1
/
of
5
www.ChineseStandard.us -- Field Test Asia Pte. Ltd.
GB/T 18271.2-2017 English PDF (GB/T18271.2-2017)
GB/T 18271.2-2017 English PDF (GB/T18271.2-2017)
Regular price
$310.00
Regular price
Sale price
$310.00
Unit price
/
per
Shipping calculated at checkout.
Couldn't load pickup availability
GB/T 18271.2-2017: Process measurement and control devices -- General methods and procedures for evaluating performance -- Part 2: Tests under reference conditions
Delivery: 9 seconds. Download (and Email) true-PDF + Invoice.
Get Quotation: Click GB/T 18271.2-2017 (Self-service in 1-minute)
Newer / historical versions: GB/T 18271.2-2017
Preview True-PDF (Reload/Scroll-down if blank)
Delivery: 9 seconds. Download (and Email) true-PDF + Invoice.
Get Quotation: Click GB/T 18271.2-2017 (Self-service in 1-minute)
Newer / historical versions: GB/T 18271.2-2017
Preview True-PDF (Reload/Scroll-down if blank)
Share
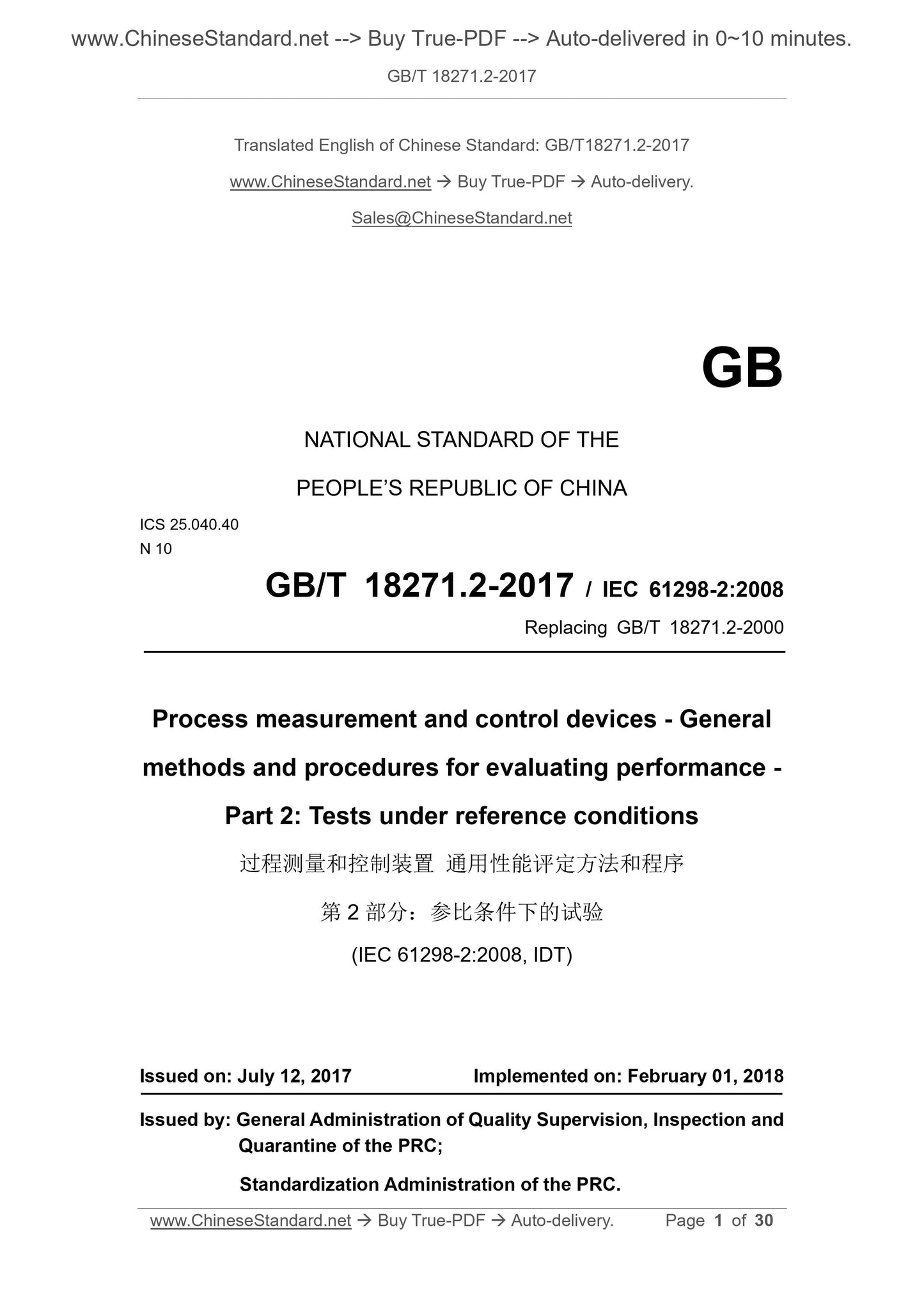
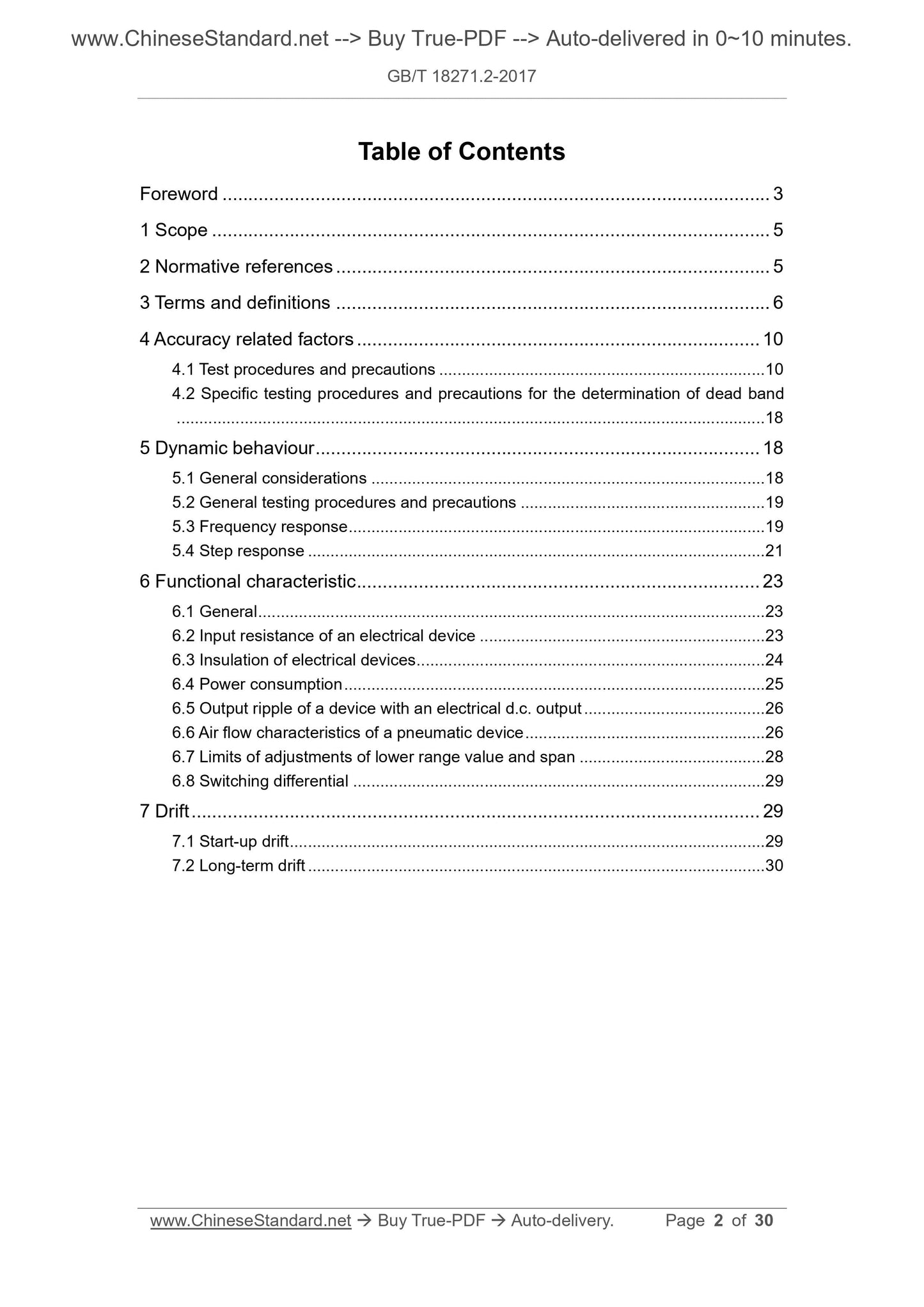
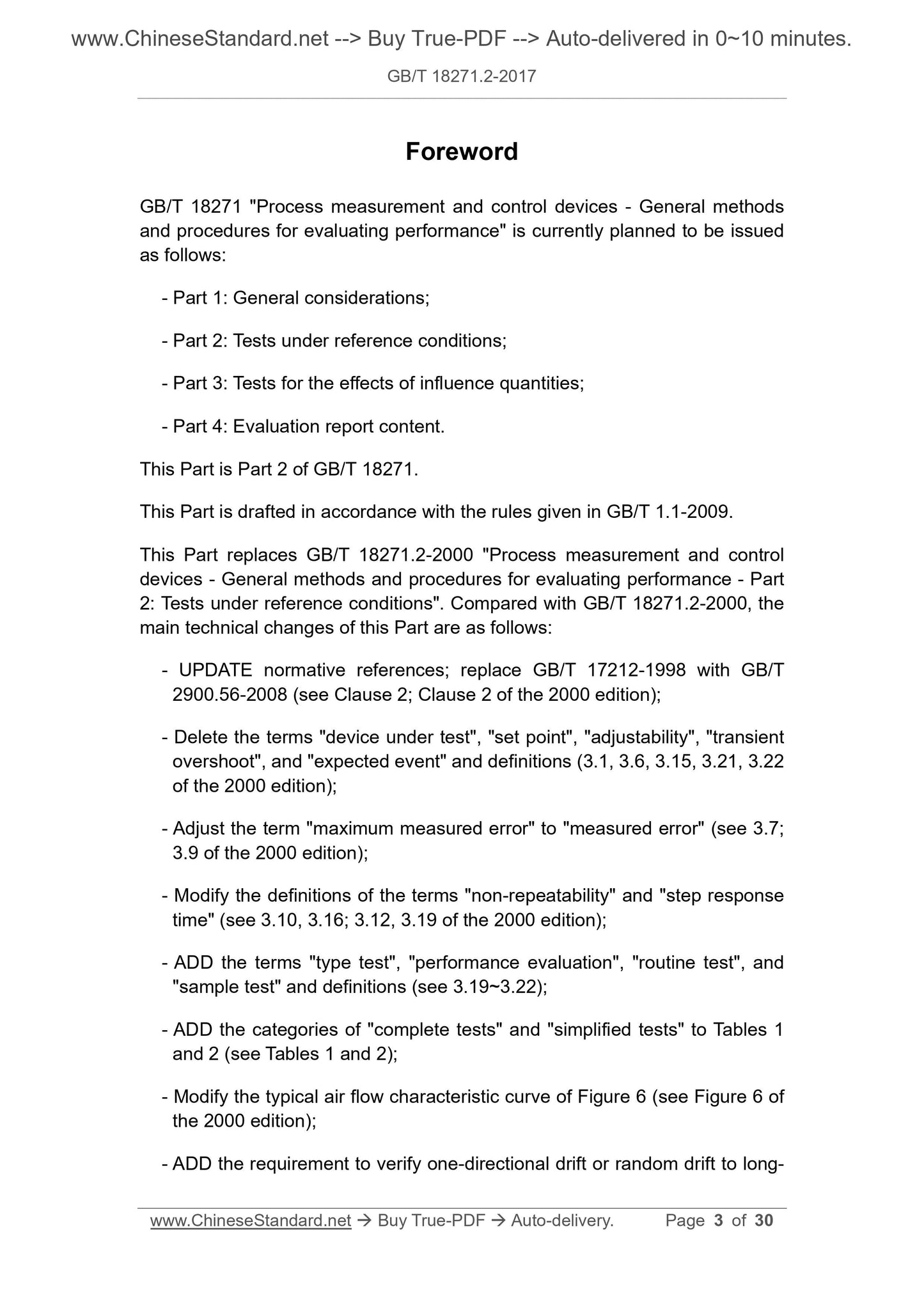
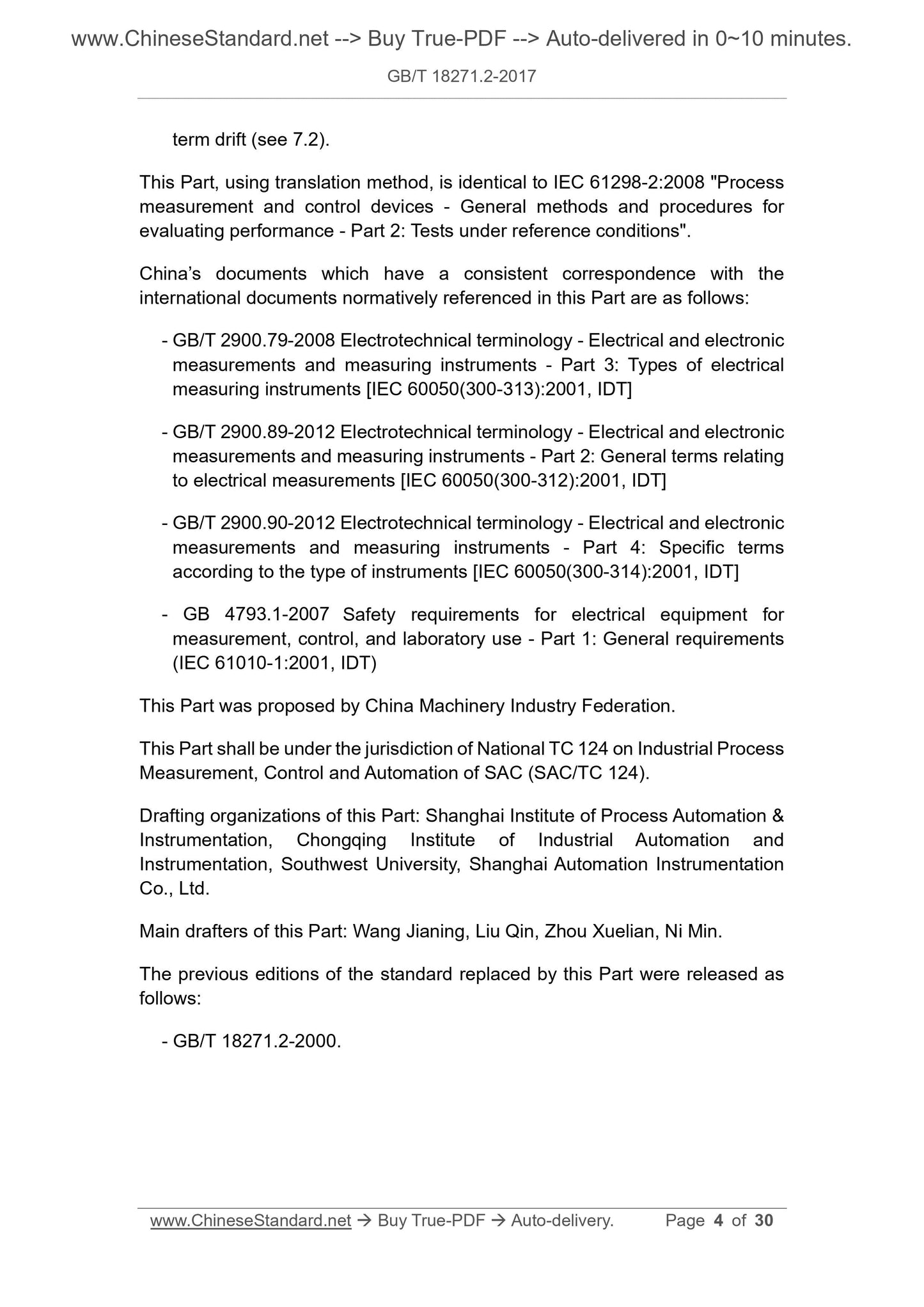
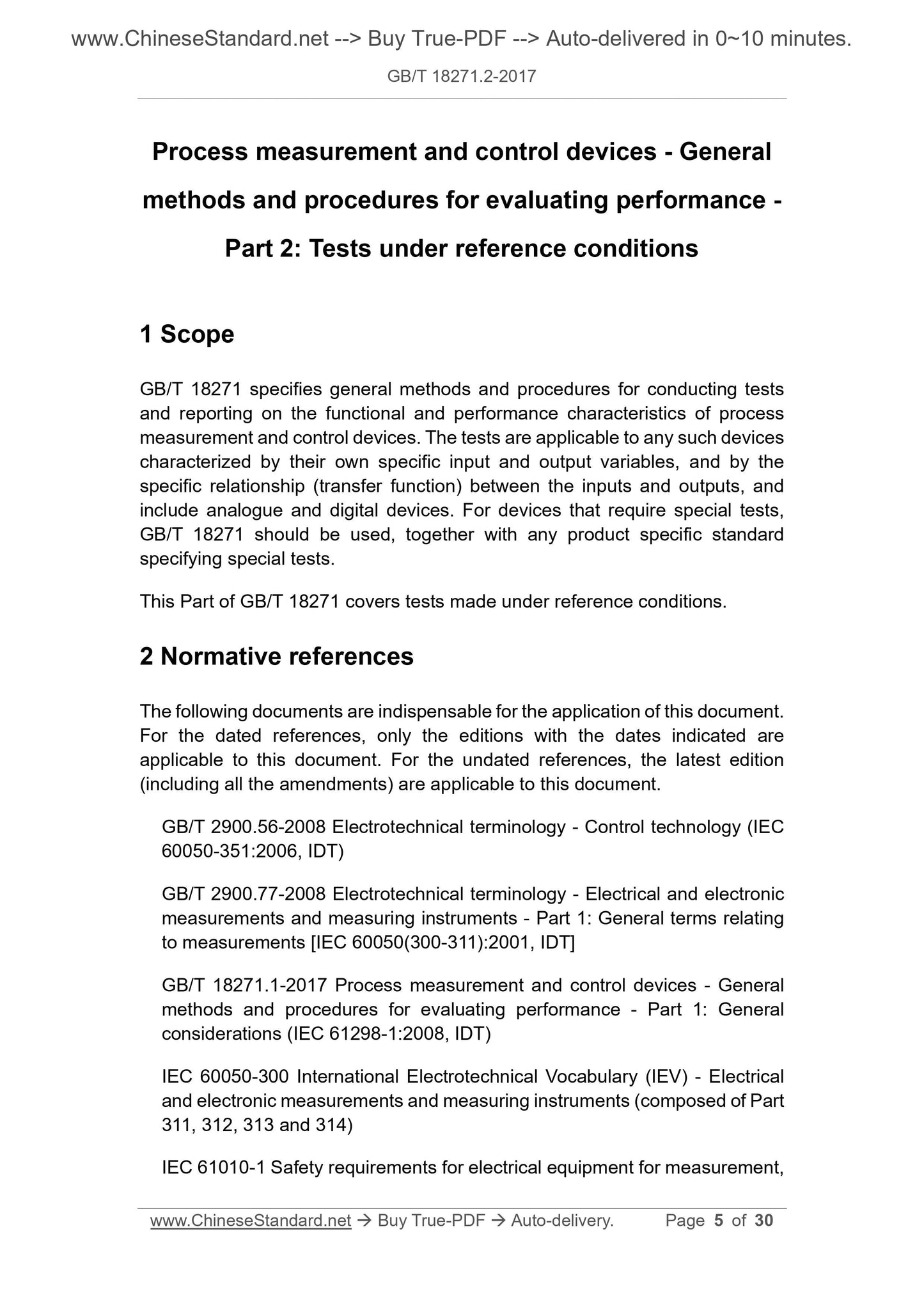