1
/
of
12
www.ChineseStandard.us -- Field Test Asia Pte. Ltd.
GB/T 20042.2-2023 English PDF (GB/T20042.2-2023)
GB/T 20042.2-2023 English PDF (GB/T20042.2-2023)
Regular price
$500.00
Regular price
Sale price
$500.00
Unit price
/
per
Shipping calculated at checkout.
Couldn't load pickup availability
GB/T 20042.2-2023: Proton exchange membrane fuel cell - Part 2: General technical specification of fuel cell stacks
Delivery: 9 seconds. Download (and Email) true-PDF + Invoice.Get Quotation: Click GB/T 20042.2-2023 (Self-service in 1-minute)
Newer / historical versions: GB/T 20042.2-2023
Preview True-PDF
Scope
This document specifies the requirements for safety, basic performance, test items, testmethods, as well as marking and instructions, of proton exchange membrane fuel cell
stacks (including direct alcohol fuel cell stacks, hereinafter referred to as fuel cell
stacks).
Note 1.The cell stack mentioned in this document is also called fuel cell stack.
Note 2.A better material or a new structure – if any – which can pass the test specified
in this document and meet the relevant requirements can also be considered as
conforming to this document.
This document is applicable to the design and testing of proton exchange membrane
fuel cell stacks (including direct alcohol fuel cell stacks).
This document only deals with situations where harm may be caused to the human body
