1
/
of
6
www.ChineseStandard.us -- Field Test Asia Pte. Ltd.
GB 26134-2024 English PDF
GB 26134-2024 English PDF
Regular price
$215.00
Regular price
Sale price
$215.00
Unit price
/
per
Shipping calculated at checkout.
Couldn't load pickup availability
GB 26134-2024: Roof crush resistance of passenger cars
Delivery: 9 seconds. Download (and Email) true-PDF + Invoice.
Get Quotation: Click GB 26134-2024 (Self-service in 1-minute)
Newer / historical versions: GB 26134-2024
Preview True-PDF (Reload/Scroll-down if blank)
Delivery: 9 seconds. Download (and Email) true-PDF + Invoice.
Get Quotation: Click GB 26134-2024 (Self-service in 1-minute)
Newer / historical versions: GB 26134-2024
Preview True-PDF (Reload/Scroll-down if blank)
Share
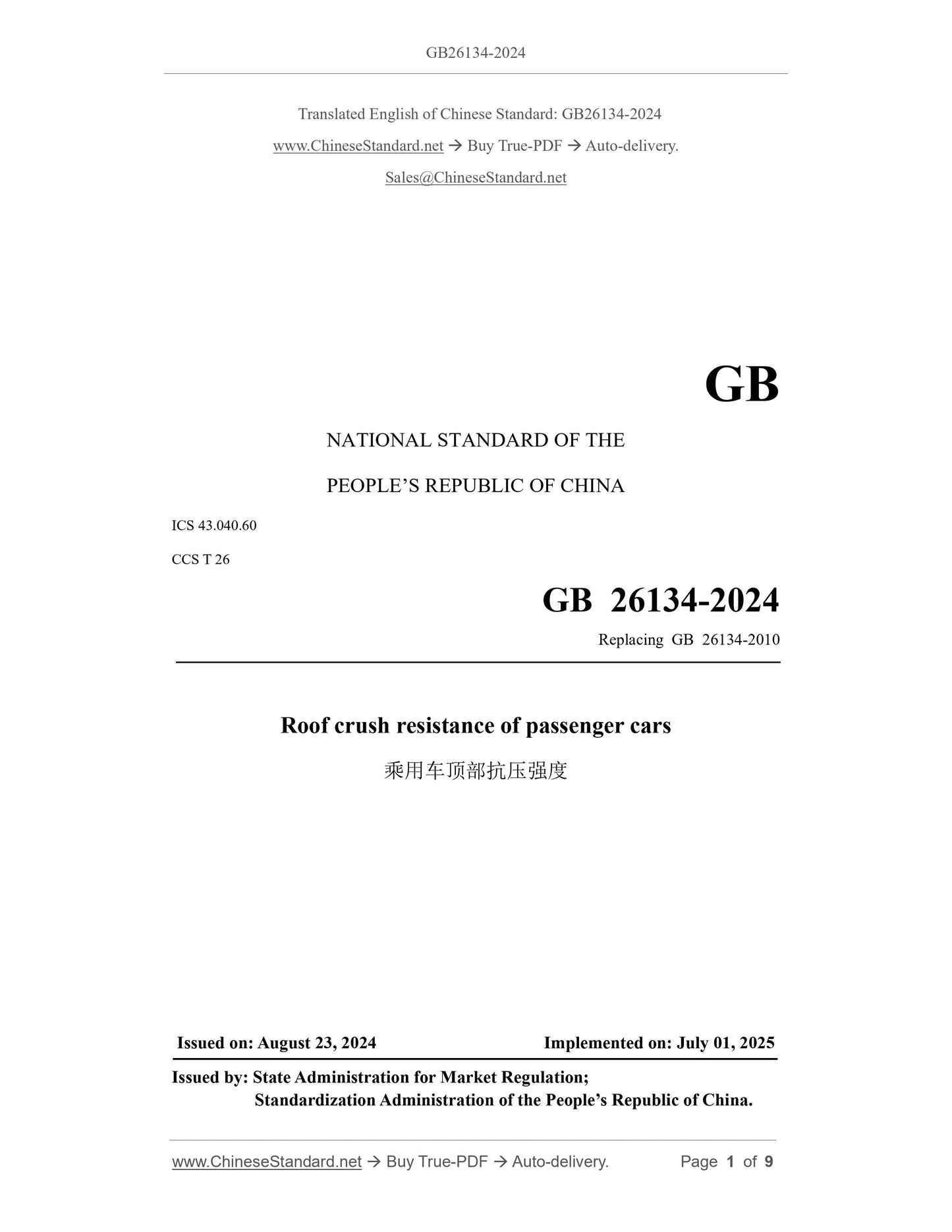
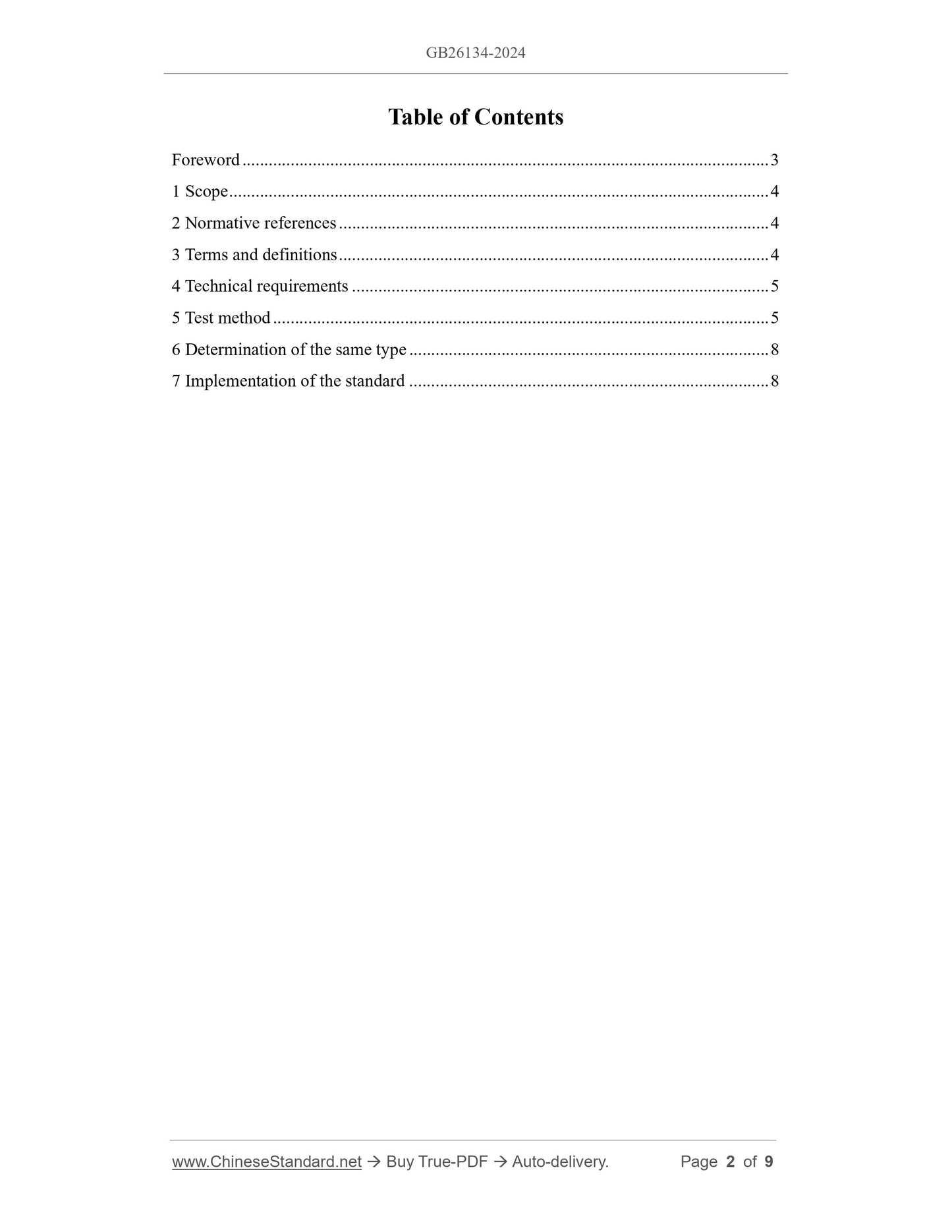
