1
/
of
11
www.ChineseStandard.us -- Field Test Asia Pte. Ltd.
GB/T 12785-2014 English PDF (GB/T12785-2014)
GB/T 12785-2014 English PDF (GB/T12785-2014)
Regular price
$1,000.00
Regular price
Sale price
$1,000.00
Unit price
/
per
Shipping calculated at checkout.
Couldn't load pickup availability
GB/T 12785-2014: Test methods for submersible motor-pumps
Delivery: 9 seconds. Download (and Email) true-PDF + Invoice.
Get Quotation: Click GB/T 12785-2014 (Self-service in 1-minute)
Newer / historical versions: GB/T 12785-2014
Preview True-PDF (Reload/Scroll-down if blank)
Delivery: 9 seconds. Download (and Email) true-PDF + Invoice.
Get Quotation: Click GB/T 12785-2014 (Self-service in 1-minute)
Newer / historical versions: GB/T 12785-2014
Preview True-PDF (Reload/Scroll-down if blank)
Share

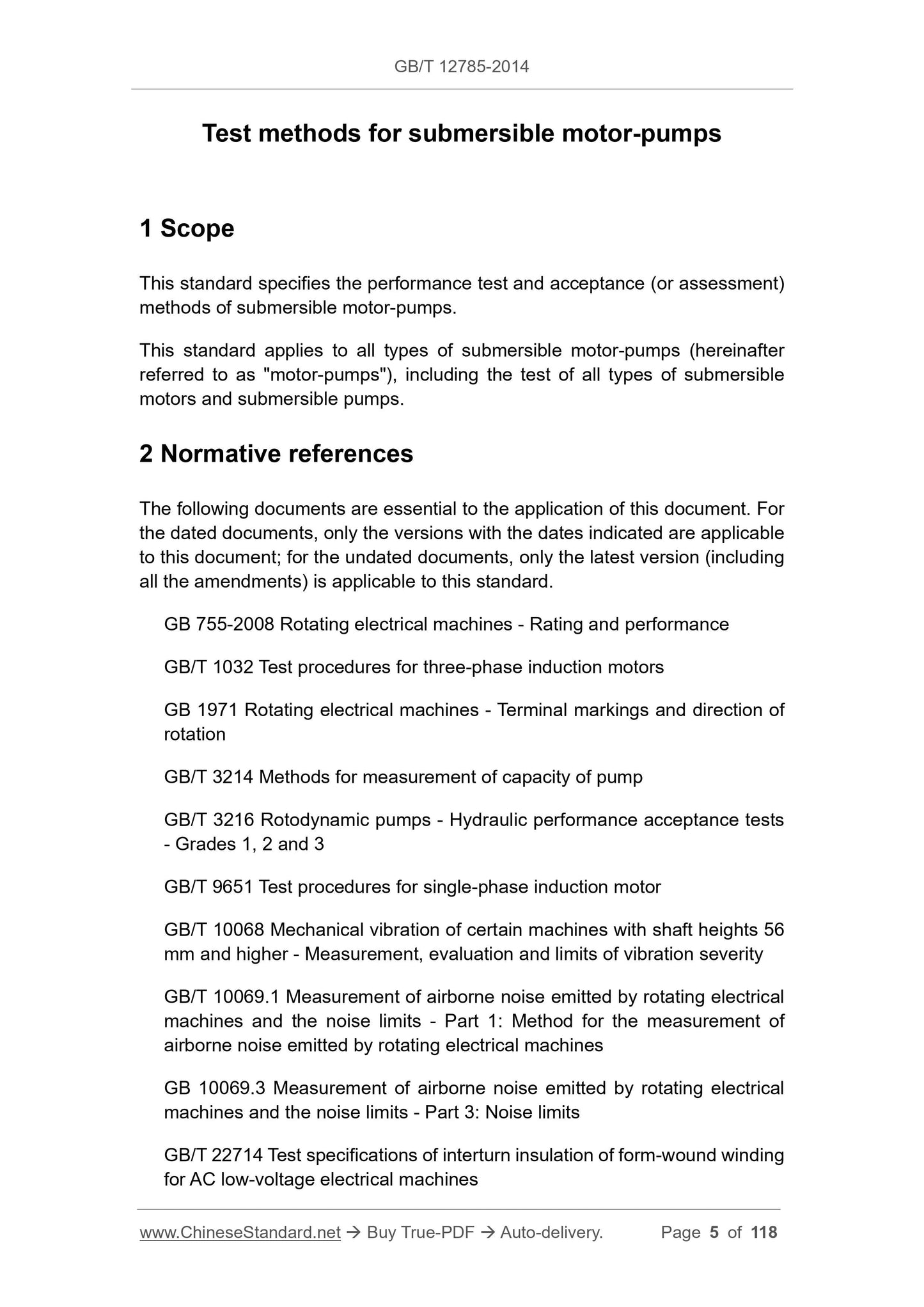
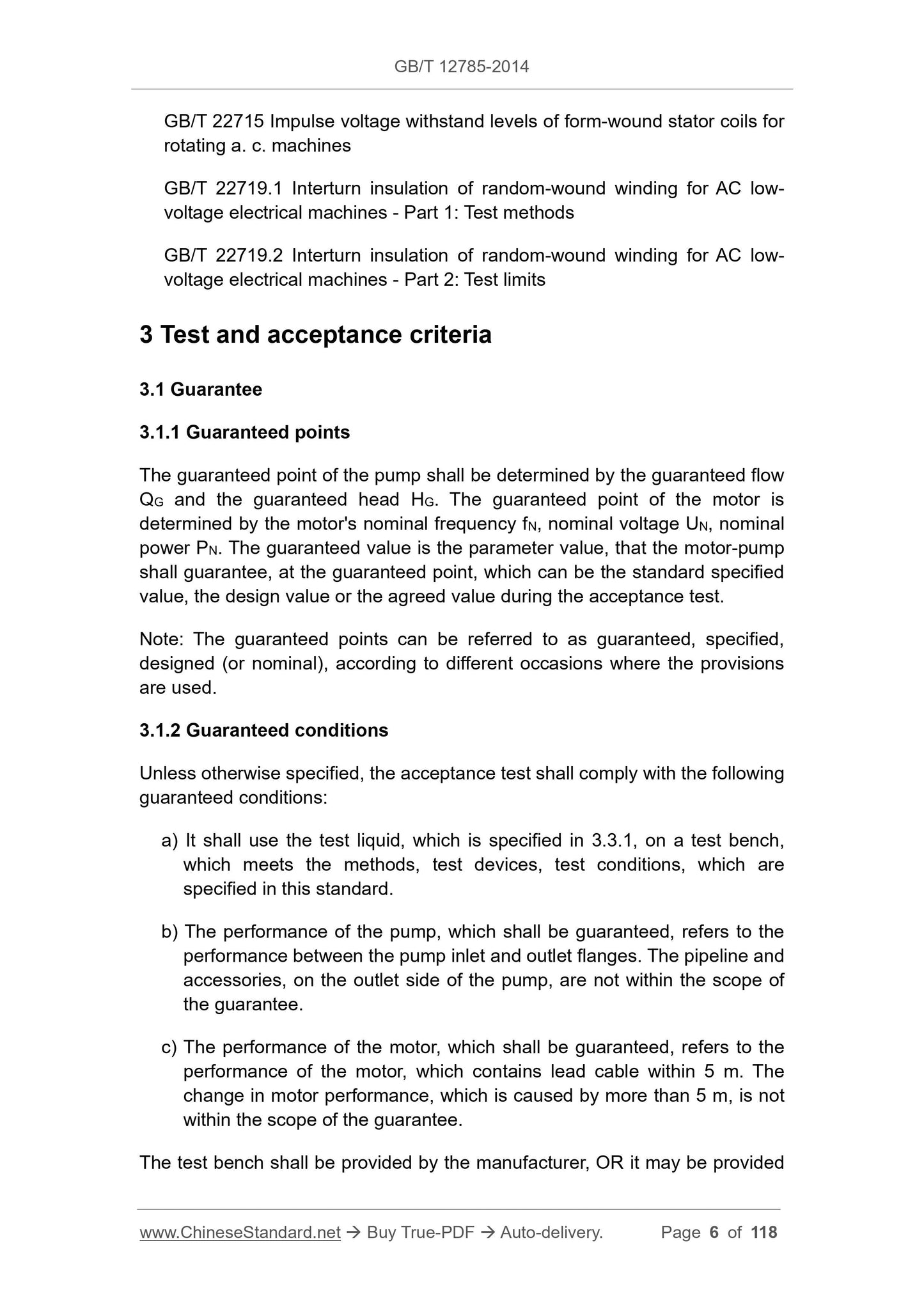
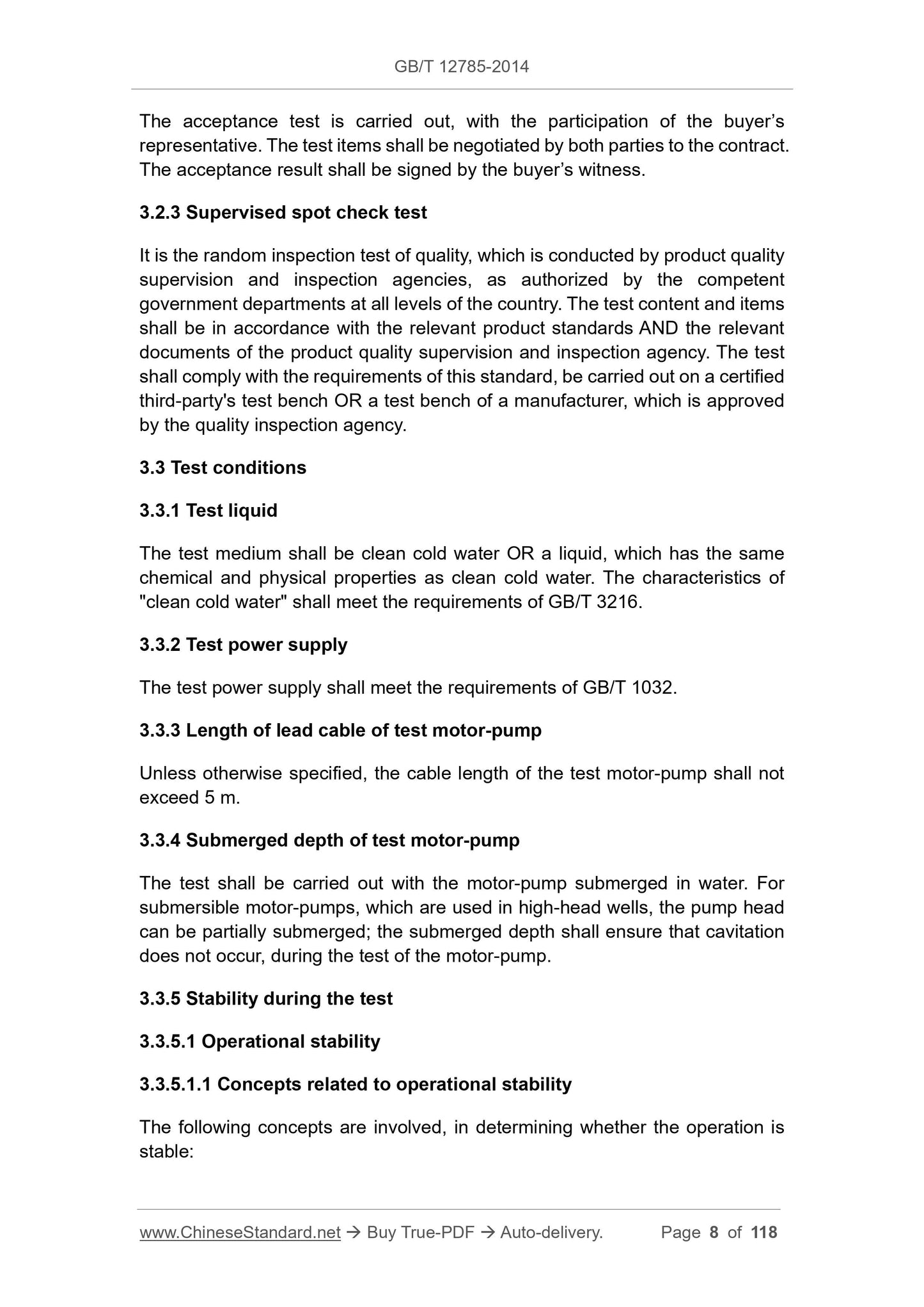
