1
/
of
9
www.ChineseStandard.us -- Field Test Asia Pte. Ltd.
GB/T 16422.3-2022 English PDF (GB/T16422.3-2022)
GB/T 16422.3-2022 English PDF (GB/T16422.3-2022)
Regular price
$290.00
Regular price
Sale price
$290.00
Unit price
/
per
Shipping calculated at checkout.
Couldn't load pickup availability
GB/T 16422.3-2022: Plastics - Methods of exposure to laboratory light sources - Part 3: Fluorescent UV lamps
Delivery: 9 seconds. Download (and Email) true-PDF + Invoice.Get Quotation: Click GB/T 16422.3-2022 (Self-service in 1-minute)
Newer / historical versions: GB/T 16422.3-2022
Preview True-PDF
Scope
This Document specifies methods for exposing specimens to fluorescent UV radiation, heat andwater in apparatus designed to simulate the weathering effects that occur when materials are
exposed in actual end-use environments to global solar radiation, or to solar radiation through
window glass.
This Document is applicable to the specimens that are exposed to fluorescent UV lamps under
controlled environmental conditions (temperature, humidity and/or water). Different types of
fluorescent UV lamp can be used to meet all the requirements for testing different materials.
Specimen preparation and evaluation of the results are covered in other Standards for specific
materials.
General guidance is given in ISO 4892-1.
NOTE: Fluorescent UV lamp exposures for paints, varnishes and other coatings are described in GB/T
