1
/
of
12
www.ChineseStandard.us -- Field Test Asia Pte. Ltd.
AQ/T 3012-2008 English PDF (AQ/T3012-2008)
AQ/T 3012-2008 English PDF (AQ/T3012-2008)
Regular price
$490.00
Regular price
Sale price
$490.00
Unit price
/
per
Shipping calculated at checkout.
Couldn't load pickup availability
AQ/T 3012-2008: Guideline of safety management system implementation for petrochemical corporation
Delivery: 9 seconds. Download (and Email) true-PDF + Invoice.
Get Quotation: Click AQ/T 3012-2008 (Self-service in 1-minute)
Newer / historical versions: AQ/T 3012-2008
Preview True-PDF (Reload/Scroll-down if blank)
Delivery: 9 seconds. Download (and Email) true-PDF + Invoice.
Get Quotation: Click AQ/T 3012-2008 (Self-service in 1-minute)
Newer / historical versions: AQ/T 3012-2008
Preview True-PDF (Reload/Scroll-down if blank)
Share
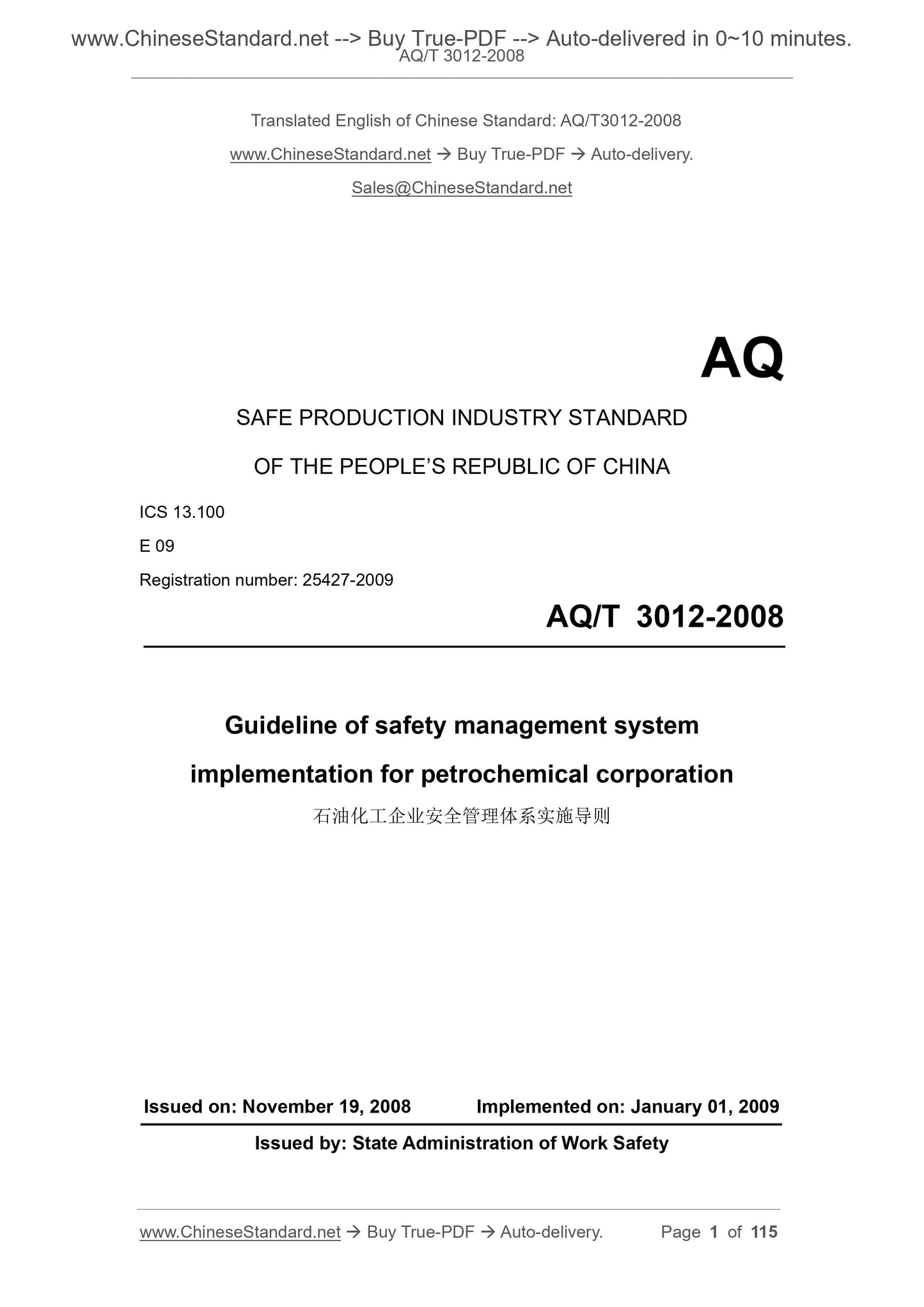
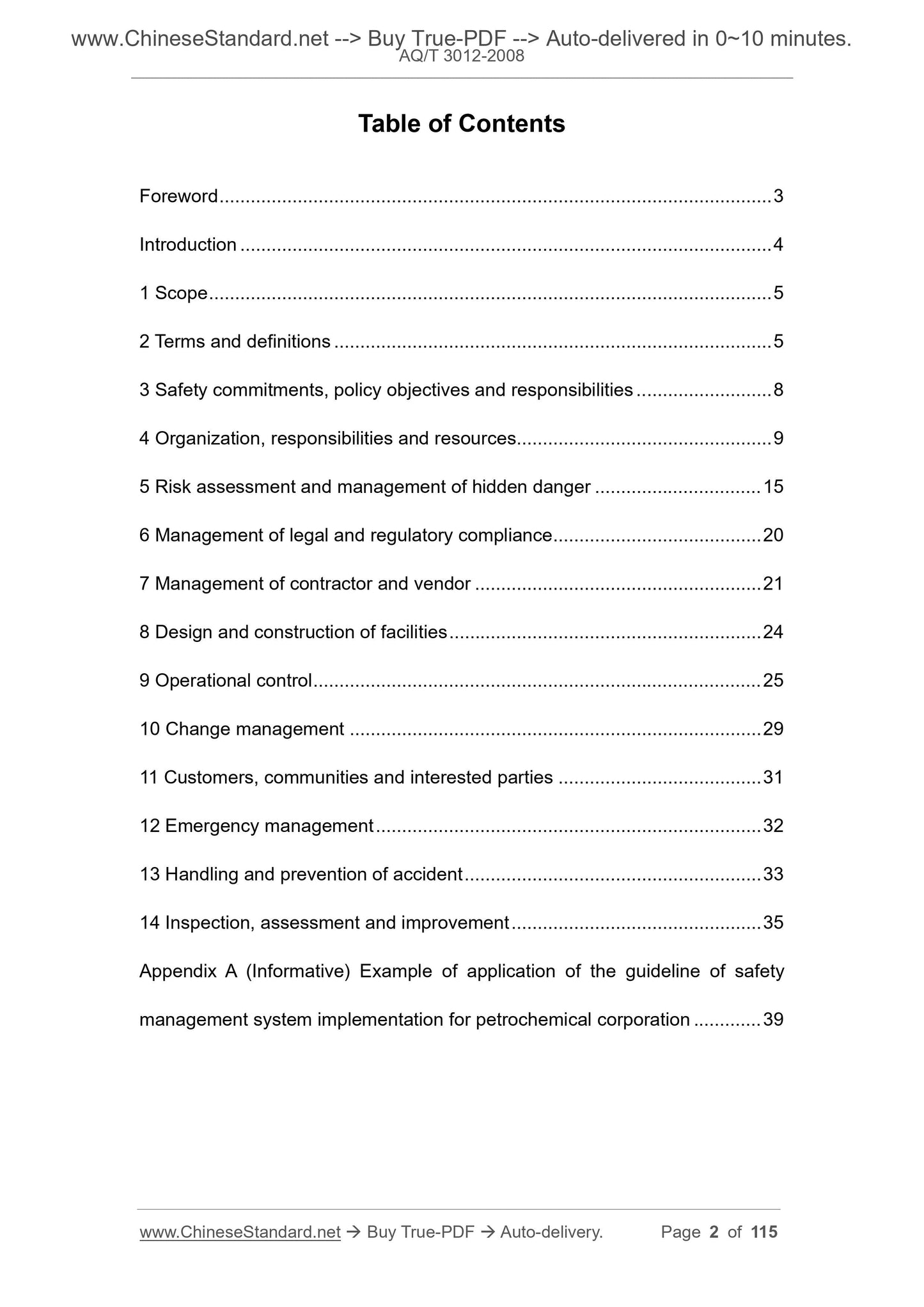
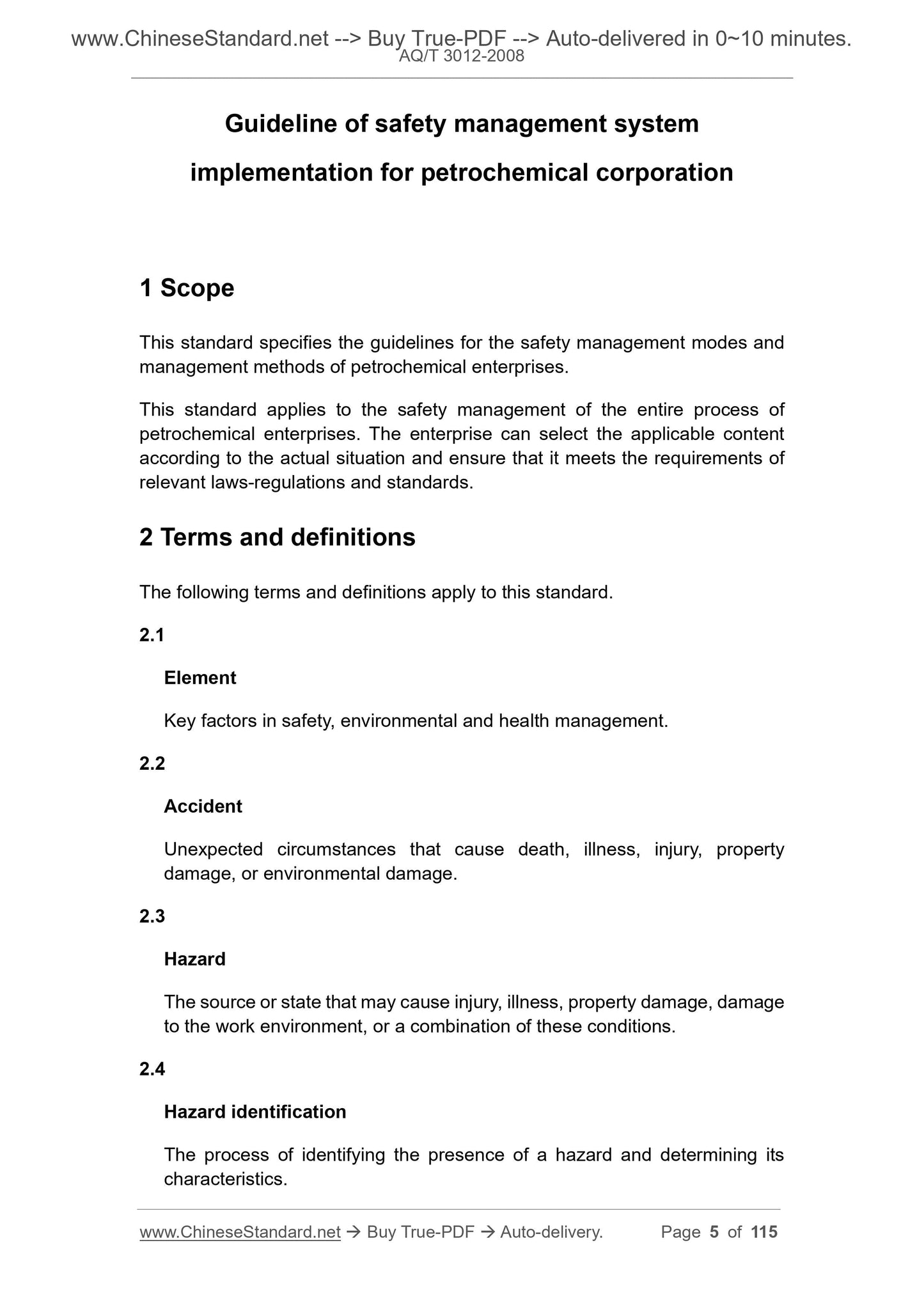

