1
/
of
8
www.ChineseStandard.us -- Field Test Asia Pte. Ltd.
GB/T 18177-2008 English PDF (GB/T18177-2008)
GB/T 18177-2008 English PDF (GB/T18177-2008)
Regular price
$250.00
Regular price
Sale price
$250.00
Unit price
/
per
Shipping calculated at checkout.
Couldn't load pickup availability
GB/T 18177-2008: Gas nitriding of steel parts
Delivery: 9 seconds. Download (and Email) true-PDF + Invoice.Get Quotation: Click GB/T 18177-2008 (Self-service in 1-minute)
Newer / historical versions: GB/T 18177-2008
Preview True-PDF
Scope
This standard specifies the gas nitriding process, equipment, inspection, energyconsumption and safety and health requirements for heating steel parts, in an
ammonia-containing atmosphere.
This standard applies to gas nitriding of carbon steel, alloy structural steel, alloy
tool steel, stainless steel, heat-resistant steel.
Basic Data
Standard ID | GB/T 18177-2008 (GB/T18177-2008) |
Description (Translated English) | Gas nitriding of steel parts |
Sector / Industry | National Standard (Recommended) |
Classification of Chinese Standard | J36 |
Classification of International Standard | 25.200 |
Word Count Estimation | 18,118 |
Date of Issue | 2008-06-25 |
Date of Implementation | 2009-01-01 |