and the external environment of the fuel cell stack. As long as the protection of the
internal damage of the fuel cell stack does not affect the safety outside the fuel cell
stack, no provisions are made in this document.
This document does not cover requirements for fuel and oxidizer storage and delivery
arrangements.
Basic Data
Standard ID | GB/T 20042.2-2023 (GB/T20042.2-2023) |
Description (Translated English) | Proton exchange membrane fuel cell - Part 2: General technical specification of fuel cell stacks |
Sector / Industry | National Standard (Recommended) |
Classification of Chinese Standard | K82 |
Classification of International Standard | 27.070 |
Word Count Estimation | 32,375 |
Date of Issue | 2023-03-17 |
Date of Implementation | 2023-10-01 |
Older Standard (superseded by this standard) | GB/T 20042.2-2008 |
Issuing agency(ies) | State Administration for Market Regulation, China National Standardization Administration |
Share
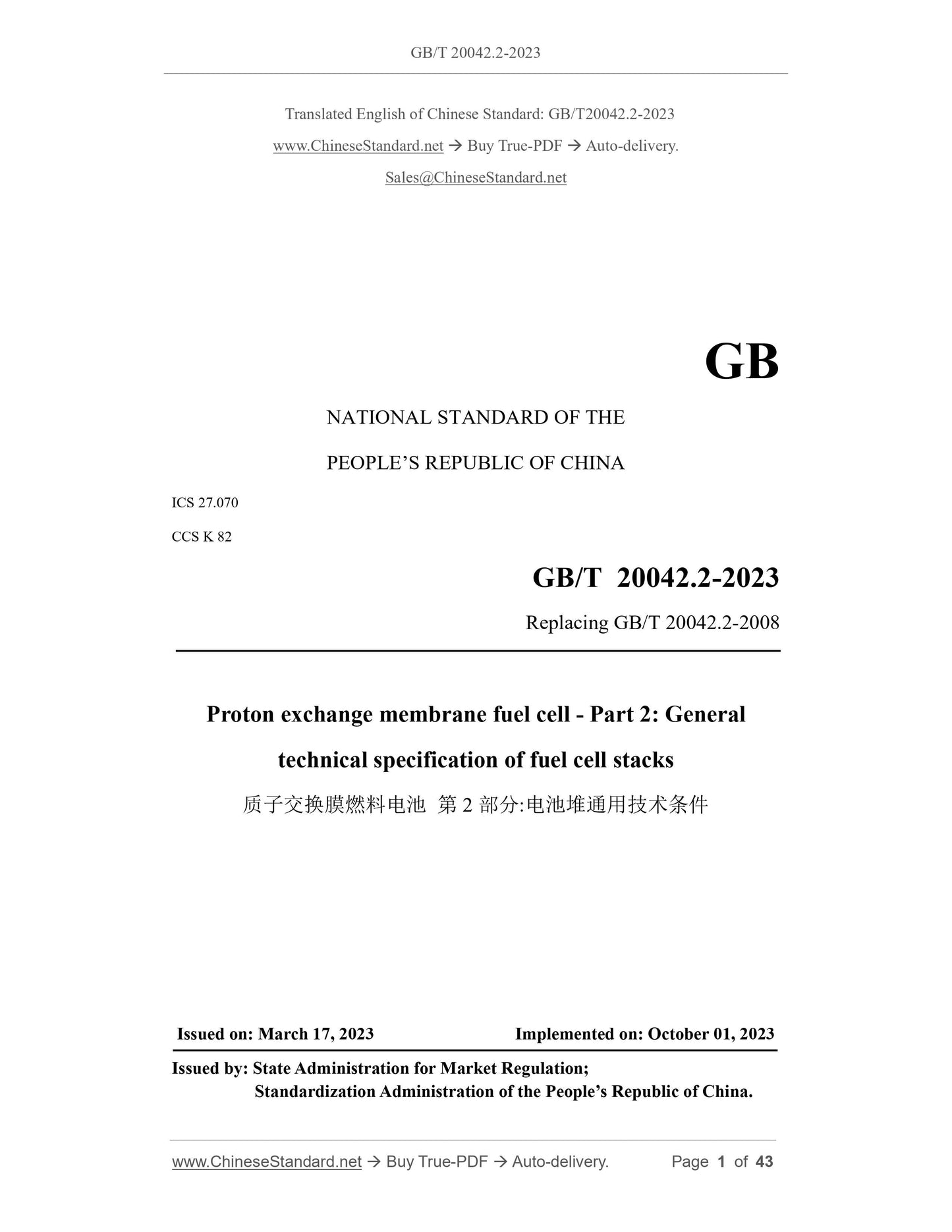
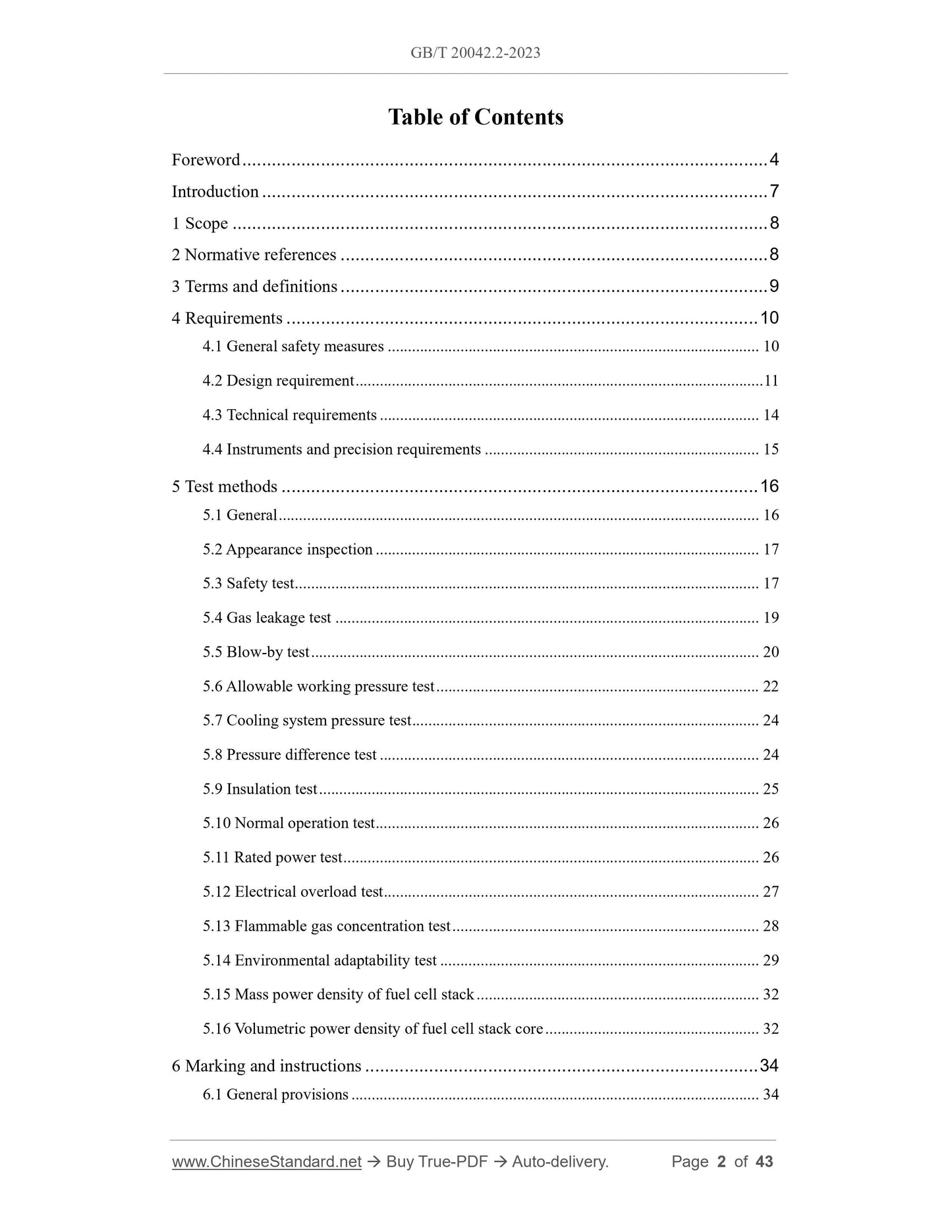
