1
/
of
12
www.ChineseStandard.us -- Field Test Asia Pte. Ltd.
GB 38031-2025 English PDF
GB 38031-2025 English PDF
Regular price
$590.00
Regular price
Sale price
$590.00
Unit price
/
per
Shipping calculated at checkout.
Couldn't load pickup availability
GB 38031-2025: Electric vehicles traction battery safety requirements
Delivery: 9 seconds. Download (and Email) true-PDF + Invoice.
Get Quotation: Click GB 38031-2025 (Self-service in 1-minute)
Newer / historical versions: GB 38031-2025
Preview True-PDF (Reload/Scroll-down if blank)
Delivery: 9 seconds. Download (and Email) true-PDF + Invoice.
Get Quotation: Click GB 38031-2025 (Self-service in 1-minute)
Newer / historical versions: GB 38031-2025
Preview True-PDF (Reload/Scroll-down if blank)
Share
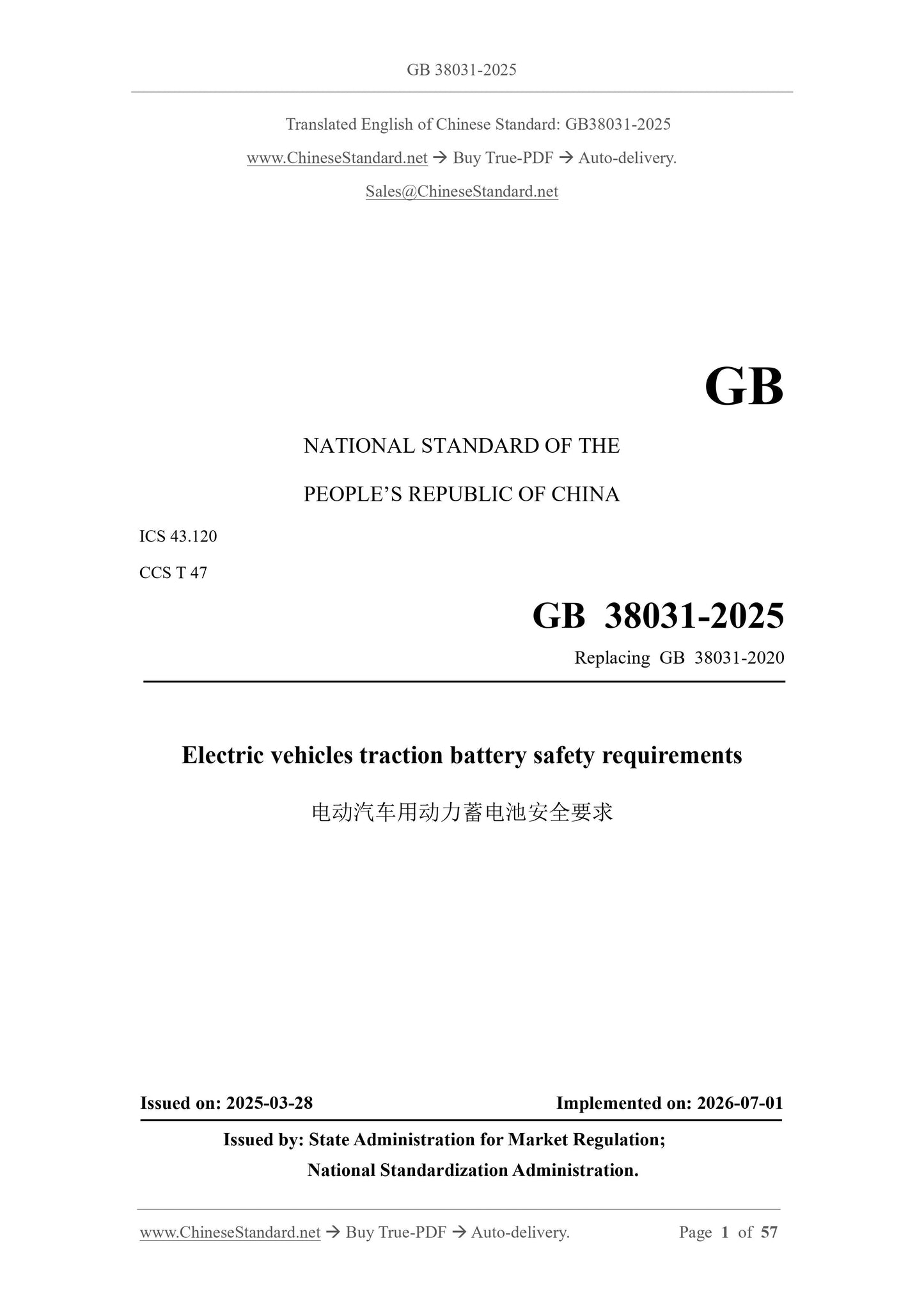
