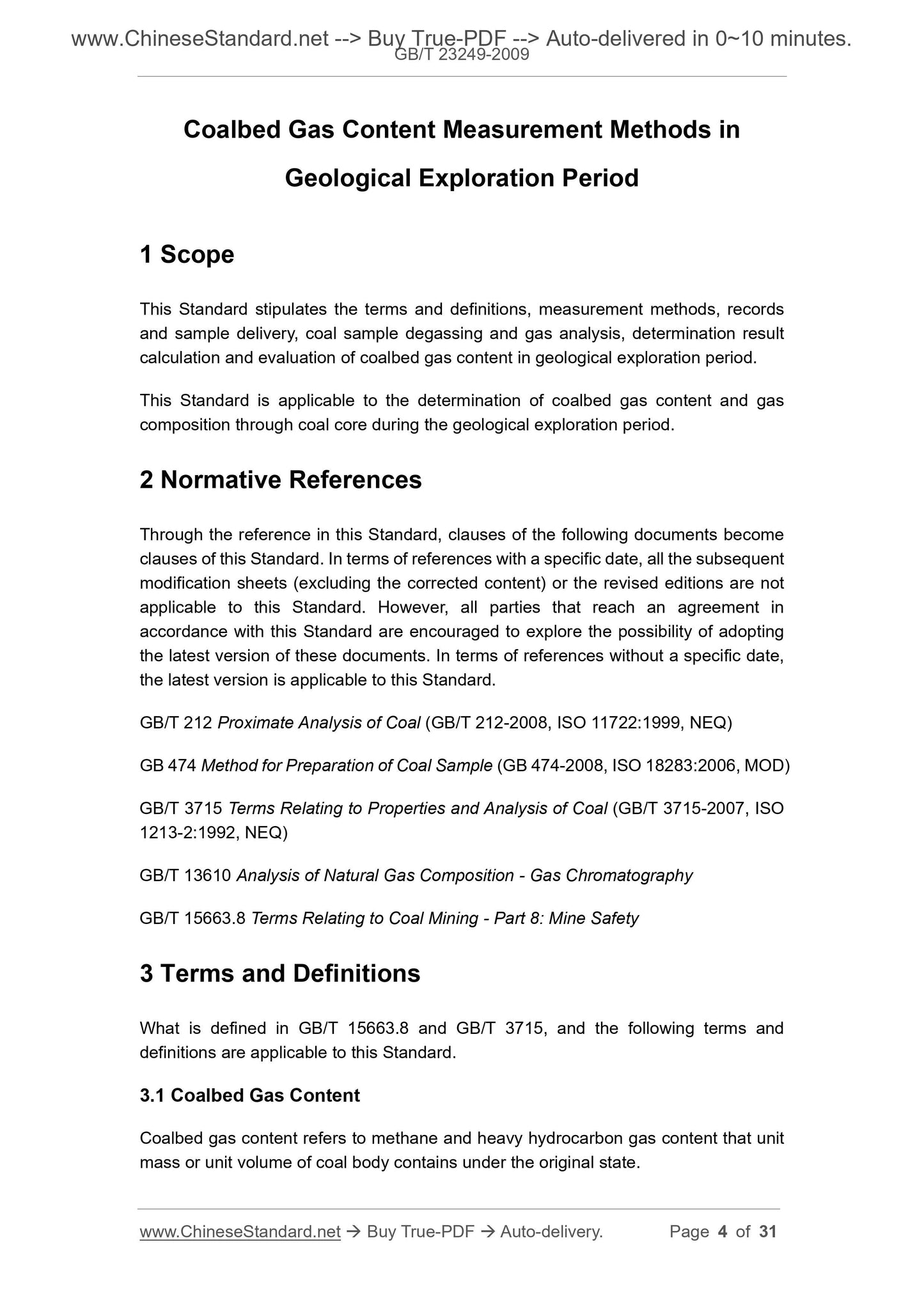
