1
/
of
12
www.ChineseStandard.us -- Field Test Asia Pte. Ltd.
GB/T 17808-2010 English PDF (GB/T17808-2010)
GB/T 17808-2010 English PDF (GB/T17808-2010)
Regular price
$560.00
Regular price
Sale price
$560.00
Unit price
/
per
Shipping calculated at checkout.
Couldn't load pickup availability
GB/T 17808-2010: Road construction and road maintenance machinery and equipment -- Asphalt mixing plant
Delivery: 9 seconds. Download (and Email) true-PDF + Invoice.Get Quotation: Click GB/T 17808-2010 (Self-service in 1-minute)
Newer / historical versions: GB/T 17808-2010
Preview True-PDF
Scope
This standard specifies the classification, technical requirements, test methods,inspection rules, marking, packaging, transportation, storage, quality assurance
requirements and complete supply of road construction and maintenance
machinery and equipment - Asphalt mixing plant (hereinafter referred to as
asphalt mixing plant) .
This standard applies to asphalt mixing plant.
Basic Data
Standard ID | GB/T 17808-2010 (GB/T17808-2010) |
Description (Translated English) | Road construction and road maintenance machinery and equipment -- Asphalt mixing plant |
Sector / Industry | National Standard (Recommended) |
Classification of Chinese Standard | P97 |
Classification of International Standard | 91.220 |
Word Count Estimation | 44,417 |
Date of Issue | 2010-12-01 |
Date of Implementation | 2011-03-01 |
Older Standard (superseded by this standard) | GB/T 17808-1999 |
