1
/
of
12
www.ChineseStandard.us -- Field Test Asia Pte. Ltd.
GB 50461-2008 English PDF
GB 50461-2008 English PDF
Regular price
$505.00
Regular price
Sale price
$505.00
Unit price
/
per
Shipping calculated at checkout.
Couldn't load pickup availability
GB 50461-2008: Code for quality acceptance of static equipment installation in petrochemical engineering
Delivery: 9 seconds. Download (and Email) true-PDF + Invoice.
Get Quotation: Click GB 50461-2008 (Self-service in 1-minute)
Newer / historical versions: GB 50461-2008
Preview True-PDF (Reload/Scroll-down if blank)
Delivery: 9 seconds. Download (and Email) true-PDF + Invoice.
Get Quotation: Click GB 50461-2008 (Self-service in 1-minute)
Newer / historical versions: GB 50461-2008
Preview True-PDF (Reload/Scroll-down if blank)
Share
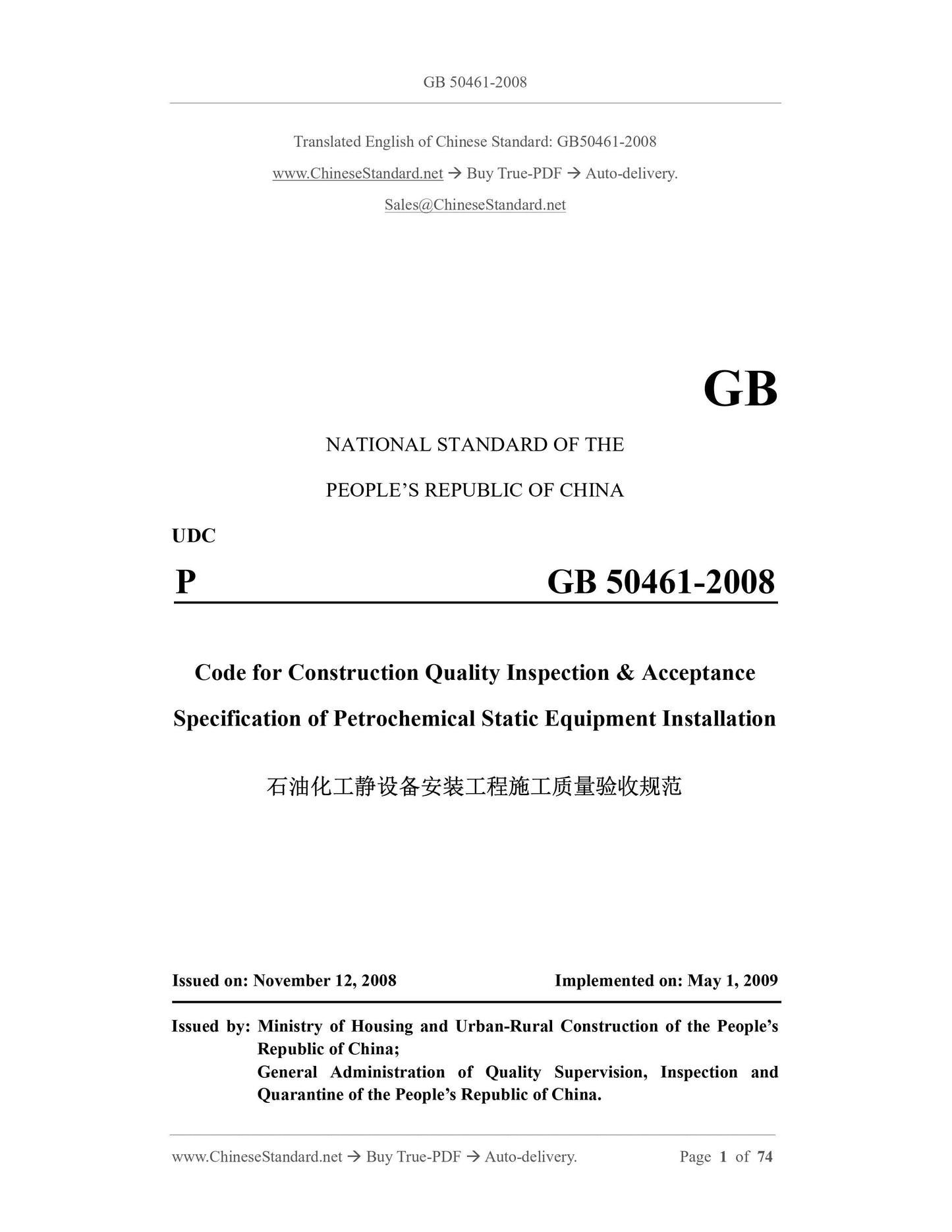
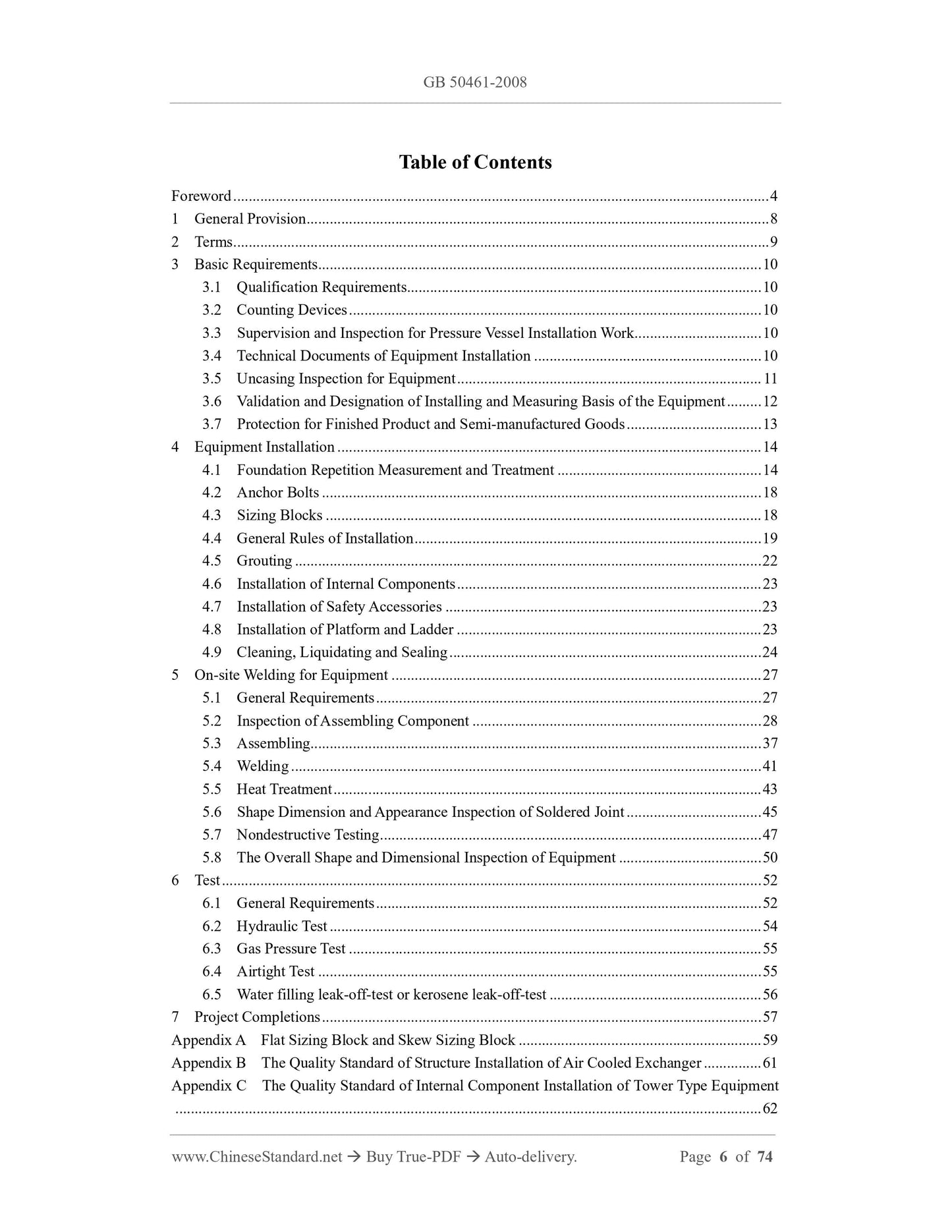
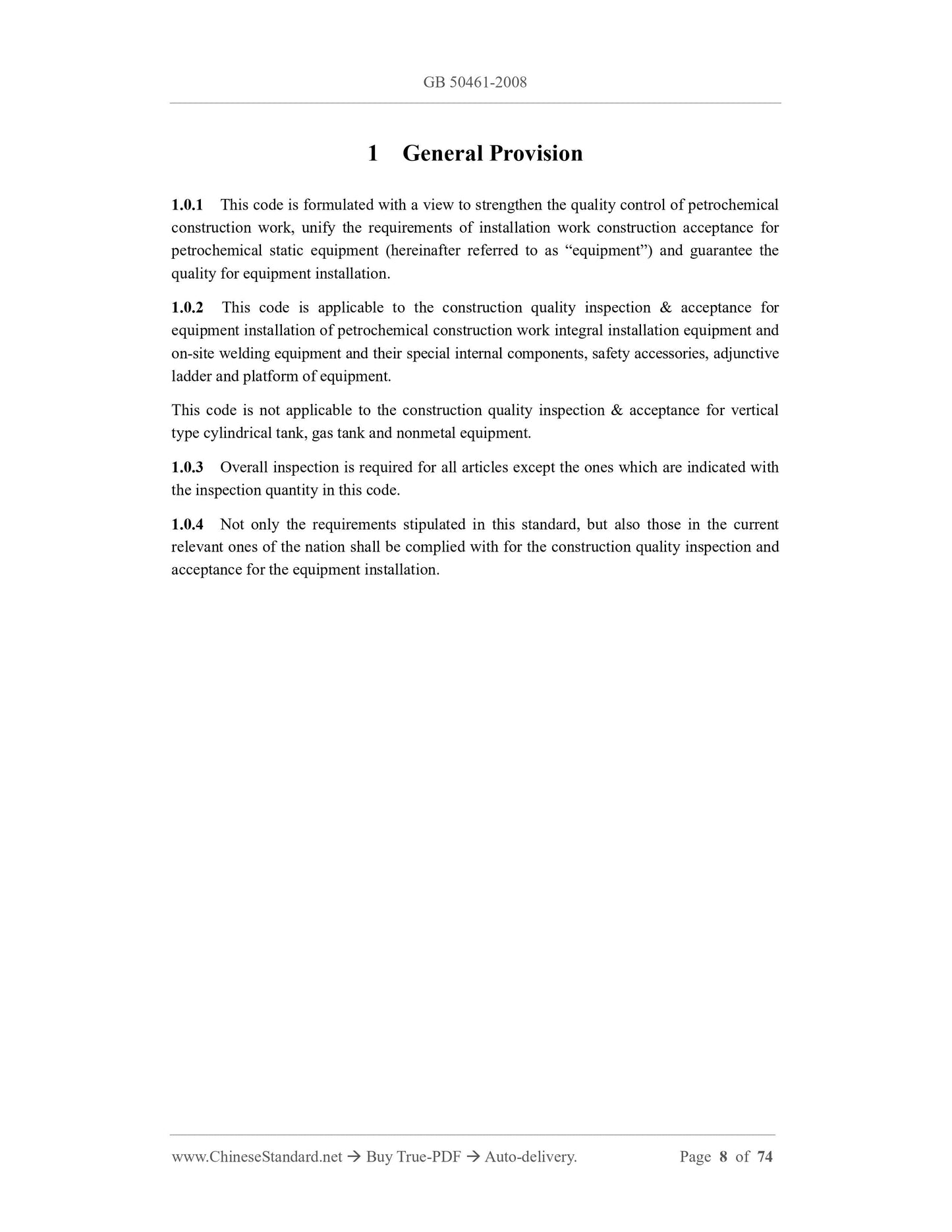
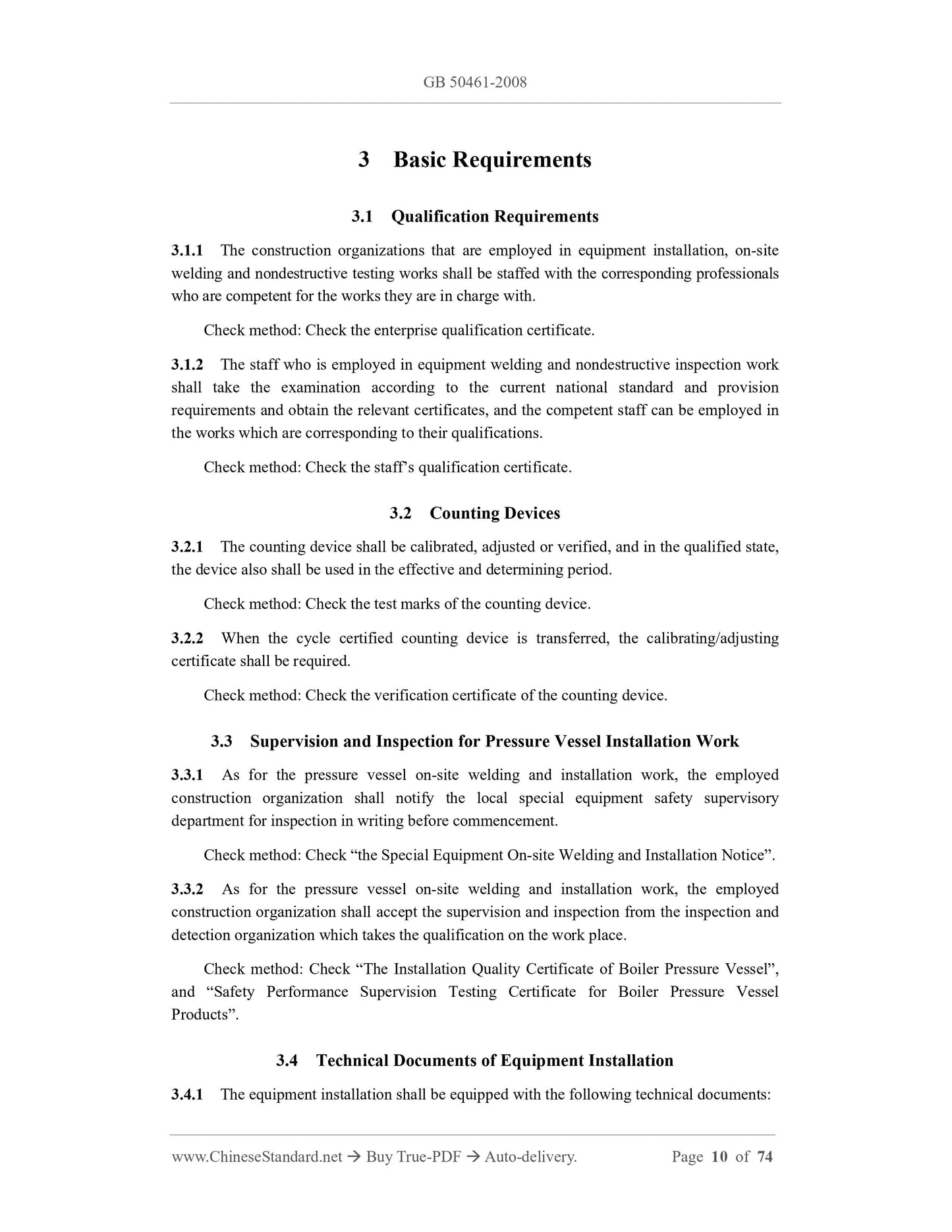