Older Standard (superseded by this standard) | GB/T 18177-2000 |
Regulation (derived from) | National Standard Approval Announcement 2008 No.11 (Total No.124) |
Issuing agency(ies) | General Administration of Quality Supervision, Inspection and Quarantine of the People's Republic of China, Standardization Administration of the People's Republic of China |
Summary | This standard specifies the steel is heated in an atmosphere of ammonia gas nitriding process, equipment, inspection, energy consumption and health and safety requirements. This standard applies to carbon steel, alloy steel, alloy tool steel, stainless steel and heat-resistant steel gas nitriding. |
Share
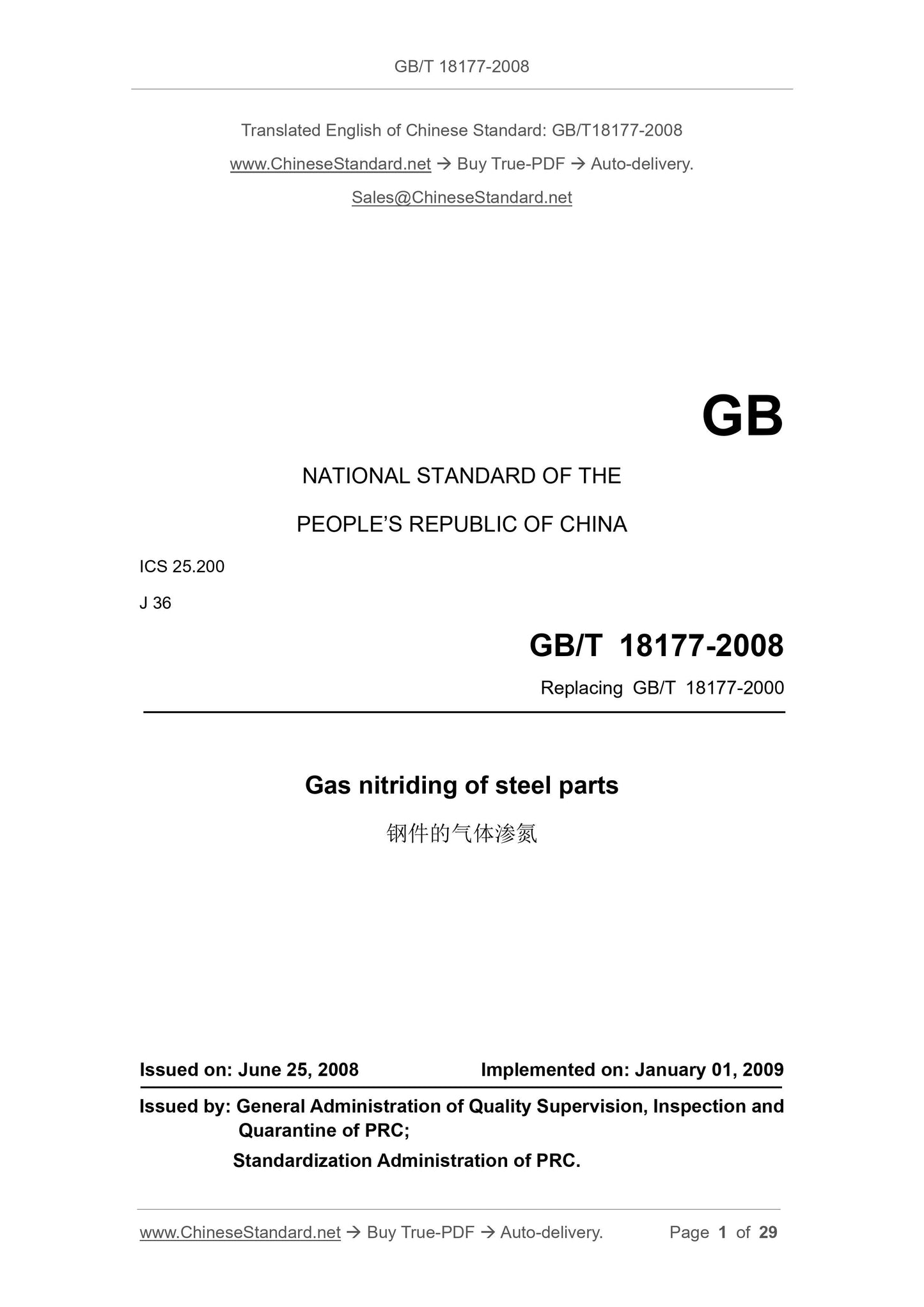
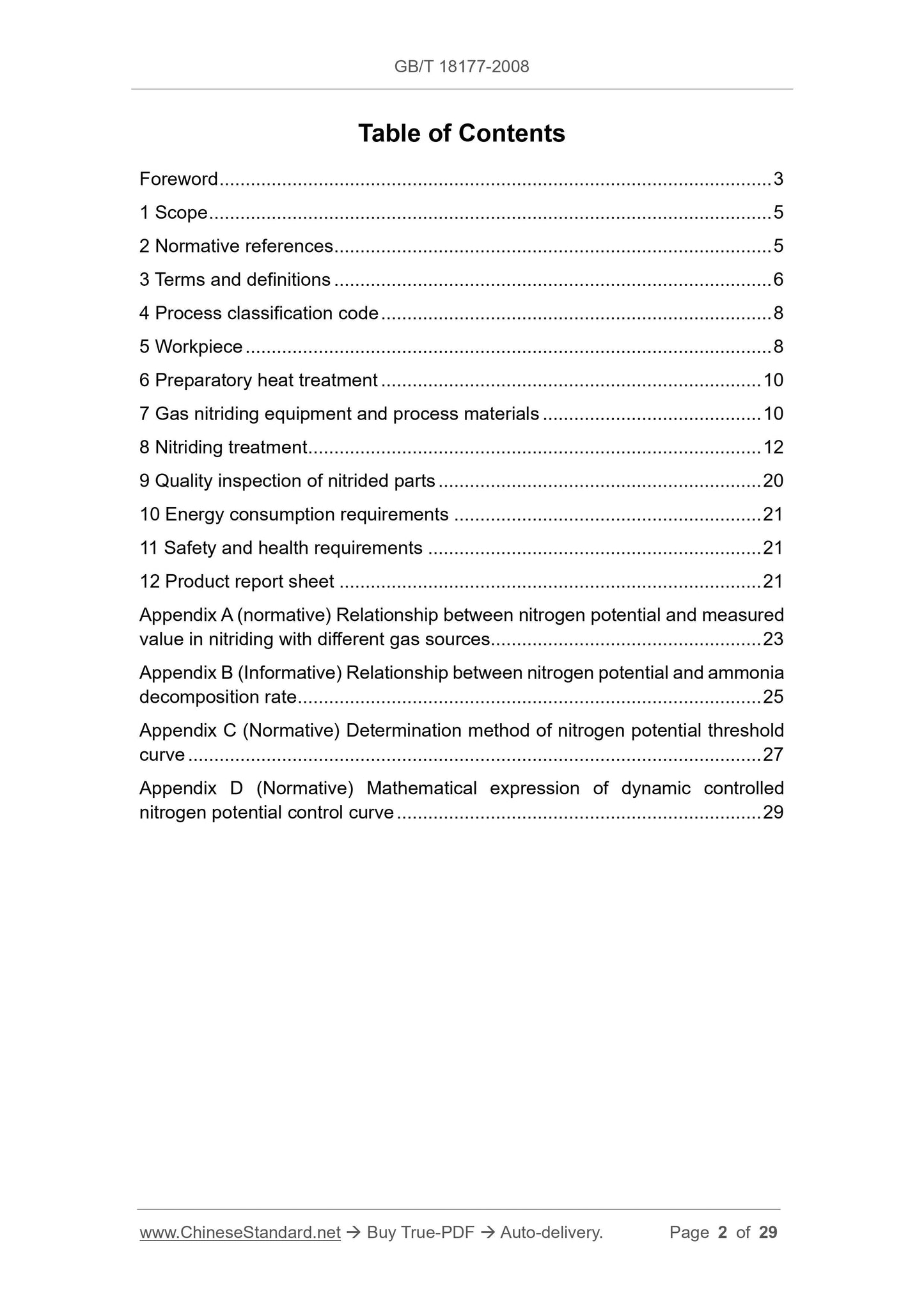
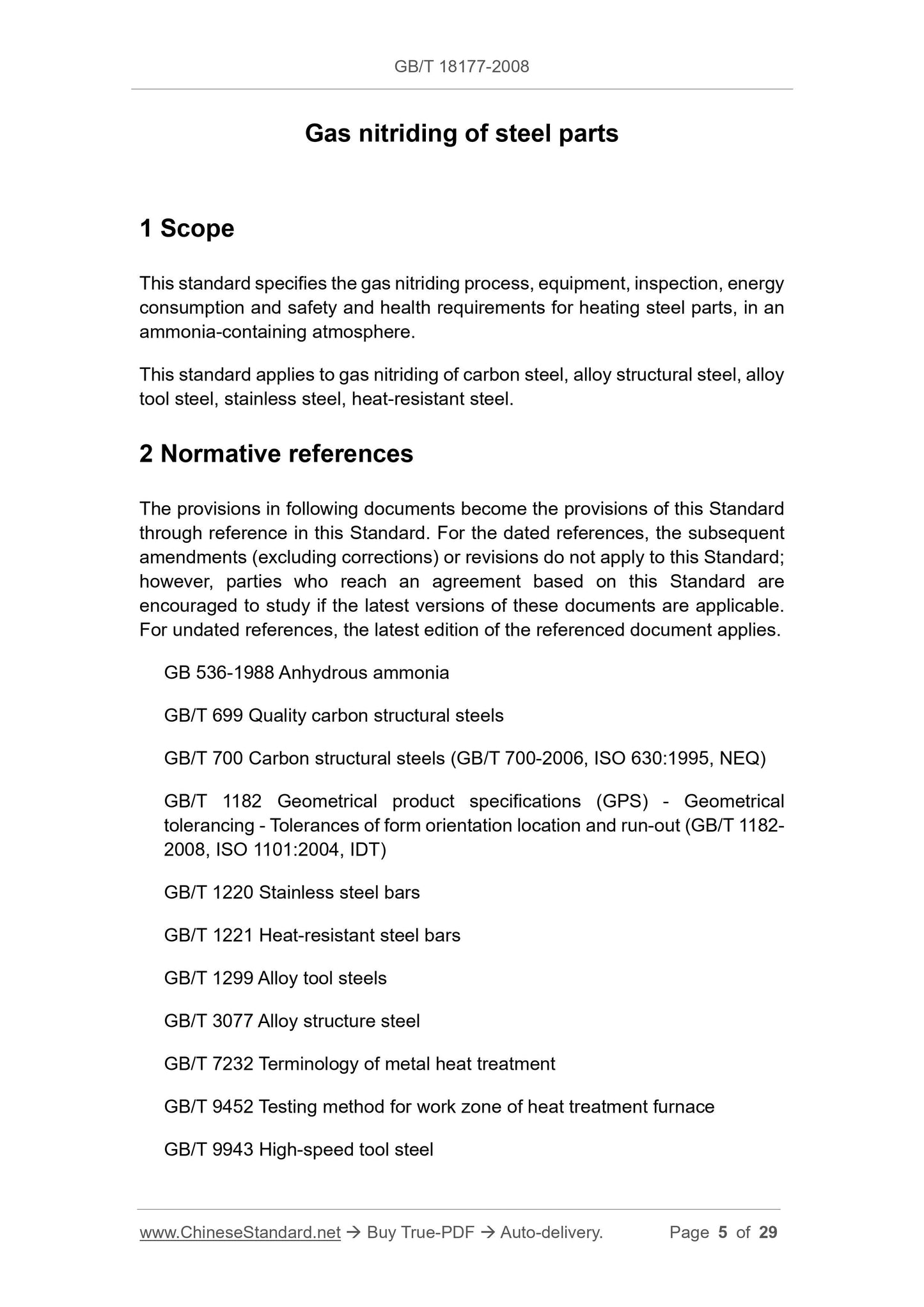
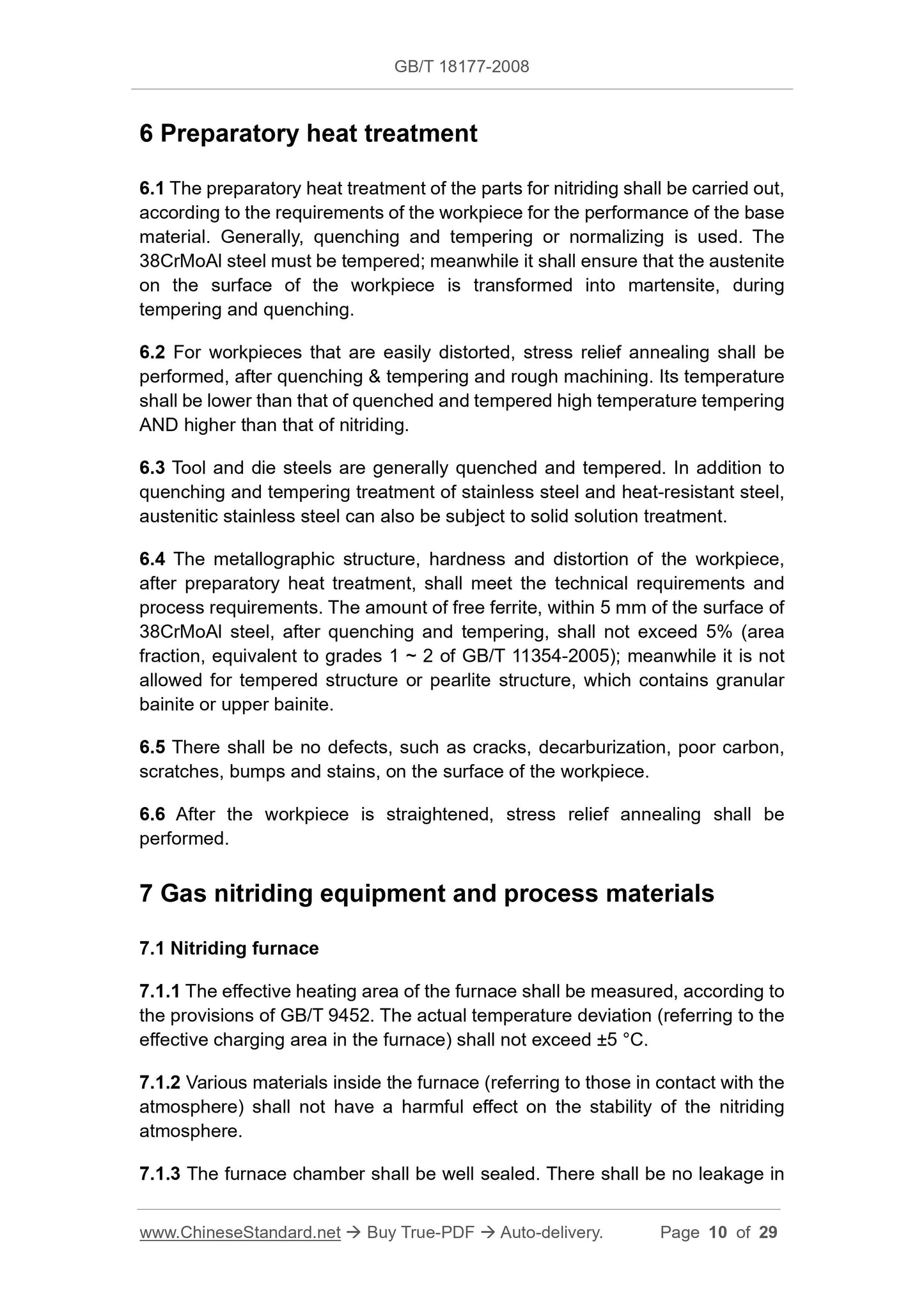

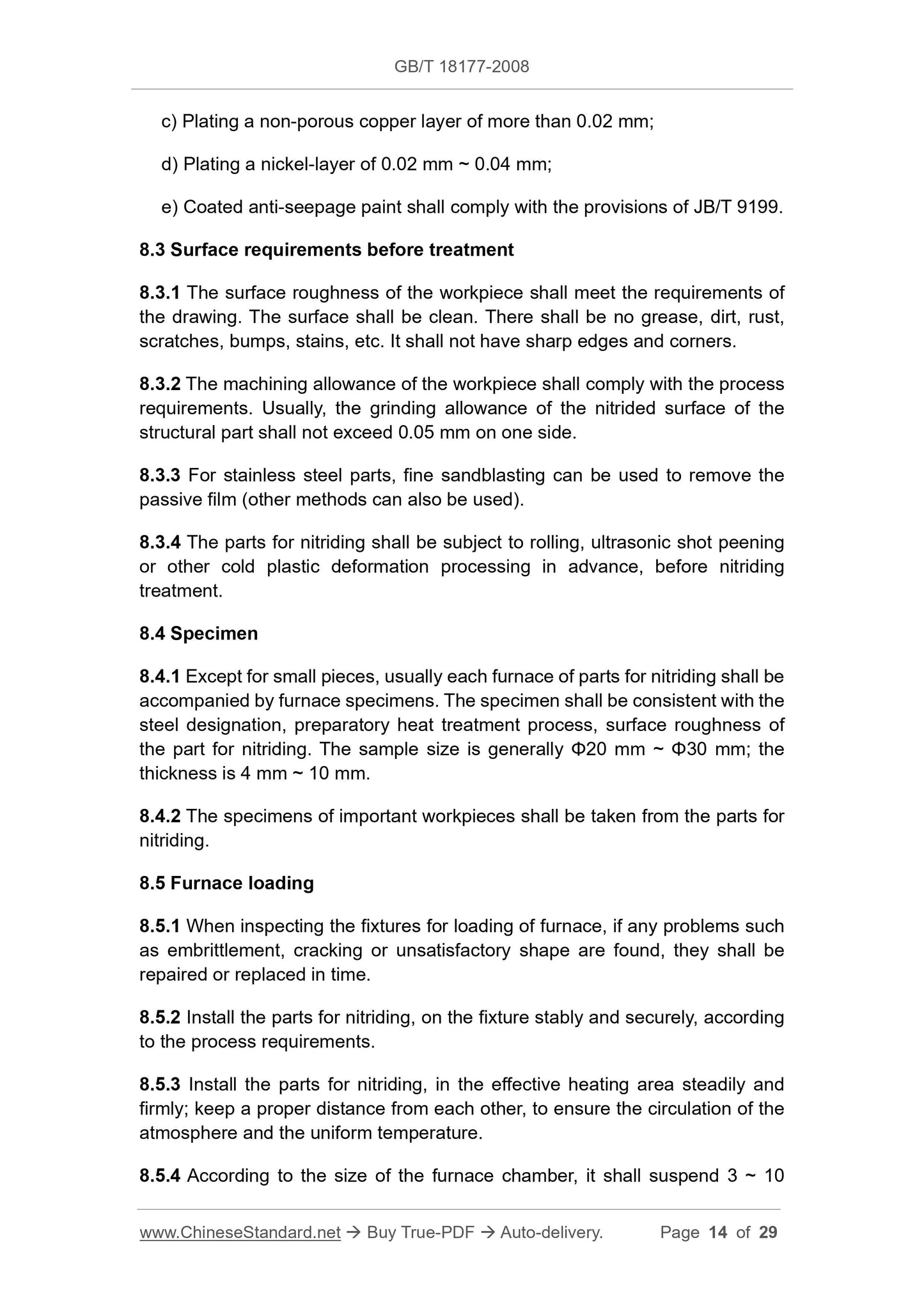
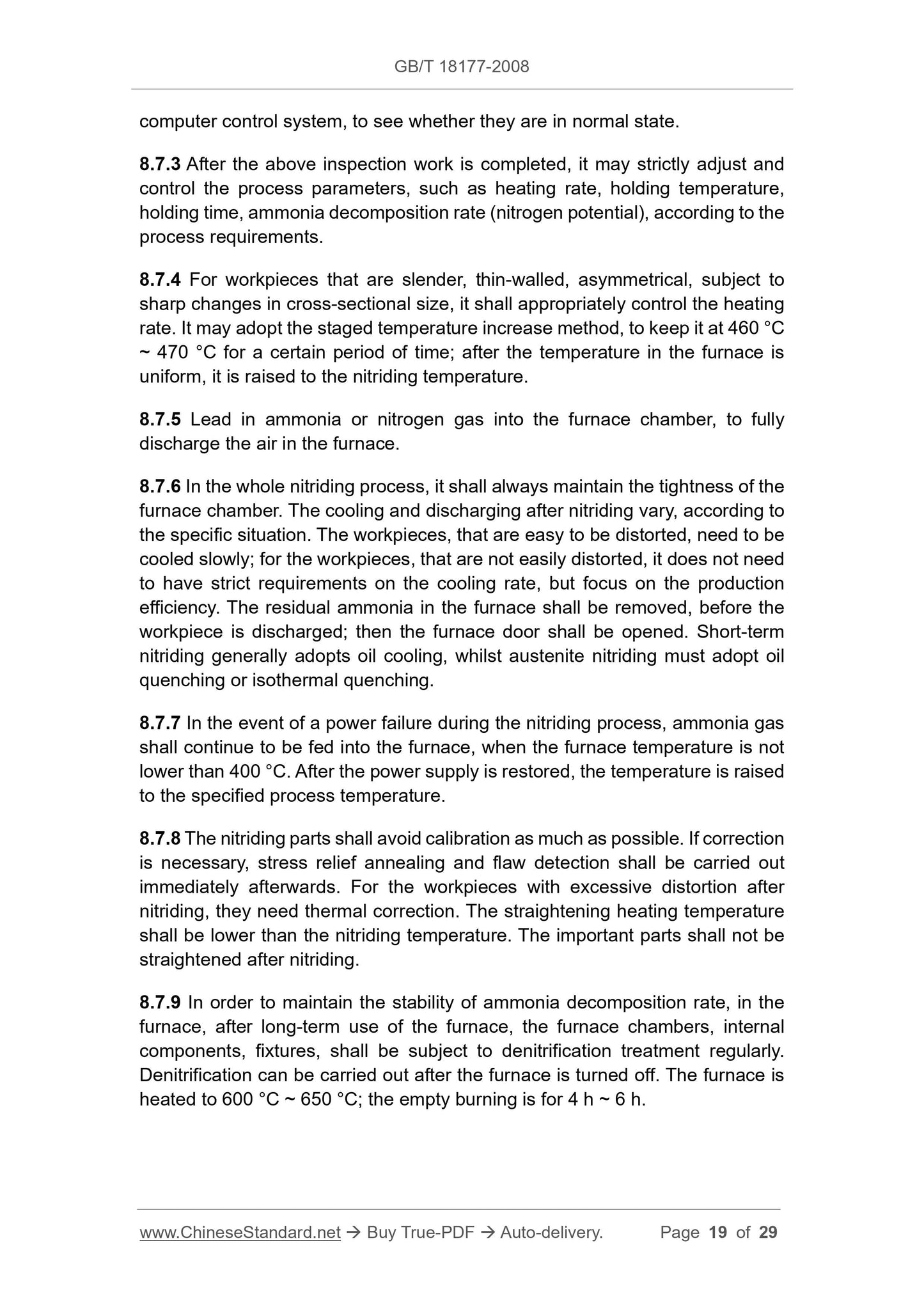
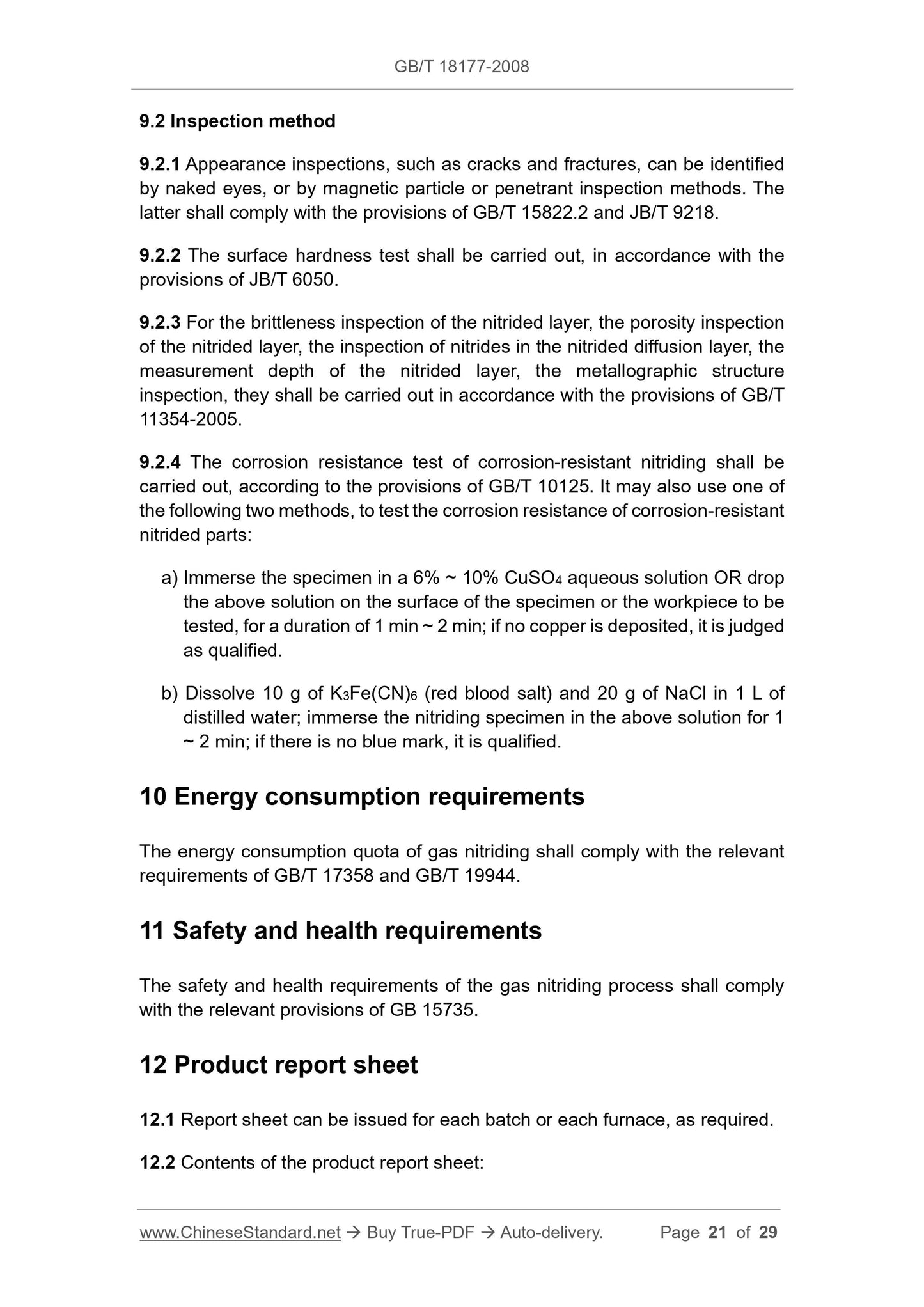