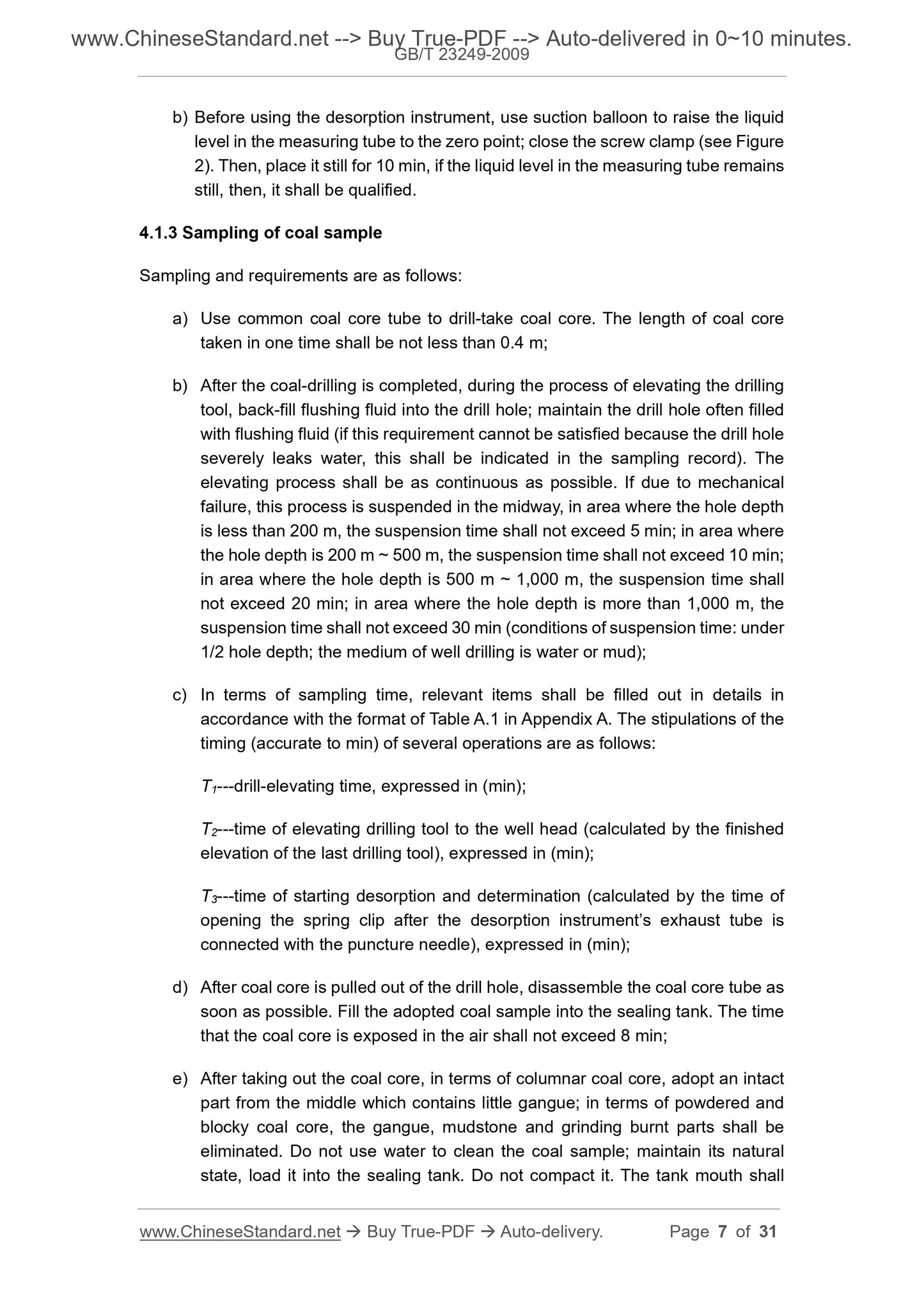