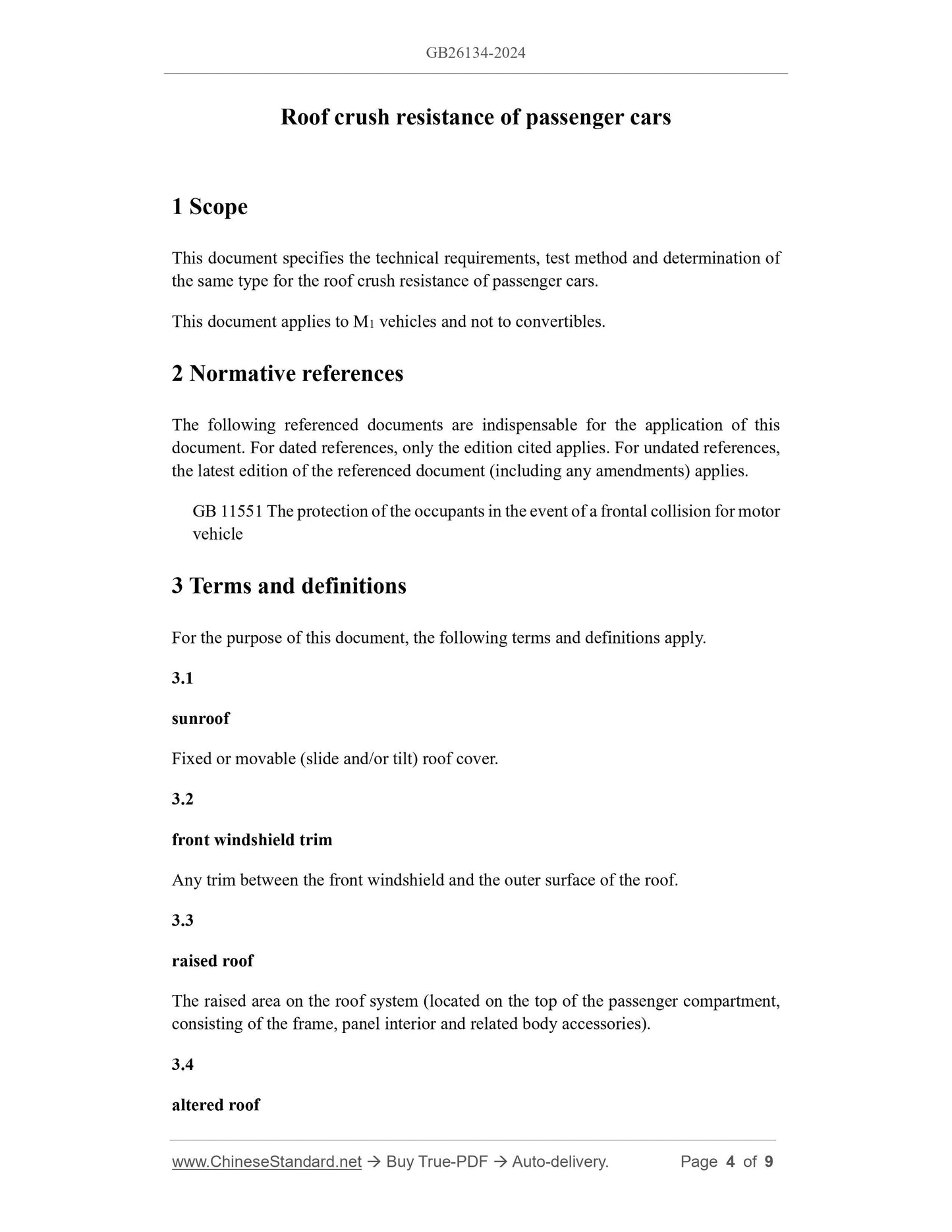
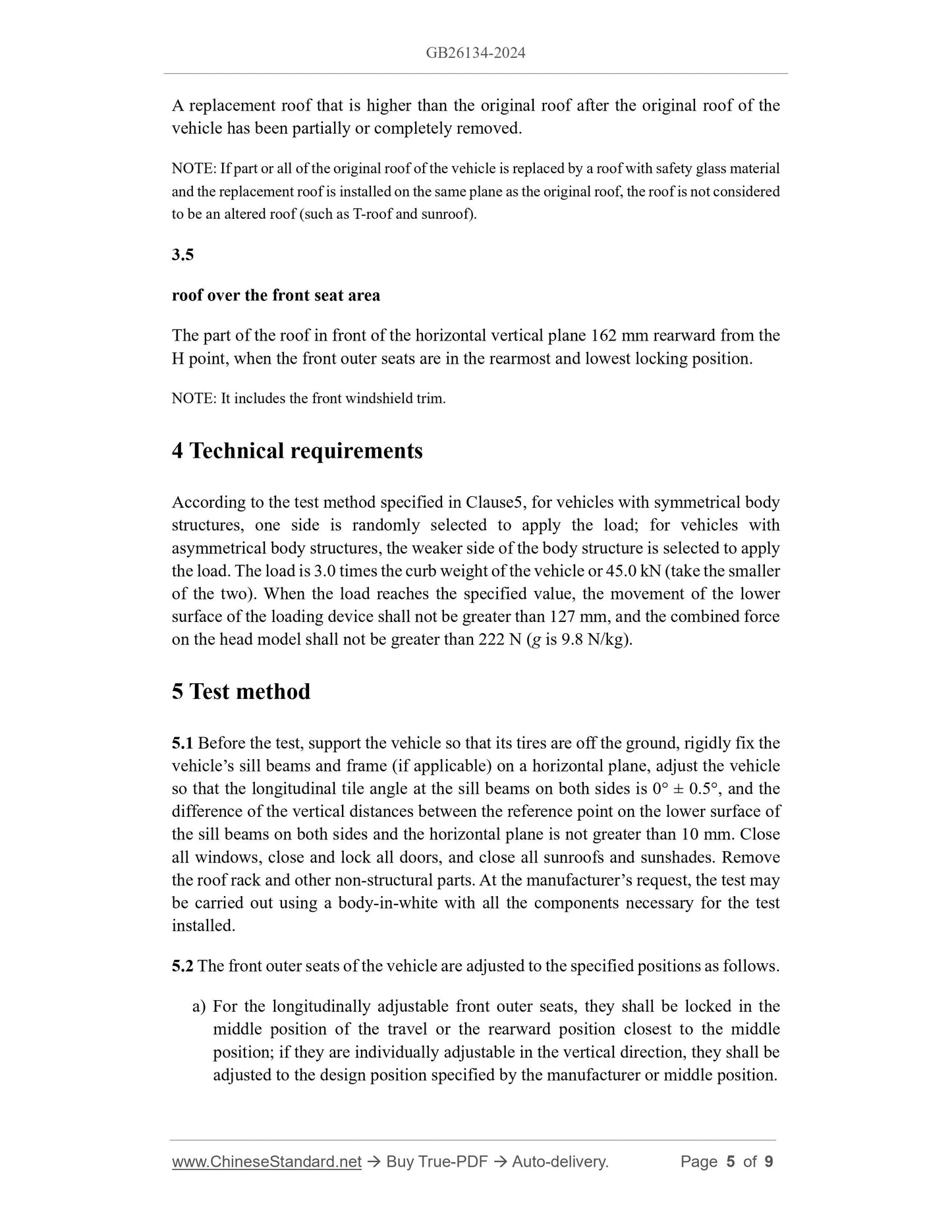
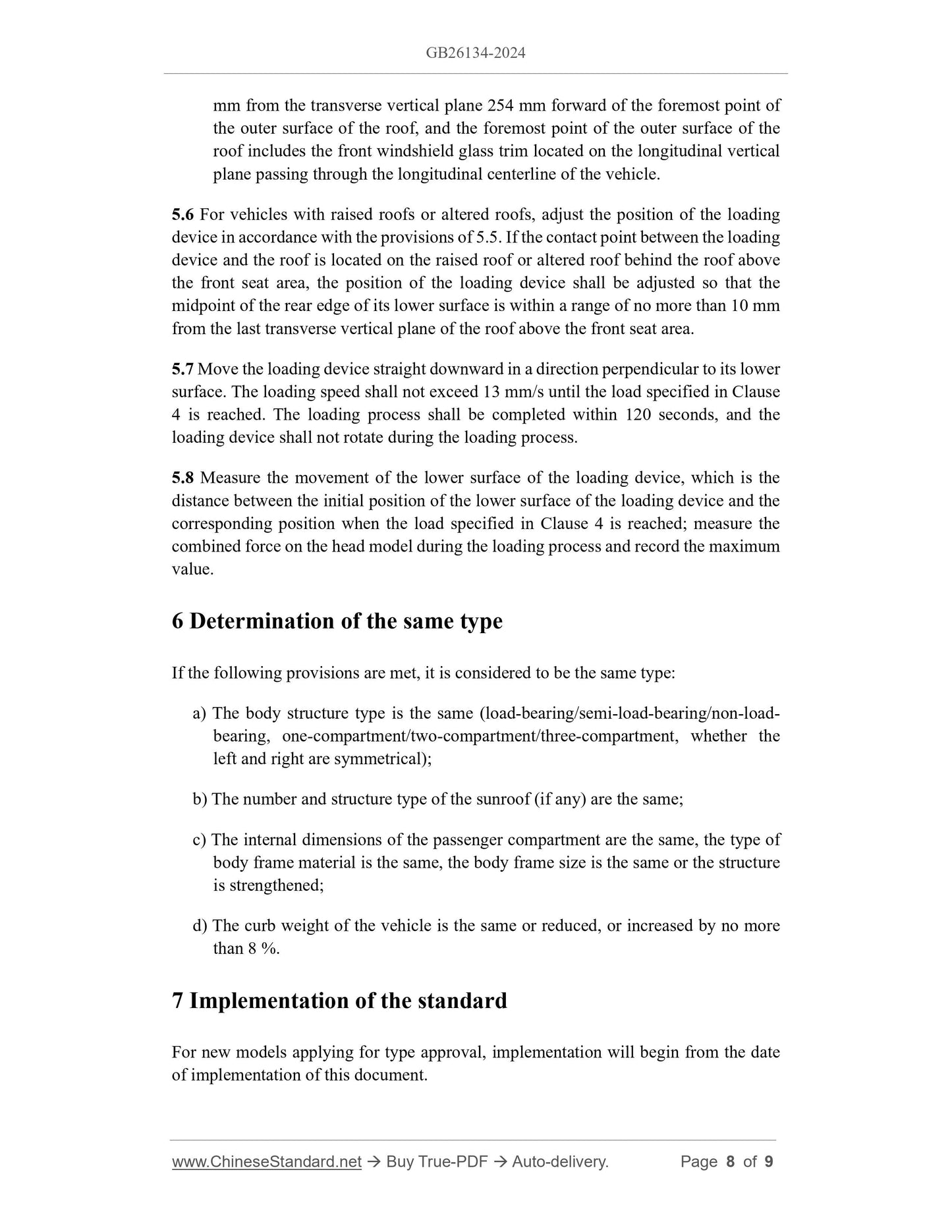
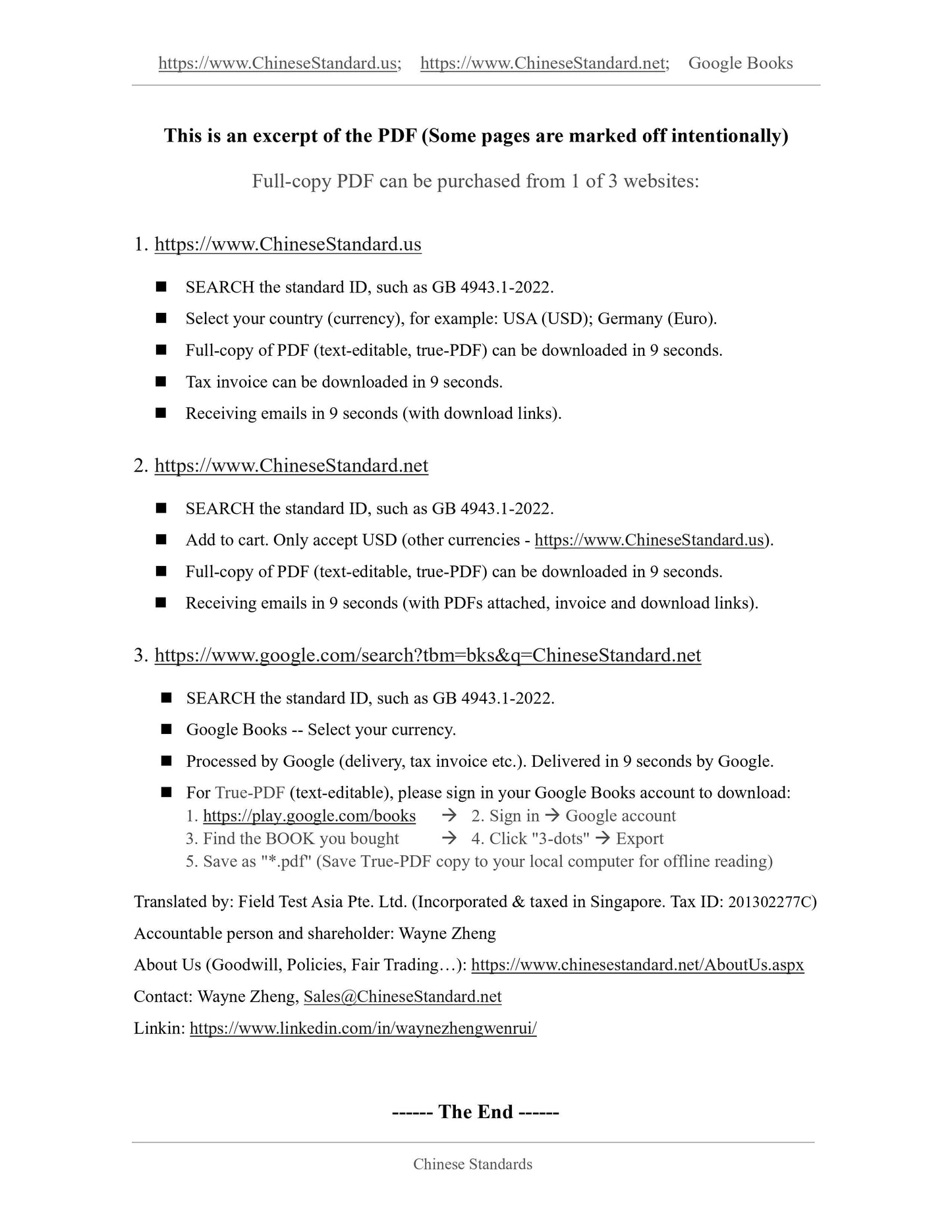