1
/
of
11
www.ChineseStandard.us -- Field Test Asia Pte. Ltd.
GB/T 16411-2008 English PDF (GB/T16411-2008)
GB/T 16411-2008 English PDF (GB/T16411-2008)
Regular price
$280.00
Regular price
Sale price
$280.00
Unit price
/
per
Shipping calculated at checkout.
Couldn't load pickup availability
GB/T 16411-2008: Universal test methods of gas burning appliances for domestic use
Delivery: 9 seconds. Download (and Email) true-PDF + Invoice.
Get Quotation: Click GB/T 16411-2008 (Self-service in 1-minute)
Newer / historical versions: GB/T 16411-2008
Preview True-PDF (Reload/Scroll-down if blank)
Delivery: 9 seconds. Download (and Email) true-PDF + Invoice.
Get Quotation: Click GB/T 16411-2008 (Self-service in 1-minute)
Newer / historical versions: GB/T 16411-2008
Preview True-PDF (Reload/Scroll-down if blank)
Share
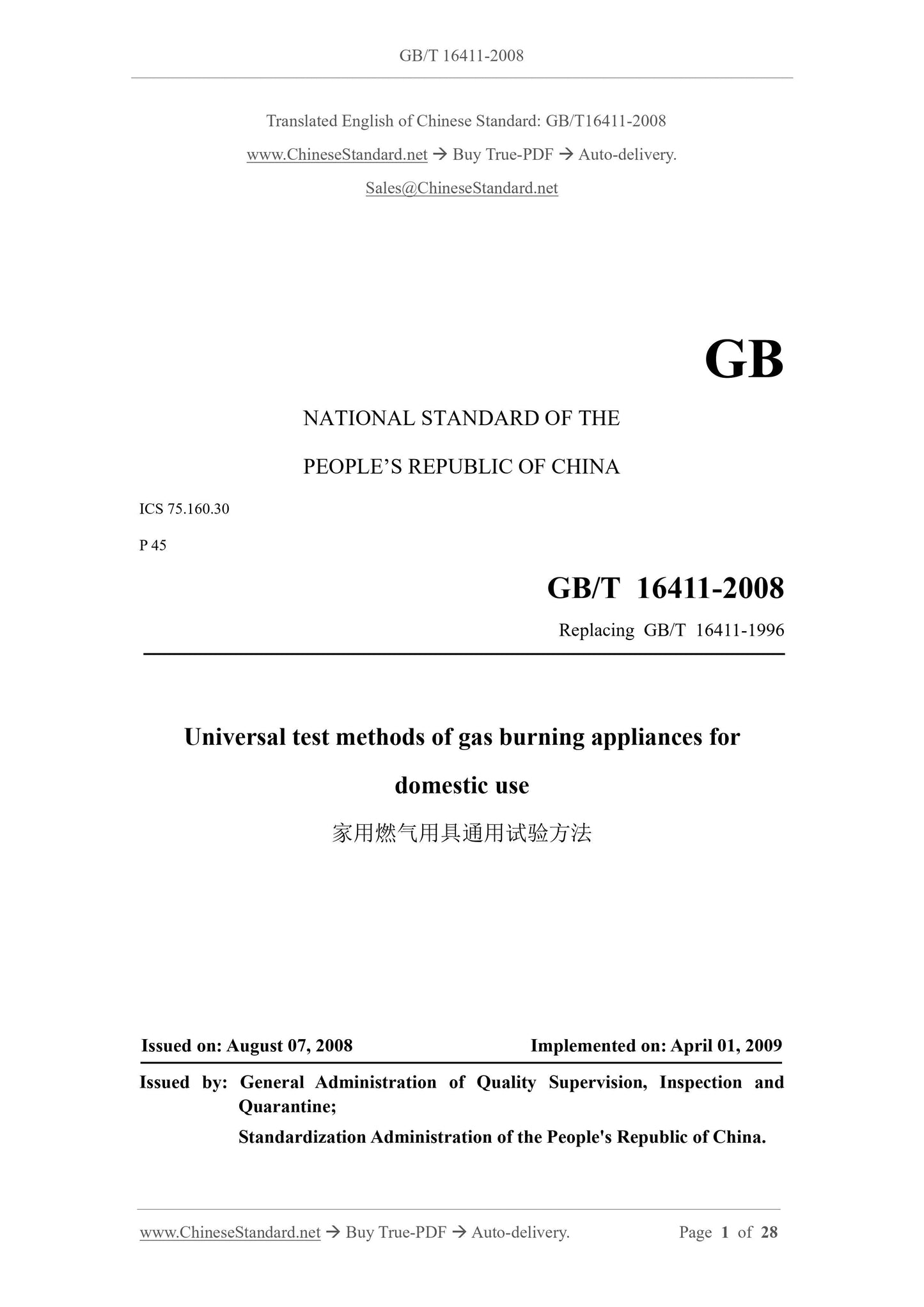
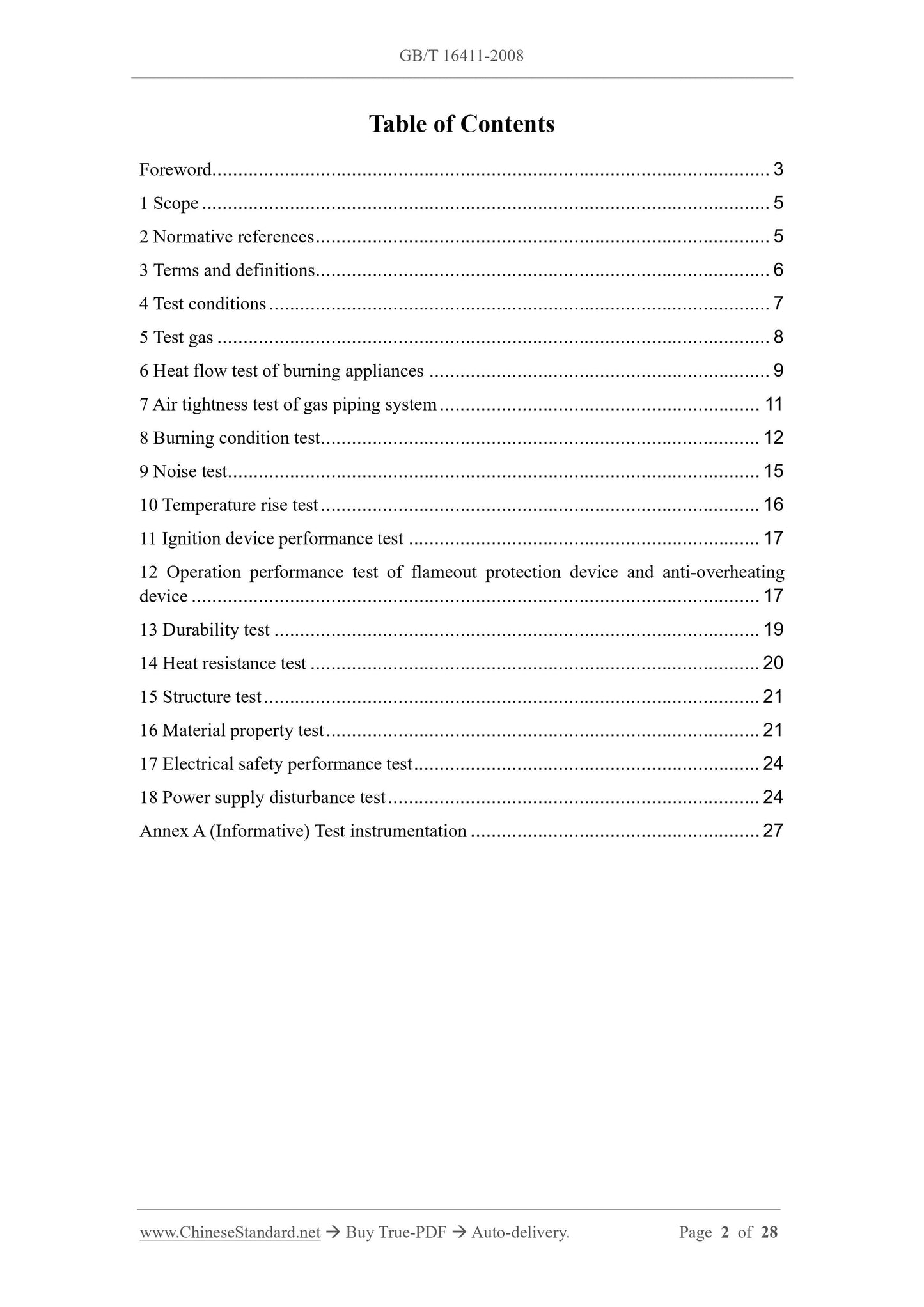
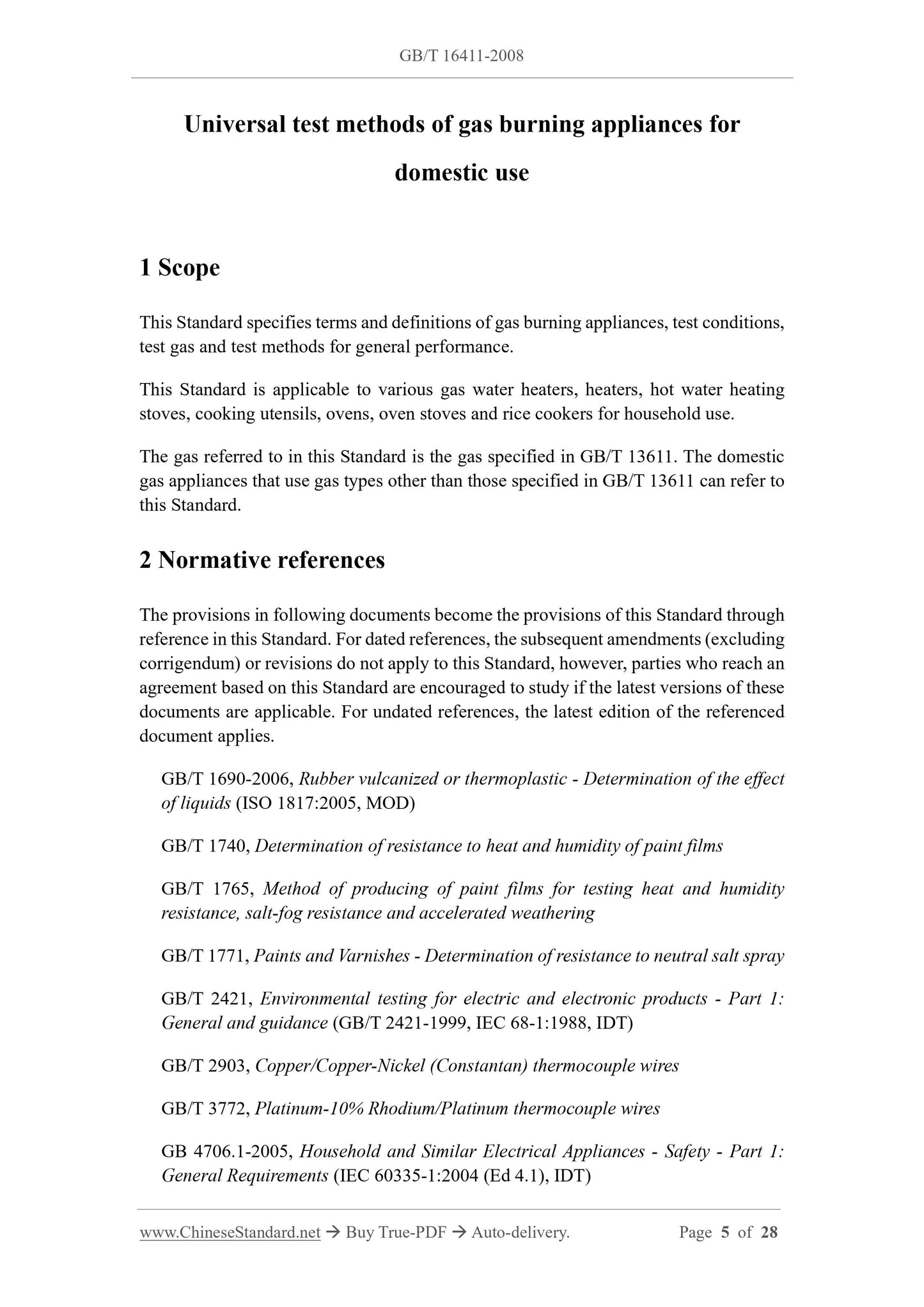