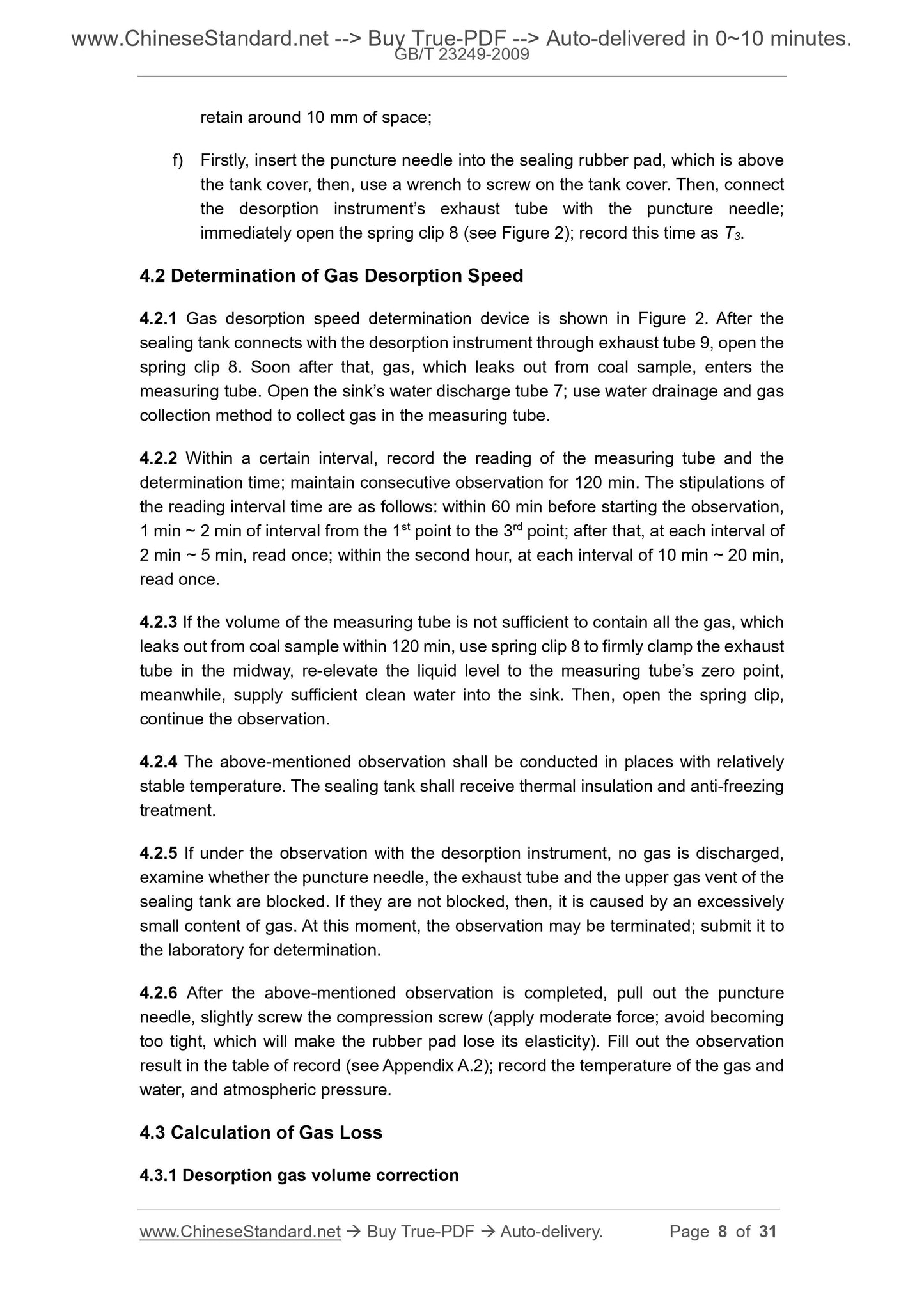
