1
/
of
12
PayPal, credit cards. Download editable-PDF and invoice in 1 second!
GB/T 18442.6-2011 English PDF (GB/T18442.6-2011)
GB/T 18442.6-2011 English PDF (GB/T18442.6-2011)
Regular price
$140.00
Regular price
Sale price
$140.00
Unit price
/
per
Shipping calculated at checkout.
Couldn't load pickup availability
GB/T 18442.6-2011: Static vacuum insulated cryogenic pressure vessel -- Part 6: Safety device requirements
Delivery: 9 seconds. Download (and Email) true-PDF + Invoice.
Newer version: (Replacing this standard) GB/T 18442.6-2019
Get Quotation: Click GB/T 18442.6-2011 (Self-service in 1-minute)
Newer / historical versions: GB/T 18442.6-2019
Preview True-PDF (Reload/Scroll-down if blank)
Delivery: 9 seconds. Download (and Email) true-PDF + Invoice.
Newer version: (Replacing this standard) GB/T 18442.6-2019
Get Quotation: Click GB/T 18442.6-2011 (Self-service in 1-minute)
Newer / historical versions: GB/T 18442.6-2019
Preview True-PDF (Reload/Scroll-down if blank)
Share
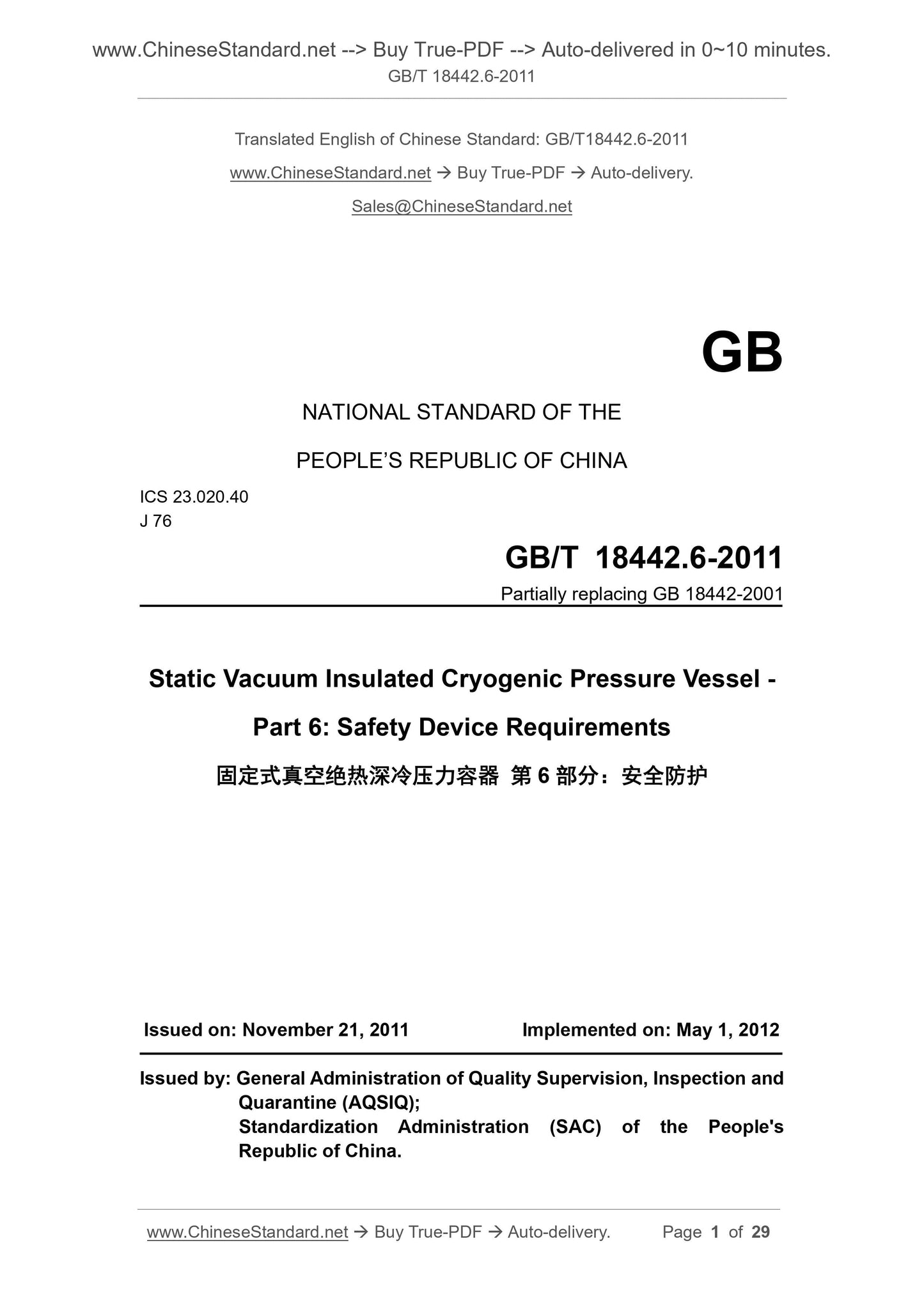
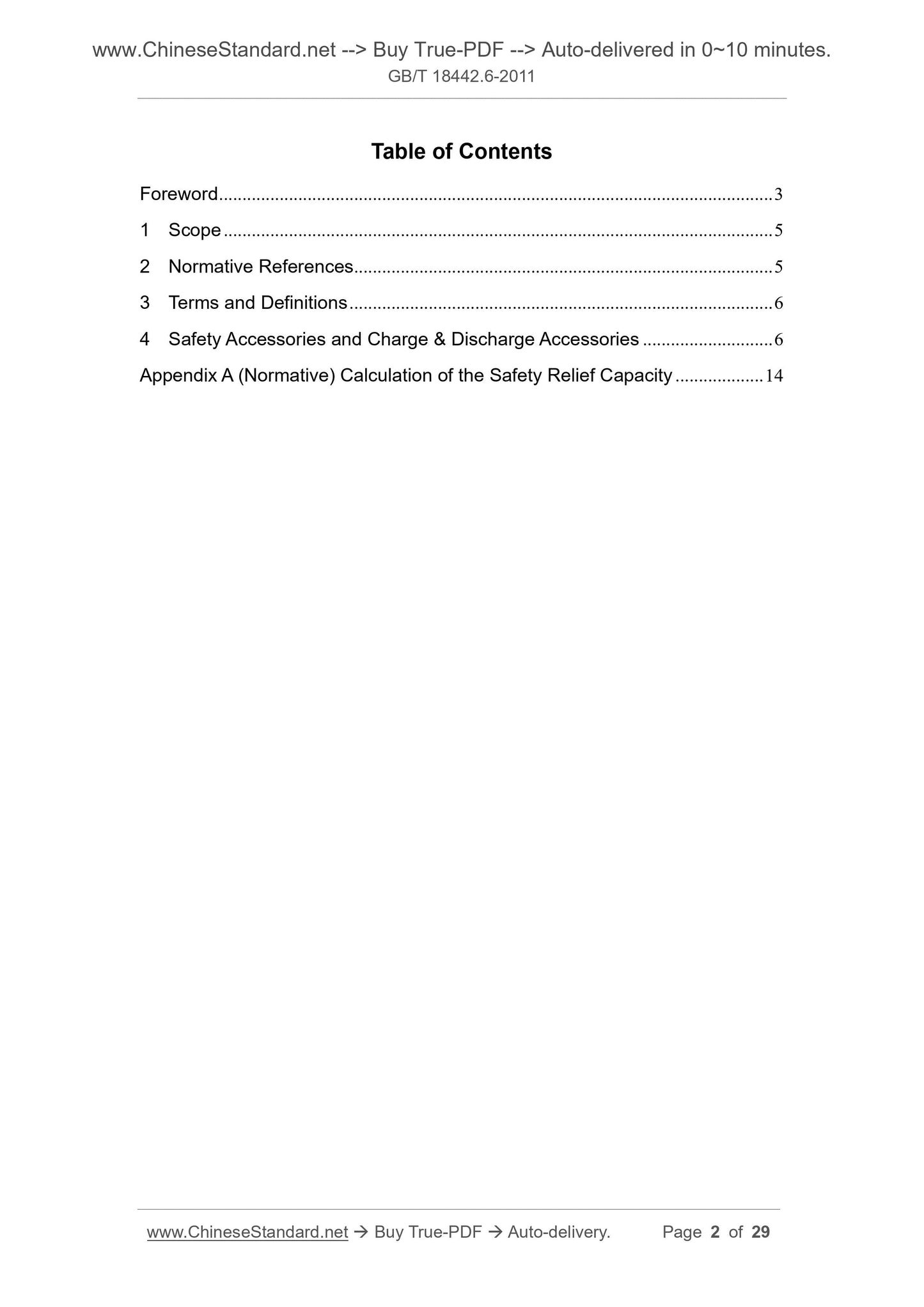
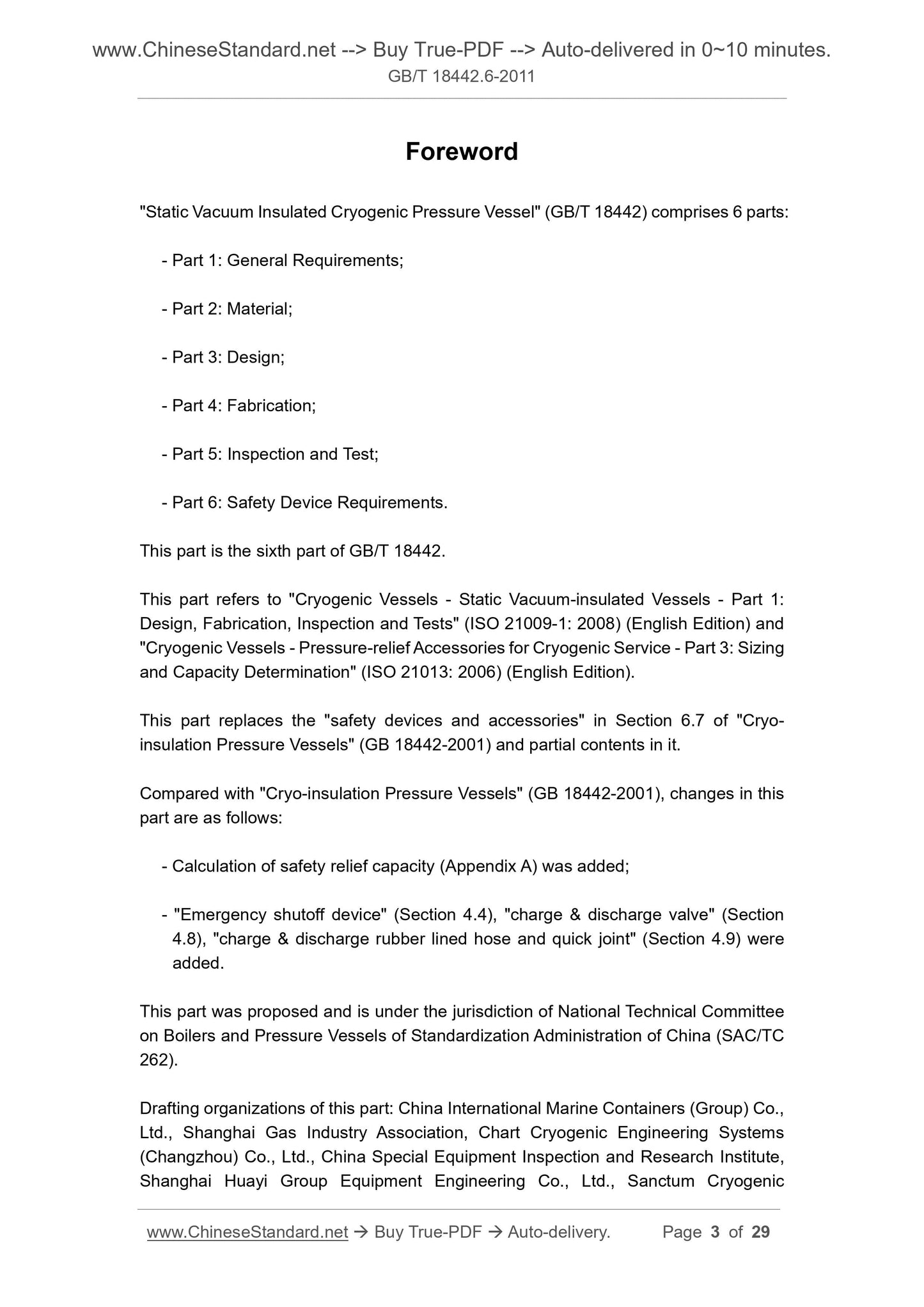