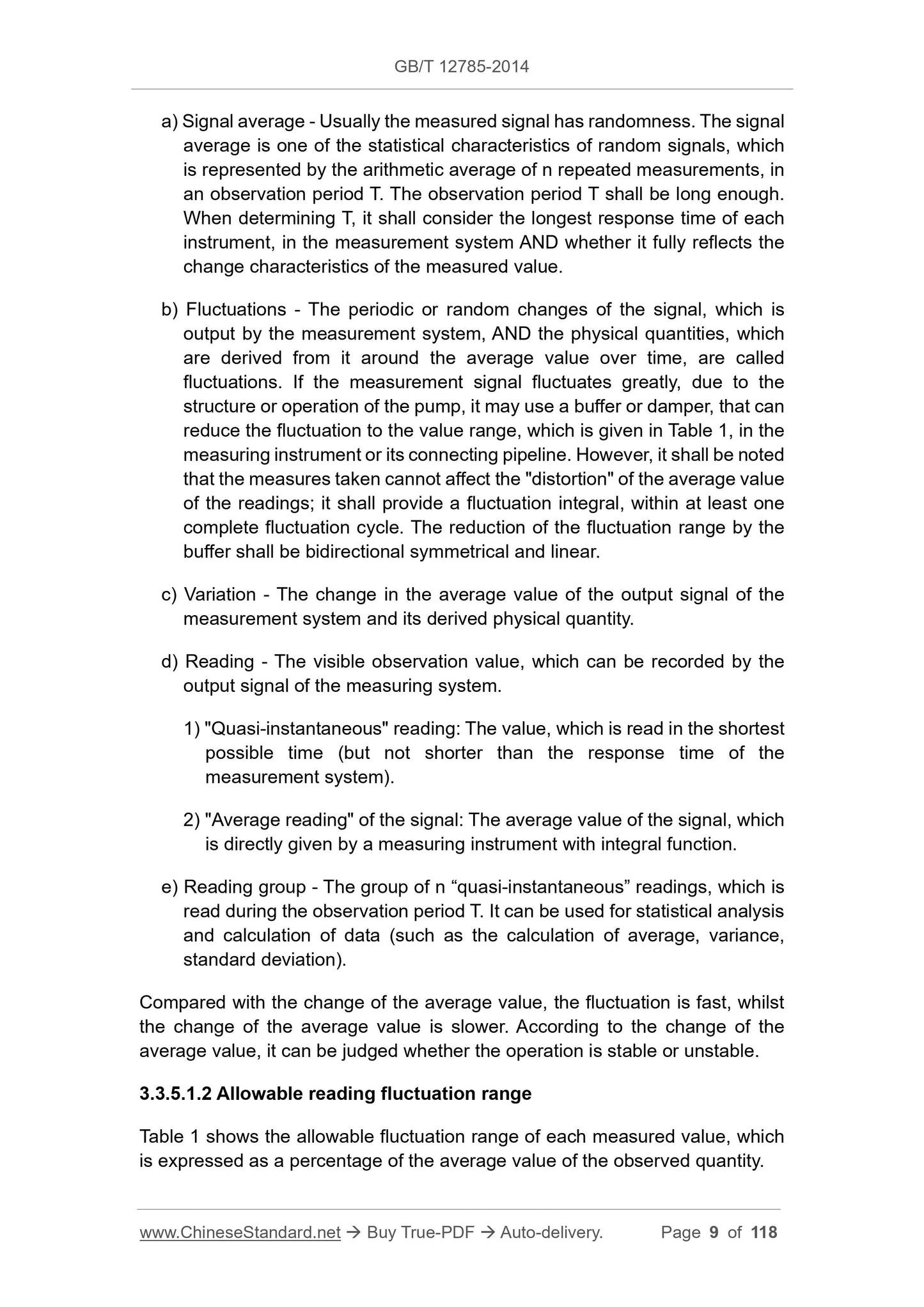
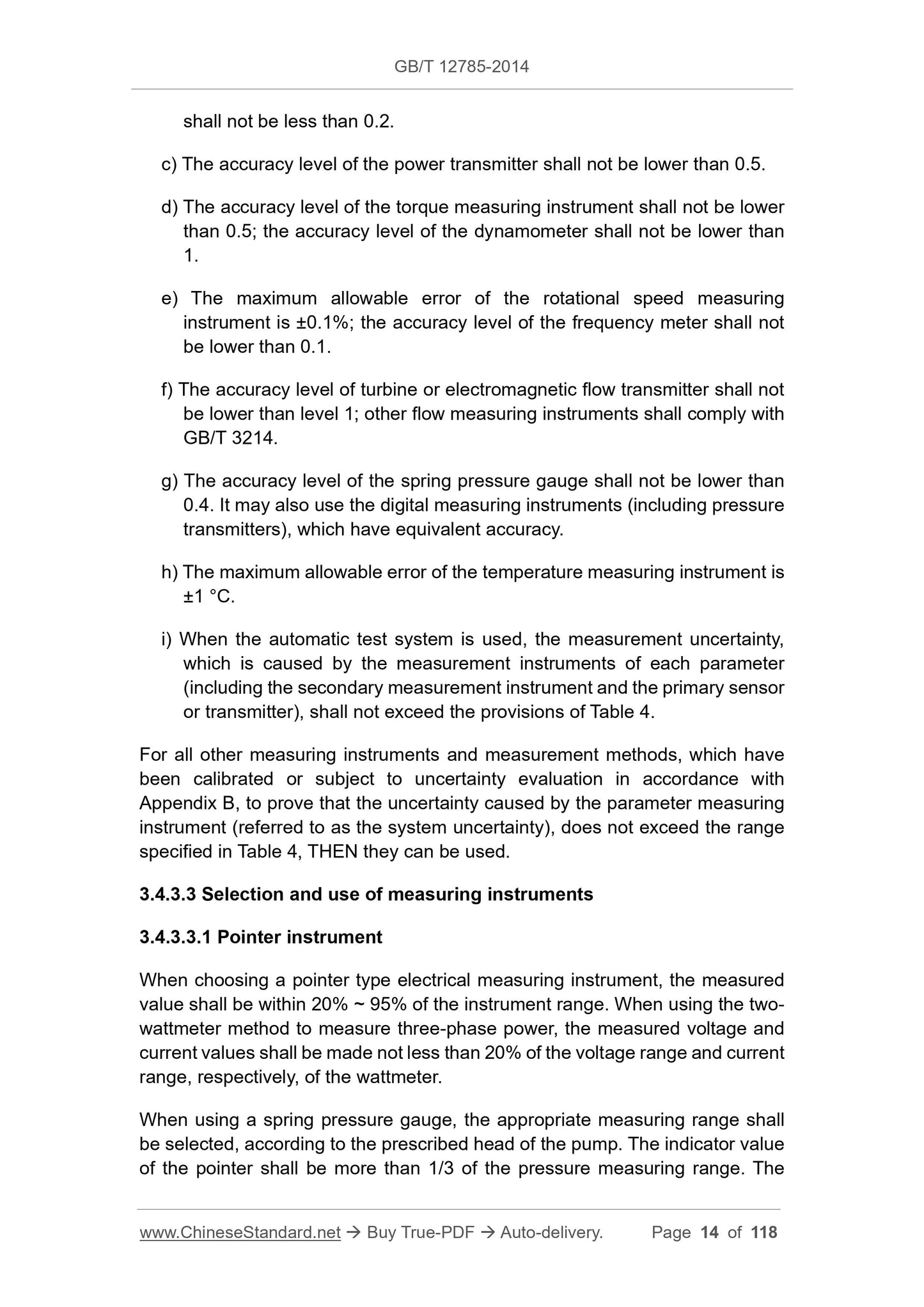
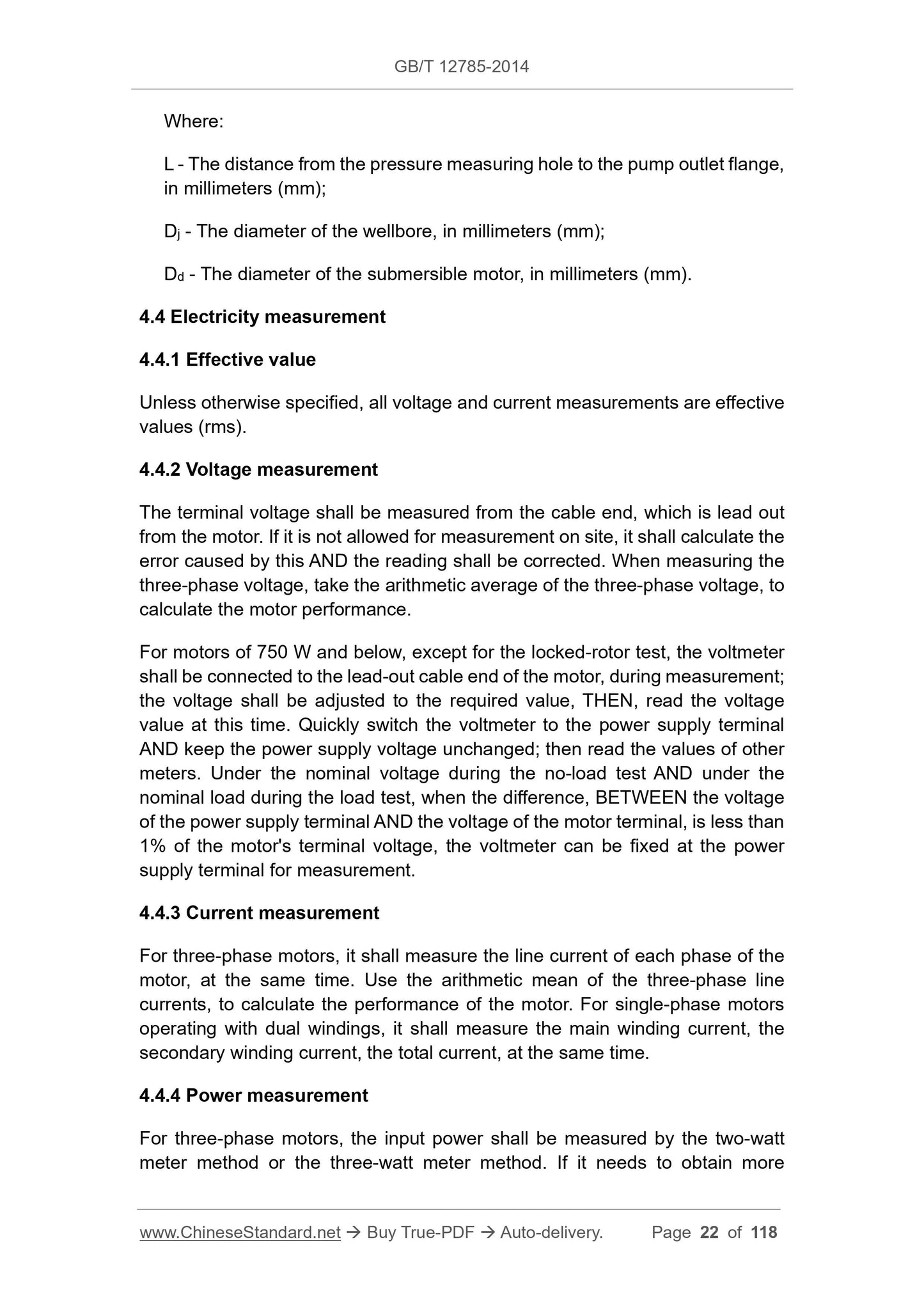