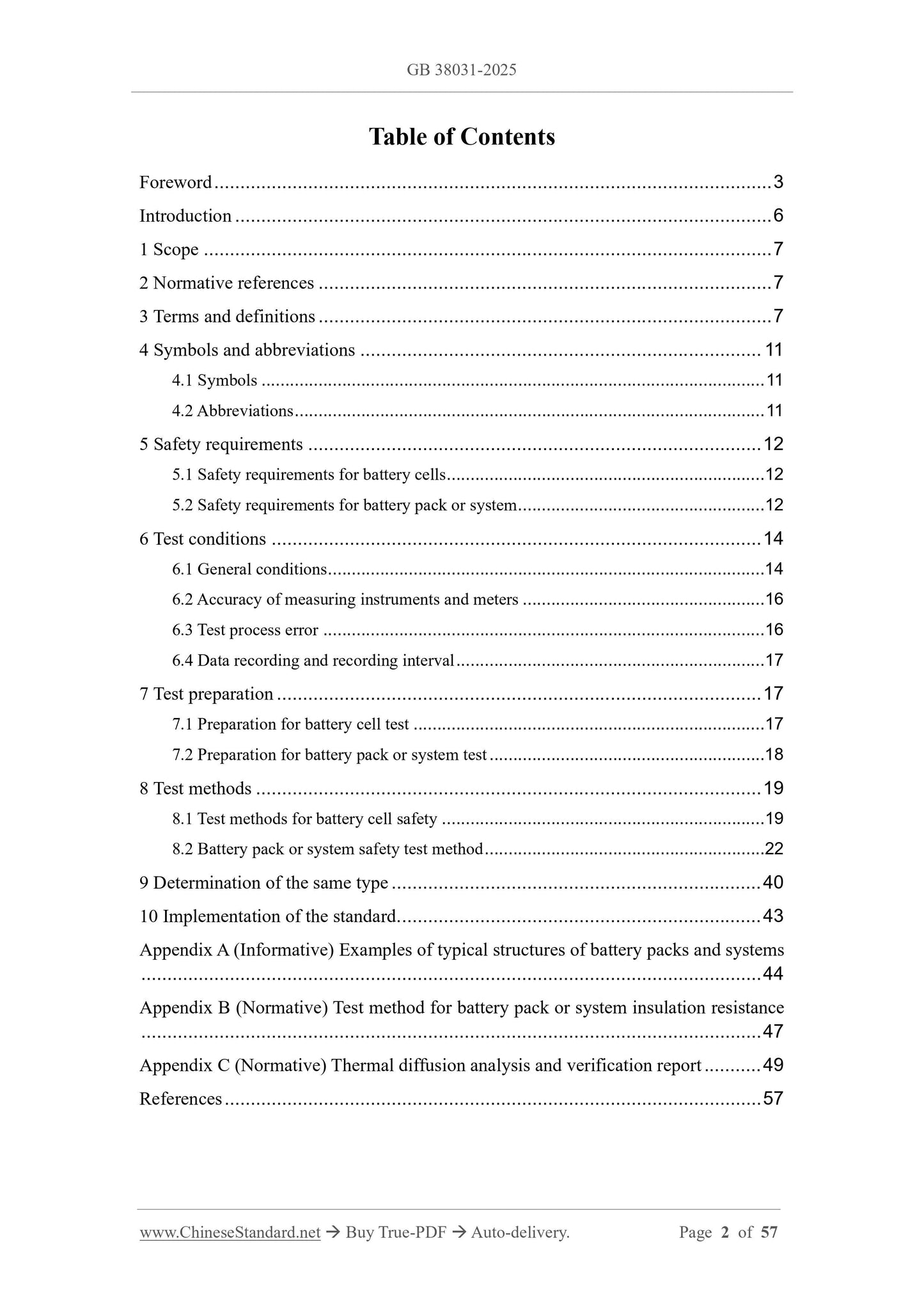
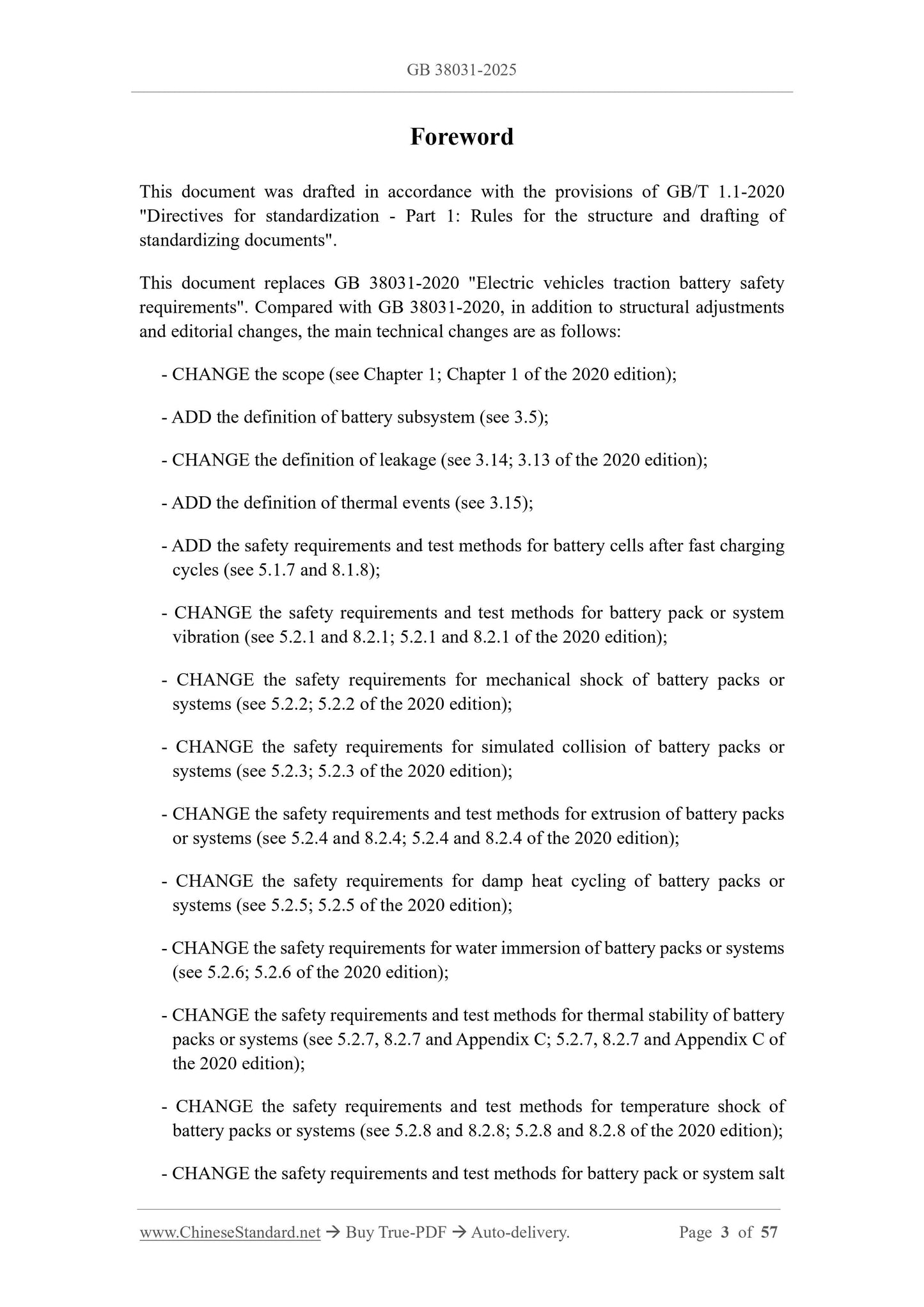
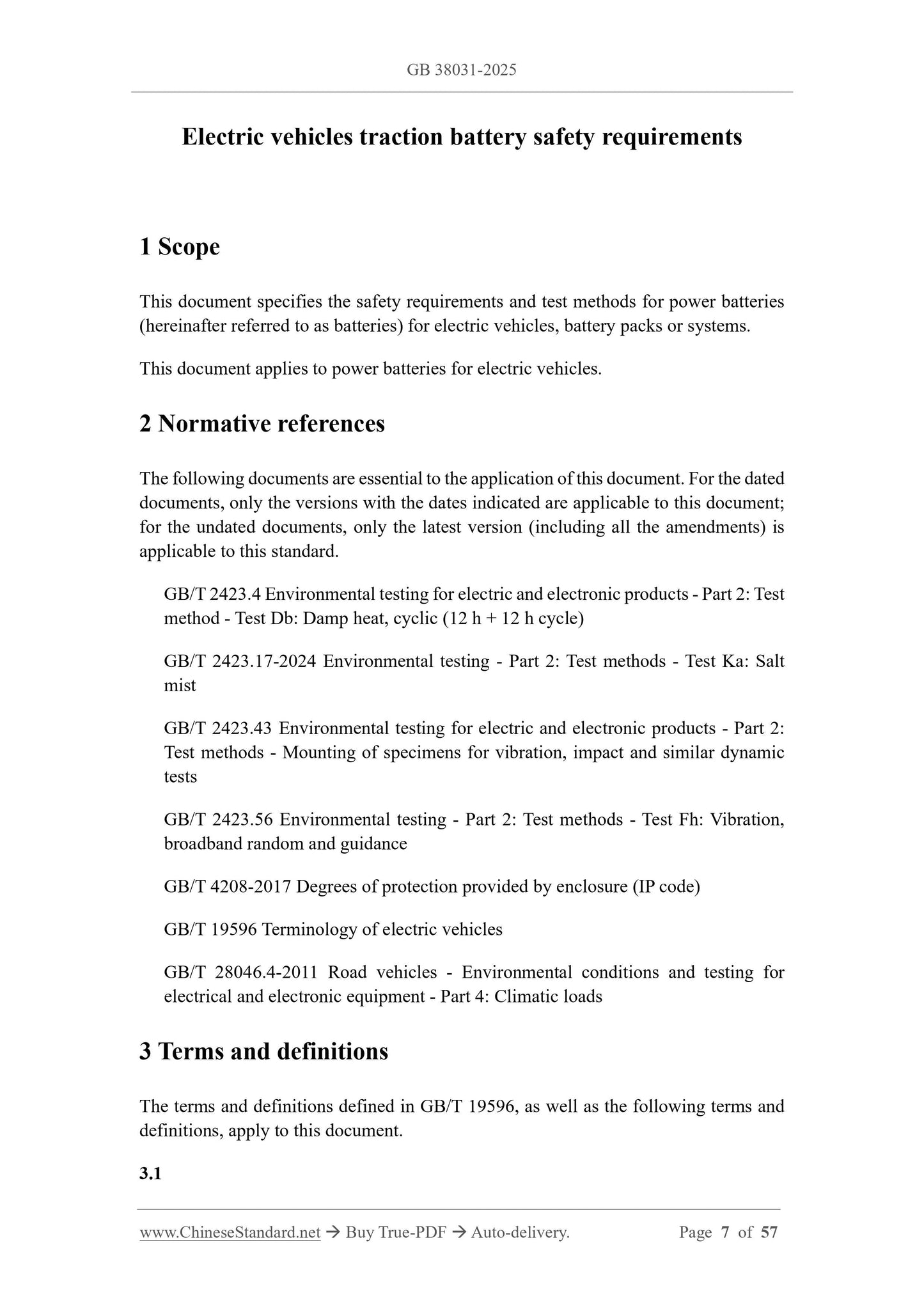