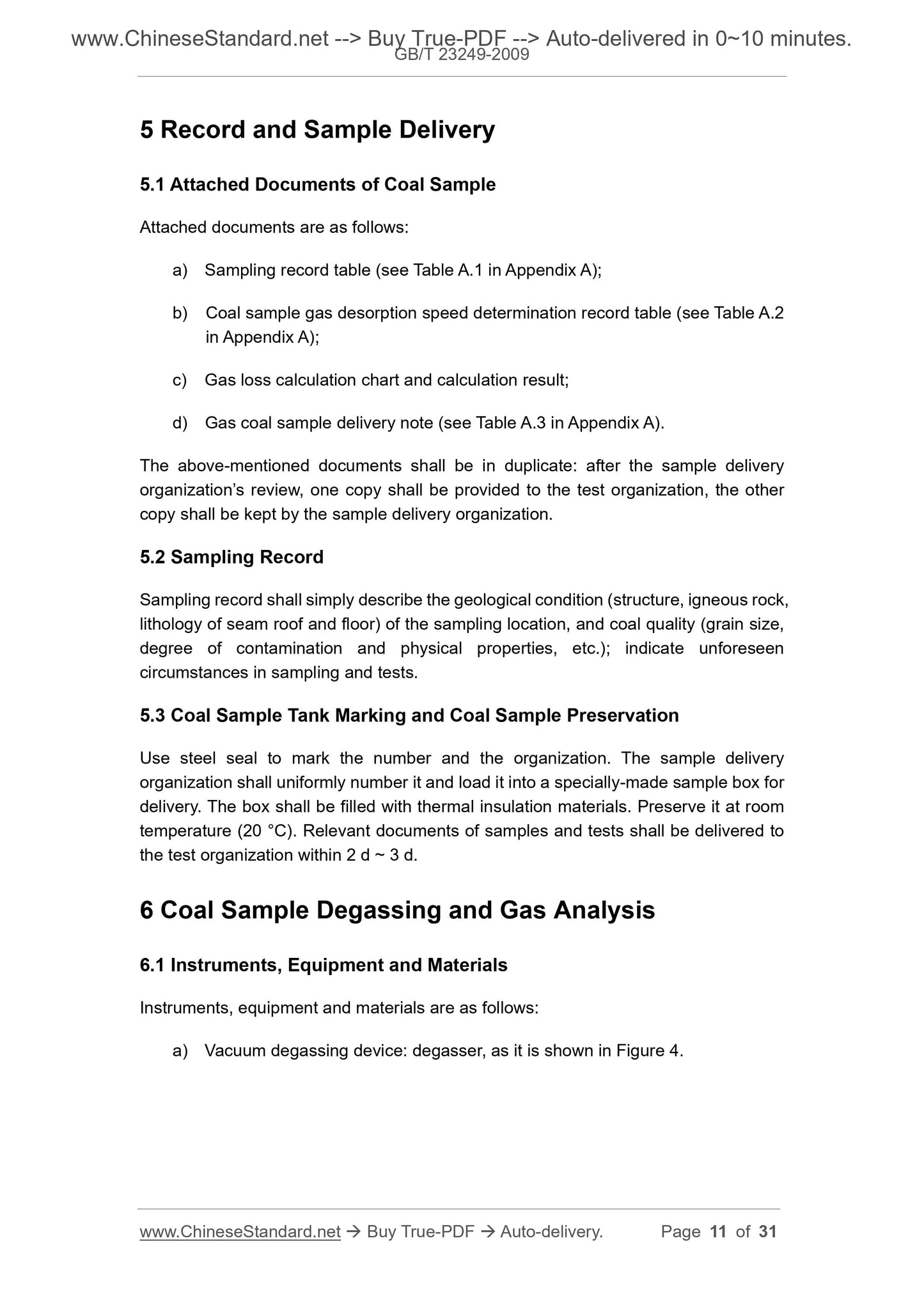