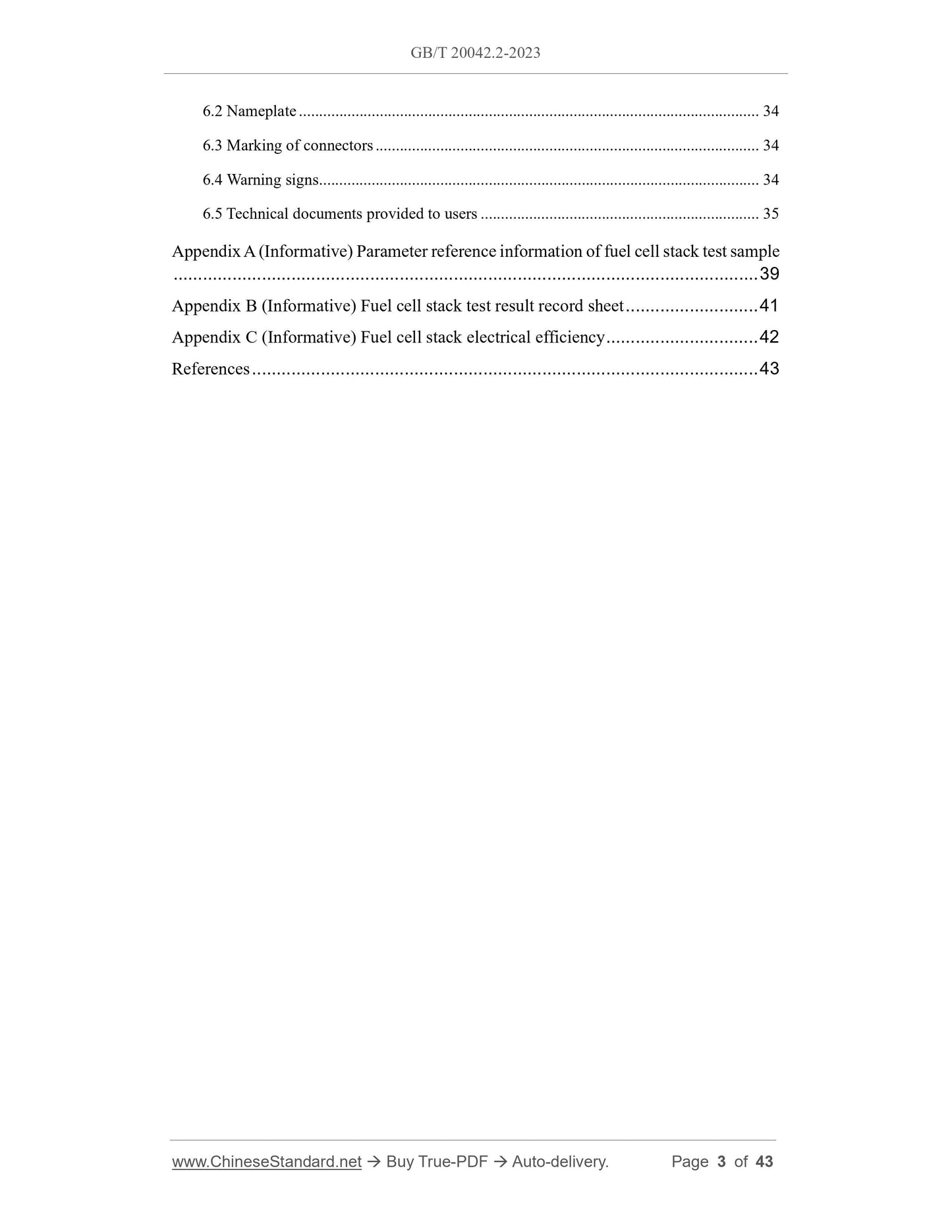
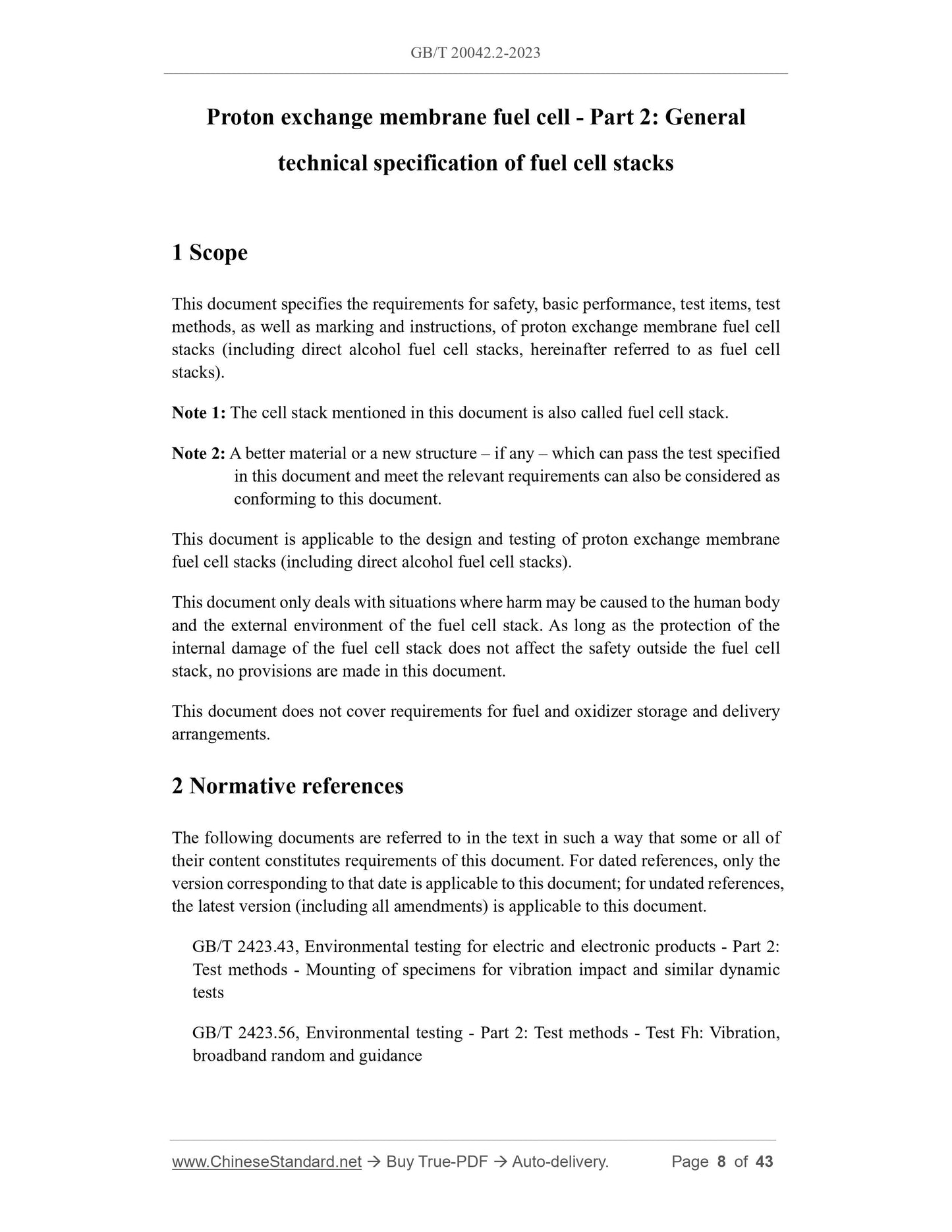
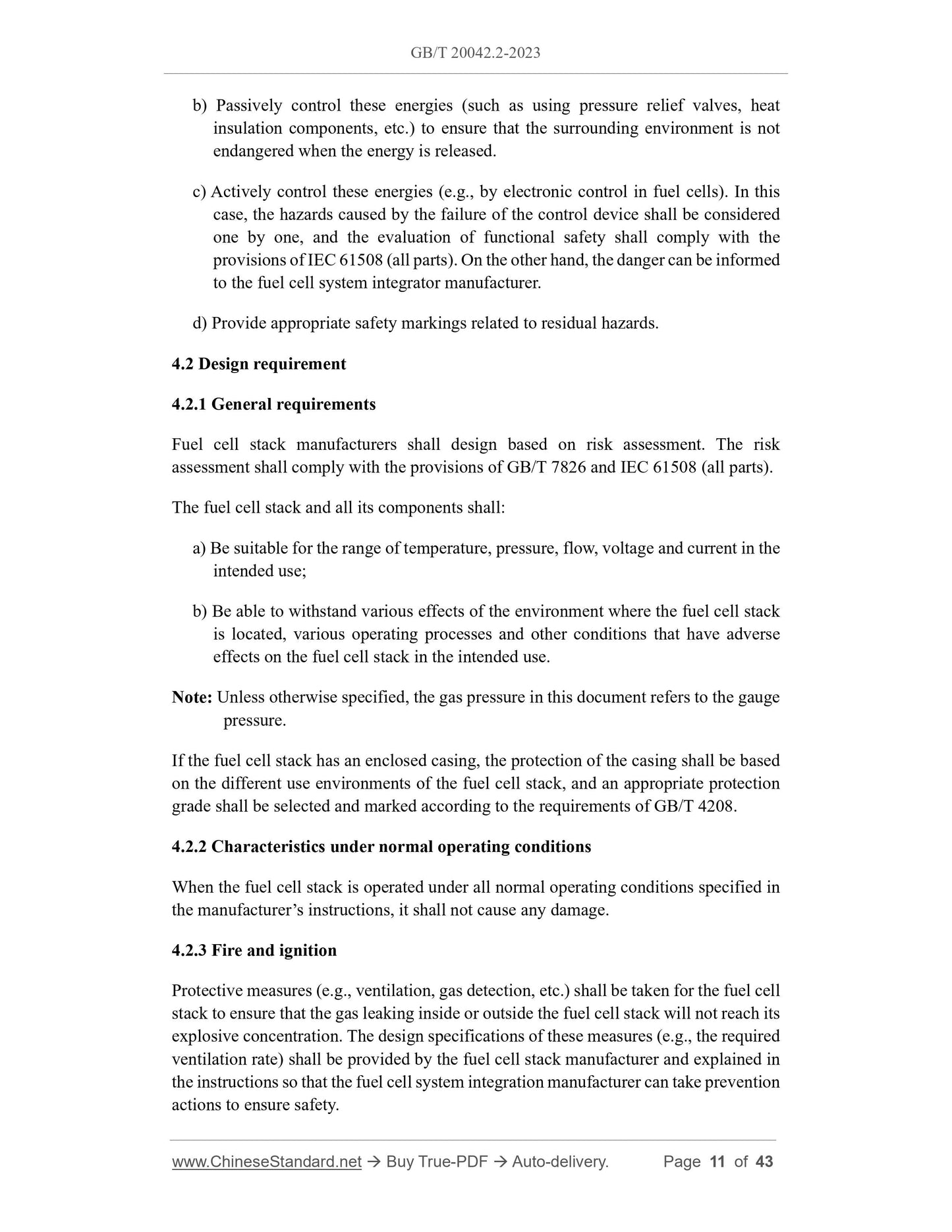
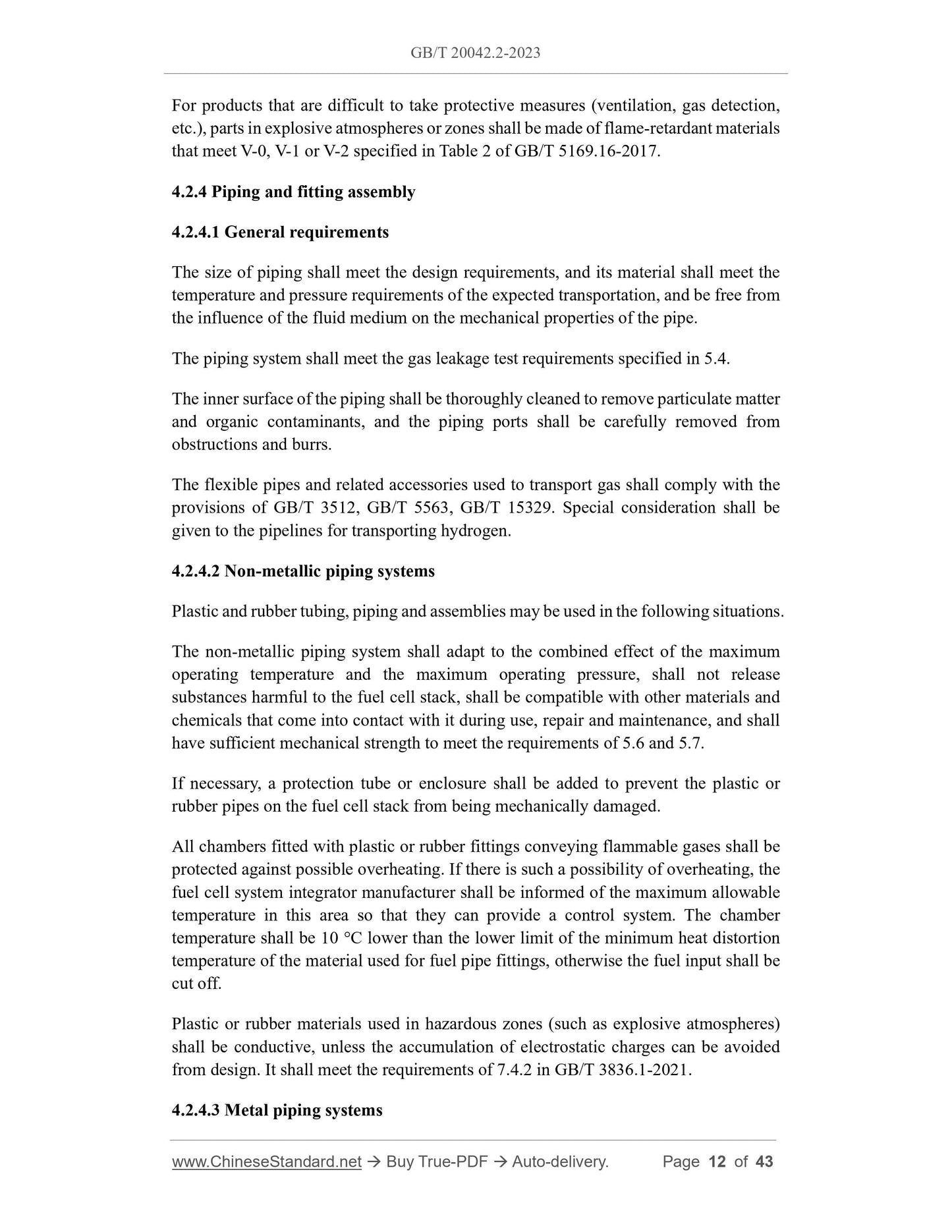
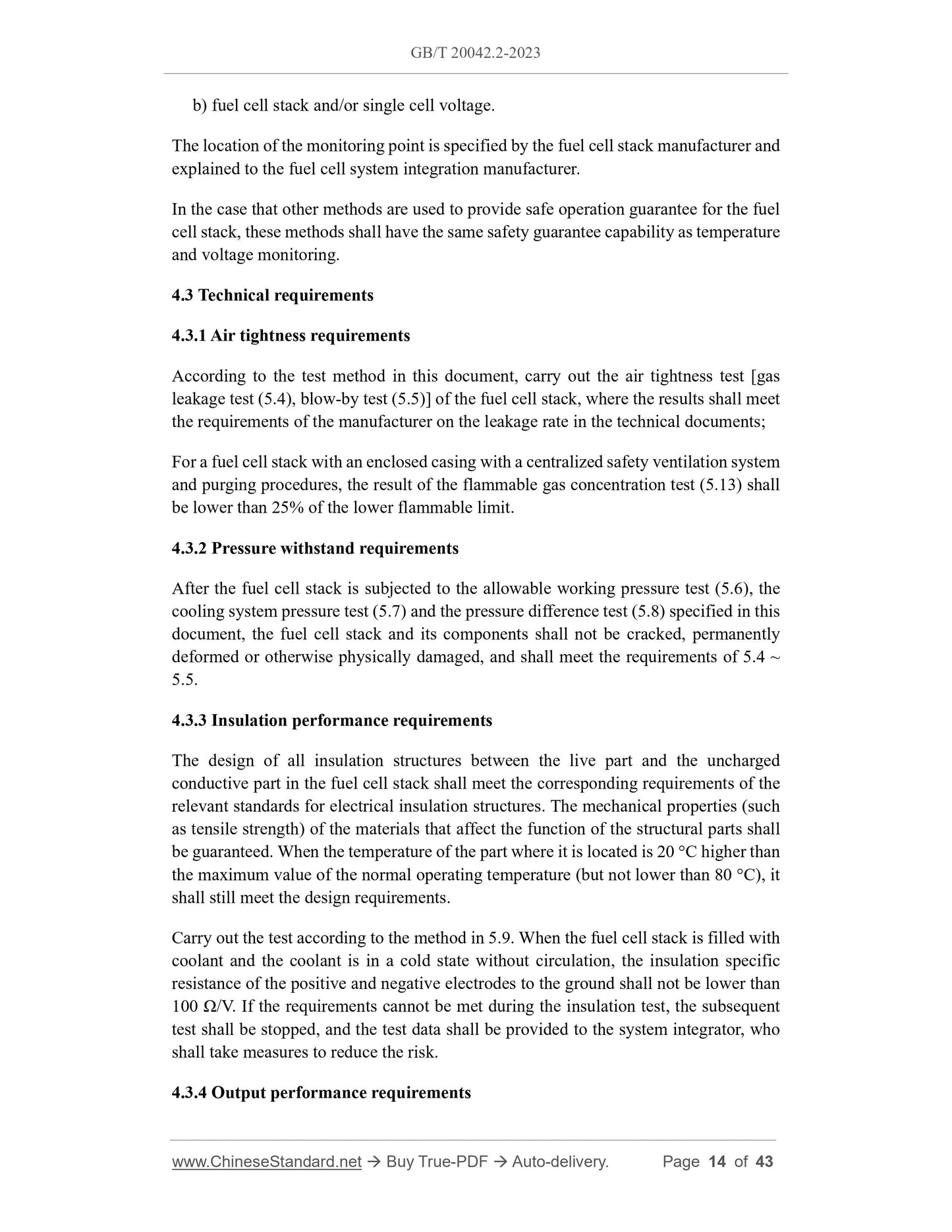
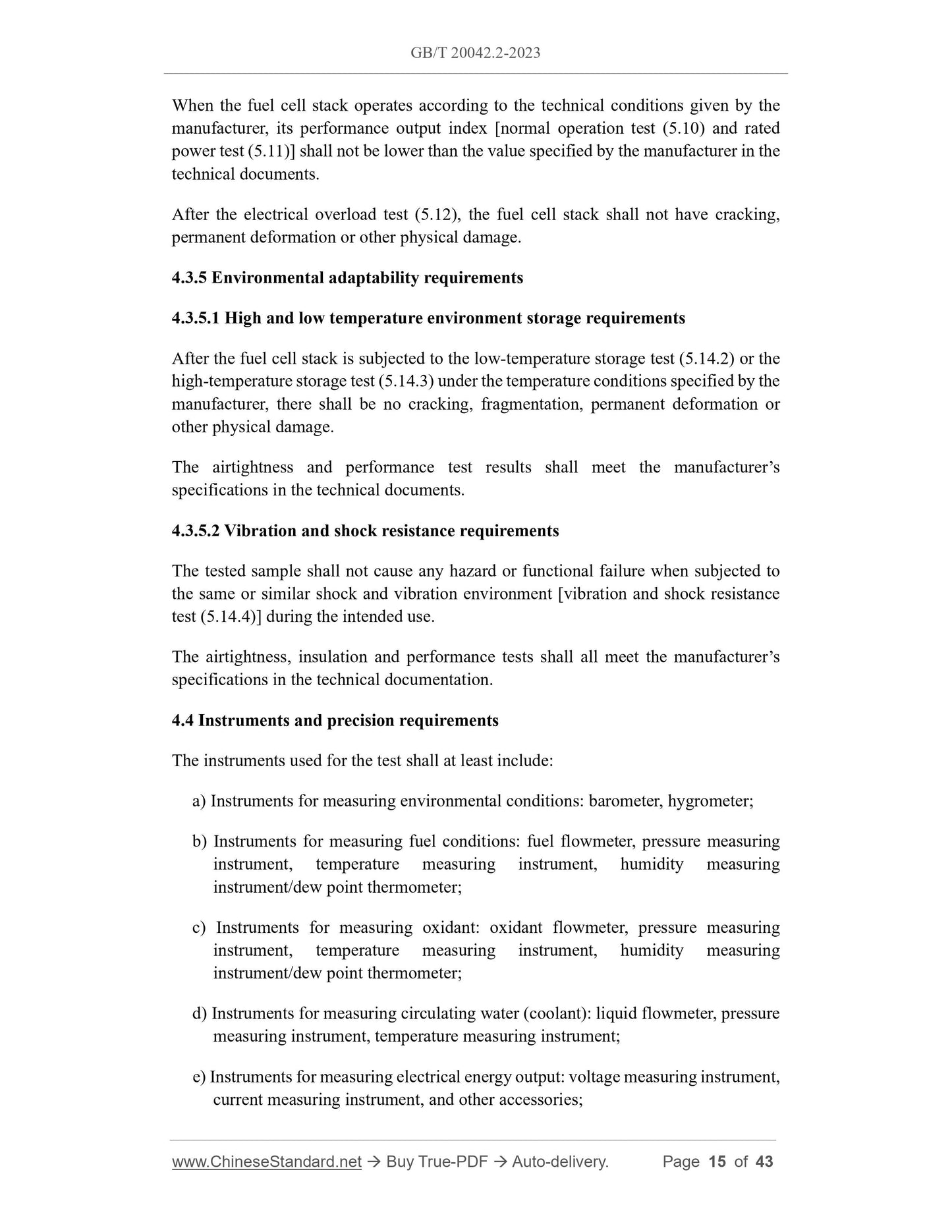

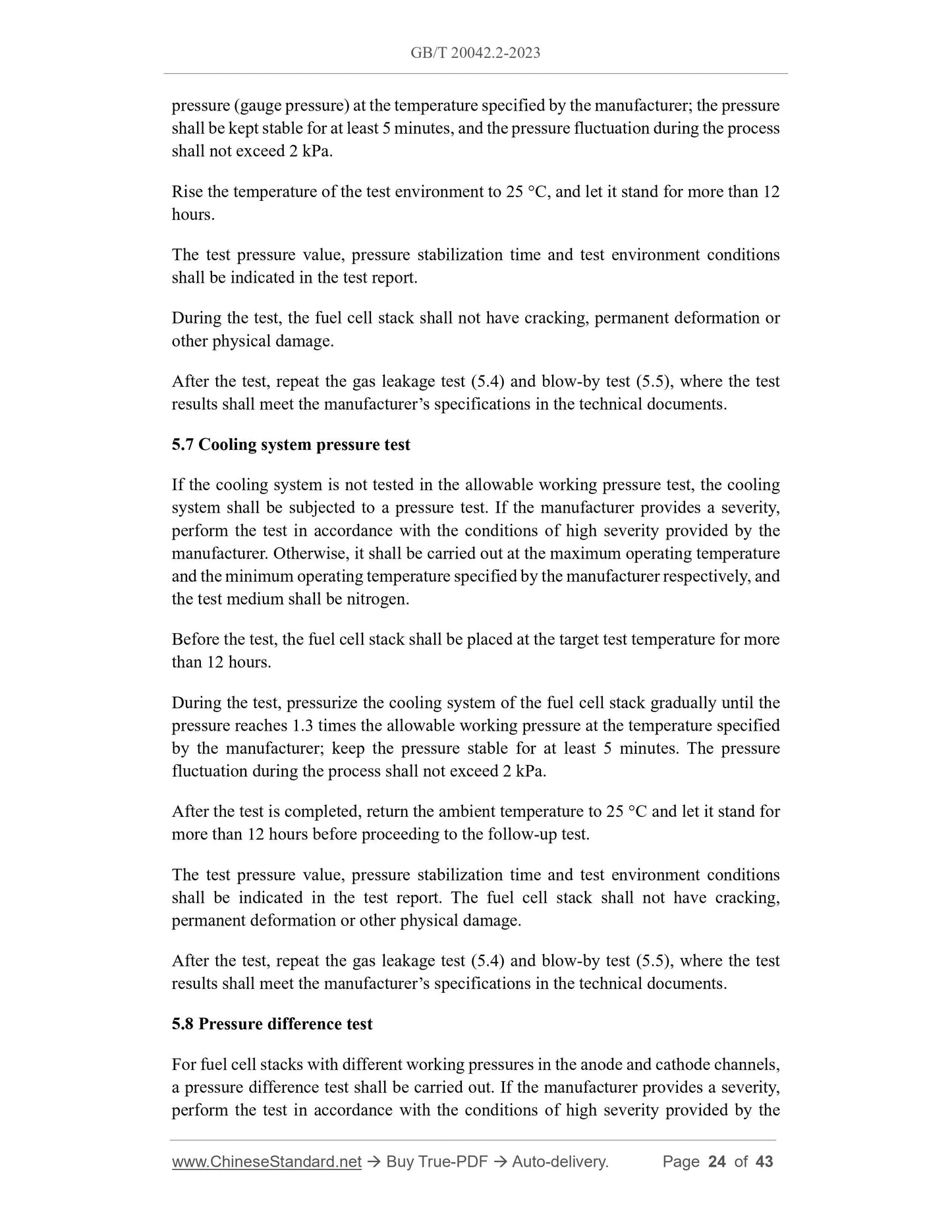
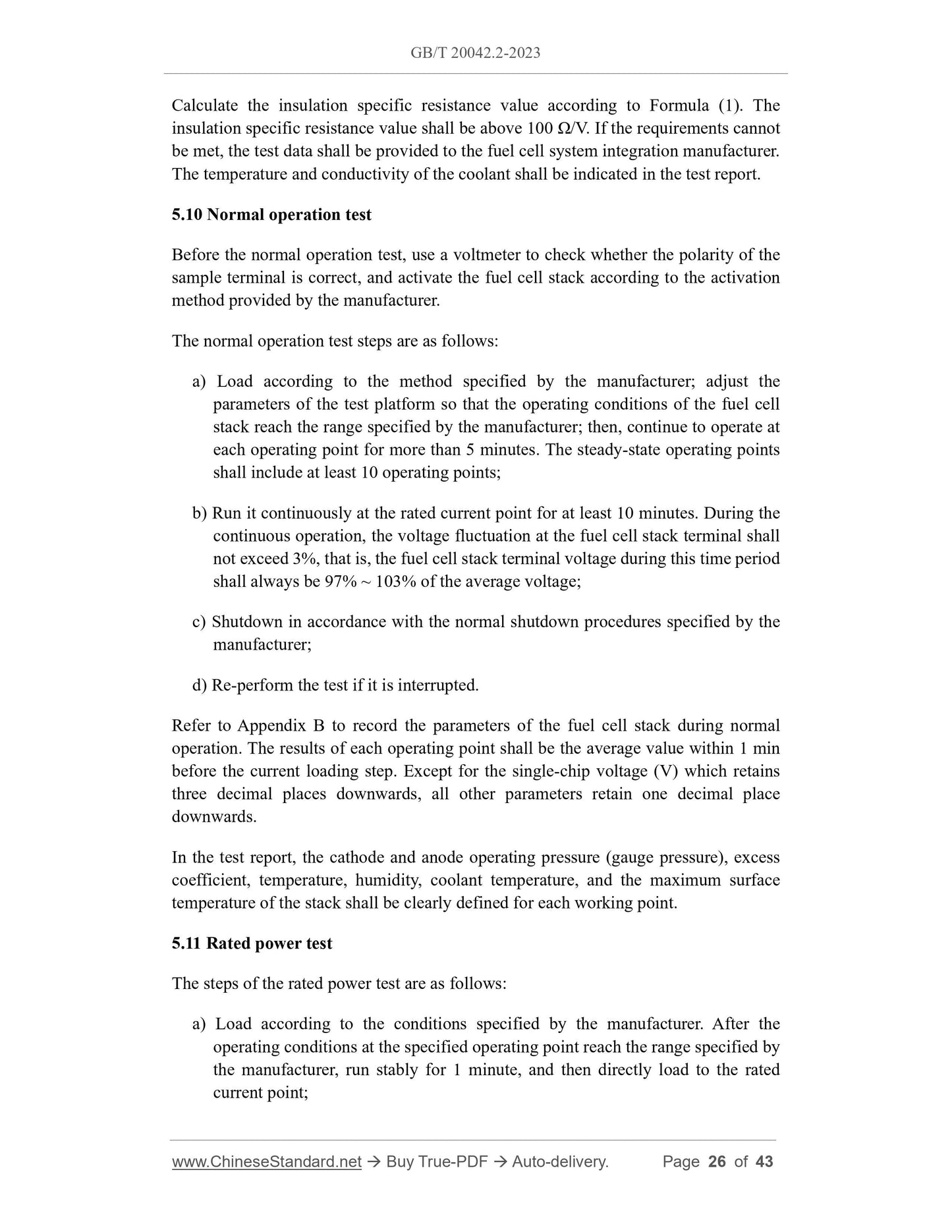
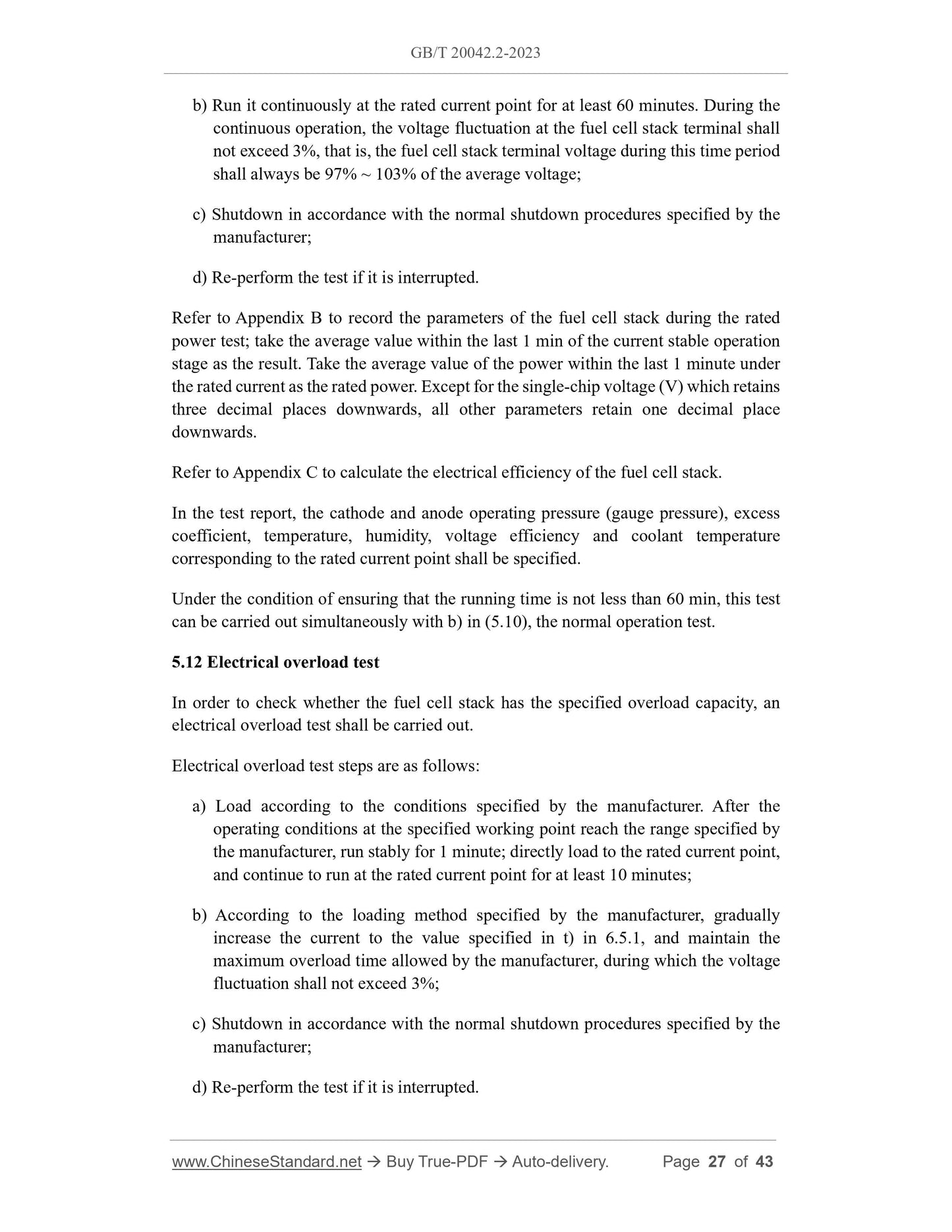