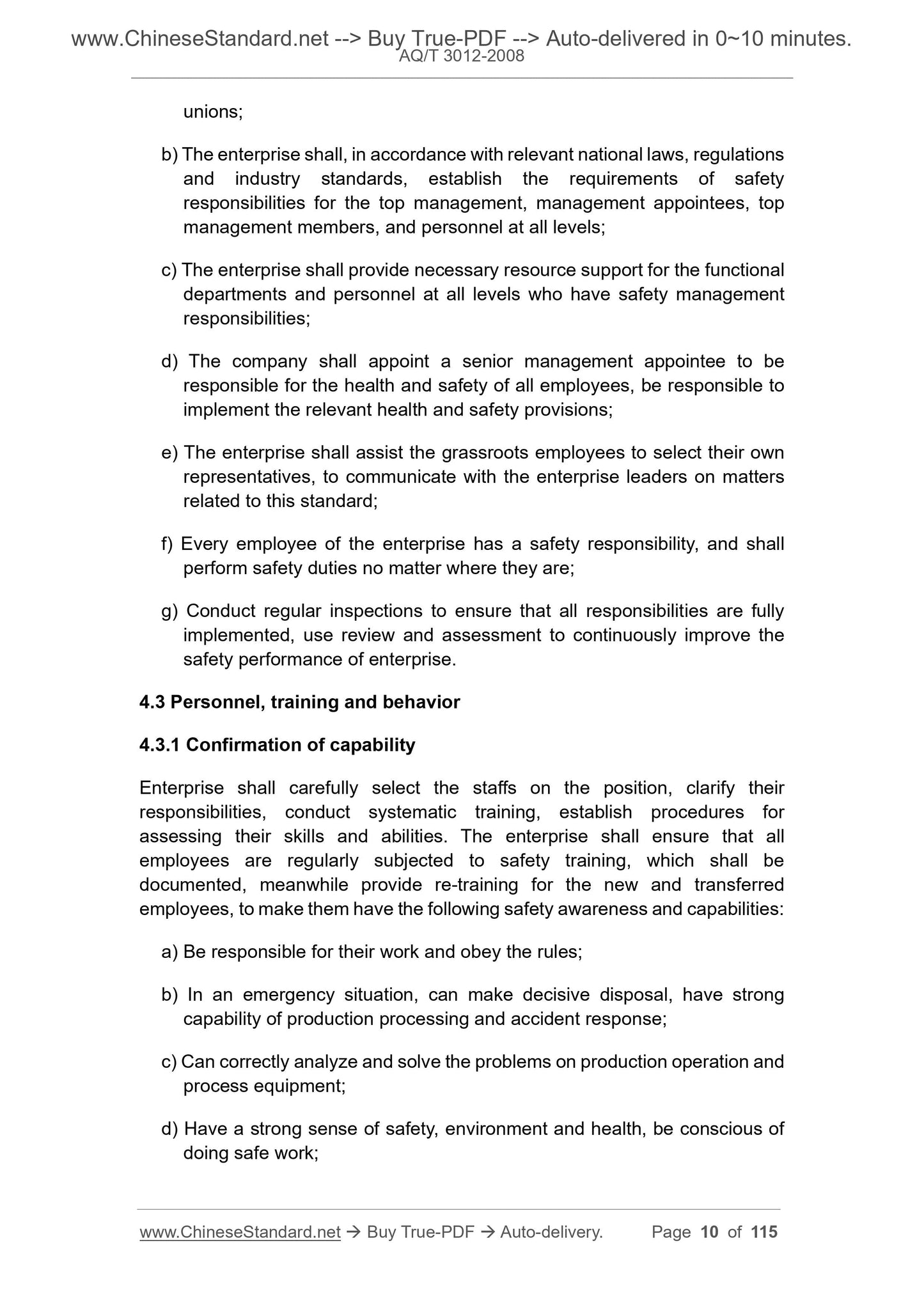
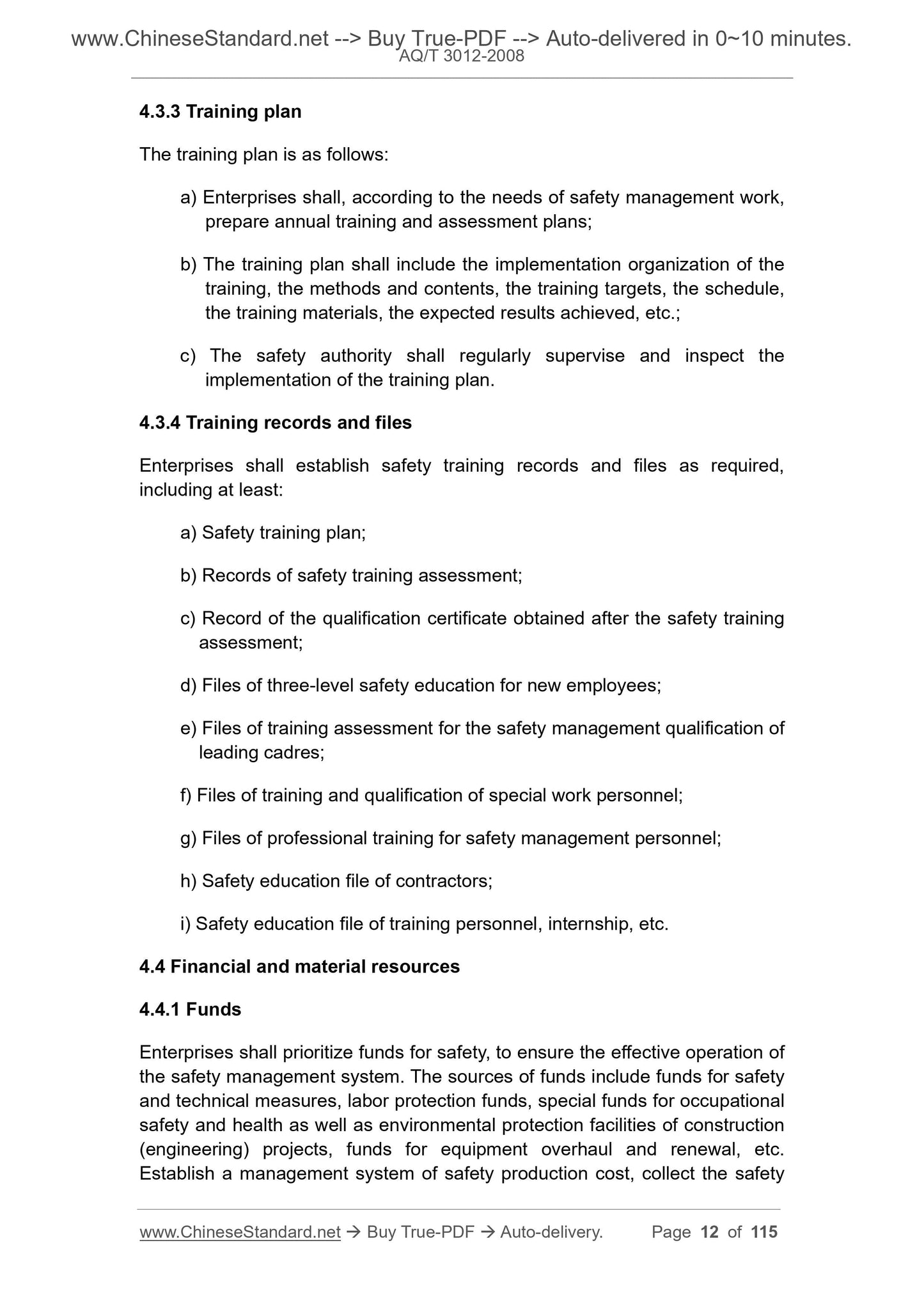
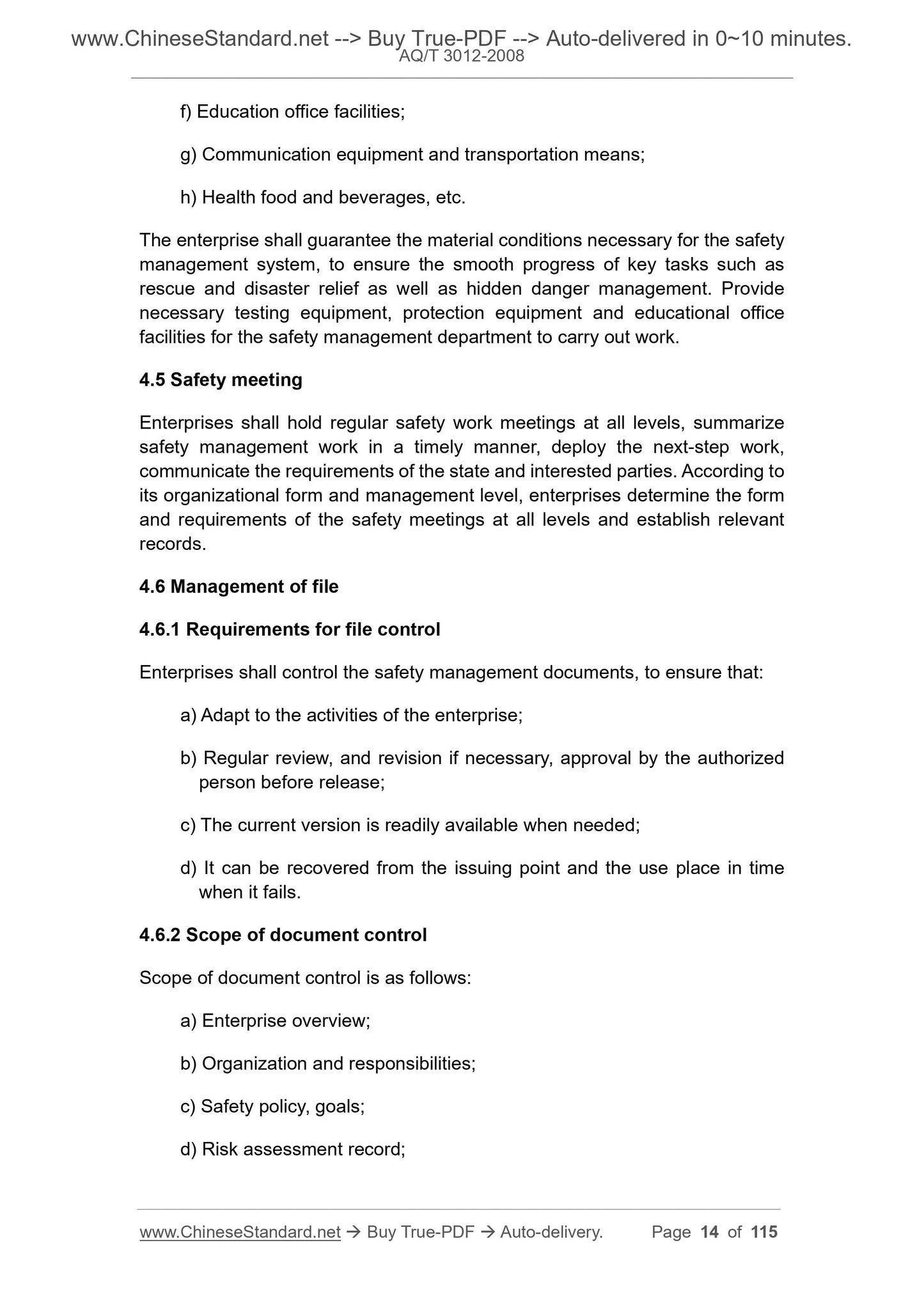
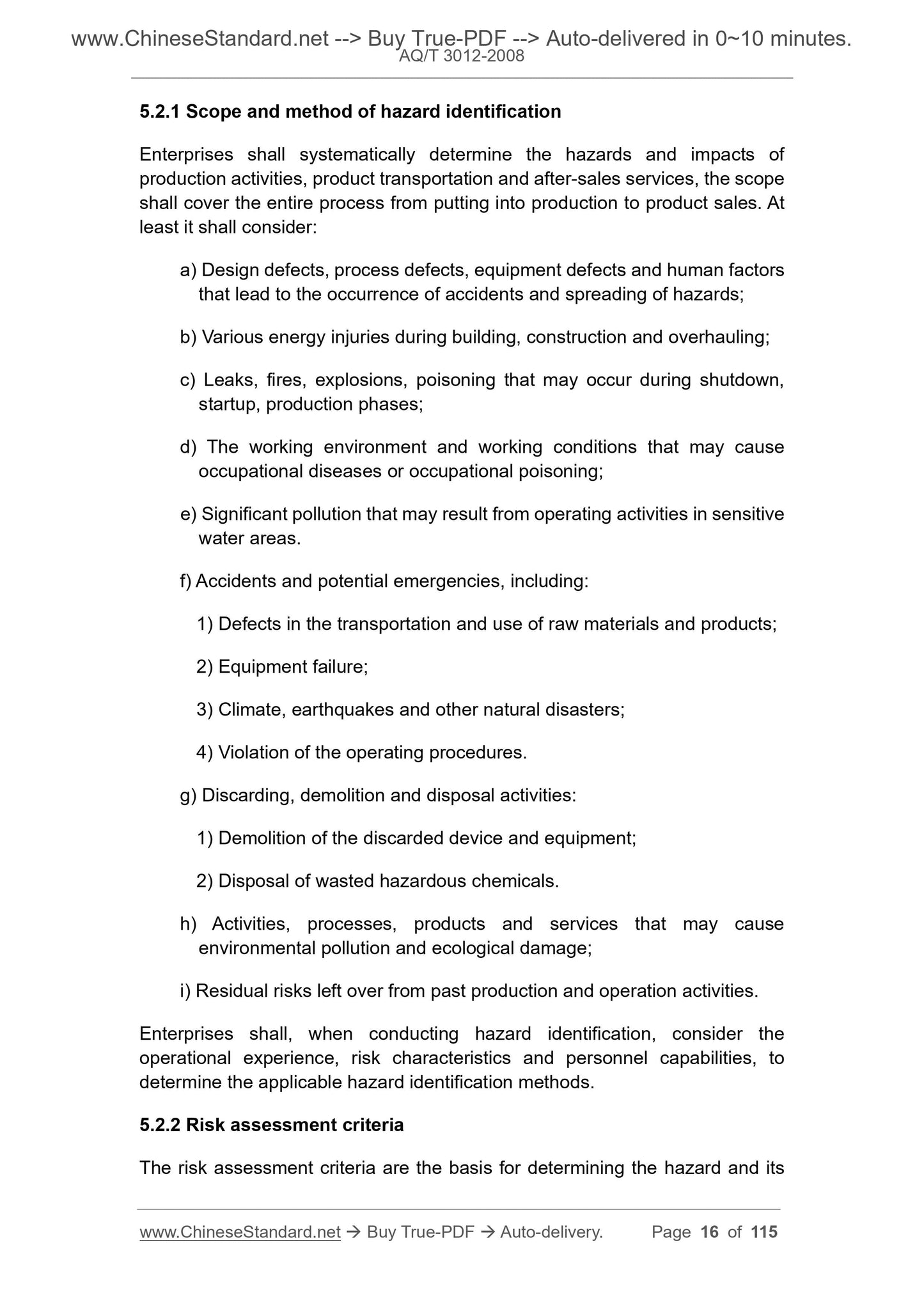