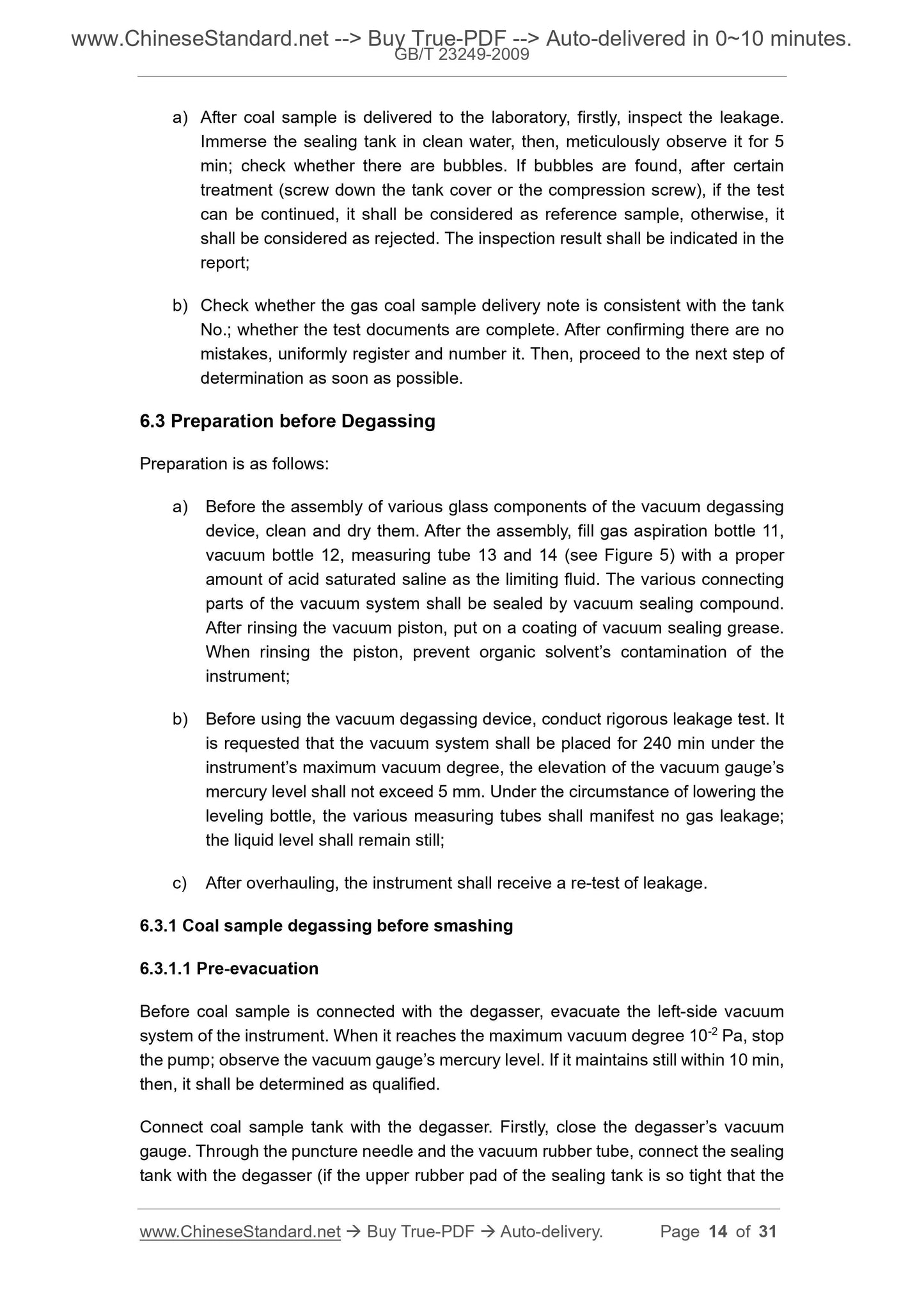
