1
/
of
4
www.ChineseStandard.us -- Field Test Asia Pte. Ltd.
GB/T 12467.3-2009 English PDF (GB/T12467.3-2009)
GB/T 12467.3-2009 English PDF (GB/T12467.3-2009)
Regular price
$70.00
Regular price
Sale price
$70.00
Unit price
/
per
Shipping calculated at checkout.
Couldn't load pickup availability
GB/T 12467.3-2009: Quality requirements for fusion welding of metallic materials -- Part 3: Standard quality requirements
Delivery: 9 seconds. Download (and Email) true-PDF + Invoice.
Get Quotation: Click GB/T 12467.3-2009 (Self-service in 1-minute)
Newer / historical versions: GB/T 12467.3-2009
Preview True-PDF (Reload/Scroll-down if blank)
Delivery: 9 seconds. Download (and Email) true-PDF + Invoice.
Get Quotation: Click GB/T 12467.3-2009 (Self-service in 1-minute)
Newer / historical versions: GB/T 12467.3-2009
Preview True-PDF (Reload/Scroll-down if blank)
Share
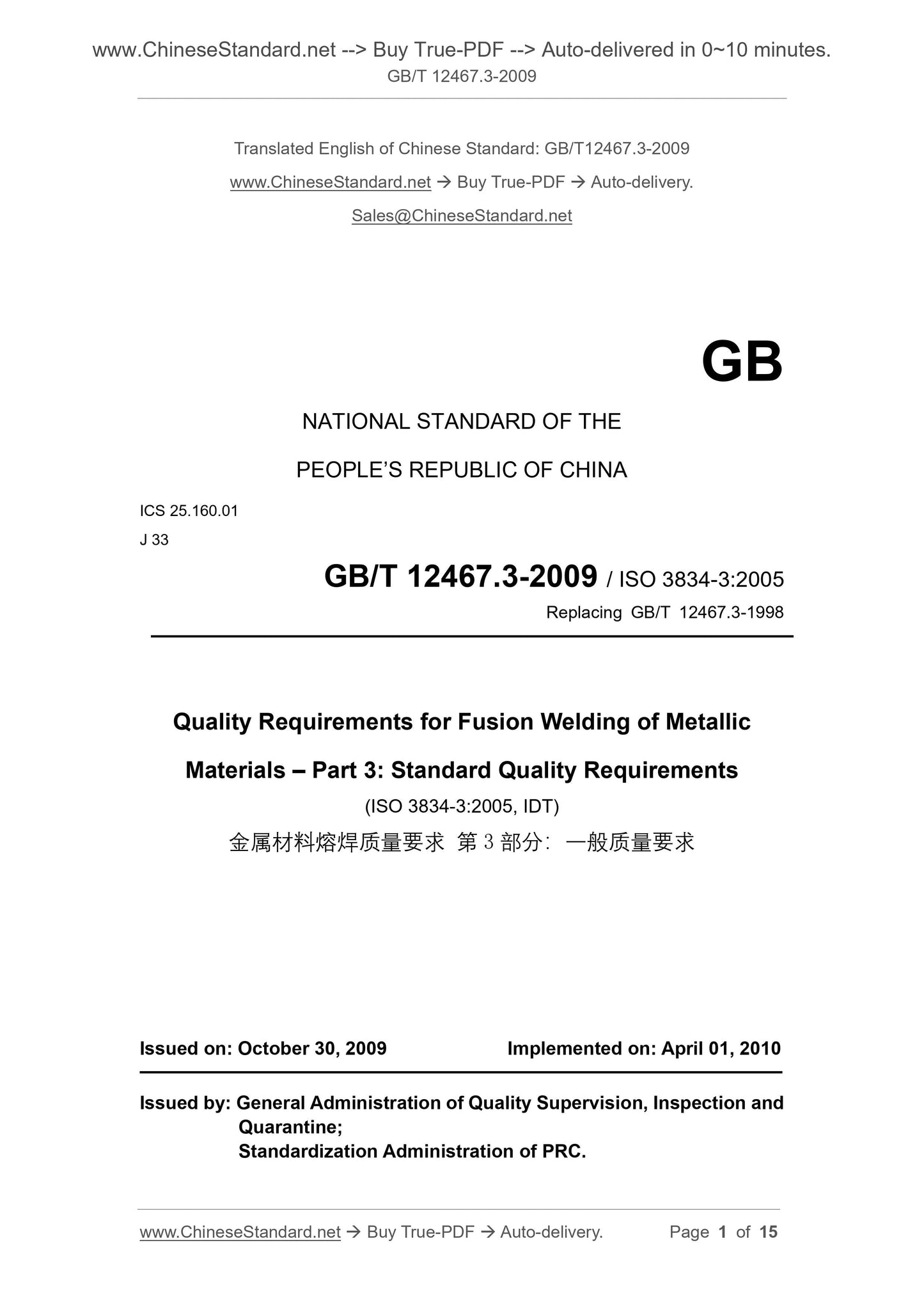
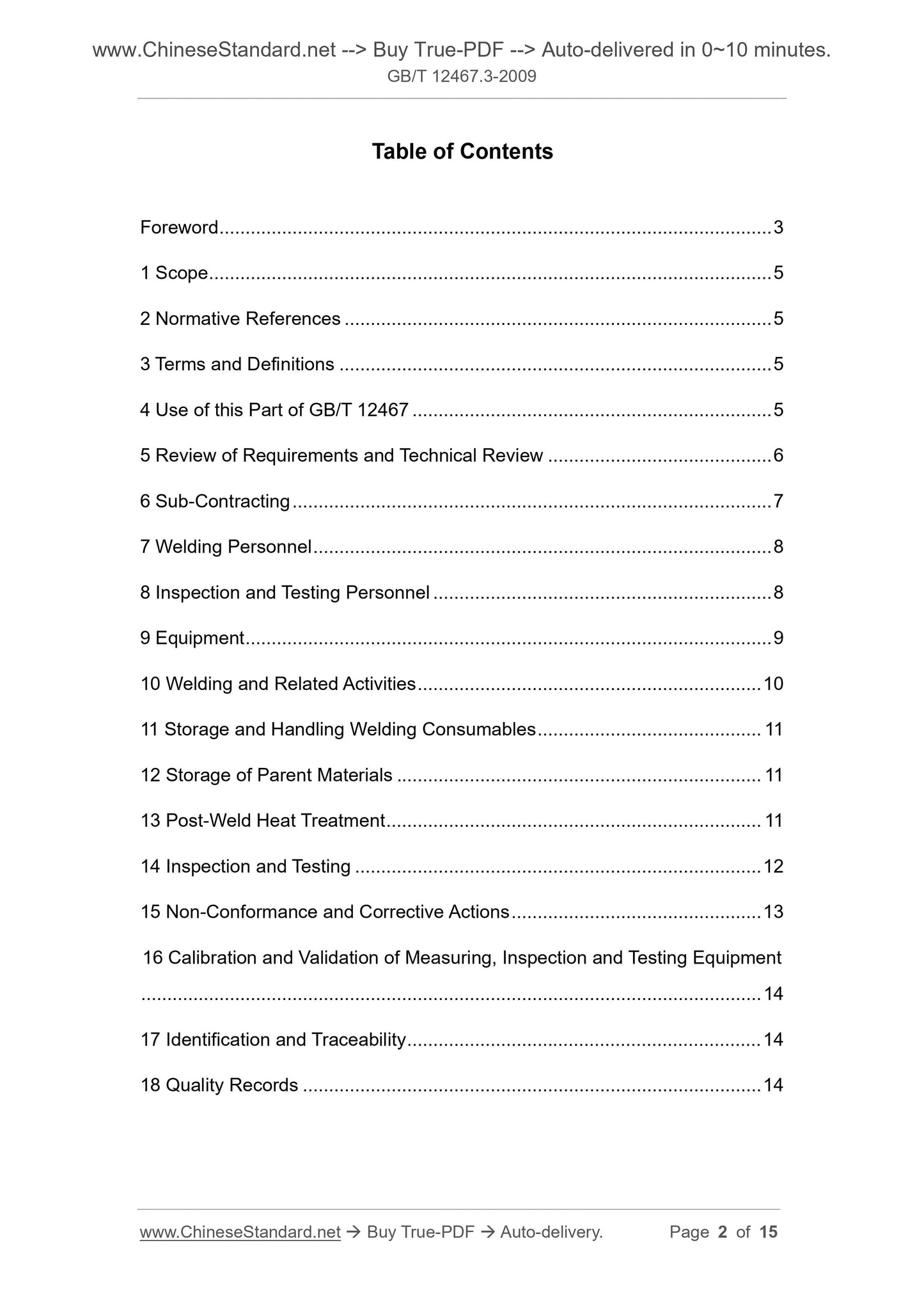
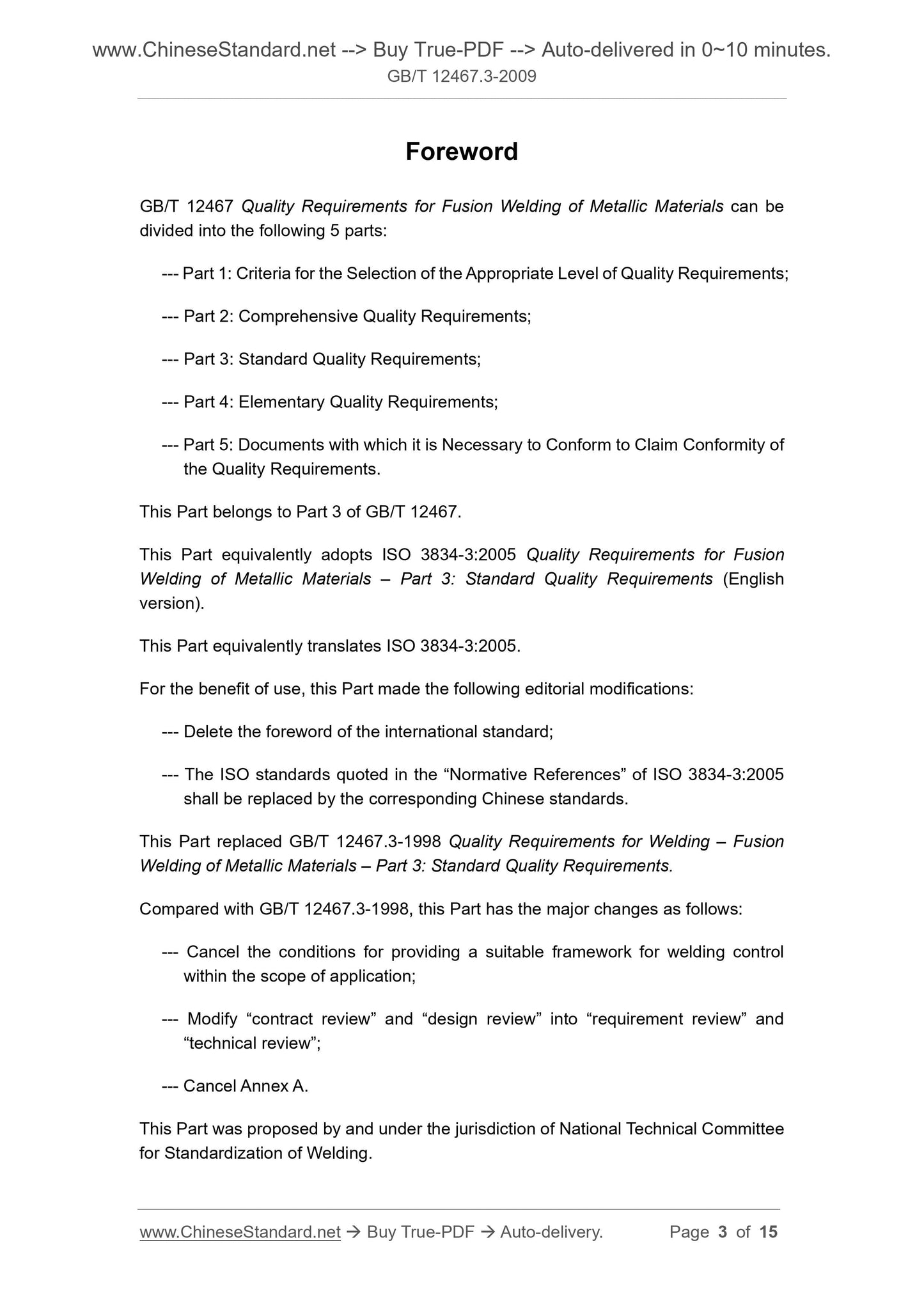
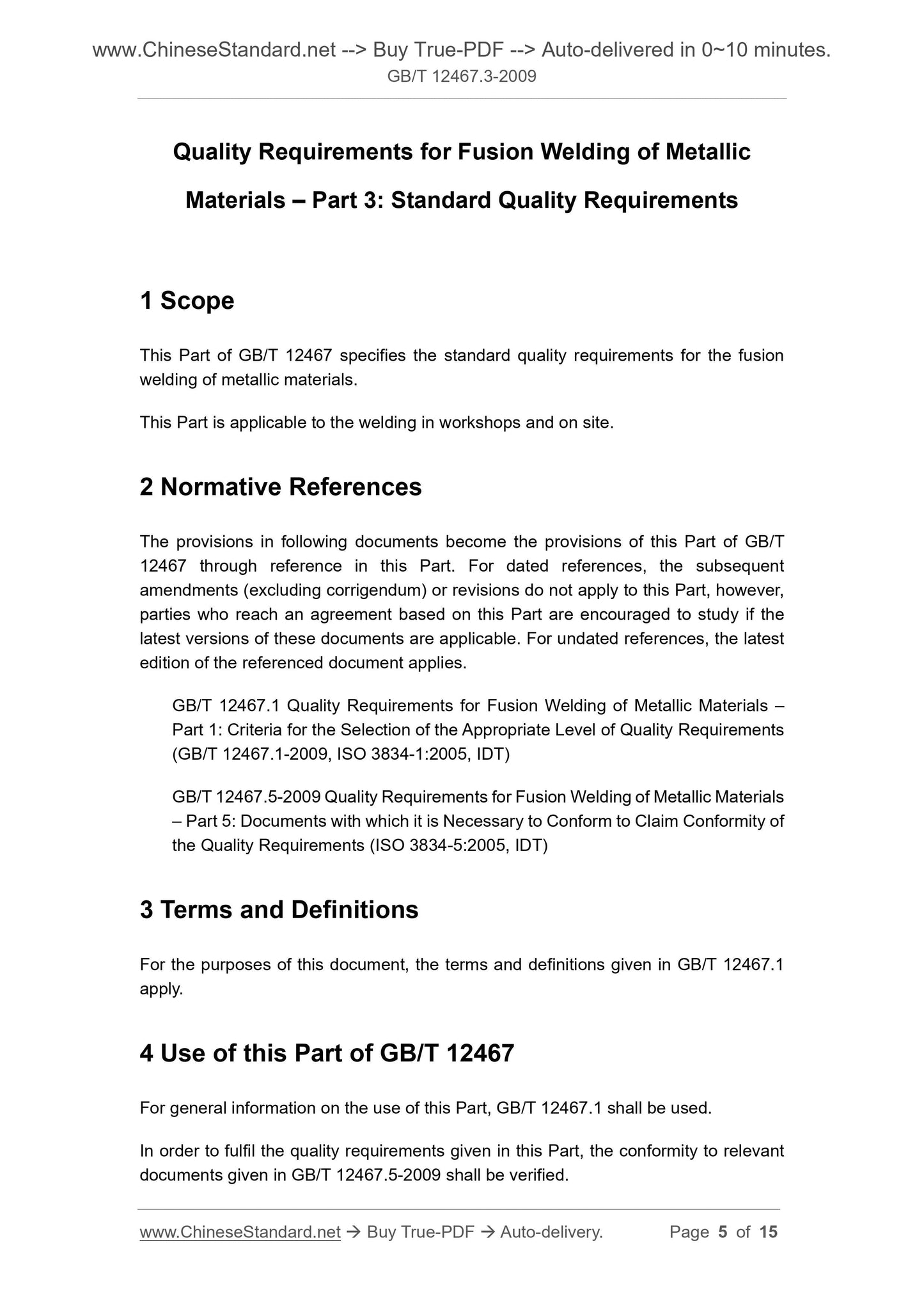