1
/
of
12
PayPal, credit cards. Download editable-PDF & invoice In 1 second!
GB/T 18442.4-2011 English PDF (GB/T18442.4-2011)
GB/T 18442.4-2011 English PDF (GB/T18442.4-2011)
Regular price
$140.00
Regular price
Sale price
$140.00
Unit price
/
per
Shipping calculated at checkout.
Couldn't load pickup availability
GB/T 18442.4-2011: Static vacuum insulated cryogenic pressure vessel -- Part 4: Fabrication
Delivery: 9 seconds. Download (and Email) true-PDF + Invoice.Get Quotation: Click GB/T 18442.4-2011 (Self-service in 1-minute)
Newer / historical versions: GB/T 18442.4-2011
Preview True-PDF
Scope
1.1 This part specifies the basic fabrication requirements of Static Vacuum InsulatedCryogenic Pressure Vessel (hereinafter referred to as "cryogenic vessel").
1.2 The application scope in this part is the same as that in part 1 of this standard.
Basic Data
Standard ID | GB/T 18442.4-2011 (GB/T18442.4-2011) |
Description (Translated English) | Static vacuum insulated cryogenic pressure vessel -- Part 4: Fabrication |
Sector / Industry | National Standard (Recommended) |
Classification of Chinese Standard | J76 |
Classification of International Standard | 23.020.40 |
Word Count Estimation | 19,185 |
Date of Issue | 2011-11-21 |
Date of Implementation | 2012-05-01 |