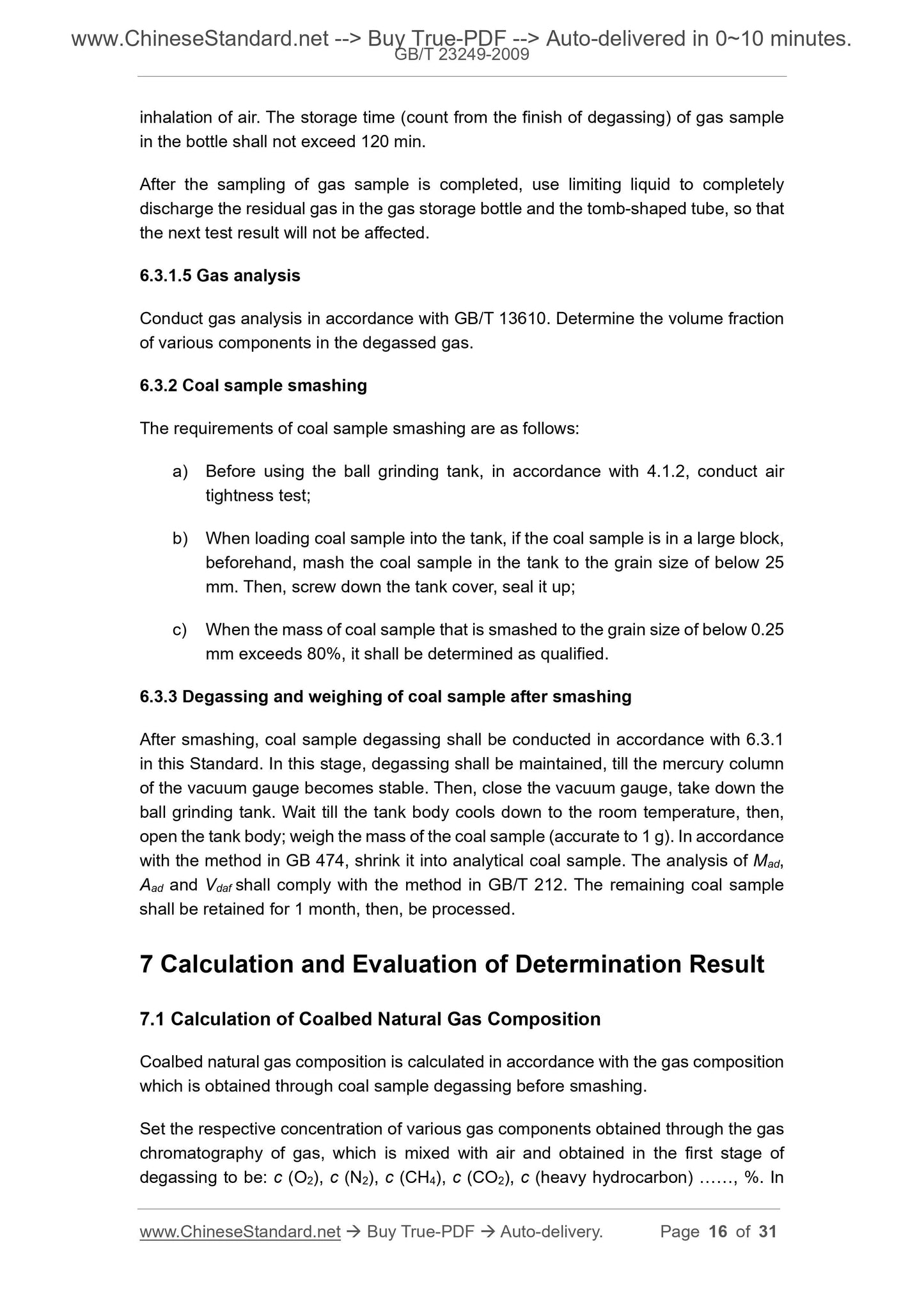