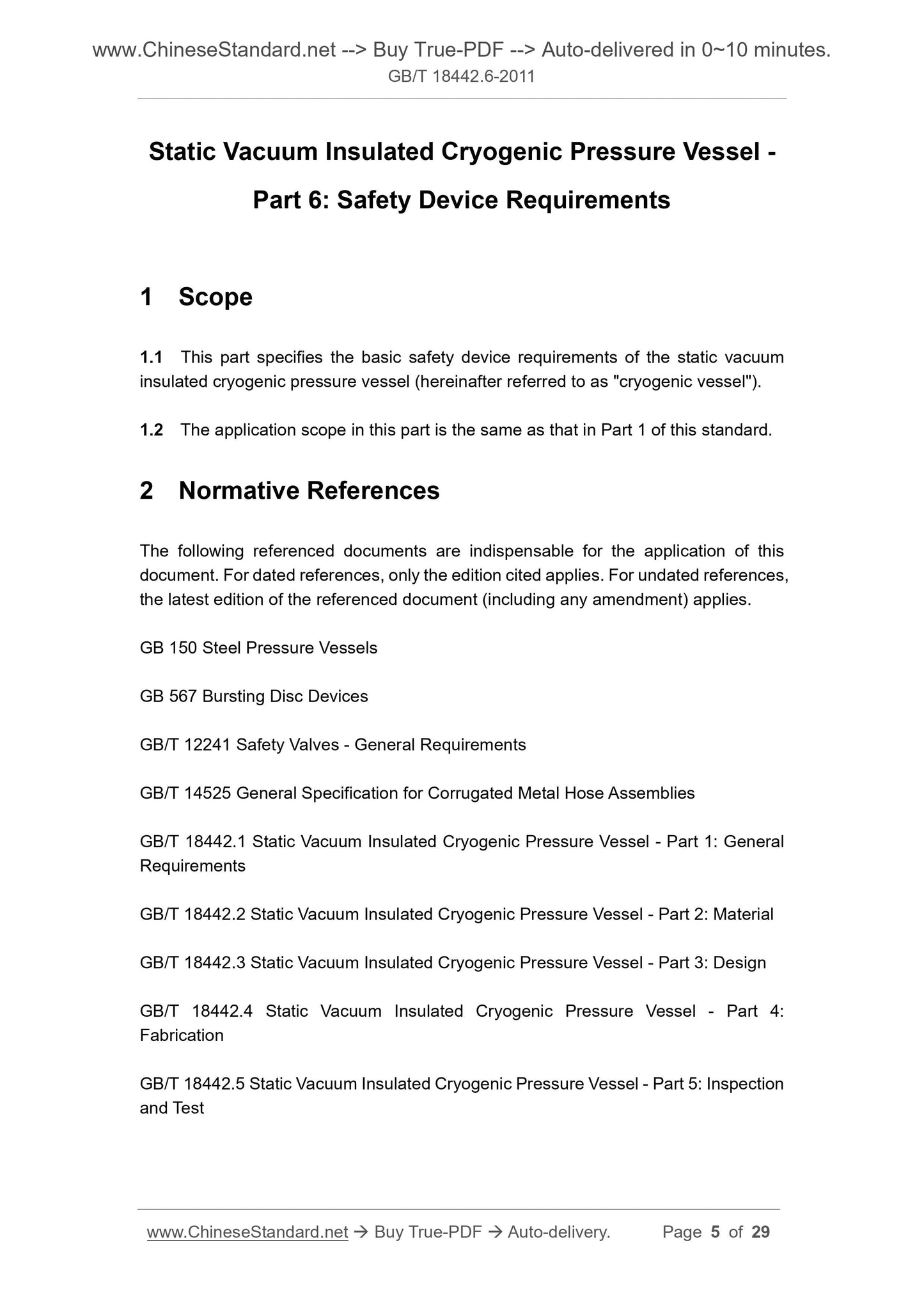
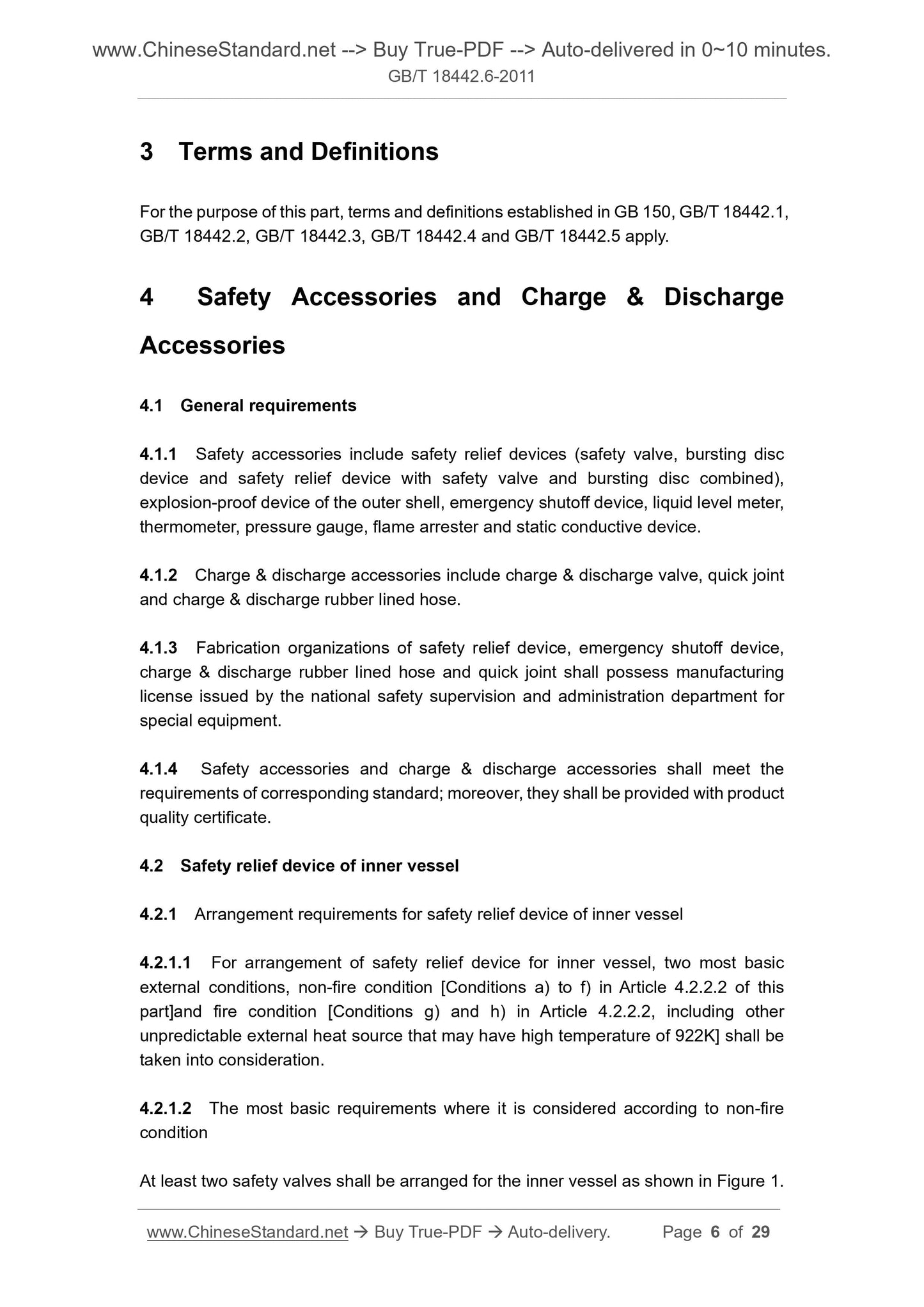
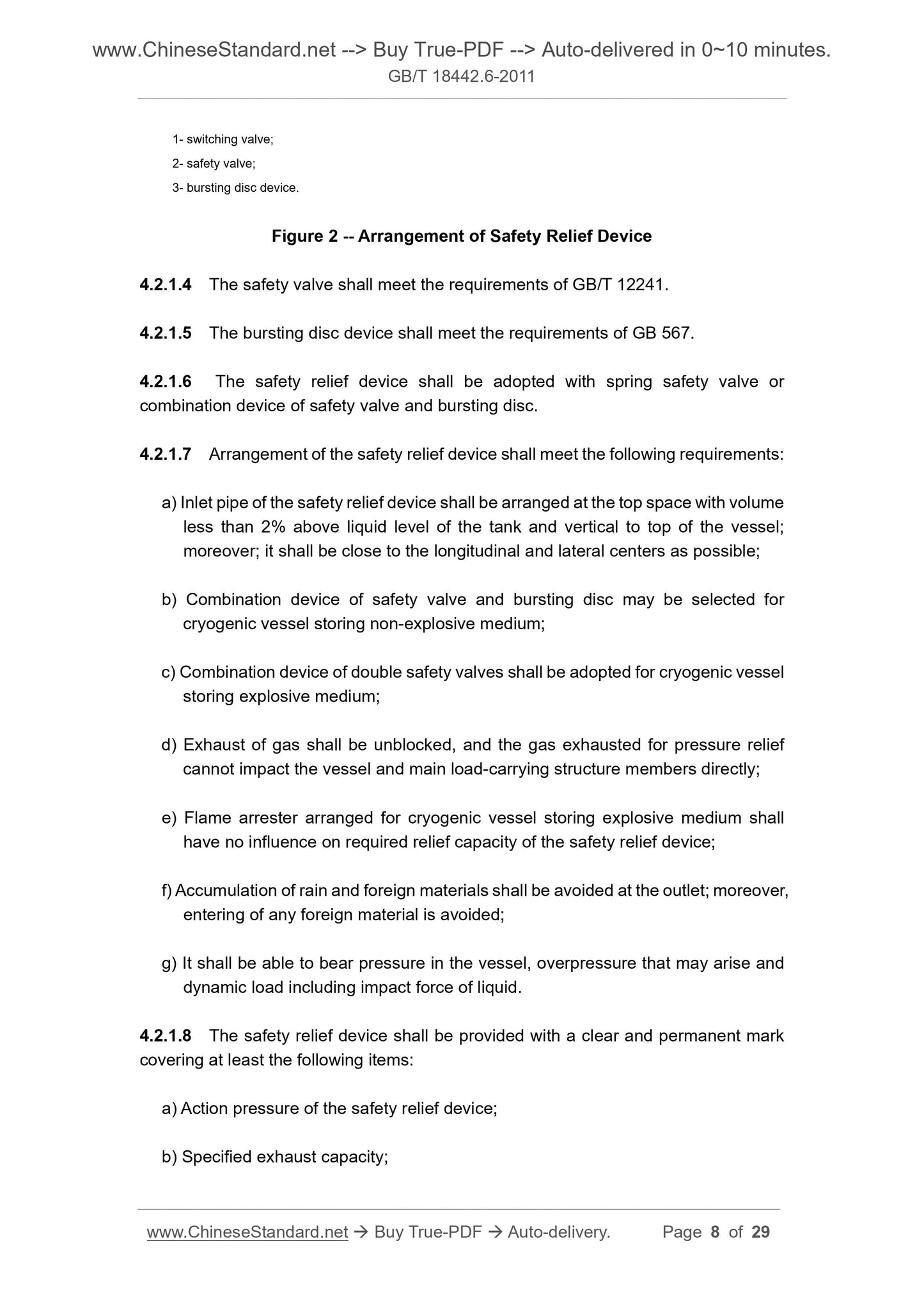
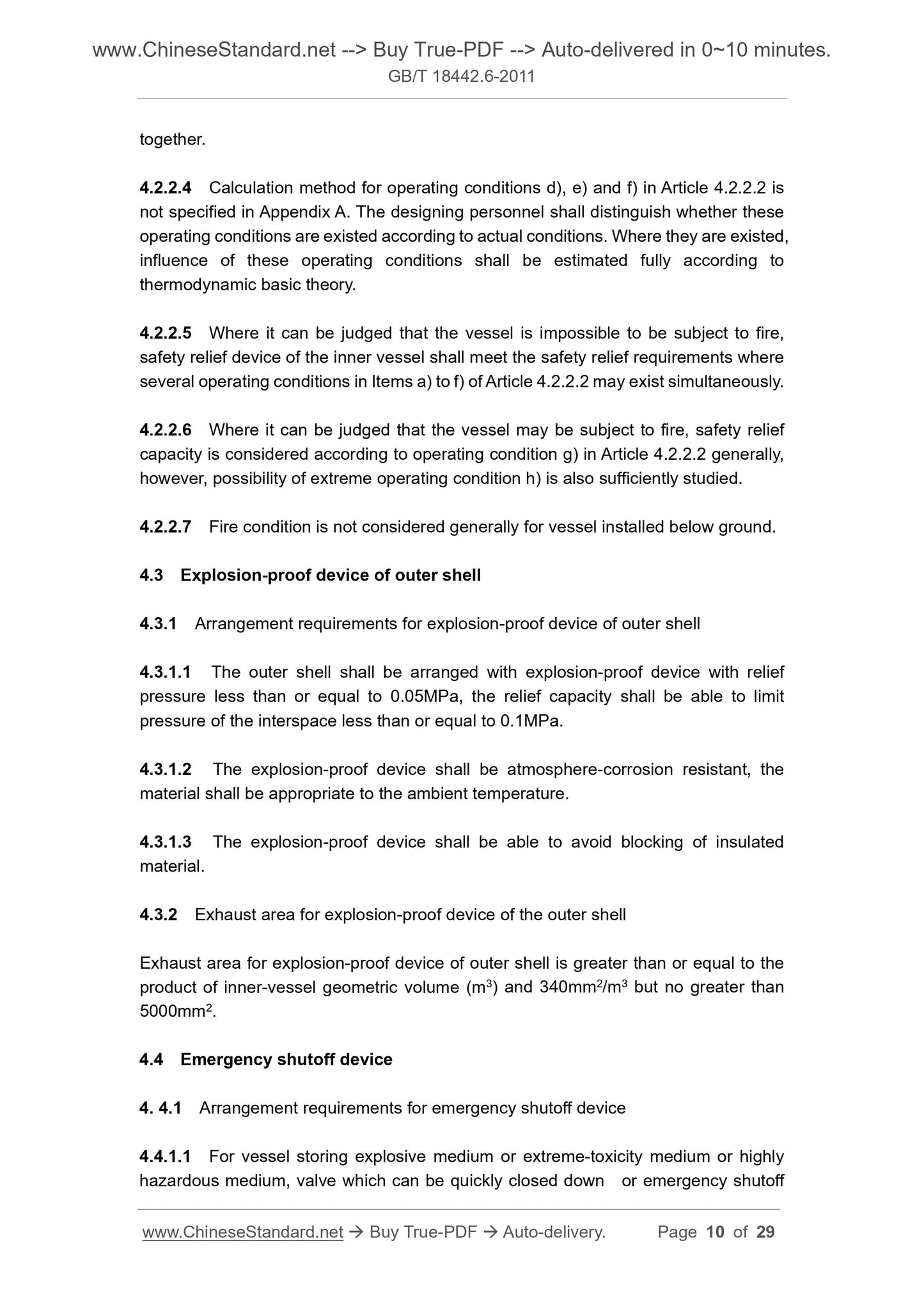