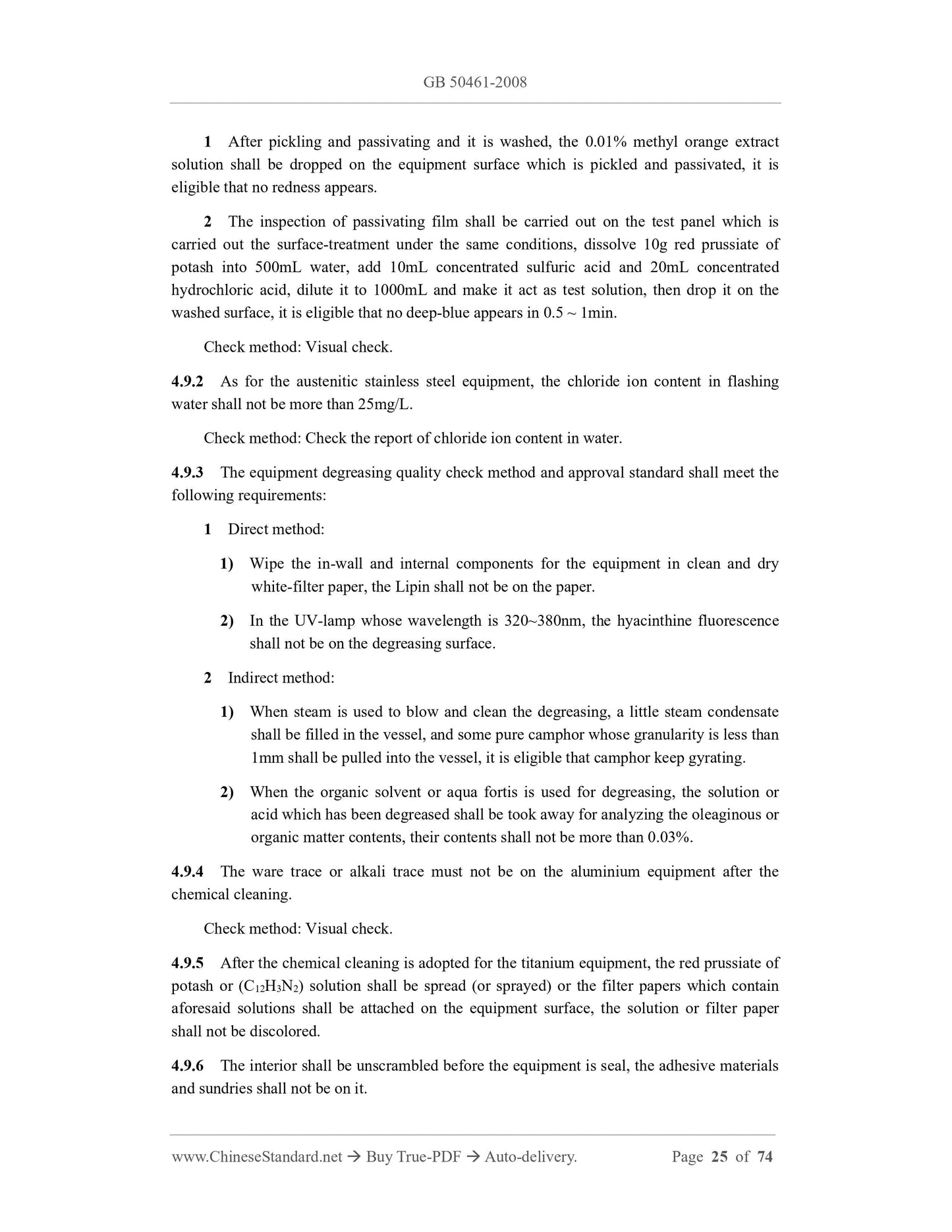
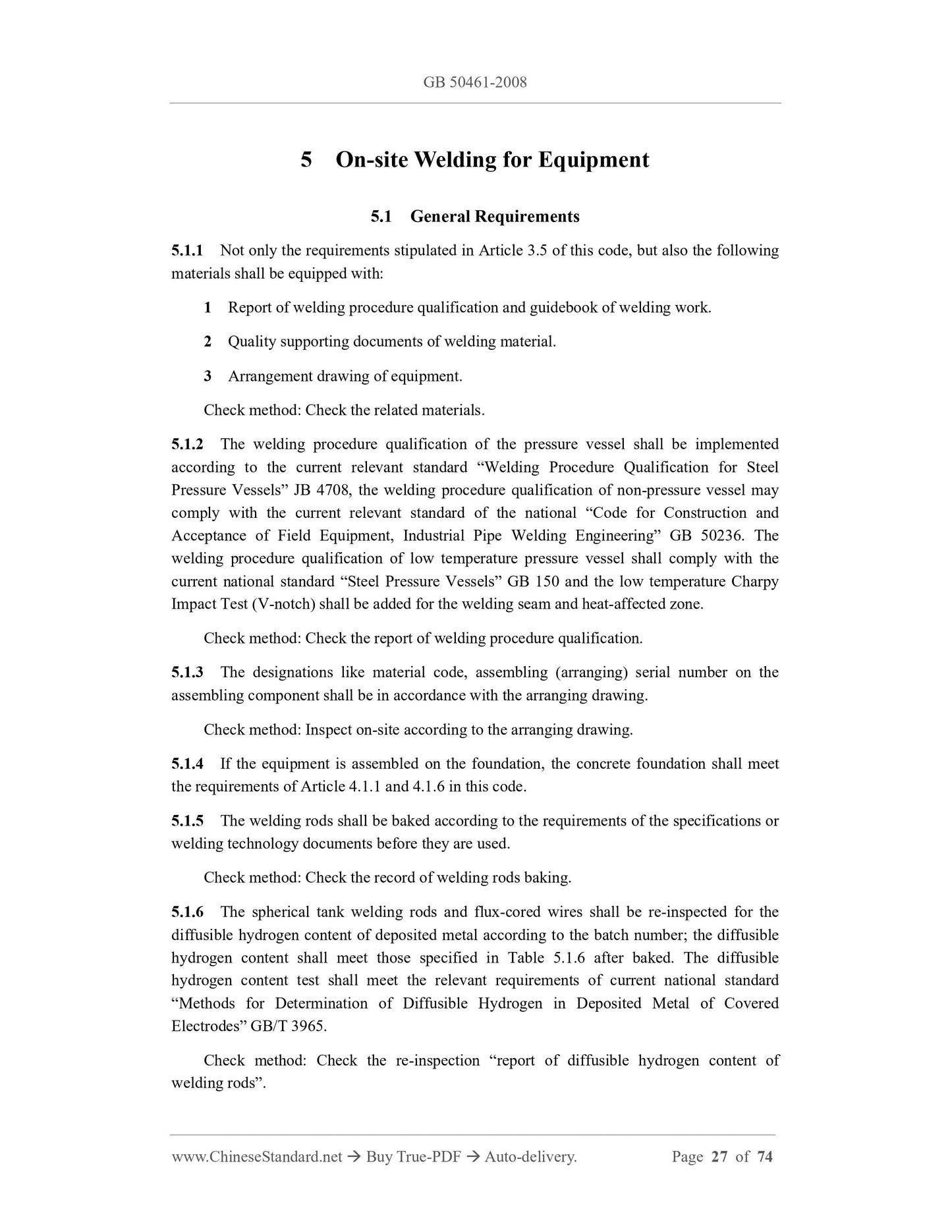
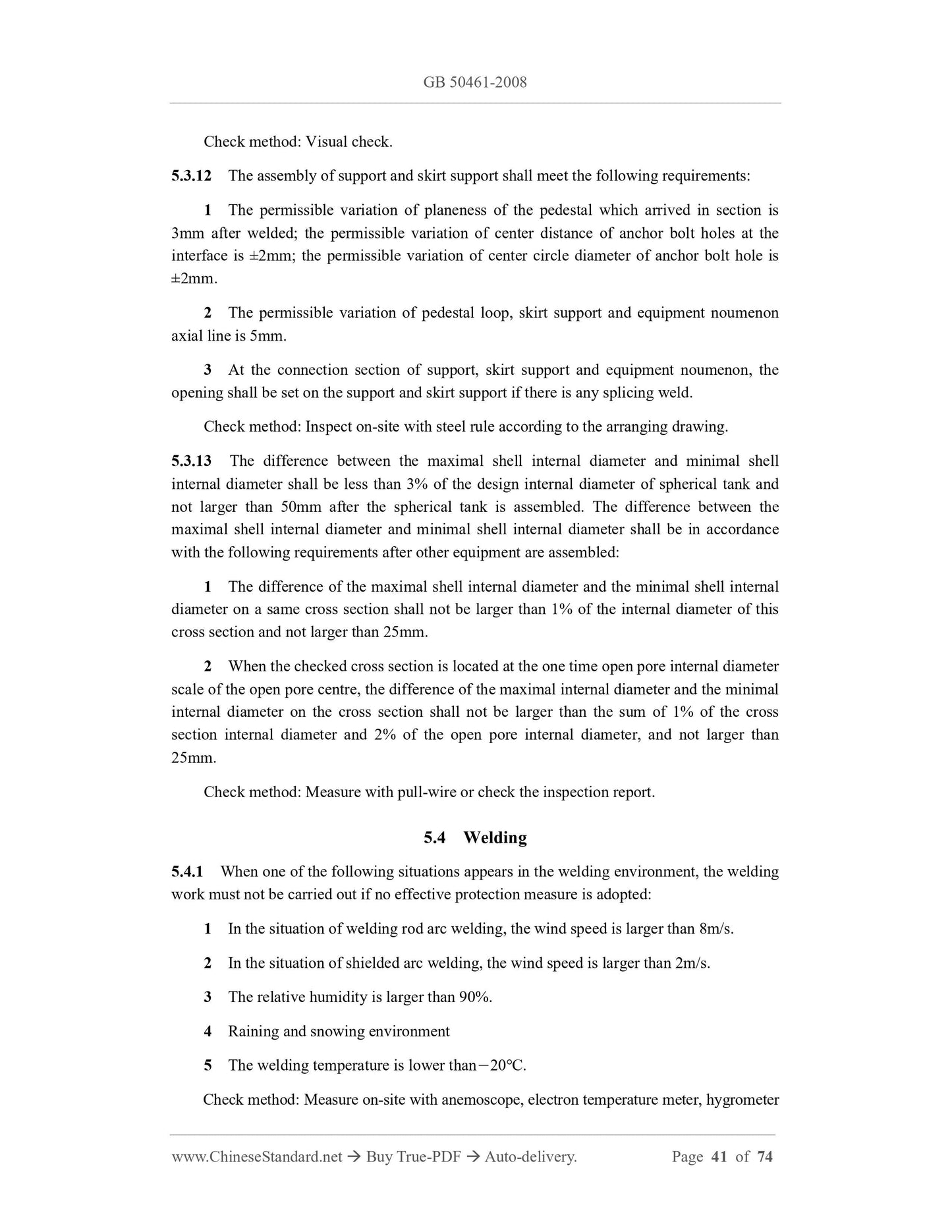
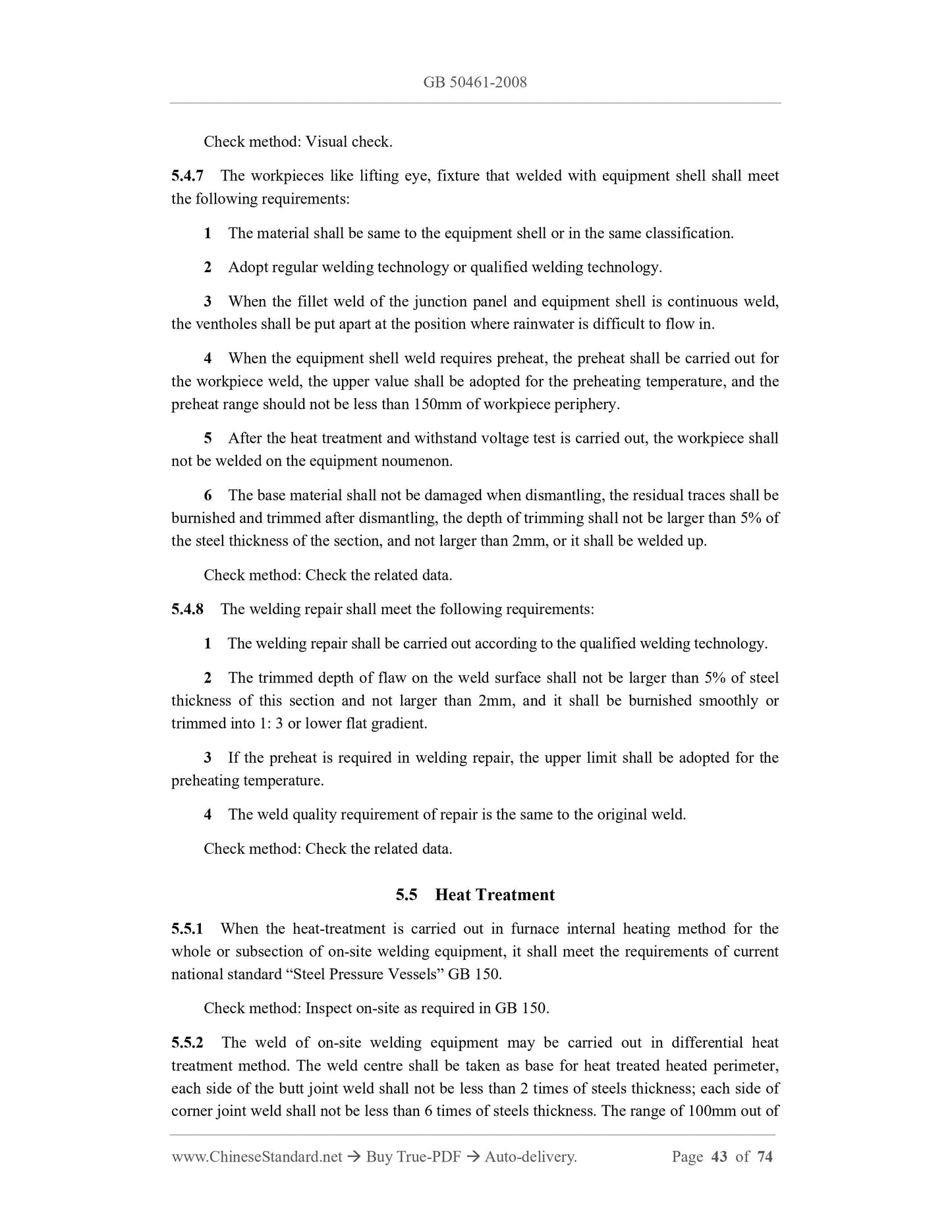