Older Standard (superseded by this standard) | GB 18442-2001 |
Quoted Standard | GB 150; GB/T 1804-2000; GB/T 9969; GB/T 18442.1-2011; GB/T 18442.2; GB/T 18442.3; GB/T 25198; JB/T 4711; JB/T 4730.1; JB/T 4730.2; JB/T 4730.3; JB/T 4730.4; JB/T 4730.5; JB/T 4730.10; NB/T 47014; NB/T 47015; NB/T 47016; TSG R0004-2009 |
Regulation (derived from) | National Standards Bulletin 2011 No. 18 |
Issuing agency(ies) | General Administration of Quality Supervision, Inspection and Quarantine of the People's Republic of China, Standardization Administration of the People's Republic of China |
Summary | This standard specifies the fixed vacuum insulated cryogenic pressure vessel manufacture the basic requirements. Scope of this section with Part 1 of this standard. |
Share
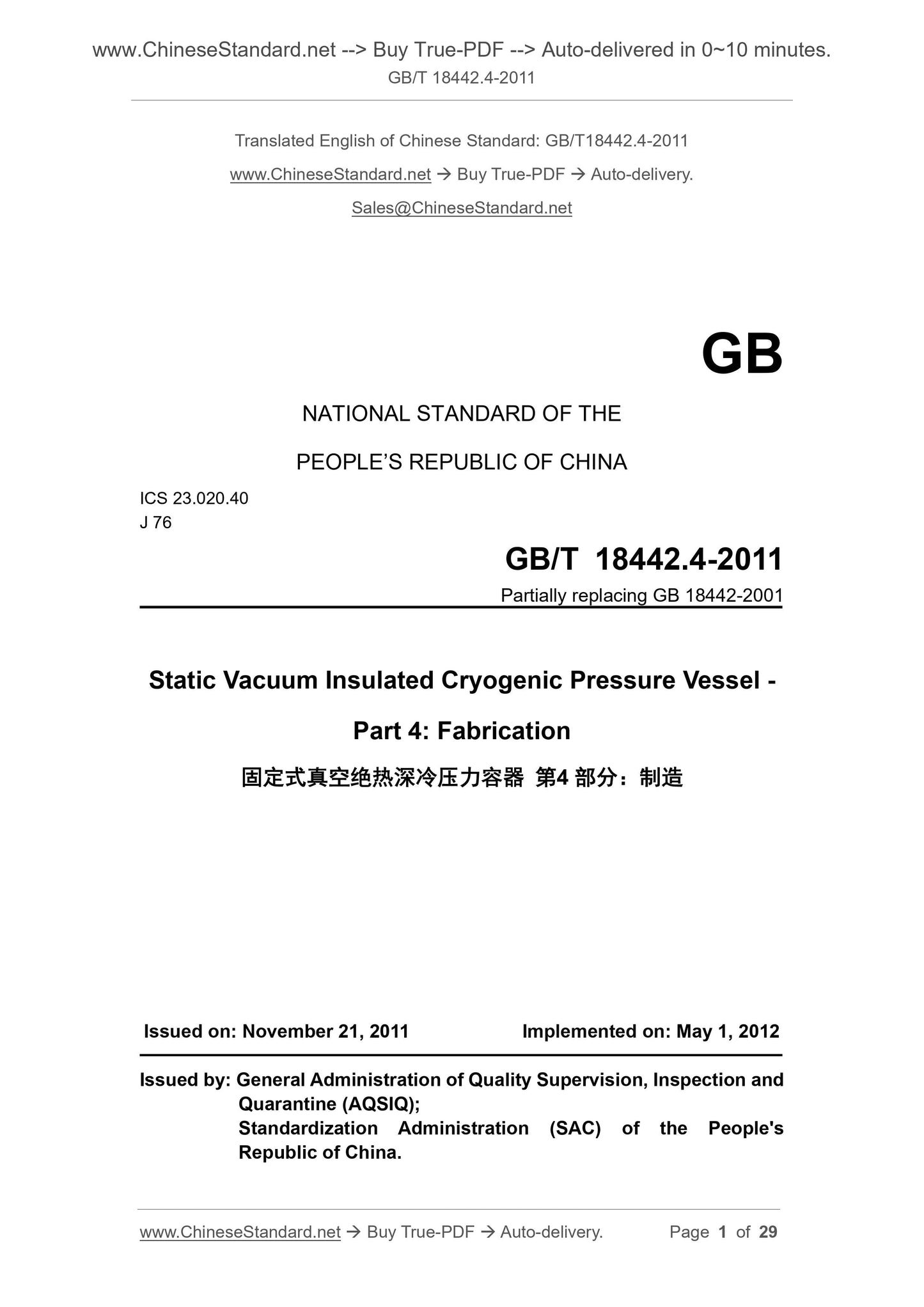
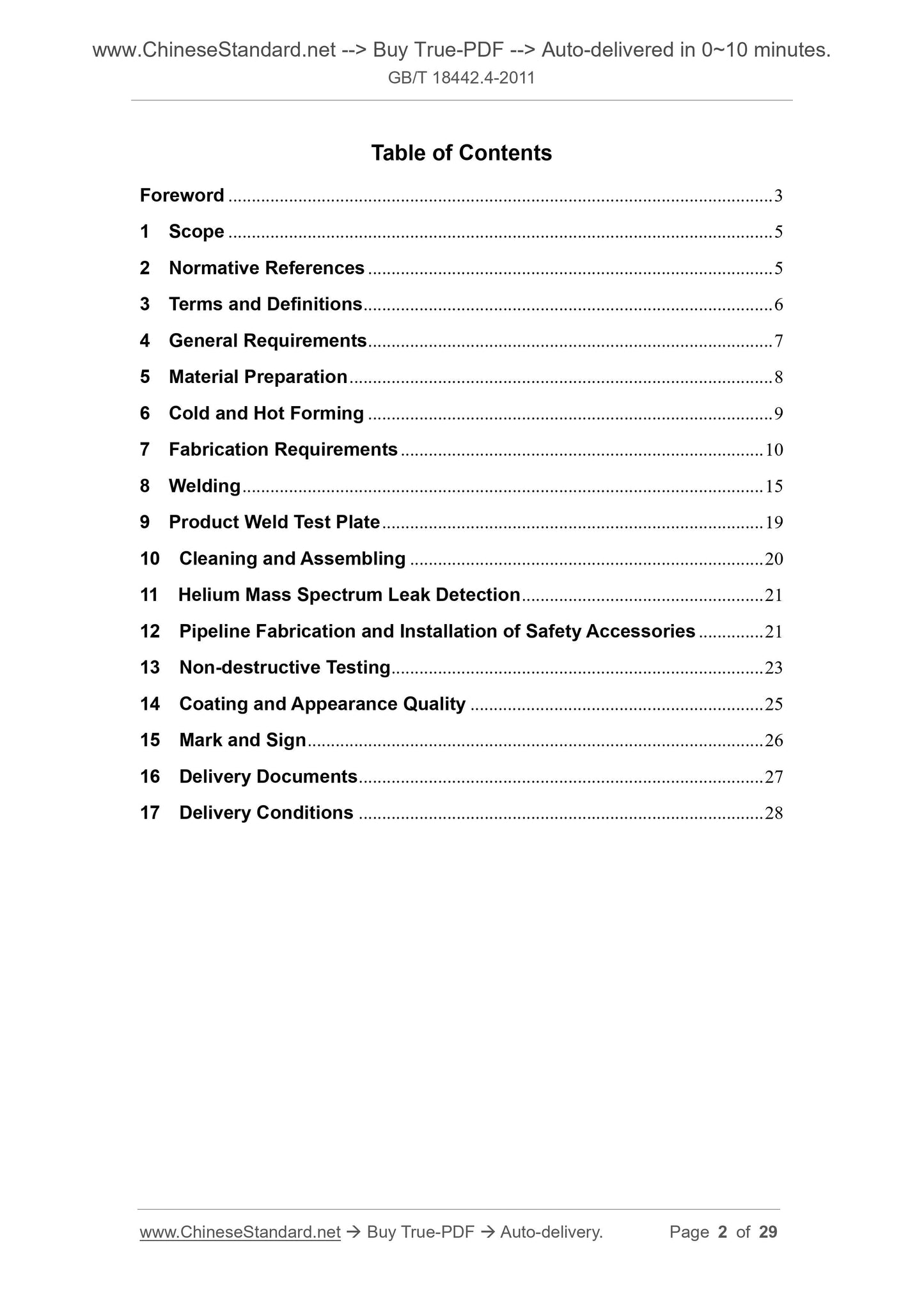
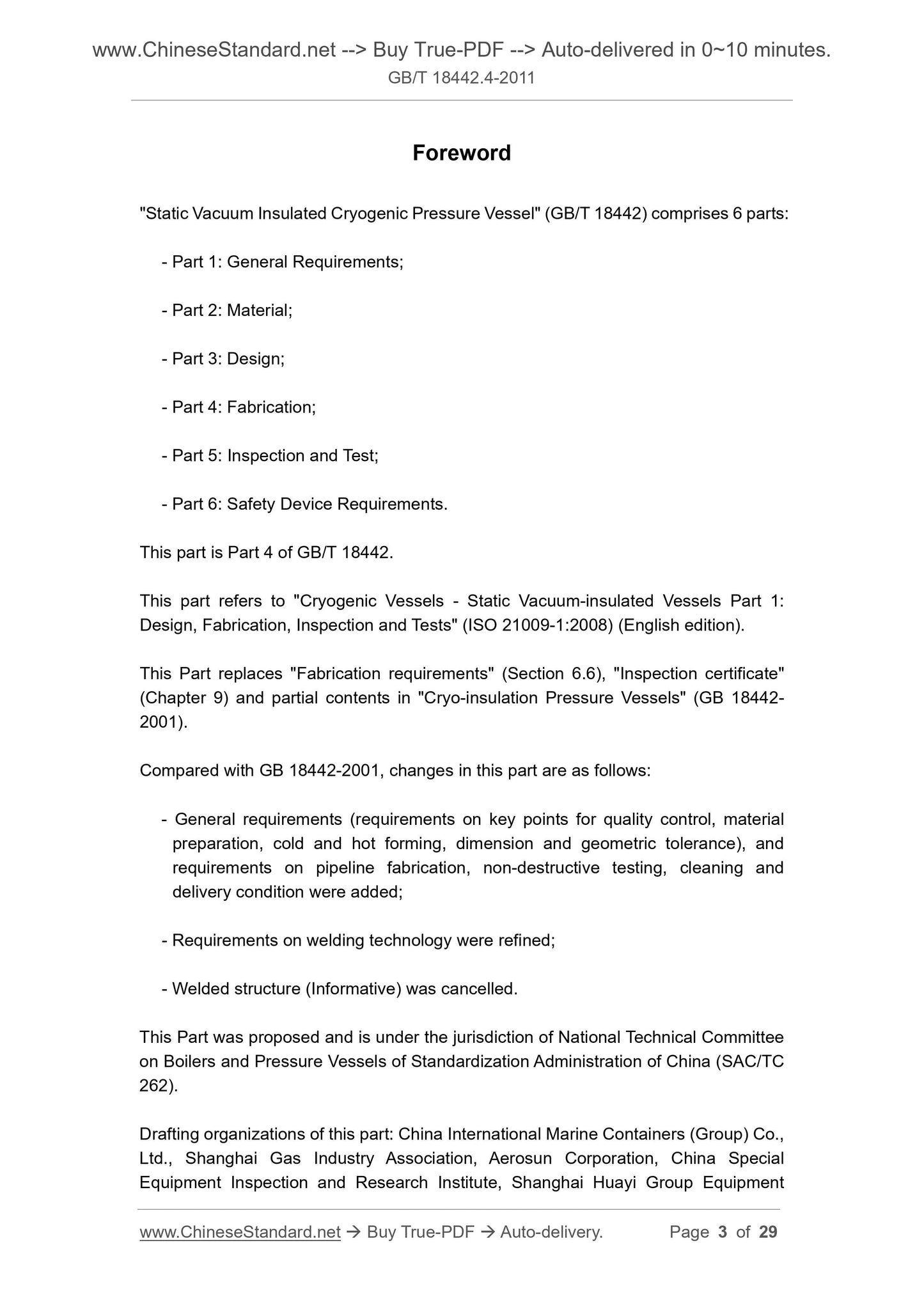
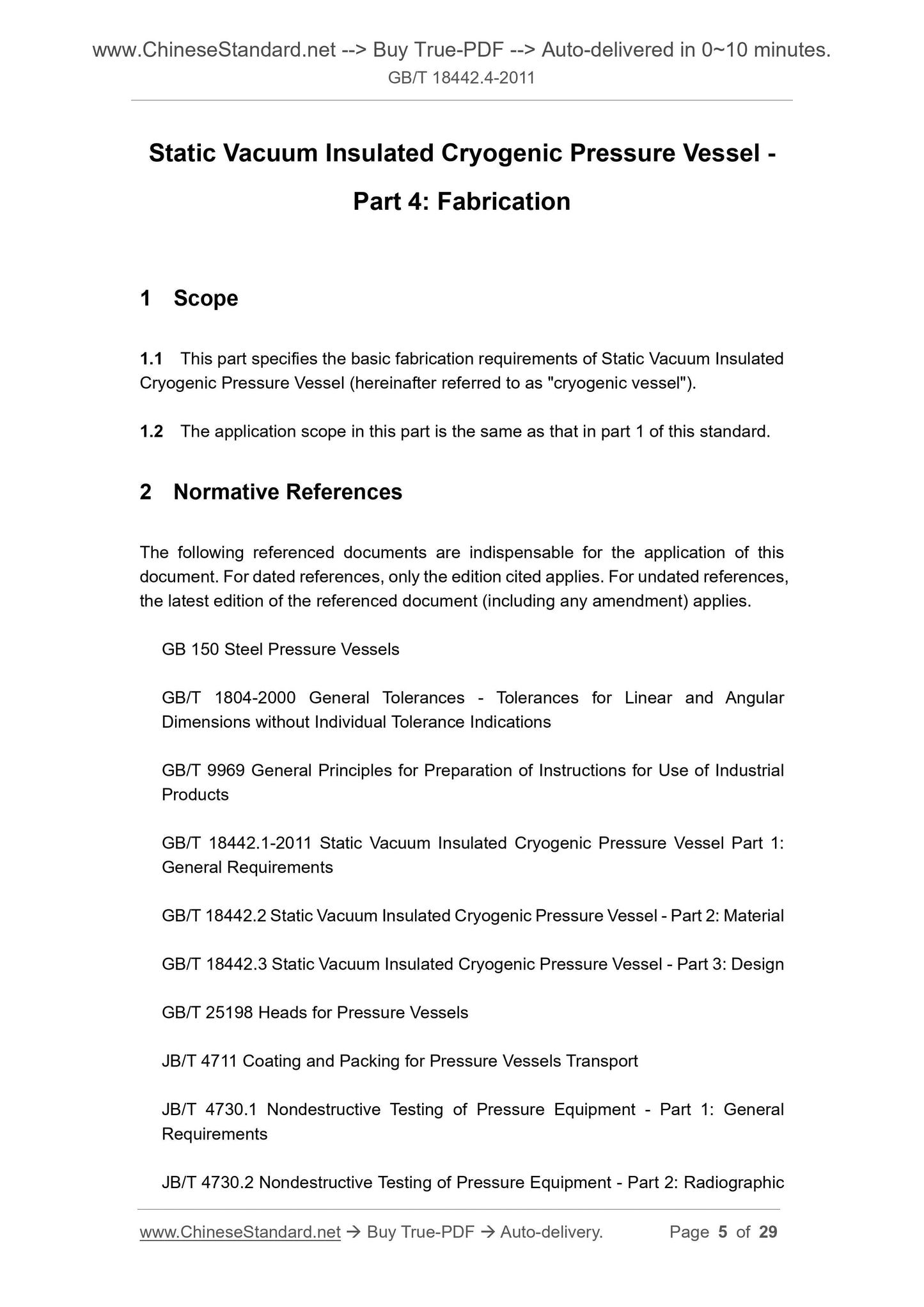