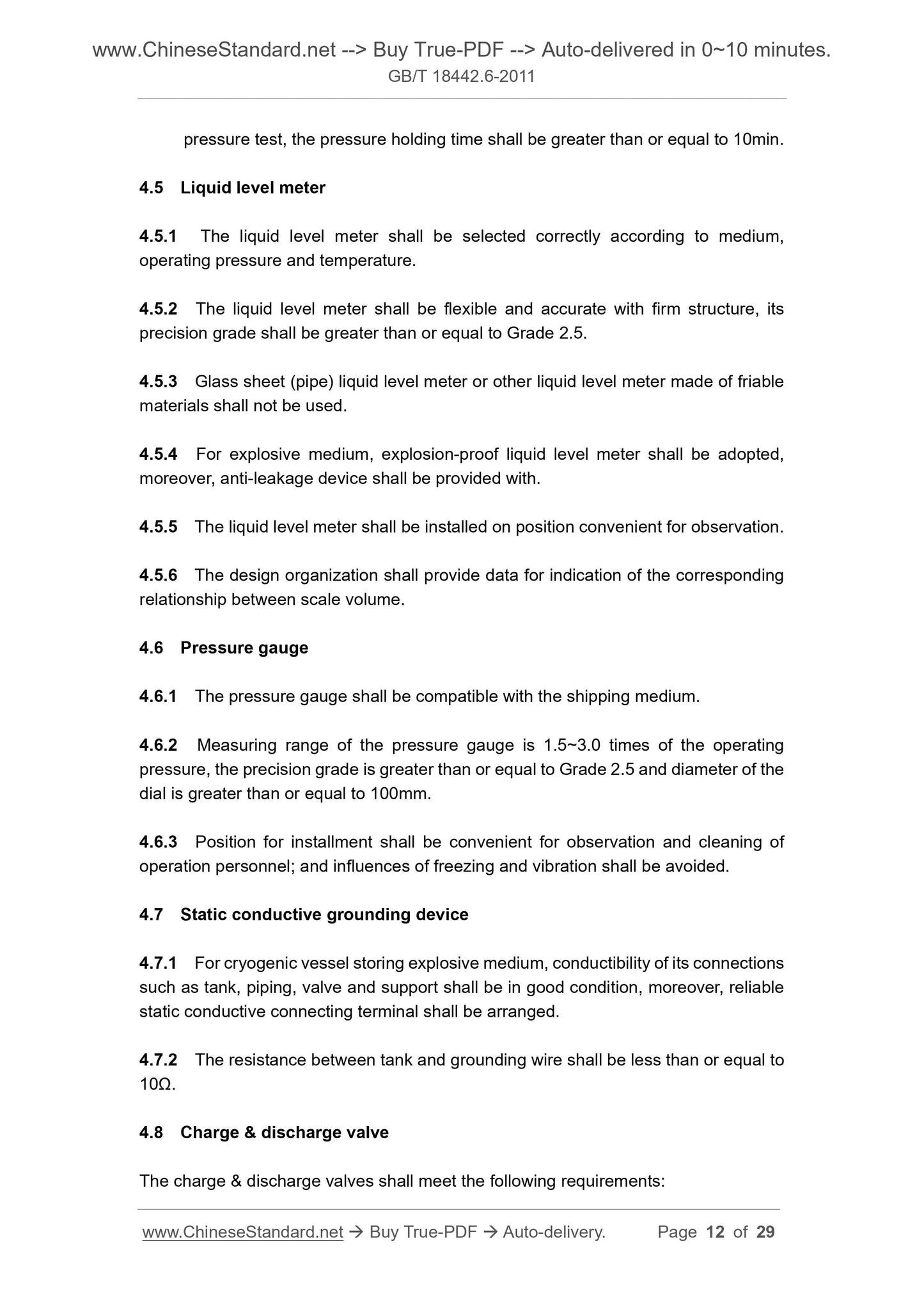
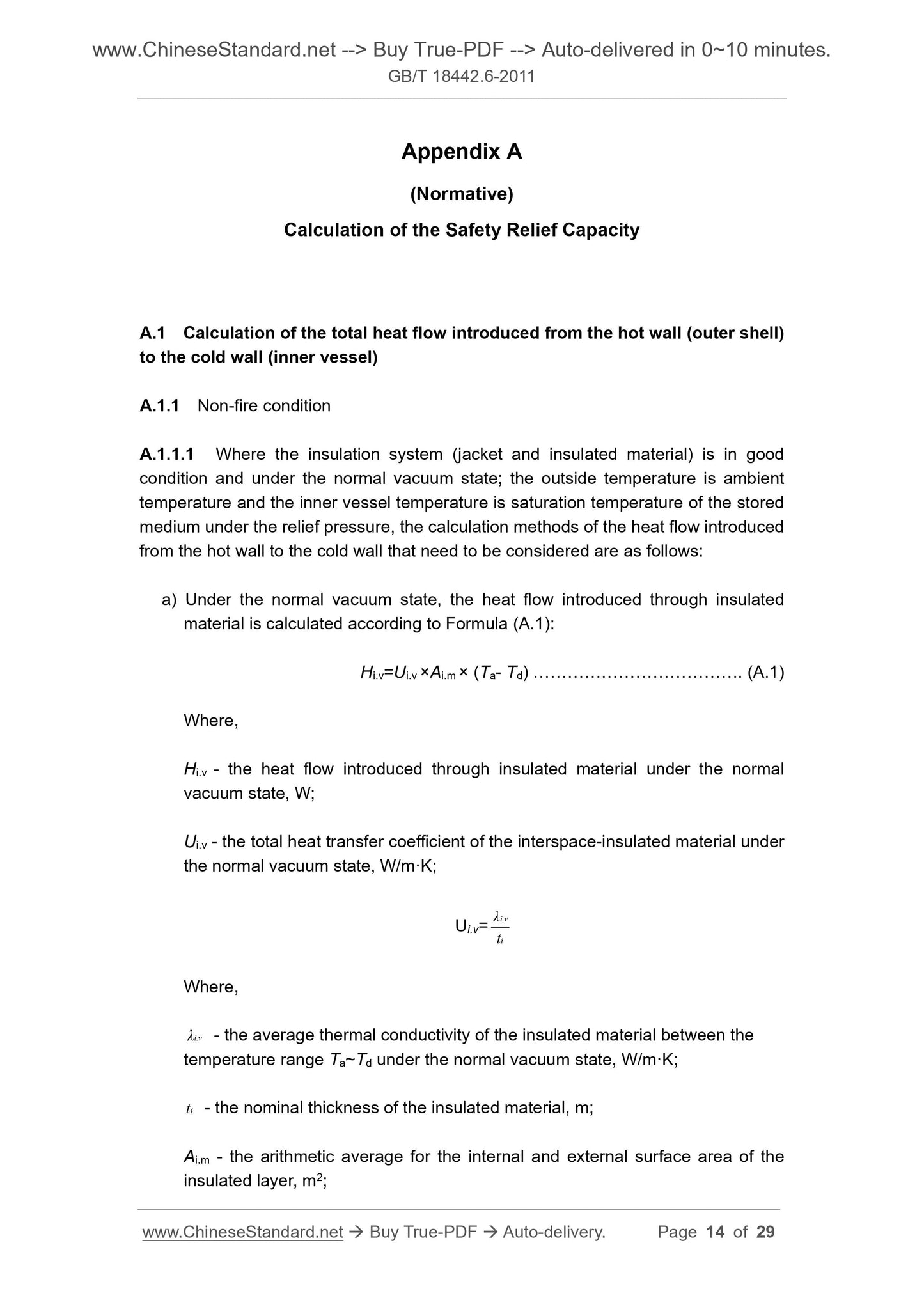
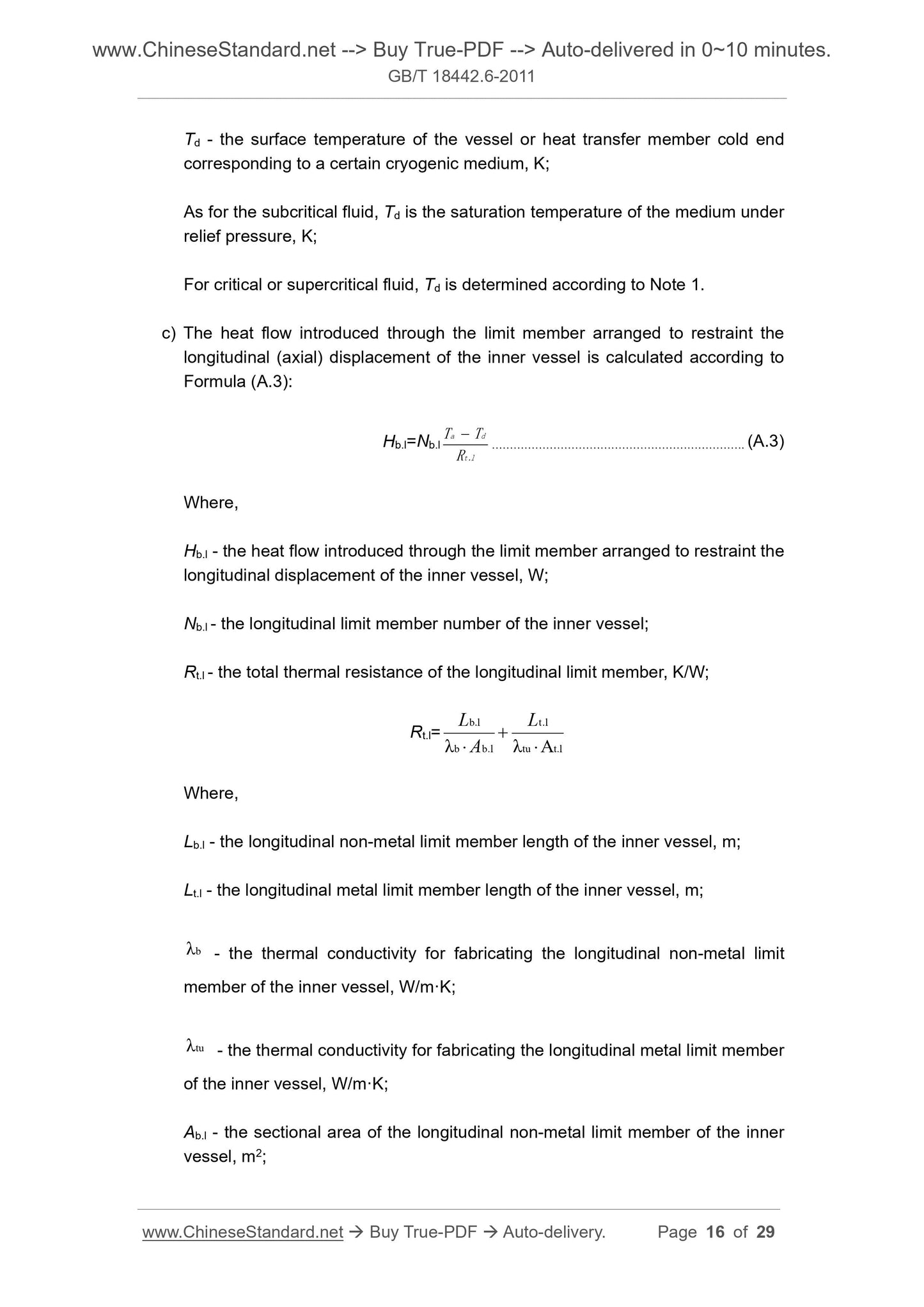
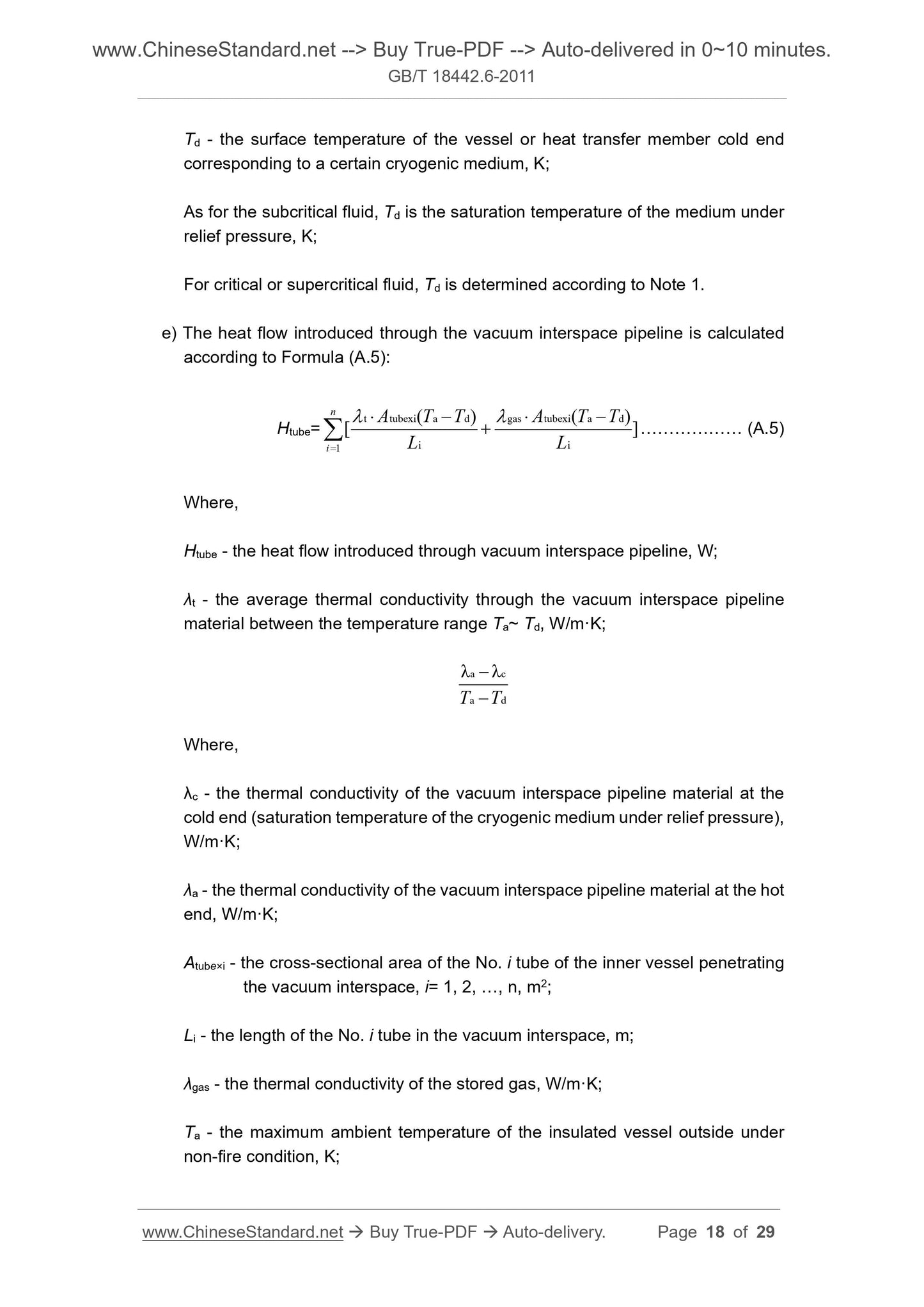
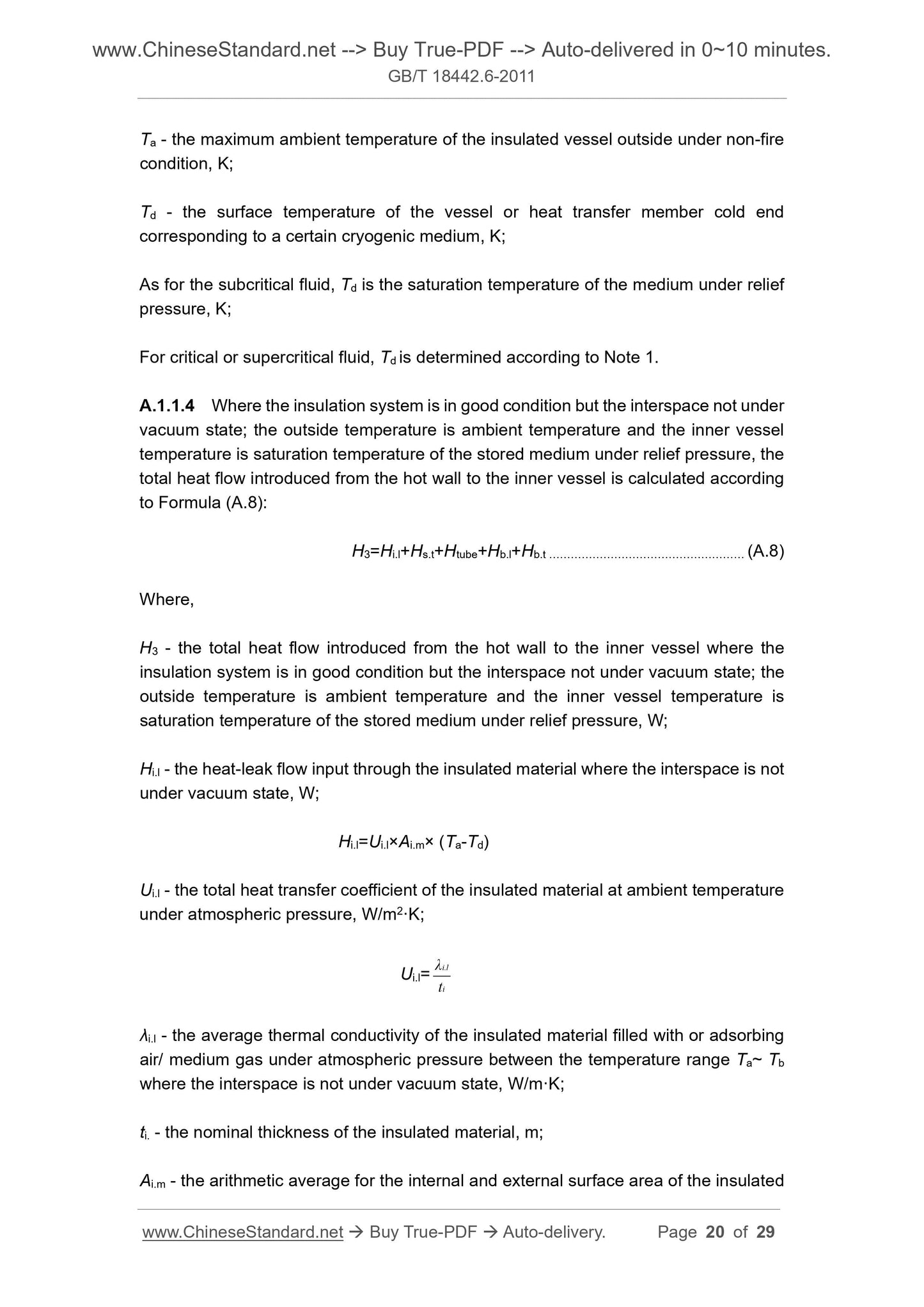