1
/
of
9
PayPal, credit cards. Download editable-PDF and invoice in 1 second!
GB/T 10322.1-2014 English PDF (GB/T10322.1-2014)
GB/T 10322.1-2014 English PDF (GB/T10322.1-2014)
Regular price
$995.00
Regular price
Sale price
$995.00
Unit price
/
per
Shipping calculated at checkout.
Couldn't load pickup availability
GB/T 10322.1-2014: Iron ores -- Sampling and sample preparation procedures
Delivery: 9 seconds. Download (and Email) true-PDF + Invoice.
Newer version: (Replacing this standard) GB/T 10322.1-2023
Get Quotation: Click GB/T 10322.1-2014 (Self-service in 1-minute)
Newer / historical versions: GB/T 10322.1-2023
Preview True-PDF (Reload/Scroll-down if blank)
Delivery: 9 seconds. Download (and Email) true-PDF + Invoice.
Newer version: (Replacing this standard) GB/T 10322.1-2023
Get Quotation: Click GB/T 10322.1-2014 (Self-service in 1-minute)
Newer / historical versions: GB/T 10322.1-2023
Preview True-PDF (Reload/Scroll-down if blank)
Share
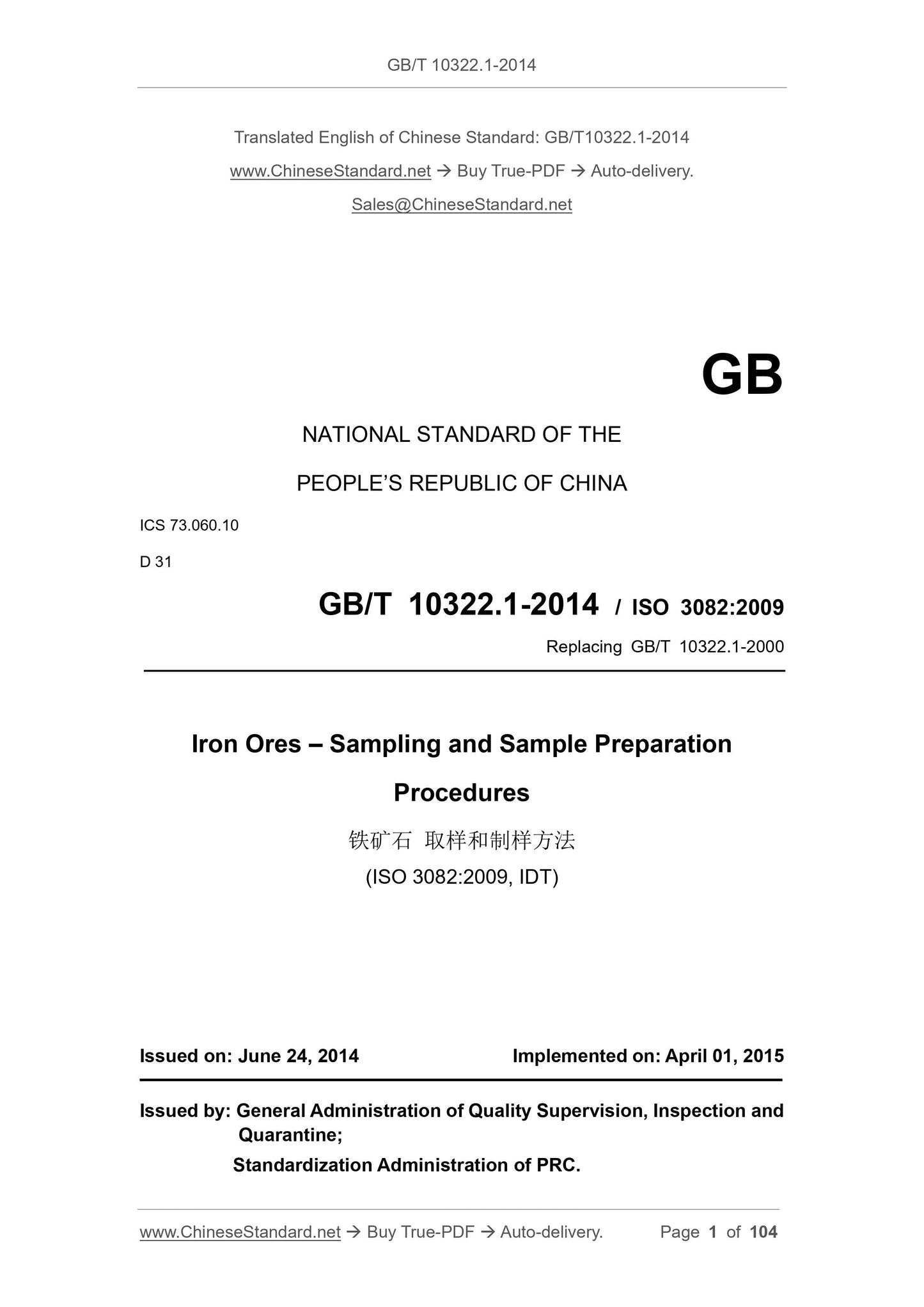