23987-2009.
Basic Data
Standard ID | GB/T 16422.3-2022 (GB/T16422.3-2022) |
Description (Translated English) | Plastics - Methods of exposure to laboratory light sources - Part 3: Fluorescent UV lamps |
Sector / Industry | National Standard (Recommended) |
Classification of Chinese Standard | G31 |
Word Count Estimation | 19,168 |
Issuing agency(ies) | State Administration for Market Regulation, China National Standardization Administration |
Share
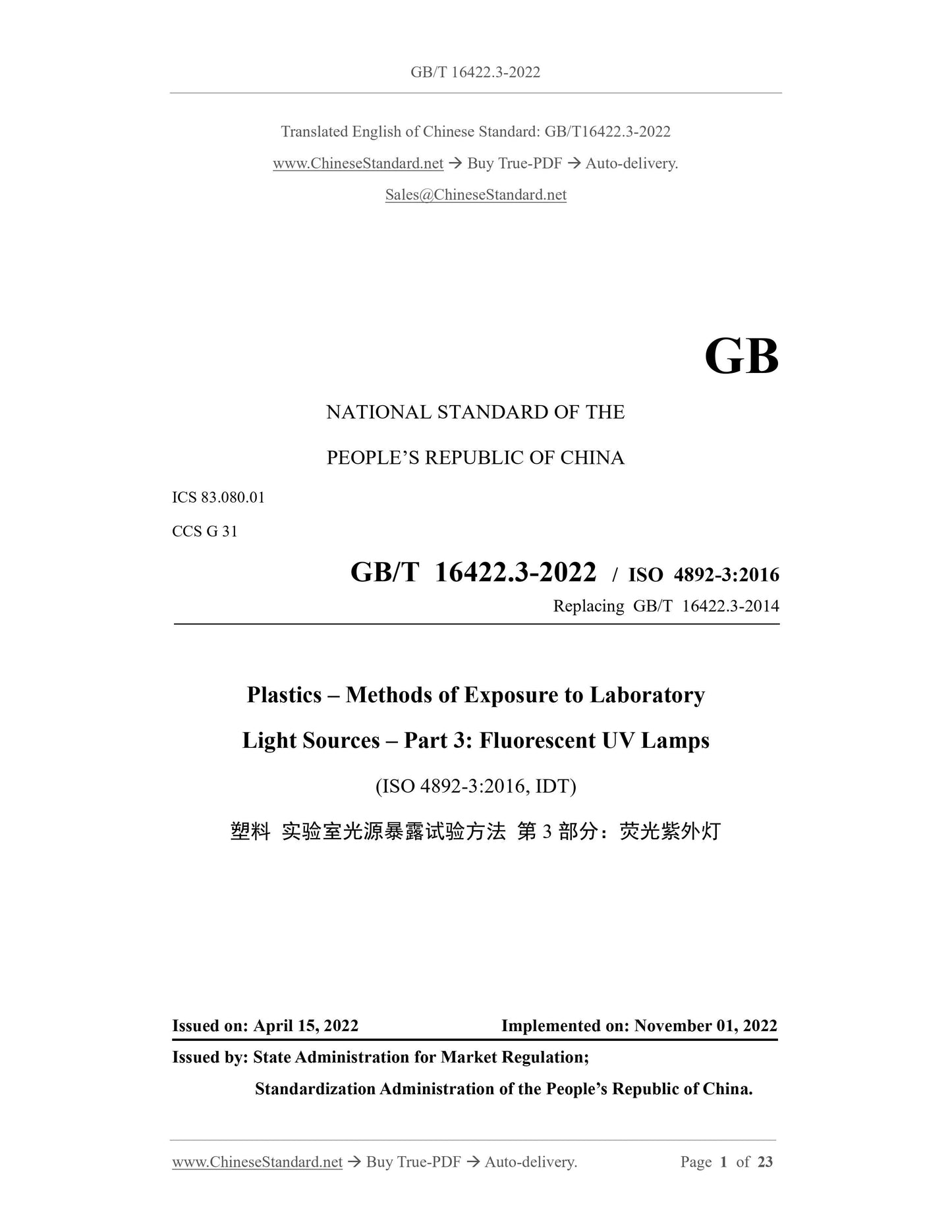
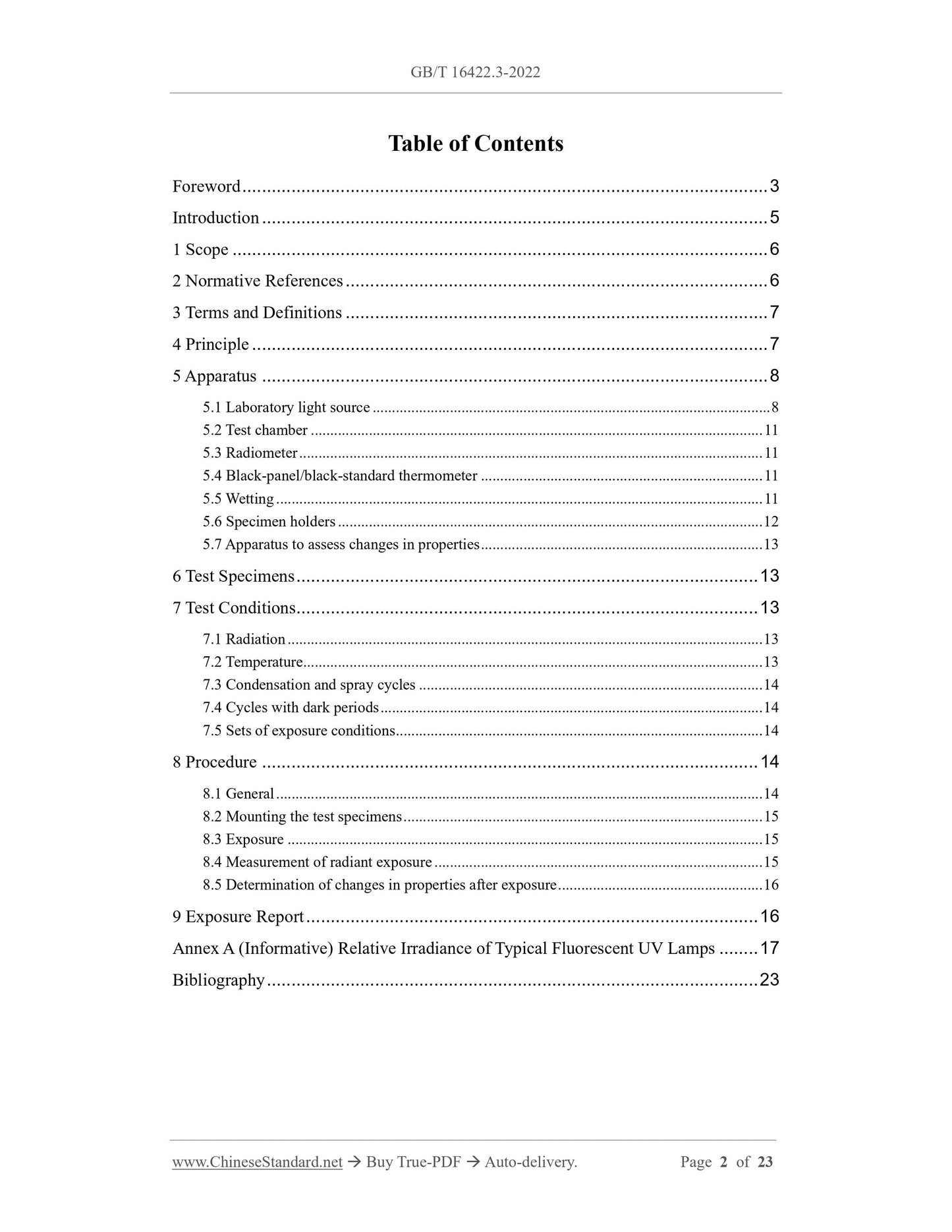