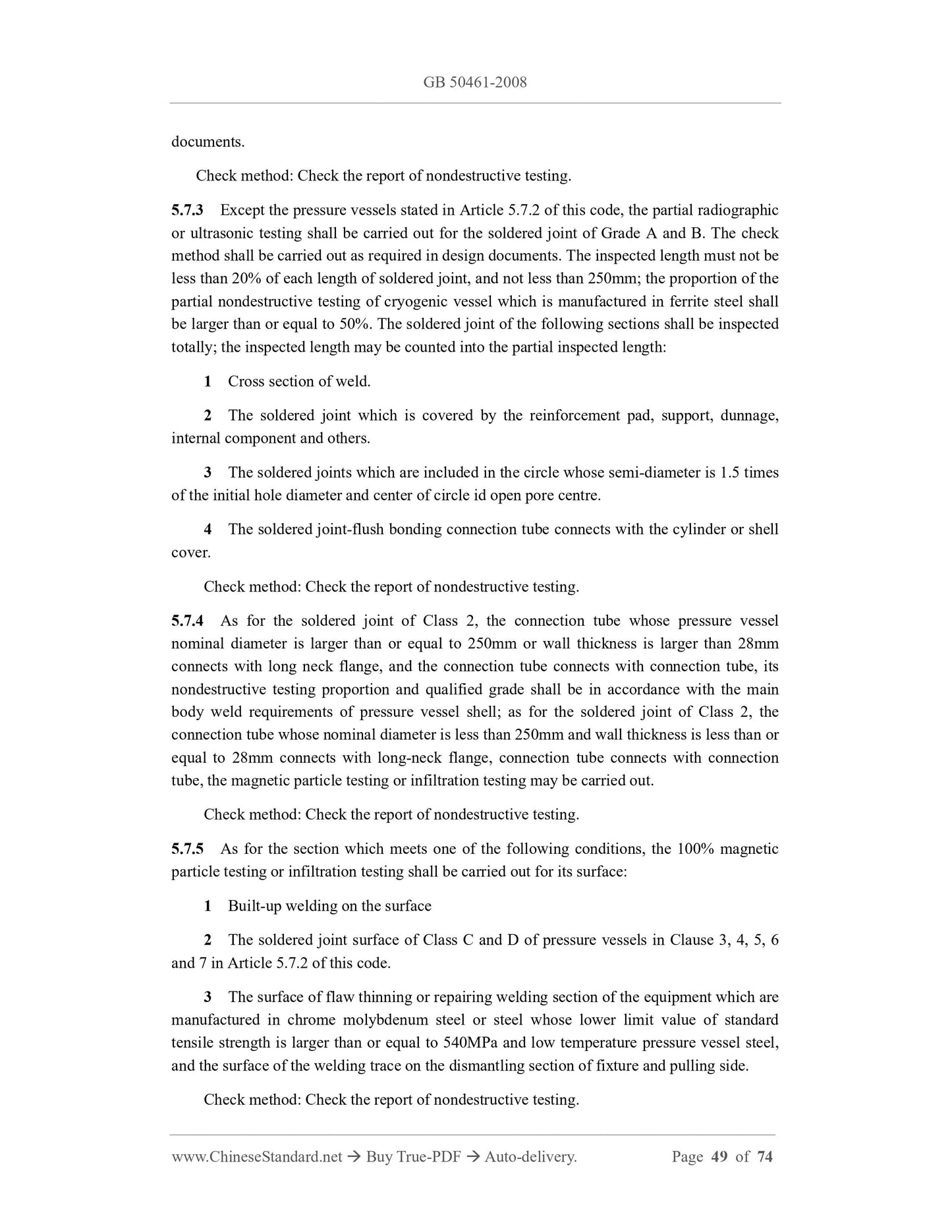
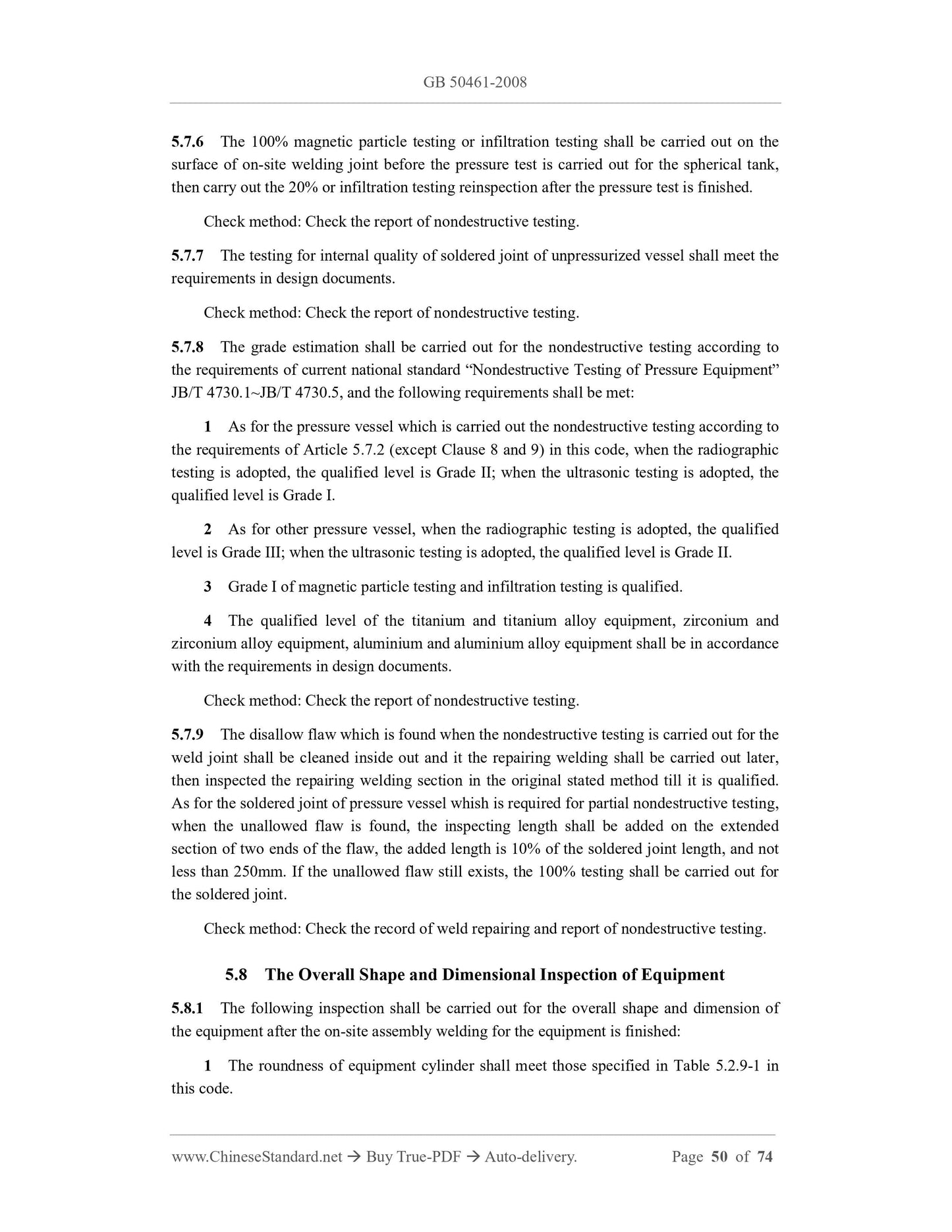
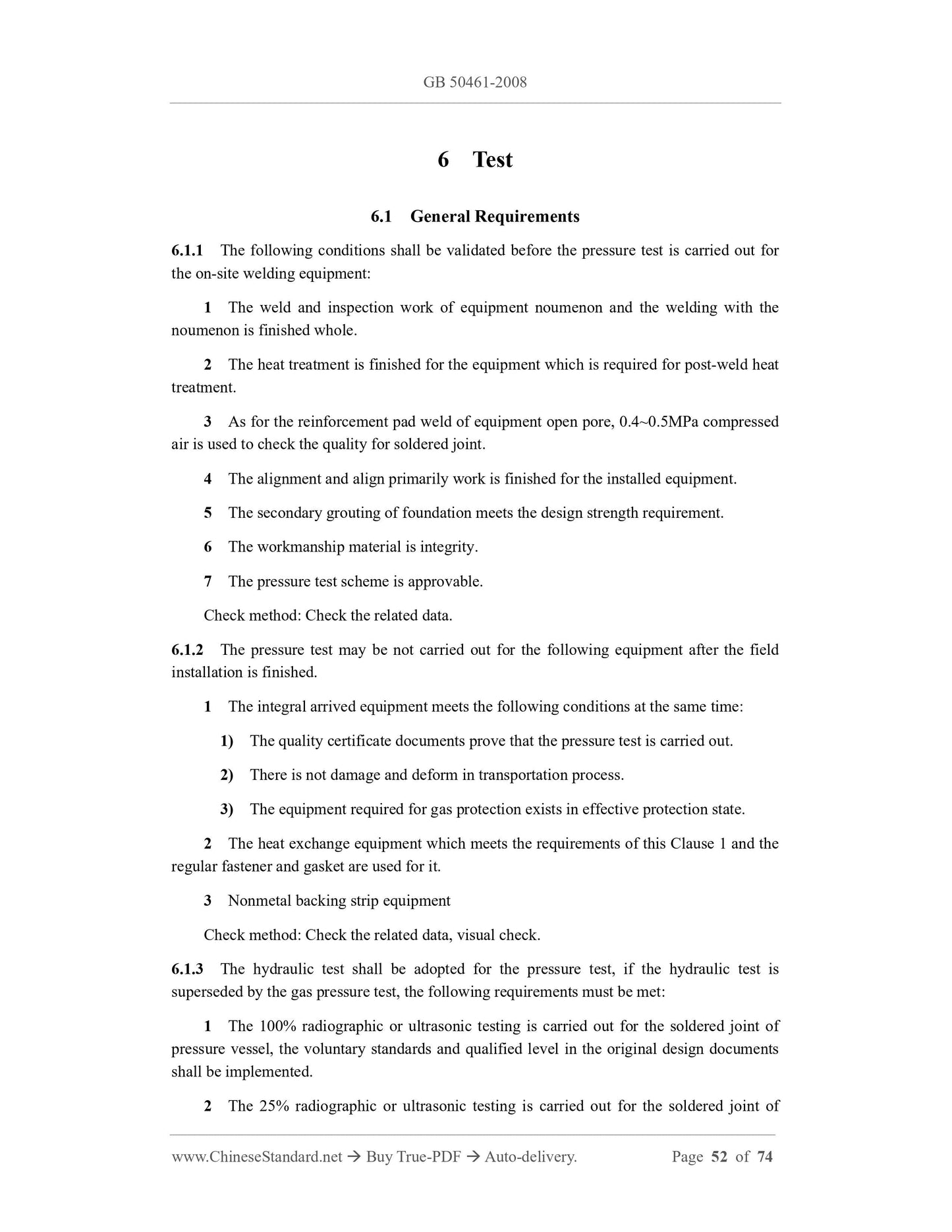
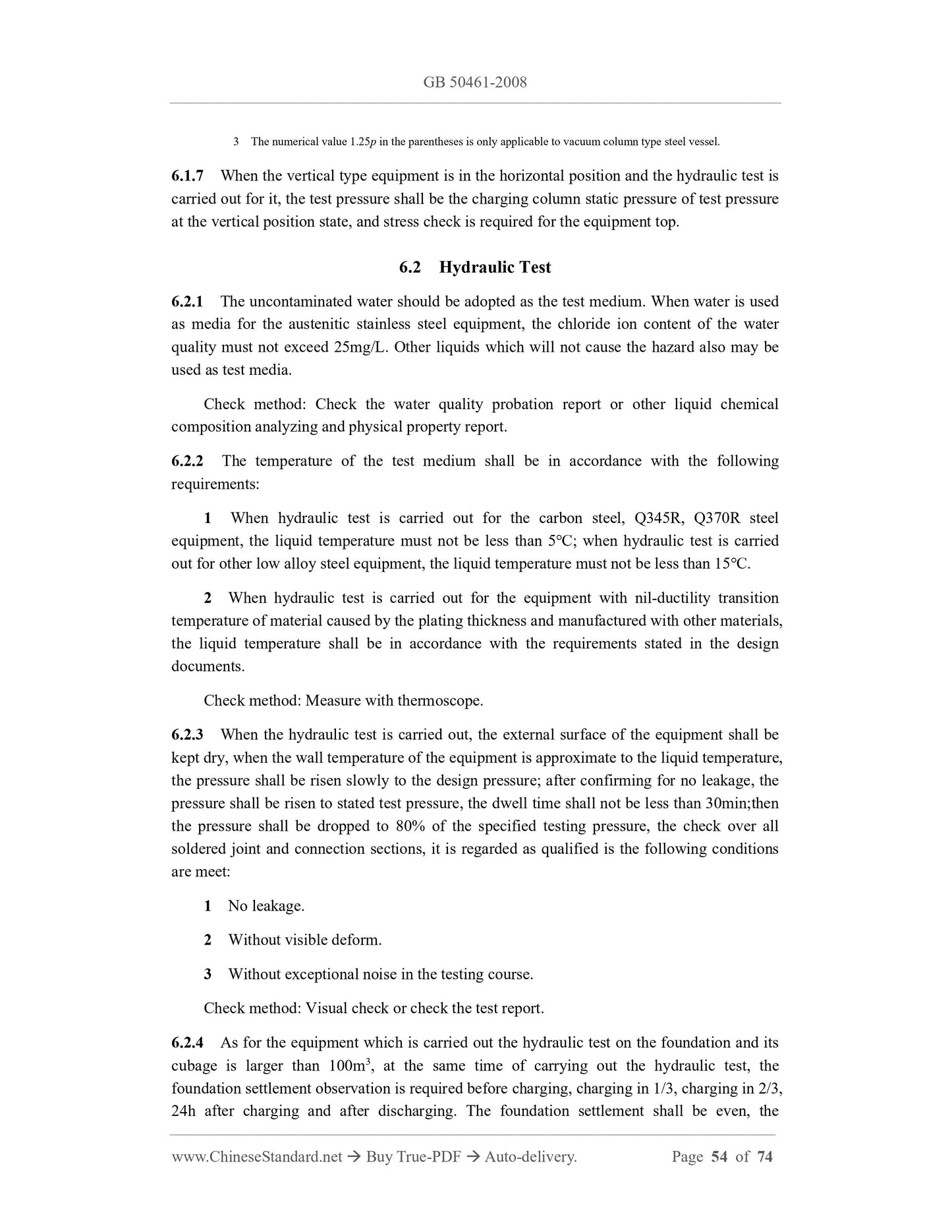