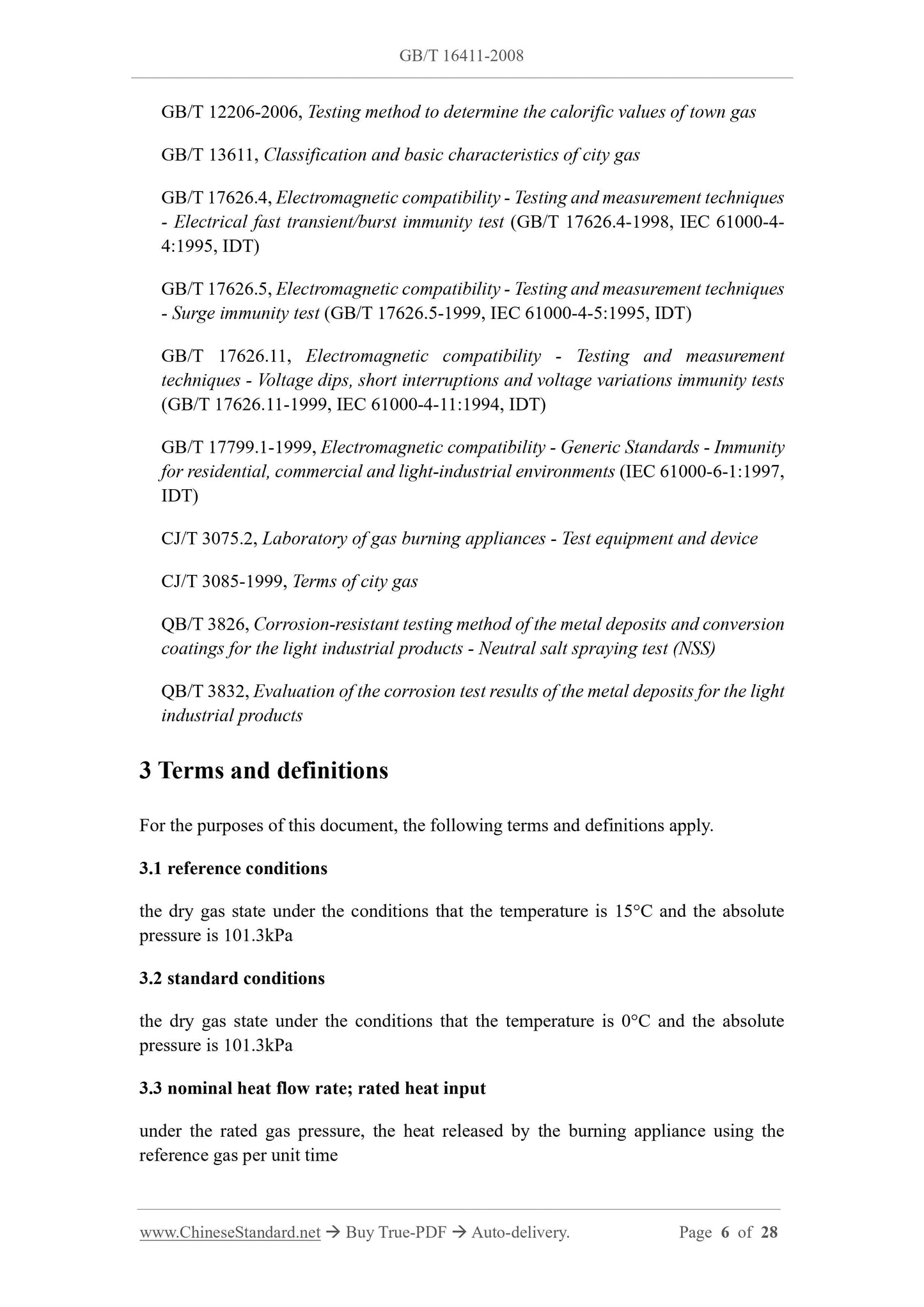
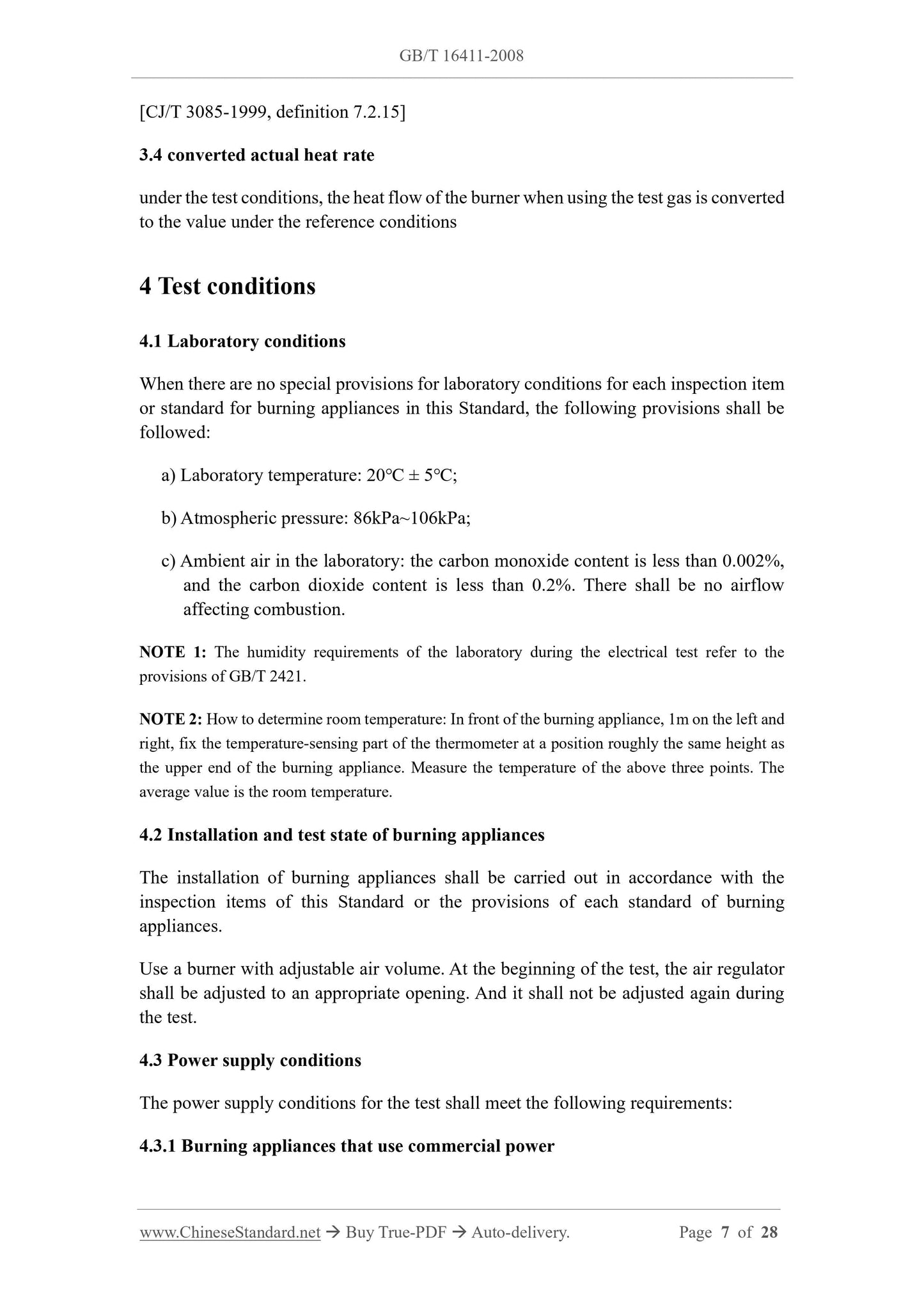
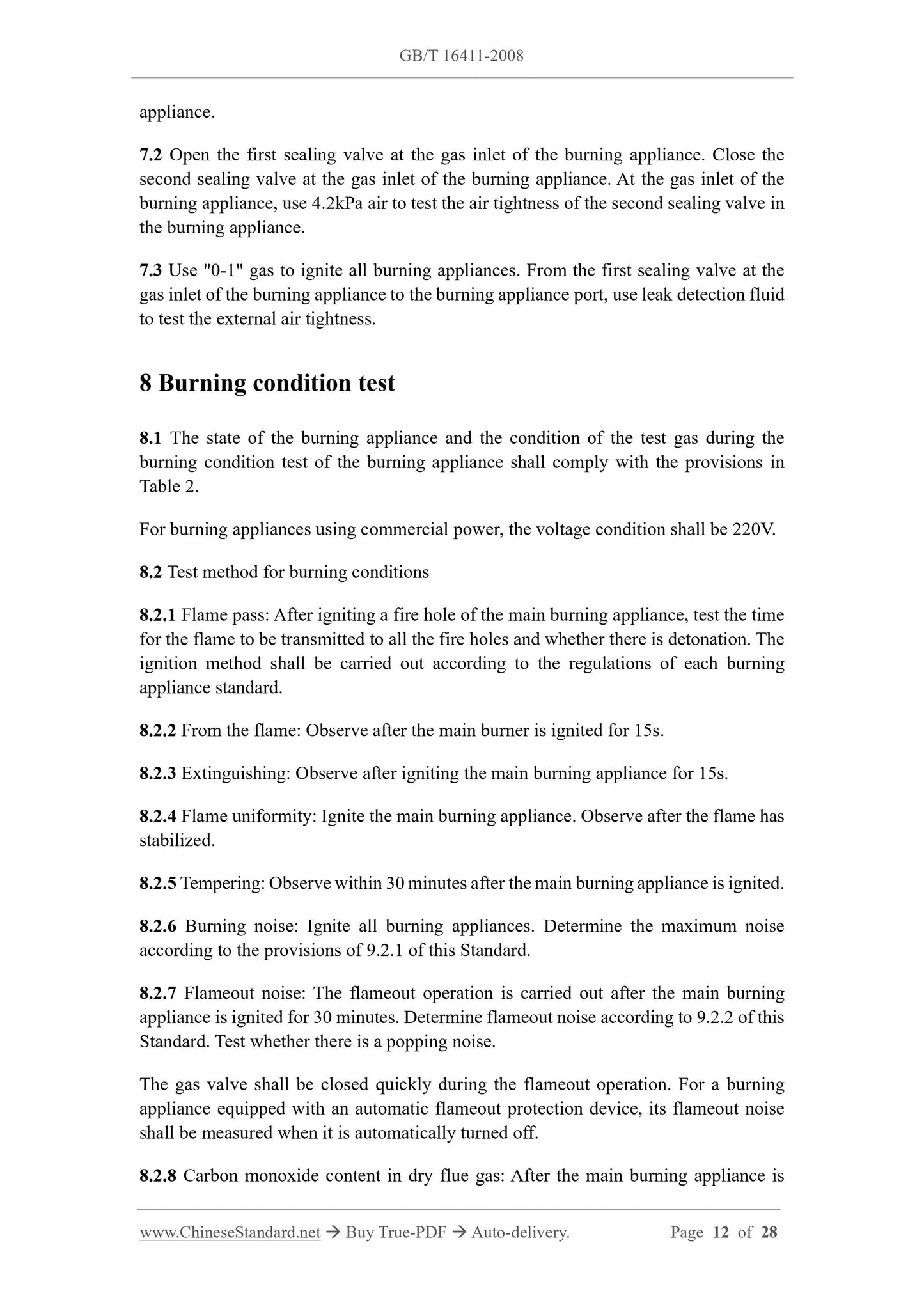
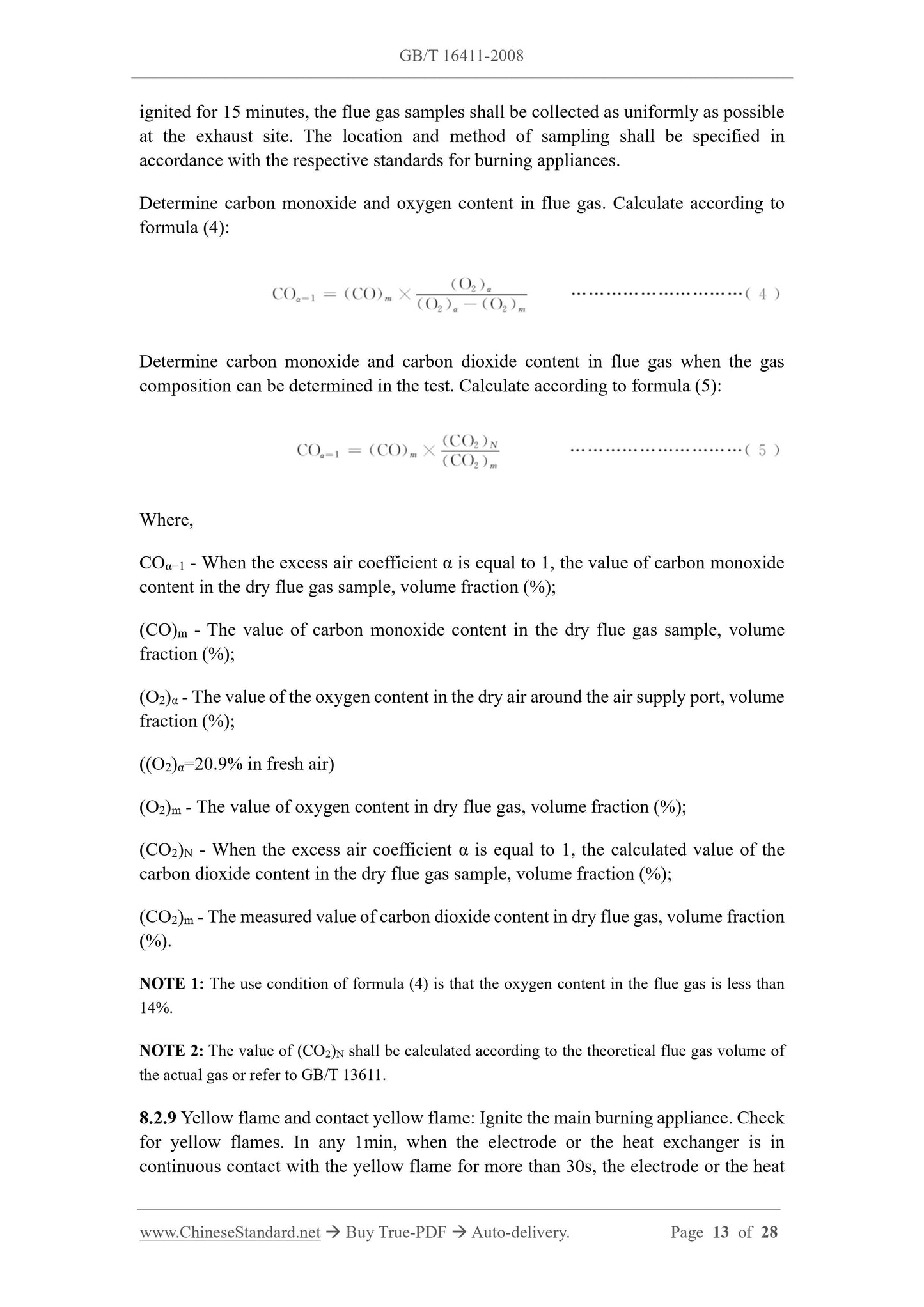