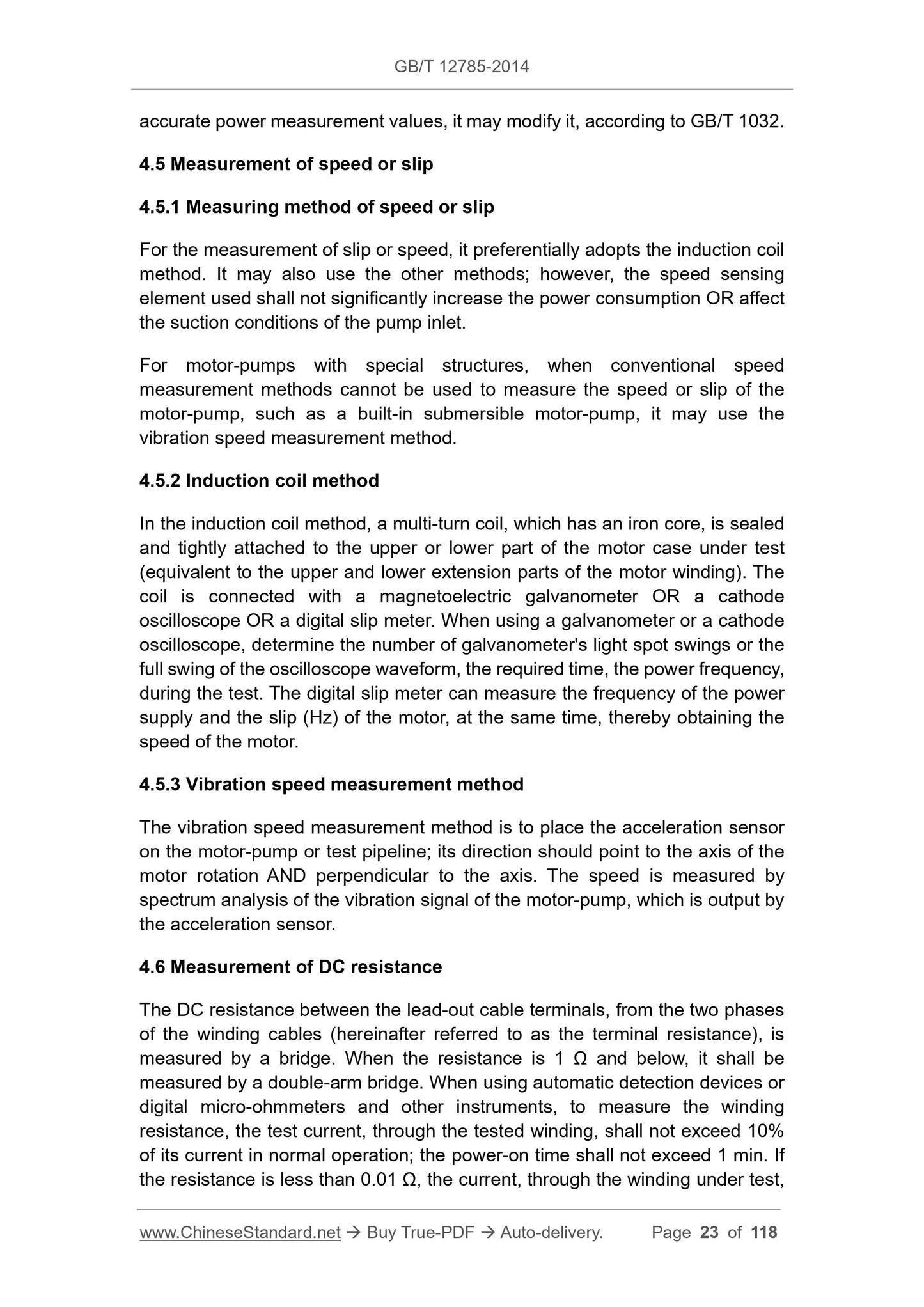
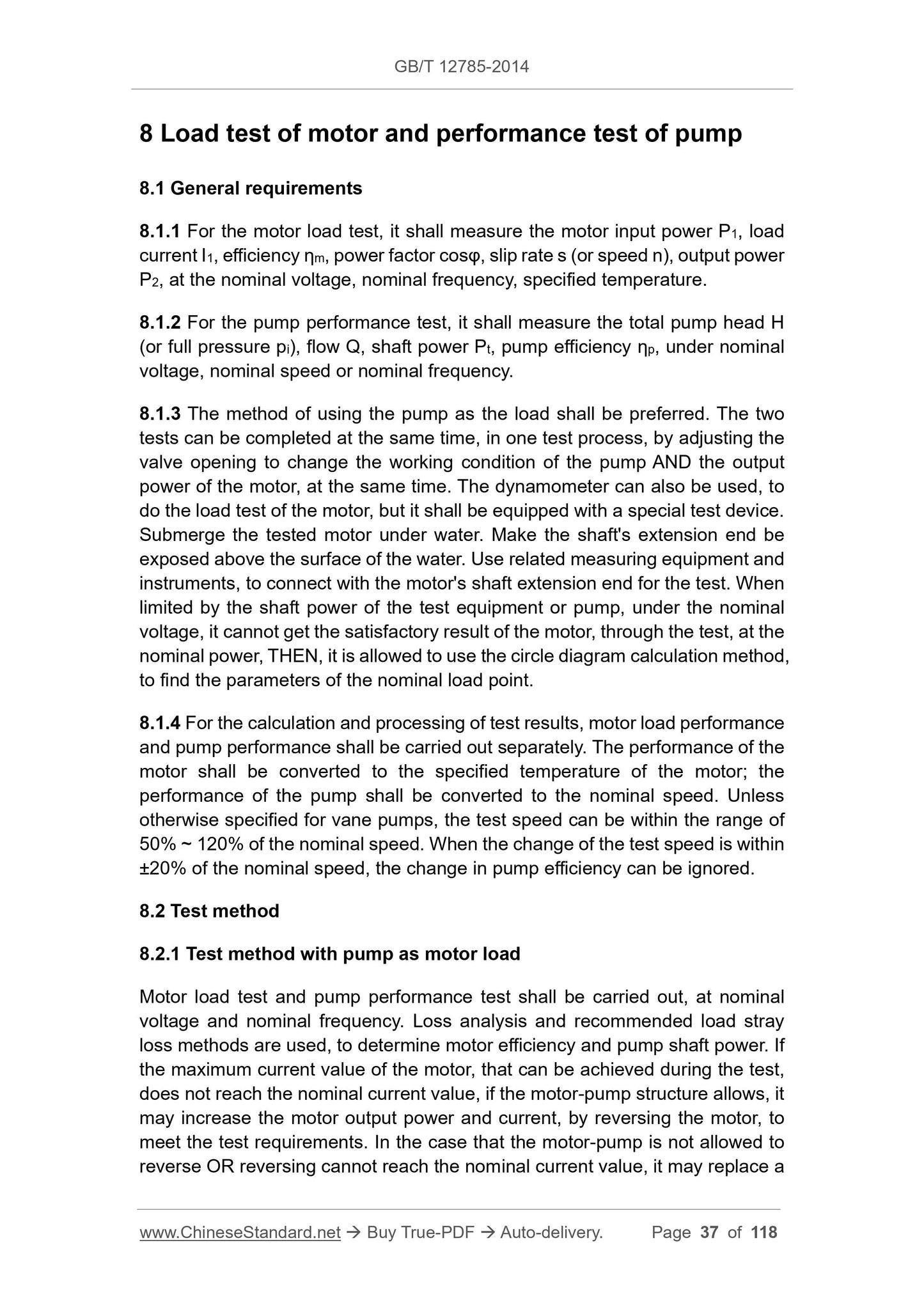
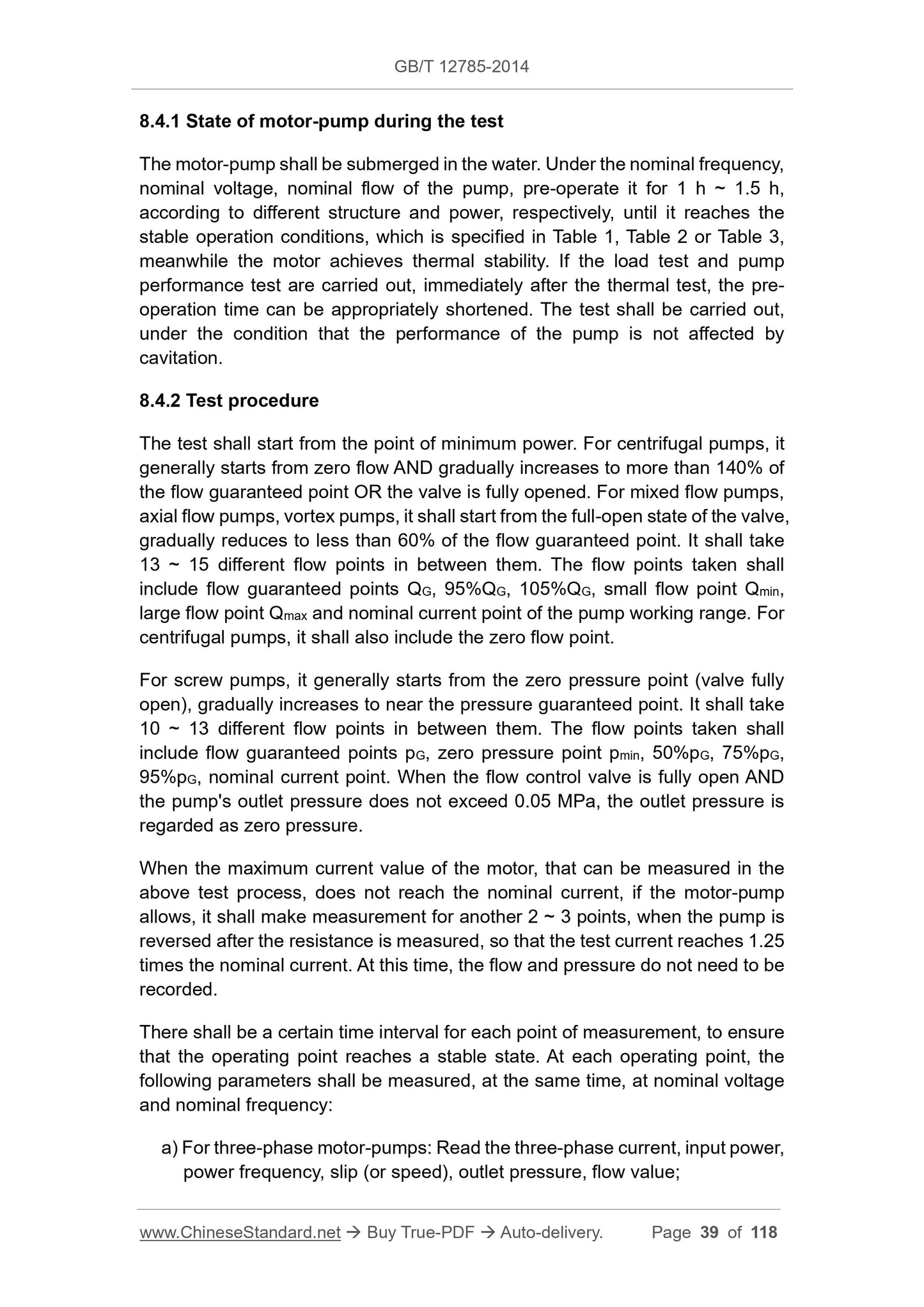
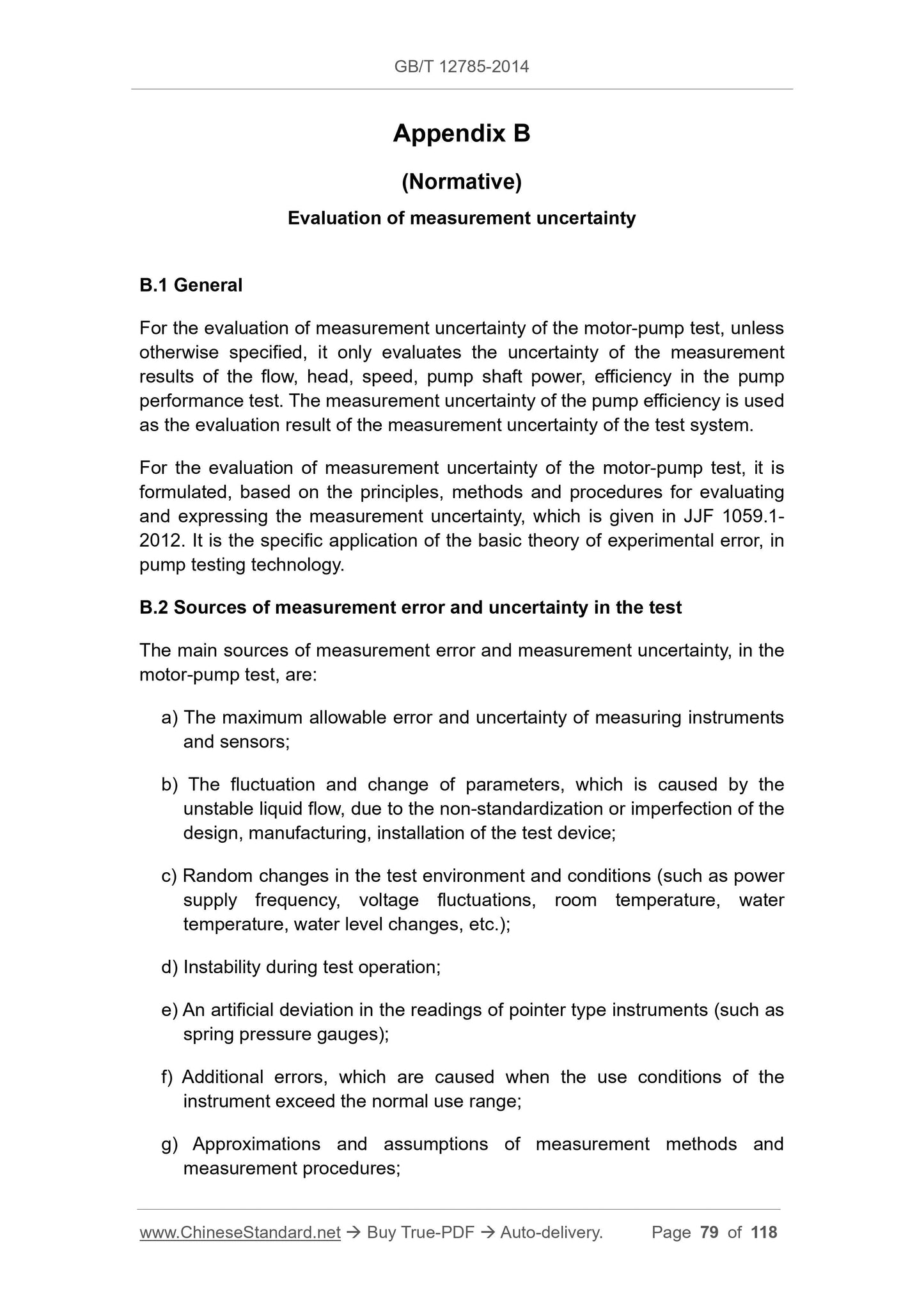