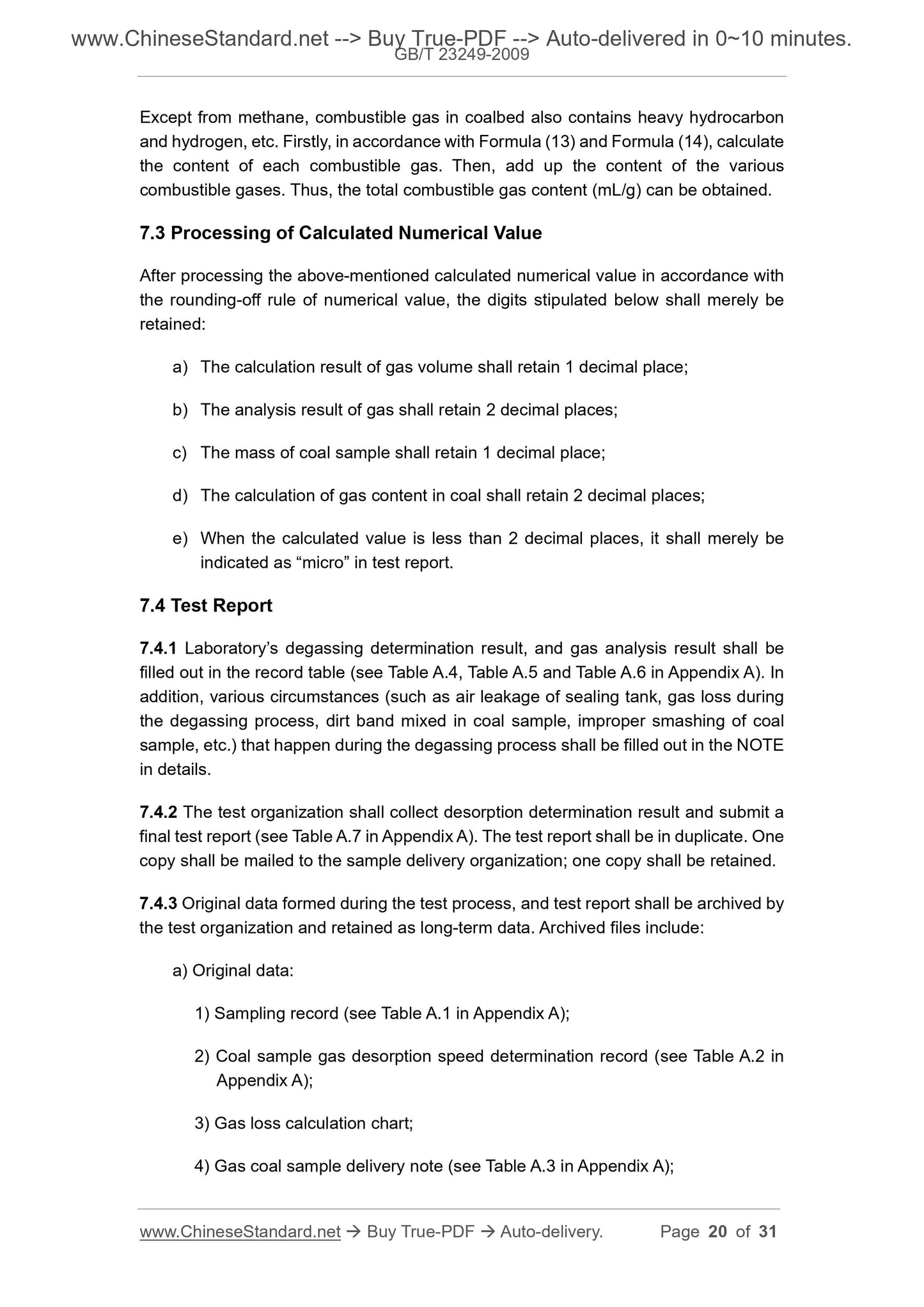
