1
/
of
12
www.ChineseStandard.us -- Field Test Asia Pte. Ltd.
GB/T 11982.1-2015 English PDF (GB/T11982.1-2015)
GB/T 11982.1-2015 English PDF (GB/T11982.1-2015)
Regular price
$270.00
Regular price
Sale price
$270.00
Unit price
/
per
Shipping calculated at checkout.
Couldn't load pickup availability
GB/T 11982.1-2015: Polyvinyl chloride floor coverings - Part 1: Heterogeneous polyvinyl chloride floor coverings
Delivery: 9 seconds. Download (and Email) true-PDF + Invoice.
Get Quotation: Click GB/T 11982.1-2015 (Self-service in 1-minute)
Newer / historical versions: GB/T 11982.1-2015
Preview True-PDF (Reload/Scroll-down if blank)
Delivery: 9 seconds. Download (and Email) true-PDF + Invoice.
Get Quotation: Click GB/T 11982.1-2015 (Self-service in 1-minute)
Newer / historical versions: GB/T 11982.1-2015
Preview True-PDF (Reload/Scroll-down if blank)
Share
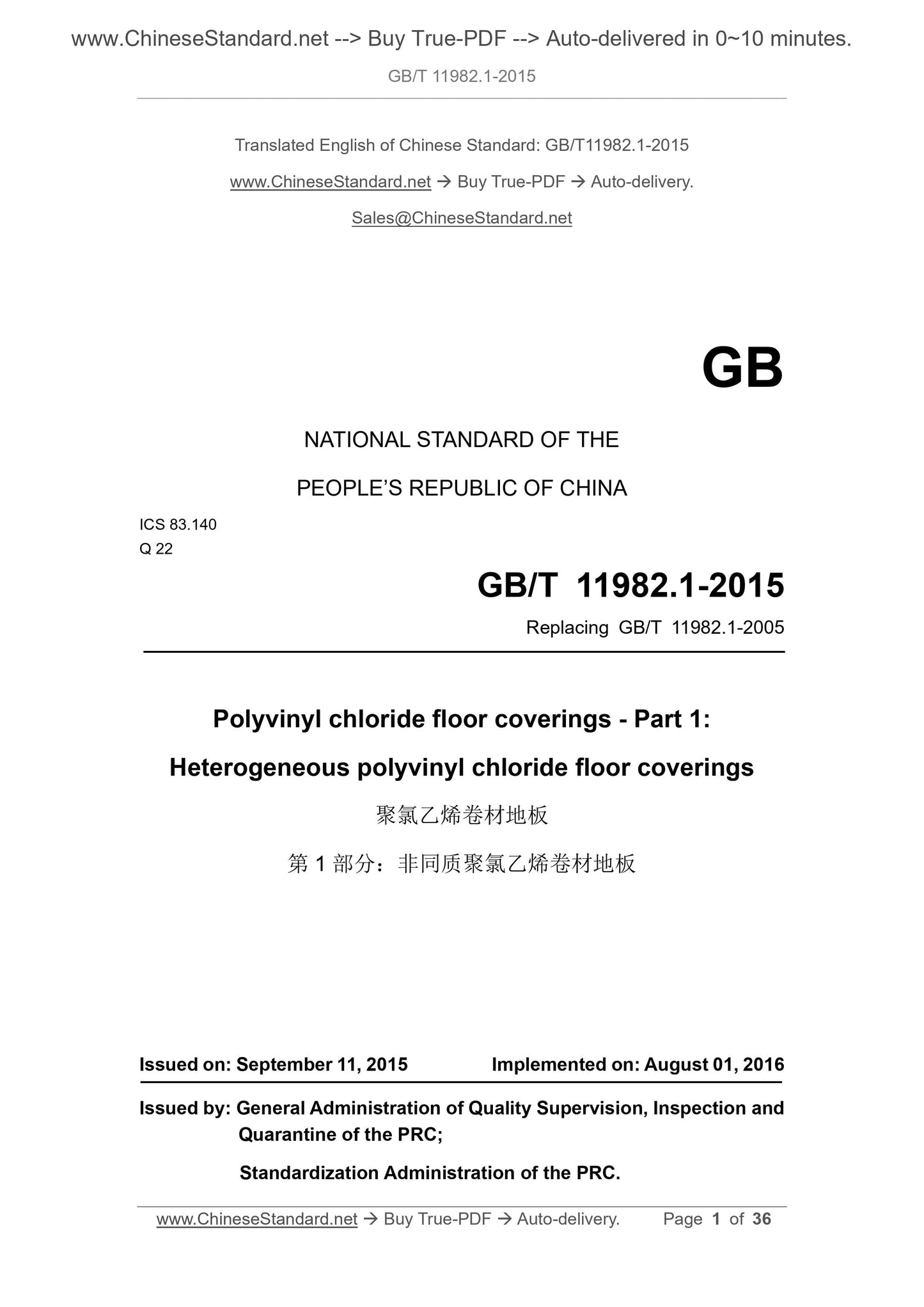
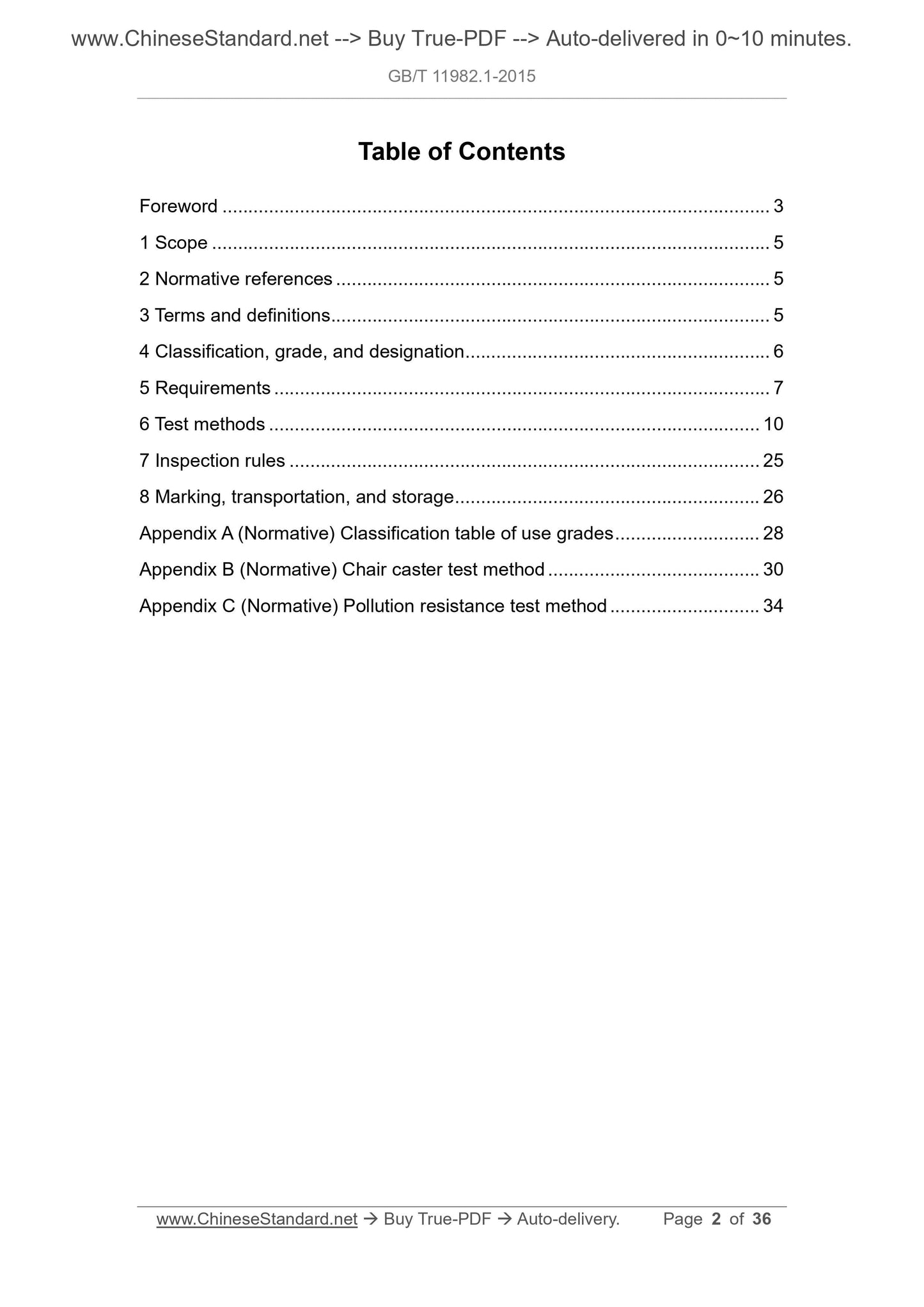
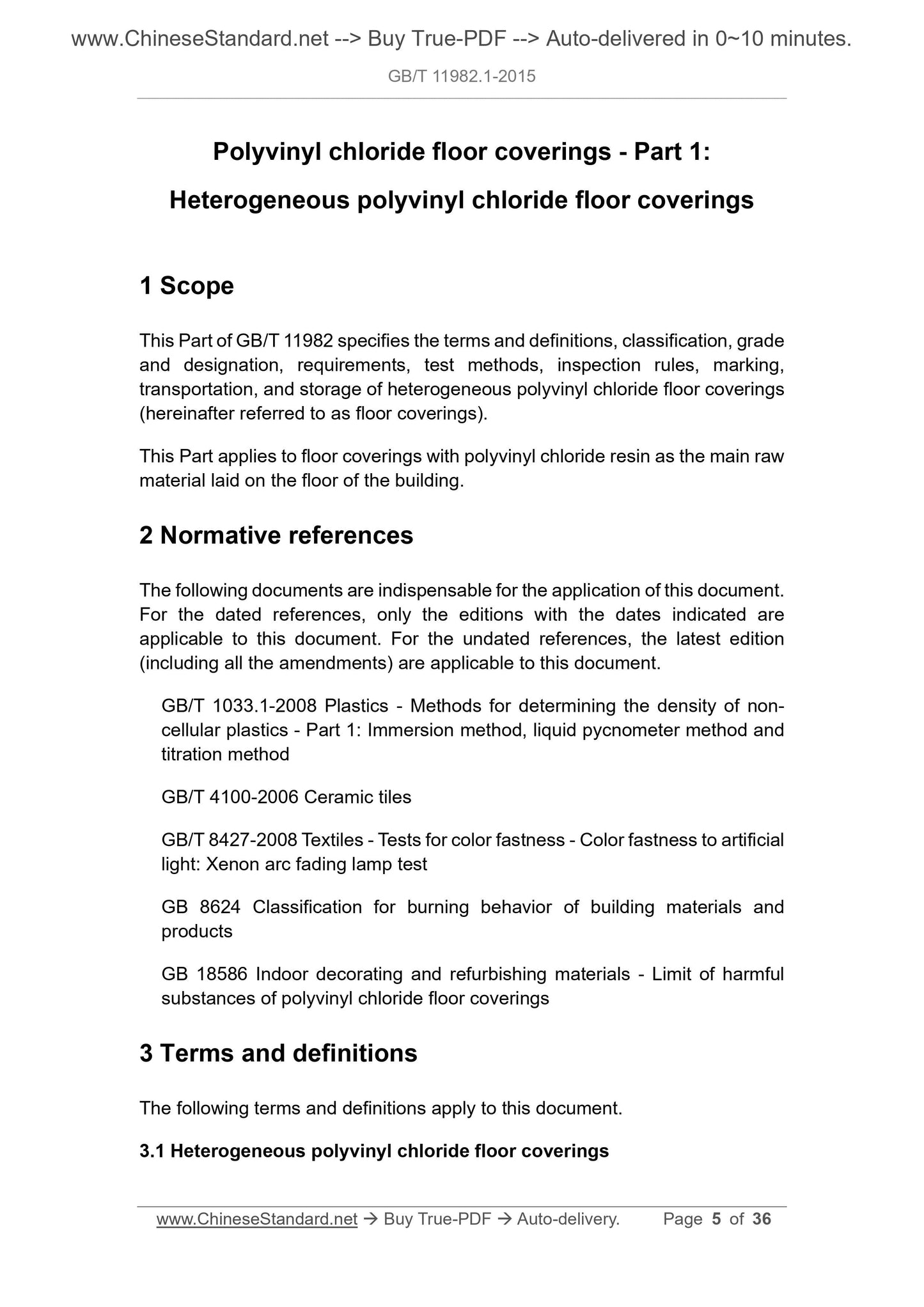
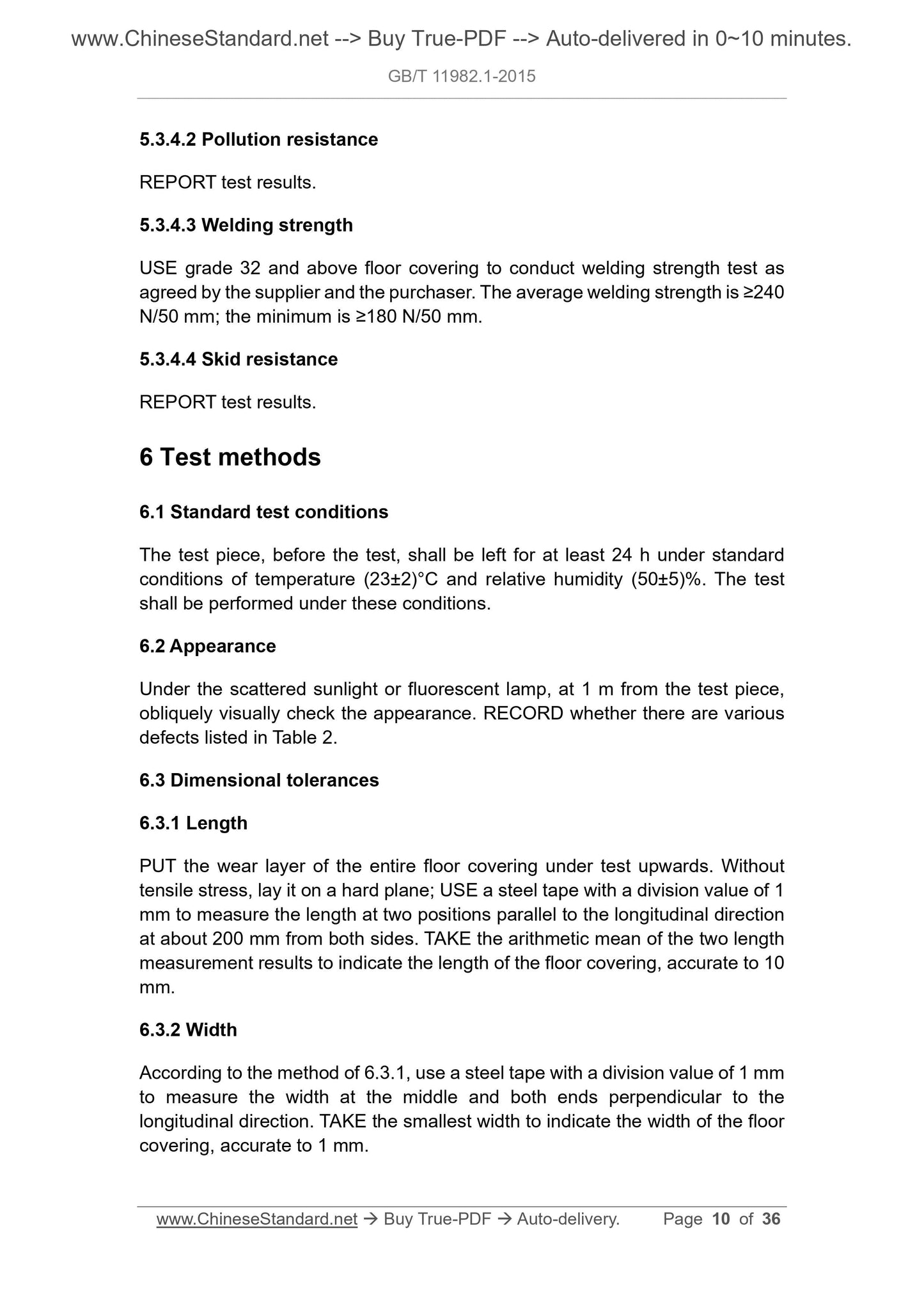