Quoted Standard | GB 150; GB/T 1955; GB/T 3766; GB 5226.1; GB 7258; GB/T 7920.11; GB/T 7932; GB/T 10595; GB/T 14249.2; GB 16297; GB/T 17410; GB 50057; JB/T 3926.2; JB/T 5000.3; JB/T 5000.4; JB/T 5000.6; JB/T 5000.11; JG/T 5011.11; JG/T 5011.12; JG/T 5012; JG/T 5079.2; JTG F40; JTJ 052 |
Regulation (derived from) | National Standard Approval Announcement 2010 No.9 (Total No.164) |
Issuing agency(ies) | General Administration of Quality Supervision, Inspection and Quarantine of the People's Republic of China, Standardization Administration of the People's Republic of China |
Summary | This standard specifies the road construction and maintenance machinery and equipment asphalt mixing equipment (hereinafter referred to as asphalt mixing equipment) classification, technical requirements, test methods, inspection rules, signs, packaging, transport, storage, complete set of quality assurance requirements and supply. This standard applies to asphalt mixing equipment. |
Share
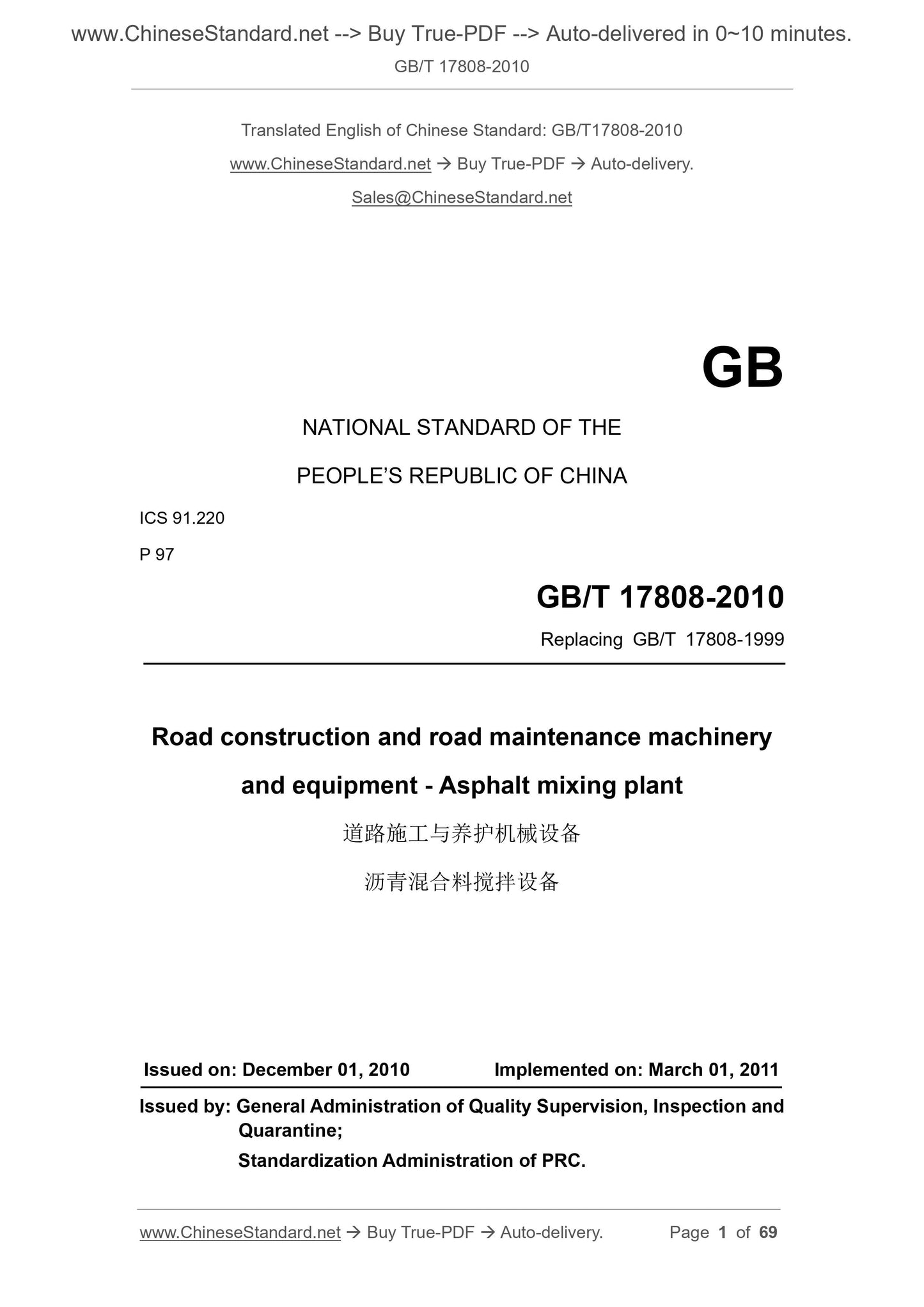
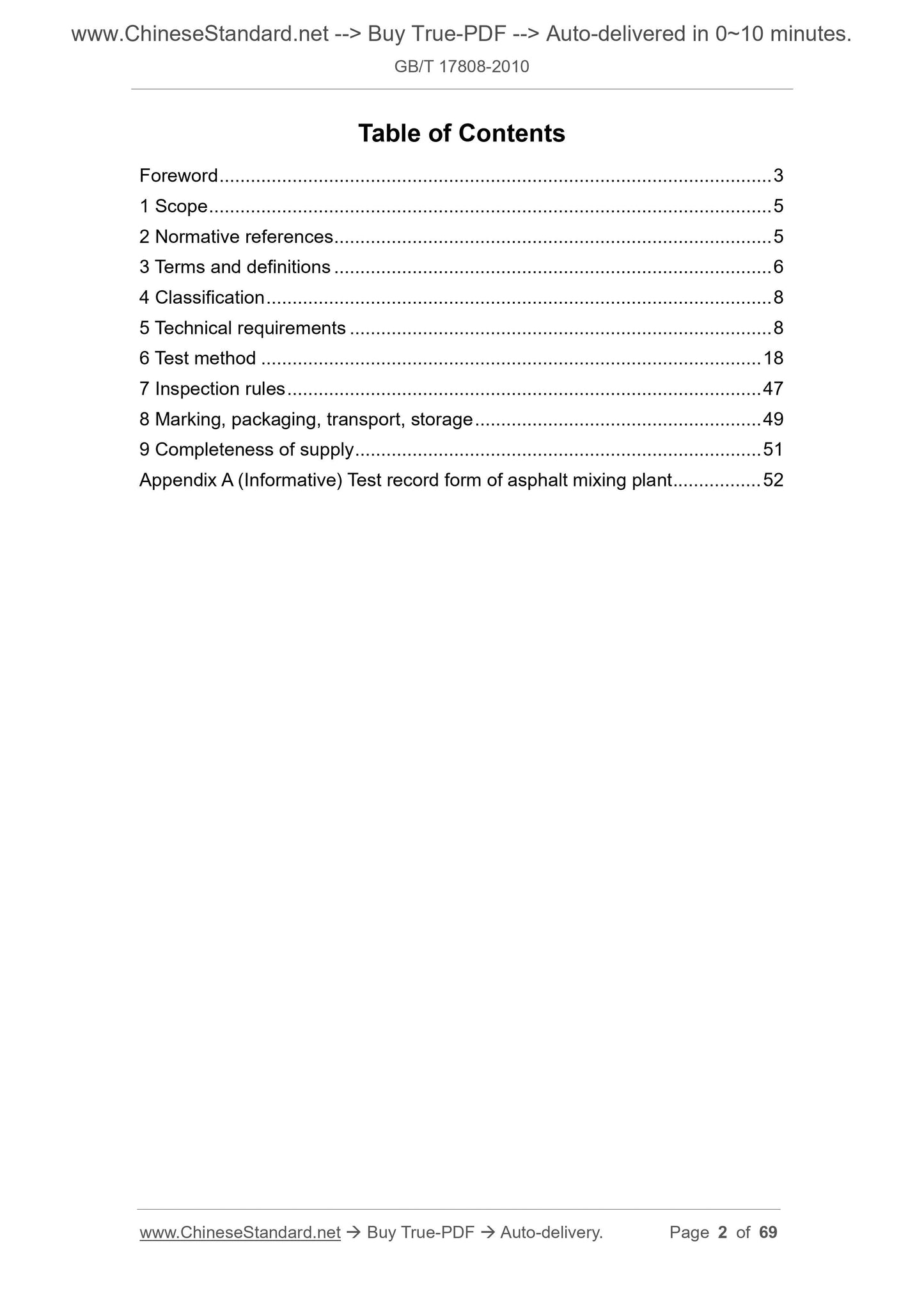
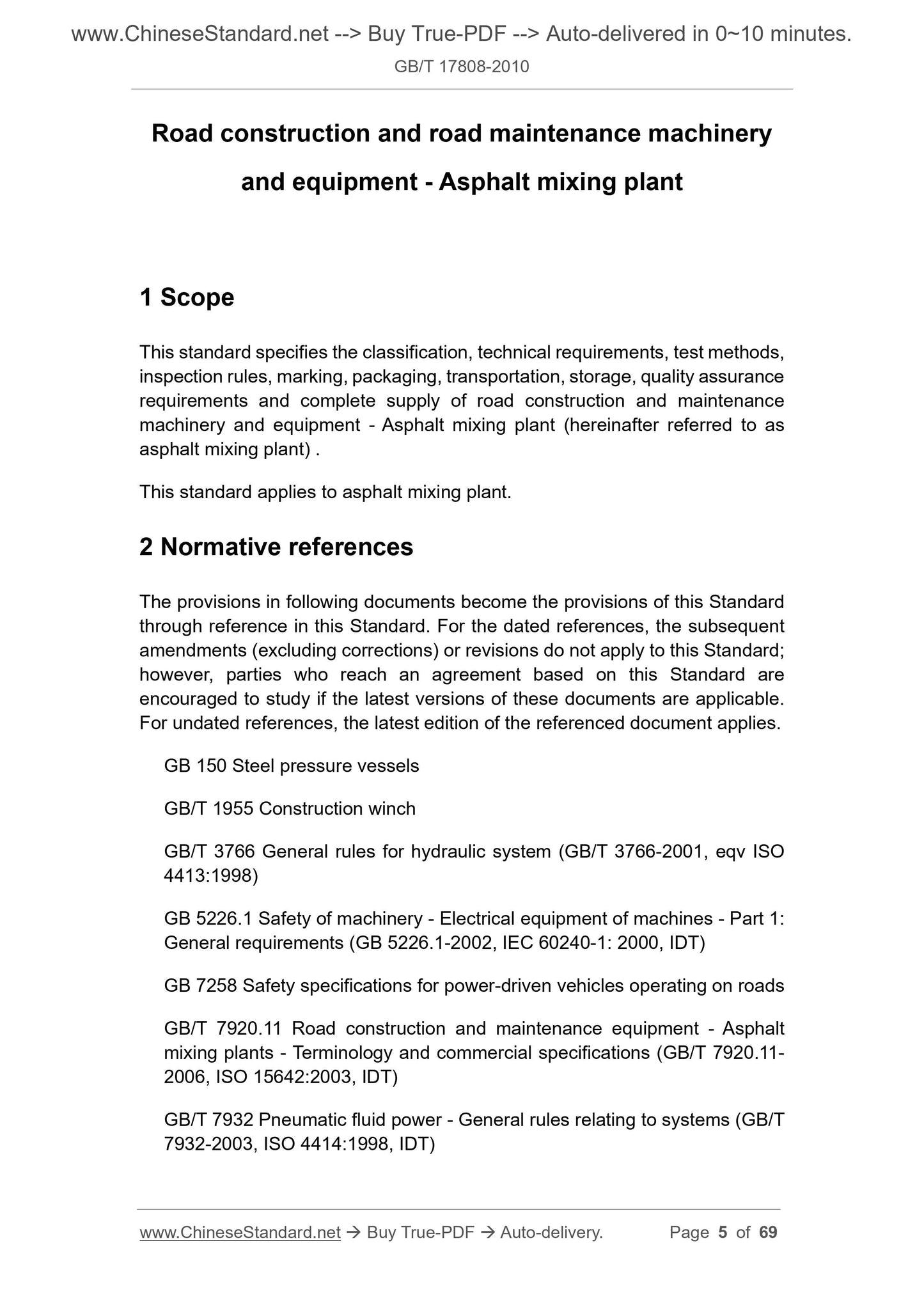