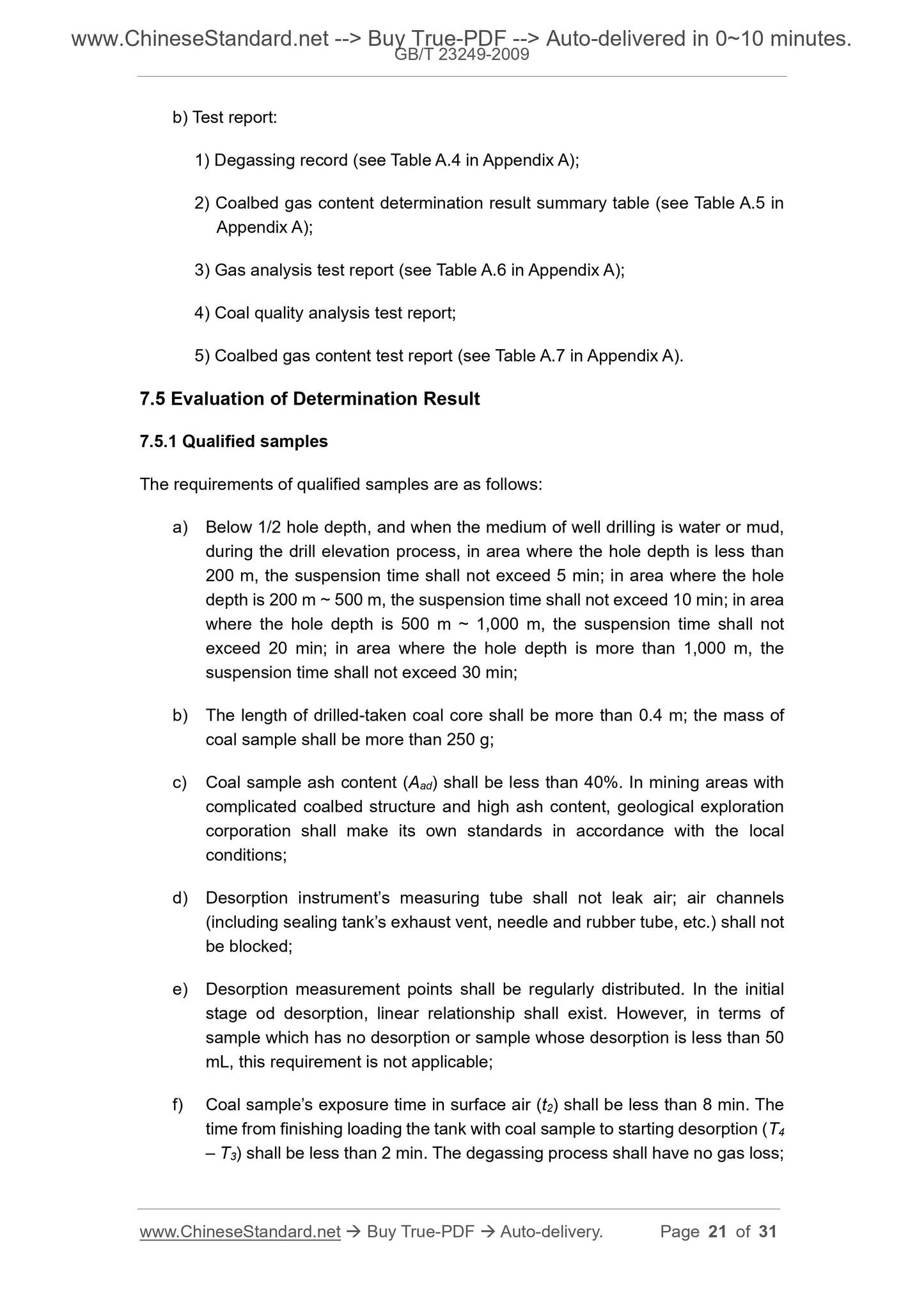