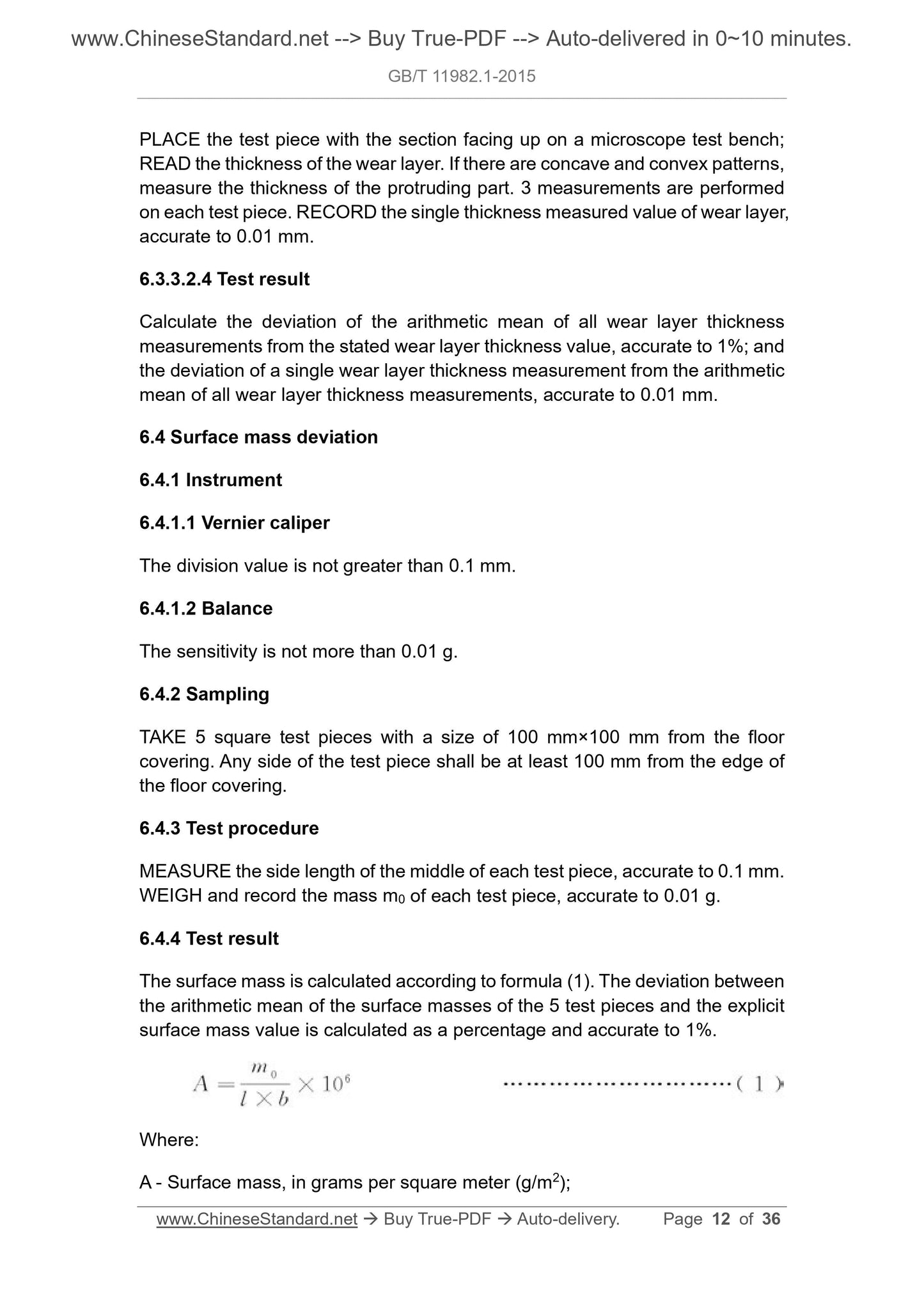
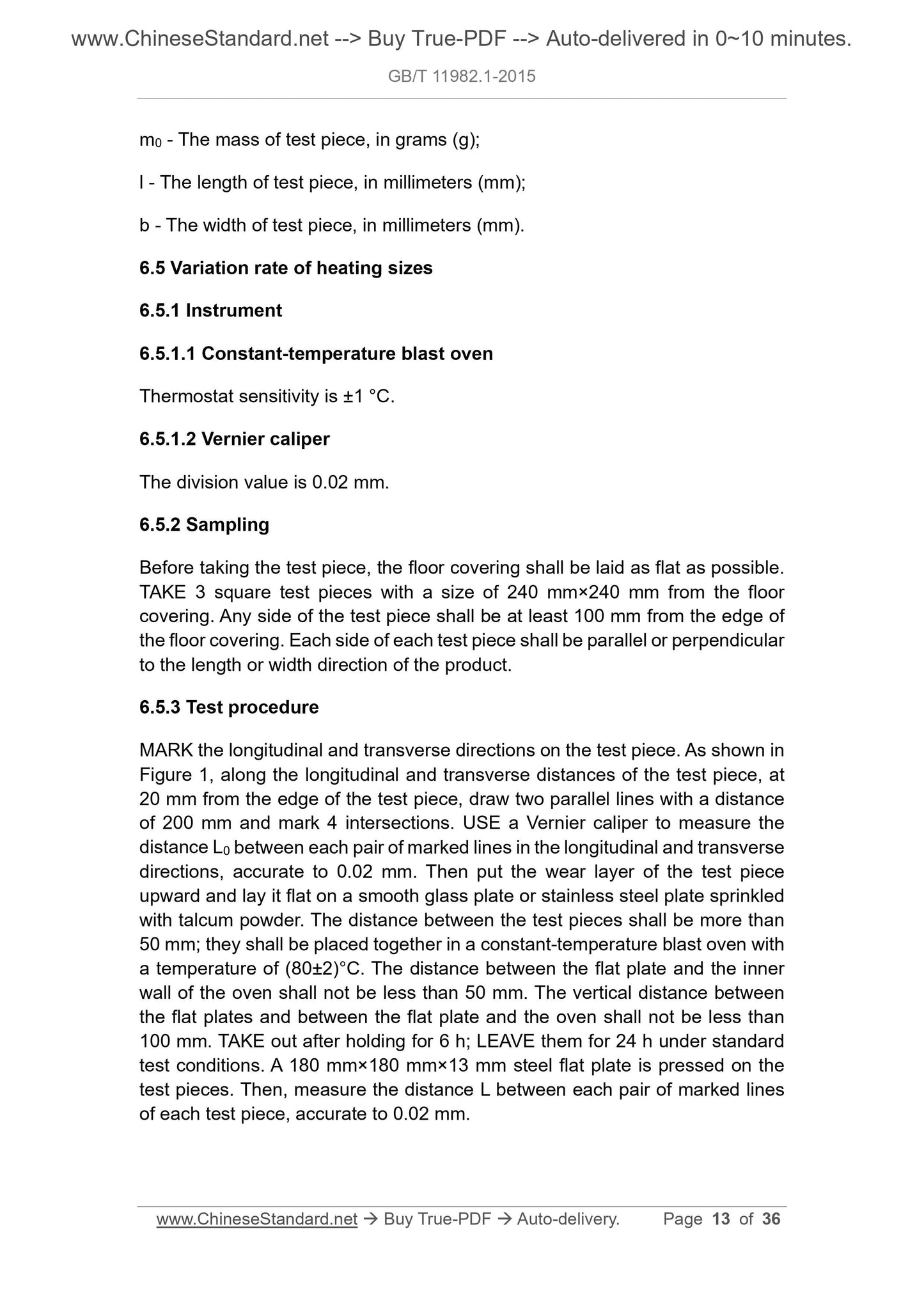
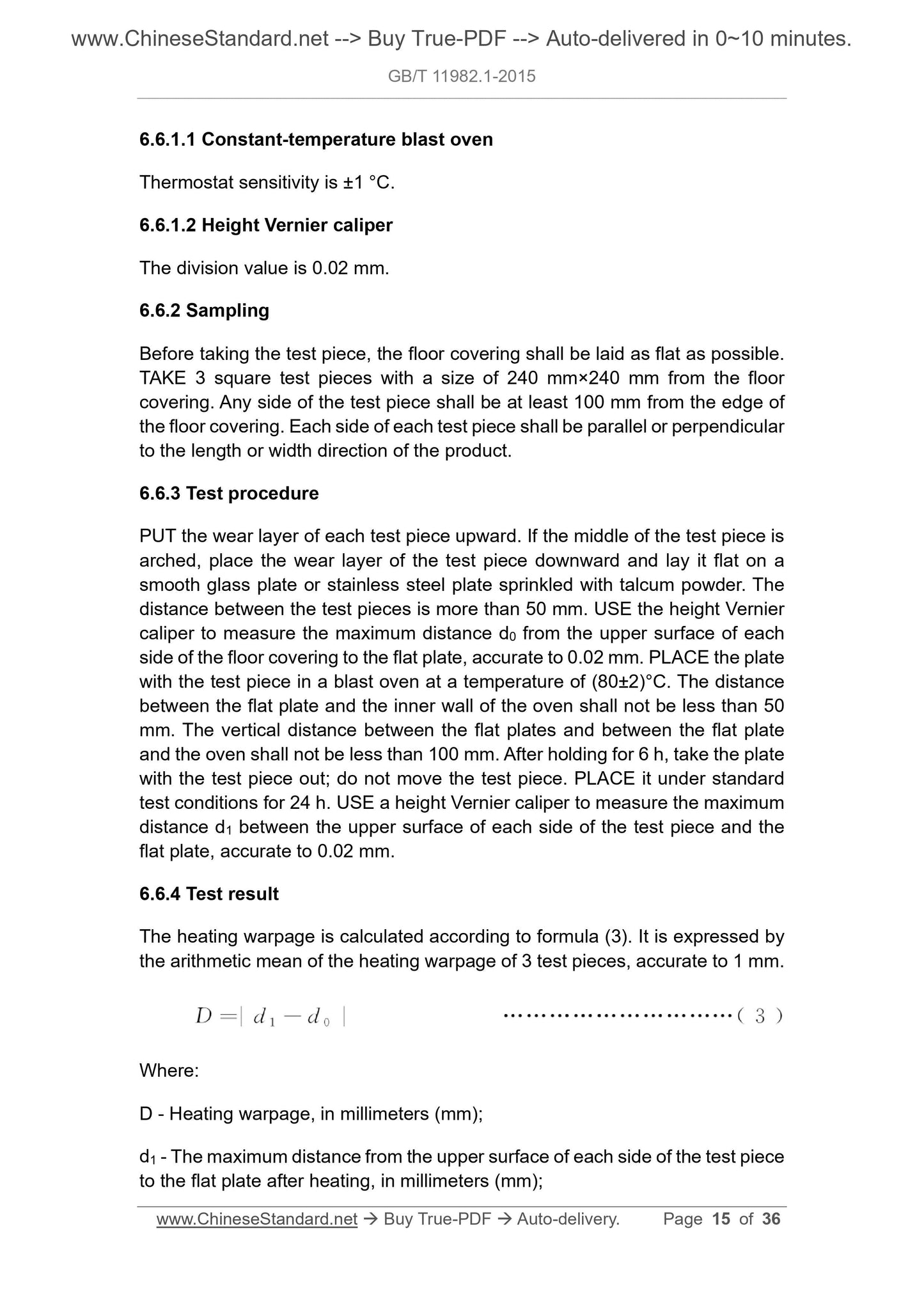
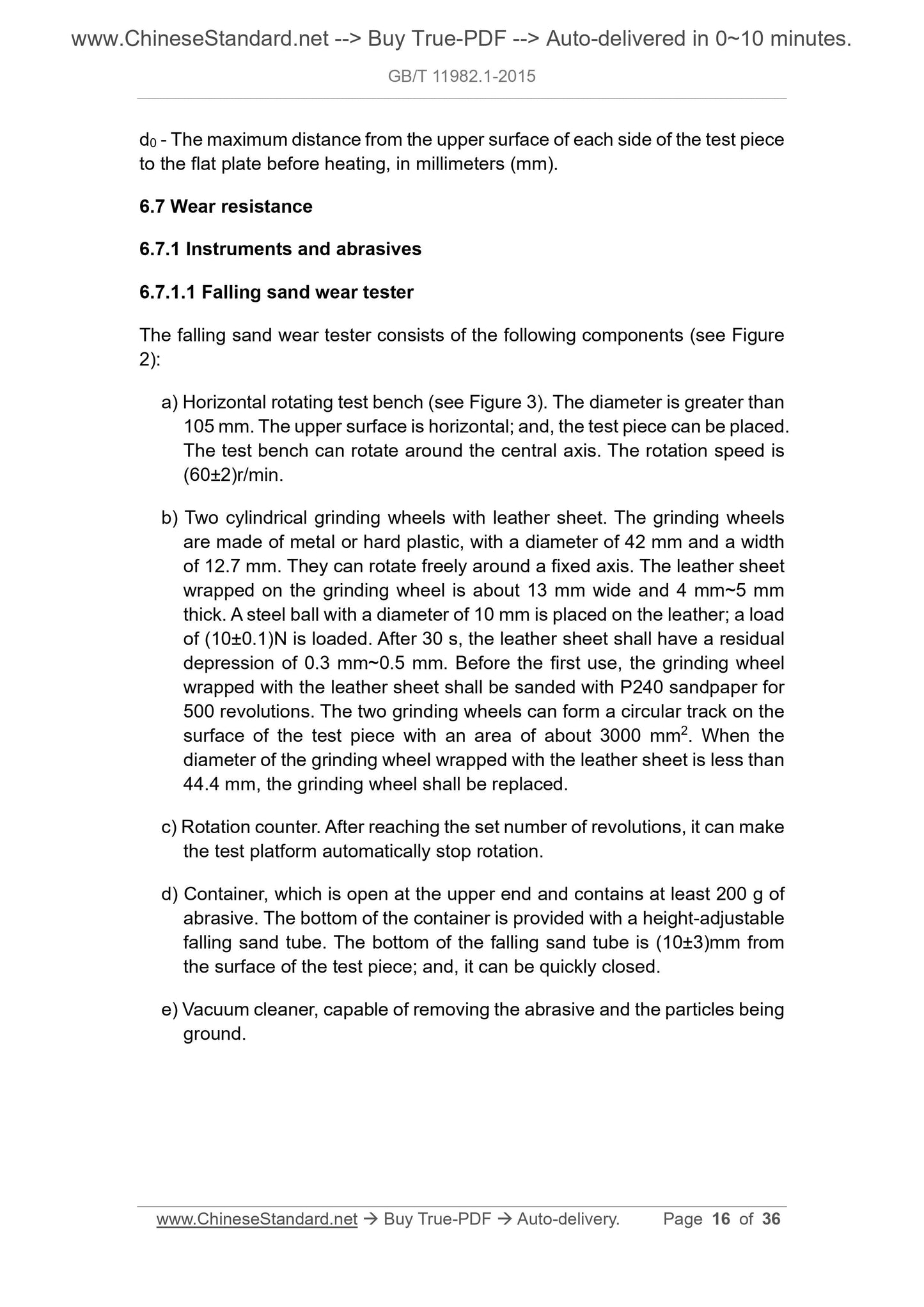