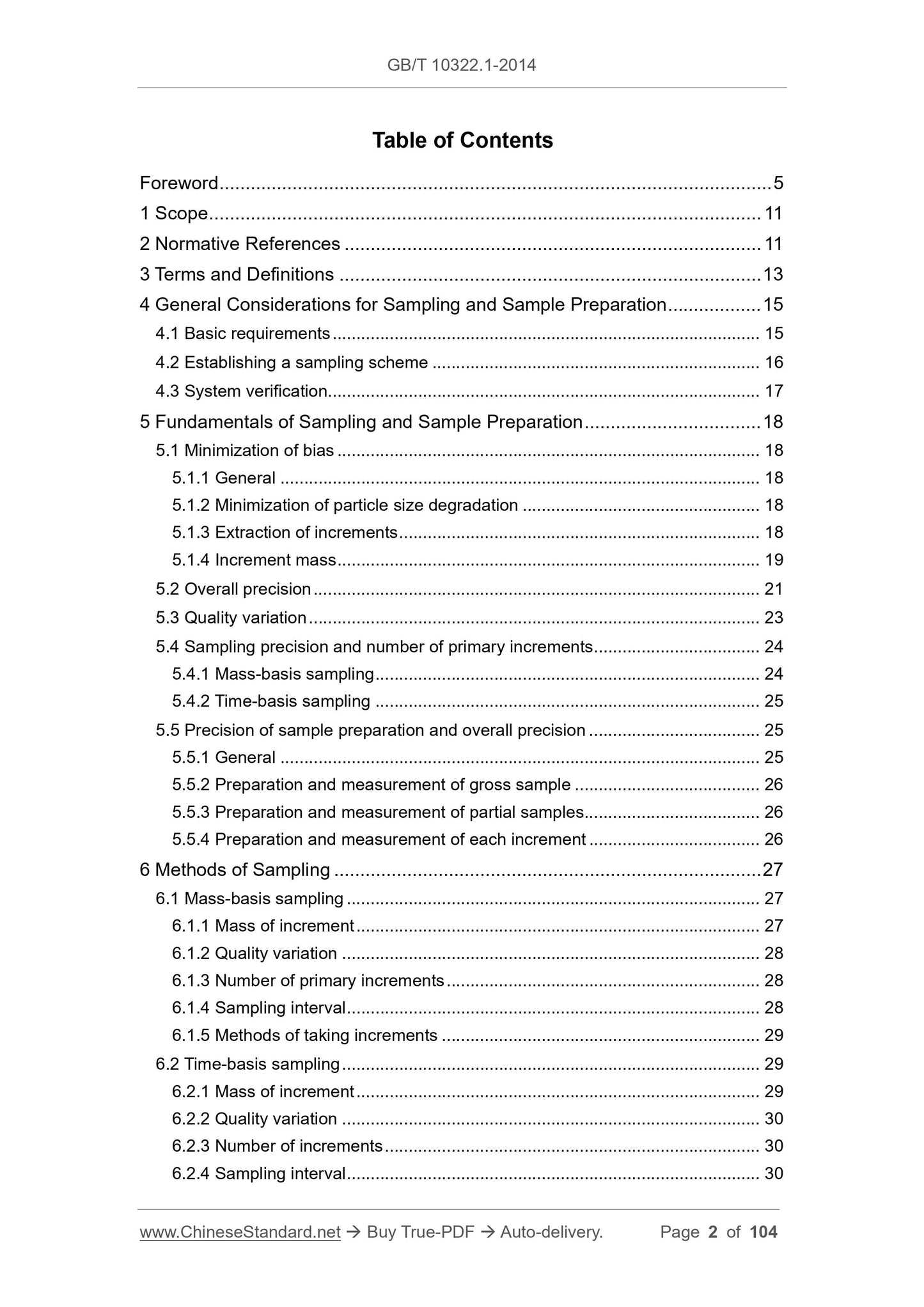
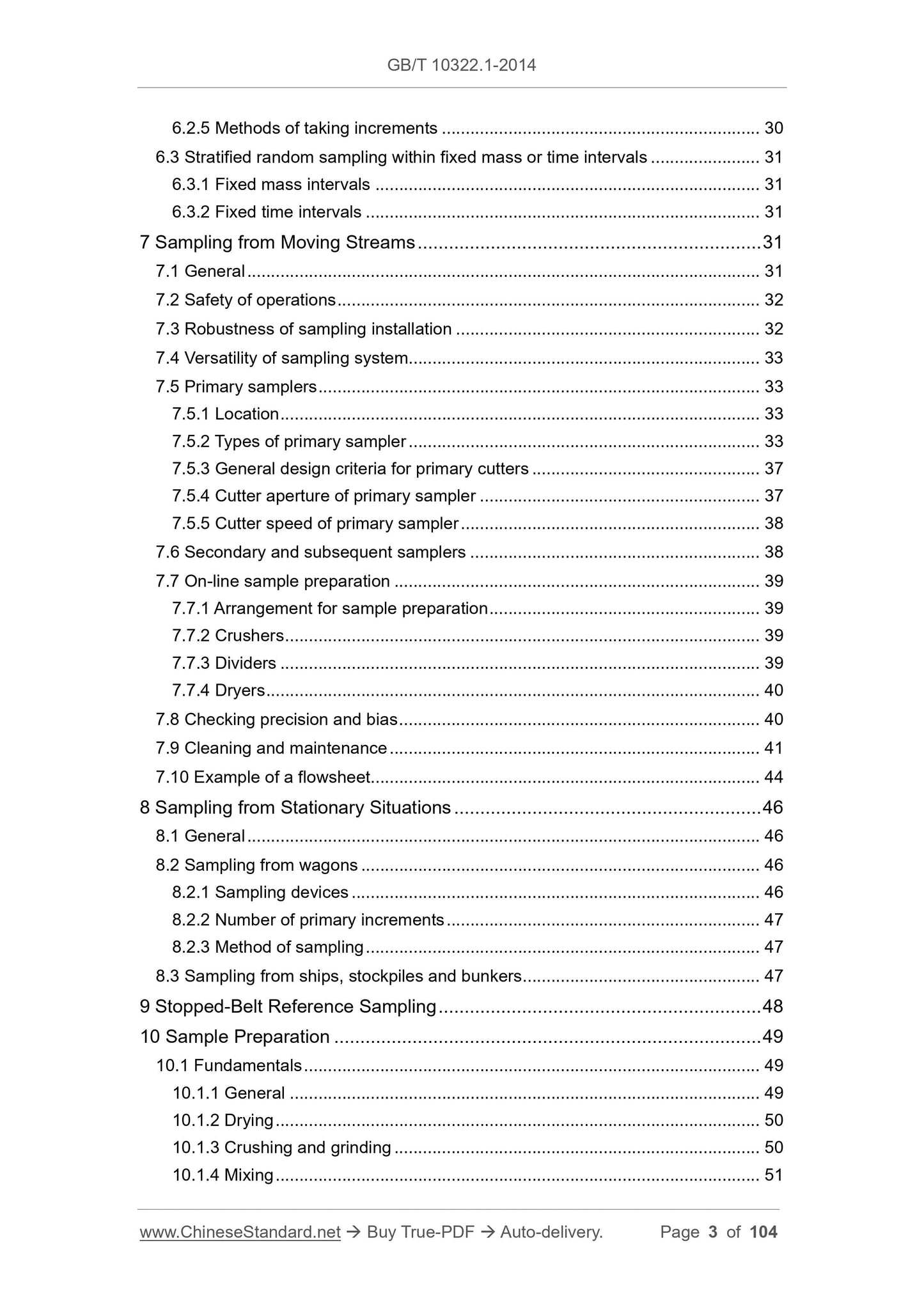
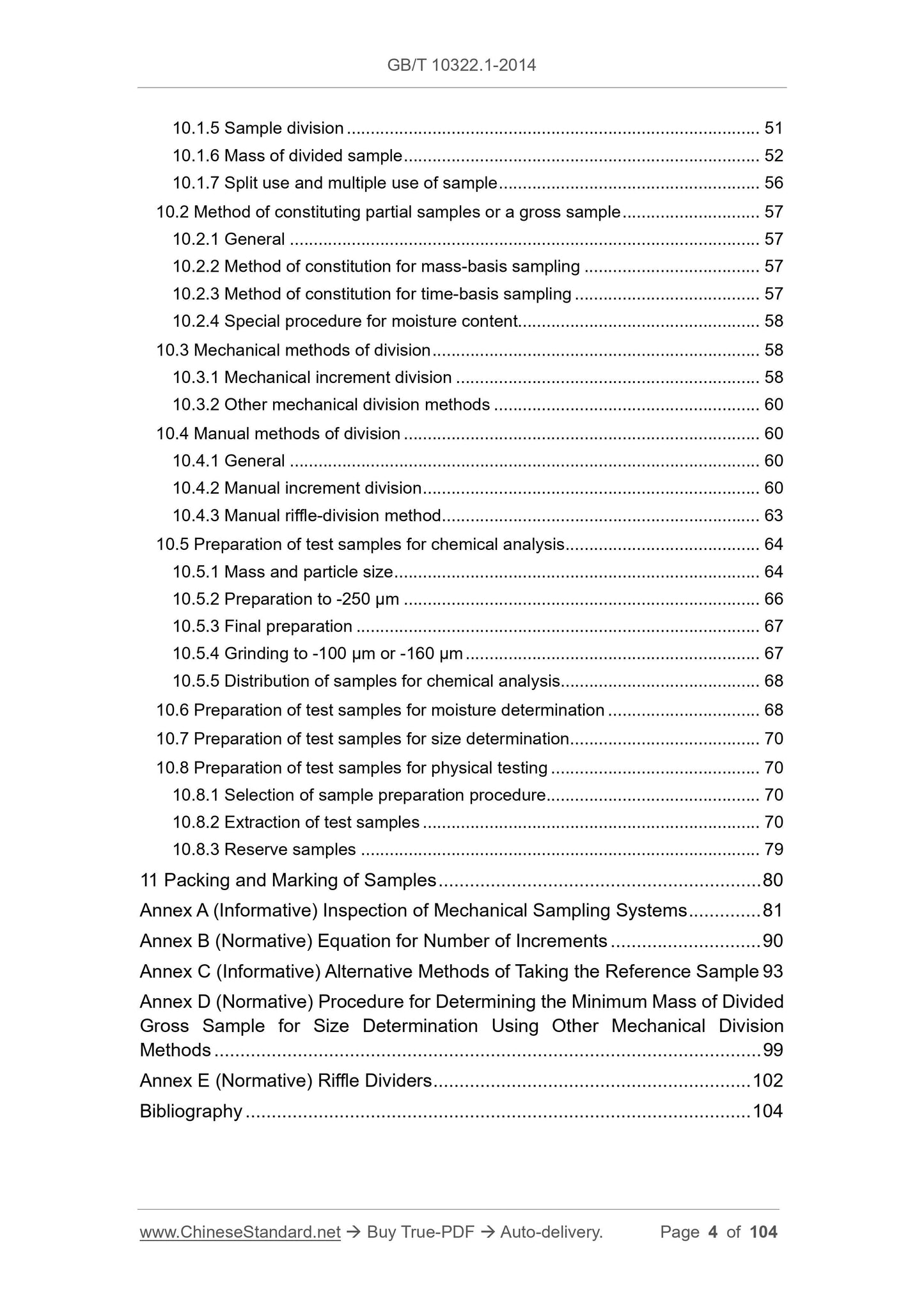
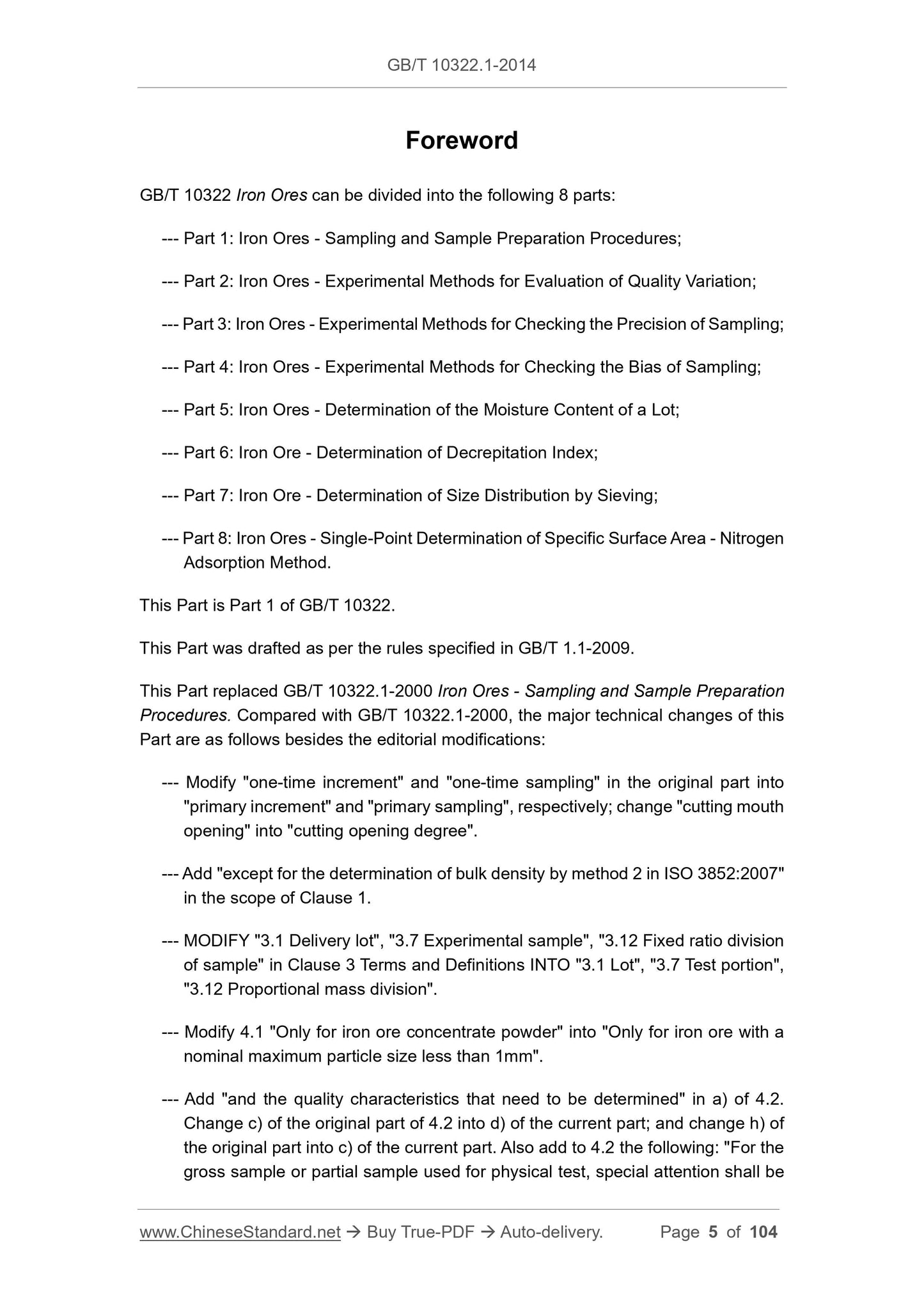