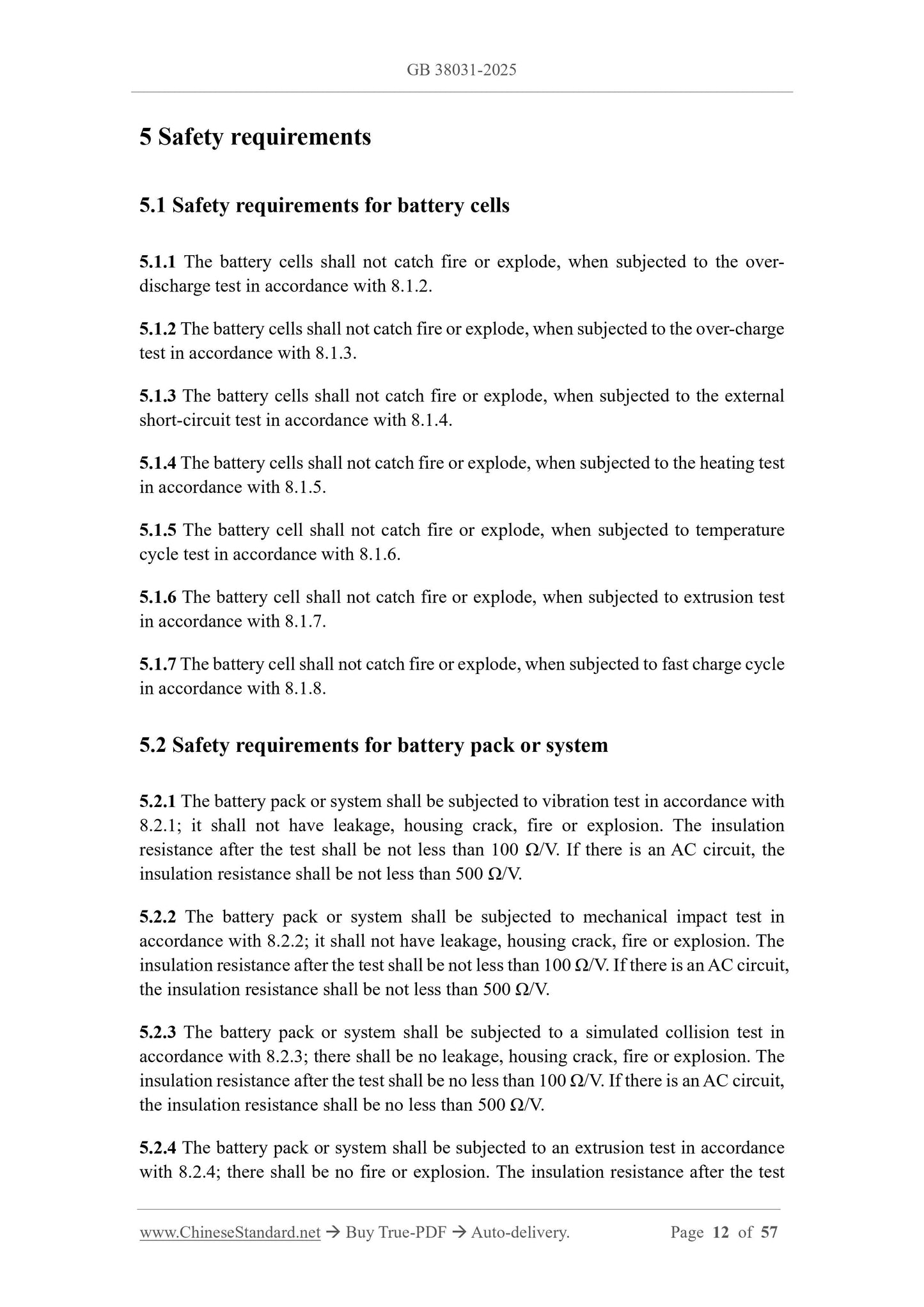
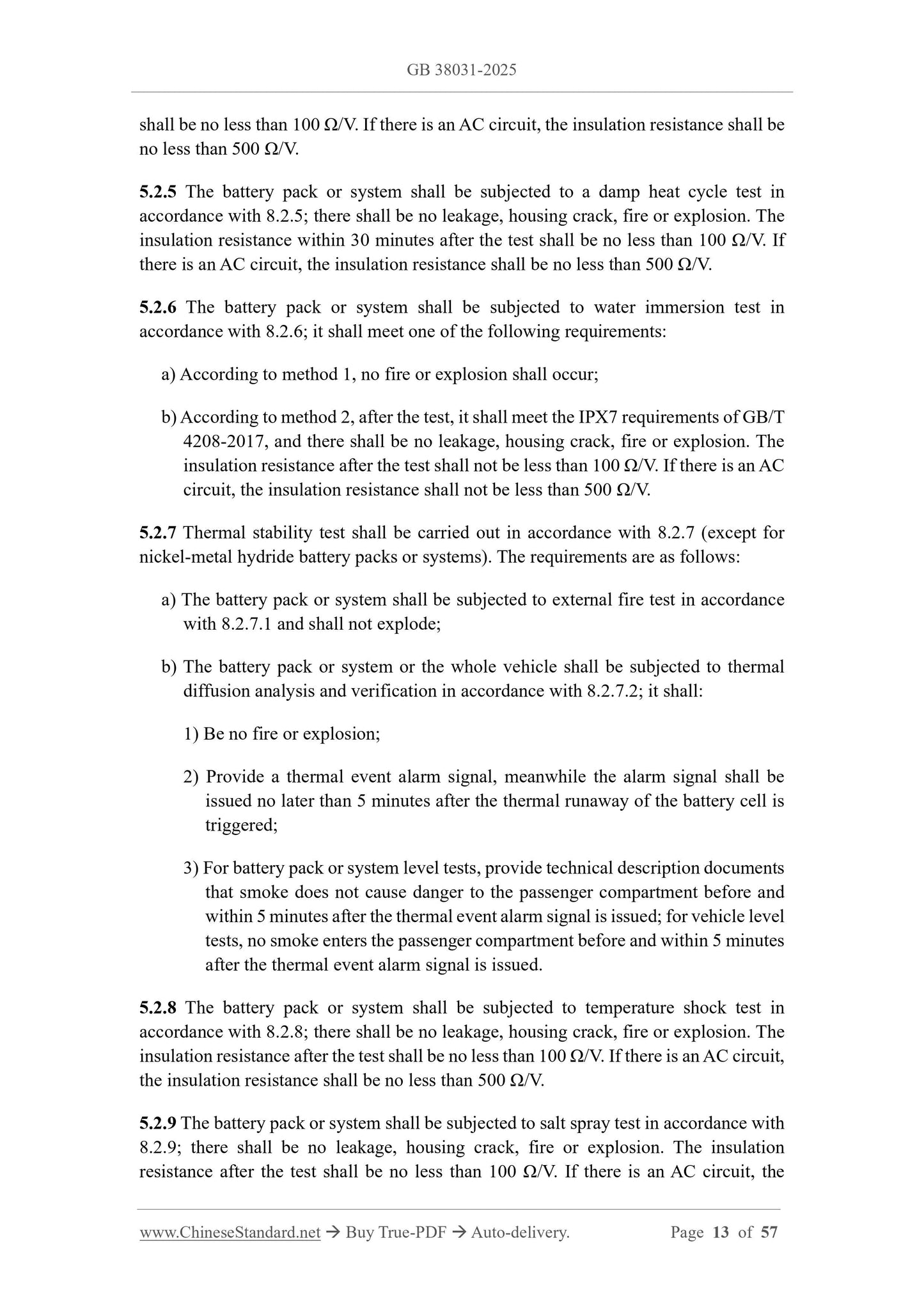
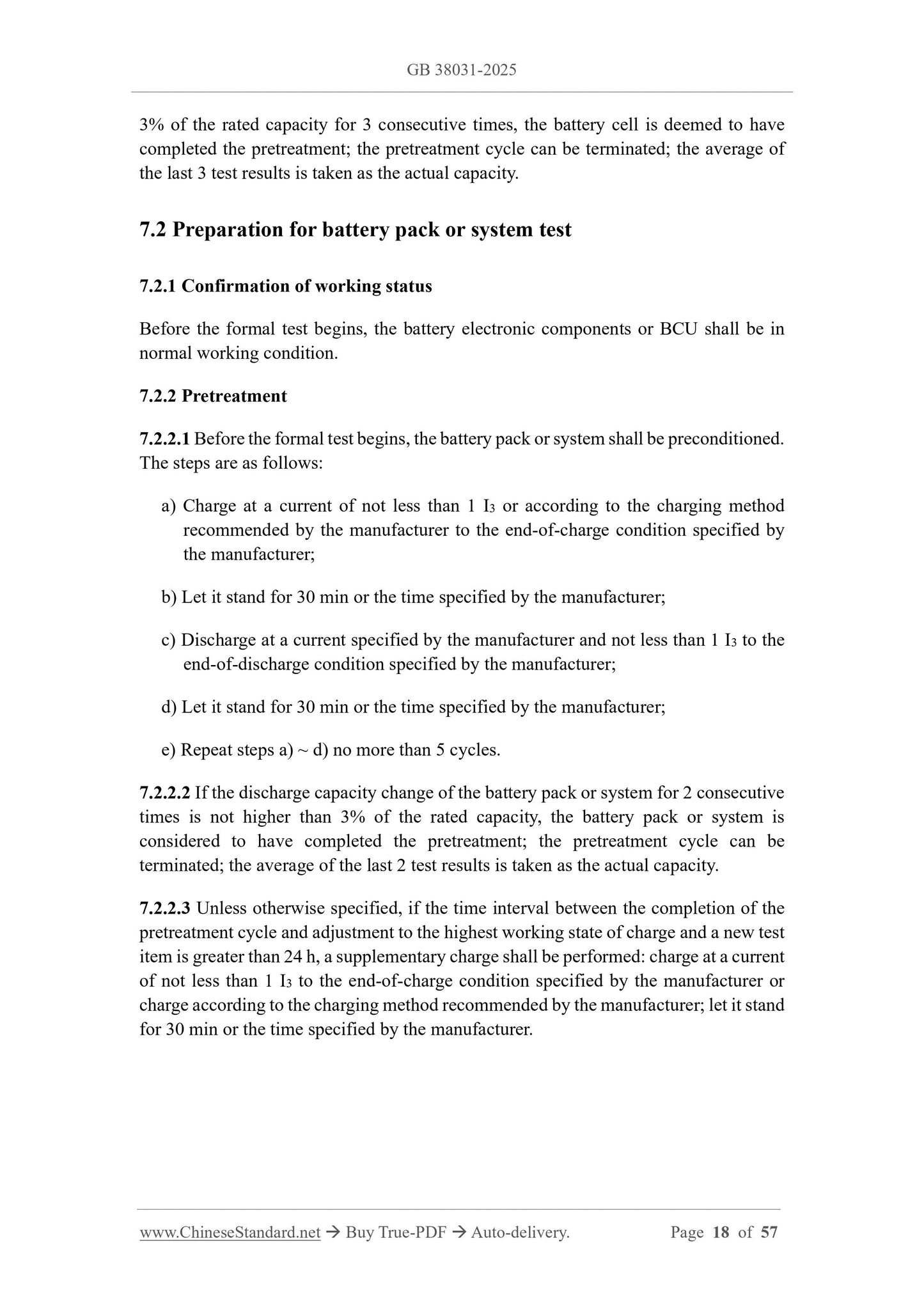
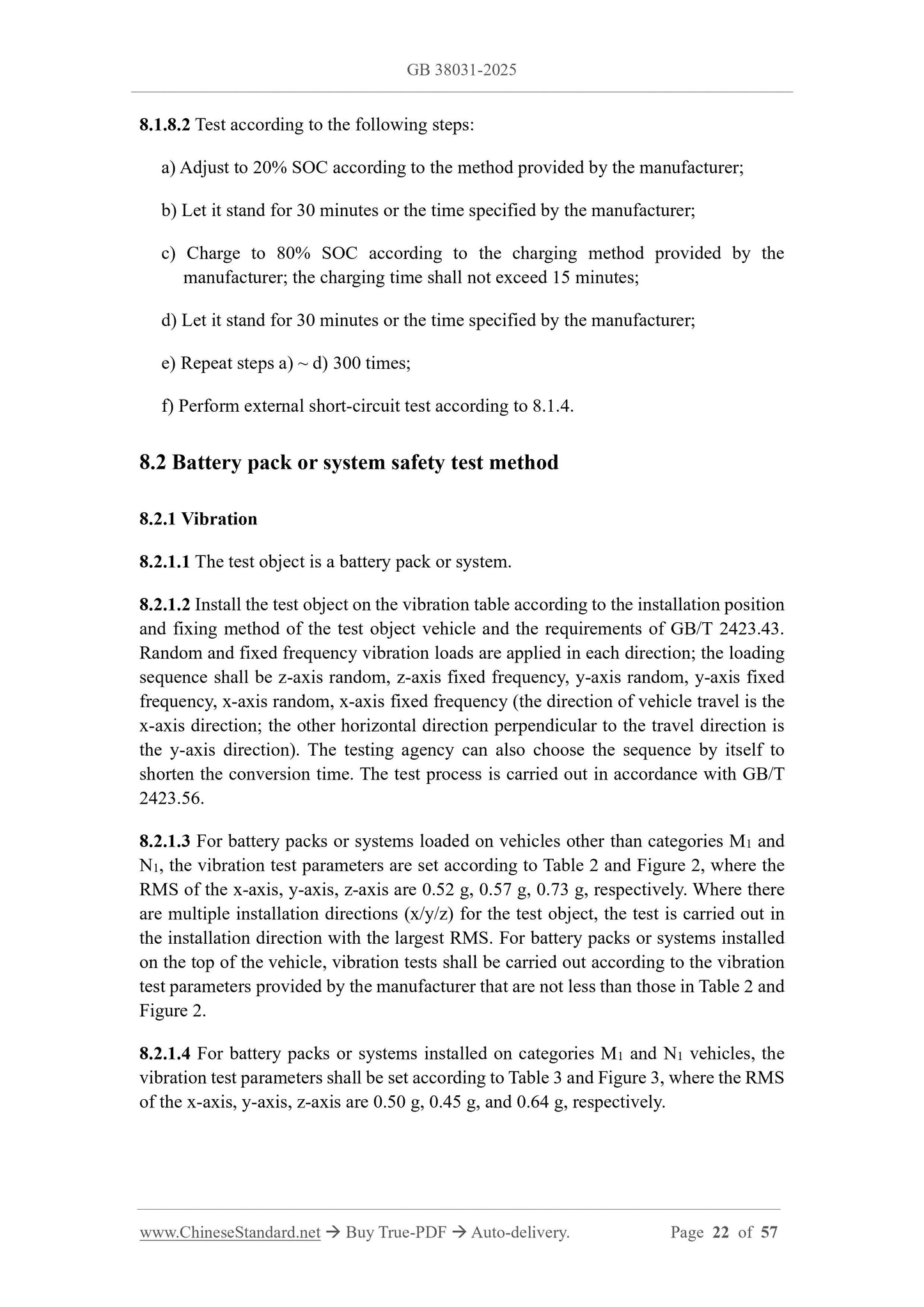