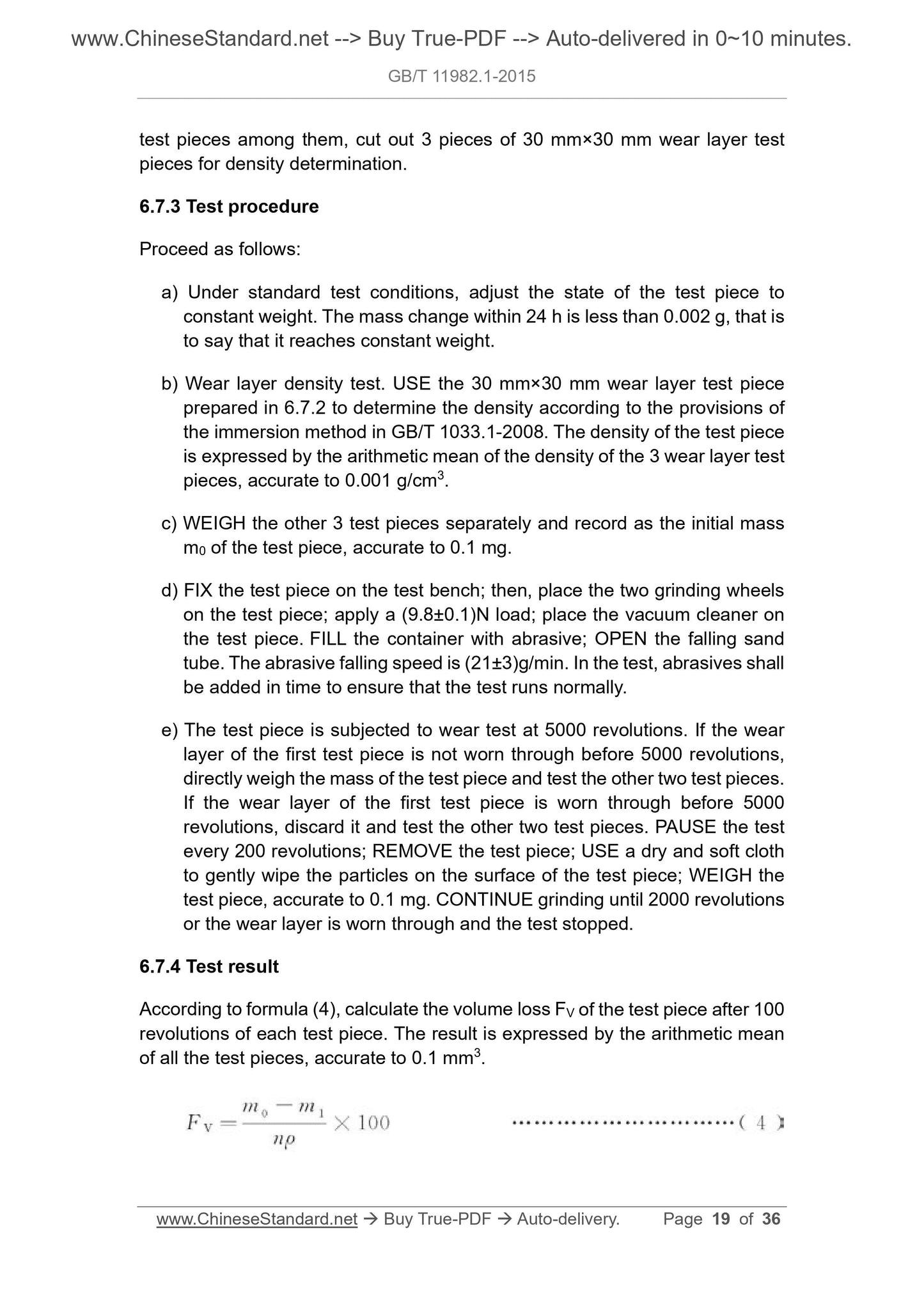
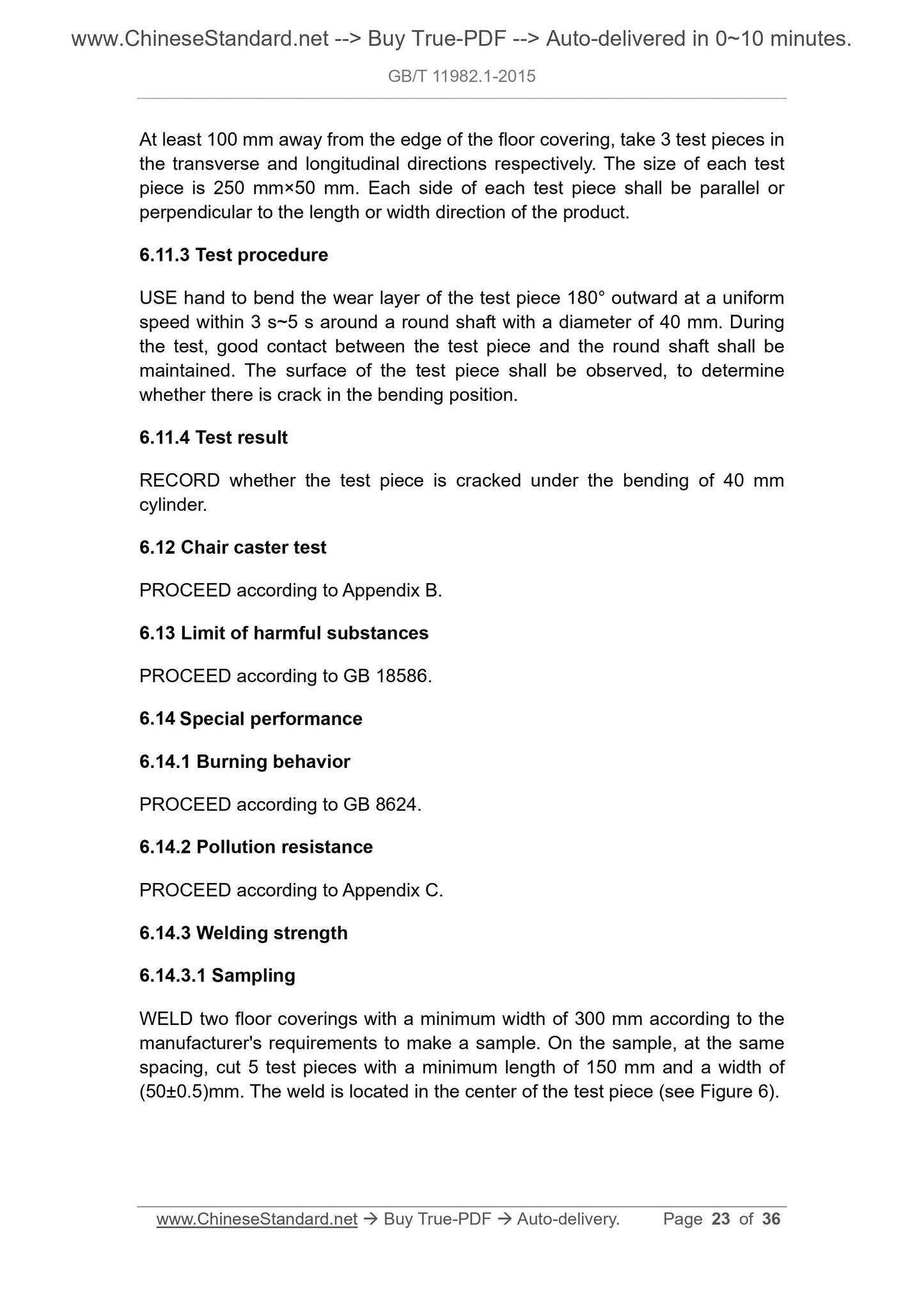
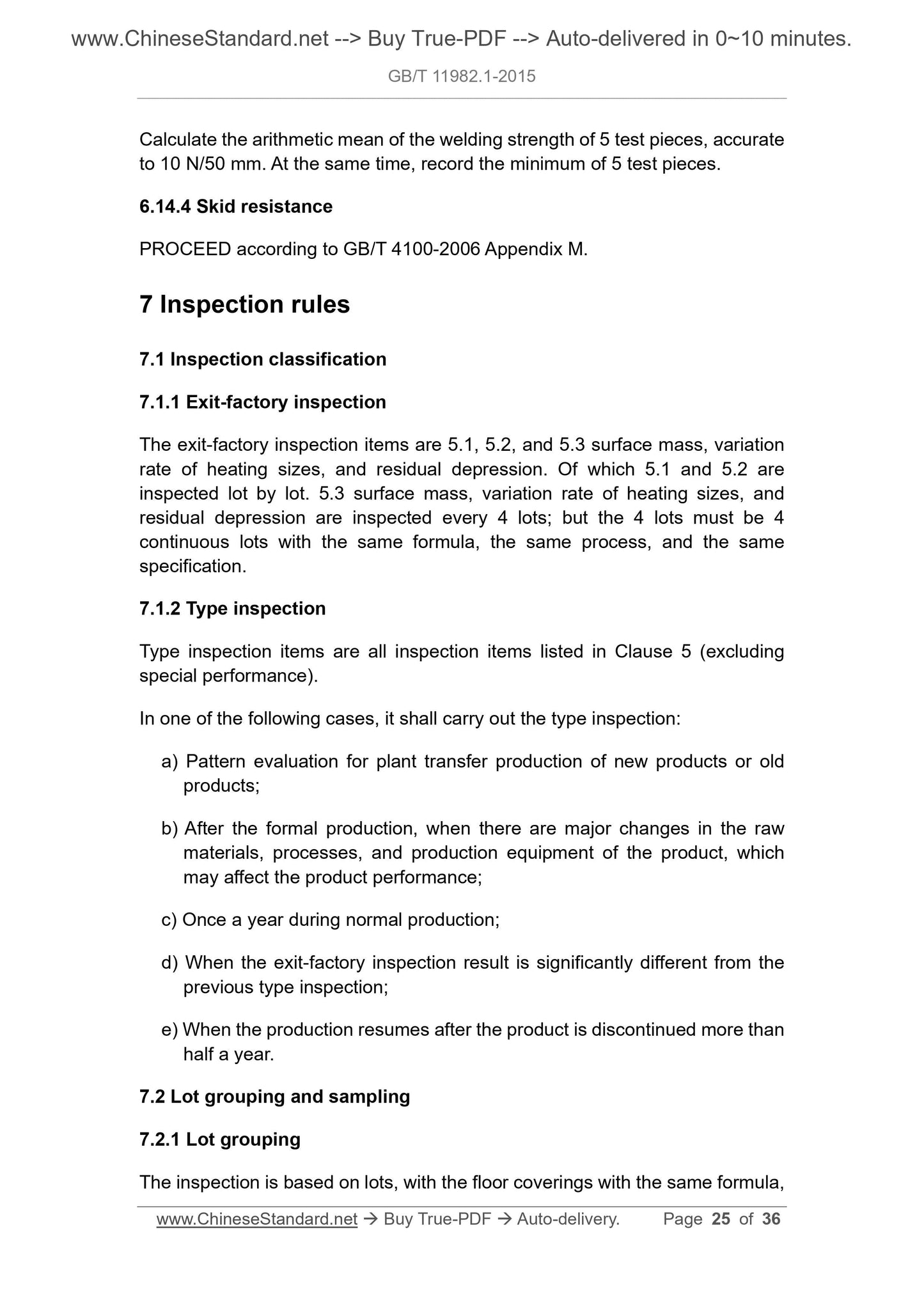
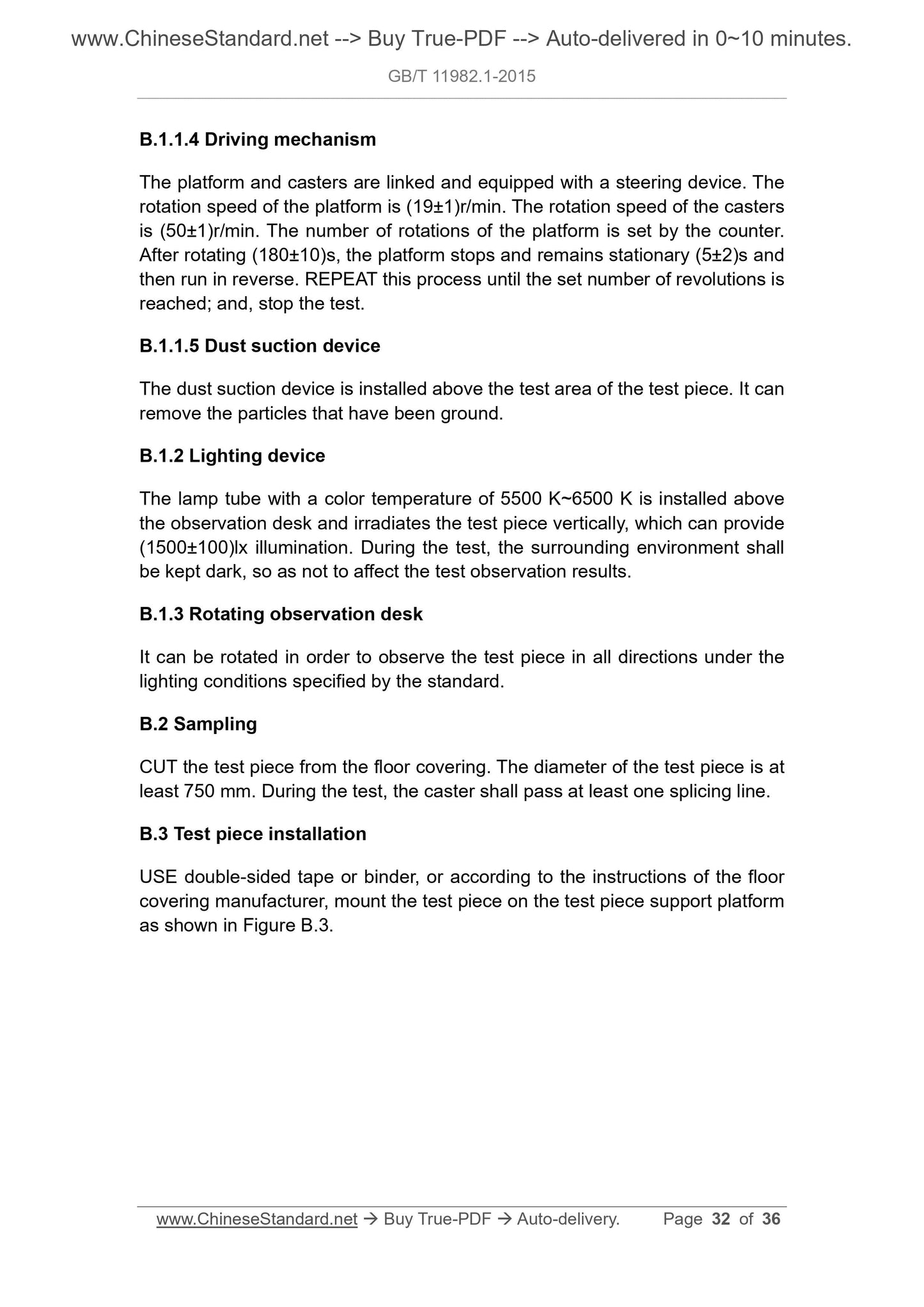