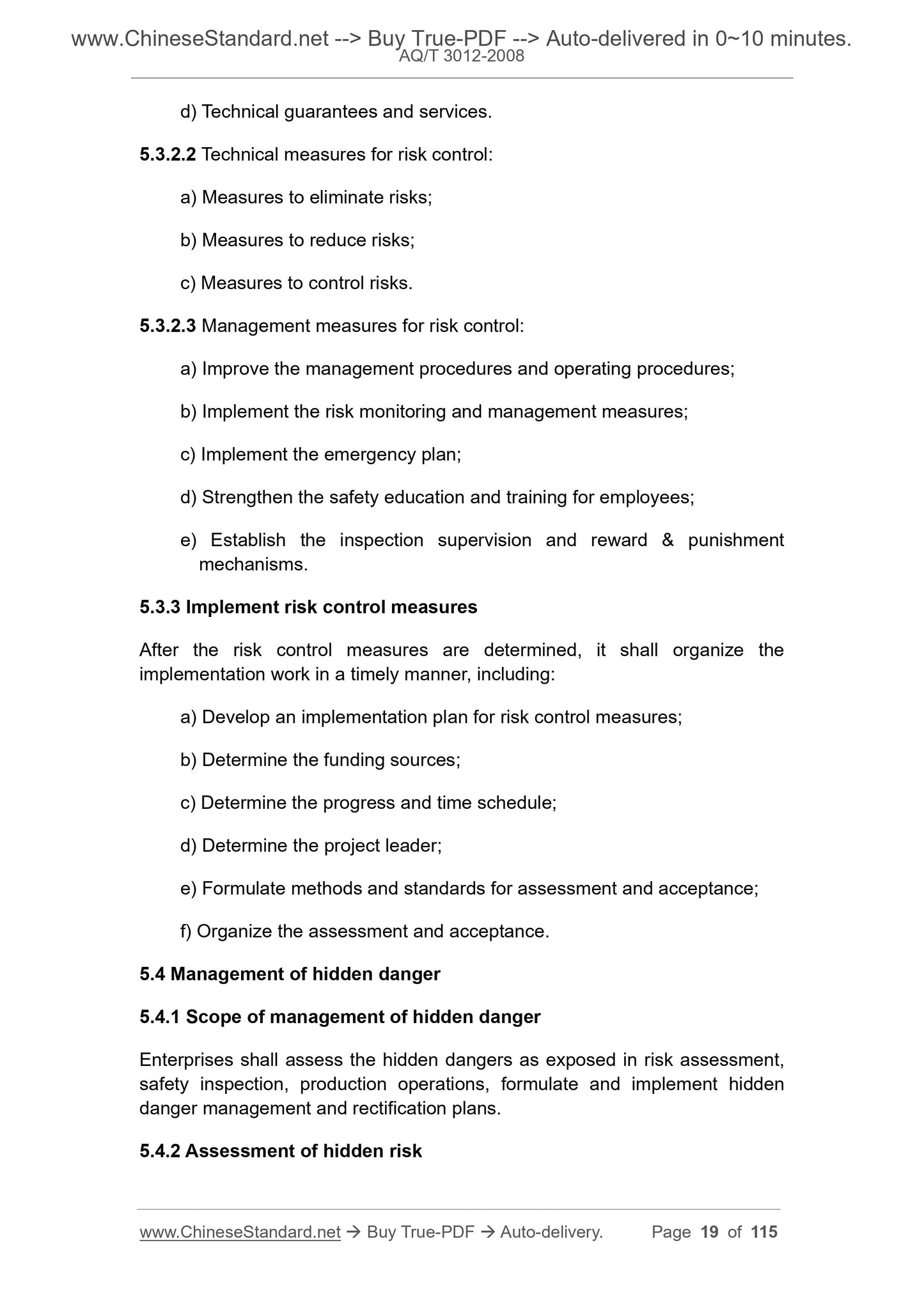
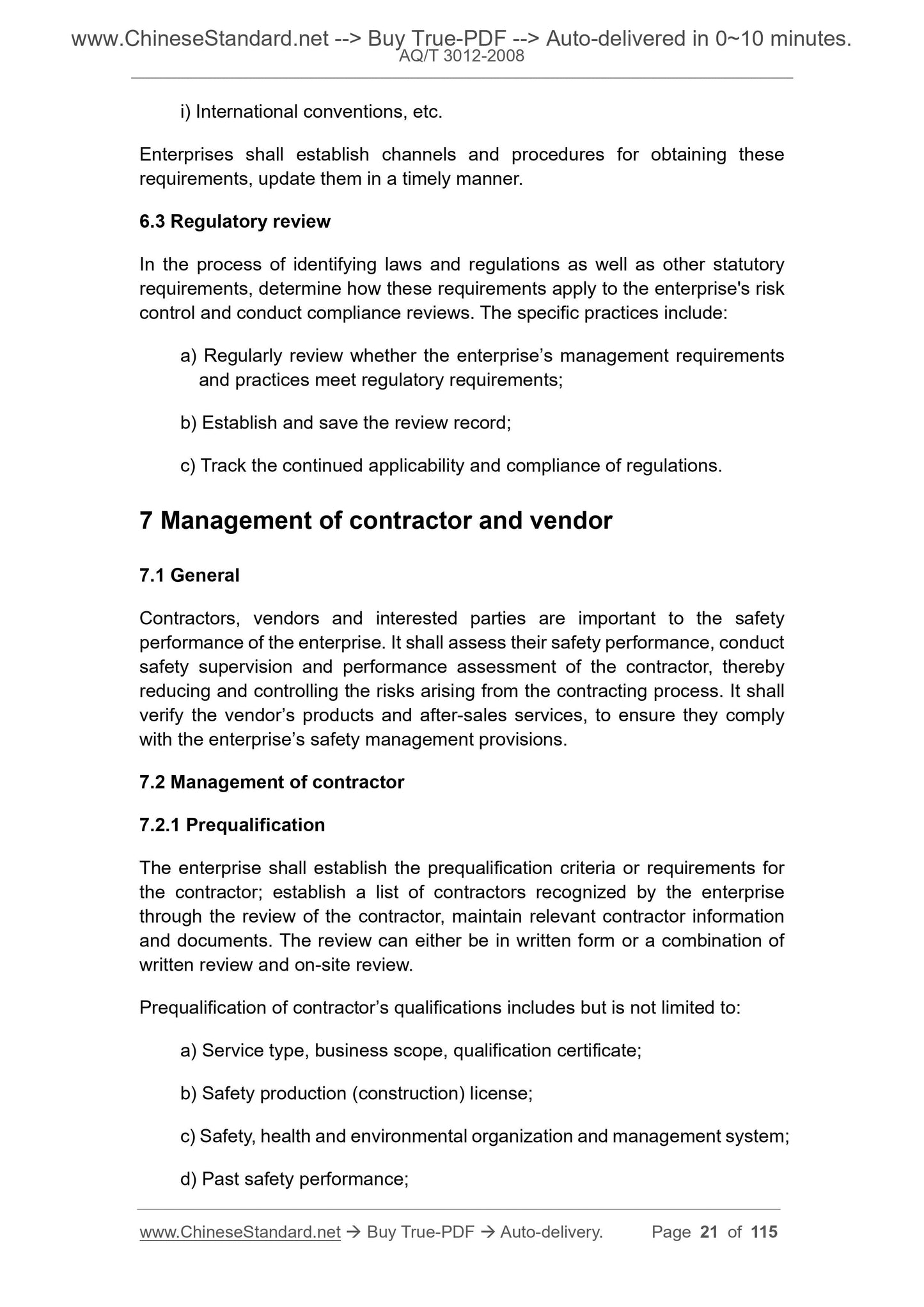
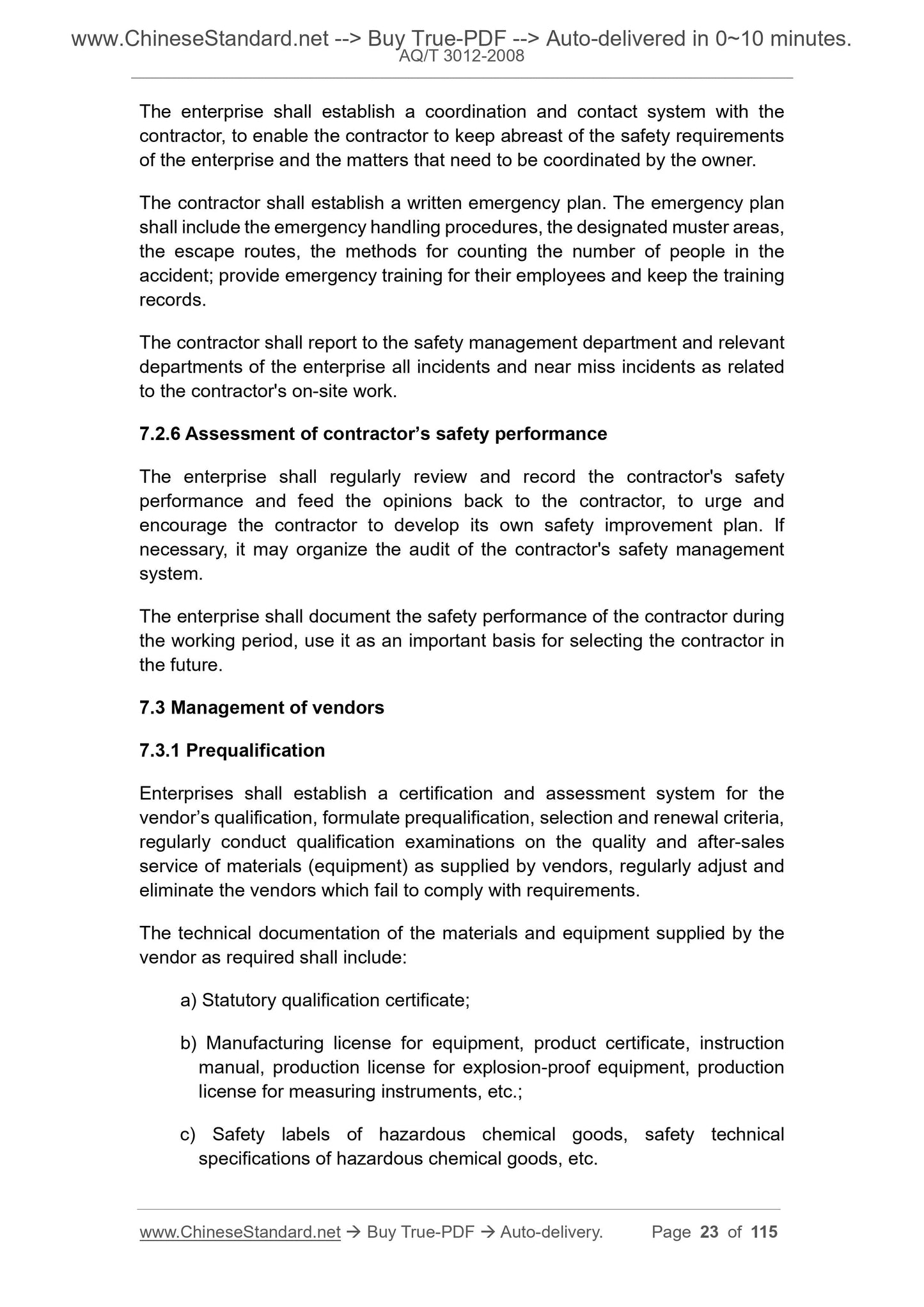
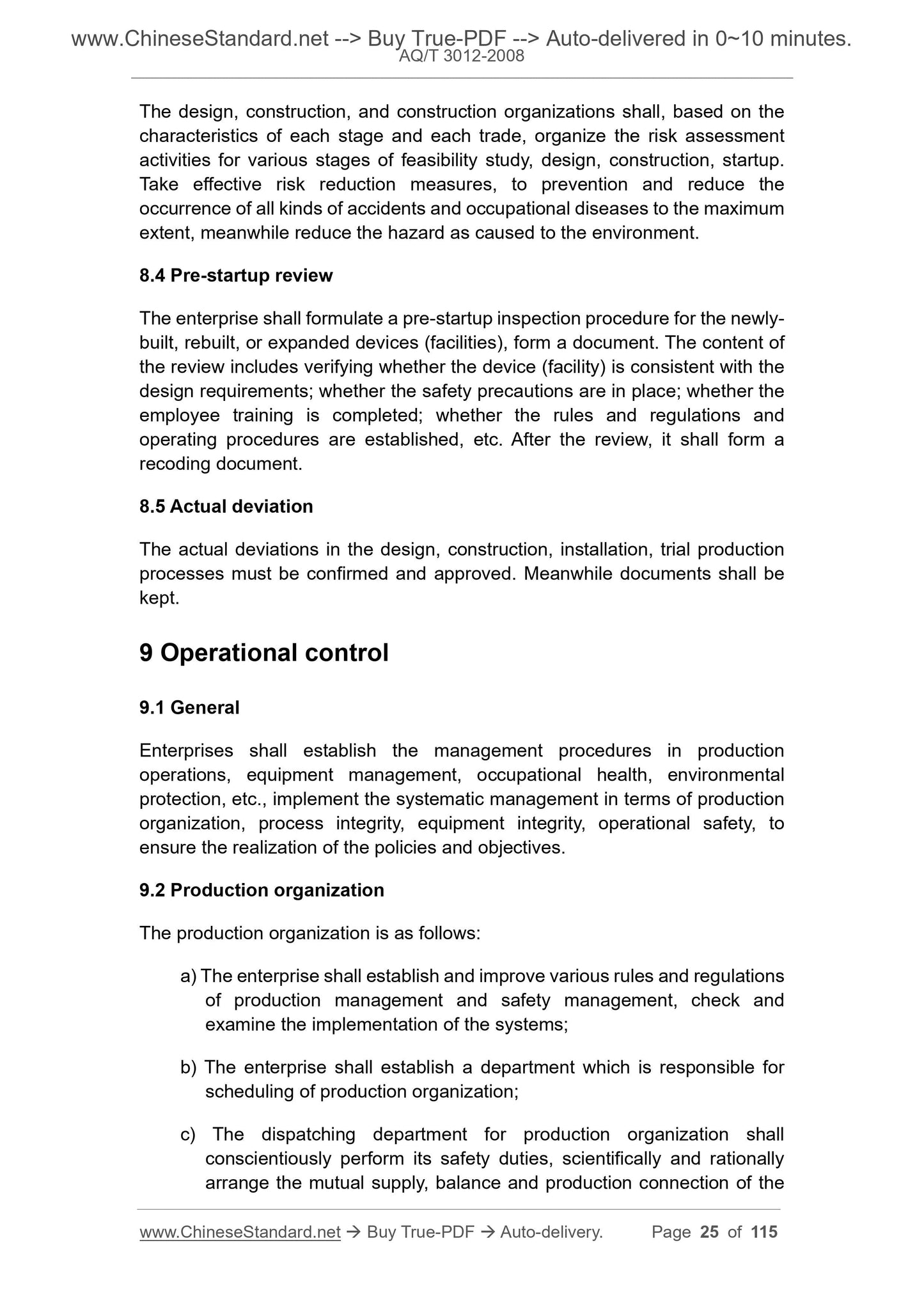