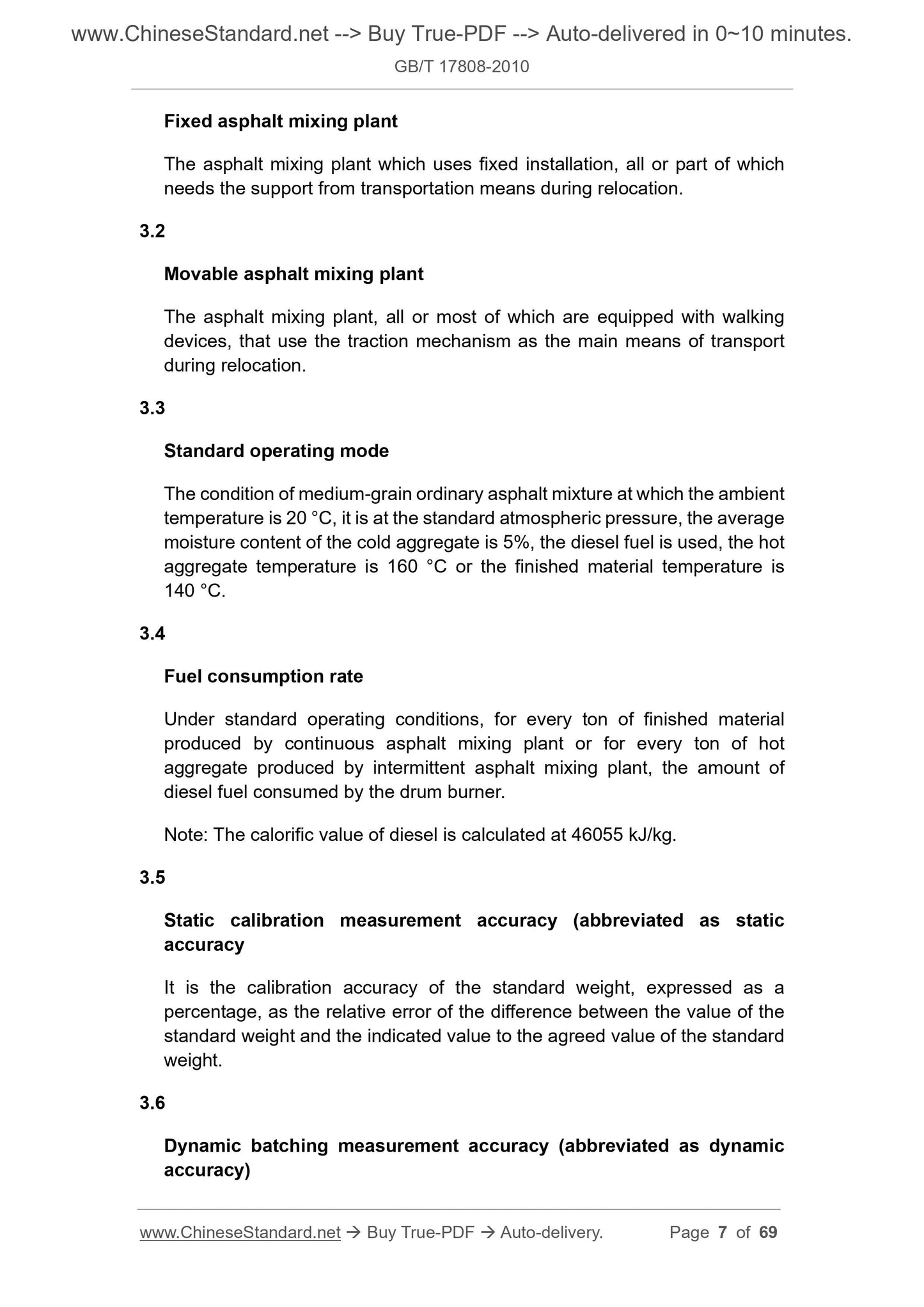
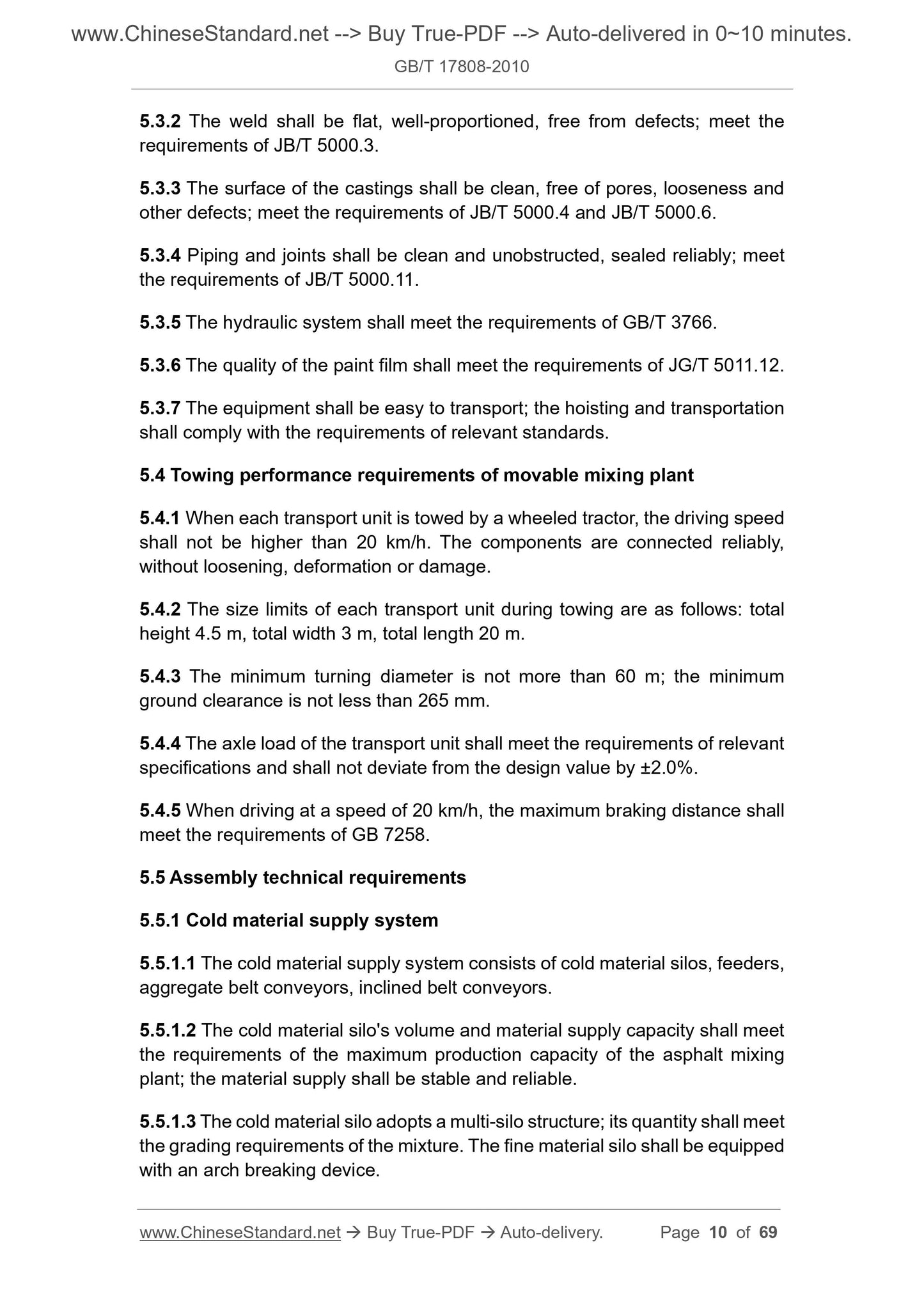
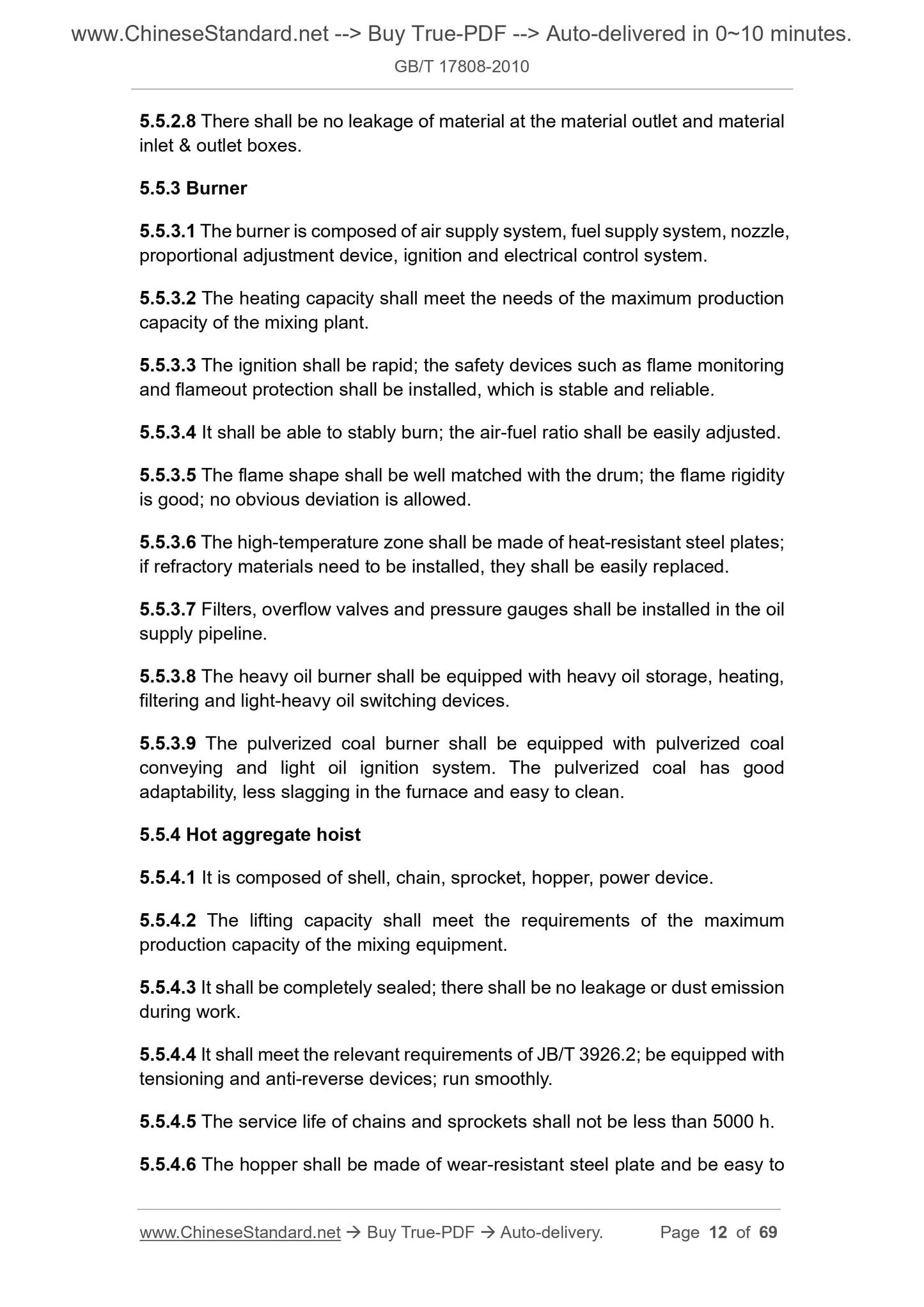
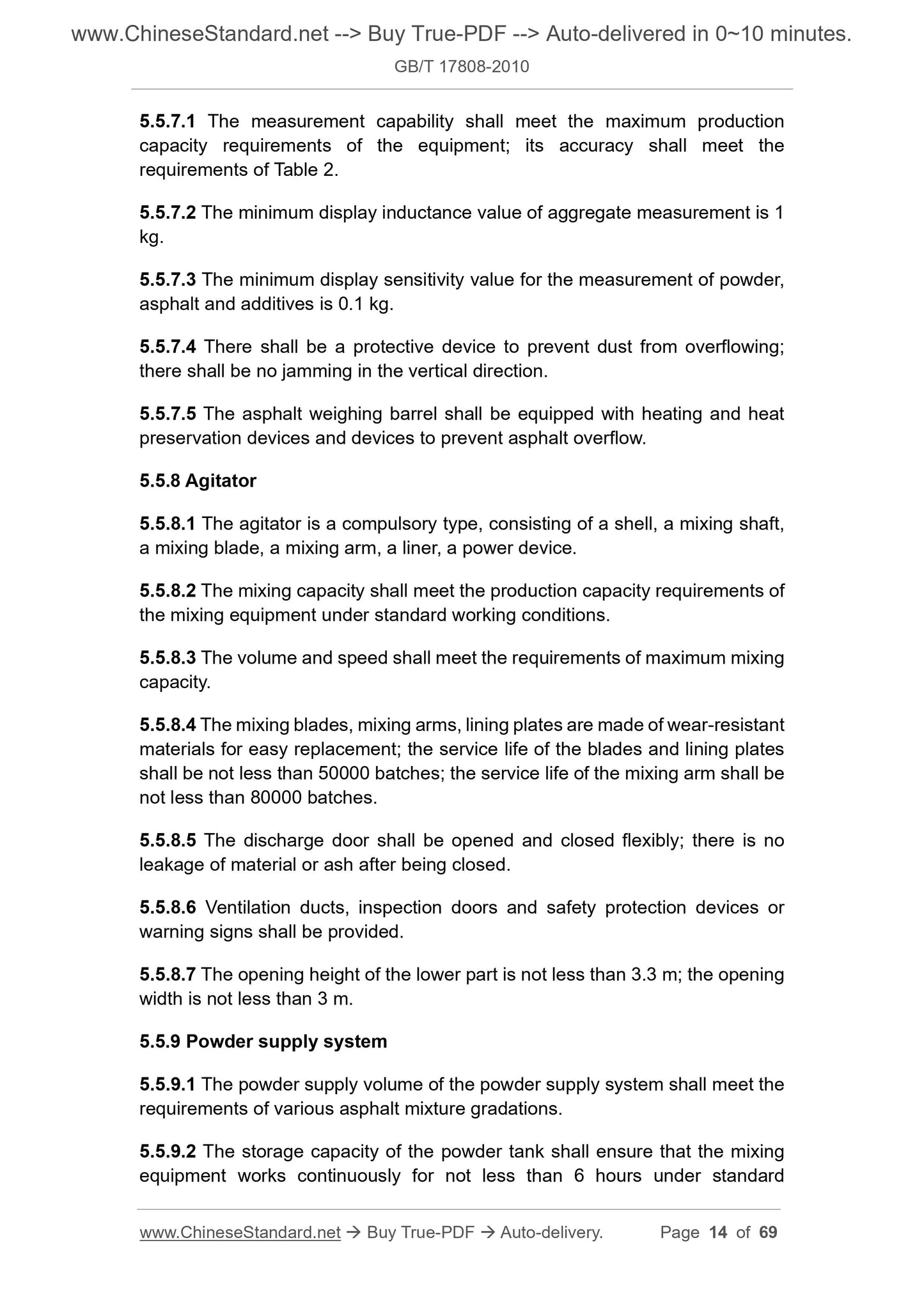
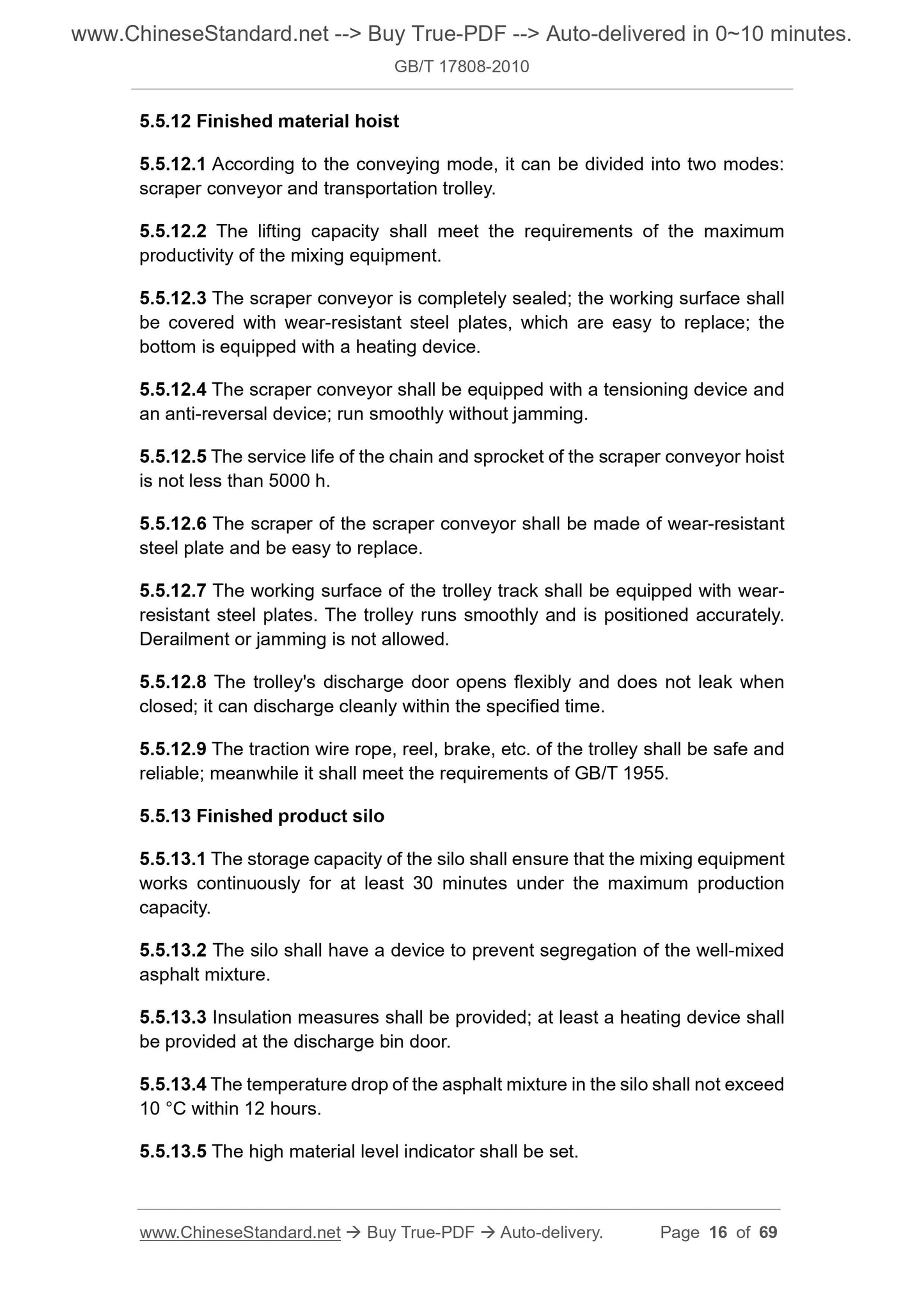
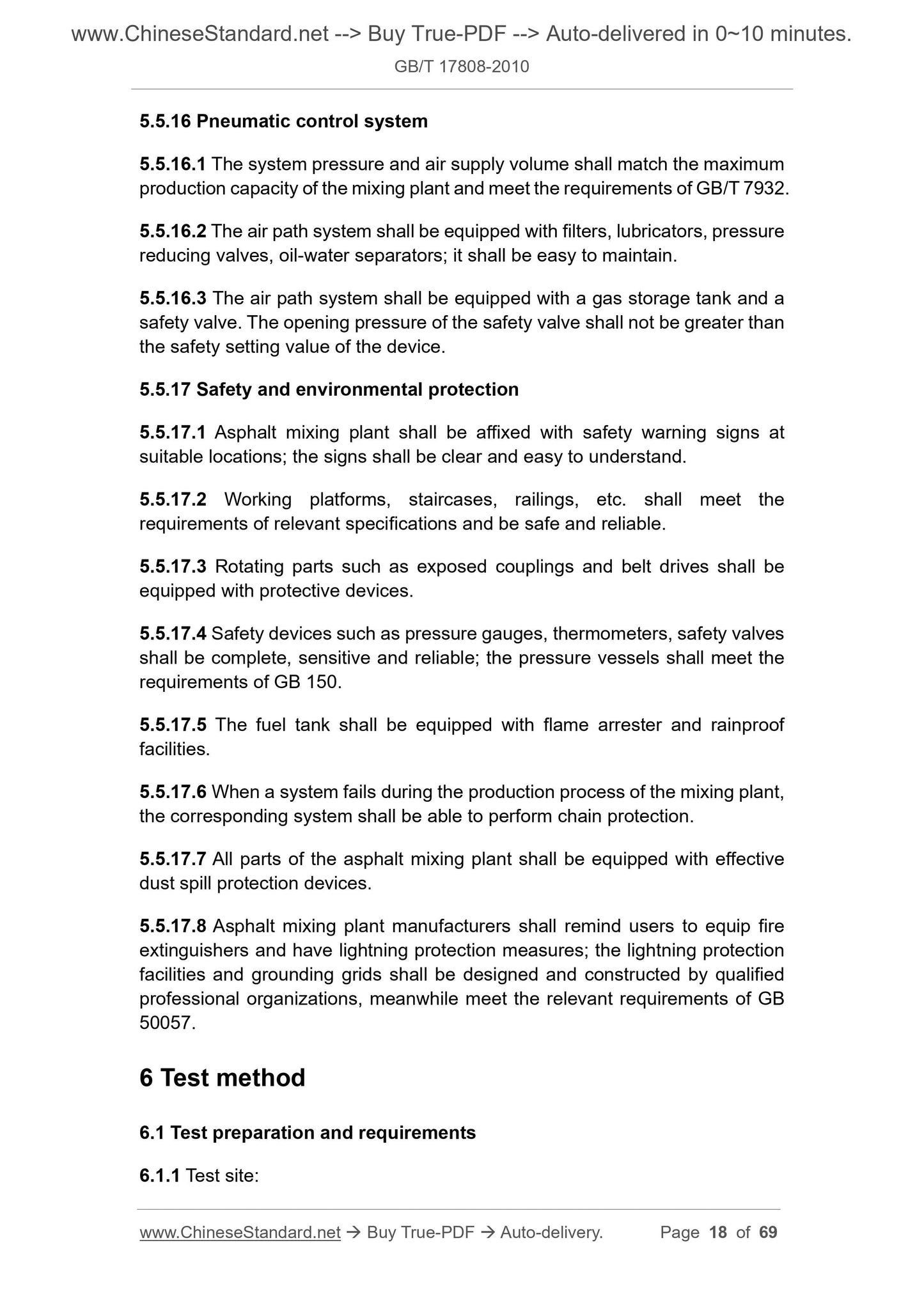
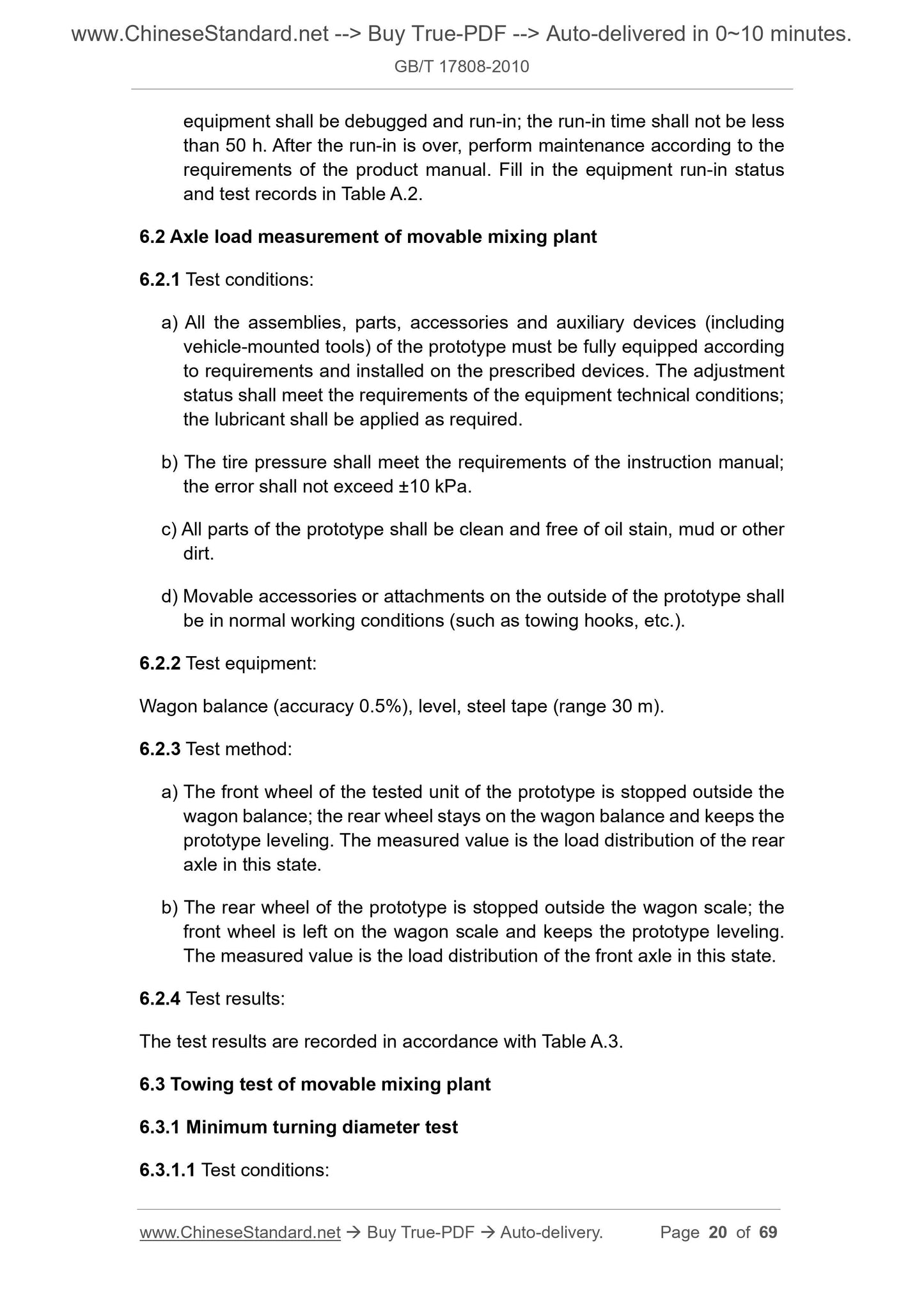
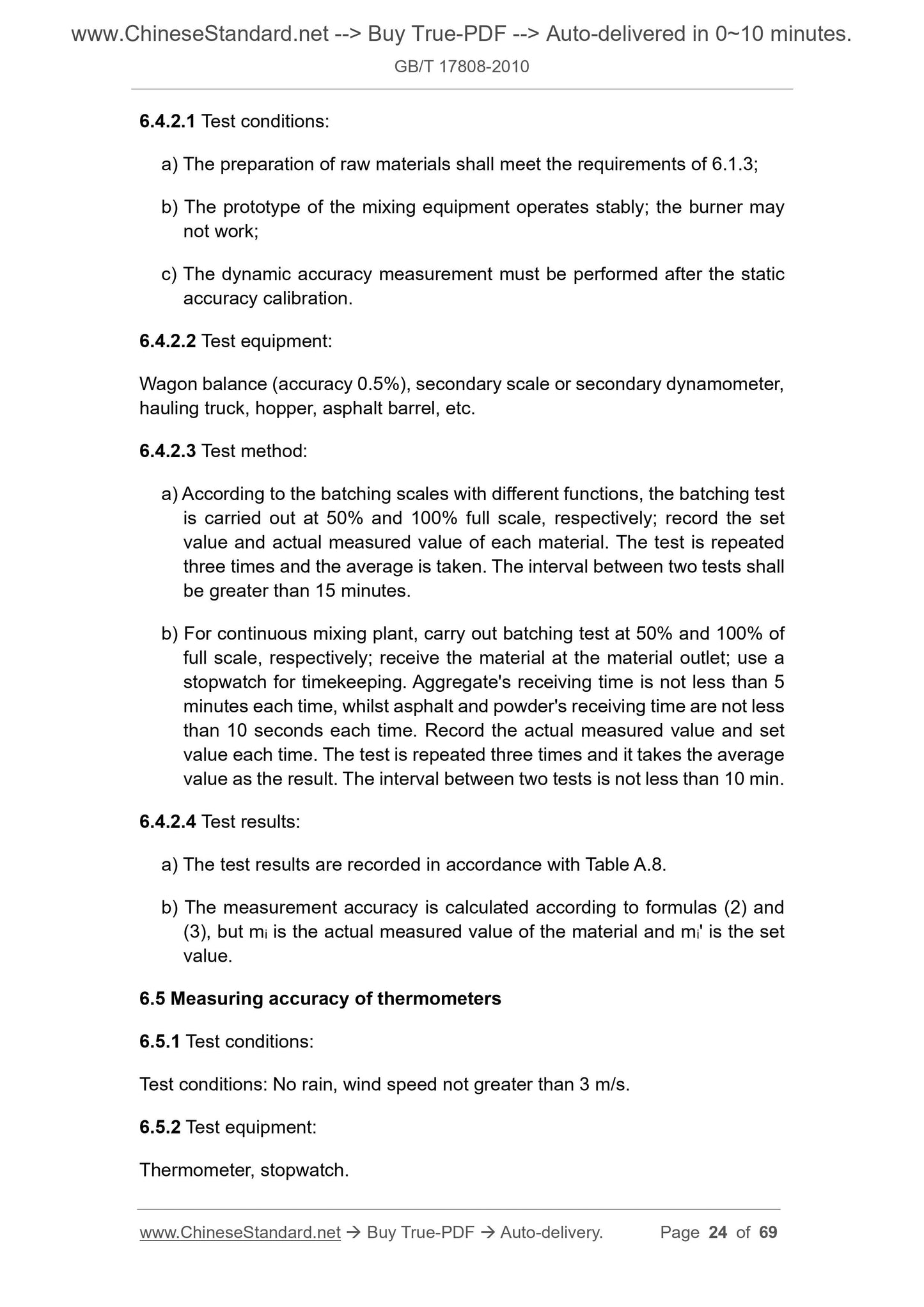
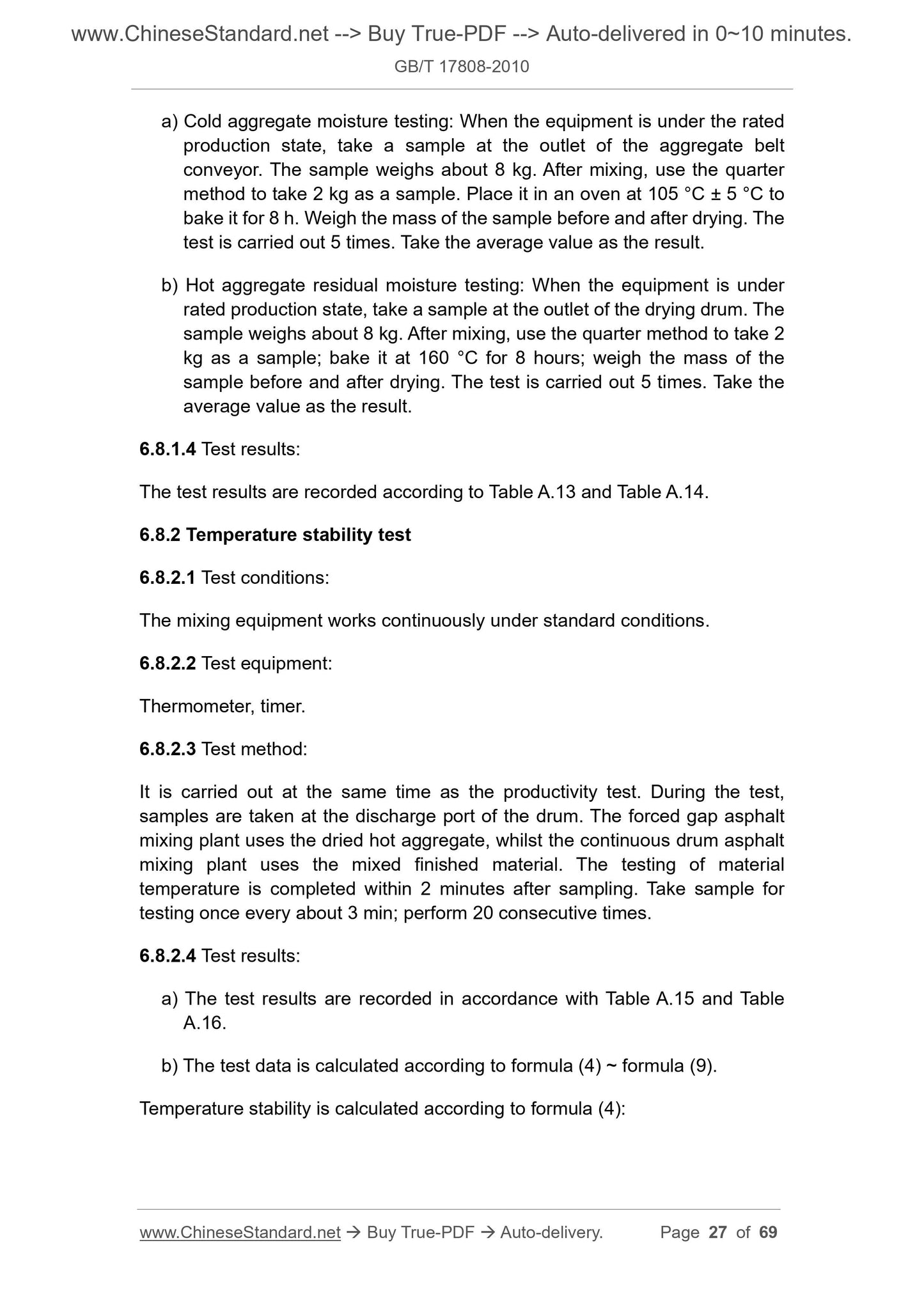