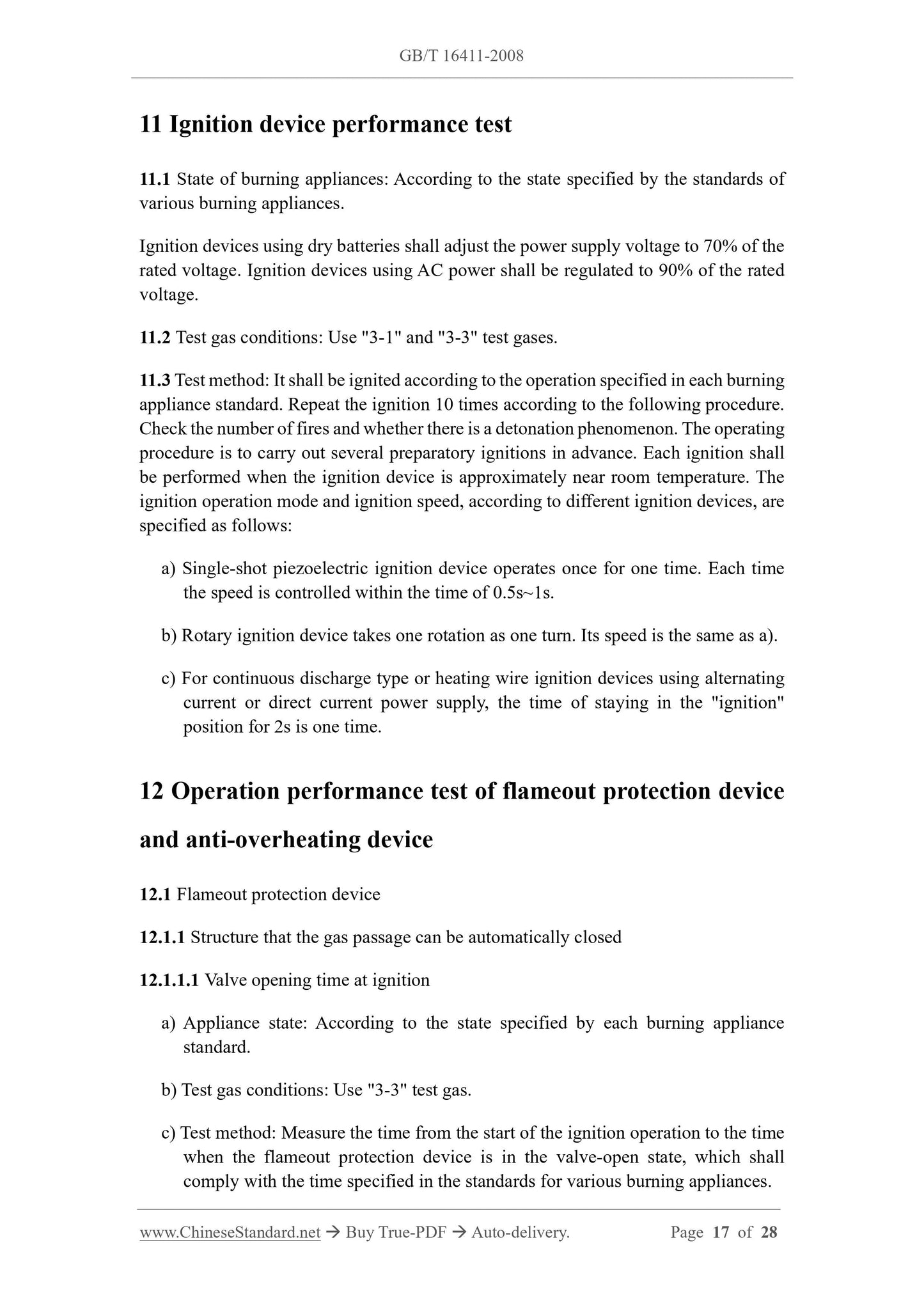
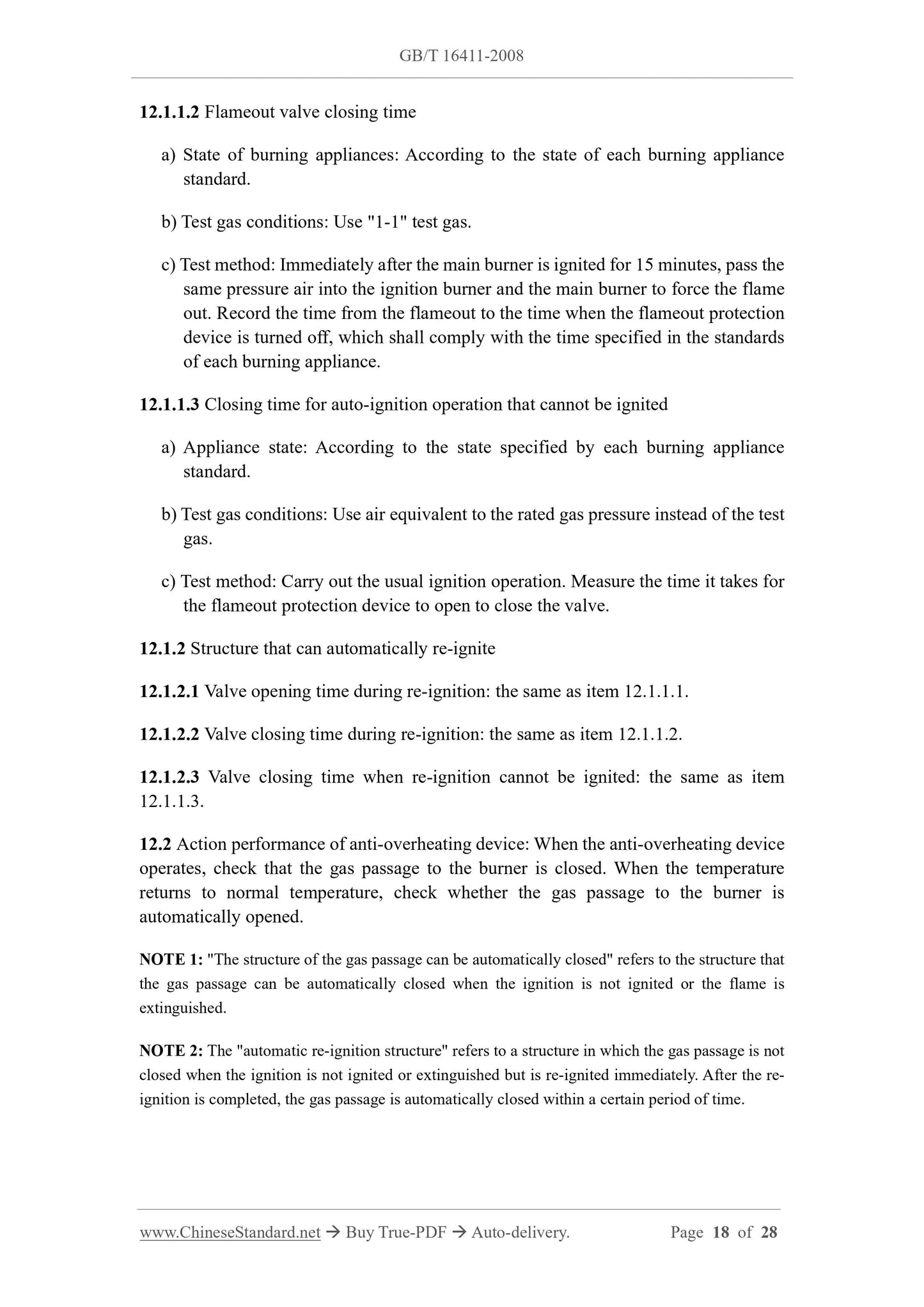
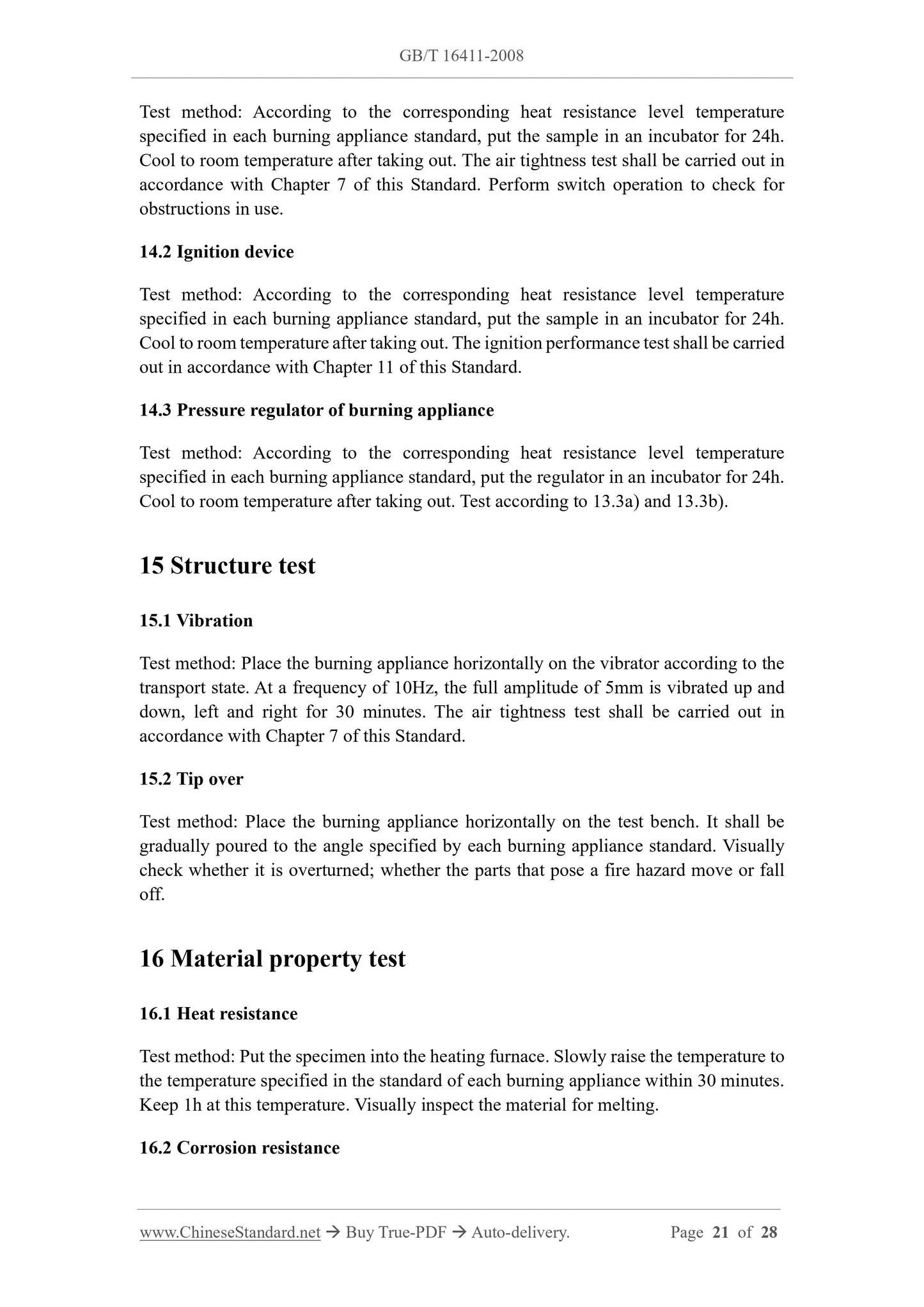
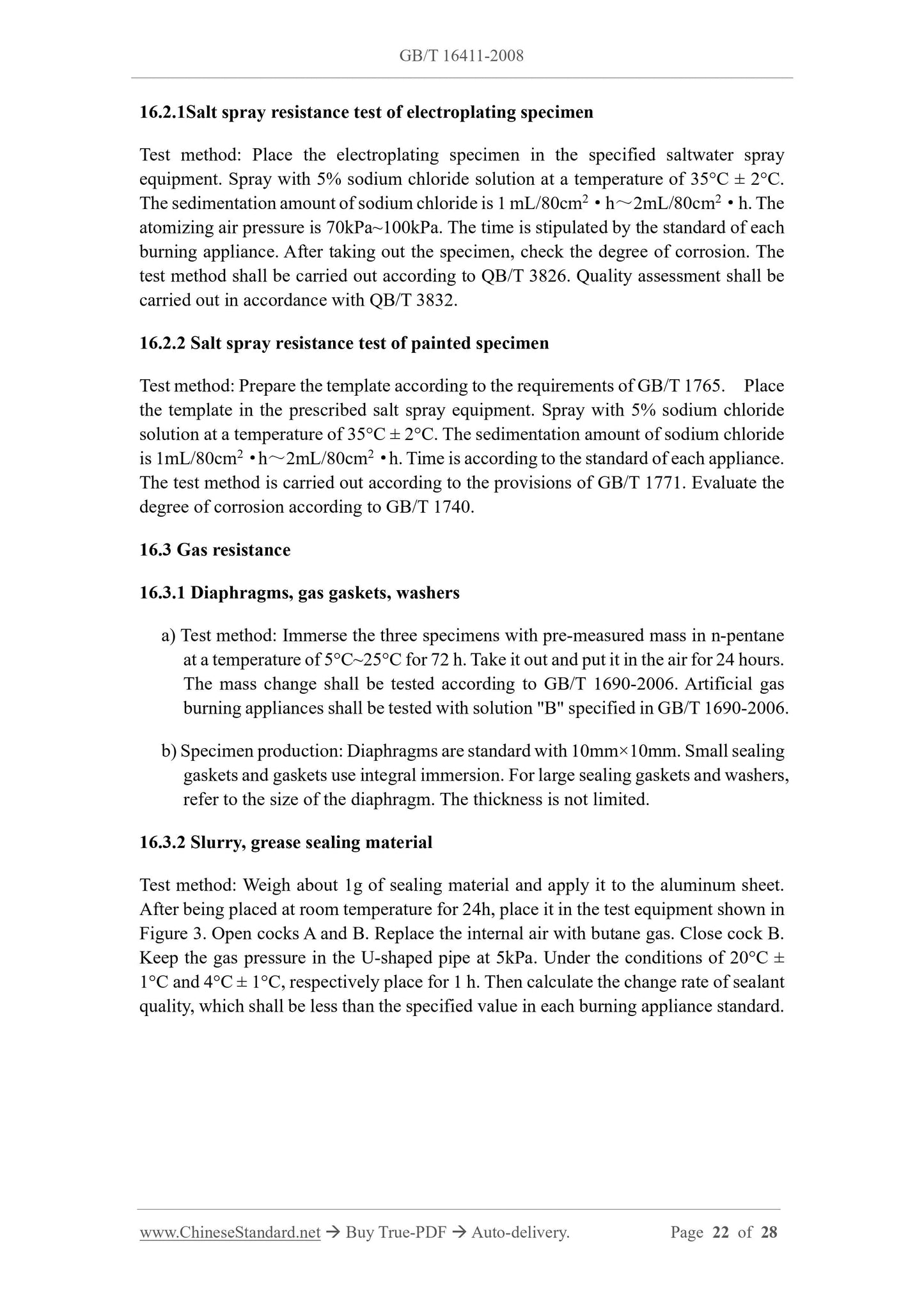