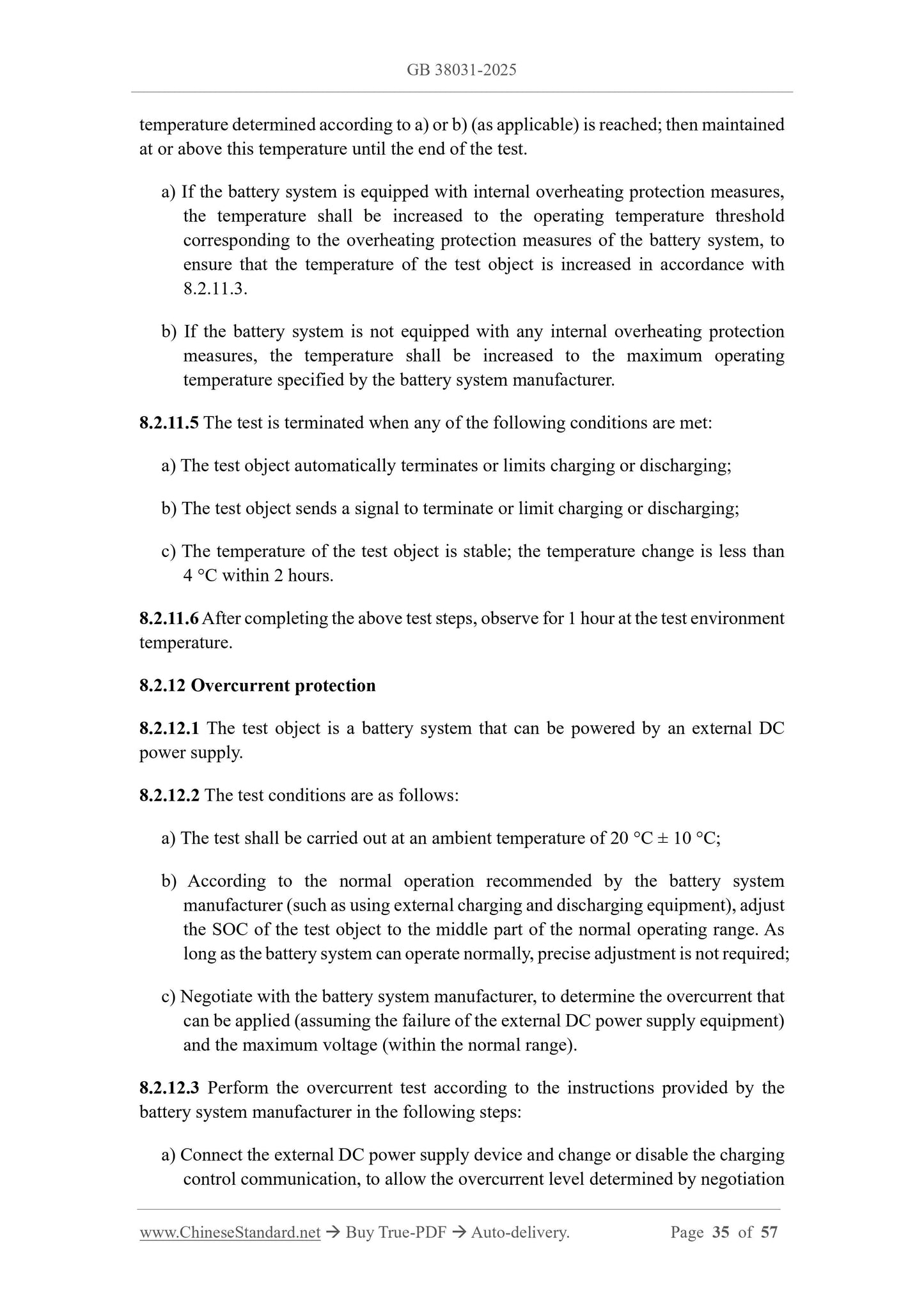
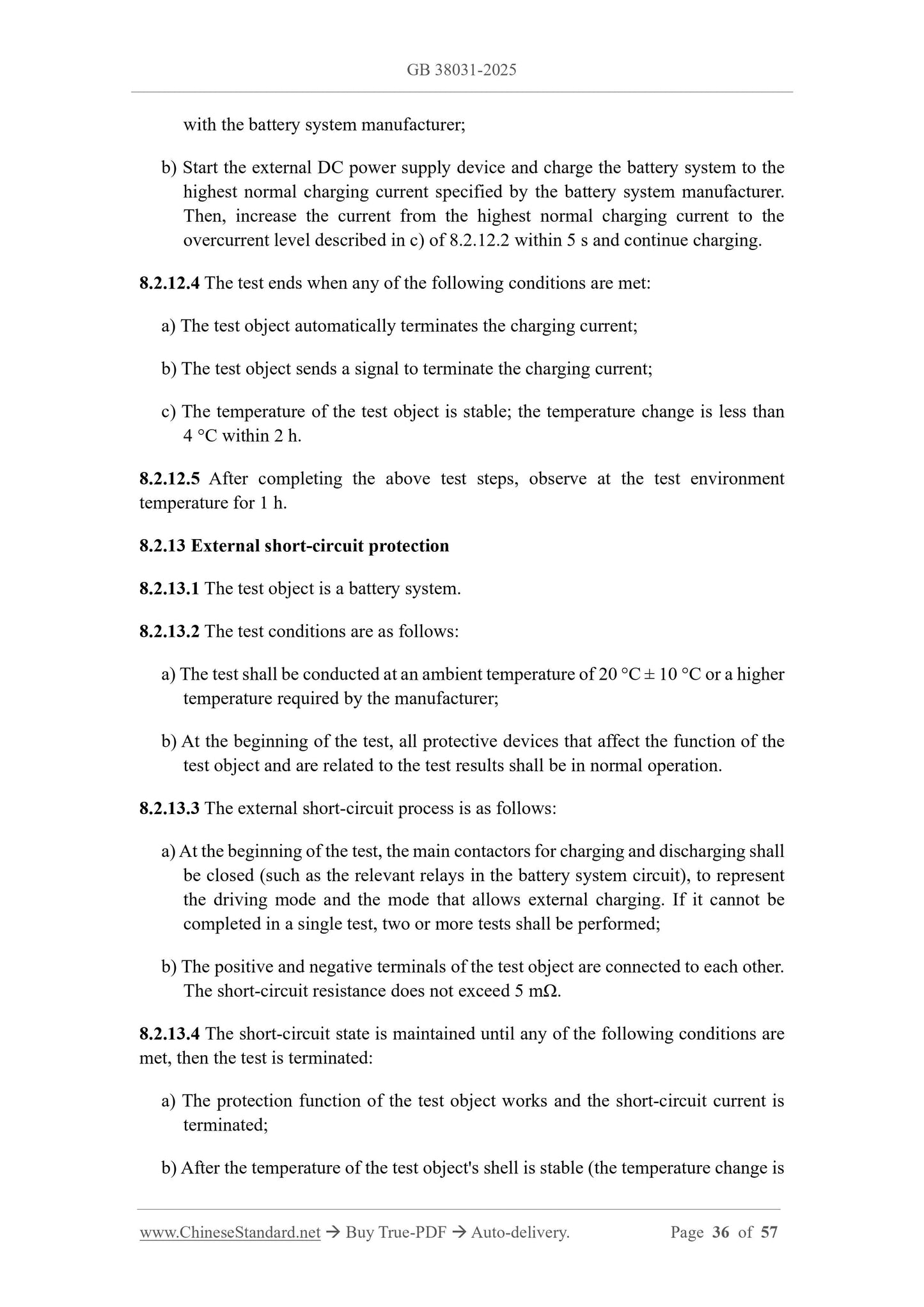
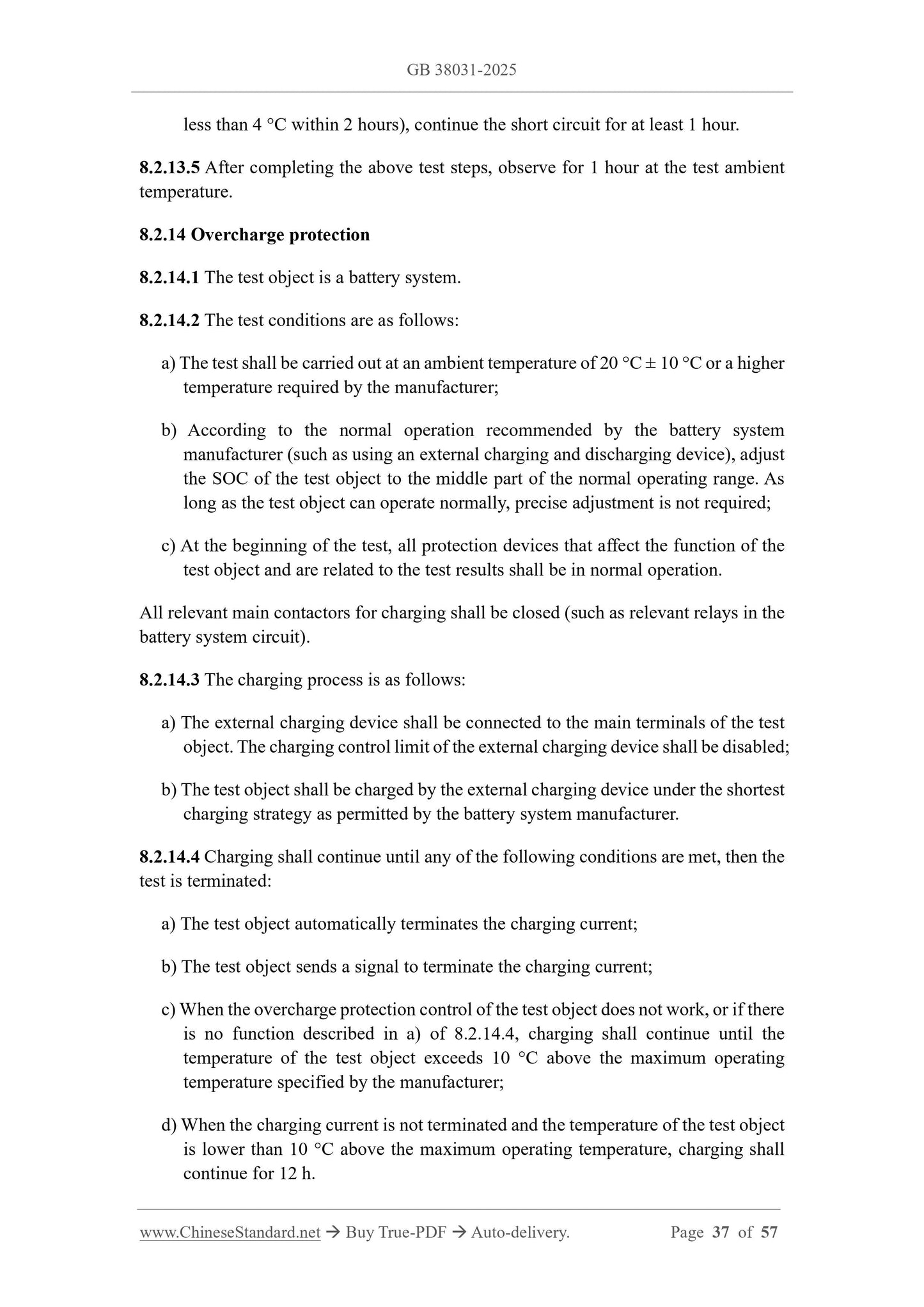
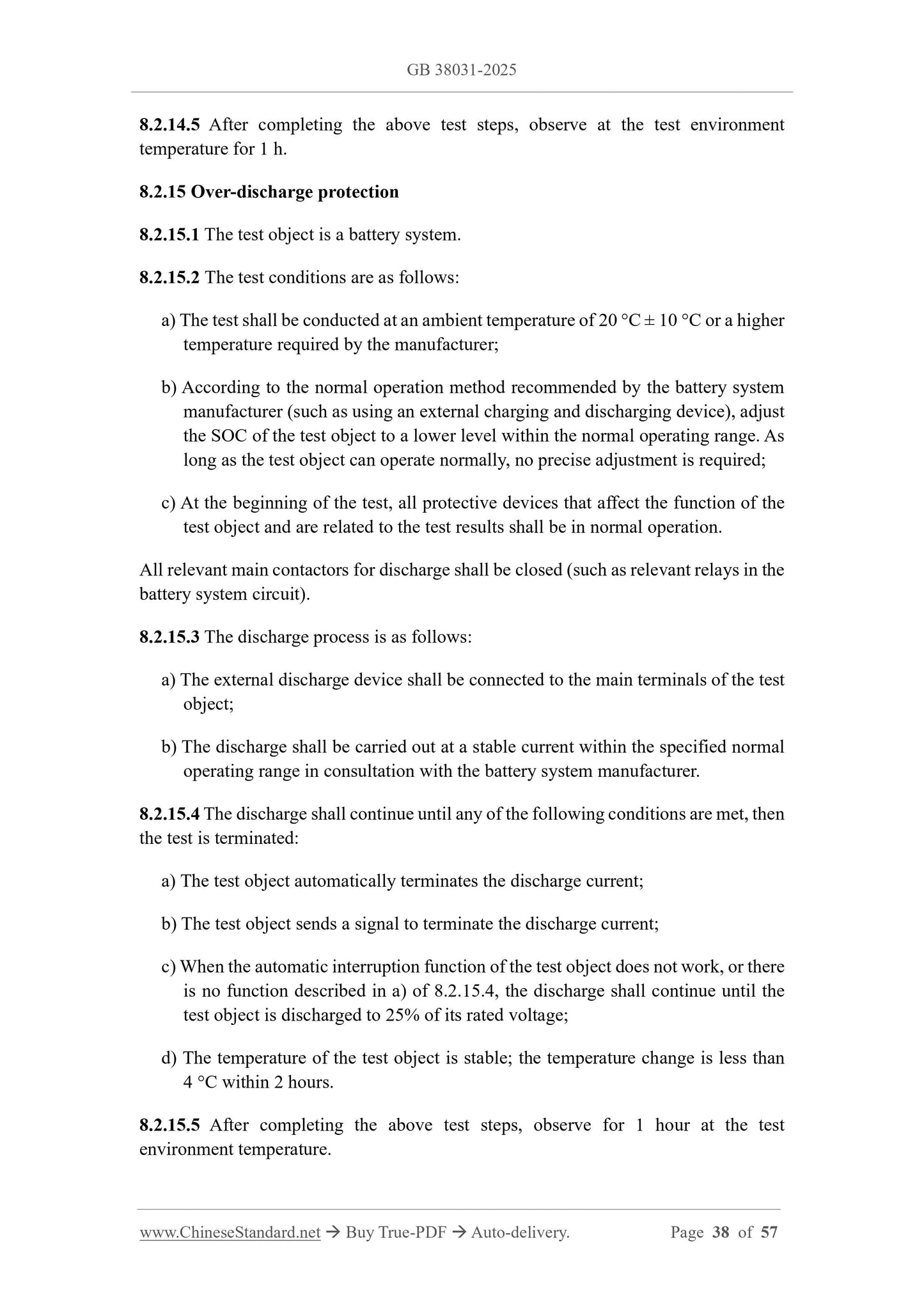