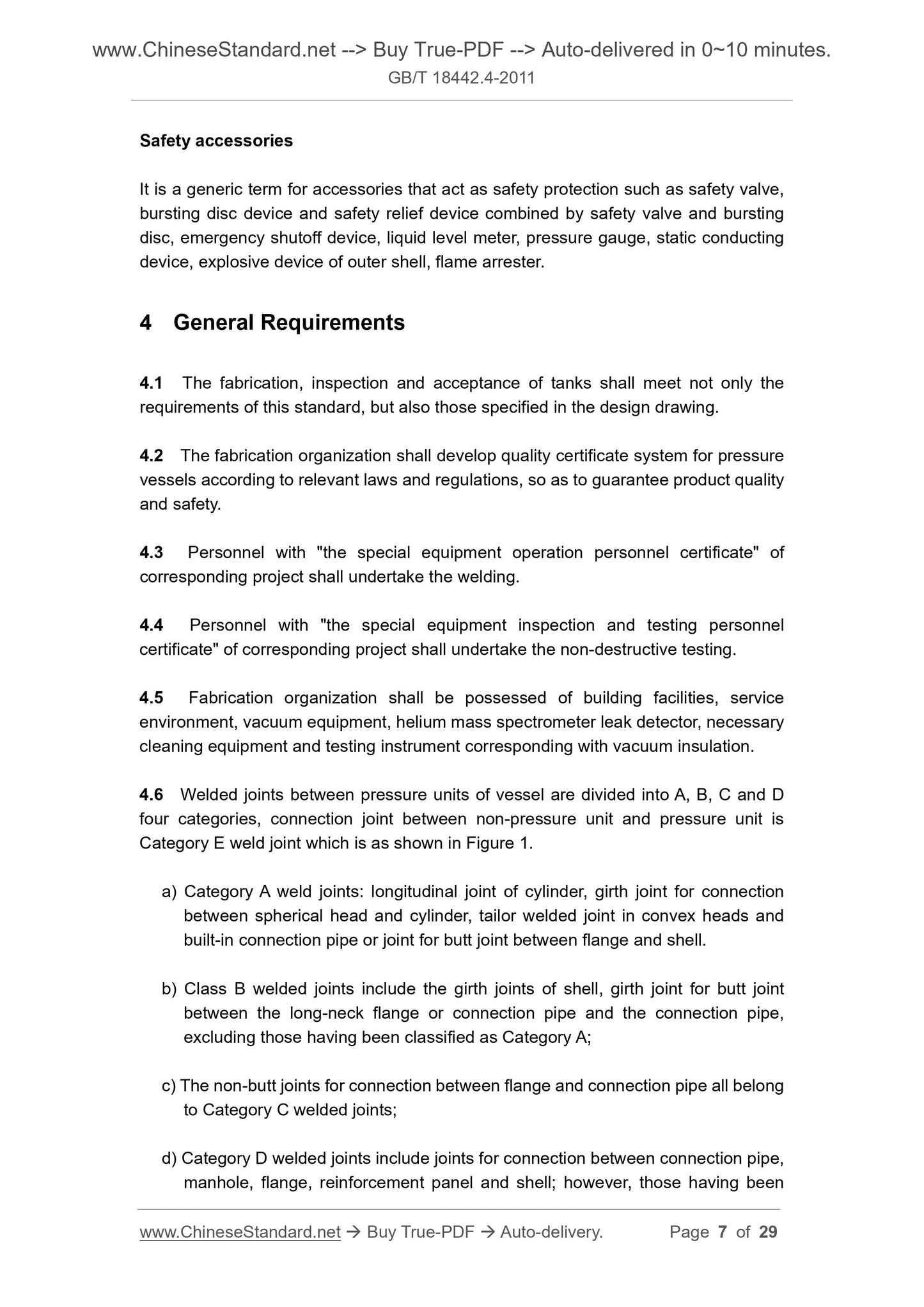
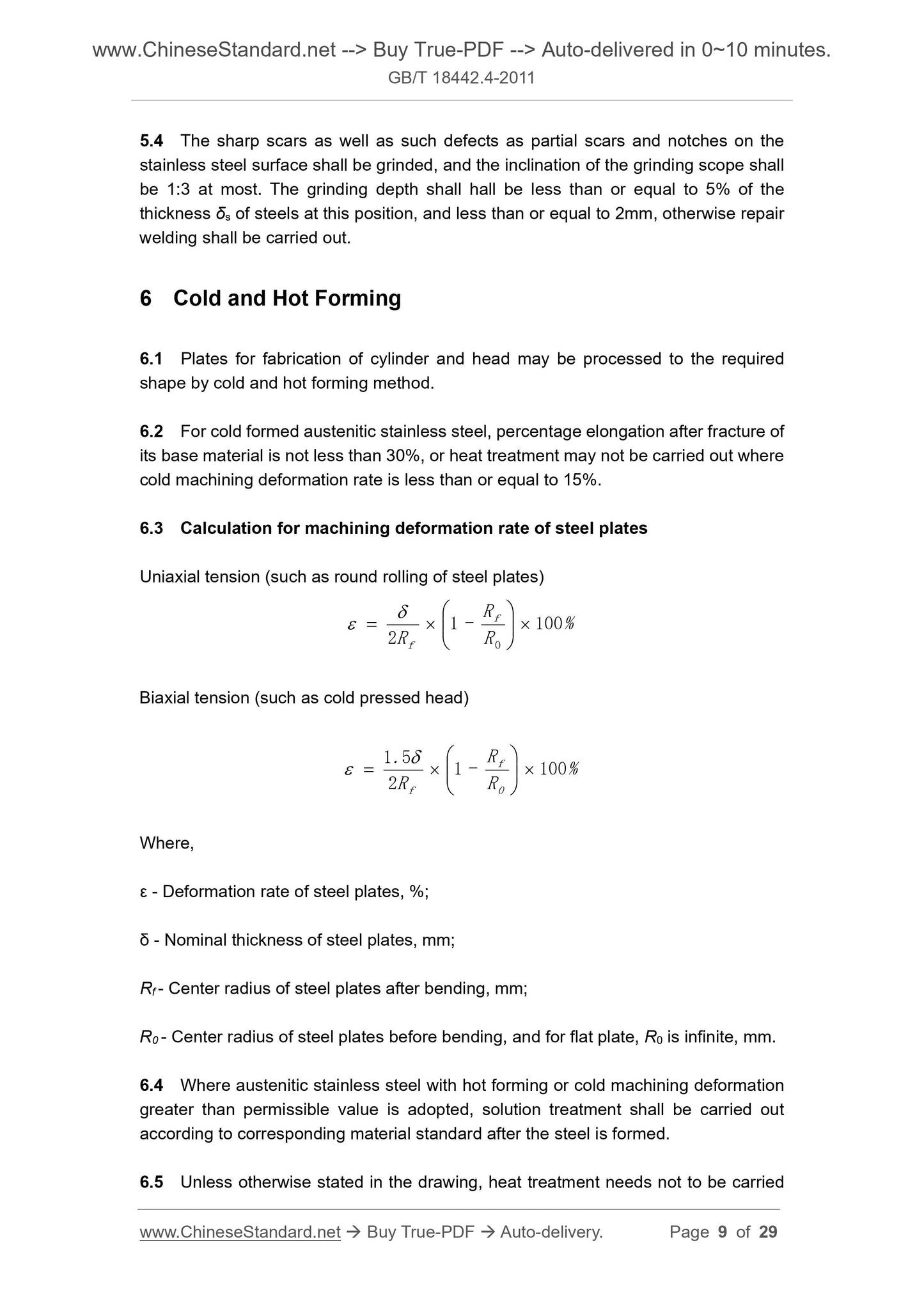
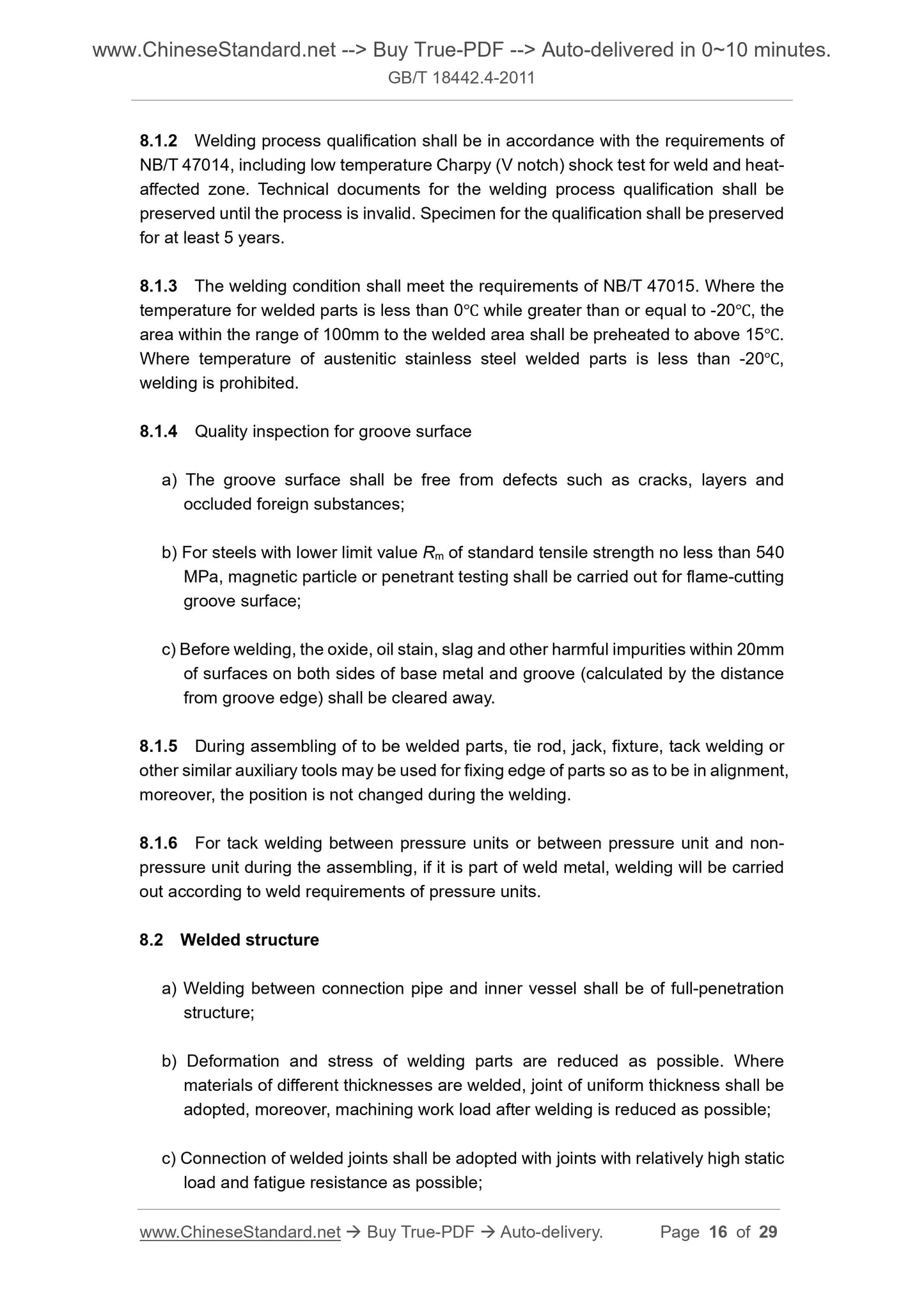
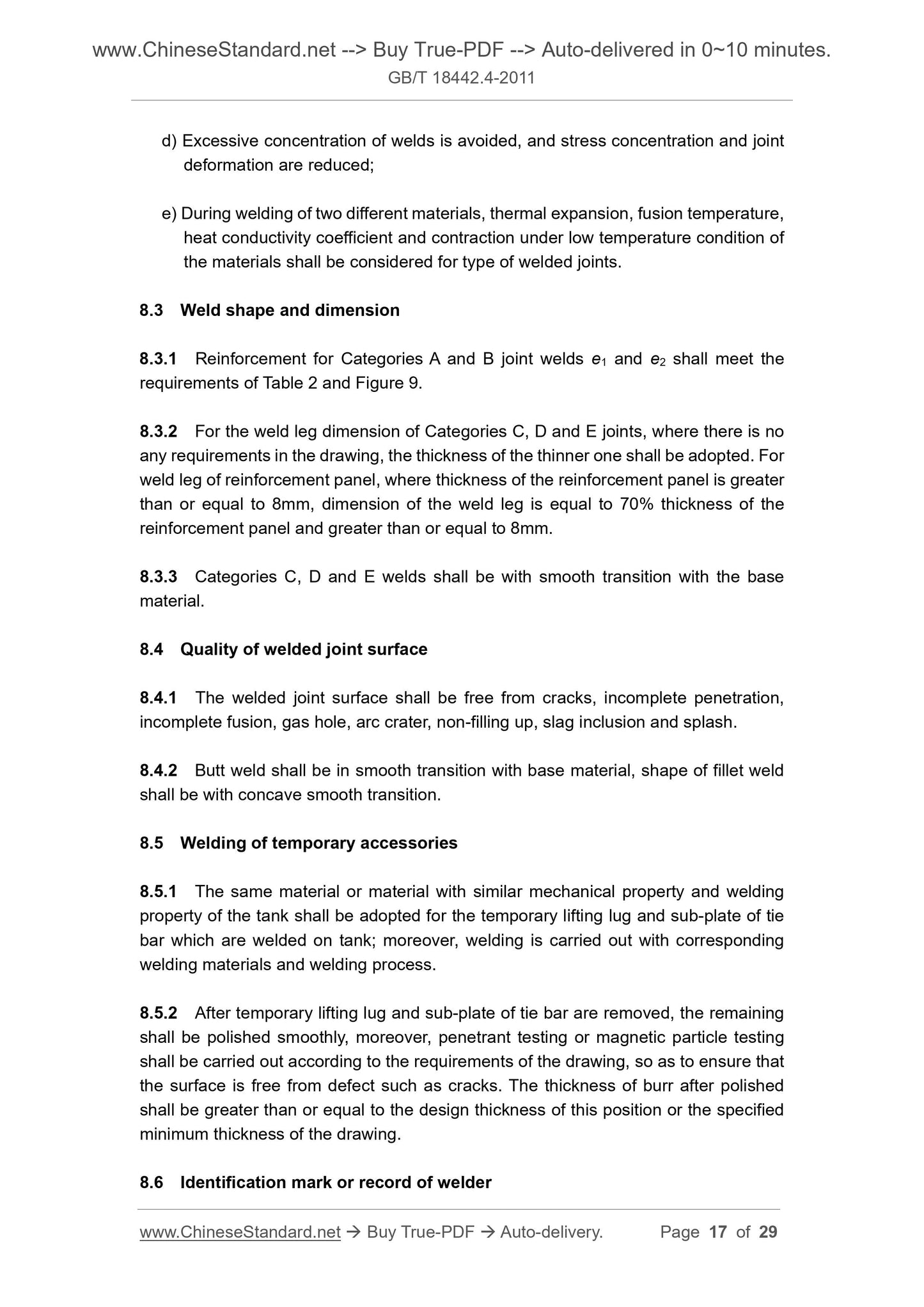
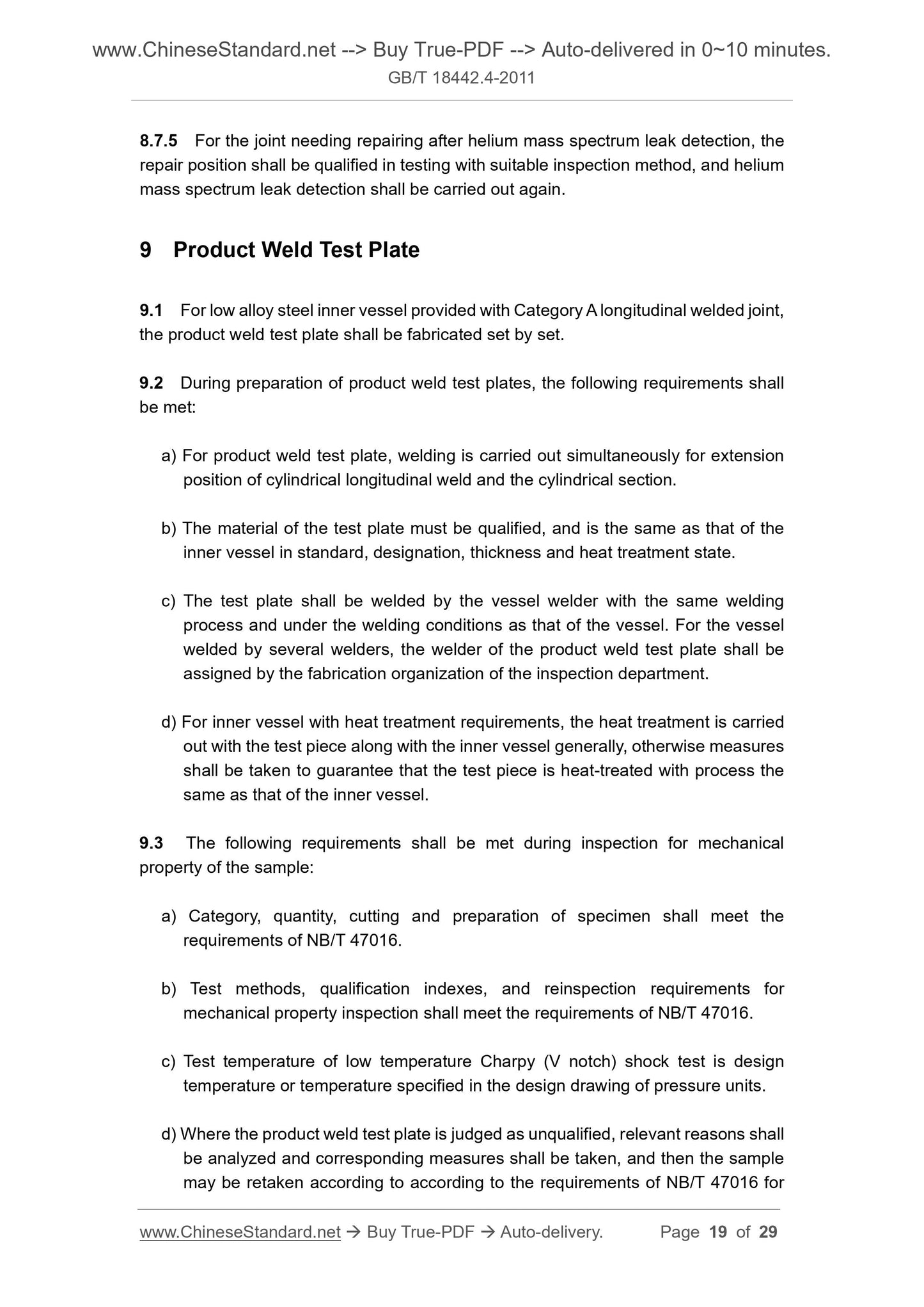
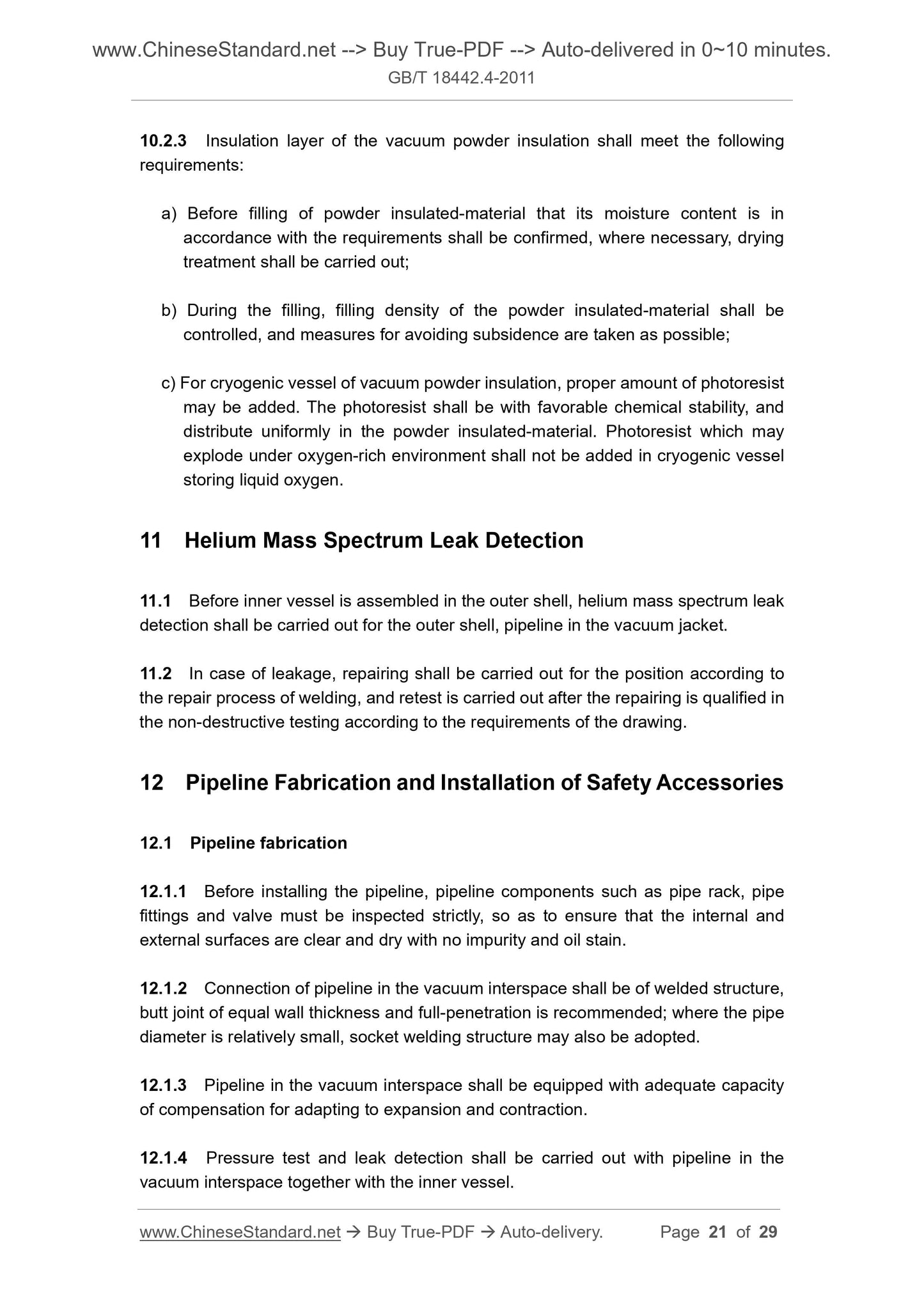
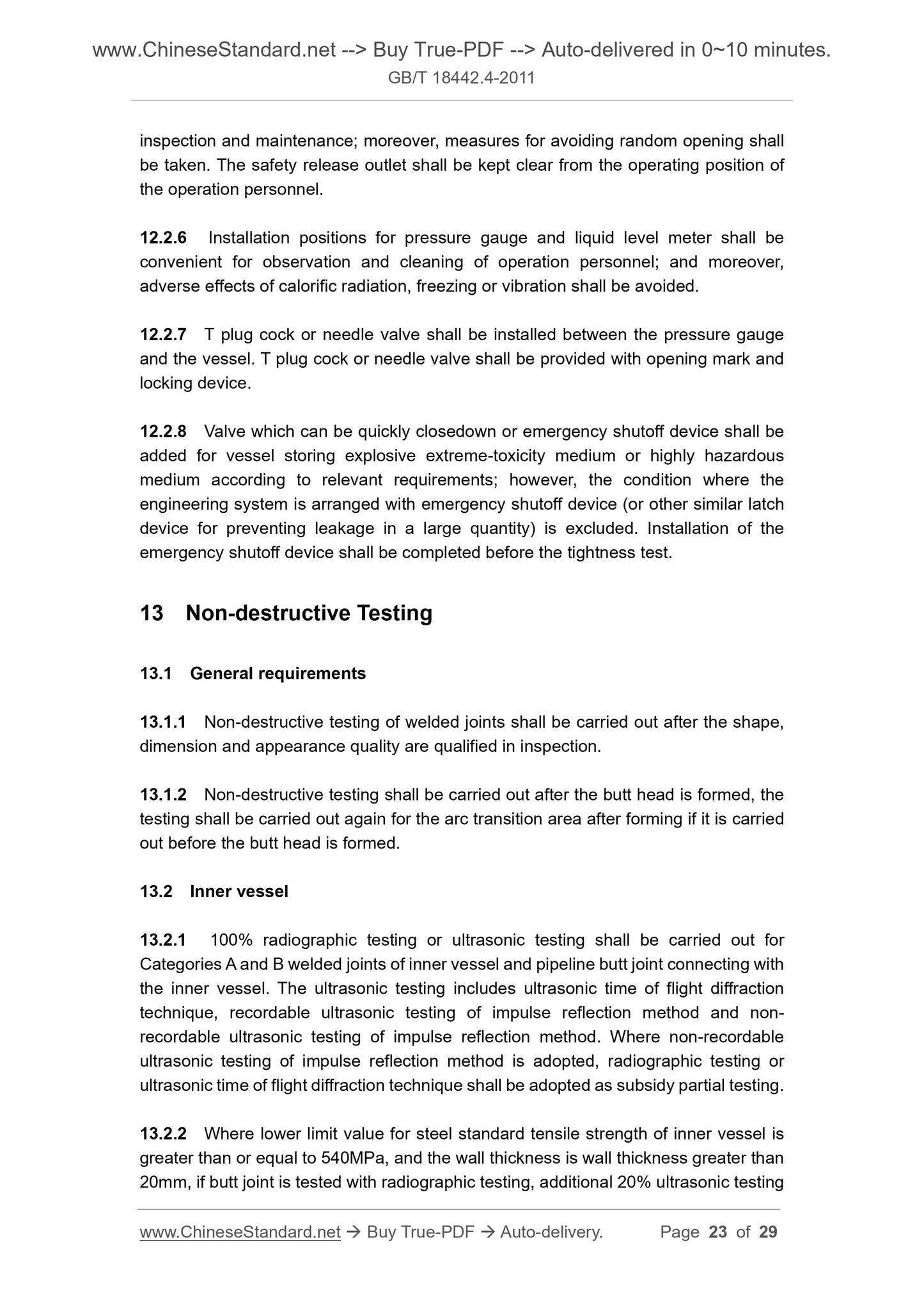
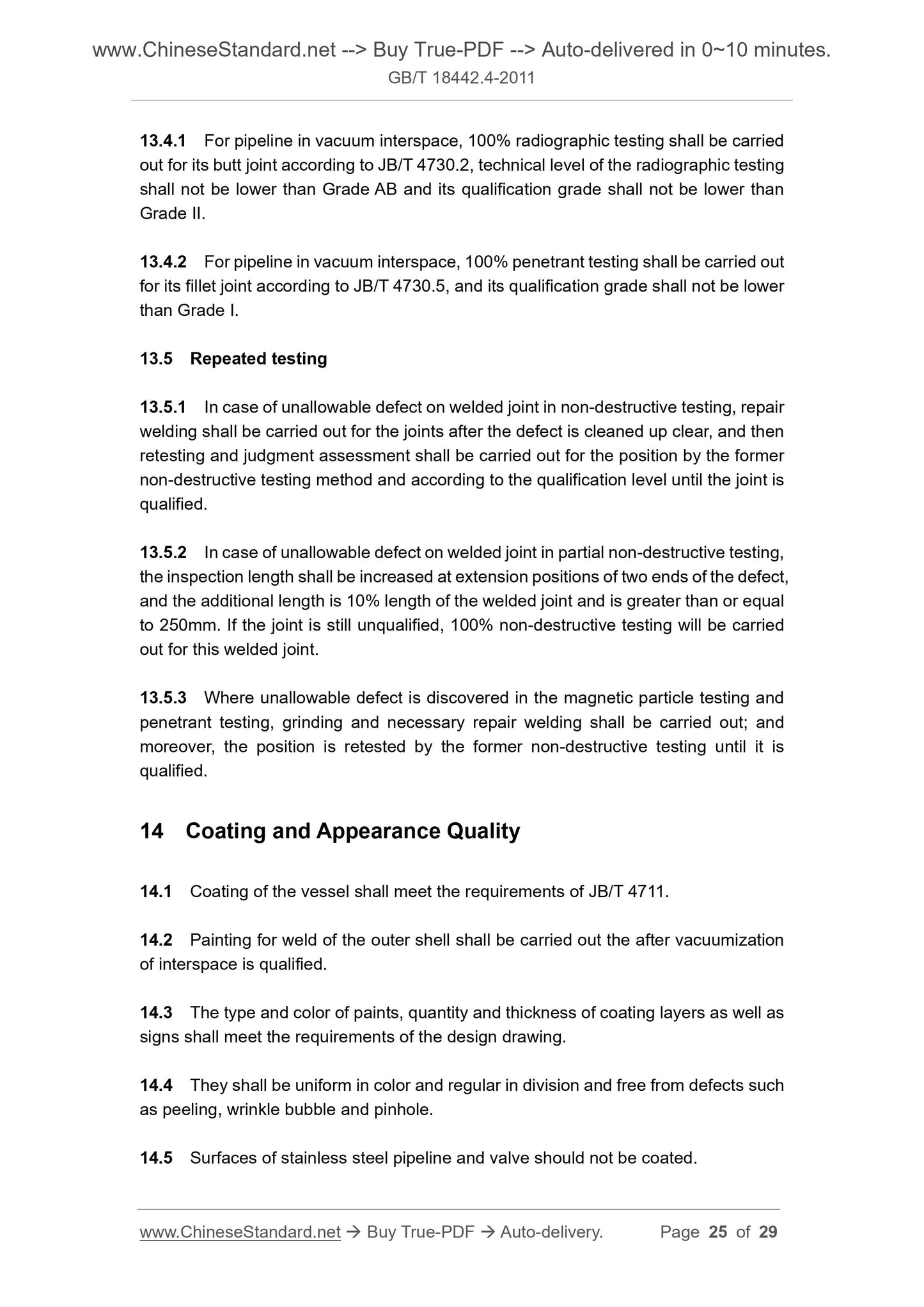