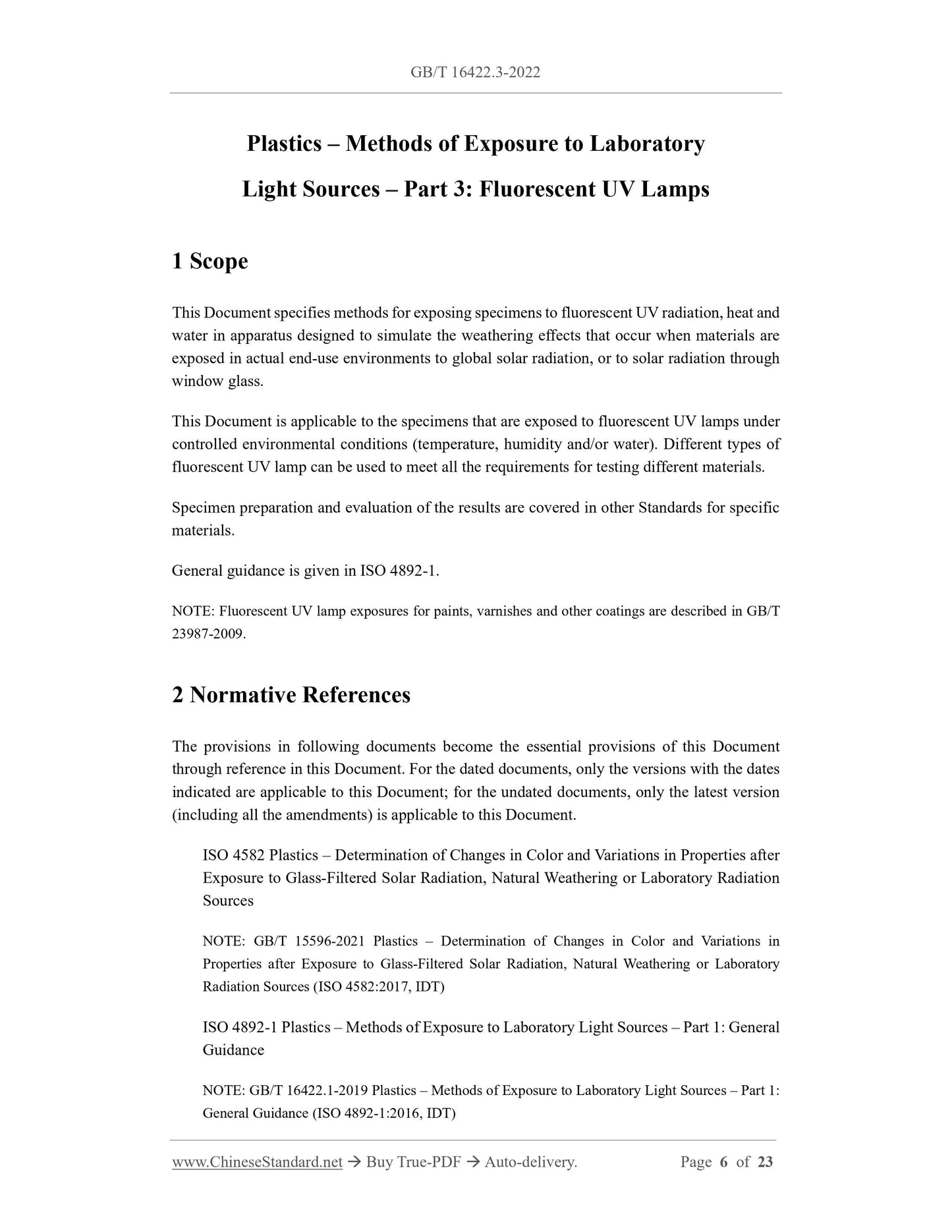
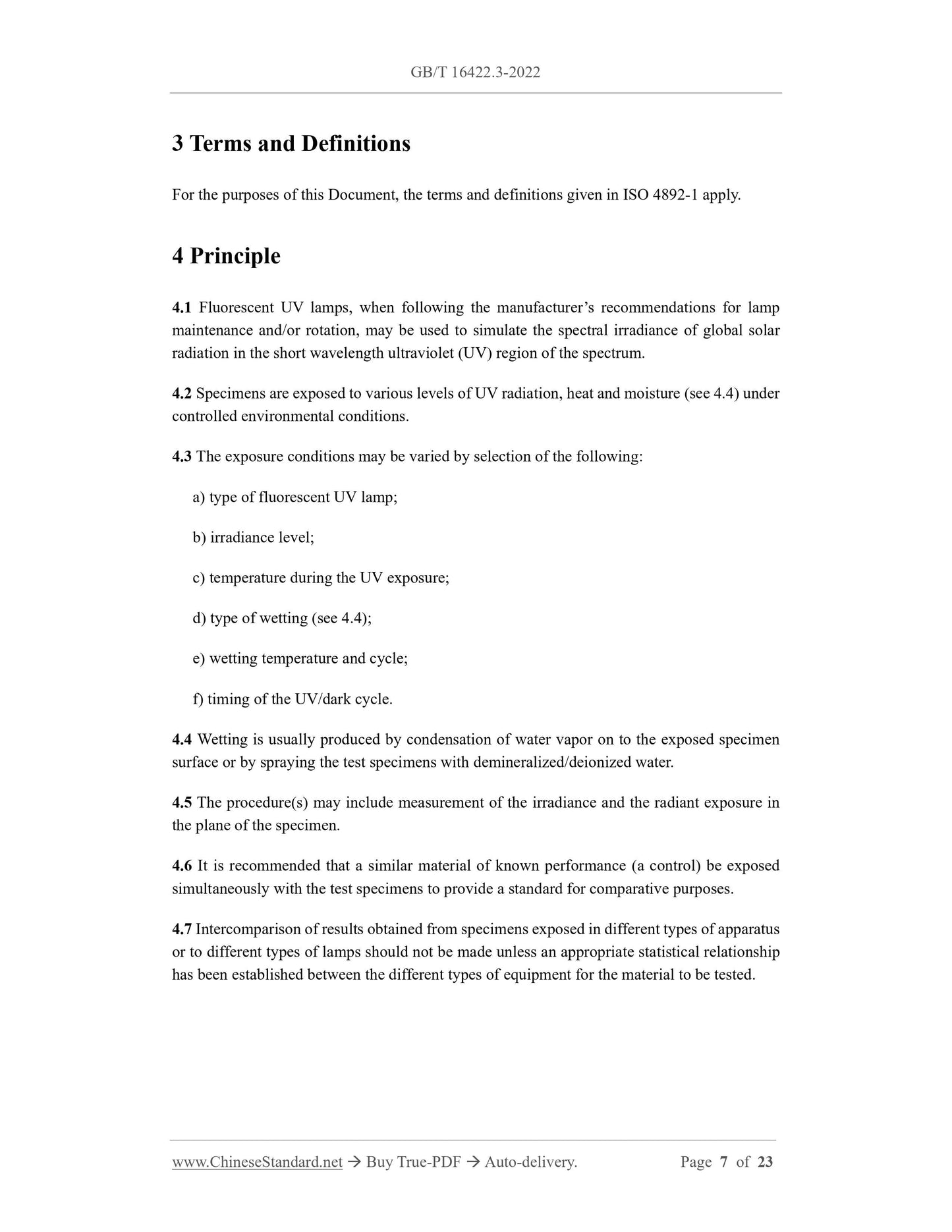
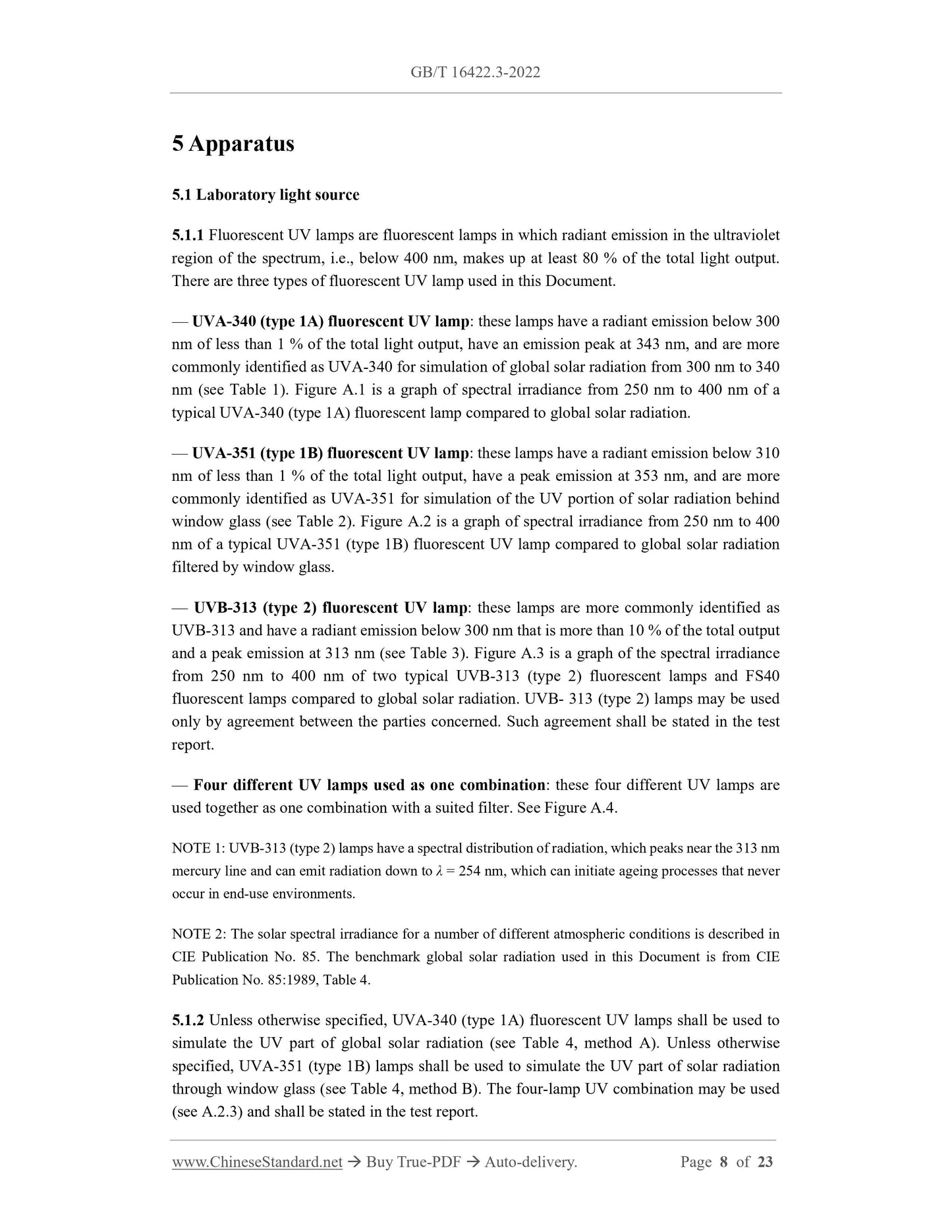
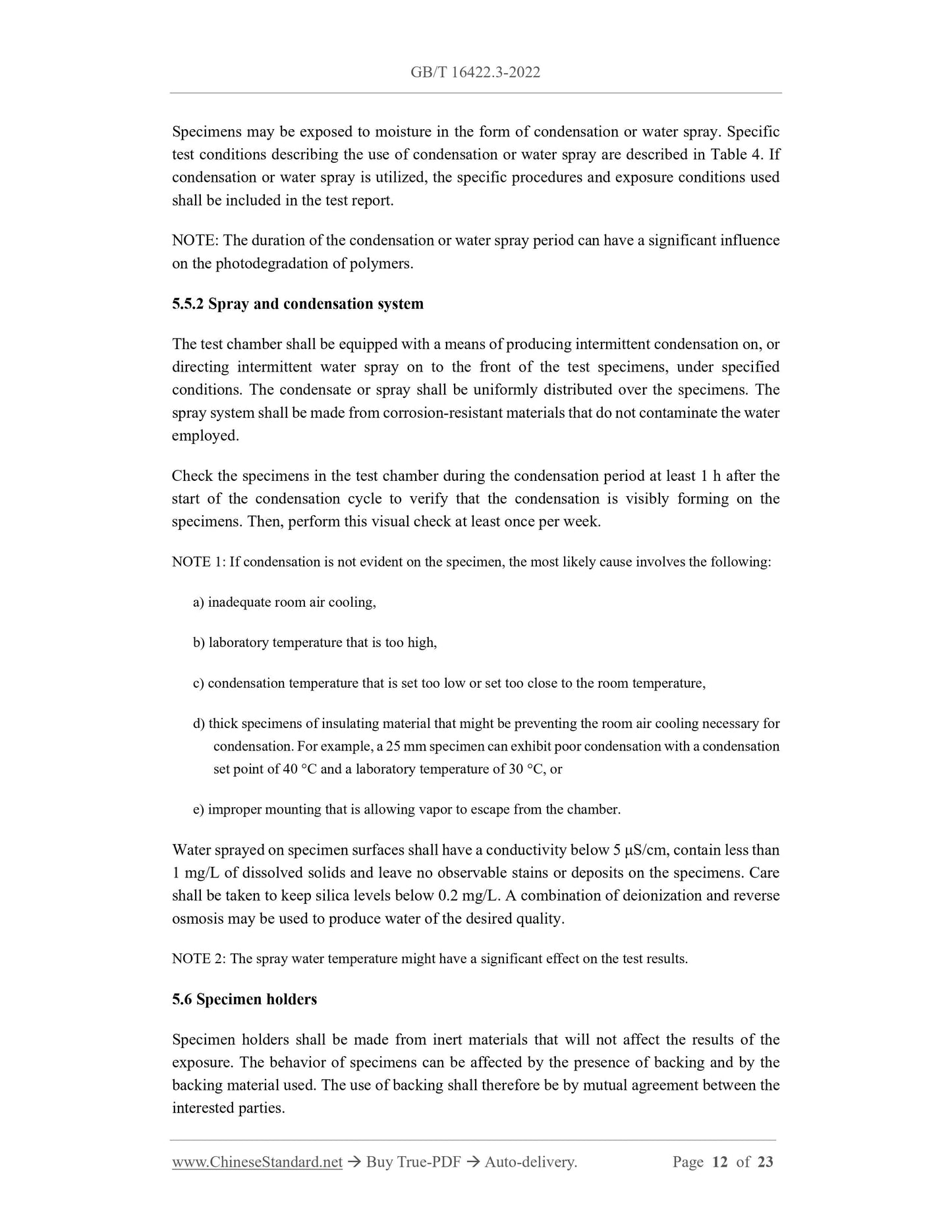
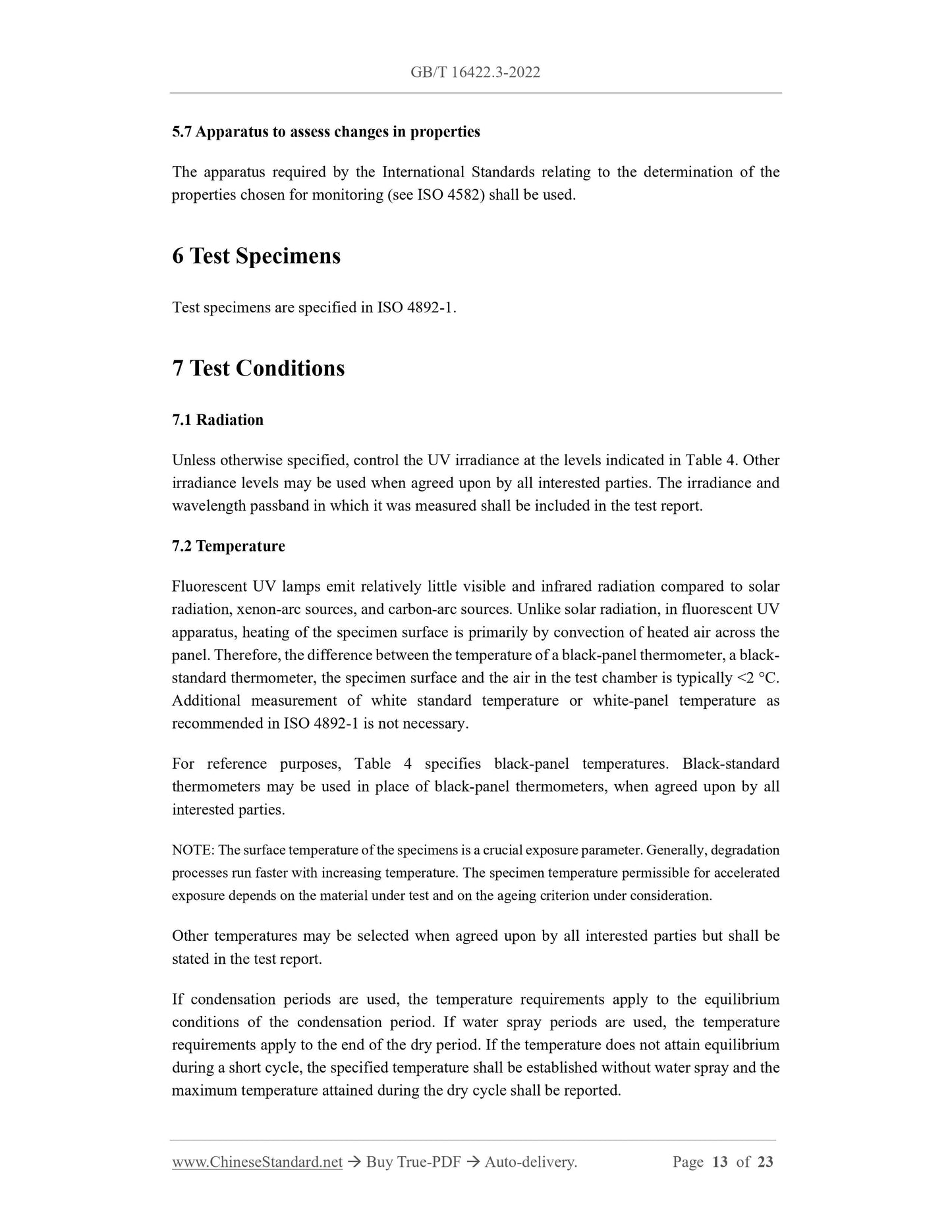
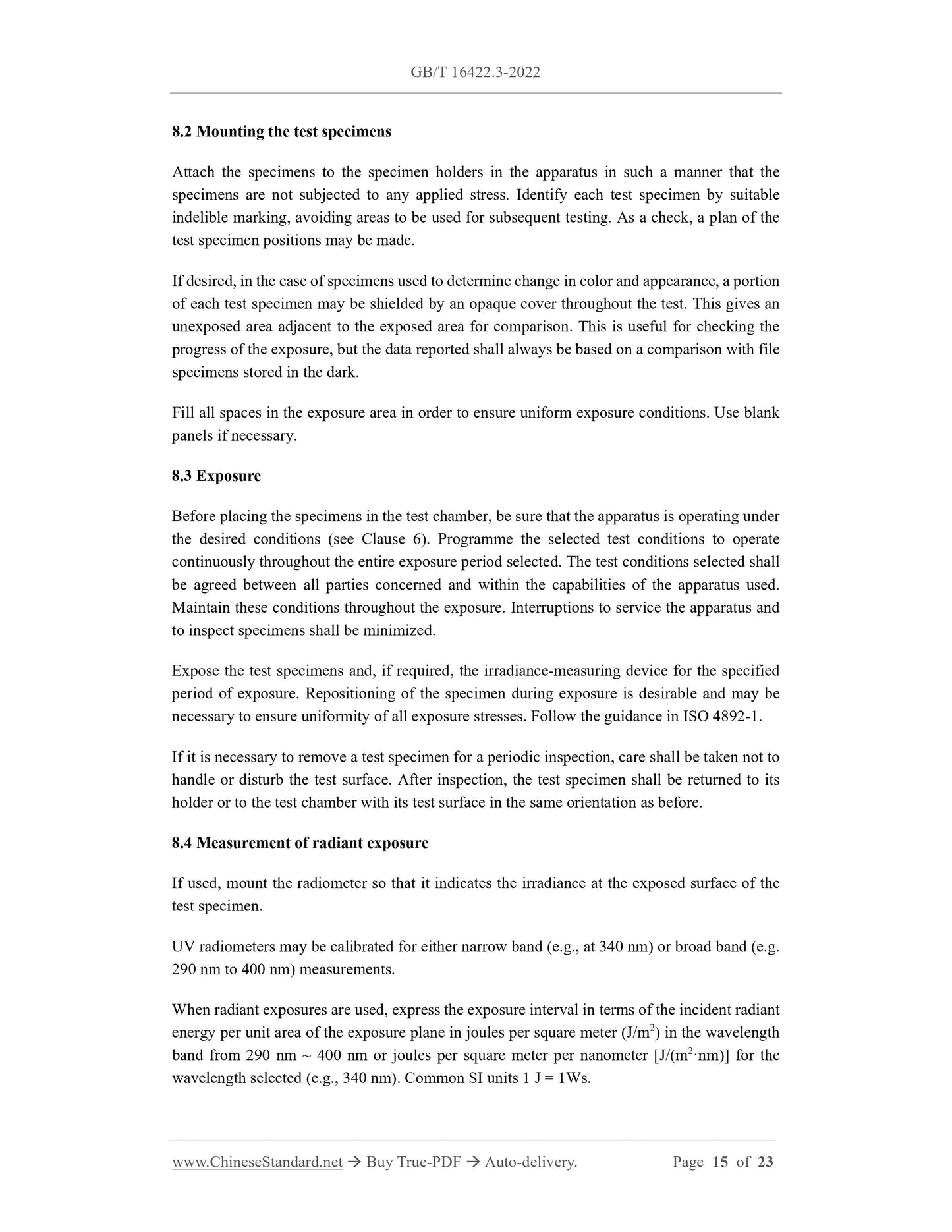
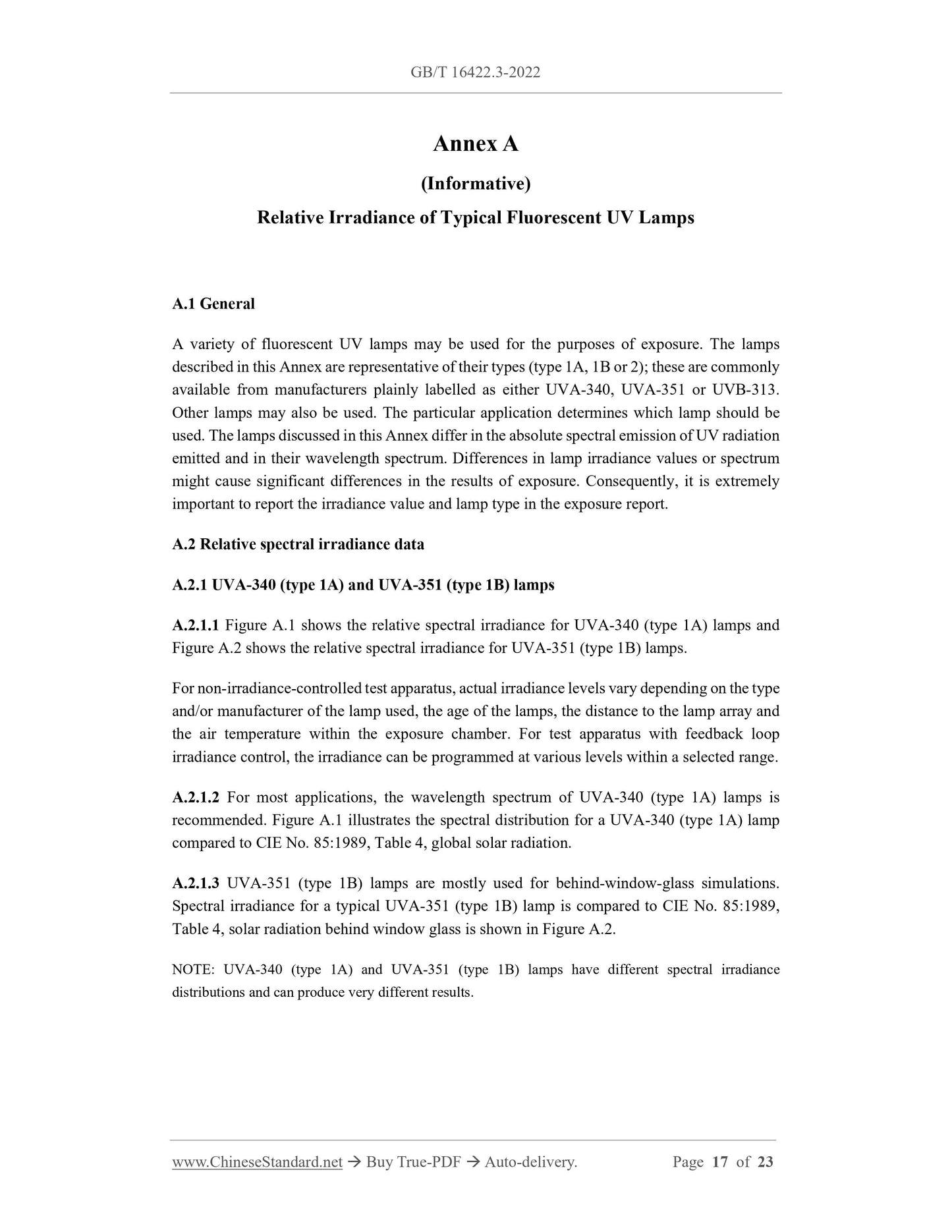