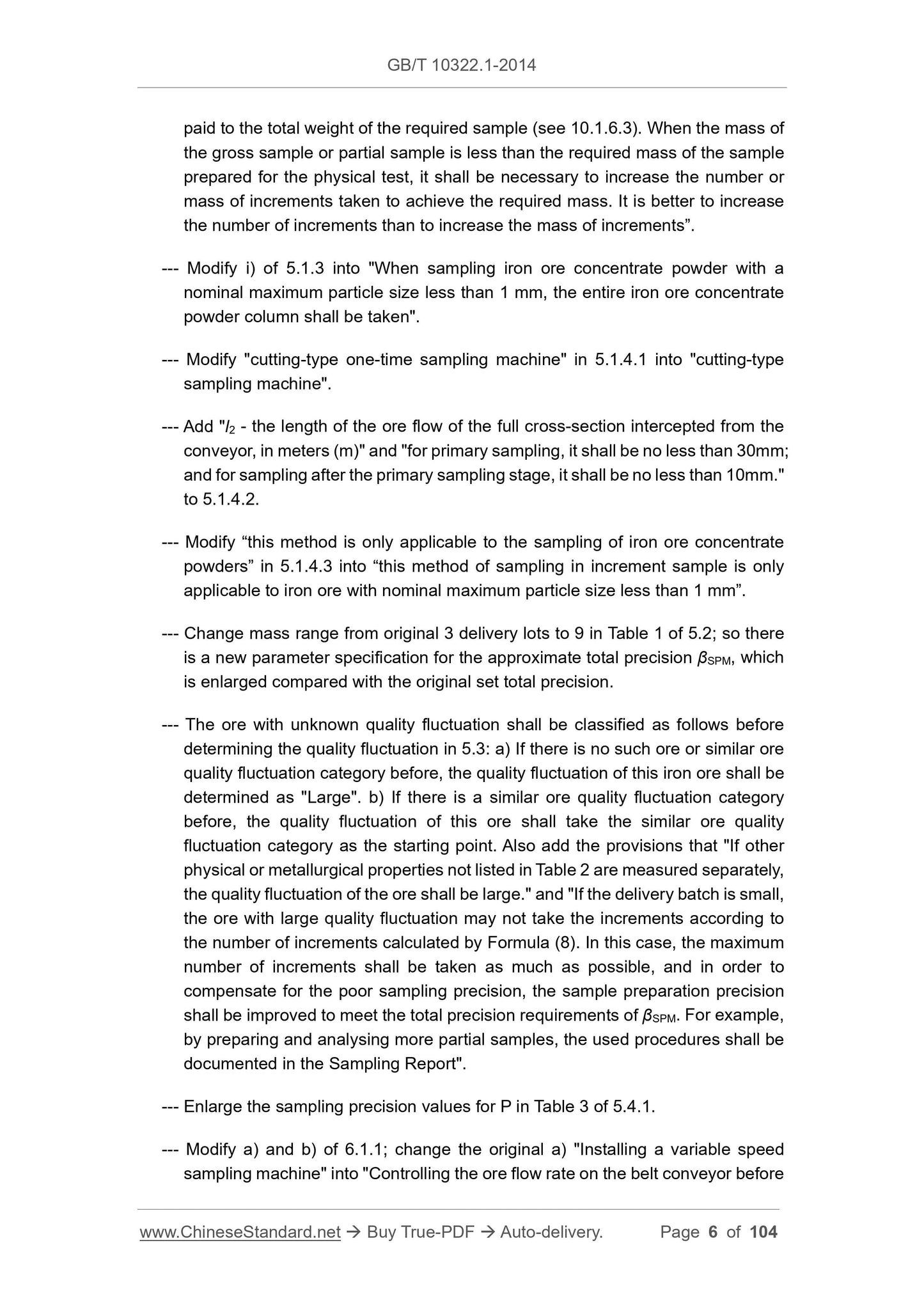
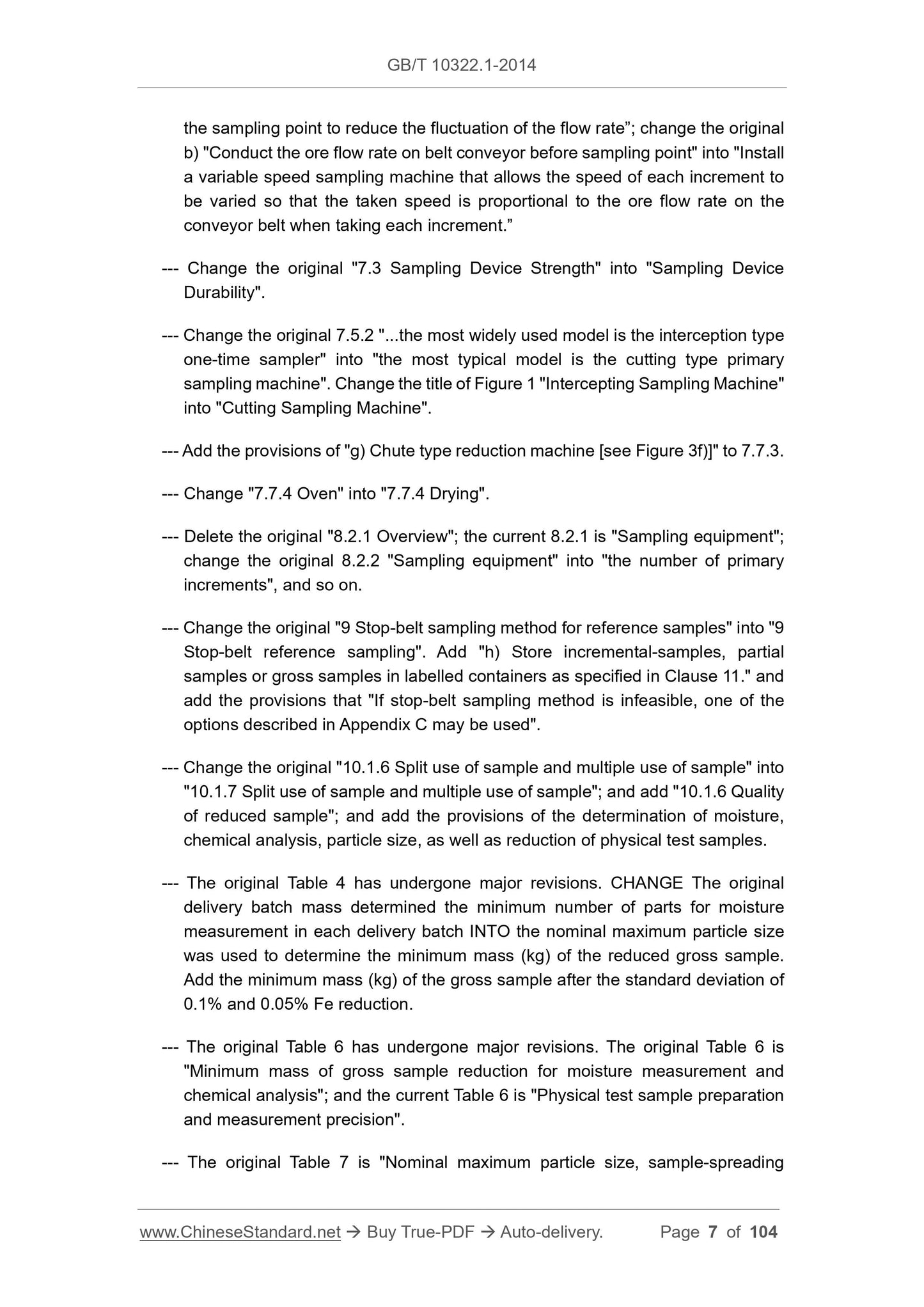
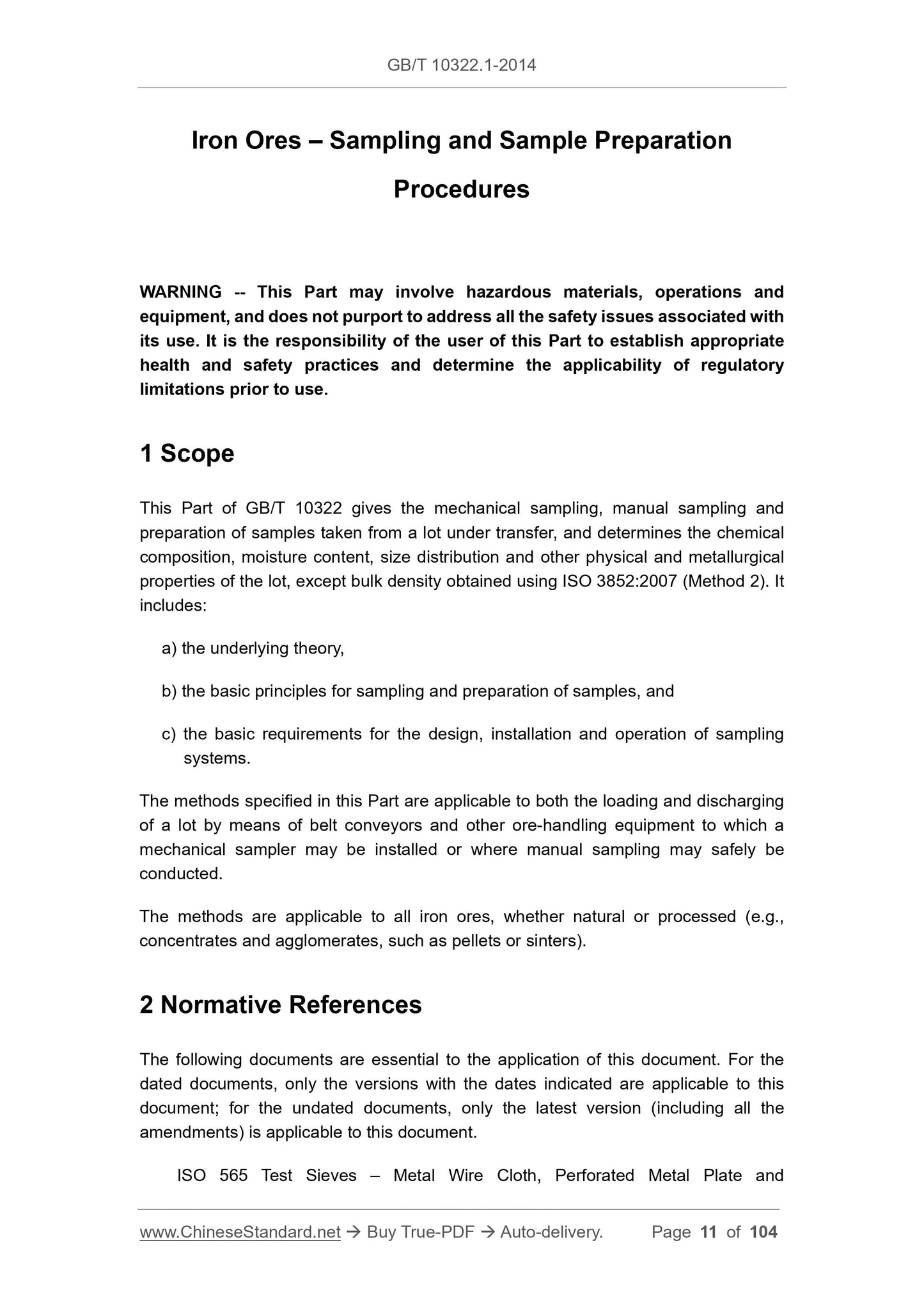
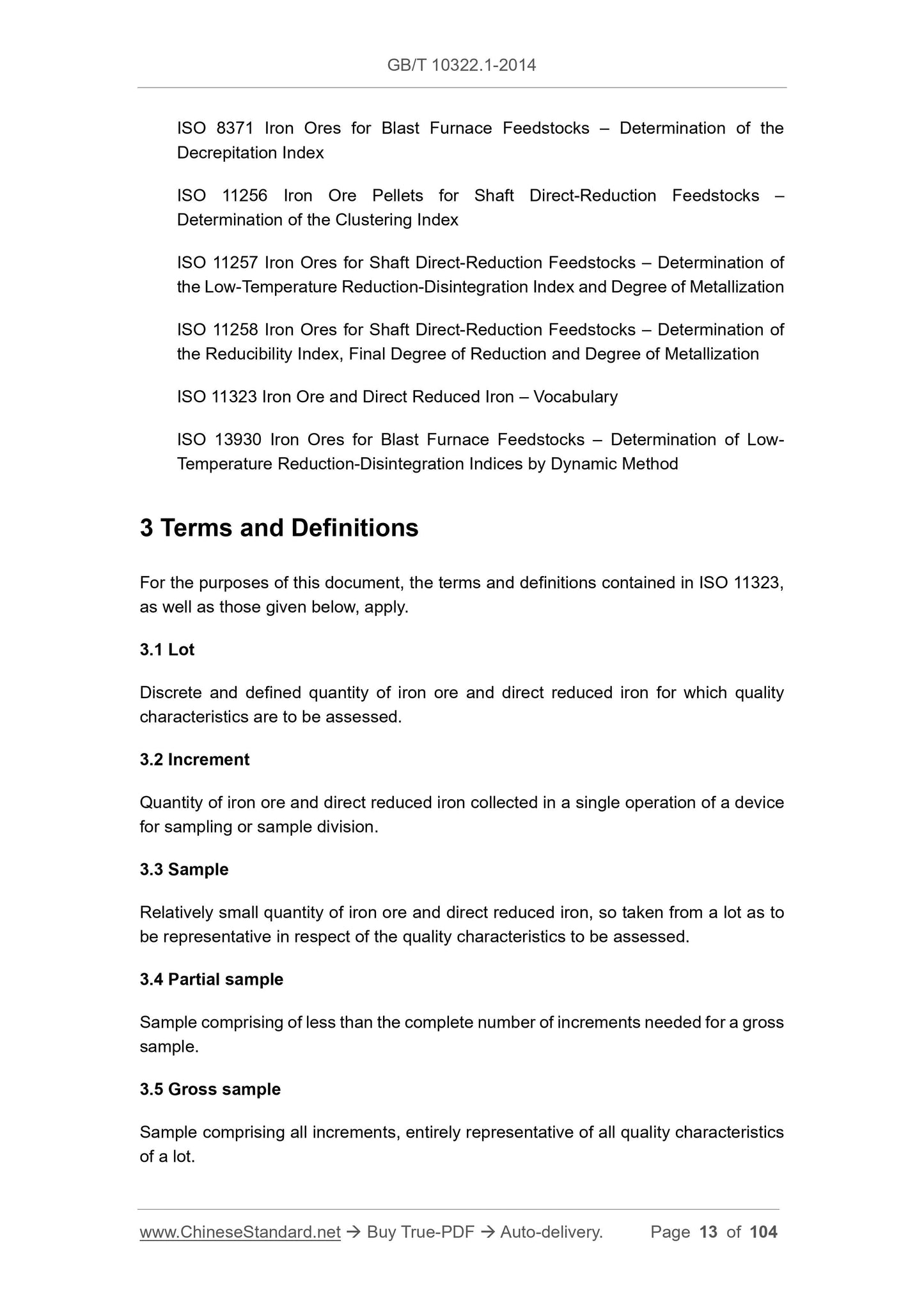